1928 Shovelhead Project Part IV
By Robin Technologies |

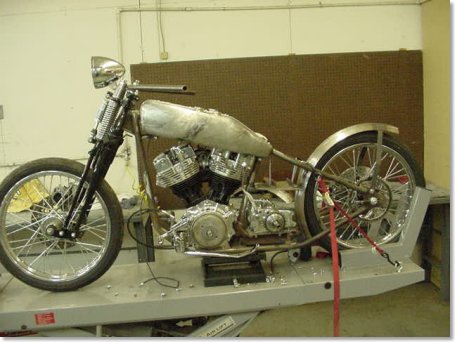
One of the best aspects of building bikes nowadays is the integrity of the components. If you get the right mixture of components together and take care with the wiring and assembly, you’ll have a bike as reliable as factory stock. That’s one of the reasons Bandit has moved to using Compu-Fire electrical components on most of his bikes. First, because even he can install them, and most of all, because Compu-Fire has been building electrical components for years. The stuff doesn’t break.
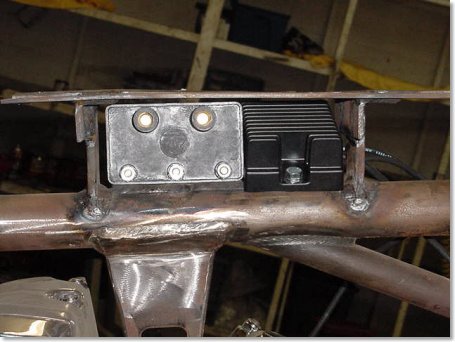
Take, for instance, this charging system. The stator slips firmly in place over the engine sprocket shaft race area and Compu-Fire suggests that you use the stock fasteners with a drop of red Loctite to ensure it won’t ever come loose. Compu-Fire alternator plugs are the protruding variety from the late-model design. Carefully oil the plug and slip it into place, then replace the plastic bridge and fasten it with blue Loctite. If you have new cases, make sure there are no sharp edges on the plug opening. File if necessary. Then with the shaft seal .090 shim in place, use a wire feeler gauge to determine that you have at least .060 of clearance between the rotor and the case.
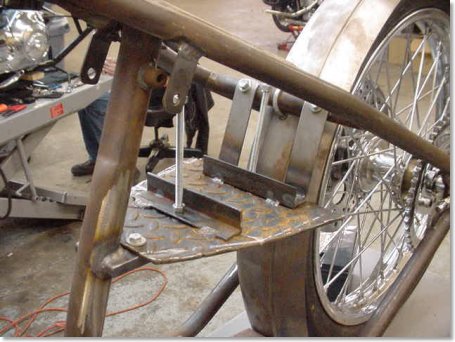
With each Compu-Fire charging kit for Shovelheads or Evolutions comes a thrust washer that goes on the outside of the rotor on chain primary systems. It may not be necessary on belt drive primaries. Mr. Gillihand from Compu-Fire recommends that you have a direct ground to the engine cases. Compu-Fire charging systems are the series type, unlike the shunt variety. The difference is that a shunt type drives the charge to ground if the battery is satisfied, causing the alternator to heat up and constantly work. The series type shuts the stator off when the battery is satisfied, which allows the unit to cool. The hot wire goes directly to the battery through a circuit breaker, or to your ignition switch on the hot side. In this case, the regulator was positioned with the coil between the tanks so the plug wire had to be extended.
That covers the basics of installation. Now here are the specs: Compu-Fire manufactures two versions of its charging kit, a 32 and 40 amp. From 1970-’75, stock charging systems were rated to 15 amps; from 1976-’80, they were 17.8 amps; between 1981 and 1988, they jumped to 22 amps; and finally, in 1989, skyrocketed to 32 amps. Now fuel injected models run 38-amp systems. So the two systems cover the lot.
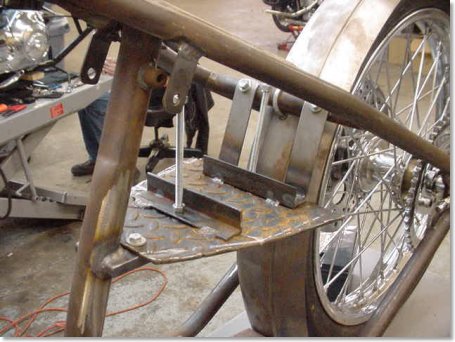
We’ll get into wiring after paint and chrome. The ignition system is Power Arc. The timing module is in the nose cone and the coil is also positioned under the seat with a chunk of angle iron. This system is about as clean as you can find.
Next week we’ll hit the final sheet metal as we close in on paint and chrome, and the lovely Princess Lena, daughter of the rich and powerful Rick Fairless, king of the Strokers Ice House plantation, makes her move on the hapless Bandit. –Wrench
Sturgis Shovel Part 12
By Robin Technologies |

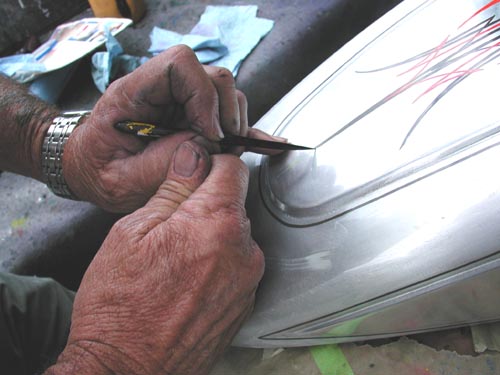
Hey, here’s quick bit on George The Wild Brush who handled the Pin Striping on the 2005 Sturgis Shovel project. He’s pin striped several other bikes for me in his 47 years behind the brush. Born in Hanford, California, a miserable military town, in 1944, he kicked tumbleweed while his mom worked on a base.
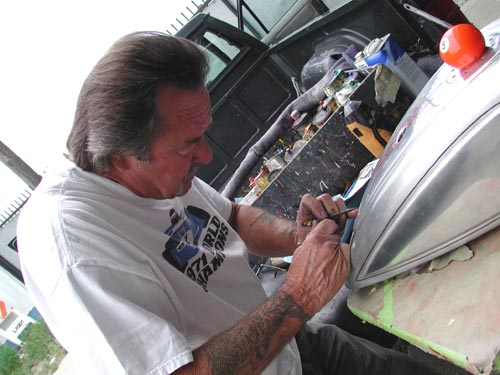
She moved to the safety of Southern California away from the miserable summer central Califa heat, to Long Beach then Lakewood (next door) where he went to school, but didn’t graduate.
He was warned that the fad would die so his vocation would fail. “The fad’s still rockin’,” George said. “My first car was a ’54 ford and I custom painted the driver’s side. I couldn’t afford enough paint to finish the passenger side, so I had the only cool side.”

He studied Von Dutch work, Larry Watson and George Barris. “I’ve striped refrigerators, toilet seats (new ones), and 50 and 110 Tom Gentry trans Atlantic ocean racing boats. He’s taught me a thing or two about striping. “It’s best to have the parts off the bike for the best quality art.”

It’s difficult to paint bare aluminum—“Paint won’t bond to it.” without a primer.” I worked at Gasoline alley for 15 years painting aluminum dragster bodies.
It’s also difficult to pin strip chrome—“It won’t hold up due to the lack of porosity.”
He only uses One-Shot enamel paints—“Can’t use any paint.”
With motorcycles it’s a good idea to clear over striping—“People don’t pour gasoline all over cars, but they do bikes.”
Cars don’t generally need to be cleared over striping work.
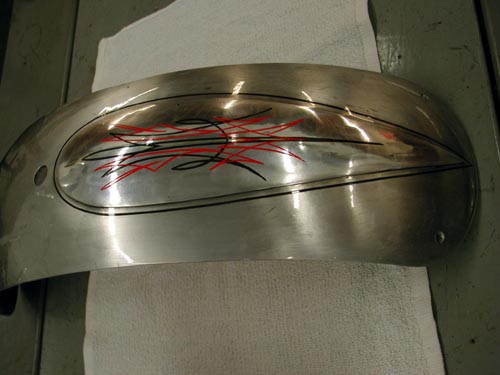
His number is (310) 488-5488 for classic pin striping and good stories.
George came to the shop just after I picked up the clear powdered aluminum sheet metal from Foremost Powder. He usually tells me what I’m going to have striped. I have a vote and initial color selection, then I best get out of the masters way.
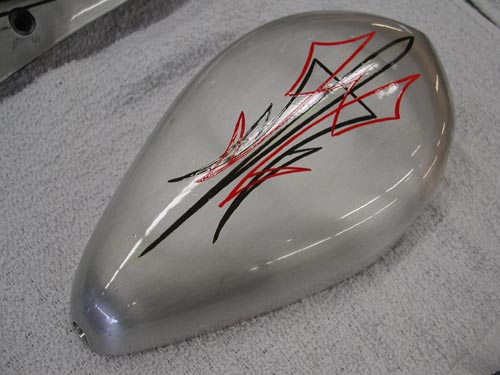
He striped the Goodsen Air Cleaner, which was treated to my holy treatment, then brushed with Scotchbrite to remove the polished appearance.
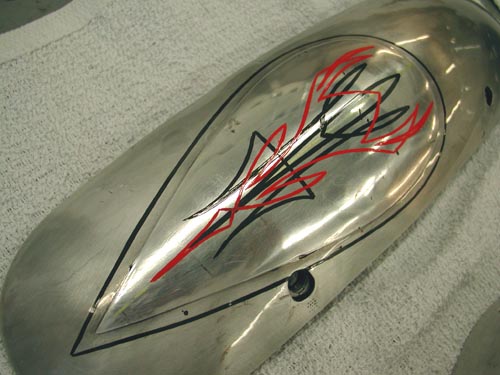
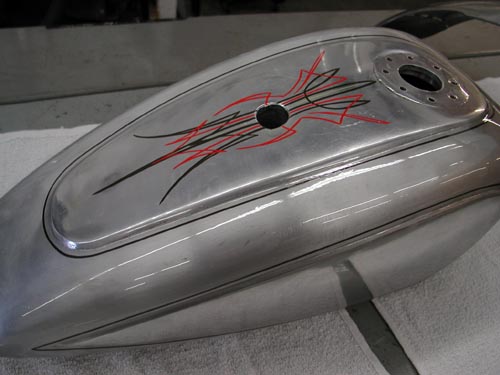
Then he striped the panel polished, highly-modified, XR750, Cyril Huze donated tank and Lucky Devil, custom made fenders. I polished the panels and brushed the rest for a two-tone effect. Not sure it worked, but George gave it a final touch.
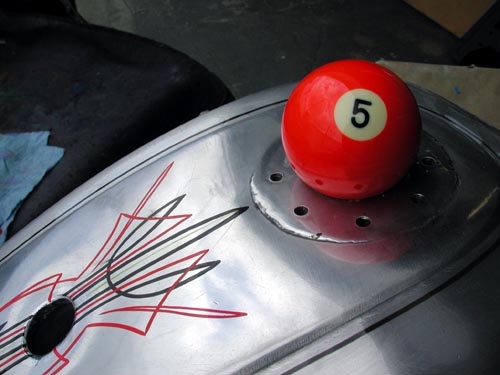
George suggested the 5-ball addition to the center of the tank. Not the gas cap. Ultimately I filled the center-mounting hole with a small 5-Ball to commemorate our company and all the women who put up with my shit over the years. In case you don’t know the story, I’ve been married five times, that’s five misses Ball.
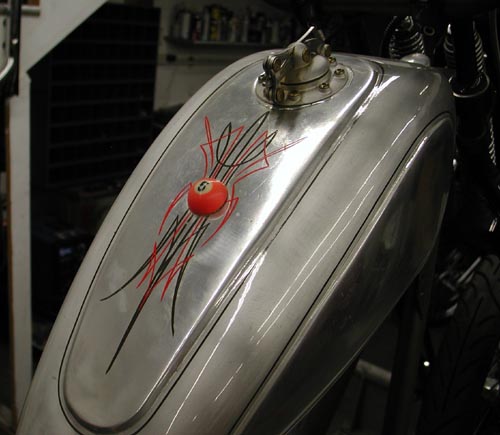
1928 Shovelhead Project Part 1
By Robin Technologies |

In an effort to stay tuned with the rapidly growing and ever changing industry the staff of Bikernet began a project Shovelhead several years ago in conjunction with Randy Simpson of Milwaukee Iron and Arlen Ness. It’s been a strange road, but we’re now rolling closer to completion with the assistance of Rick Fairless of Dallas Easyriders and his ace fabricator Jim.

The project began with the purchase of a slightly destroyed Mexican Police bike from Arlen a couple of years ago. He had scored some 300 1984 Mexican cop bikes that had been ridden through several revolutions and costly rebellions. The bikes were shot at, dragged, bombed and ridden harder than any V-twins on the planet. When we first purchased the Shovel complete with police sirens and blinkers, we assumed foolishly that we would restore it to it’s original fighting condition. Arlen even hand picked our unit specifically with our goal in mind.
Well it’s one thing to dream of a restoration, but when the cast iron triple trees are broken, the frame is bent, all the sheet metal destroyed we took a step back and said, Help! We pulled the Engine and sent it to JIMS Machine for a rebuild along with the Transmission. With the cases replaced along with the barrels and heads and all the internals replaced, the engine was ready to rock once more. A similar concoction was mixed for the transmission and a couple of us dressed all in black and prepared to bury the chassis in a shallow grave in the desert outside of 29 Palms, California when the Editor of “Biker” pointed out that we had a valid pink slip. Dean, salivating, over the dying chassis took the entire unit and paid us handsomely for the paperwork. We suspect that he made a rocking chair out of the frame and wheels. During one of our weekly Bikernet meetings we discussed what to do with the Shovelhead drive train, and in the process we started discussing various options and some of the customs we respected the most. Several suggestions were thrust onto the rusting boardroom table. First Randy Simpson had volunteered to help us build an old time looking bike from the remnants of the ’84. We voted unanimously to pursue this avenue, since we had always been impressed with the workmanship and design Randy injected into his own 1928 Shovelhead projects, and he had a desire to create a simple chassis kit to build one of these puppies to market to the public. We agreed to help him promote the concept. We also all agreed that a gesture to the community of San Pedro was a necessity since several members of the staff had been arrested and the headquarters were constantly under surveillance, so we decided that Bikernet needed its own private San Pedro Police bike. How else could we crash the local parades. Randy is a persnickety builder who takes great pains to build quality parts for the market. Two years passed and he still didn’t have the frame built. He was obviously so successful with his growing line of fenders that his chassis concept was slipping onto the back burner. Arlen Ness was also taking giant strides to build a similar machine and if you picked up a recent Easyriders you would have seen the fruits of his labor in his 50/50 Shovelhead. In addition Chrome Specialties with the assistance of Chico in Southern California had recently completed a similar project around a Sportster (It’s called Trick and is featured on Bikernet right now). The competition was stiffening. Randy dropped out, and we moved ahead, and with some research we discovered that a number of reproduction parts are being built in Europe for early Harleys. Early like in 1915.
Devoted to successfully completing this project we picked up a rigid frame from Paughco. This is a standard scale Paughco Rigid for Shovelheads. From there our old part contact was Fred Lange in Santa Maria California. Fred informed us that a European group is remanufacturing 1915 springer front ends, flat track tanks, headlights, fenders and Fred was making appropriate sprung seats for these models. We were in business. We ordered the flat track tanks, the fender for a side car so it could be used for the front and the rear, a hand leathered seat and snuck out of the hills over looking Santa Barbara.
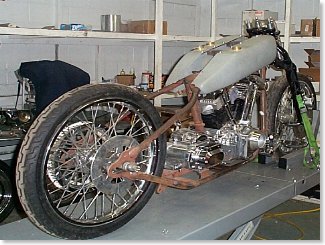
We had a Bad Boy front end, Wheels, etc. We’re in the market for some Custom Cycle Engineering lowering rockers. At that point we needed miscellaneous parts, pipes, etc., and we could get this puppy on the road. It was time to call in a favor. Rick Fairless had purchased the exclusive Bandit I Pat Kennedy Built bike from Bandit and part of the deal was parts and labor on a bike project in the future. It was time to call in that note. Then in a stroke of bad luck and good, Marty Ruthman decided to close his shop abruptly due to health problems and he had a massive sale.
–Wrench
Mudflap Girl Part 2, the Bandit Engine and Spitfire update
By Robin Technologies |
Okay, you have the story behind this build, and Chris Kallas is refining the concept drawing. My engine arrived from the factory, and Eric Bennett immediately noticed the return address, in Viola, Wisconsin.
As it turns out, the factory hired the S&S crew to assemble their Evo line of engines. What a natural. I liked that notion all the way around the block. First, it means more American hands in my new engine. Plus, what could be better than to have the best performance engine company on the planet working with the factory on the last and most refined V-twin configuration?
For this crew, and lots of riders all over the world, the FXR Evo is the best of the best. So, for Bikernet, this became the year of the FXR and the Evo engine. I asked the factory about their Evo engine program and received the following information.
A Modicum of Harley Engine History
The first 74 cubic-inch V-Twin engine on the JD and FD models was introduced in 1921 and the 45 cubic-inch side-valve V-twin engine (later to be known as the Flathead) on the D model debuted in 1929. The Flathead engine proved so reliable that variations of it were available on Harley-Davidson motorcycles as late as 1973 (servi-car trikes).
In 1936, Harley-Davidson introduced the EL model with an overhead valve, 61-cubic-inch engine. With increased horsepower and bold styling changes, the motorcycle earned the Knucklehead nickname, due to the shape of its rocker boxes.
New features were added to the 61 and 74 overhead valve engines in 1948, including aluminum heads and hydraulic valve lifters. New one-piece, chrome-plated rocker box covers shaped like cake pans earned this engine the nickname Panhead. The engine introduced on the Electra Glide models in 1966 to replace the Panhead became known as the Shovelhead, again due to the shape of its rocker covers.
1340CC Evolution Softail Engine – Silver and Polished SPECS
Type: 4-cycle, 45 degree V-twin
Bore X Stroke: 3.498 X 4.250
Displacement: 80 cubic inches or 1340 cc
Compression: 8.5:1
Torque ratings at 3,500 rpms: Touring with fuel injection, 83 ft./lb.
Touring w/carb 77 ft./lb. @ 4000 rpm
Dyna/Softail 79/76 ft./lb.
Miles per gallon: 50 hwy/ 43 city with a touring model using a carb
55 hwy/ 43 city Dyna or Softail
Variety and sales info:
1340CC Evolution Softail Engine – Silver and Polished
Since the first single-cylinder built in 1903, engines have been the heart and soul of Harley-Davidson history. Each motor has made its unique contribution, and the V2 Evolution engine is no exception. With the Smart Start Engine Program, buying a new Evolution engine has never been easier. When replacing your Evolution motor, Smart Start offers brand-new, factory-tested engines at an unbeatable price. Choose the standard silver and polished Evolution, sinister black, the classic black and chrome or the silver and chrome finish. Either way, you won’t just be making a new start; you’ll be making a smart start.
16161-99
IN-STORE PURCHASE ONLY, Contact dealer for pricing and availability.
Fits all ’99 Softail models. Does not include carburetor, manifold or timer cover.
MSRP US $3,295.00
1340CC Evolution Softail Engine – Black and Chrome
16160-99
IN-STORE PURCHASE ONLY, Contact dealer for pricing and availability.
Fits all ’99 Softail models. Does not include carburetor, manifold or timer cover.
MSRP US $3,995.00
1340CC Evolution Softail Engine – Silver and Chrome
16177-99
IN-STORE PURCHASE ONLY, Contact dealer for pricing and availability.
Fits all ’99 Softail models. Does not include carburetor, manifold or timer cover.
MSRP US $3,495.00
When my engine arrived, I immediately hauled it in the Bikernet Hearse to Bennett’s Performance for a slight performance upgrade. I needed to let that puppy breath without messing with the reliability aspect. Sharing the same building on the edge of Signal Hill, California is the headquarters for Branch O’Keefe. John O’Keefe worked for Jerry Branch for decades and ultimately bought the business when Jerry Branch decided to retire.
We’re looking at several options for stock engines and for rebuilds. We have three touring models coming together right now, and they are all 80-inchers. One for my son, my factory motor, and Dr. Hamsters 200,000-mile Evo rebuild by Bennett’s.
I’m running the brand-new factory plain Evo engine with the Andrews EV-27 cam and Andrews chrome-moly adjustable pushrods for less flex, a new cam bearing and the Branch flowed stock heads, for 8.9:1 compression, 78 cc Branch-flowed chambers, and 75-80 horses at 2,600 rpms.
The next higher upgrade step from Branch is the EV-51 cam and additional headwork and shaved heads for a 10:1 compression and 85 horses at the same rpms. And finally, a customer can run with an EV-59 Andrews cam and 10.5:1 compression and 90-95 horses. Not bad for never taking the barrels off.
“I like rpms,” John O’Keefe said, “and the new ignitions allow these engines to burn more fuel and bring out the horses.”
The key to all this performance is the headwork set to match the cam, and John O’Keefe has studied this science for most of his life. The key is building a mid-range hot rod without sacrificing reliability.
The first move was to strip the engine and deliver my fresh factory heads to the Branch team. Eric Bennett set my beautiful, plain H-D Evo engine on his clean room bench and removed the top motormount, the top rocker box that came off with the middle ring. We noticed much improved, one-piece factory Teflon gaskets. We won’t mess with them. Then Eric removed the rockers, the pushrods, pushrod tubes and rocker boxes. We also retrieved the new base gaskets to reuse.
Then he removed the head bolts, the front head, and the rear head. I had already purchased the Andrews EV-27 cam from Branch O’Keefe, and Eric and I started to prepare for installation. He removed the point cover, ignition, and cam sensor.
He had a terrific Trock tool for removing the cone cover. It’s always a bastard to try to carve around the narrow gasket surface with a screwdriver or a knife, hoping to find opening and risk damage to the cases or create a leak by scratching the gasket surface.
“We always replace the new factory cam bearing,” Eric said, “with a full compliment Torrington bearing. The factory ran the good ones from ’55 to ’92, then they shifted to a cheapo brand. It’s also not a bad idea to replace the factory plastic breather gear with a solid JIMS unit.”
I scrambled to take notes and photographs while Eric peeled into my engine. He popped a factory set of magnetic tools into the lifter stools to hold the lifters up during cam removal. I wish I had a set of those puppies.
“It’s interesting,” Eric said. “Virtually every stock cam is .060 longer than any aftermarket cam.”
Eric pre-measures the cams and adjusts the thrust washers before replacing the cam, which you will see in the next report, when we study the Branch recipe for performance, the headwork, and modifications. He replaces the valve seats for larger valves, then ports and polished the chambers. You won’t believe the long-lasting components Branch uses.
Then we will watch Eric replace the stock cam with the Andrews unit and adjustable pushrods, and put the whole Evo puppy back together. “Don’t forget to order a top end gasket set,” Eric reminded me as the rain cut loose outside and I wondered if this winter season would ever end. I need a ride.
Then Eric grabbed a JIMS tool and a couple of wrenches and in 30 seconds pulled the cheap cam bearing from the new cases.
“I’ve seen these go south in 10,000 miles,” Eric said. “I’ll never understand why they replaced a perfectly good quality bearing with this junk.”
Just as quickly Eric took an aluminum guide and a mallet and tapped the new bearing in place, another 10 seconds passed, and we were finished.
A couple of days passed and I thought, just maybe my frames and front ends would be completed at Spitfire. On a hunch, I peeled 57 miles away from the coast in the hearse while listening to KJazz on the radio.
It was quiet as I wandered into the vast machine shop, welding shop, bike assembly area and ran into Joe Cavallo, Paul’s dad, who was hunting around the shop for Softail brake anchor brackets. He greeted me and said something about shop organization. The Spitfire and American Made business model has faced serious transformations over the last couple of years.
As I mentioned before, Paul was the partner and manufacturing arm of Hellbound Steel motorcycles. American Made manufactured fast moving products for a bunch of now defunct companies such as WCC. At one time, they were building hundreds of choppers each month, and thousands of products in a much larger facility. During the last year, they adjusted their business model and tightened their facility. They rewired their building, replumbed it with compressed air lines, and kept building products.
It’s tough to stop everything and regroup, scour through boxes of tools, base material, parts, and junk. With a skeleton crew they are still building any frame a customer needs, including big twins, rigid Sporty frames, British custom frames, and even frames for Yamaha 650s and Honda fours. They also build an entire line of forward controls, gas tanks, handlebars, girders, and glide front ends (bowling pin), pegs, oil tanks (a variety of styles), trees and taillights. Paul is the mad scientist of the group. As a kid, he manufactured exotic gun cases.
He’s the kind of guy who will catch a notion in a cup of Starbucks coffee, in the morning and by the evening, he has a new product. It’s not a one-off either. It’s fully designed and configured for multi-manufacturing.
Some of his crew have been working with Paul and his dad for decades, including Larry, who is their master motorcycle assembly guru. He knows it all. “Pull the alternator rotor off that engine before you run it,” Larry told me. “Check the wires for twists or tears.”
I made a note. Then we made our way into the frame jig area to see the FXR frame progress. The FXR fever caught on and there were at least five FXR frames in the making. The first was based on the pro-street configuration with additional gussets, the squished wishbone, for the single-loop notion and 36 degrees of rake for a 2-inch longer girder front end.
They discovered some issues with my request for a V-style frame in keeping with the stock FXR configuration. I also hoped for less rake and a shorter Frisco style girder front end style. Paul was working on my unit with a 30 or 33 degree rake, but he also started building a couple of drop seat FXR frames, including one for himself.
We are also going to try a slightly longer swingarm suggested to us by Dar, the boss of Brass Balls for his FXR configuration. He wanted to pull the rear tire out of the frame some, and I was willing to try it. They are hot after these frames, since Paul plans to ride one on the Diablo run that kicks off on May 5th in Temecula, California and rolls toward the border. Don’t know if we will make it.
The plan for now is to pick up the frames, swingarms, axles, and Spitfire girders, on Friday April 8th. Between now and then, hopefully we will wrap up the engine and bring that puppy home to the headquarters. We are trying to match up these Mudflap Girl FXRs wherever possible, but not always. We are going to run long and short dogbone risers from Custom Cycle Engineering, but we’ve ordered a new set of Raw 2-into-1 performance pipes from Bub for Frank’s FXR, and I’m running a D&D 2-into-1 system. I’m running a Frisco’d and stretched tank and he’s running something completely different. He’s running a Klockwerks rear fender and I’m running something bobbed. I’m getting seriously ahead of myself. See you in a couple of weeks with the next report.
–Bandit
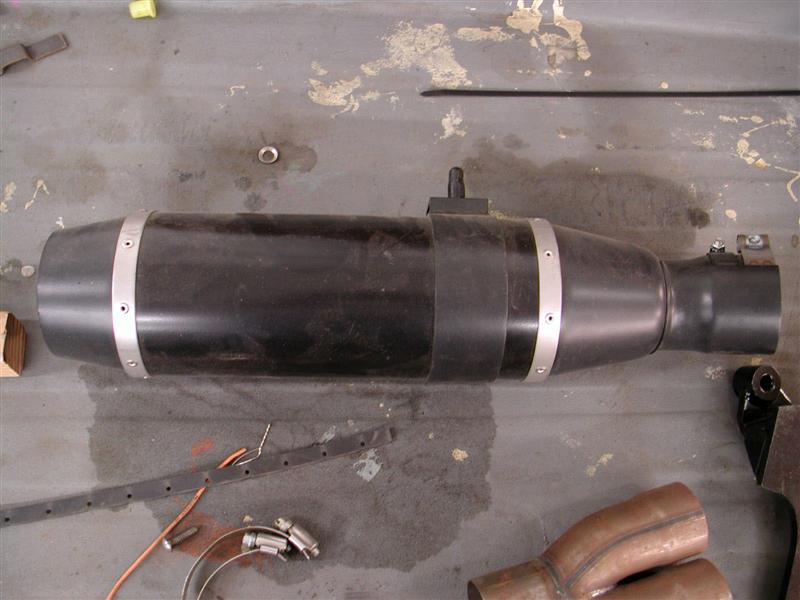
Sources:
Bennett’s Performance
Branch O’Keefe
JIMS
Spitfire
Custom Cycle Engineering
D&D
Harley-Davidson
Rivera Primo Inc.
Belt Drive Unlimited
Metal Sport Wheels
Sturgis Shovel Part 6
By Robin Technologies |
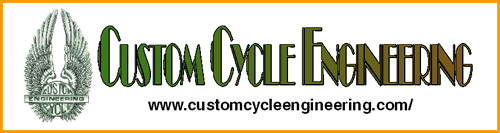
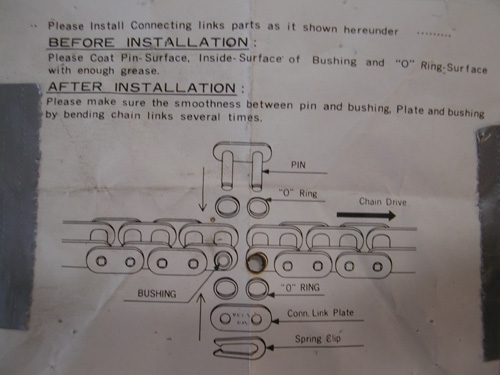
Here we go. I’m relunctantly behind the eight ball, or more likely the 5-Ball in this case. The bike is nearly complete and I haven't caught up with the articles. For the most part I was working at Primedia on the bike mags and didn’t have time to breath. No fucking lame excuses. Let’s hit it.
My original plan called for brass sculptures to hang this bastard together in a purely Bandit way. I messed with some odd heavy brass cloverleaf rod that was over a ½ inch in diameter. I wasn’t having my usual creative luck with bending or messing with this material. Kent from Lucky Devil Metal Works in Houston recommended that I use silicone Bronze rod and I’ve since messed with it. I shifted gears from Gargoyles and sculptures to pure mechanics. I started drilling holes is everything.
I discovered a piece of ½-inch wide strap that I thought was copper. Remember that the notion behind this mess is to use as much bare metal as possible. As it turned out the strap was brass so I gave it the Scotch Brite treatment and went to work. Before I made or positioned the rear Custom Chrome chain I needed to align the wheel, the transmission and the engine. I used my BDL inner primary and pulled the loose engine and tranny into position. Then I centered my chain axle adjuster and installed the chain using the CCI instructions (above). I have an old chain breaking tool, so I took out just enough links.
With the chain in place, aligned and adjusted the wheel using the Doherty wheel spacer kit (a life saver). I couldn't mess with the requisite chain guard until all was in the correct groove. Although the Paughco custom frame is designed for a belt, I choose the old school route and it worked out well. Lots of extra space to mess with.
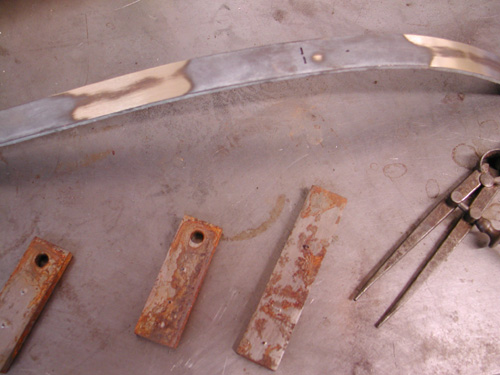
I dug through my drawers of tabs and crap that I’ve had around for 25 years. In the old days Mil Blair would call me from Jammer from time to time and tell me when it was time to shit-can scrap iron. I picked up tabs, spacers and brackets by the fist full and I’ve been moving them from place to place ever since. But damn, when you need a tab it’s bitchin to find just the right size in a drawer. Since I was going nuts with the drilling treatment, I matched the work on the frame with holes in the chain guard and counter sunk the edges for a more rounded look.
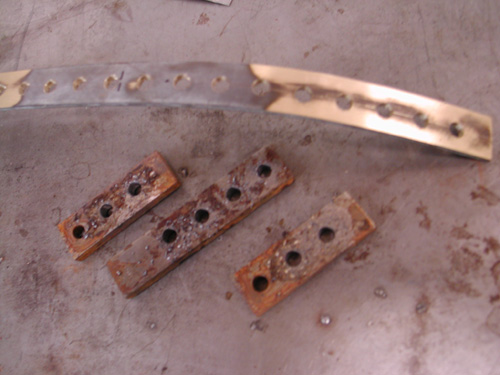
I also hit the top motor mount with a similar treatment. To give it a bit of consistency I measured from center to center on the holes and made all the holes the same diameter, 1/4-inch.

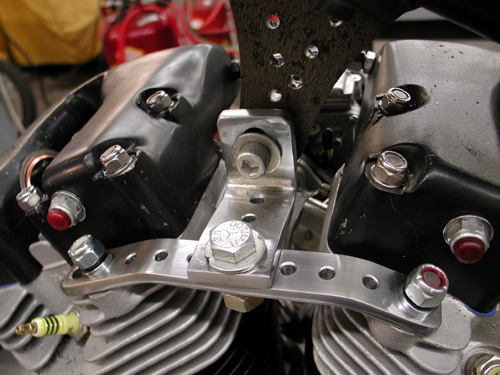
The hole deal became an obsession. I started drilling ¼-inch holes in everything including the Joker machine foot controls. I also went after Russell Mitchell’s Scotch Brite code. I swallowed hard and rubbed a piece of chrome with the coarse material and discovered that chrome reflects everything until it’s brushed with the wiry fabric. It gave it a raw material appearance and I decided that it was cool but a pain in the ass to do.
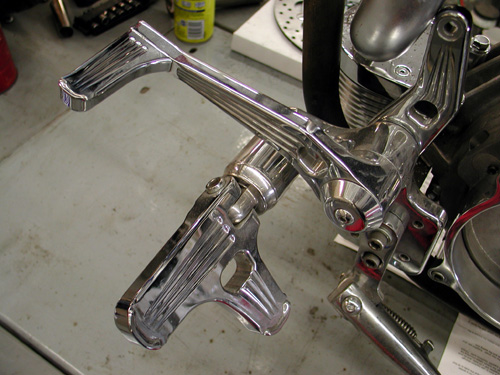
Again, I drilled the holes the same space apart, ¾ of an inch. It’s not always that easy, though. Sometimes the formula just doesn’t work. I use a pair of calipers to hold and mark the distance from hole center to center. If a hole ends up being located too close to an edge of the material, I back off and try another formula. Make sure to plan before you start drilling.
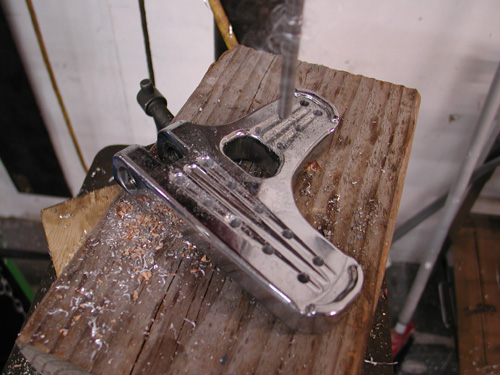
Here’s that damn brass stock. I was determined to have Brass, Copper, Stainless, Aluminum and a bare metal effect on the frame. You’ll see shortly how it worked out. I couldn’t bend that brass shit without destroying it, so I made the shift linkage out of it. I cut it off on a bench lathe and drilled and tapped the ends to 5/16 fine threads to fit the fine thread heim joints. Then I drilled the rod and countersunk the holes to remove the sharp edge.
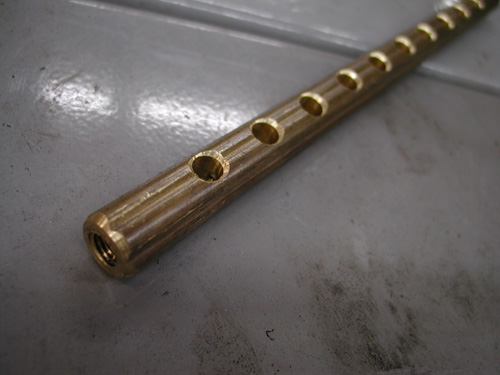
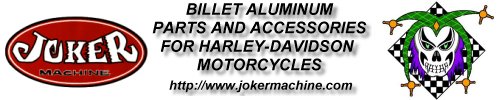
Here’s one of the Joker Machine control sets, rubbed with Scotch Brite and drilled. They make fine controls, some of the best. You can adjust these puppies anyway you choose to fit your riding position, inseam or foot angle.
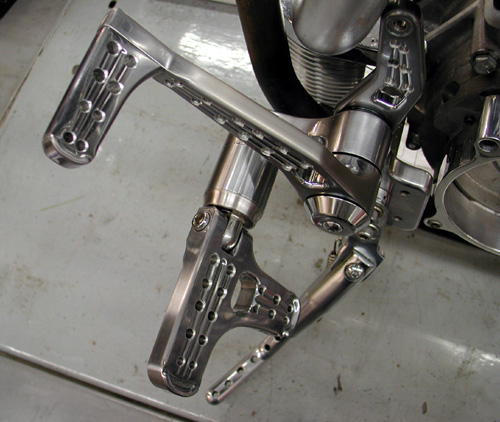
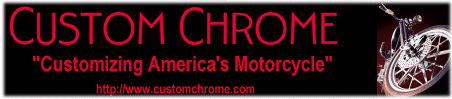
Before I leave this chapter I’ll touch on this new petcock from Spyke. It’s incredible, if it works well. It’s designed to give you every option for positioning and spigot direction. I ran into only one problem. No wrench lands to help tighten the bastard.
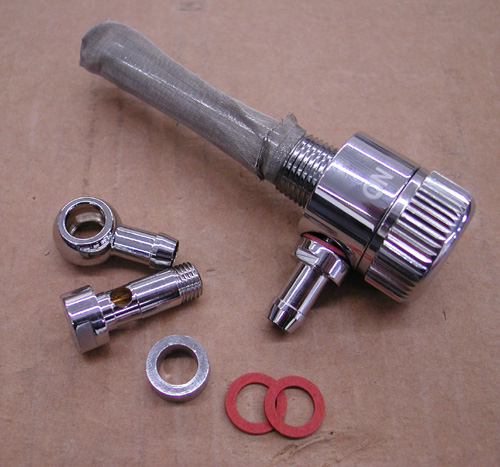
Check it out. You can run it faced in any direction and still read the switch locations and turn the knob without a lever smacking the frame and components. The spigot set allows builders to face the gas line in any direction.

I used the straight spigot and took off one of the fittings because my tank threads are female. The only problem I had was tightening it down, but I’ll get to that after the powder coating returns from Foremost Powder in Gardenia, California.
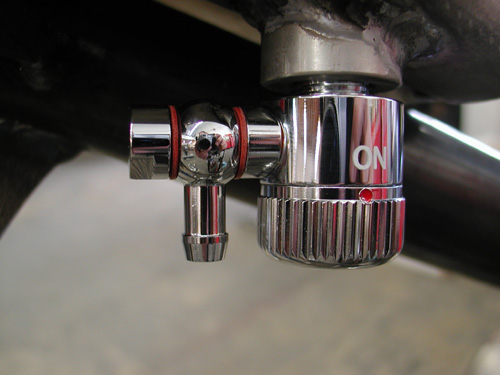
This puppy will revolutionize the industry for petcocks, if it works. I’ll let you know in a week or two.
Ride Forever,
–Bandit
Sturgis Shovel Part 9
By Robin Technologies |
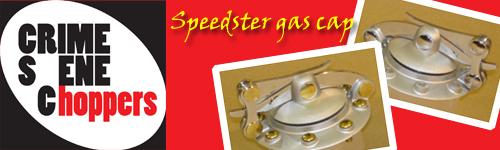
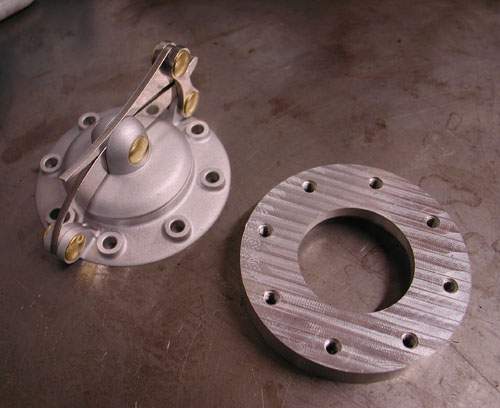
This is strange. I’m writing several Sturgis Chop Techs after I returned from Sturgis. I’ll try to remedy that in the future, but we were so damn busy trying to complete the bike and run Bikernet, we didn’t keep up on the techs. Many apologies.
This piece covers the installation of the hot Speedster cap from Crime Scene Choppers in the modified stock XR 750 factory tank. Later, you’ll discover, that this highly modified, strengthened and extra rubber mounted beast was my Sturgis nemesis. But more on that later.
We added rubber-mounted bungs to the back of the tank. I moved the petcock to the rear and filled the center for a 2.76-gallon gas capacity before it hit reserve. I doubt that it contained more than a quarter tank of reserve, so I’ll toss it a 3-gallon total gas capacity.

Oh, I need to thank Cyril Huze, who designs beautiful steel tanks for the opportunity to experience an aluminum tank once more. He suggested this classic for the Sturgis effort.
I’m not holding it against Cyril. He’s a master and I’m the bungler for attempting aluminum on a 93-inch rigid S&S hot rod. As you’ll see the vibration aspects came from several sources that I could have remedied. It’s all just a roll of the dice.
When I received the Speedster cap I drug the cap and tank down the street, about three doors, to Bill Hall’s Welding. He handles my aluminum welding, since I don’t have a TIG welding system. I’ve got the rest, but not TIG. I would highly suggest a TIG system for quality welding capacity and good looking welds. It’s much like welding with a torch, so you’re certain of the bead and depth of penetration.
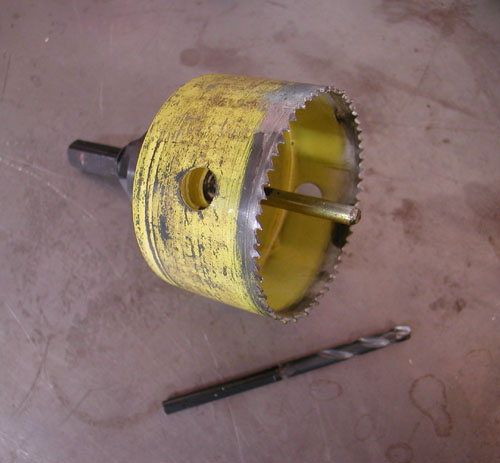
Bill’s a retired designer who enjoys welding and fuckin’ with his customers. “How are you going to drill the hole for the bung,” he asked?
I was thinking about die-grinders and files. I knew it would make a mess. Bill hooked me up with a 3-inch hole saw. He suggested that we hit a marine store for a tapered dowel pin (used for plugging holes in the leaking hulls).
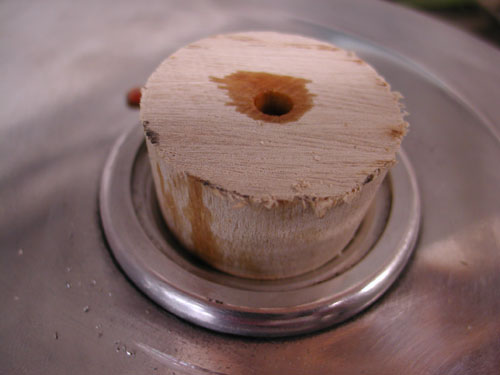
The key was to drill a perfectly centered ¼-inch hole to maintain a center approach to the cap bunghole. I drilled it and then ran the tapered wood dowel into the tank.
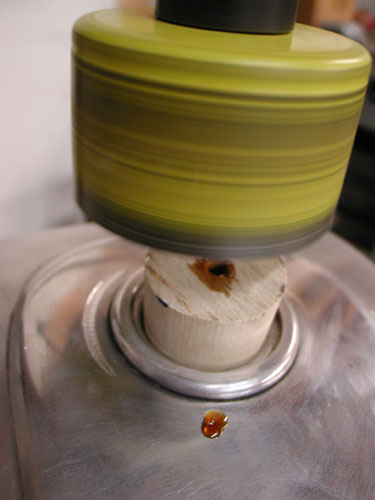
Then we set the tank on a pad on the drill press platform and lined up the hole saw. I used plenty of cutting oil on the edge of the blade and aluminum face to prevent the tank from snagging or catching. I knew how tender the surface of the tank was. We oiled the hole in the tapered wooden plug and carefully went to work. Bill’s formula worked like a charm.
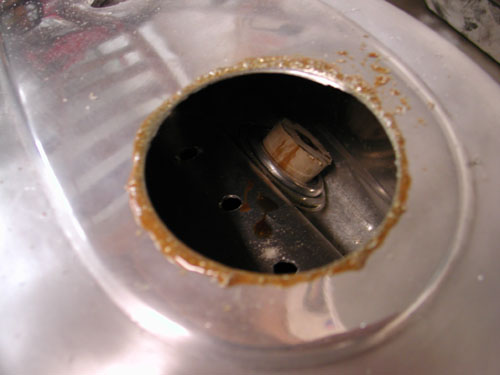
Next, we needed a tool to hold the Crime Scene Speedster bung in place. I grabbed a piece of strap, drilled a hole or two and mounted it with the supplied hardware, which was brass. You can order the cap with several styles of fasteners for your application.
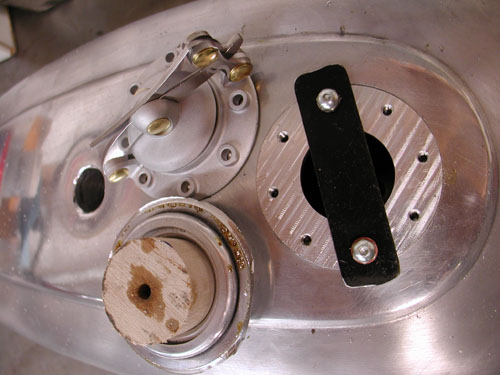
It was off to Bill’s for welding. While the gaping 3-inch hole was available I could have made a tapping tool and tapped out any imperfections in the tank walls. I dinged it way back in the beginning and never got around to fixing it. I left her be, as if it was the first injury and she needed to stay. I know it’s one of those wild superstitions.
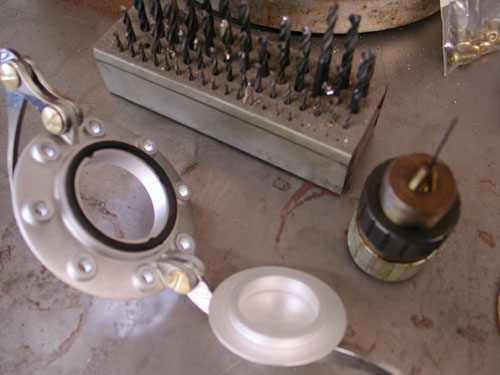
Okay, so during the “read the directions” phase, I noticed the bit about a non-vented tank. I would need to drill a tiny, cunt-hair hole in the cap of the tank. I discovered that I actually had such a tiny fuckin’ drill and dug it out. I had to find a chuck that pinched down to that size. Then I had a wise ass notion to drill the initial hole about 1/8 inch in diameter, since drilling with hair-thin bits causes easy drill bit breaks. The thinner the surface the better.
So, I initially drilled the inside of the cap with a 1/8-inch drill and drilled right through—Bummer. Ultimately I tapped the cap with a 10-32 then drilled the stainless Allen stud with the tiny drill bit. Then I screwed the stud into place and the job was finished.
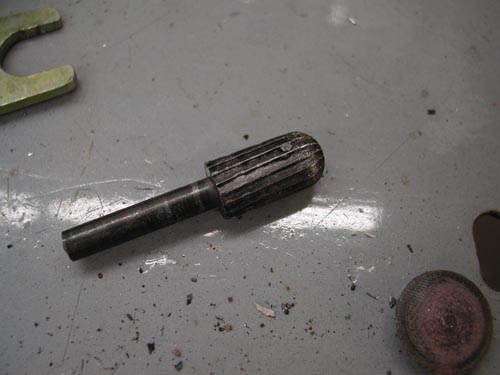
After Bill welded the bung into place it was my job to grind the welds down and ship the tank to Foremost Powder for a clear coat. I hit the big spots with a grinding tool. I tried my damnest to take only meat off the welds and not off the surrounding tanks surface.
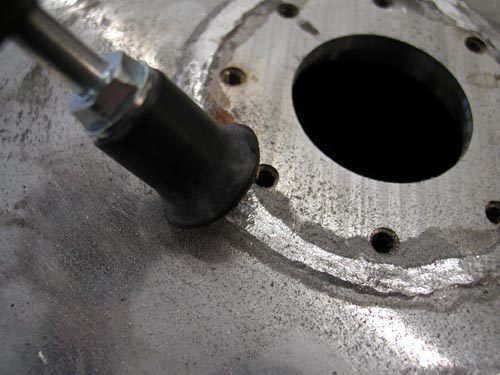
Next I used small emery discs to carve at the aluminum bead. I also smoothed some of the welds on the front of the tank where we filled the tunnel for additional gas capacity.

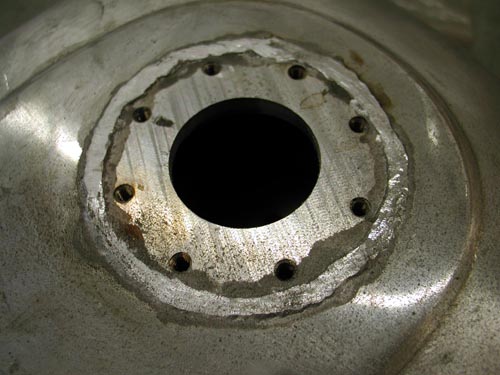
This shows the different grinding phases to reach a level that’s still strong with weld bead but handsome enough to live with. This was an interesting effort, since no bondo or thick urethane would be applied, covering a myriad of mistakes. This was the final stage before clear powder from Foremost in Gardenia, California.
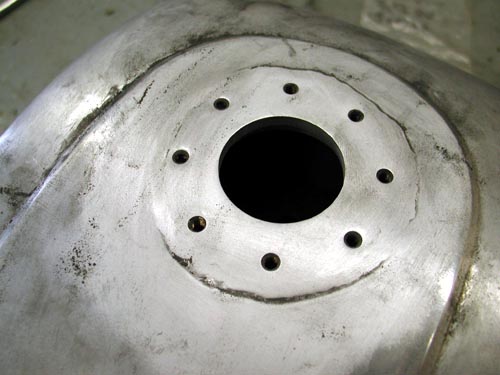
After this stage I polished the panels of the tank and hauled it off to the powder masters. There’s one other process I need to explain. I made every effort to clean the tank of debris and shavings. I also made sure to run a gas filter. I still had problems, which I will explain in my Sturgis Saga. They were easily remedied through Lee Chaffin at Mikuni. Just needed to dial the right number.
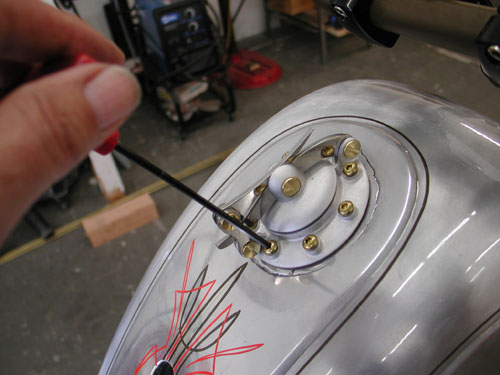
This shot was taken after powder and pin striping when I installed the gasket, decided which direction I wanted the cap to face and screwed the brass fasteners down. The cap worked flawlessly all the way to the Black Hills.
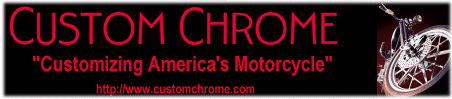
5-Ball Factory Racer Closing in on New Cam and Ignition
By Robin Technologies |
We were fortunate to hook up with Heather New, of New-Line Engraving several years ago. Since I was about to switch out my CrazyHorse engine ignition with a Blackhawk Motorworks cone cover I needed to come up with a classic point cover for the new unit and the 5-Ball Factory Racer. It was a natural choice to send her a chunk of aluminum, or I shoulda sent a piece of brass, but oh well. Either way I knew she would bring the project to life.
Heather started engraving in a small shop in downtown Edmonton in the Early 80’s, where she took care of over 100 jewelry stores. “I was engraving everything from I.D. bracelets to wine goblets to pocket watches, and more,” said the raving redhead, “items which other engravers said could not be done, I soon learned to do!!! This was when I first met Frank.”
Frank Gurney was (and still is) the best Hand-Engraver in Canada. “He is a true artist and craftsman, and along with the Alberta Apprenticeship Program, arranged for me to be his understudy,” Heather said. “I was thrilled!!! I learned so much from Frank in those years, confidence, trouble-shooting, and above all HUMOR!!!! We spent hours working and laughing (hoy-deedle-doy!!). He taught me so many things before he eventually retired out near Victoria, B.C.”
She then moved on to the largest Jewelry stores in Canada. “I was doing all of their machine engraving, as well as custom wedding bands, and one-of-a-kind jewelry pieces,” Heather said. “They treated me like gold, and I will always be thankful for the kindness I experienced there. I relocated near Calgary, Alberta, and began working for a gigantic company with more talent than I had ever seen gathered in one place. I naturally did the engraving there, and also moved on to operating CNC machines, and hand-carving moulds used in casting.” She became a programmer, writing the programs, which would later be used by the CNC machines to cut the actual moulds.
She started New-Line Engraving in the summer of 2005. “I hand-carved an inspection cover for my good buddy ‘Chicken’ and with her over-whelming encouragement, (she cried when she saw it) I decided to branch out into custom bike carving too (after all, a derby cover is just like a signet ring, only BIGGER.”
So here’s how the short, two-week process rolled:
Cover the piece in white water-soluble paint, and transfer the artwork onto the surface
I highlight the general outline, scratching the paint leaves a more permanent mark than pencil, and you don’t rub it off as you work!
For removing large areas you can try a dermal, but they tend to vibrate too much for any fine work…I used small gravers hooked into a pin-vice to cut in between the letters,
as this cover was done mostly under a microscope.
I also use fine sandpaper, jeweler’s files, and burnishers to “round-off” curves (as seen on her legs), and give some dimension to whatever artwork you are dealing with…
Details like hair, the features in the face, and fine shading are all done with fine gravers and files.
I then add an aluminum-oxidizing agent, which blackens the entire piece. When it is re-polished, the highest surfaces will become shiny again, while the black remains in all the nooks and crannies of the background. (I only do this by hand—a buffing machine can remove hours of work in a heartbeat!!)
“If anyone out there in Cyberspace wants to give it a whirl, I am always here with support and tips,” said Heather
Sources:
NewLine Engraving: http://www.new-lineengraving.com/
Blackhawk Motorworks:
http://www.blackhawkmotorworks.com/
Compu-Fire Ignitions: http://www.compufire.com/
Custom Chrome:
S&S:
Sturgis Shovel Part 7
By Robin Technologies |
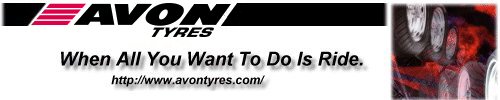
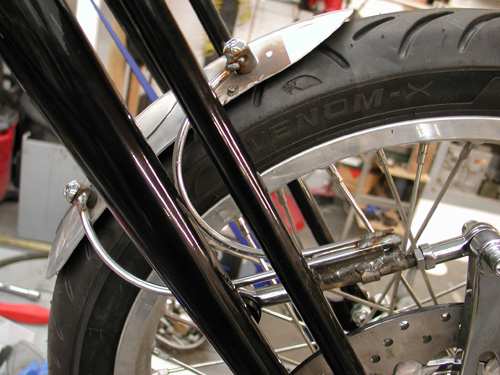
Brembo has a solid worldwide reputation, and I ran into a hot looking Brembo representative at an illustrious bike function and decide I’d give them a try. They’re hot and ready to rock. The only items I needed were the locking nuts for the back of the rotors bolts and the springer axle spacer. This set-up was designed for a stock springer replacement.
Because of the wild, light, taper-legged Paughco Springer my hiem joint link wasn’t long enough and I bastardized two fine bolts together temporarily. At that point I wasn’t considering a front fender. There are two aspects of chopperdom that I have a tough time working around. Bikes need front fenders and brakes. Can’t ride ‘em much without those two bastards. Even in the old days I ran front fenders, Avon Tyres and front brakes.
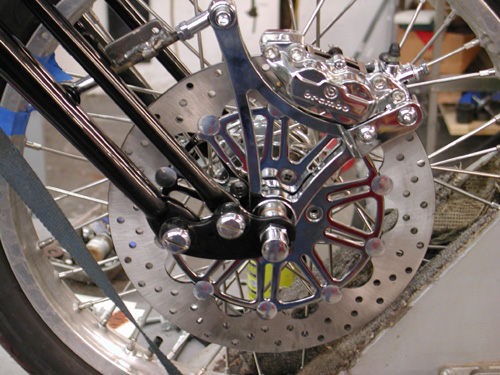
Chris Kallas came over at just the right moment. He’s as old at riding as I am and an artist. We’ve featured his work in special reports. He knows his bike shit and I’ve been trying to convince him to see Jim Murillo about a job. Jim has a paint shop in Torrance, but he’s not the graphics guy, Chris is.
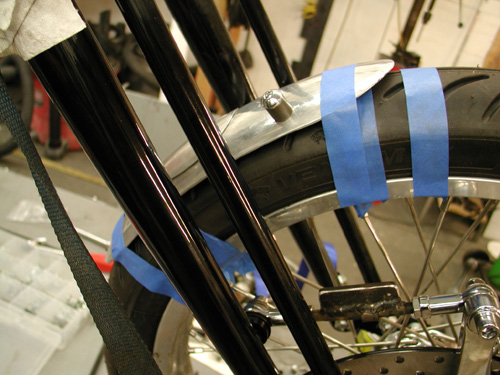
As usual, about the time I think it’s going to be easy, the devil pops up on my shoulder. Kent, from Lucky Devil Metal Works in Houston called, “What are you going to do about a front fender,” he said? “Yeah, that’s what I thought. I’ll send you some shots of my springer front fenders.” He hung up and Chris looked at me sorta strange.
”Who the hell was that,” he said?
”Never mind,” I said flipping my computer on. Kent developed a system of mounting springer front fenders that’s clean as a whistle and odd as only the devil would make it. An engineer wrote Bikernet when I first featured his wild notion and chewed us out. “That idea’s not worth the powder the blow it to hell,” he shouted.
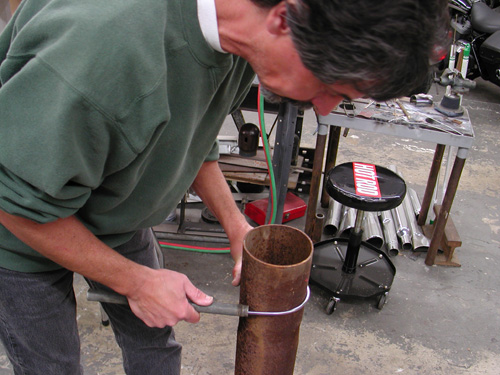
At first I thought he was correct, but the more I considered it, the more I determined that he was wrong. The caliper follows the line of the rotor, so the fender will follow the circumference of the Avon tire. Of course when I stepped into the ring to create a similar configuration I couldn’t do it like the Devil does. The Brembo caliper runs too far ahead of the rotor to mount the fender so we ran carefully designed struts off the brake linkage. Chris drew up the plan, then bent struts out of coat hanger for a guide.
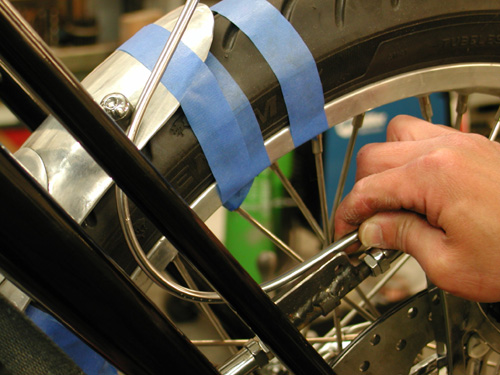
We constantly tried fitment again and again before tacking them into place. I wouldn’t recommend this configuration to anyone. If you run struts off the caliper they’re solid. The heim joints allow the fender to fluctuate, especially side to side. I had to find a concave washer that would allow the heim joints to work up and down but not side to side.
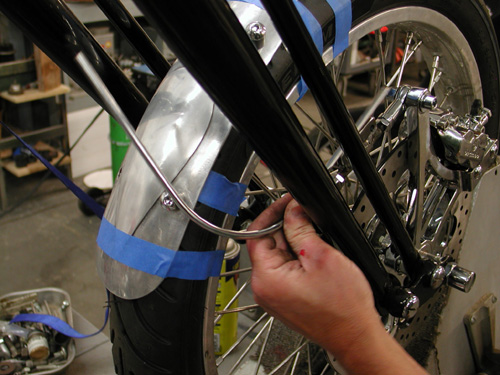
Chris bent each rail to match in pure artistic form. Then I tacked them.
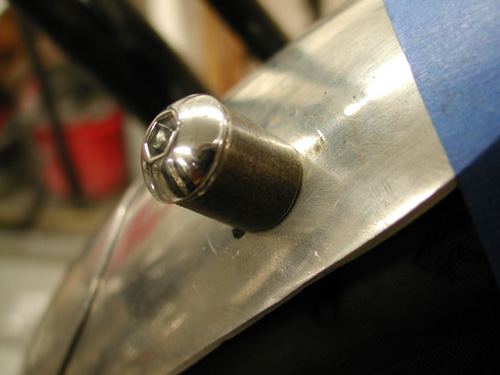
Kent built the front fender with threaded aluminum bungs underneath. I figured out some slender spacers to fit on top of the fender and tacked the rails to them. I must have welded them a dozen times trying to grab just enough rail, weld and spacer to prevent cracks.
There you have it. It’s wild, but will it last to the Badlands?
–Bandit
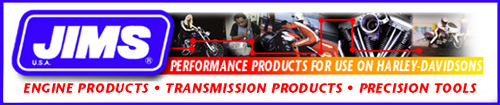
Sturgis Shovel Part 11
By Robin Technologies |
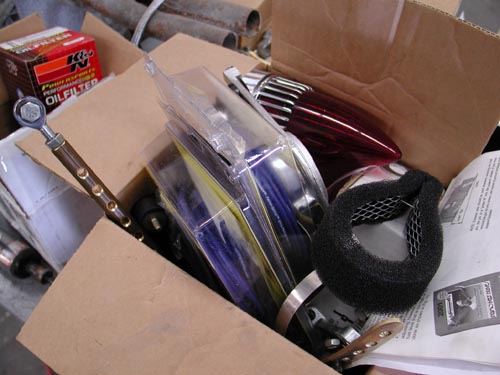
I’m not sure if I’m keeping everything in line. But this segment took us to Foremost Powder Coating in Gardena California. I was at that point when these shots were taken. I’ve had a Powder Coating Sponsor for years, Custom Powder Coating in Dallas. They’re good people and know how to handle custom work. They’ve handled jobs for Strokers Dallas, our custom for American Rider and even the 1928 Shovelhead for Bikernet.com.

Powder coating costs have dropped and it doesn’t make sense to ship a frame to Dallas. It would cost less to have it Powdered in LA than to pay for the shipping. So I looked around the area and was recommended to Foremost Powder Coating (877) We-Coat-it, 1608 W. 139th, Gardena, CA 90249. These people have their shit together and the girl who runs day-to-day operations, Esmeralda, is a delight on the eyes and to work with.
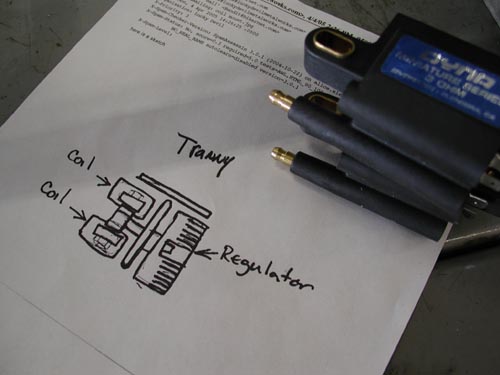
Let’s back up, though. Just before teardown for Powder I needed to think electrics. Kent from Lucky Devil Metal Works in Houston sent the above illustration for mounting the Compu-Fire voltage regulator under the tranny with the small Dyna Coils from Custom Chrome. I pondered that drawing and decided that I didn’t like the notion of putting my coils at ground level. What if I ran through a rain puddle? He’s built bikes using this technology several times and so has the guys at WCC, so it must work in most circumstances.
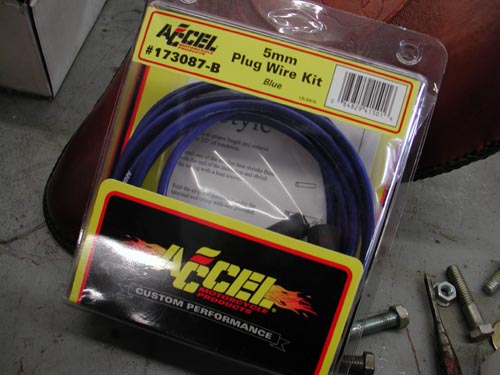
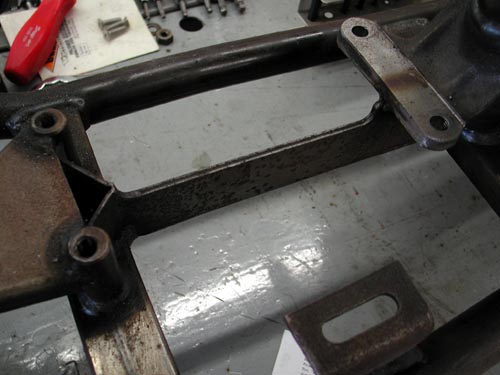
I decided that since I was going to run the Compu-Fire engine based electric starter that I had room under the oil bag for the coils. I still installed the sealed voltage regulator under the tranny on a 3/16 sheet of aluminum. But then welded brackets under the Craft Tech Oil bag to hold the two coils apart.
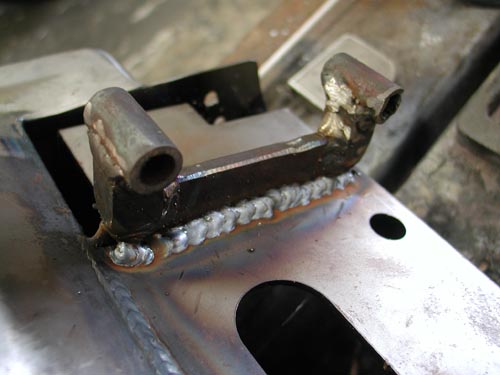
This was a delicate operation and ultimately the new Accell Sparkplug wires run right across the top of the RevTech Tranny. I also had just enough room behind the coils to house the wiring for the single-fire Compu-Fire ignition system. I thought through most every aspect of this motorcycle right up to the wiring business, then came up with a nuts notion, which I will explain during the final assembly process. It actually worked out fine with a handful of scary moments.
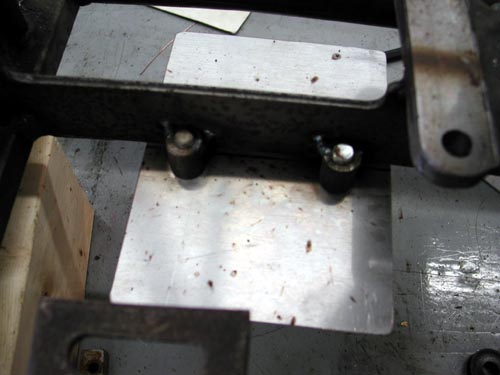
I welded four bungs that housed 3/8 fine threads to the frame with my Miller MIG welder. Ultimately I mounted the Compu-Fire voltage regulator to the pipe side (right) and it worked out fine.
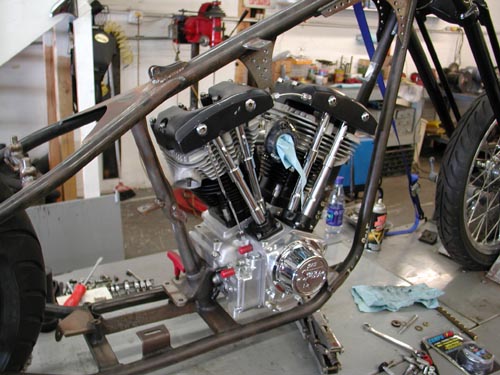
It was time to strip the Engine out of the frame, complete final welds, grind the welds and ship the parts to Foremost Powder. I needed to create a temporary engine stand to hold the S&S 93-inch Shovel in place. I used a RevTech engine stand and mounted it to a junk metal table leg. It worked perfectly and I shoved it in a corner for future use.
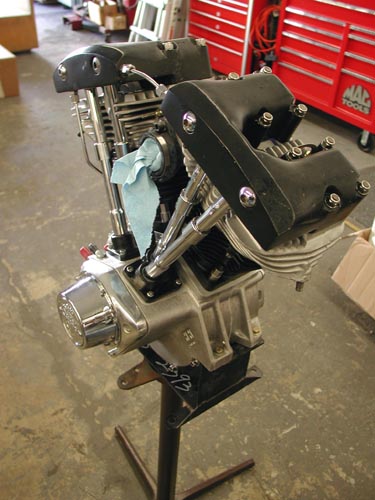
As I tore portions of the bike down I formed zip-lock bags with labels to hold the fasteners. You’d be surprised how fast you forget which spacer fit what, unless you organize. Mike Egan told me years ago that he takes photos of every part and organizes his assembly with photographs to demonstrate how components matched or were fastened. Since I try to take shots constantly I had an archive of various aspects. Hell, I just need to turn on Bikernet and look up the tech.
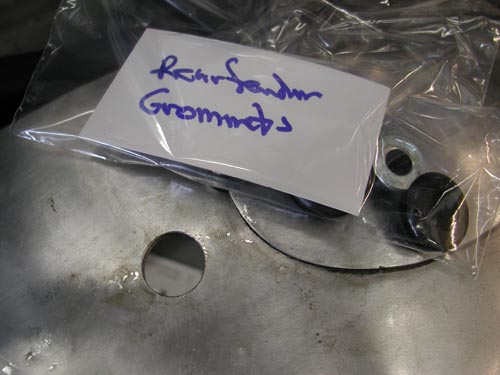
The next move was to finish welding any tab or bracket that had been tacked or partially welded. MIG welding is a breeze, but not as dead certain as TIG and I’m after a Lincoln TIG welder.
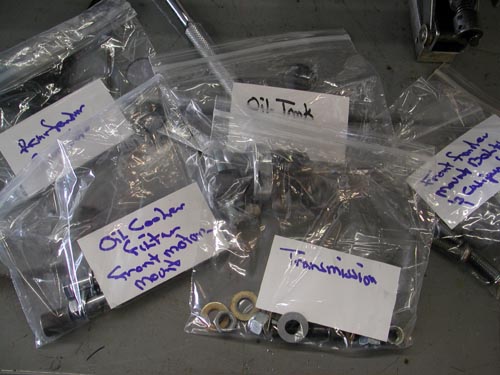
Here’s all the fasteners, grommets and spacers in bags with biz card labels. It works like a champ although I replaced some of these fasteners with stainless Allens wherever possible.
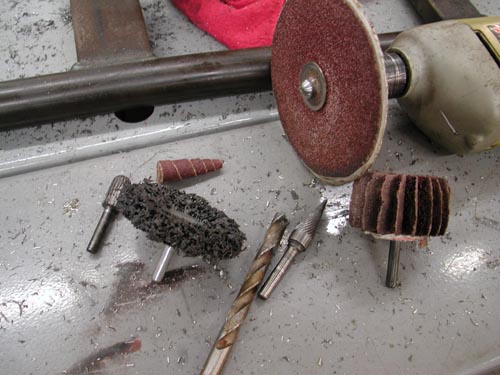
Next I dug out all my tools for grinding welds and went to work. This level takes a great deal of patience and artistic style, which I don’t have. The more time and patience, the better each weld will look. There is actually a process for bondo filling powder now, but it’s more costly. If you don’t want welds to show ask about it. If you don’t mind the look of a clean weld, just powder. I wanted the look of a machine, nothing slick.
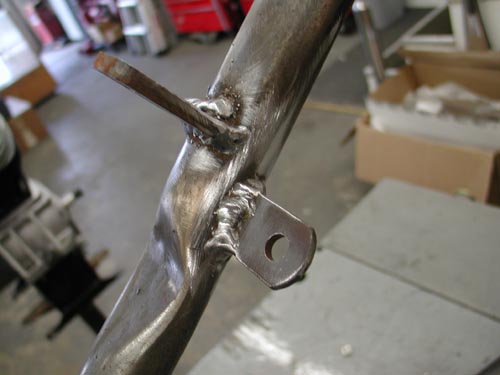
There’s one more consideration. Try to make each weld look the same as the next one for consistency. In my case that was tough. Some of my welds were decent, others sucked. I did my best, but my welds didn’t compete with the Paughco paid professional beads.
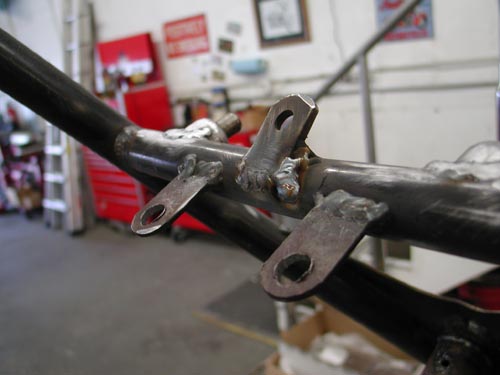
As I finished grinding and drilling holes in the frame for wiring I separated each group of powder finish parts and took a shot for the Powder guys at Foremost. It was a lifesaver to be able to hand them a shot of each group of parts since some had to be sand blasted before the finish was applied.
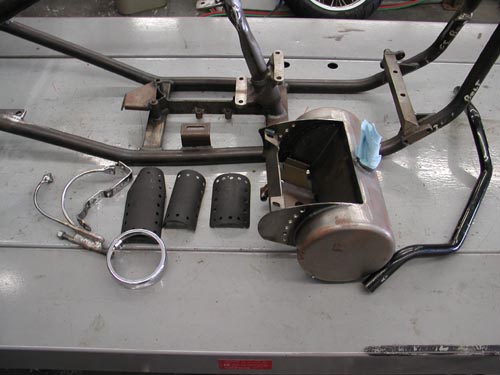
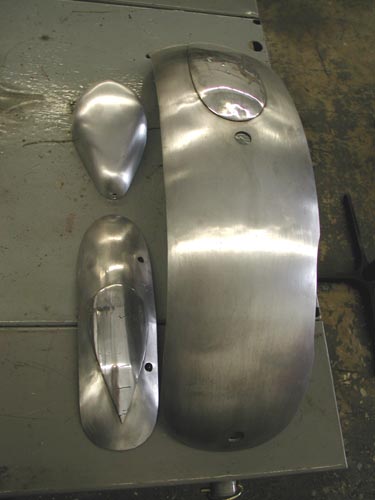
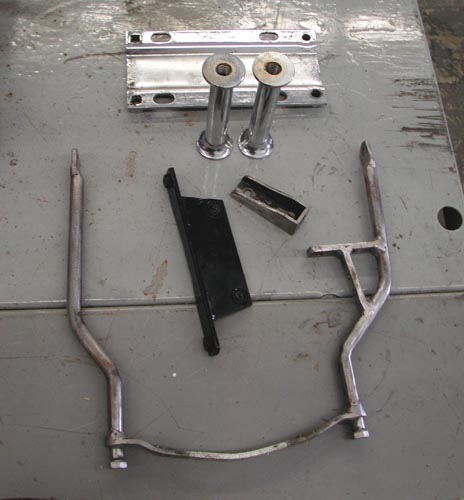
One more comment on drilling holes for wiring. This was one of the first times I drilled plenty of wiring holes. Remember Frank Kaisler’s rule? Drill the hole. Ream it out on a taper to prevent cutting your wires. Then with emery cones make sure there are no razor-sharp burrs in the tubing. Frank ran the emery paper then he’s twisted a Kleenex and shoved it in the hole. If it caught he’d sand the edges more. If not it was good to go. Let’s hit it to the next chapter, we’re burnin' daylight.

1928 Shovelhead Project Part III
By Robin Technologies |

The lovely Lena Fairless, who has threatened to marry Bandit (the sixth Mrs. Ball) and make him work for her folks at the Easyriders Dallas store, has been pushing to see that this 1928 Shovelhead project is completed in time for her wedding plans. Bandit doesn’t seem to move unless there’s a motorcycle and a woman involved. There’s just one problem in this case, which Lena is well aware of, she’s under age…
The other news on this project is that we now have a corporate sponsor, Ed Martin of Chrome Specialties, and a mentor, Chica, who builds bikes in Newport Beach, Calif. Chica built “Trick,” the old-time Sportster that Chrome Specialties is displaying at all the events it attends, such as Laughlin this month. Randy Simpson from Milwaukee Iron and Arlen Ness are also building spindly retro scoots with late-model drivelines. I spoke to Arlen the other day and he told me that a number of top builders in the country are building this style of beast for upcoming shows. Arlen is now building Sportster frames, sidecar frames and the tubs for these units. He’s sold 10 sets. Don Hotop is building aluminum tanks, so soon the parts for building these retro bikes will be even more available.
The contact stateside for the European parts we used is Fred Lange at (805) 937-4972. He has access to seats, fenders, front ends, tanks, headlights and more. Let’s see if we can pick up where we left off.

The frame is a stock rigid Panhead configuration from Paughco, with a stock, late-model Bad Boy front end. To drop the front slightly, Jim Stultz, Rick’s main fabricator/bike builder, used a KT components lowering kit to make the frame level because the newer springers are XA length. The retro tanks are sweat-brazed together and contain the oil in one half and the gas in the other. Unfortunately, the tanks did not fit the frame at all and had to be disassembled, cut and re-welded to fit. The fun part of such a round-the-town project is that it can be a true swap meet special once you have the basics in hand, and you can slip as far back into the retro world as you want. You can roll with chain or belt. You can use any old brakes you have around. Rick chose to use disc brakes and a chain, but he’s going with a jockey shift and internal throttle assembly from Chrome Specialties. The charging system will be state-of-the-art Compu-fire and the carburetor S&S. The engine and transmission were rebuilt from the ground up by JIMS machine and the engine cases are STD.
Both wheels are 21s for that spindly look. The handlebars were designed by Jim and bent by Milwaukee Iron. With the internal throttle cables, there will be a minimum of controls on the handlebars. Since the transmission was rebuilt with the notion that it would be electric start, an aluminum inner primary will be used with an old-time-looking tin outer primary that Rick picked up at a swap meet. Rick ordered a narrow Karata belt drive for the primary.
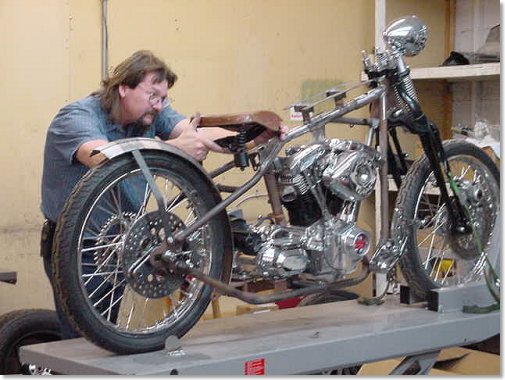
Jim sliced all the mounts off the frame except the front footpeg mounts, the engine and tranny mounts. Since the oil tank is part of the gas tanks, the only additional container would be for a battery to conceal a car-type marine ignition switch and a light/toggle switch.
“I try to fabricate components to be user friendly,” Jim said. He designed the battery box so it would only take two bolts out of the seat post and two out of the rear section and the whole pan will lift out through the top. The two sides covering the battery will meet in the middle in a flying wedge configuration, and Jim plans to build a top cap to conceal the battery from the area under the seat.
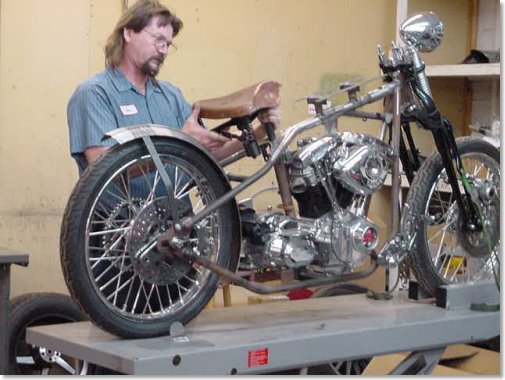
The steel gas tanks, once cleansed of the brass, were chopped and channeled to clear the rear head. The entire center of the tanks was removed to fit over the frame. Unfortunately that reduced the gas capacity to 1.5 gallons. The European threads in the cap bungs were tapped out of sync, so they had to be re-machined.
Lena teases Bandit with occasional shots from her mother’s digital camera. Next week we’ll discuss the mounting and installation of the Compu-fire ignition. Some members of the staff will be happy to see Bandit go to Texas, others, mostly the women, are bummed. He even called to see if he could ride it back to the coast and was told that it didn’t carry enough gas to get him out of town. Evidently the tank is Lena’s design.
–Wrench