Sturgis Shovel Part 2
By Robin Technologies |
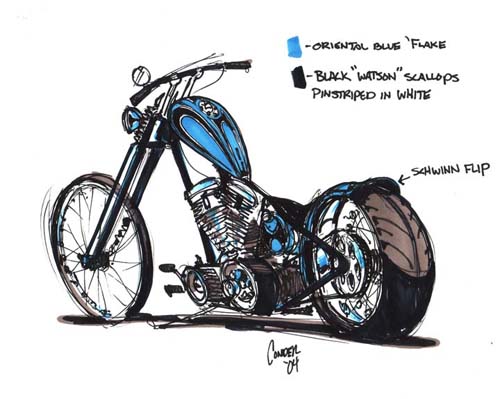
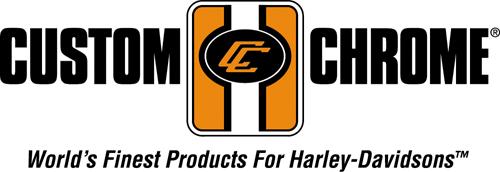
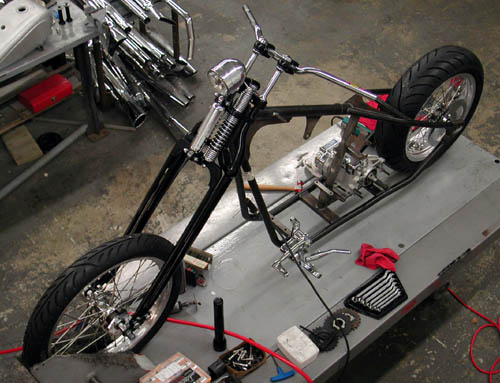

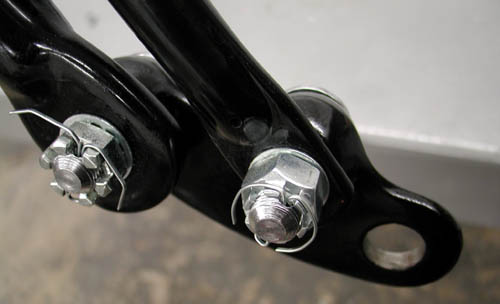
This bike might look like shit, but it should work perfectly. I'm endeavoring to keep it light, tight, narrow and right. So far so good. We've even decided to eliminate paint from the equation, except for rusty metal that may need black powder coating from Custom Powder Coating in Dallas, and the front end was powder coated black at the Paughco factory.

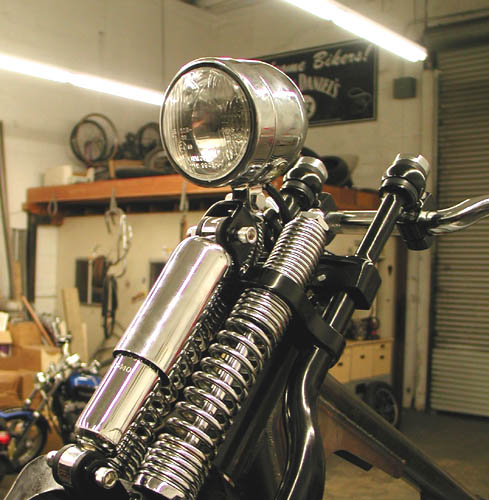
Let's jump into the shop. I was jazzed to receive my Rev Tech wheel order from Custom Chrome. I needed to mock up the frame and ship an image to Tim Conder for a concept drawing. Conder's images inspire any builder. I couldn't move on it until the Custom Chrome wheels were delivered and mated to the Avon Venom tyres. I'm also going to avoid chrome and flashy stuff as much as possible. We're running bare metal in several instances: Wheel rims, aluminum tank, brass fender rails and linkage, copper hard oil lines, and thick wall copper tubing bars. Dig this, we're going to galvanize the frame, rear fender and oil bag. The XR Sportster racing tank which is aluminum was delivered from Cyril Huze. I'm going to leave it brushed aluminum, but the capacity was a minimum 1.75 gallons. I'm mounting it high on the frame so we'll open the tunnel for additional fuel capacity and weld the area shut.
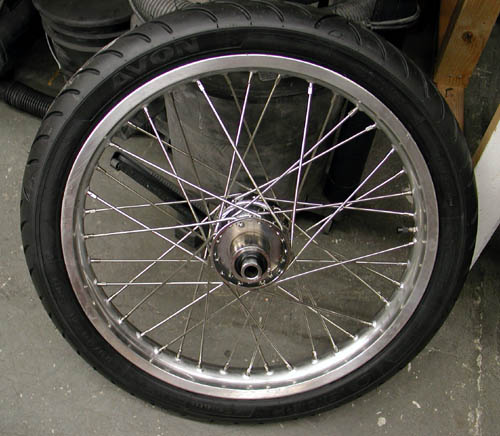
I'm jumping around. Let's get back to the Rev Tech wheels. The spokes are stainless with polished aluminum rims for a long lasting approach. Even the Paughco frame came with brushed aluminum axle plates. We're going to leave 'em alone. Cyril Huze designed a new, between the heads, coil and ignition switch mount. I ordered one without polish or chrome. It's unfortunate that we can't get wheels with Stainless hubs and eliminate chrome all together. The front is a 21 with a 18 by 5-inch rear for a 180 Avon Venom. I don't want a super wide tire. I'm specifically avoiding wide tires. I think they make choppers look like fat-assed chicks. They lose their chopper code of agility and lightness.
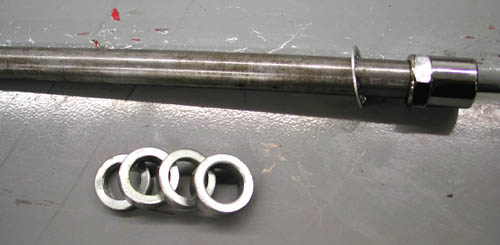
With my Doherty wheel spacer kit I was able to set up wheel spacing quick, for the time being. It's a trick working in the shop by myself and I will try to explain some operations from that perspective. We all face shop blues from time to time. Makes me kick back and rethink various operations when six hands are needed and I'm limited to one on the part and one on the arm of the drill press.
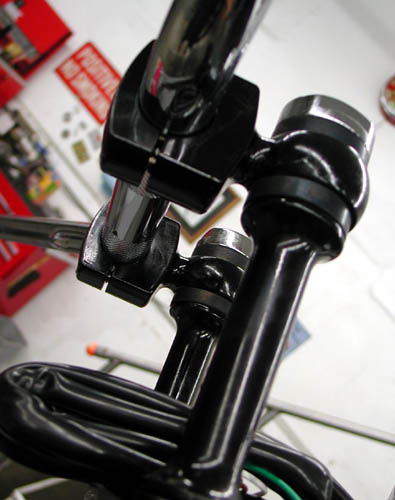
So alone one night I grappled with the installation of the CCI neck bearings (I need a JIMS tool for the races), to install the Paughco springer front end. After a trip to a local fastener store I was able to weave two studs into the rear legs of the front end for traditional, vibration dampening Custom Cycle Engineering risers. The studs needed were 1/2 inch about 2.5 inches long with 1/2-20 threads on one end and 1/2-13 on the riser end. The shop only had two different-length studs and one needed additional tapping to fit.
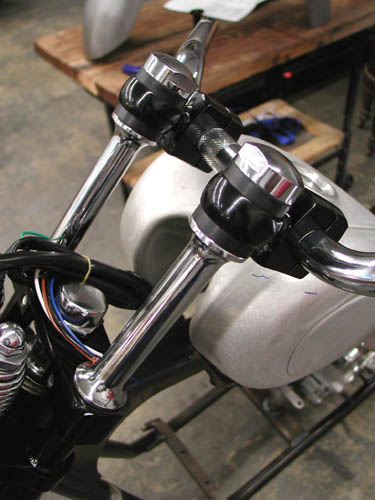
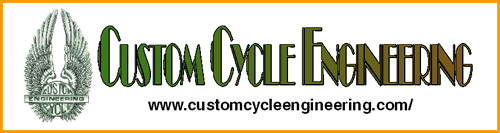
I use these risers on most of my bikes because of the traditional, old school appearance and the vibration element for long runs, but they take a degree of thinking since they shove the bars toward the rider (and often the tank) about 2 inches. I needed to watch for the appropriate amount of tank clearance and ultimately needed the 1-inch longer stems. Very high bars can be a problem with the leverage against the flexible rubber, but with patience, they will work fine. Since each riser is a single unit, they will flex and pivot until they're aligned and tightened down.
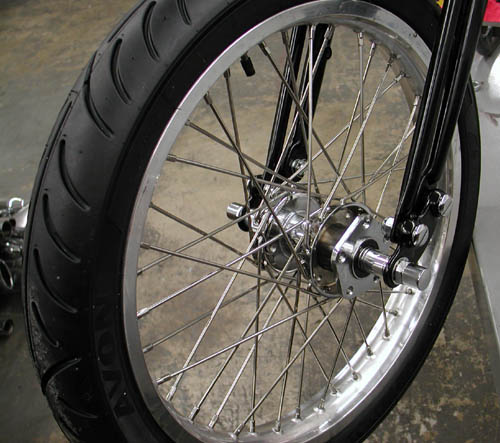
I installed low rise drag bars from Custom Chrome/Khrome Works. I'll see how they fit as the seat is mounted. I ordered a seat at a swapmeet this weekend, black with brass buttons by West Eagle. My plan is to bend thick-walled copper tubing and polish it for the final bars.
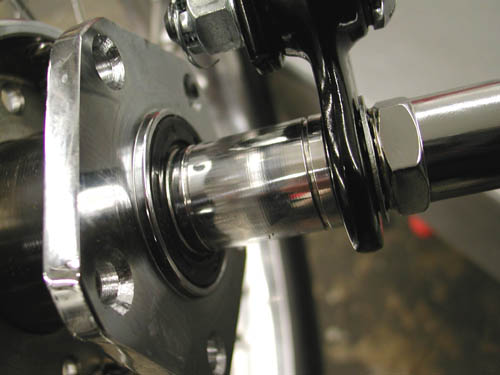

Now Imagine the first time I installed the front wheel, wrestling with the slipping front end and frame, the front wheel, the axle and the spacers simultaneously. Fortunately my 11-year-old grandson was on hand with a rubber mallet to assist. For the rear I used a crate to hold the wheel and the approximate height so I could muscle the axle and spacers through to align it with the frame. It was time for a Corona.

The engine is currently in the hands of S&S for a breast reduction from 103-inch to 93 smooth inches of reliable horse power. I'm waiting on the engine build images to share with you.
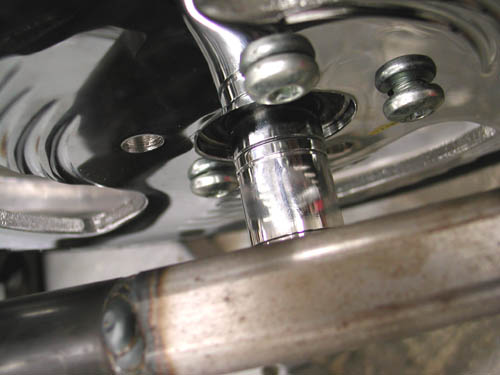
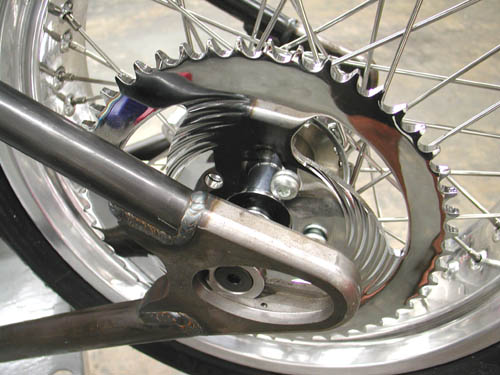
Hold on, I'm slipping the clutch again. Next I mounted the Rev Tech rear wheel with another Avon Venom within the Paughco frame. Unfortunately my Kraft Tech Fender is 9-inches wide and the tire on the 5-inch wide rim runs only 7-inches. I need about an 8-inch wide fender. I'm waiting for the shipment to arrive.
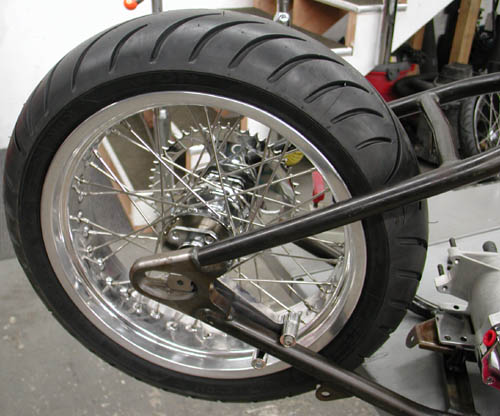
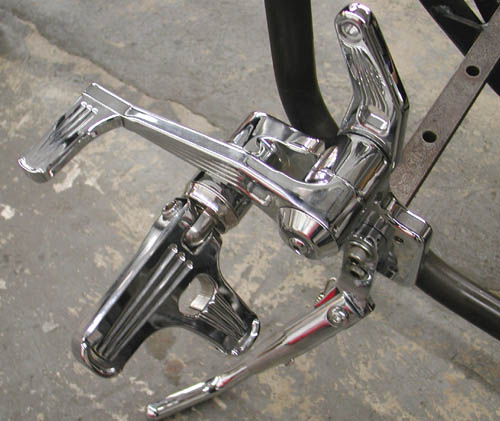
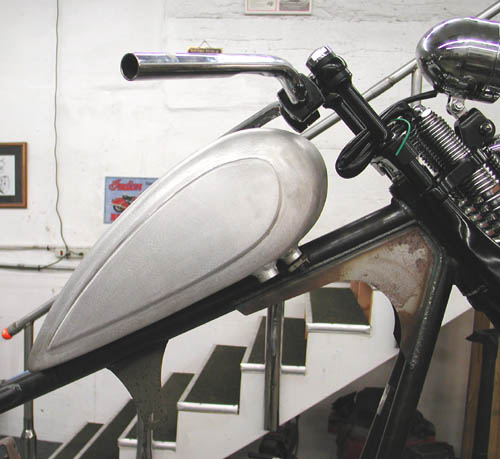
Then I moved onto the tank. I needed to create a couple of bungs for rubber mounting the rear of the tank and tap them for 1/4-20 threads. It was the first time I used our new/old lathe. This is all a new learning experience at the new Bikernet Headquarters. I grabbed a lathe that was rusting in Japanese Jay's backyard. He wasn't using it and I wanted one to cut wheel spacers. I reworked and cleaned the lathe until it was operational then the Doherty crew created a wheel spacer kit? Ah, but the lathe has a myriad of uses, like cutting bungs from a chunk of aluminum. Worked great.
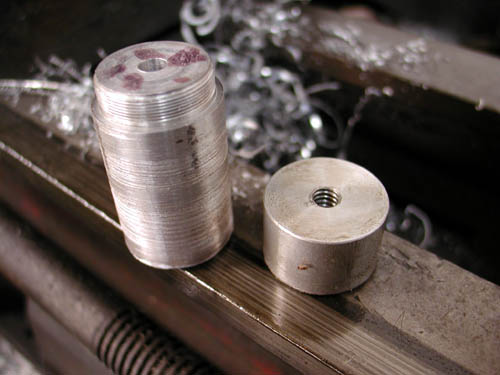
Then I tapped them using the lathe chuck. I discovered that the tank petcock bung needed moving to the rear, since the tank was mounted at an angle. I cut it out with a die grinder and returned to the lathe to machine off the welds.
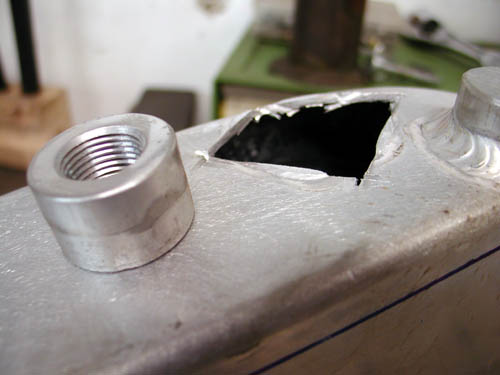
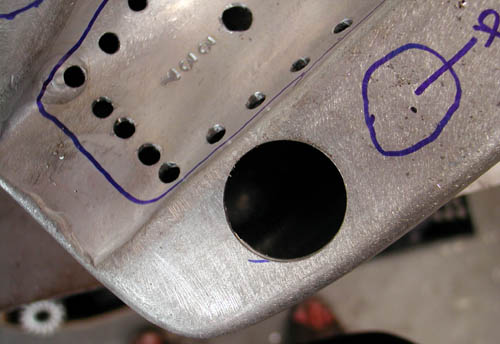
Next I need to learn how to use my new/real old, milling machine. My dad was a machinist most of his life and ultimately an engineer in the oil well industry. As a teenager I worked in machine shops and picked up equipment experience between smoking joints. I swear I learned something.
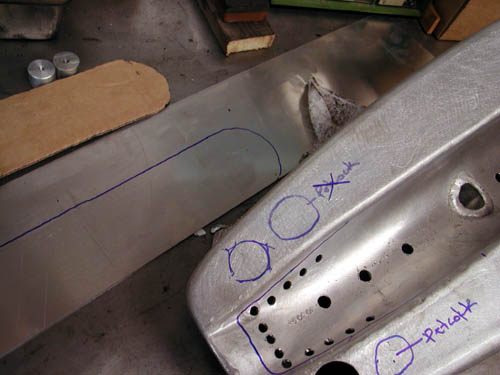
Let's see, what else. I dug through our parts bins and found the exact bracket I needed to mount the Kraft Tech oil bag. I need to cut off the existing coil and oil bag brackets and make a new front mount.
Wait a minute I'm slipping again. I dug through my bracket drawers and pulled a couple of old Jammer brackets 1/4-inch thick. I drilled 1/2-inch holes for the rubber mount grommets from Cyril Huze. I bolted them in place.
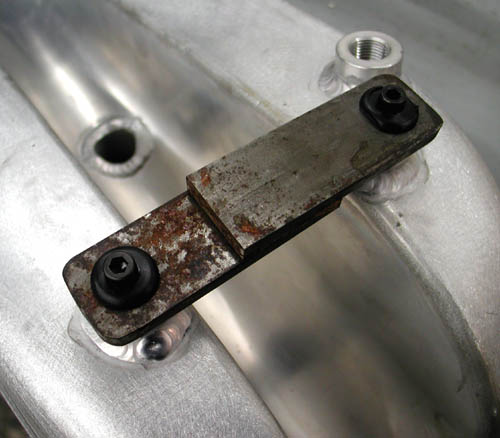
Next, I carefully measured the backbone tubing of the frame and figured the dimensions of the tabs and carefully marked and cut them, then beveled the edges for strong welds.
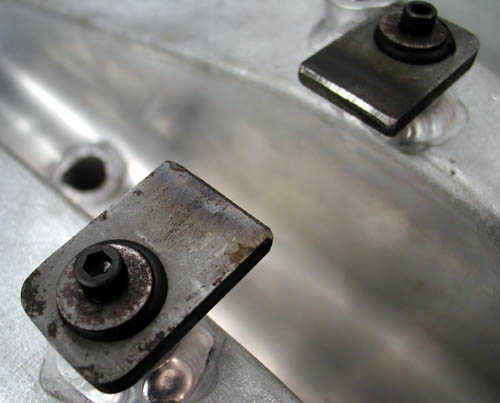
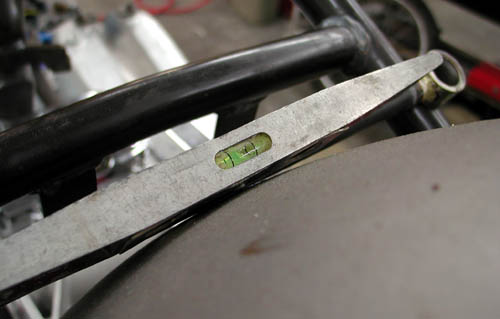
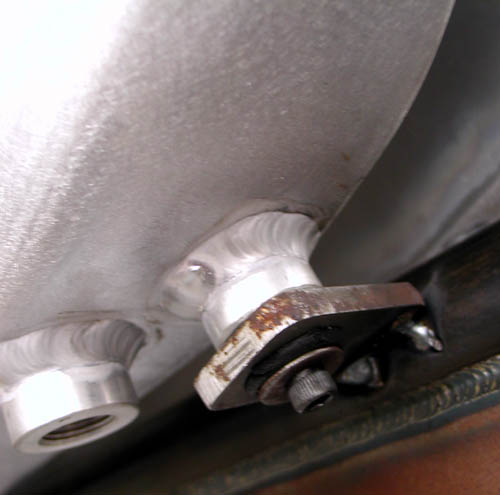
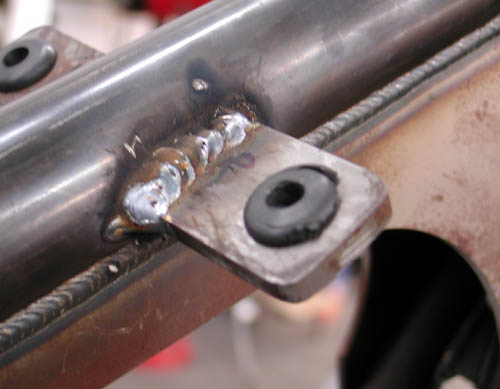
The next day under a sober sky, I refit the tank, tacked and MIG welded the tabs. Once the Bill Hall, pro-welder, welds my tank bungs in place and the tunnel is capped, I can make the final rear tabs and mount the tank semi-permanently. Is that possible?
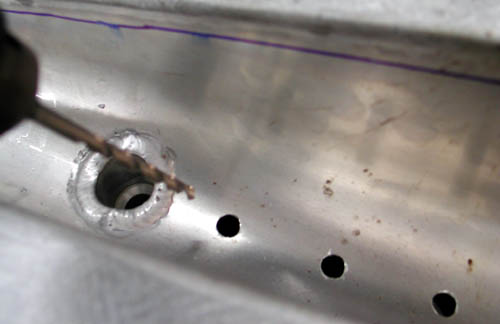
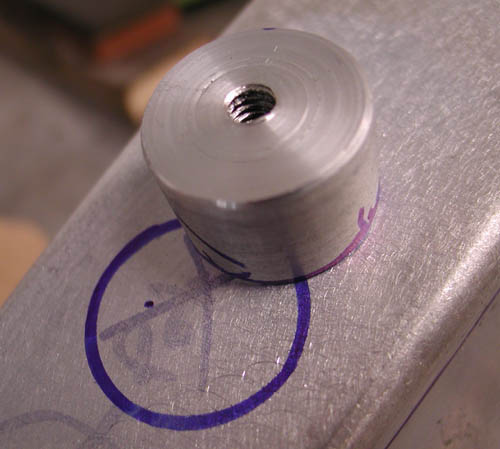
Next, I will mount the Kraft Tech Oil bag, the rear fender and sprung seat mechanism. I'm also dealing with the rear drive. The frame was set up for belt, but more and more I like the chain notion.
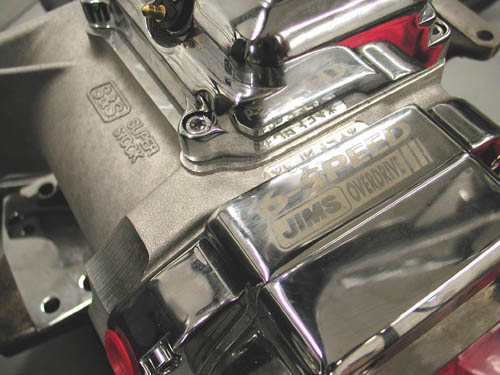
The JIMS machine tranny is set up for 4-speed applications with 6-speed gears. First, I ordered the wrong Custom Chrome tranny plate, then I was twisted about the sprocket vs. belt pulley needed to drive the bastard. I dug through old parts bins until I found gears, since it looked like a gear-driven job. Then the sprocket didn't fit. I'm still trying to figure it out.
I'm going to meet with Jim of JIMS in the next couple of days and get to the bottom of it.

Although the frame is set up for a belt, that means if I run a chain, I'll have plenty of alignment flexibility. Hang on for my next report.
–Bandit
Doherty Machine
1030 Sandretto Dr Unit L
Prescott, AZ 86305
928-541-7744
mailto:Dohertymachine@aol.com
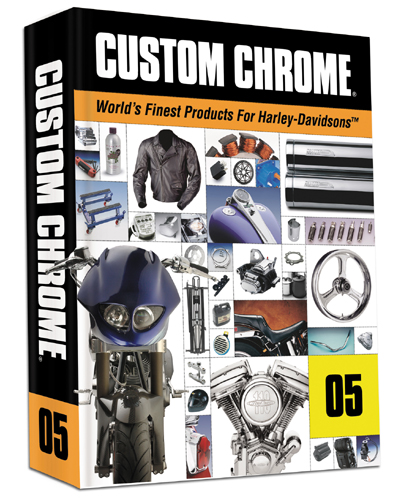
BRAND NEW CUSTOM CHROME CATALOG RELEASED–
Want the Custom Chrome's new offering for 2005. The California based distributor brings you the most comprehensive product offering in the Harley-Davidson aftermarket! At over 1,500 pages and over 25,000 part numbers, their 2005 Catalog features the new RevTech 110 Motor, Hard Core II, bikekits, frames and forks–everything from nuts & bolts to performance products. It's the Custom Bike Bible for the year. No, this is not the latest book, just click on it to find the real deal.
ONLY $9.95 + 6.95 Shipping**
** Price may have changed.
Sturgis Shovel Part 3
By Robin Technologies |
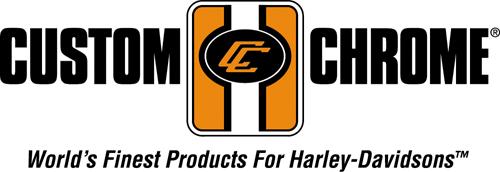
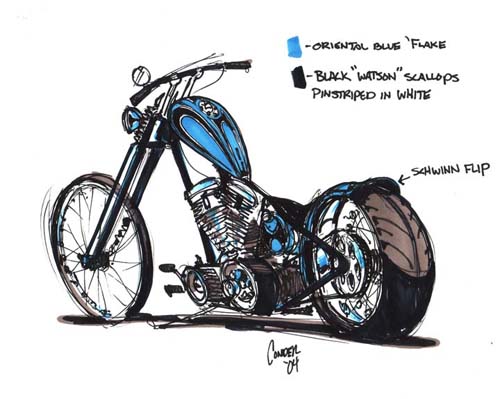
We've developed a working relationship with S&S, and I was concerned about the 105-inch Shovelhead Richard Kranzler scored for my Sturgis Chop project. His motorcycle ran like a raped-ape, but the 105 tore the livin' shit out of his old school chassis. The mirrors became frisbies, the footpegs vibrated lose and ditched him at 125 mph on the freeway. The stress was more than the old swingarm frame could take.
Hot Rod engines are cool but will beat the shit out of a solid mount frame configuration. The best bet is to let them stretch out in a rubber mounted chassis. I called S&S to see what they would recommend and they suggested a smaller 93-inch configuration. James Simonelli put me in touch with Steve George, a 10-year S&S veteran, who said under his breath that they prefer not to mess with engine configurations other than they're own, but he would look mine over.
Made a lot of sense. S&S now builds a complete line of Shovelhead engines in four configurations: Two cone motor and two generator style. Each are available in 80-inch and 93-inch power configurations. Here's a description of their new units:
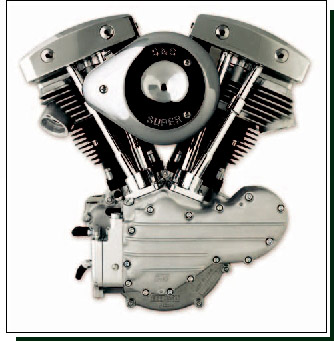
With the addition of the new S&S billet Shovelhead style rocker boxes and tappet guides, along with new pushrods and forged roller rocker arms for Shovelheads, S&S can now offer complete Shovelhead style engines. These engines will be available in 2005
S&S Shovelhead style engines feature the finest parts on the market today. Start with the bulletproof crankcases, flywheels, cylinders, and heads that they've offered for years, and finish the engine with new premium valve train components. S&S billet gear cover, tappet guides, and rocker boxes look outstanding and offer the performance level Shovel builders have come to expect.
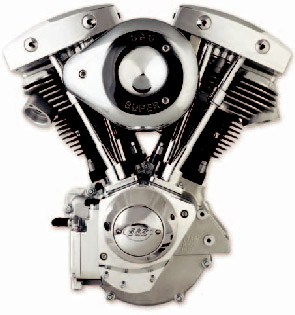
What you can't see inside the engine is just as impressive. The new S&S Shovelhead style tappet guides are designed around the quiet, dependable Evolution style tappets. Corrected tappet guide bore geometry assures correct valve timing using Evolution style cams. The unique adjustable pushrods are collapsible for easy removal and installation, but are stronger than our old style adjustable pushrods.
Inside the billet rocker covers are S&S's exclusive straight rocker shafts and the new S&S forged Shovelhead style roller rocker arms. The result is a Shovelhead engine with the kind of quiet power that some folks may just have a hard time believing.
A new addition to the S&S Shovelhead family is the 93-inch alternator/generator engine. This is the perfect engine for that “retro” chopper, but with a modern alternator charging system.
In addition, the late style sprocket shaft used in this engine allows the use of late style transmissions for additional modern functionality. So when you take your chopper out for a late-night cruise, and you want to see the road ahead as you click `er into 6th gear, this is the one.

Note:S&S Shovelhead style engines equipped with S&S tappet guides and tappets will be supplied with an Evolution style camshaft. Custom engines ordered without S&S tappet guides and tappets will be supplied with a standard Shovelhead style camshaft.
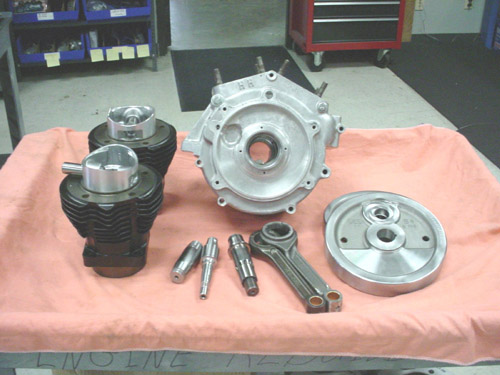
My engine was equipped with House of Horsepower cases. We used the same bore (3 5/8-inch) but S&S barrels and pistons with a 4.5-inch stroke (instead of 5-inch stroke). Stock bore is 3 7/16 and 3 1/2-inch for all 80 and 88 inch engines. This operation basically involved a S&S Sidewinder kit, including (left to right) cylinders, pistons, crank pin, connecting rods, cases and flywheels.
First Steve assembled the short block which was balanced to a 1300 bob weight for smooth operation and reliability. The S&S forged pistons are 8.2:1 compression with longer skirts for longer lasting reliability.
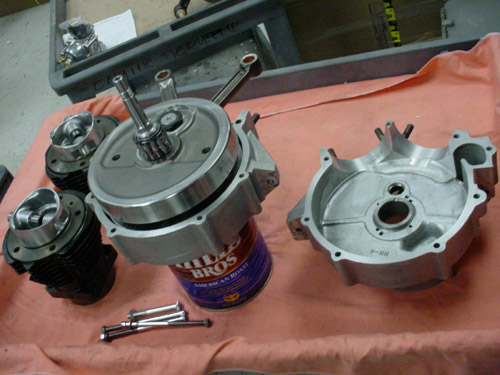
Then he assembled the wheels in the left case with fresh Timken bearings. My cases needed a ledge bored away for the longer skirted S&S barrels.
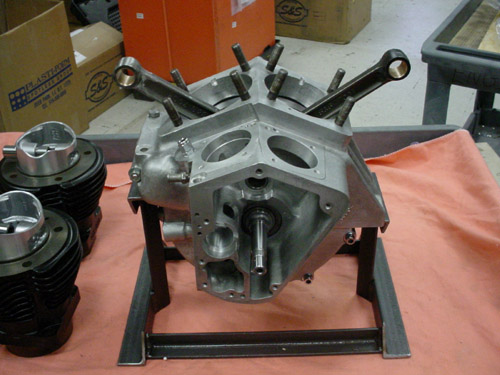
Next the other side of the case was slipped over the pinion shaft roller bearings and the lower end was complete. The flywheel weight is approximately the same as stock Evolution (lighter than Shovelhead wheel) for a balanced running engine and added reliability.
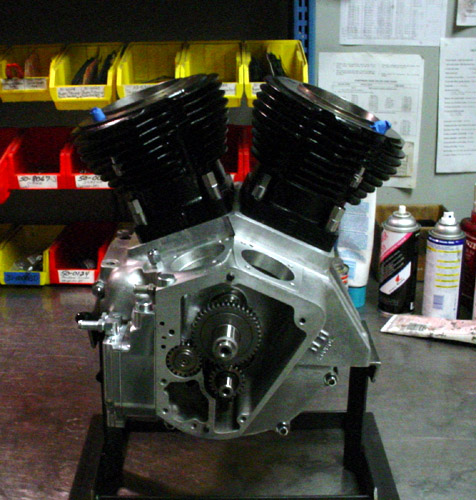
Ah, next came the pistons and barrels. I know we don't have all the details here, but at least you can see the big steps in building an engine. It's not tough but takes precision workmanship and quality components.
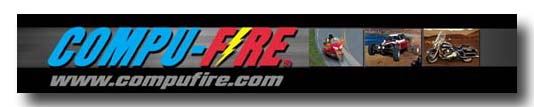
The final steps before shipping included the S&S oil pump installation and the cone cover. I'm returning a Compu-Fire ignition system to the cone in short order.

The engine is now at Phil's Speed shop. He're rebuilding the heads and will install S&S roller rockers, shafts, new Custom Chrome Black Diamond valves, new lifters (with bored-to fit lifter stools) and pushrods. Hopefully it'll be completed next week and ready to set into that Paughco frame. Then I can start bending pipes and making shit.
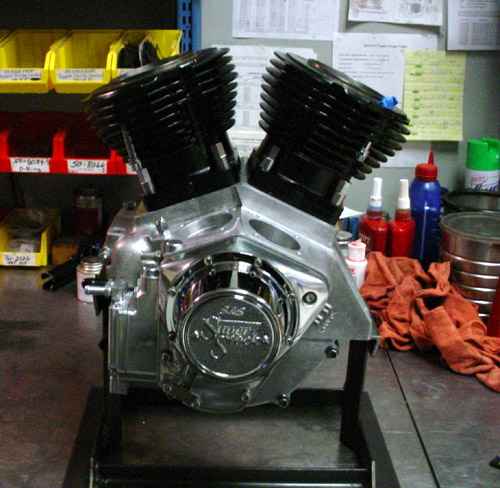
I've worked with Paughco for over 25 years, for quality frames and front ends, then this frame arrived and the tranny wouldn't fit. I had a 4-speed tranny plate that the JIMS trans slip right into, but the holed in the frame didn't align. I spoke to my tech guru, Frank Kaisler who contributes to Hot Bike, Street Choppers and was the editor of Hot Rod Bikes. He lives tech. Of course he pointed out that I needed a first electric start vintage plate. I had a late model, dipped, single sheet plate and the 4-speed job and neither worked. So I sat as my desk and poured a glass of jack. I had the bike buildin' blues.
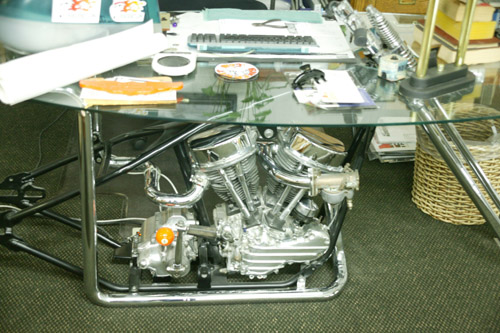
Here's the famous Bikernet Desk. I made calls about the tranny plate, unsuccessfully and slugged that amber liquid until my brow bounced off the glass top and I spied the tranny below–on the wrong plate. I couldn't believe it. All these years that desk ran with the wrong tranny plate, and it just happened to be the one I needed.
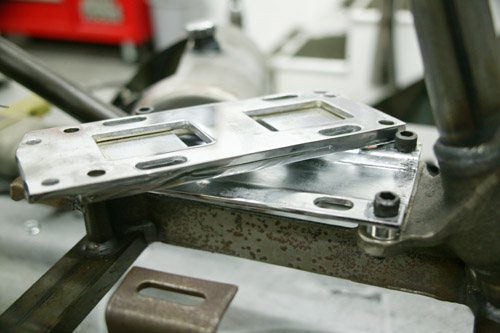
Here's both tranny plate together. The thick one with two slabs of steel is the original 4-speed job. The single, bent-in-the-center sheet with the four frame mount spacers was designed for the first electric start transmissions beginning in 1965.
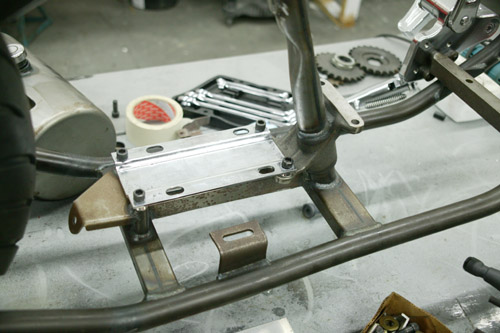
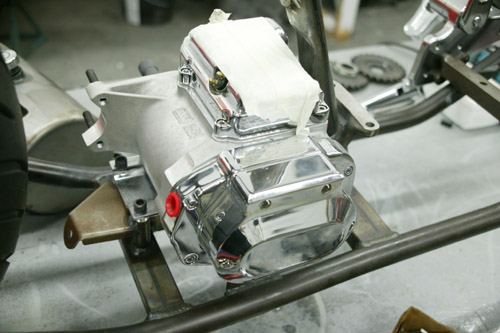
Finally the JIMS trans is in place with the proper mounting plate, and I was ready to move onto mounting the oil bag.
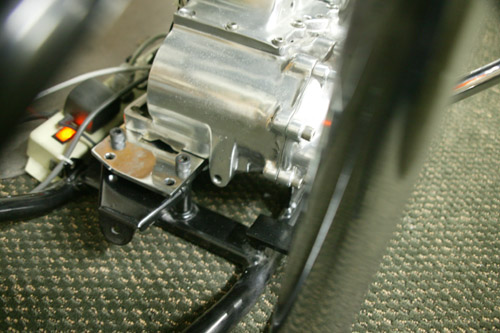
At last, after 15 years I installed the correct tranny plate into my desk. Damn, I'm embarrassed.
The rear fender is on it's way from Lucky Devil and I installed the Kraft Tech round oil bag last weekend. Movin' right along. You'll see that tech shortly. A new oil cooler/oil filter set-up is on it's way. It's a must for making the old iron last.
Sturgis Shovel Part 12
By Robin Technologies |

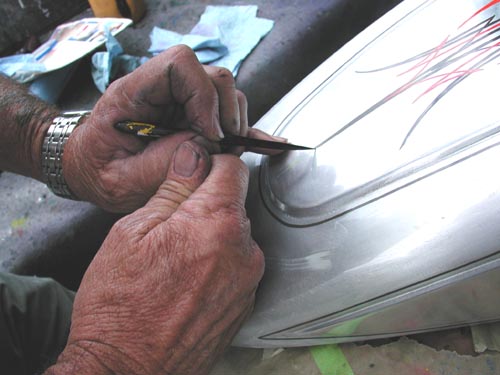
Hey, here’s quick bit on George The Wild Brush who handled the Pin Striping on the 2005 Sturgis Shovel project. He’s pin striped several other bikes for me in his 47 years behind the brush. Born in Hanford, California, a miserable military town, in 1944, he kicked tumbleweed while his mom worked on a base.
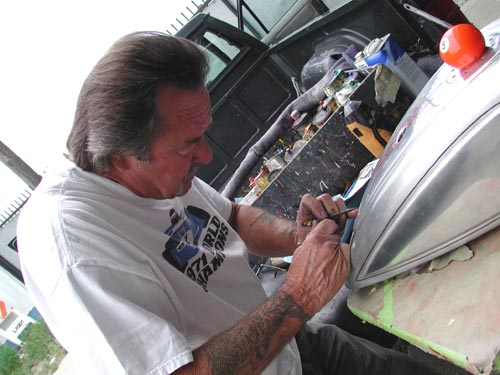
She moved to the safety of Southern California away from the miserable summer central Califa heat, to Long Beach then Lakewood (next door) where he went to school, but didn’t graduate.
He was warned that the fad would die so his vocation would fail. “The fad’s still rockin’,” George said. “My first car was a ’54 ford and I custom painted the driver’s side. I couldn’t afford enough paint to finish the passenger side, so I had the only cool side.”

He studied Von Dutch work, Larry Watson and George Barris. “I’ve striped refrigerators, toilet seats (new ones), and 50 and 110 Tom Gentry trans Atlantic ocean racing boats. He’s taught me a thing or two about striping. “It’s best to have the parts off the bike for the best quality art.”

It’s difficult to paint bare aluminum—“Paint won’t bond to it.” without a primer.” I worked at Gasoline alley for 15 years painting aluminum dragster bodies.
It’s also difficult to pin strip chrome—“It won’t hold up due to the lack of porosity.”
He only uses One-Shot enamel paints—“Can’t use any paint.”
With motorcycles it’s a good idea to clear over striping—“People don’t pour gasoline all over cars, but they do bikes.”
Cars don’t generally need to be cleared over striping work.
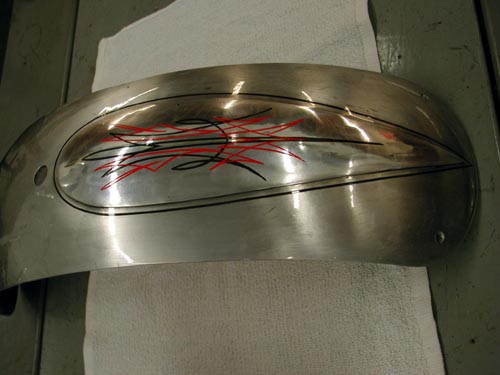
His number is (310) 488-5488 for classic pin striping and good stories.
George came to the shop just after I picked up the clear powdered aluminum sheet metal from Foremost Powder. He usually tells me what I’m going to have striped. I have a vote and initial color selection, then I best get out of the masters way.
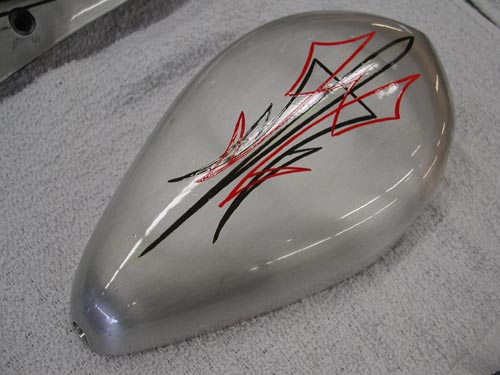
He striped the Goodsen Air Cleaner, which was treated to my holy treatment, then brushed with Scotchbrite to remove the polished appearance.
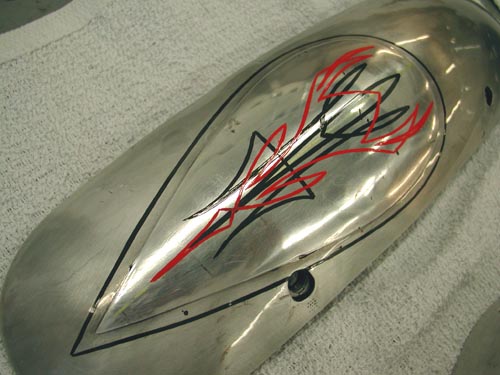
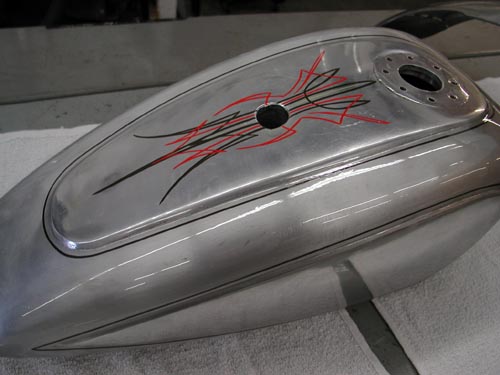
Then he striped the panel polished, highly-modified, XR750, Cyril Huze donated tank and Lucky Devil, custom made fenders. I polished the panels and brushed the rest for a two-tone effect. Not sure it worked, but George gave it a final touch.
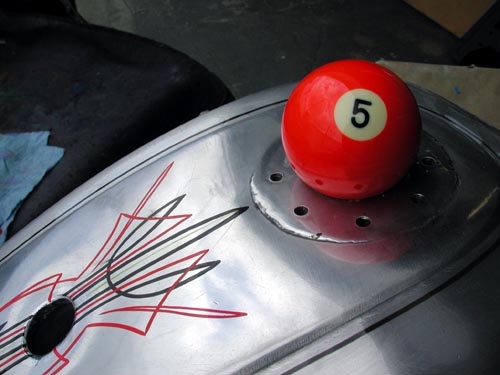
George suggested the 5-ball addition to the center of the tank. Not the gas cap. Ultimately I filled the center-mounting hole with a small 5-Ball to commemorate our company and all the women who put up with my shit over the years. In case you don’t know the story, I’ve been married five times, that’s five misses Ball.
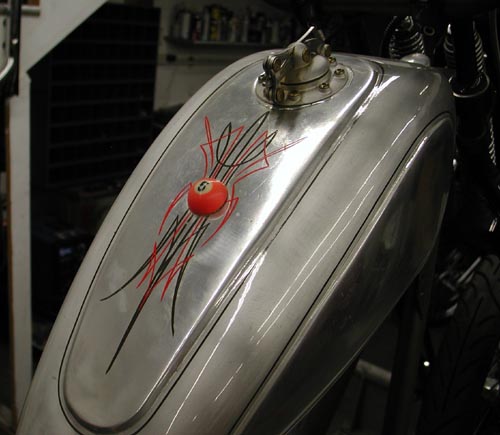
Sturgis Shovel Part 5
By Robin Technologies |

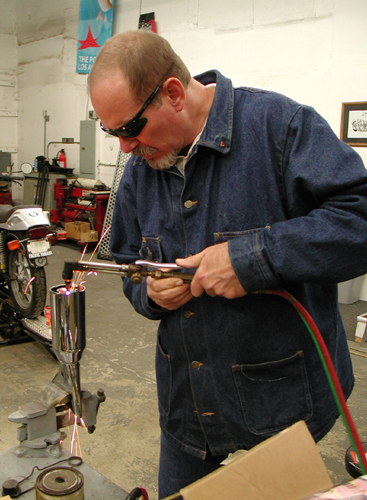
Helluva weekend. Anytime there's lots of motorcycle carnage,sex, whiskey and writing, I'm all for it. Maybe it's Valentines Daycreeping up. Make a note. Here's the deal on the Sturgis Shovelhead. Sincethe engine was in and mounted I went to work on the exhaust system,then seat mounting, position and played with the bars. I made a runto a local steel joint, because I had a notion that I doubt will worknow, but I'm still investigatin'.
Let's hit the highlights. I'm fortunate to have a young,talented fabricator/builder who I'm sharing ideas and resources with.Kent from Lucky Devil Metal Works in Houston is on the phone dailyfor tips and knowledge sharing. It's damn healthy to have someone whois in the trenches daily to assist. In fact I had a couple ofcrucial metallurgy question that morning, but let's hit what Iaccomplished.
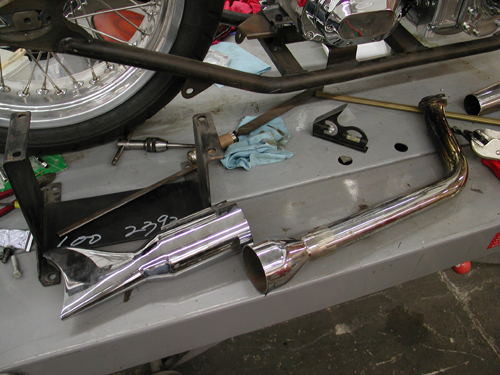
A crucial aspect of building any bike is planning. That'snot to say all my eggs are in a row. We'll see, but the more you canaccommodate, the less redo's will be necessary. Also, don't throwanything away. That junk part might be a critical bracket tomorrow. Idug through my partially organized pipe bin and found a set of oldglass pack, shorty muffler, shot gun pipes. I could use the rear one.I decided, since noise issues are a concern and performance issue area constant priority, I would build a set of shorty mufflers withBandit tuned baffles.

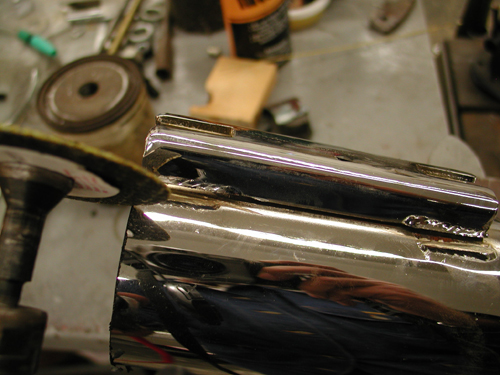
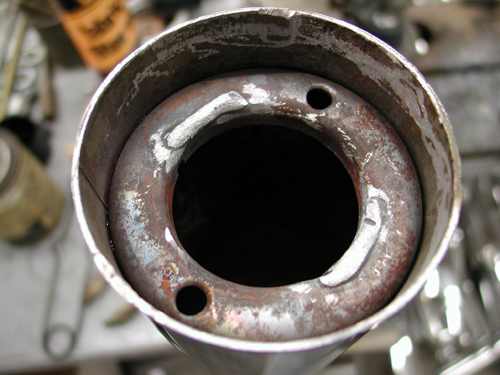
Then I spotted the fishtips in the pile and myconsideration changed. I dug further. Kenny Price from Samson allowedme to dig through his warranty bin when I was looking for stanchionsfor my Bikernet office railing. I remembered touring mufflers withfish tips, I kept digging.
Sure enough I had a set and in quick movesI sliced them into chunks. You know me, I'm a gambler. I cut themwith no methodology in mind past the size and looks, but I came uplucky. Samson designed a baffle system with a cone at the front toguide exhaust pulses into the baffle and it seems to be working fortouring applications. I cut off that portion and discarded themajority of the baffle. But there was still 2 inches of baffle and astandard donut in the rear of the muffler. That's where fate movedit's evil hand over Richard Kimball again. Or in other words I rolledthe dice.
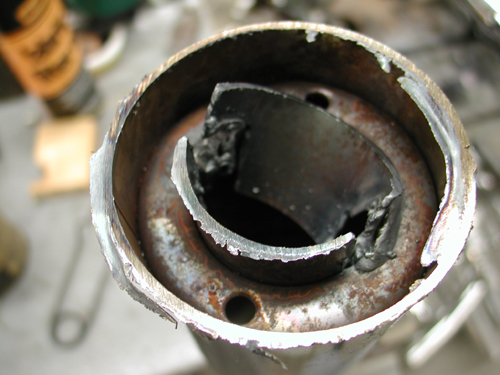
I spoke to Kendall Johnson recently and he told me aboutperformance stepped exhaust systems and reversion cones used to tunesystems at the rear of the pipe. I couldn't make this donut move upand back, but I had the makings of a reversion cone at the stern.With a torch I cut out the remaining baffle, then after speaking withthe HOT BIKE staff member, Craig Murrow, for a reversion cone descriptionI knockout out the remaining baffle, then with various cutting andgrinding cones I formed and smooth departure for the exhaust pulses.Then I had to remove the old touring mounts with a die-grinder andthey were ready to weld.
The rear pipe was comparatively easy since the pipe wasalready made except for the muffler and brackets. Shovelheads arenotorious for louse exhaust manifold connections and tearing out thesingle stud, so I wanted to mount them in the front and rear for asolid, secure connection. The only port for the connection at thefront was the oil bag. That was a bad choice and I'll run a bracket off the seat post before all is said and etched in stone.
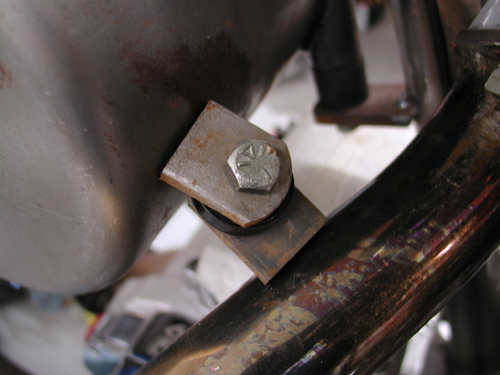
I had to make sure the pipe could be removed with the tabs onthe bottom, then I spaced the tabs apart with a heat sink material. Imay use Teflon, then the notion that the oil bag is rubbermountedfloated to the surface. What bearing would that have on thiscoupling? Hell the frame will vibrate like a mad dog. I'm stillquestioning that link, but we'll see, maybe a spring between the tabs? The final decision was the seat post bracket to come.
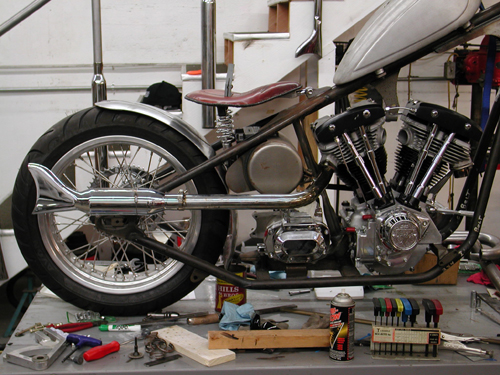
There was one other pipe design consideration–the length.I try to keep the pipes somewhat equal and between 32 and 38 inches.Buster's Sportster runs sharp and crisp with his hand-made 38-inchesfrom the Bikernet Headquarters, as seen in Street Chopper. So Idesigned this pipe to be 38-inches and not protrude past the tire. Mygoal was to make the front pipe curve out the other side and be ofequal length.
At the end of Friday night, one pipe was complete, toolswere scattered all over the shop and I had a couple of Hooker Headerchunks of 1 3/4 pipes segments cut and was fooling with the frontheader. The front was tricky as hell. I wanted to scoop out the leftside of the bike, which added length. I also had a bitchin Rohm Engineering oil filter/cooler system that mounts to the front motormounts and aims the filter at the ground for ease of removal anddraining. The pipe had to clear it significantly. This puppy was alifesaver. I planned to run an oil cooler (Shovelheads run hot) andfilter, for a lasting driveline and more oil capacity. My originalplan called for old school mounting on either side of the oil bag.This eliminated all of that and the plumbing for two elements, the cooler and the filter, wasreduced to one hot looking job in front of the engine for maximum cooling.
I spentall day long on Saturday, dodging the phone and working in thegarage. I had all the tools and materials I needed, even two new setsof welding glasses, which came in damn handy. The trick was to lineup the pipes, make all the right decisions, hope for the best andtack 'em. I did and with a level I constantly compared the pipe tothe top of the lift. The spacing worked out fine.
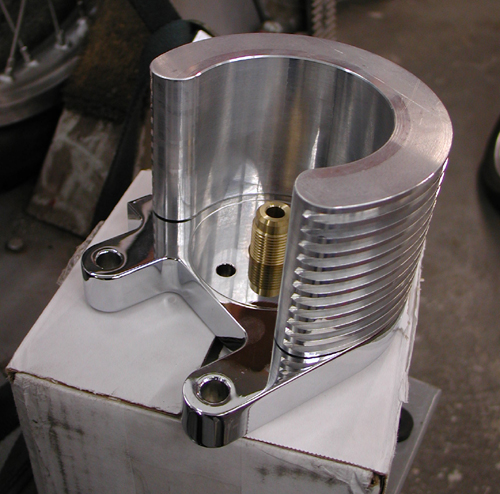
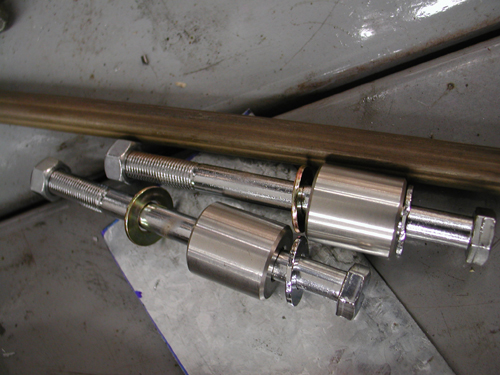
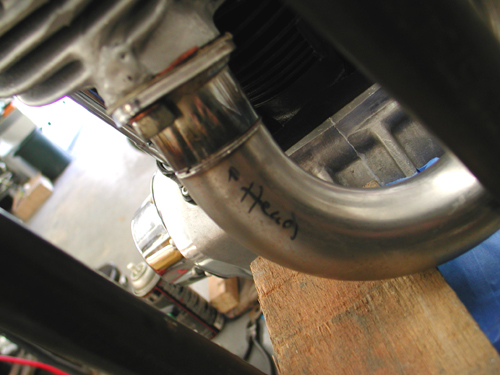
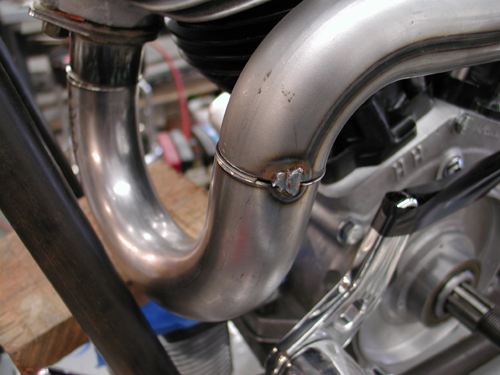
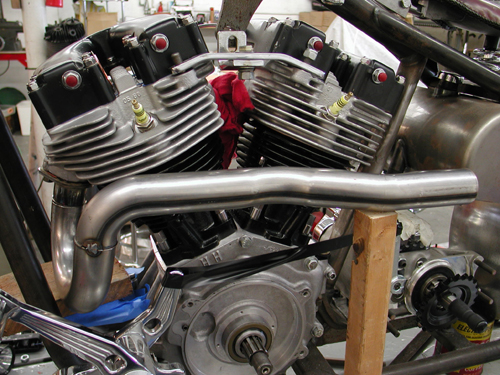
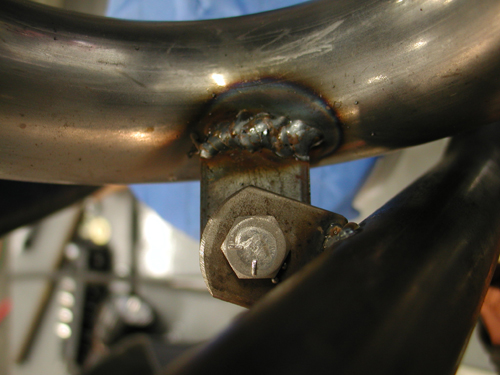
I cleared the top of the Rohm bitchin' oil cooler/filter mounthopefully by enough to allow the pipe slip down and out of the head (I was recommended to use a CCI Filter part number 270126).I tacked the tab with a spacer between the two for some jiggle room.And I made damn sure that the pipe tab was below the frame tab. Atthe back, the muffler was fabricated the same as the other one with aslight exception.
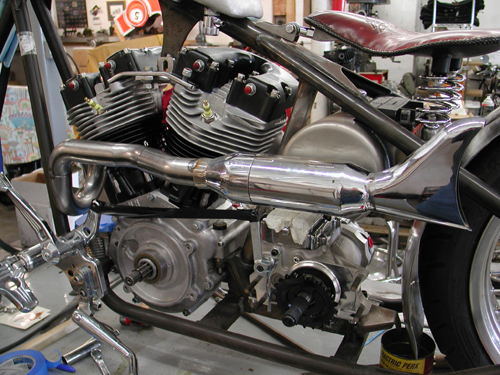
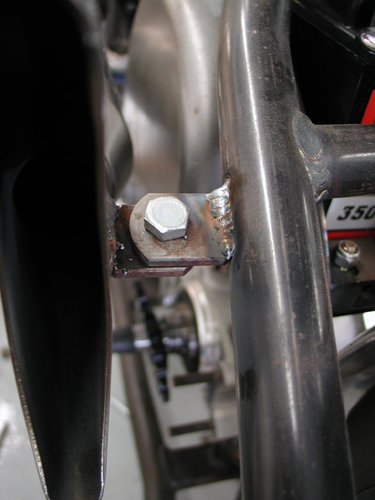
I shaped the reversion cone the same, cut off thetouring mounts and ground the tabs. Then I used a couple of V-blocksto hold it perfectly in line for tacking the halves together. Then Isliced off the crush tabs on the front of the Samson tapered muffler.They were wider and different than the other side, so I cut them off.You'll notice the difference, if you check both side.
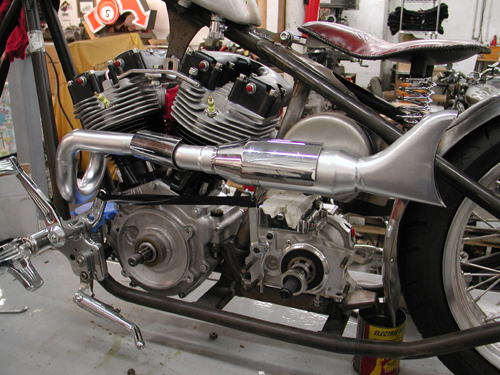
The front parts of the pipe were Hooter elements and theyare smooth mandrel bent segments. I used another one for joggedstraight piece between the muffler and the head. I took the 13/4-inch exhaust to my Muffler Master bender and bent it slightly oneway, then reversed the sucka and bent it the other way. It fit like adream and looped out enough to pass the oil bag. I used Hooker headeralignment sleeves to hold the front pieces in perfect alignment. Donedeal, I tacked them, constantly comparing the level with the lift,the pipes then the muffler. After the tacking was secure, another tabwelded to the frame, avoiding the oil bag (a Lucky Devil concern,since the oil bag is rubbermounted), then all elements wererechecked, I removed both pipes and MIG welded them as complete aspossible.

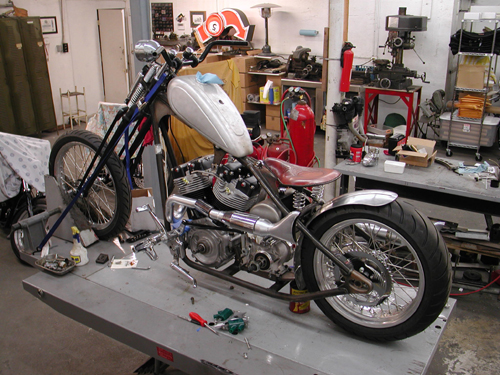
I find that MIG welding is a pain and blows holes in pipes easily.I also discovered that after I MIG weld a pipe I can flow the weldeasily with a torch and smooth out all the welds, fix holes and fillgaps. I actually found a piece of old steel rod, not much bigger thana piece of wire. I usually use old coat hanger, but it pops andwheezes from the paint coating.

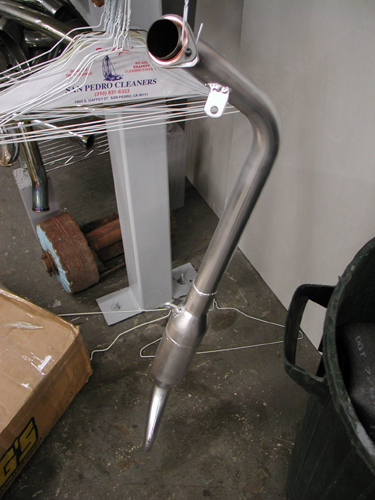

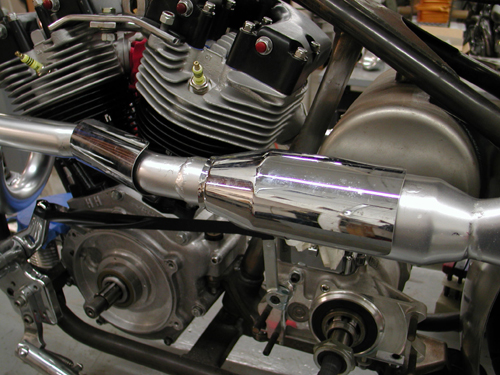
After the pipes were welded, flowedand checked twice, I ground all the surfaces with an emery disc andpainted them with whatever barbecue heat paint I had laying around.The lovely Layla is currently on her way back from Home Depot withsome flat black heat paint. We'll see how that works.
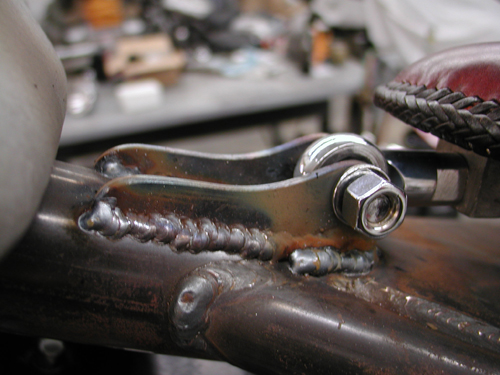
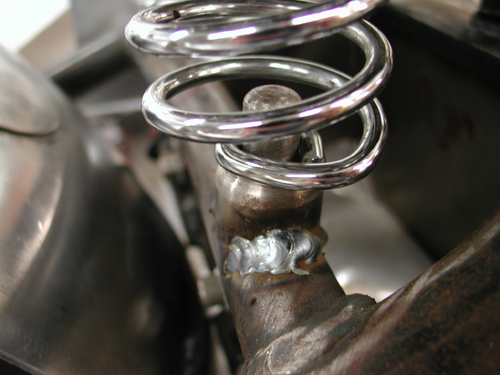
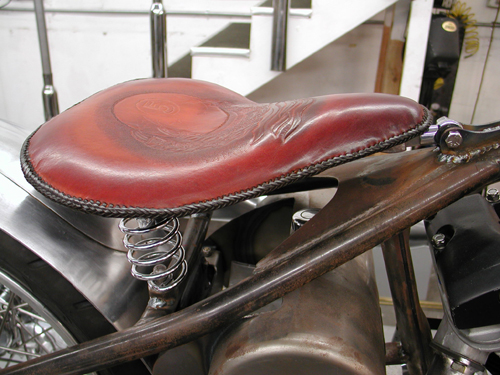
Kent from Devil hand fabricated the seat pan, brackets andbungs. I set them up and welded the parts in place. Then it was timeto roll the bike off the lift and see how she fit and where I mightneed heat shields. I discovered a couple of things. Yes, the scootwould require left side heat shields and nothing on the right. I alsotested my notion to sculpt claws out of brass, unsuccessfully.
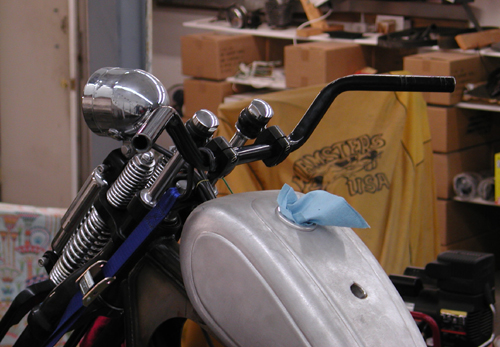
I also found that the existing bars wouldn't cut it. Igrabbed the old '48 Panhead TT-bars, narrowed them by 4 inches, and Isorta like them.
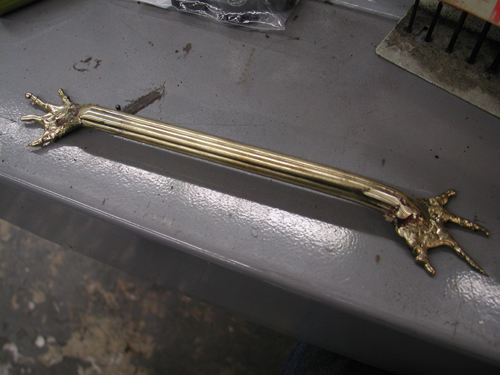
Okay, so I grappled with the sculpting business fora couple of hours and discovered that I can't control the brass likeI can steel. I spoke to Kent from Lucky Devil and he recommended thatI try TIG Silicon Bronze rod. I'll try that next week. In themeantime, my first brass sculpting attempt ended up on the shop door.Let's get the hell out of here.
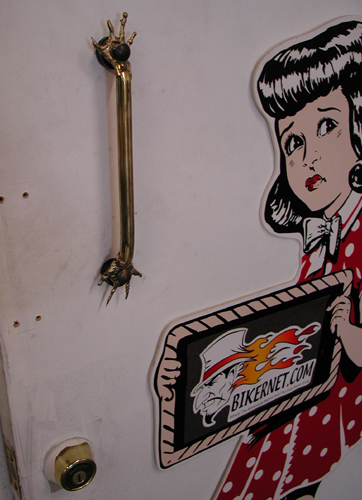
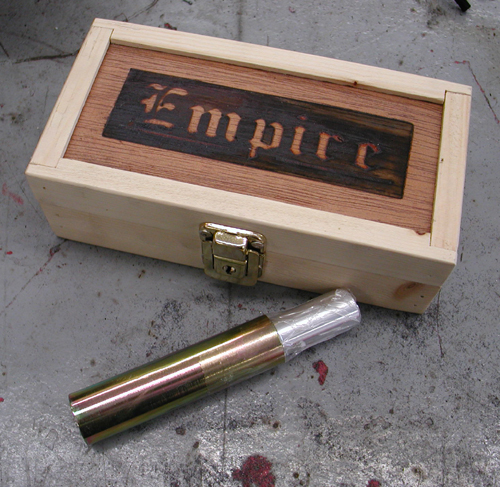
Ride forever,
–Bandit
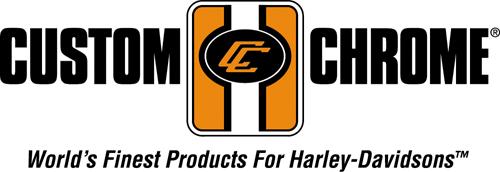
1928 Shovelhead Project Part 1
By Robin Technologies |

In an effort to stay tuned with the rapidly growing and ever changing industry the staff of Bikernet began a project Shovelhead several years ago in conjunction with Randy Simpson of Milwaukee Iron and Arlen Ness. It’s been a strange road, but we’re now rolling closer to completion with the assistance of Rick Fairless of Dallas Easyriders and his ace fabricator Jim.

The project began with the purchase of a slightly destroyed Mexican Police bike from Arlen a couple of years ago. He had scored some 300 1984 Mexican cop bikes that had been ridden through several revolutions and costly rebellions. The bikes were shot at, dragged, bombed and ridden harder than any V-twins on the planet. When we first purchased the Shovel complete with police sirens and blinkers, we assumed foolishly that we would restore it to it’s original fighting condition. Arlen even hand picked our unit specifically with our goal in mind.
Well it’s one thing to dream of a restoration, but when the cast iron triple trees are broken, the frame is bent, all the sheet metal destroyed we took a step back and said, Help! We pulled the Engine and sent it to JIMS Machine for a rebuild along with the Transmission. With the cases replaced along with the barrels and heads and all the internals replaced, the engine was ready to rock once more. A similar concoction was mixed for the transmission and a couple of us dressed all in black and prepared to bury the chassis in a shallow grave in the desert outside of 29 Palms, California when the Editor of “Biker” pointed out that we had a valid pink slip. Dean, salivating, over the dying chassis took the entire unit and paid us handsomely for the paperwork. We suspect that he made a rocking chair out of the frame and wheels. During one of our weekly Bikernet meetings we discussed what to do with the Shovelhead drive train, and in the process we started discussing various options and some of the customs we respected the most. Several suggestions were thrust onto the rusting boardroom table. First Randy Simpson had volunteered to help us build an old time looking bike from the remnants of the ’84. We voted unanimously to pursue this avenue, since we had always been impressed with the workmanship and design Randy injected into his own 1928 Shovelhead projects, and he had a desire to create a simple chassis kit to build one of these puppies to market to the public. We agreed to help him promote the concept. We also all agreed that a gesture to the community of San Pedro was a necessity since several members of the staff had been arrested and the headquarters were constantly under surveillance, so we decided that Bikernet needed its own private San Pedro Police bike. How else could we crash the local parades. Randy is a persnickety builder who takes great pains to build quality parts for the market. Two years passed and he still didn’t have the frame built. He was obviously so successful with his growing line of fenders that his chassis concept was slipping onto the back burner. Arlen Ness was also taking giant strides to build a similar machine and if you picked up a recent Easyriders you would have seen the fruits of his labor in his 50/50 Shovelhead. In addition Chrome Specialties with the assistance of Chico in Southern California had recently completed a similar project around a Sportster (It’s called Trick and is featured on Bikernet right now). The competition was stiffening. Randy dropped out, and we moved ahead, and with some research we discovered that a number of reproduction parts are being built in Europe for early Harleys. Early like in 1915.
Devoted to successfully completing this project we picked up a rigid frame from Paughco. This is a standard scale Paughco Rigid for Shovelheads. From there our old part contact was Fred Lange in Santa Maria California. Fred informed us that a European group is remanufacturing 1915 springer front ends, flat track tanks, headlights, fenders and Fred was making appropriate sprung seats for these models. We were in business. We ordered the flat track tanks, the fender for a side car so it could be used for the front and the rear, a hand leathered seat and snuck out of the hills over looking Santa Barbara.
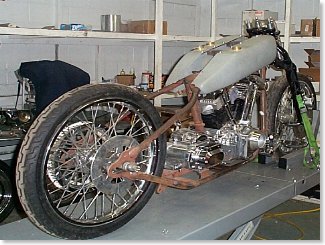
We had a Bad Boy front end, Wheels, etc. We’re in the market for some Custom Cycle Engineering lowering rockers. At that point we needed miscellaneous parts, pipes, etc., and we could get this puppy on the road. It was time to call in a favor. Rick Fairless had purchased the exclusive Bandit I Pat Kennedy Built bike from Bandit and part of the deal was parts and labor on a bike project in the future. It was time to call in that note. Then in a stroke of bad luck and good, Marty Ruthman decided to close his shop abruptly due to health problems and he had a massive sale.
–Wrench
5-Ball Factory Racer Closing in on New Cam and Ignition
By Robin Technologies |
We were fortunate to hook up with Heather New, of New-Line Engraving several years ago. Since I was about to switch out my CrazyHorse engine ignition with a Blackhawk Motorworks cone cover I needed to come up with a classic point cover for the new unit and the 5-Ball Factory Racer. It was a natural choice to send her a chunk of aluminum, or I shoulda sent a piece of brass, but oh well. Either way I knew she would bring the project to life.
Heather started engraving in a small shop in downtown Edmonton in the Early 80’s, where she took care of over 100 jewelry stores. “I was engraving everything from I.D. bracelets to wine goblets to pocket watches, and more,” said the raving redhead, “items which other engravers said could not be done, I soon learned to do!!! This was when I first met Frank.”
Frank Gurney was (and still is) the best Hand-Engraver in Canada. “He is a true artist and craftsman, and along with the Alberta Apprenticeship Program, arranged for me to be his understudy,” Heather said. “I was thrilled!!! I learned so much from Frank in those years, confidence, trouble-shooting, and above all HUMOR!!!! We spent hours working and laughing (hoy-deedle-doy!!). He taught me so many things before he eventually retired out near Victoria, B.C.”
She then moved on to the largest Jewelry stores in Canada. “I was doing all of their machine engraving, as well as custom wedding bands, and one-of-a-kind jewelry pieces,” Heather said. “They treated me like gold, and I will always be thankful for the kindness I experienced there. I relocated near Calgary, Alberta, and began working for a gigantic company with more talent than I had ever seen gathered in one place. I naturally did the engraving there, and also moved on to operating CNC machines, and hand-carving moulds used in casting.” She became a programmer, writing the programs, which would later be used by the CNC machines to cut the actual moulds.
She started New-Line Engraving in the summer of 2005. “I hand-carved an inspection cover for my good buddy ‘Chicken’ and with her over-whelming encouragement, (she cried when she saw it) I decided to branch out into custom bike carving too (after all, a derby cover is just like a signet ring, only BIGGER.”
So here’s how the short, two-week process rolled:
Cover the piece in white water-soluble paint, and transfer the artwork onto the surface
I highlight the general outline, scratching the paint leaves a more permanent mark than pencil, and you don’t rub it off as you work!
For removing large areas you can try a dermal, but they tend to vibrate too much for any fine work…I used small gravers hooked into a pin-vice to cut in between the letters,
as this cover was done mostly under a microscope.
I also use fine sandpaper, jeweler’s files, and burnishers to “round-off” curves (as seen on her legs), and give some dimension to whatever artwork you are dealing with…
Details like hair, the features in the face, and fine shading are all done with fine gravers and files.
I then add an aluminum-oxidizing agent, which blackens the entire piece. When it is re-polished, the highest surfaces will become shiny again, while the black remains in all the nooks and crannies of the background. (I only do this by hand—a buffing machine can remove hours of work in a heartbeat!!)
“If anyone out there in Cyberspace wants to give it a whirl, I am always here with support and tips,” said Heather
Sources:
NewLine Engraving: http://www.new-lineengraving.com/
Blackhawk Motorworks:
http://www.blackhawkmotorworks.com/
Compu-Fire Ignitions: http://www.compufire.com/
Custom Chrome:
S&S:
Mudflap Girl Part 2, the Bandit Engine and Spitfire update
By Robin Technologies |
Okay, you have the story behind this build, and Chris Kallas is refining the concept drawing. My engine arrived from the factory, and Eric Bennett immediately noticed the return address, in Viola, Wisconsin.
As it turns out, the factory hired the S&S crew to assemble their Evo line of engines. What a natural. I liked that notion all the way around the block. First, it means more American hands in my new engine. Plus, what could be better than to have the best performance engine company on the planet working with the factory on the last and most refined V-twin configuration?
For this crew, and lots of riders all over the world, the FXR Evo is the best of the best. So, for Bikernet, this became the year of the FXR and the Evo engine. I asked the factory about their Evo engine program and received the following information.
A Modicum of Harley Engine History
The first 74 cubic-inch V-Twin engine on the JD and FD models was introduced in 1921 and the 45 cubic-inch side-valve V-twin engine (later to be known as the Flathead) on the D model debuted in 1929. The Flathead engine proved so reliable that variations of it were available on Harley-Davidson motorcycles as late as 1973 (servi-car trikes).
In 1936, Harley-Davidson introduced the EL model with an overhead valve, 61-cubic-inch engine. With increased horsepower and bold styling changes, the motorcycle earned the Knucklehead nickname, due to the shape of its rocker boxes.
New features were added to the 61 and 74 overhead valve engines in 1948, including aluminum heads and hydraulic valve lifters. New one-piece, chrome-plated rocker box covers shaped like cake pans earned this engine the nickname Panhead. The engine introduced on the Electra Glide models in 1966 to replace the Panhead became known as the Shovelhead, again due to the shape of its rocker covers.
1340CC Evolution Softail Engine – Silver and Polished SPECS
Type: 4-cycle, 45 degree V-twin
Bore X Stroke: 3.498 X 4.250
Displacement: 80 cubic inches or 1340 cc
Compression: 8.5:1
Torque ratings at 3,500 rpms: Touring with fuel injection, 83 ft./lb.
Touring w/carb 77 ft./lb. @ 4000 rpm
Dyna/Softail 79/76 ft./lb.
Miles per gallon: 50 hwy/ 43 city with a touring model using a carb
55 hwy/ 43 city Dyna or Softail
Variety and sales info:
1340CC Evolution Softail Engine – Silver and Polished
Since the first single-cylinder built in 1903, engines have been the heart and soul of Harley-Davidson history. Each motor has made its unique contribution, and the V2 Evolution engine is no exception. With the Smart Start Engine Program, buying a new Evolution engine has never been easier. When replacing your Evolution motor, Smart Start offers brand-new, factory-tested engines at an unbeatable price. Choose the standard silver and polished Evolution, sinister black, the classic black and chrome or the silver and chrome finish. Either way, you won’t just be making a new start; you’ll be making a smart start.
16161-99
IN-STORE PURCHASE ONLY, Contact dealer for pricing and availability.
Fits all ’99 Softail models. Does not include carburetor, manifold or timer cover.
MSRP US $3,295.00
1340CC Evolution Softail Engine – Black and Chrome
16160-99
IN-STORE PURCHASE ONLY, Contact dealer for pricing and availability.
Fits all ’99 Softail models. Does not include carburetor, manifold or timer cover.
MSRP US $3,995.00
1340CC Evolution Softail Engine – Silver and Chrome
16177-99
IN-STORE PURCHASE ONLY, Contact dealer for pricing and availability.
Fits all ’99 Softail models. Does not include carburetor, manifold or timer cover.
MSRP US $3,495.00
When my engine arrived, I immediately hauled it in the Bikernet Hearse to Bennett’s Performance for a slight performance upgrade. I needed to let that puppy breath without messing with the reliability aspect. Sharing the same building on the edge of Signal Hill, California is the headquarters for Branch O’Keefe. John O’Keefe worked for Jerry Branch for decades and ultimately bought the business when Jerry Branch decided to retire.
We’re looking at several options for stock engines and for rebuilds. We have three touring models coming together right now, and they are all 80-inchers. One for my son, my factory motor, and Dr. Hamsters 200,000-mile Evo rebuild by Bennett’s.
I’m running the brand-new factory plain Evo engine with the Andrews EV-27 cam and Andrews chrome-moly adjustable pushrods for less flex, a new cam bearing and the Branch flowed stock heads, for 8.9:1 compression, 78 cc Branch-flowed chambers, and 75-80 horses at 2,600 rpms.
The next higher upgrade step from Branch is the EV-51 cam and additional headwork and shaved heads for a 10:1 compression and 85 horses at the same rpms. And finally, a customer can run with an EV-59 Andrews cam and 10.5:1 compression and 90-95 horses. Not bad for never taking the barrels off.
“I like rpms,” John O’Keefe said, “and the new ignitions allow these engines to burn more fuel and bring out the horses.”
The key to all this performance is the headwork set to match the cam, and John O’Keefe has studied this science for most of his life. The key is building a mid-range hot rod without sacrificing reliability.
The first move was to strip the engine and deliver my fresh factory heads to the Branch team. Eric Bennett set my beautiful, plain H-D Evo engine on his clean room bench and removed the top motormount, the top rocker box that came off with the middle ring. We noticed much improved, one-piece factory Teflon gaskets. We won’t mess with them. Then Eric removed the rockers, the pushrods, pushrod tubes and rocker boxes. We also retrieved the new base gaskets to reuse.
Then he removed the head bolts, the front head, and the rear head. I had already purchased the Andrews EV-27 cam from Branch O’Keefe, and Eric and I started to prepare for installation. He removed the point cover, ignition, and cam sensor.
He had a terrific Trock tool for removing the cone cover. It’s always a bastard to try to carve around the narrow gasket surface with a screwdriver or a knife, hoping to find opening and risk damage to the cases or create a leak by scratching the gasket surface.
“We always replace the new factory cam bearing,” Eric said, “with a full compliment Torrington bearing. The factory ran the good ones from ’55 to ’92, then they shifted to a cheapo brand. It’s also not a bad idea to replace the factory plastic breather gear with a solid JIMS unit.”
I scrambled to take notes and photographs while Eric peeled into my engine. He popped a factory set of magnetic tools into the lifter stools to hold the lifters up during cam removal. I wish I had a set of those puppies.
“It’s interesting,” Eric said. “Virtually every stock cam is .060 longer than any aftermarket cam.”
Eric pre-measures the cams and adjusts the thrust washers before replacing the cam, which you will see in the next report, when we study the Branch recipe for performance, the headwork, and modifications. He replaces the valve seats for larger valves, then ports and polished the chambers. You won’t believe the long-lasting components Branch uses.
Then we will watch Eric replace the stock cam with the Andrews unit and adjustable pushrods, and put the whole Evo puppy back together. “Don’t forget to order a top end gasket set,” Eric reminded me as the rain cut loose outside and I wondered if this winter season would ever end. I need a ride.
Then Eric grabbed a JIMS tool and a couple of wrenches and in 30 seconds pulled the cheap cam bearing from the new cases.
“I’ve seen these go south in 10,000 miles,” Eric said. “I’ll never understand why they replaced a perfectly good quality bearing with this junk.”
Just as quickly Eric took an aluminum guide and a mallet and tapped the new bearing in place, another 10 seconds passed, and we were finished.
A couple of days passed and I thought, just maybe my frames and front ends would be completed at Spitfire. On a hunch, I peeled 57 miles away from the coast in the hearse while listening to KJazz on the radio.
It was quiet as I wandered into the vast machine shop, welding shop, bike assembly area and ran into Joe Cavallo, Paul’s dad, who was hunting around the shop for Softail brake anchor brackets. He greeted me and said something about shop organization. The Spitfire and American Made business model has faced serious transformations over the last couple of years.
As I mentioned before, Paul was the partner and manufacturing arm of Hellbound Steel motorcycles. American Made manufactured fast moving products for a bunch of now defunct companies such as WCC. At one time, they were building hundreds of choppers each month, and thousands of products in a much larger facility. During the last year, they adjusted their business model and tightened their facility. They rewired their building, replumbed it with compressed air lines, and kept building products.
It’s tough to stop everything and regroup, scour through boxes of tools, base material, parts, and junk. With a skeleton crew they are still building any frame a customer needs, including big twins, rigid Sporty frames, British custom frames, and even frames for Yamaha 650s and Honda fours. They also build an entire line of forward controls, gas tanks, handlebars, girders, and glide front ends (bowling pin), pegs, oil tanks (a variety of styles), trees and taillights. Paul is the mad scientist of the group. As a kid, he manufactured exotic gun cases.
He’s the kind of guy who will catch a notion in a cup of Starbucks coffee, in the morning and by the evening, he has a new product. It’s not a one-off either. It’s fully designed and configured for multi-manufacturing.
Some of his crew have been working with Paul and his dad for decades, including Larry, who is their master motorcycle assembly guru. He knows it all. “Pull the alternator rotor off that engine before you run it,” Larry told me. “Check the wires for twists or tears.”
I made a note. Then we made our way into the frame jig area to see the FXR frame progress. The FXR fever caught on and there were at least five FXR frames in the making. The first was based on the pro-street configuration with additional gussets, the squished wishbone, for the single-loop notion and 36 degrees of rake for a 2-inch longer girder front end.
They discovered some issues with my request for a V-style frame in keeping with the stock FXR configuration. I also hoped for less rake and a shorter Frisco style girder front end style. Paul was working on my unit with a 30 or 33 degree rake, but he also started building a couple of drop seat FXR frames, including one for himself.
We are also going to try a slightly longer swingarm suggested to us by Dar, the boss of Brass Balls for his FXR configuration. He wanted to pull the rear tire out of the frame some, and I was willing to try it. They are hot after these frames, since Paul plans to ride one on the Diablo run that kicks off on May 5th in Temecula, California and rolls toward the border. Don’t know if we will make it.
The plan for now is to pick up the frames, swingarms, axles, and Spitfire girders, on Friday April 8th. Between now and then, hopefully we will wrap up the engine and bring that puppy home to the headquarters. We are trying to match up these Mudflap Girl FXRs wherever possible, but not always. We are going to run long and short dogbone risers from Custom Cycle Engineering, but we’ve ordered a new set of Raw 2-into-1 performance pipes from Bub for Frank’s FXR, and I’m running a D&D 2-into-1 system. I’m running a Frisco’d and stretched tank and he’s running something completely different. He’s running a Klockwerks rear fender and I’m running something bobbed. I’m getting seriously ahead of myself. See you in a couple of weeks with the next report.
–Bandit
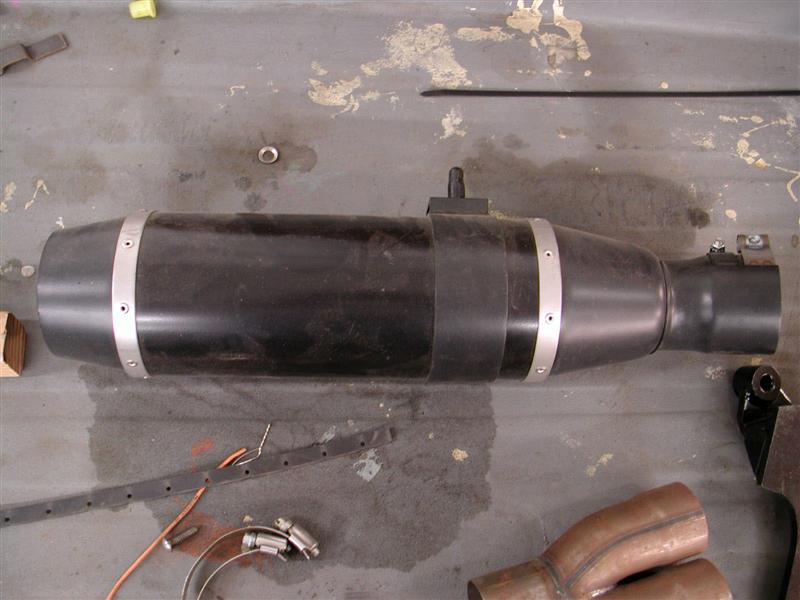
Sources:
Bennett’s Performance
Branch O’Keefe
JIMS
Spitfire
Custom Cycle Engineering
D&D
Harley-Davidson
Rivera Primo Inc.
Belt Drive Unlimited
Metal Sport Wheels
Sturgis Shovel Part 6
By Robin Technologies |
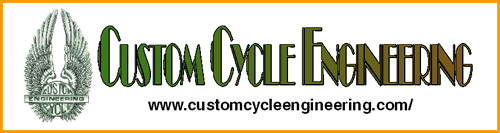
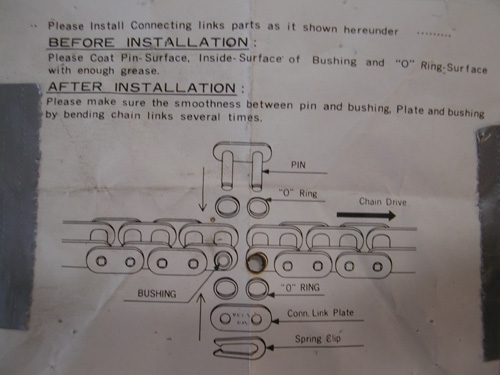
Here we go. I’m relunctantly behind the eight ball, or more likely the 5-Ball in this case. The bike is nearly complete and I haven't caught up with the articles. For the most part I was working at Primedia on the bike mags and didn’t have time to breath. No fucking lame excuses. Let’s hit it.
My original plan called for brass sculptures to hang this bastard together in a purely Bandit way. I messed with some odd heavy brass cloverleaf rod that was over a ½ inch in diameter. I wasn’t having my usual creative luck with bending or messing with this material. Kent from Lucky Devil Metal Works in Houston recommended that I use silicone Bronze rod and I’ve since messed with it. I shifted gears from Gargoyles and sculptures to pure mechanics. I started drilling holes is everything.
I discovered a piece of ½-inch wide strap that I thought was copper. Remember that the notion behind this mess is to use as much bare metal as possible. As it turned out the strap was brass so I gave it the Scotch Brite treatment and went to work. Before I made or positioned the rear Custom Chrome chain I needed to align the wheel, the transmission and the engine. I used my BDL inner primary and pulled the loose engine and tranny into position. Then I centered my chain axle adjuster and installed the chain using the CCI instructions (above). I have an old chain breaking tool, so I took out just enough links.
With the chain in place, aligned and adjusted the wheel using the Doherty wheel spacer kit (a life saver). I couldn't mess with the requisite chain guard until all was in the correct groove. Although the Paughco custom frame is designed for a belt, I choose the old school route and it worked out well. Lots of extra space to mess with.
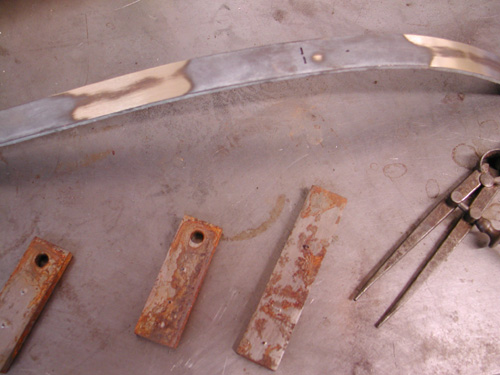
I dug through my drawers of tabs and crap that I’ve had around for 25 years. In the old days Mil Blair would call me from Jammer from time to time and tell me when it was time to shit-can scrap iron. I picked up tabs, spacers and brackets by the fist full and I’ve been moving them from place to place ever since. But damn, when you need a tab it’s bitchin to find just the right size in a drawer. Since I was going nuts with the drilling treatment, I matched the work on the frame with holes in the chain guard and counter sunk the edges for a more rounded look.
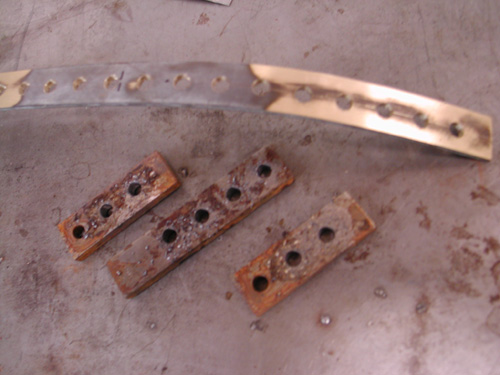
I also hit the top motor mount with a similar treatment. To give it a bit of consistency I measured from center to center on the holes and made all the holes the same diameter, 1/4-inch.

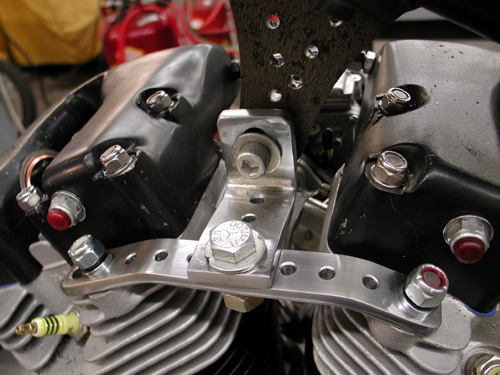
The hole deal became an obsession. I started drilling ¼-inch holes in everything including the Joker machine foot controls. I also went after Russell Mitchell’s Scotch Brite code. I swallowed hard and rubbed a piece of chrome with the coarse material and discovered that chrome reflects everything until it’s brushed with the wiry fabric. It gave it a raw material appearance and I decided that it was cool but a pain in the ass to do.
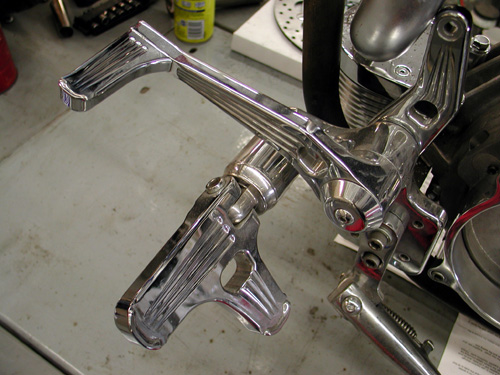
Again, I drilled the holes the same space apart, ¾ of an inch. It’s not always that easy, though. Sometimes the formula just doesn’t work. I use a pair of calipers to hold and mark the distance from hole center to center. If a hole ends up being located too close to an edge of the material, I back off and try another formula. Make sure to plan before you start drilling.
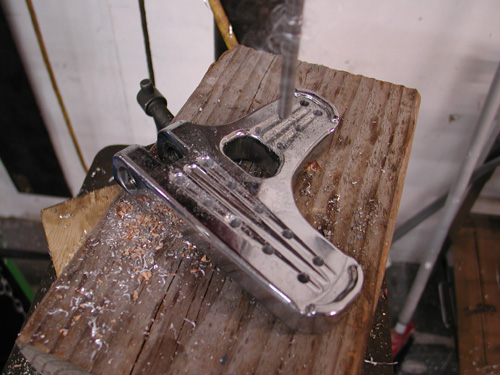
Here’s that damn brass stock. I was determined to have Brass, Copper, Stainless, Aluminum and a bare metal effect on the frame. You’ll see shortly how it worked out. I couldn’t bend that brass shit without destroying it, so I made the shift linkage out of it. I cut it off on a bench lathe and drilled and tapped the ends to 5/16 fine threads to fit the fine thread heim joints. Then I drilled the rod and countersunk the holes to remove the sharp edge.
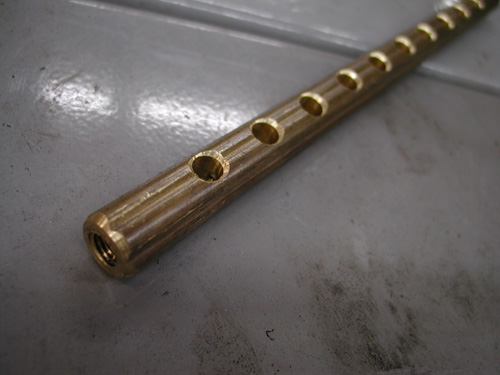
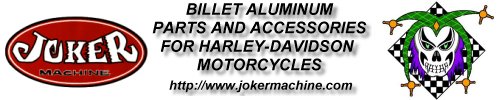
Here’s one of the Joker Machine control sets, rubbed with Scotch Brite and drilled. They make fine controls, some of the best. You can adjust these puppies anyway you choose to fit your riding position, inseam or foot angle.
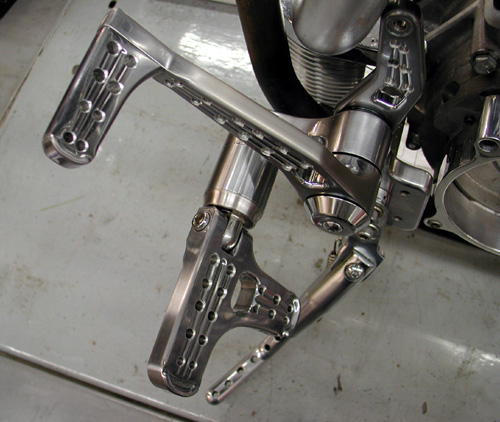
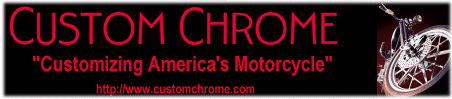
Before I leave this chapter I’ll touch on this new petcock from Spyke. It’s incredible, if it works well. It’s designed to give you every option for positioning and spigot direction. I ran into only one problem. No wrench lands to help tighten the bastard.
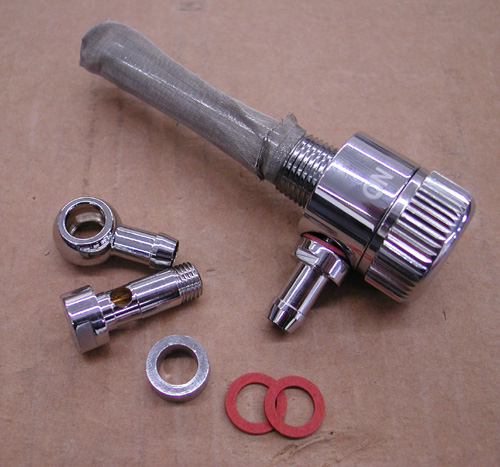
Check it out. You can run it faced in any direction and still read the switch locations and turn the knob without a lever smacking the frame and components. The spigot set allows builders to face the gas line in any direction.

I used the straight spigot and took off one of the fittings because my tank threads are female. The only problem I had was tightening it down, but I’ll get to that after the powder coating returns from Foremost Powder in Gardenia, California.
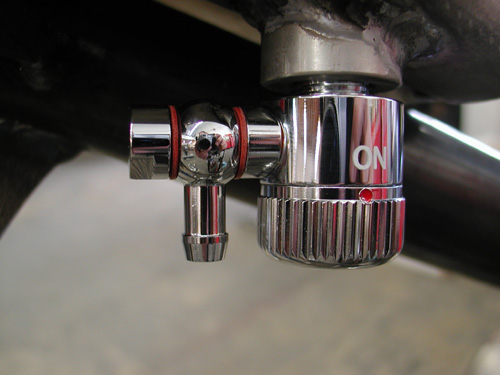
This puppy will revolutionize the industry for petcocks, if it works. I’ll let you know in a week or two.
Ride Forever,
–Bandit
5-Ball Factory Racer Build for 2009-2
By Robin Technologies |

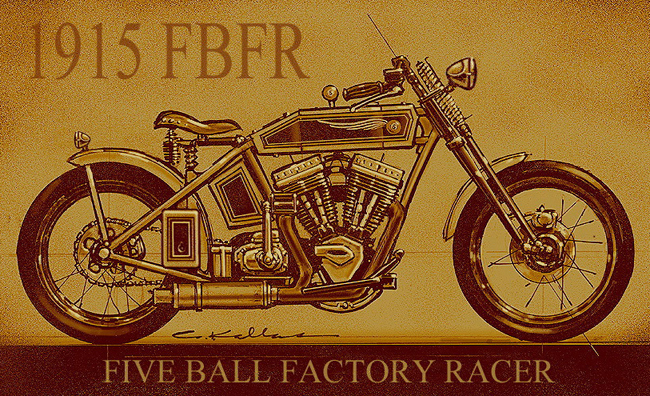
Moving right along, I overcame the Wilmington Mung and slipped back into the shop. It’s like self-induced Christmas for the homebuilder each week when UPS arrives or I score something at the bike swap meet. Ya plan, save small bags of gold and reach out to vendors to make deals, then wait.

I got all pumped when the bronze risers drifted in from DPPB in Europe, and I immediately tackled the mounting and handlebars. I hit two hardware stores looking for the proper length hardened studs and the second score was doubtful, but I rolled the dice and bought them anyway. As it turned out, 3-inch ½-inch studs with coarse threads on one end and fine on the other worked perfectly.
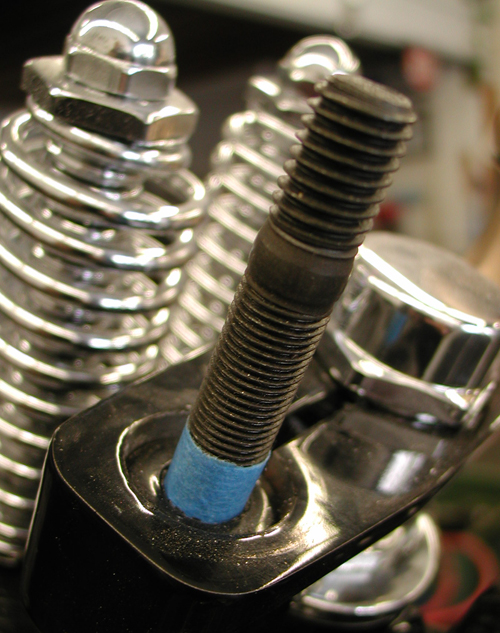
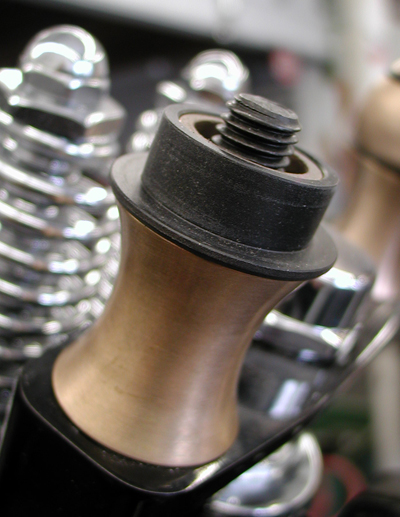
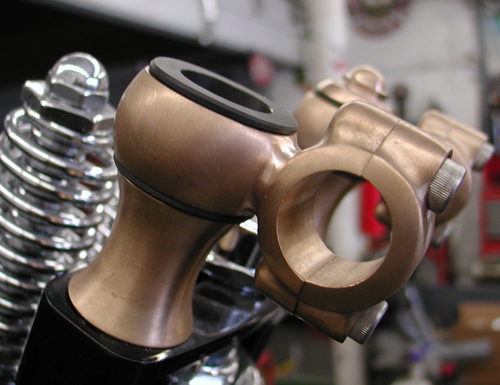
I tested the fitment by wrapping masking tape around the fine end 3/8-inch up from the bottom. I screwed them into the narrow Paughco leg, and then installed the riser components to see if I had enough length to reach the top bronze nut. I had plenty of threads, so I move the tape to 5/8 inches of securing fine threads and installed all the components. It all fit like a dream.
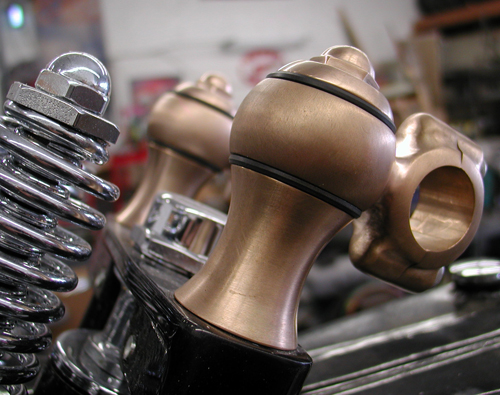
Then I went to work searching the shop for a set of bars that would give me the look and be reasonably comfortable. I’m shooting for that 5-Ball Factory Racer look, but a bike comfortable enough to ride to Sturgis. That’s always the acid test, and the road-test adventure. I found a set of sorta TT 1-inch bars sans the dimples, since I was going to turn them upside down. I mounted them to the risers, and then determined that I could cut almost three inches out of the center.
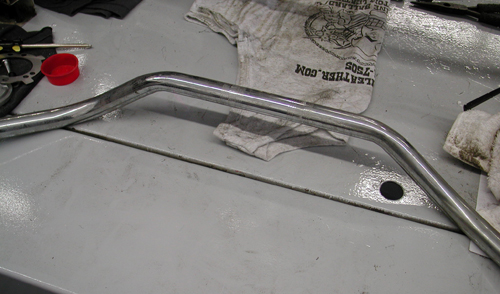
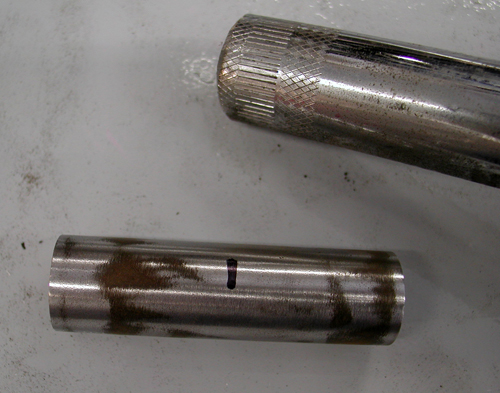
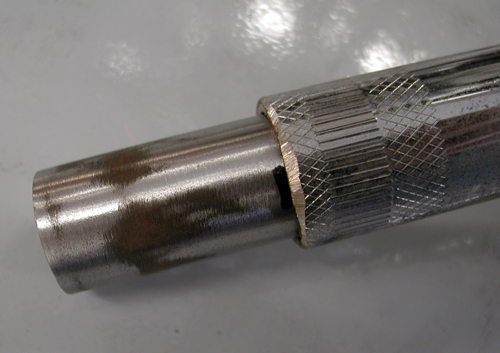
I searched the shop for a chunk of mild steel rod that would make the perfect alignment, strengthening slug for the bars. I removed the burrs from the split tubing and marked the slug center. I tapped it into place, strapped the bars down, so they were perfectly aligned, and MIG-welded them. Just having the bars and risers in place was a rush.
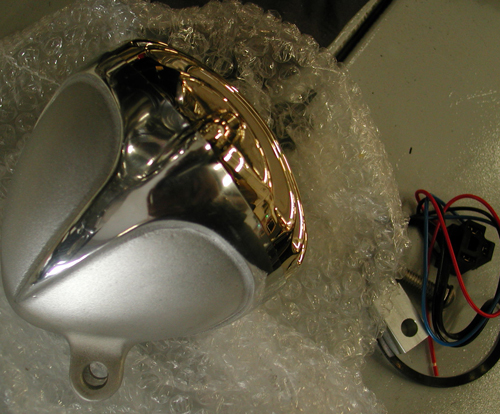
I finally muscled enough cash to have all my welding tanks filled. I took the opportunity to have one tank filled with pure Argon for welding stainless or aluminum. I’ve never welded aluminum, so I broke out my welding book and read the appropriate chapter. I needed twice the gas pressure and almost twice the rod speed and power.
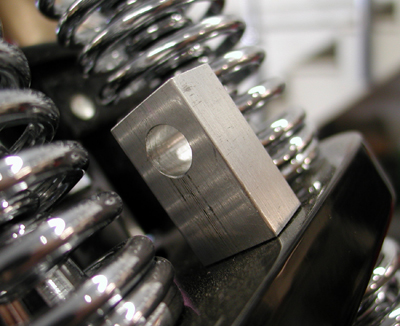

Let me back up for a second. The project was mounting the Crime Scene Rapide headlight. It was a bolt-on procedure, except for the simple aluminum-mounting bung. Once in place, it was impossible to remove the headlight-mounting fastener. I reviewed my options. The fastener would actually touch the top Paughco springs. I looked for an option and found one, but it required welding the existing square bung to the fine-threaded round spacer. I tapped the spacer for clean threads, and then proceeded to weld the two together.
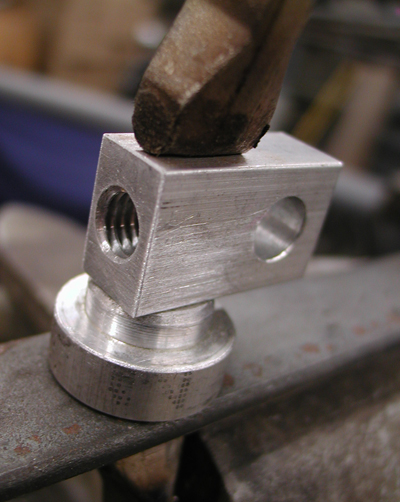


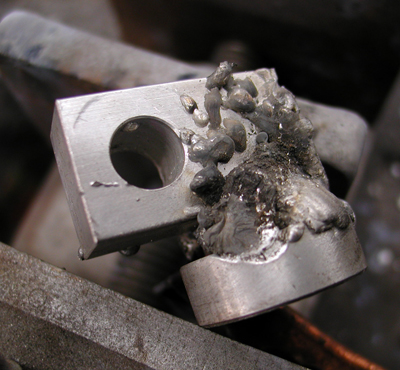
This was a trick. Aluminum must be extremely clean before welding. And since this piece was very small, it could heat up and melt like butter before one pass was completed. I also had some problems with the welder. Since aluminum heats and expands faster that steel, I needed to bore out the tip or run a larger welding tip. The tips come in various sizes, and natch, I didn’t have a slightly larger tip. So Jeremiah grabbed a micrometer and all my tiny drill bits, and started to study the sizes and attempted to drill the tips out. Interesting procedure. We broke bits and jammed them into the bronze MIG welding tips. Finally we succeeded in boring out a tip and the welding moved along.
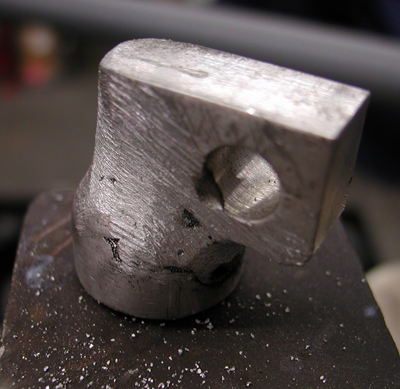
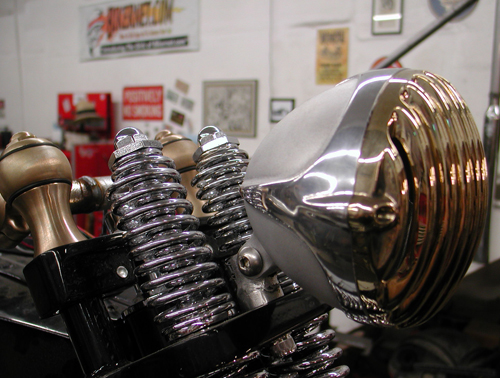
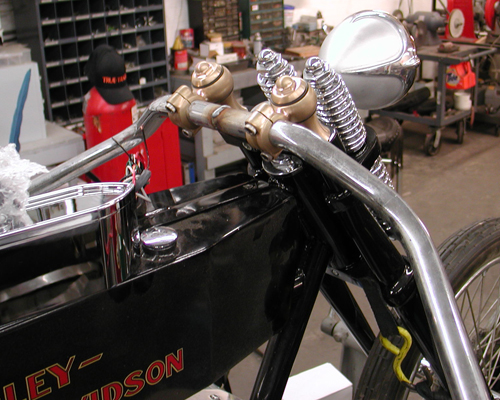
Then I took to grinding, filing, and rewelding until this headlight bracket was completed. Not bad. I need Jeremiah, the master shaper, to return and give it his final touch.
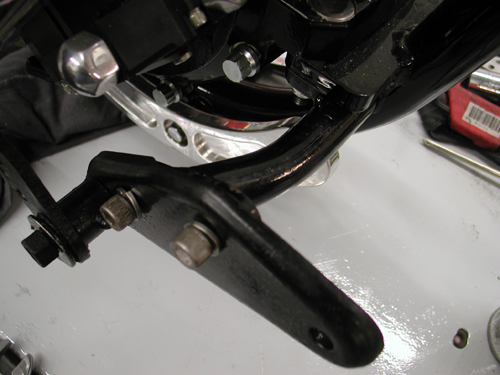
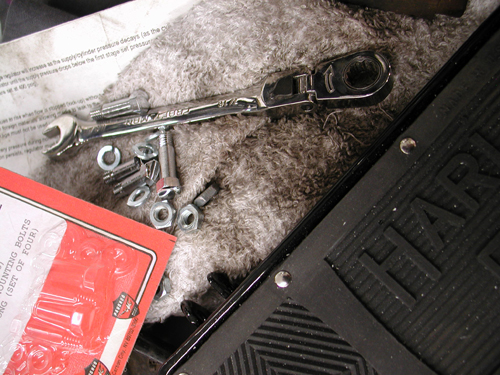
Next, I had a plan to use as many vintage H-D parts as possible. I snatched a stock 1936-1957 mechanical brake pedal and mounting plate, which also acted as the front peg or footboard mount. Paughco already made a bracket that bolts under the front motor mount. It makes the stock mounting bosses available for these components.
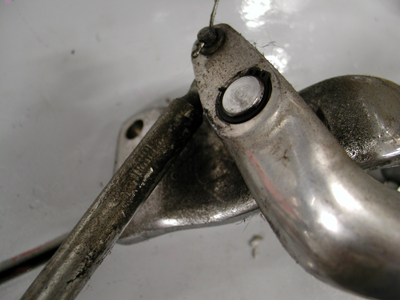
This effort placed me eyeball-to-eyeball with a couple of challenges. I needed to make the old mechanical brake pedal operate a hidden hydraulic master cylinder and somehow I had to create a mounting bracket for the rear of the footboard.
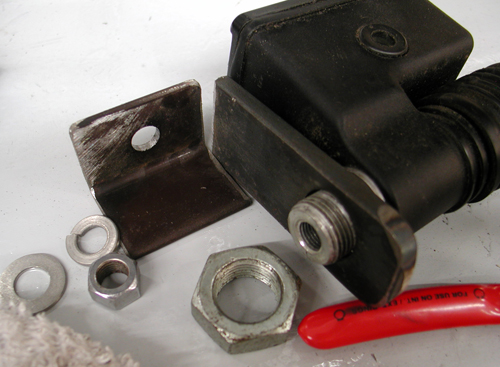
There was one more element rearing its ugly head at this point, but yet we turned it into an opportunity. There was no fifth stud mounting plate on the frame, so I started to tinker with a chunk of angle iron. Then I discovered a complete ’98 Dyna rear brake set-up with linkage and the master cylinder. Suddenly, lots of answers were available using the fifth stud-mounting placement.
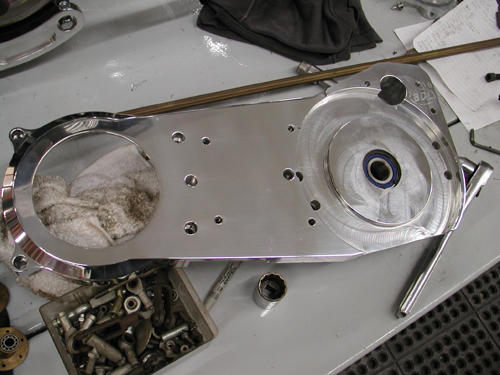
I had to stop dead in my tracks right there. I needed to make sure the transmission was aligned properly for the whole system to work. The brown Santa arrived with a new BDL Softail, 2-inch enclosed belt drive system I’d ordered just a couple of days ago. I pulled out the inner primary, loosened all the mounting bolts for the engine and trans and started my historic alignment procedure. First, I bolted down the rear of the engine and looked for any gaps at the front motor mount. It had a .020 gap. I found a shim and slipped it into place.
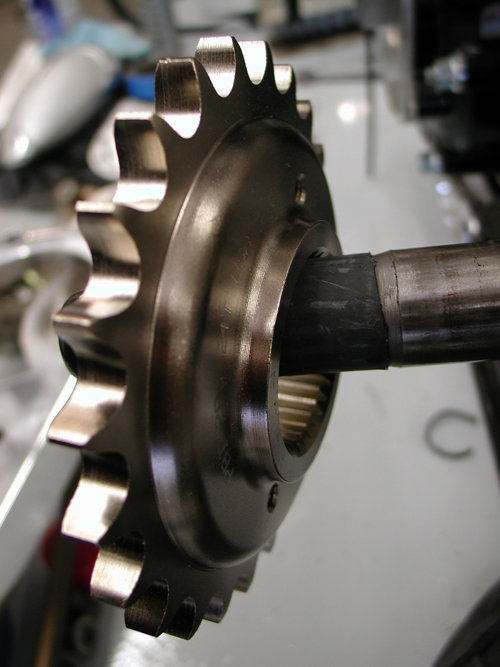
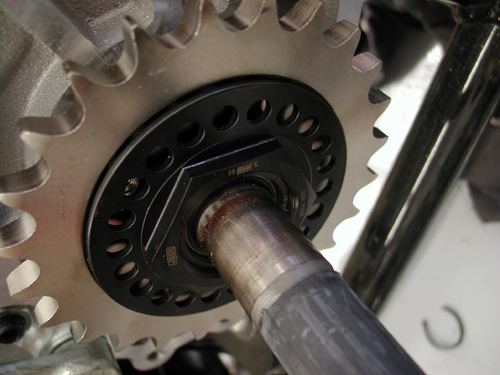
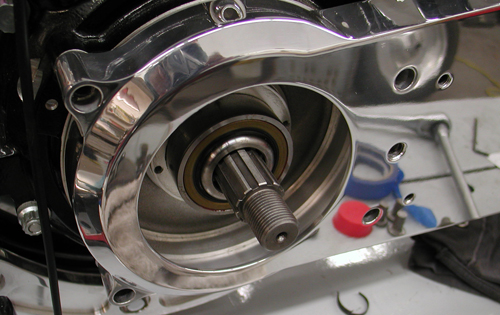
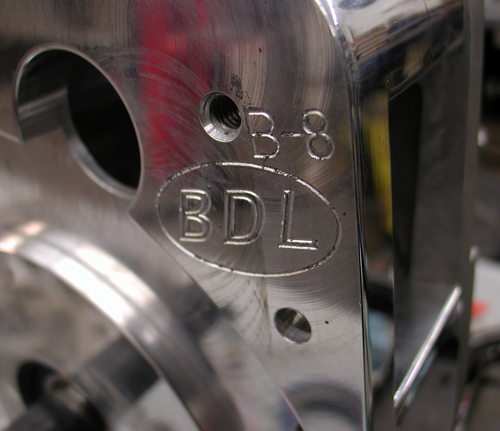
Next, I attached the BDL inner primary and pulled the JIMS tranny into alignment with the Crazy Horse V-Plus engine. Then I started on the fifth tranny stud-mounting bracket. I planned to run a kicker, and since this power plant is 100 inches strong, the additional mounting element will strengthen the entire driveline.
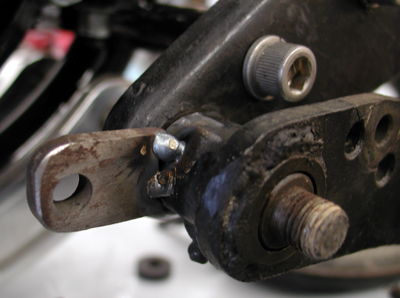
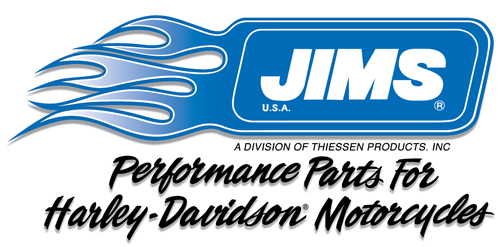


No, this system didn’t fall into place. I had oil lines to contend with and the brake pedal and master cylinder didn’t align. At first, I had a grand plan to bend the linkage rod into a jog-over to reach the tab I had welded onto the brake pedal pivot tube. That would have created more problems, specifically with the rear footboard mounting. I needed to straighten it out and machine a 2-inch offset link from the pedal over, which kept the entire system in alignment. The critical aspect will be my tab welding. There will be considerable strain on that puppy, but I think it will work.
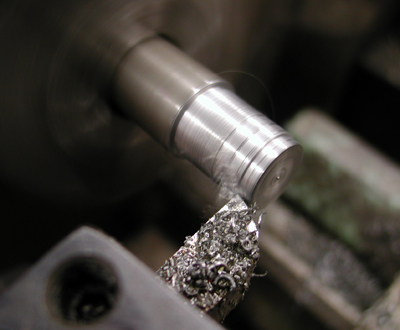
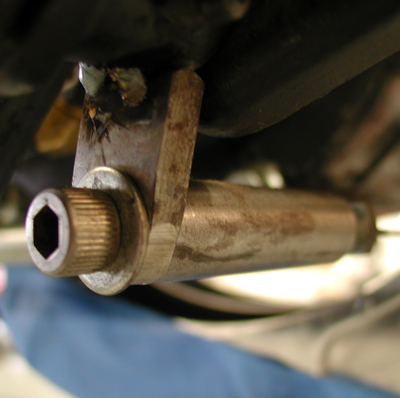
Then I ran a ½-inch rod off the top of the pedal bracket and machined a spacer that would catch an original classic footboard-mounting arm. I’m trying to tack-weld everything so I can make final adjustments or catch mistakes before it’s too late. I like welding and sometimes can’t stop myself. I tack my handiwork, step back, eyeball it, check it twice and weld the shit outta it. The next morning I discover something I forgot and I’m fucked.
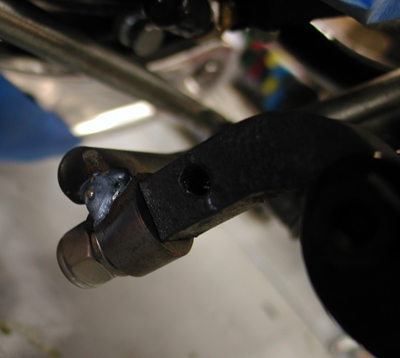
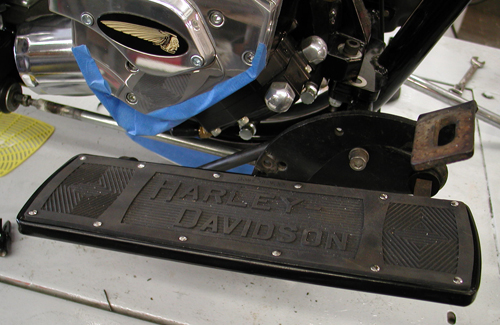
Since I was into footboards, I moved onto the left one. With the help of Sin Wu on her knees, we checked the angle of my 2003 Road King footboards and attempted to match that angle on the 5-Ball Factory Racer. Again, I used a stock mounting plate with foot clutch pedals. I’m going to make the racer a tank shift, so I bolted up the mounting plate and a vintage kicker arm and bracket, but I needed to drill and tap the Paughco bracket for the lower left 5/16 kickstand mount.
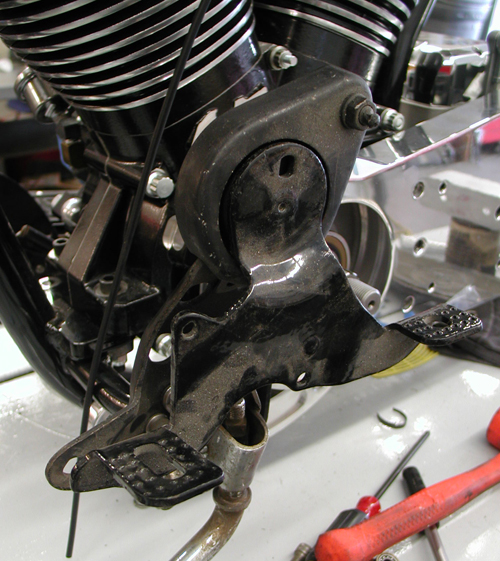
I tried to handle a few moves at once and failed. I broke off the tape in the kickstand mounting hole and I’m still pondering my options. I shifted back to floorboard mounting. I was burnin’ daylight trying to remove the tap. I mounted the front of the footboard and snugged it down at the Sin Wu estimated floorboard angle, then pondered how to mount the rear to the BDL outer primary.
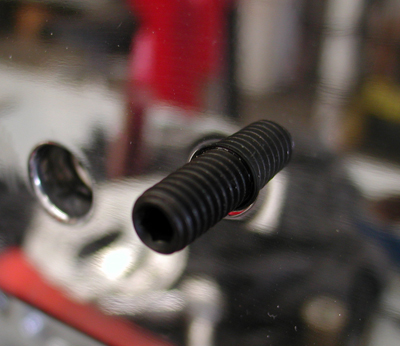
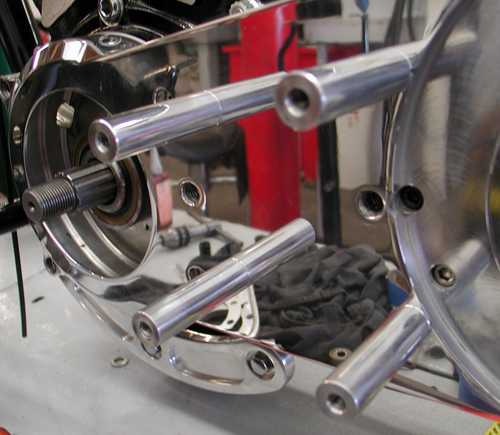
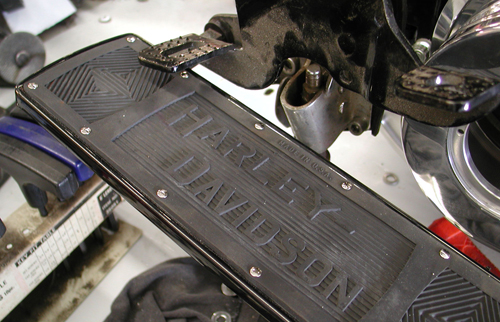
I had to insert the BDL mounting studs into the inner primary with red Loctite first, then the aluminum stud arms, and finally the cool, clean outer primary cover. This turned out to be a breeze. I took a vintage footboard mount, cut it off, and welded it to a Bandit-made bracket. It had to carry my weight, so I added a strengthening gusset to the bottom and believed I was good to go.
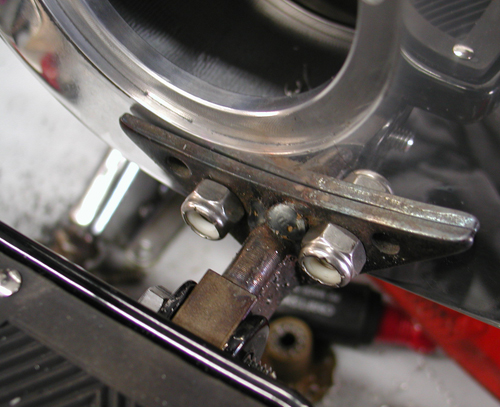
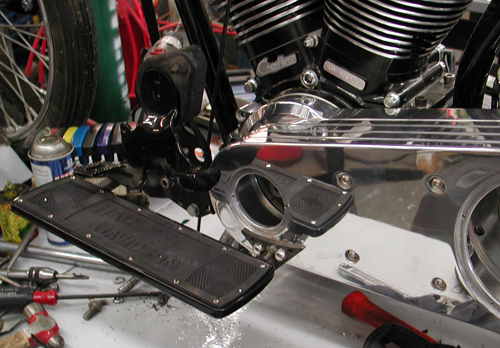
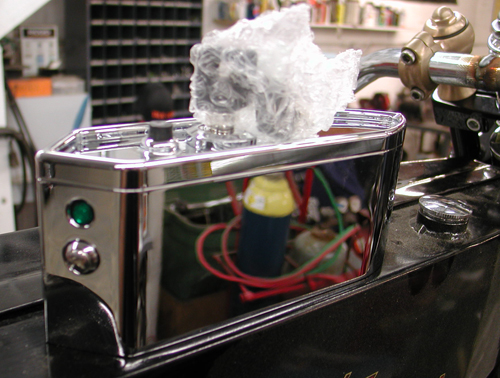
In the next segment, we will start to tackle the shift linkage system. Duane Ballard’s wife, Lisa, a contributor for the Cycle Source magazine, delivered this vintage tractor seat assembly for us to test and you’ll see our wacky test next issue. We might also start to tackle mounting the Paughco/U.S. Choppers tanks, Phil’s Shop wiring system and the Biker’s Choice Speedometer, which we hope to mount in the tradition of rear-wheel driven speedometers of the ’20s.
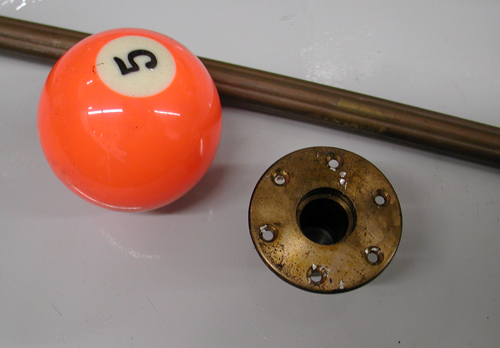
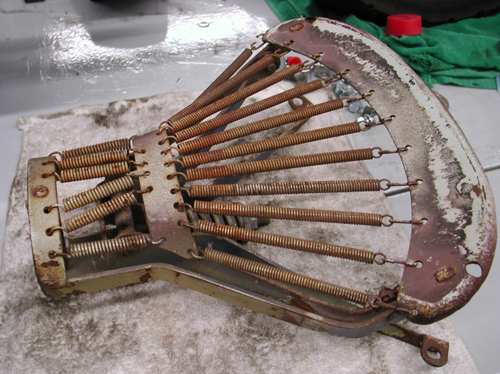
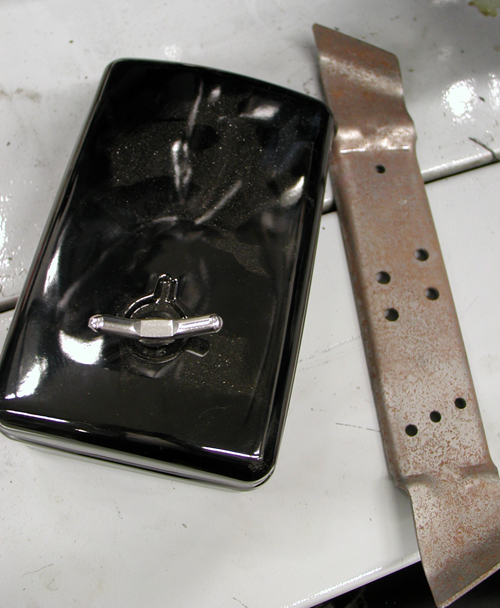
It’s all headed your way in the next couple of weeks.
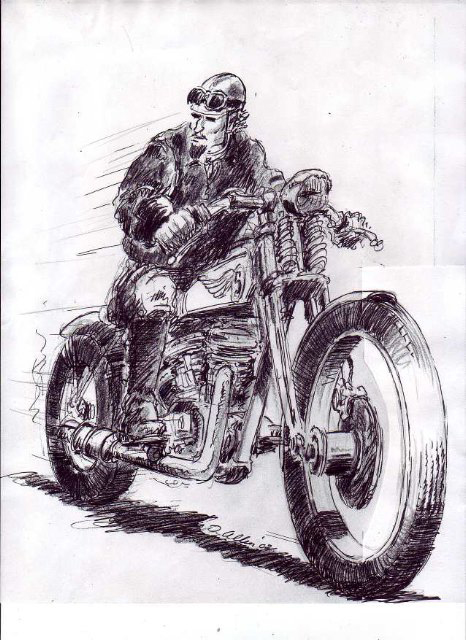
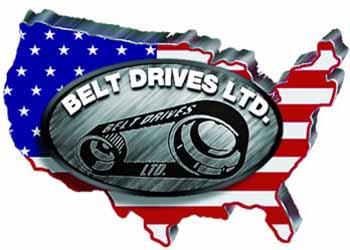
Amazing Shrunken FXR 11: Mid Controls
By Robin Technologies |
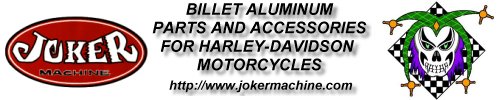
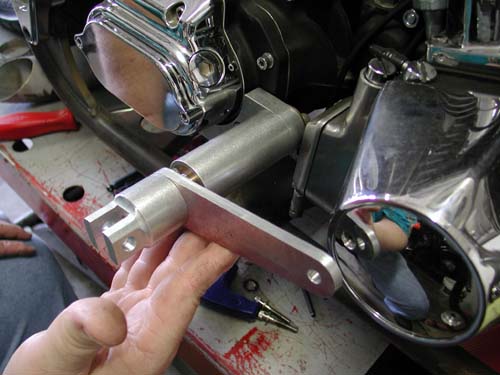
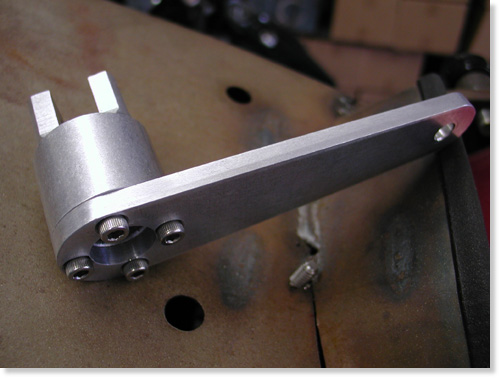
Shrunken FXR mid-controls by Giggie at Compu-Fire. Note: we need flat-headed Allens.
Giggie our master machinist from Compu-Fire rolled up to the Bikernet Headquarters last Saturday. We haven’t seen him for months due in part to his work on new starting systems for the custom market. They are dancing through the final development stages of a system configured to drive off the crank shaft of the motor with a 60- to-one ratio compared to stock 48-to-1. That will leave the area about the tranny available for custom applications or lower seat heights.
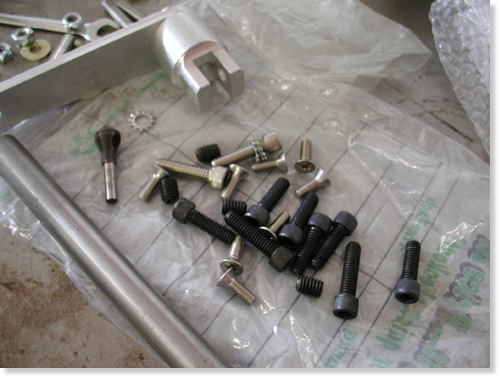
Giggie brought some wrong fasteners but lots of them and counter-sunk drilling tool.
Currently Compu-fire is soon to release a standard starting system, the Gen-2 HT, with 33 percent stronger magnets, 6-roller longer clutch (32 percent longer) with 30 percent more cranking while drawing the same amps from the battery.
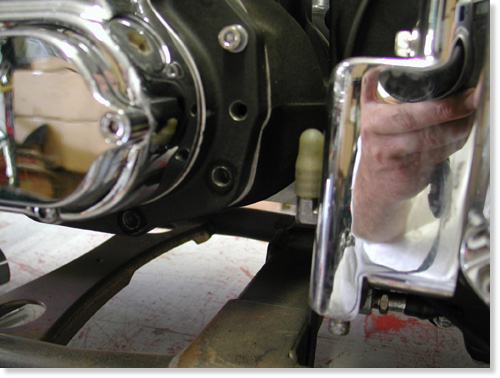
Here’s the tranny without the brake pedal components. There’s some tight tolerances going on.
I spoke to him about our cooling debate and here are some of his thoughts. “You want your oil to run at a minimum temp of 205 to eliminate water vapor or condensation that accumulates in oil,” Giggie said. “At 240 to 260 degrees petroleum based oils begin to break down, although synthetic lubricants could be good to 360 degrees. I have my doubts.”
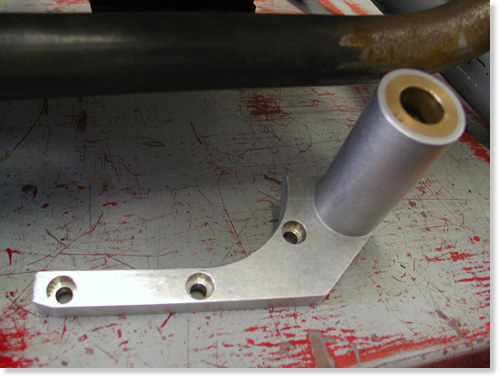
Base bracket to be bolted to the transmission.
Giggie developed an oil cooler for his FLH that kicks on at 220 degrees and off at 200. It has an in-line thermal switch continuously reading oil temp. He installed his cooler in a box with vents and two small electric fans wired to the thermal switch (to cool while idling).
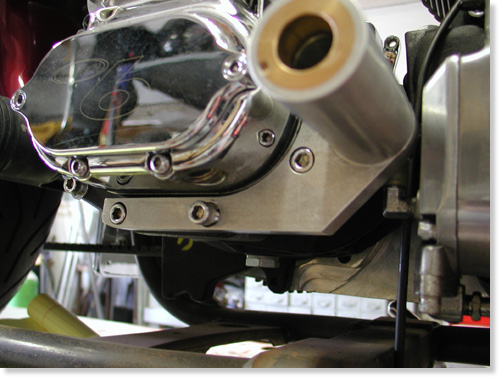
Giggie’s mounting bracket bolted in place.
Regarding our project Giggie dropped off hand machined mid-controls for shifting and rear brakes. Next, we must buy a H-D slave cylinder with remote reservoir with a built in brake switch. We will hide the reservoir behind the oil bag and design a bracket to hold the slave under the trans.
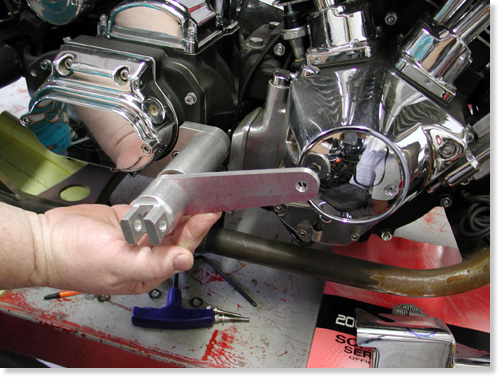
This shows the pedal and shaft in the mounting bracket.
Giggie will supply us with four more bushings to run behind the shift and brake levers, two 1/8-inch thick and two 1/2-inch thick, to allow us variable spacing away from the engine pulley or point cover on the cone.
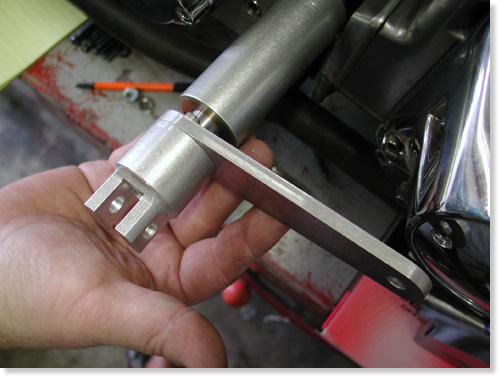
Giggie will supply two different bushing to be installed between the brake lever and the mounting sleeve. We’ll need the space to clear the point cover.
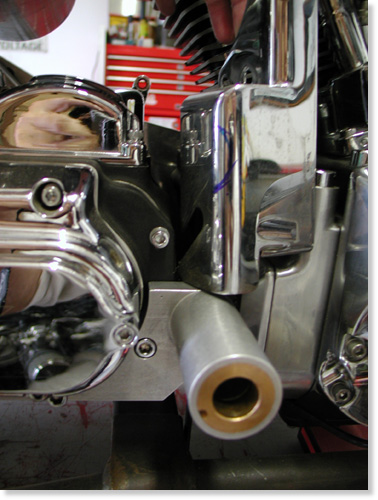
Unfortunately the sleeve hit the oil pump cover. We may be able to remove enough material or just polish the pump. The oil pump inlet fitting will also need to be turned down. It’s close.
With the bushings in hand we can develop our final linkage behind the BDL belt drive plate and Giggie’s tranny plate to connect with the slave piston.
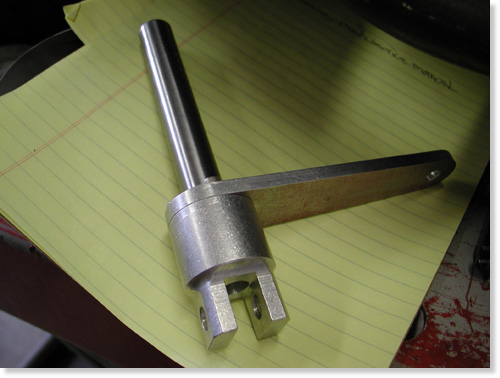
In both cases we need to cut and machine the other end of the shaft, depending on the linkage.
I’ve decided to remanufacture the exhaust system which is now a tight fit around the new brake linkage. Giggie also machined the foot peg mounts to accept any standard, pivoting foot pegs.
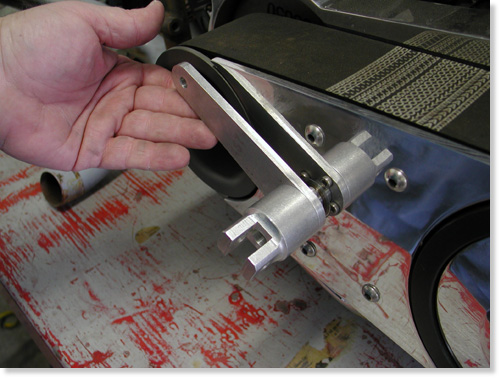
The slick new mid controls for shifting slid through bushings machined into the BDL outter and inner covers.
Next we need the bushings, slave cylinder and a day in the garage hammering and welding a new set of pipes.
–Bandit
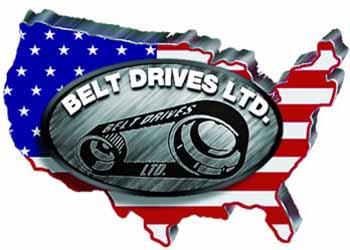
Back To Part 10, Page 2