Timbo’s ’64 FL Restoration (Part Five)
By Robin Technologies |
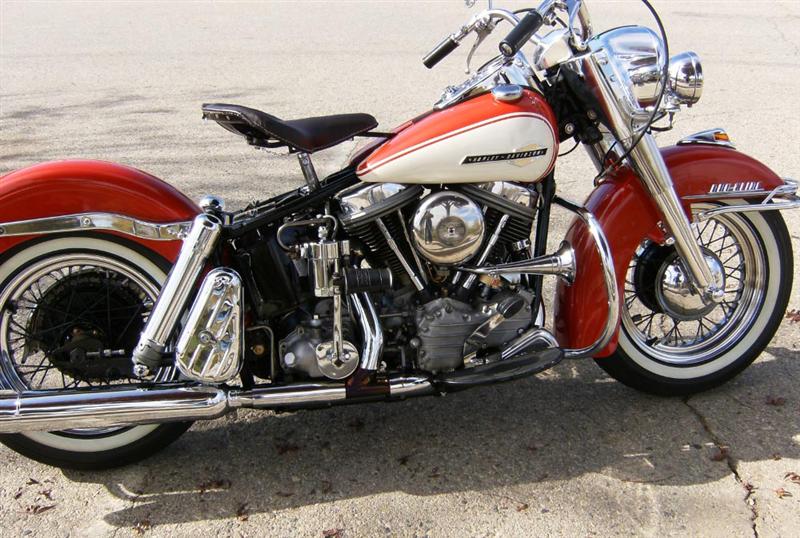
Well here she is, finally complete and out for her last shake down run. We stopped at a scenic area and shot a few pictures before I have to hand her over to the owner, Tim.
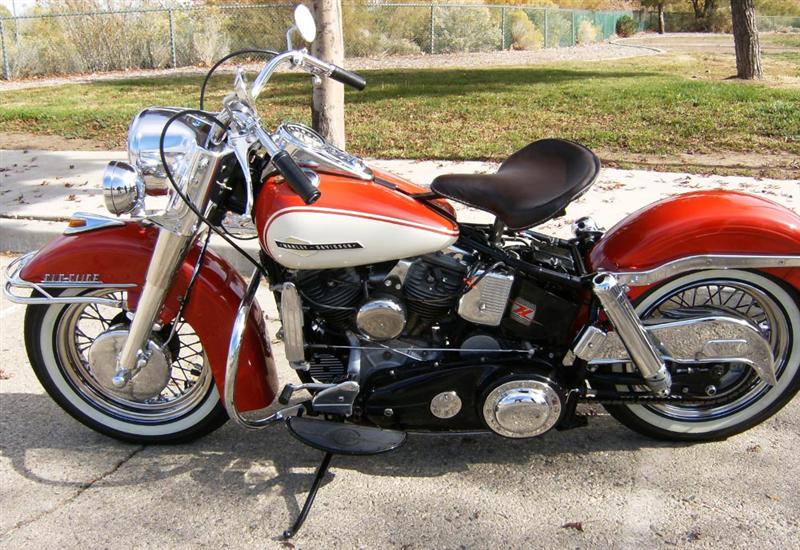
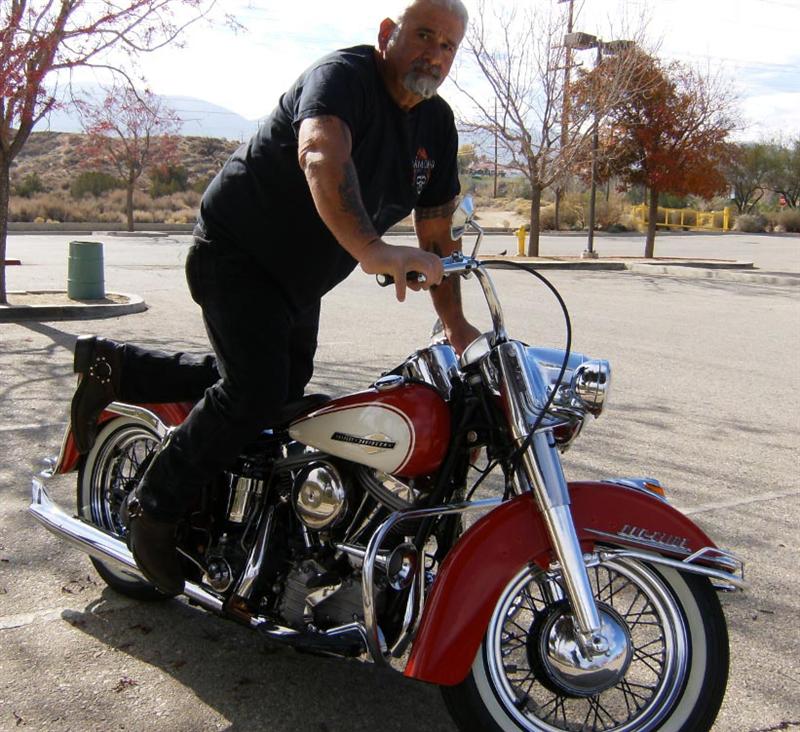
Riding the Pan is an art form in itself. The steering is spot on; it will turn on a dime! The suspension is wonderful for the age of the bike. It floats along better than most modern Harleys. The only thing I can’t get use to yet is the pogo seat, feels like it wants to buck you off sometimes.
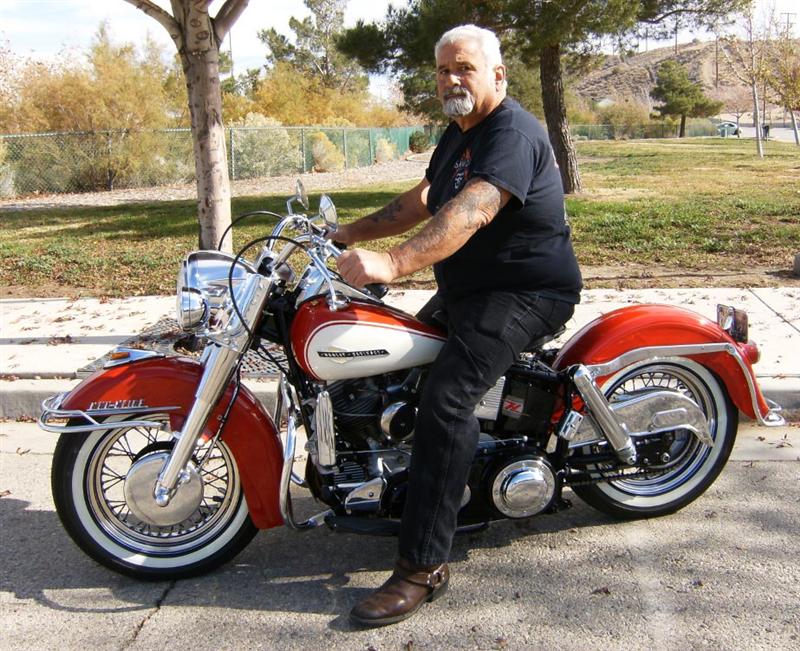
On the way back from our ride, I noticed a loud noise as I pulled to the stoplight. It’s Sal, yelling at me to slow down, YOUR DOING 85!!
If you followed the articles from the past year and a half, you know that hundreds of man-hours and a little mega money went into this restoration. And I loved every minute of it!
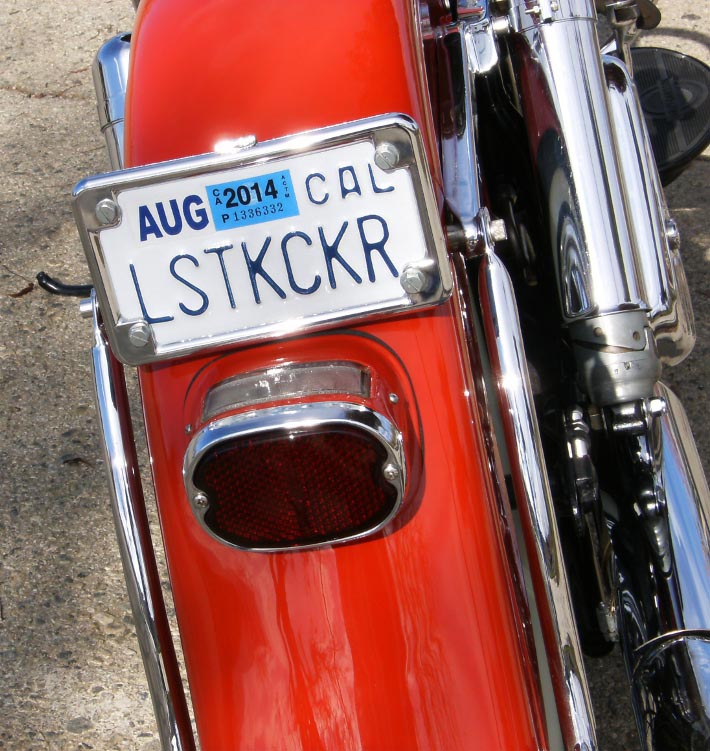
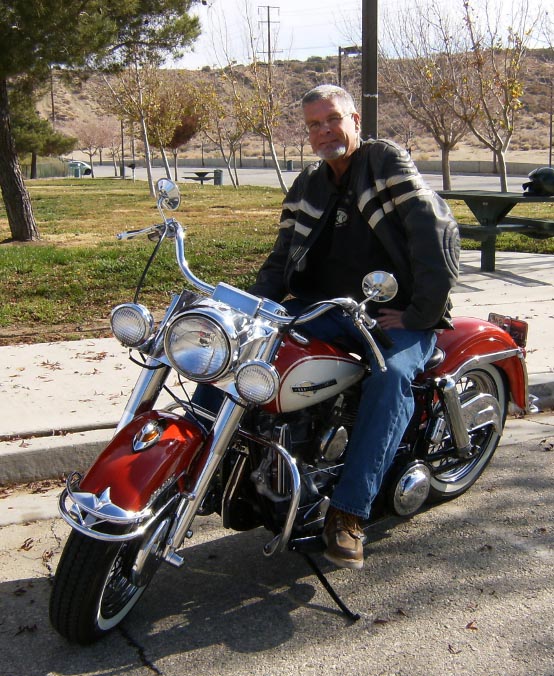
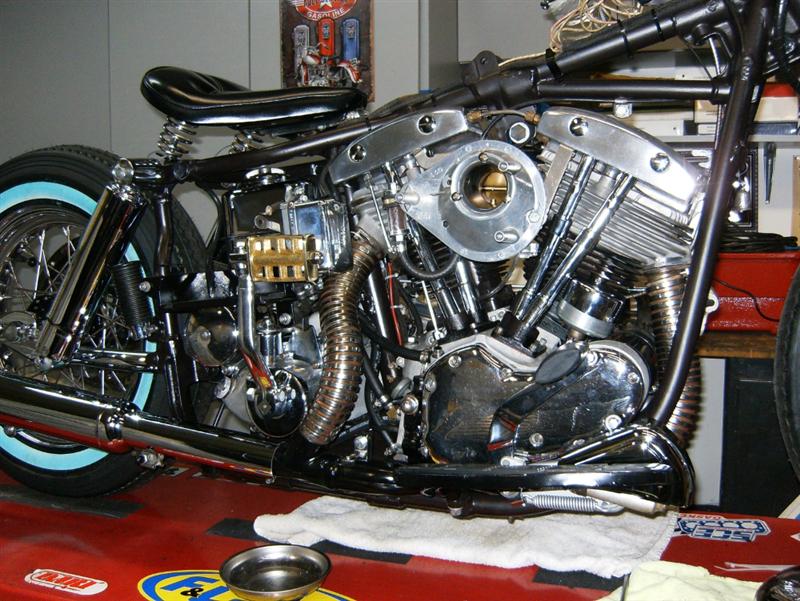
Doug Coffey’s RetroMod Panhead Part 3
By Robin Technologies |
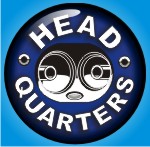
Bikernet Project: Widowmaker Charity Build, Part 4
By Robin Technologies |
I cannot stress enough to plan ahead.
The “Grip Ace” makes for a super clean and simple install without the dopey look of stock switch housings. If you are not familiar with this product, visit them at www.gripace.com. This product allows you to have all of your bike functions literally at your fingertips of your left hand. The system is compiled of a four button key pad that is installed on your left hand grip and a slim line module that can easily hidden almost anywhere on your bike.
The wiring is super simple. Once your left hand grip is fitted with the key pad, run your preformed wire and plug through your bars and plug into the module. All of your bike functions are wired to the module. The unit comes with clean and clear wiring instructions and easy to follow schematics. On our bike, we chose to keep the system super clean and mounted our key pad to the inside tunnel of the gas tank. As for the rest of your wiring, test each circuit as you assemble it. Try not to rely on butt connectors, solder as many of your wire connections as possible and keep in mind the serviceability of the bike. Make sure that future removal of the headlight and rear fender can be done by unplugging the wiring rather than cutting it.
Item Five: Last pieces of the puzzle, installation of the tins. This can be the most rewarding part of the job, seeing your new bike in all its glory or it can be a bad day and a trip back to the painter. Make sure you take your time in this installation. Make good choices of hardware. I personally like to use rubber washers on painted surfaces so as not damage the paint with the installation of the mounting hardware. Once everything is hooked up, top off your fluids and add only enough fuel to get the bike running. I suggest this in case there is a an issue of a gas leak or oil leak that may require you to remove the tank.
Once everything has checked out, get out and enjoy that first test ride. Make it short, come back, check everything over. Once all is good, pack up and enjoy your new ride.
Mudflap Girl FXRs, Part 10, Suspension Tuning and Le Pera Seat
By Robin Technologies |
Mudflap 8: http://www.bikernet.com/pages/Mudflap_Girl_FXRs_Part_8_Wiring_World.aspx
Mudflap 9: http://www.bikernet.com/pages/Mudflap_Girl_FXRs_Build_part_9.aspx
I’ve been riding and tuning Mudflap Girl FXR for a couple of months. We finally dialed in our rear shocks, maybe. David Zelma, from Progressive taught me the ropes regarding spring pressure and travel. We will get into that. We have also been monkeying with my Spitfire Girder shocks. Again, the problem is travel.
My son’s FXR faces similar dilemmas, but hopefully we will be able to transfer knowledge from my bike to his. Fortunately, Progressive suspension is just down the street in Orange County, so David Zelma stopped by with a variety of springs. “Your shock angle is more like a Dyna Glide than an FXR,” David said, “which makes for much more severe spring rates.”
I kept trying tougher and tougher FXR or touring H-D springs and the rate of sag was too much, indicating a too-soft spring. Also, I had to mess with additional bumpers, limiting the shock travel to prevent the fender from smacking the Avon tyre. It’s a humorous dilemma, one that any sport bike rider would scoff at, since he doesn’t care if there’s a foot of air between the rear tire and the fender.
Ultimately, we ended up with 12.5-inch Progressive Dyna shocks, but my travel, with limiters, is just over ¾ of an inch, sort of the same as a lowered Softail.
“I’m not happy with this system,” David said. “I want to see more travel for a comfortable ride.”
I like the way the bike looks, and I will ride it to Mammoth Lake next weekend to hook up with the Hamsters on their long road to Sturgis from the West Coast. That’s the iron test.
Next, I looked at the front Spitfire Girder shocks and discussed it with Rick Krost, who messes with bicycle seat shocks for custom applications. He removes the stock springs and switches them for cut springer springs. They were, unfortunately, too soft for the girders. Our problems with the seat shocks were two fold. The springs were 300-pound jobs and the shocks did very little to dampen the ride. So I went on a hunt. I discovered RockShox and Fox bicycle shocks, which run over $500 a piece. Good god!
Rick supplied me with a couple of RockShox with springs rated at 500 pounds per inch. Again that’s too tough, so I tried running one shock in a position more directly in line with the girder, another Rick suggestion. With one 300-pound rated spring I received good movement, but again very limited, like just over a ½ inch of travel. I’m still on the hunt for 2 inches of travel, and fortunately the Spitfire girder affords me the ability to mess with the positioning of a shock. I found a Fox shock that could be perfect, but the cost was prohibitive. RockShox also allows me a variety of spring rates, but of course I can’t find a price on their web site.
While on the girder shock hunt, we worked with Le Pera on a seat for my son’s Mudflap Girl FXR. Christine and Bob Le Pera took over their dad’s company when he passed. Christine picked my brain for styling, and then sent me a seat pan.
First, I made a bracket to catch the supplied tongue, welded under the seat. Before final welding, I may move the frame bracket back a ½-inch. Even with the tongue extended, I’m still not perfectly happy.
With the pan in place, we marked mods and adjustments with a felt pen and started hours of grinding and fitment. Then Ray C. Wheeler hacked-out an extension to afford my son enough seat for a passenger.
We cut a chunk of like thickness sheet metal and made a cardboard template, which was transferred to the sheet of tin and cut out with cut-off wheels. We could have made smooth work of it with a plasma cutter, but the grinding would burn the clock, and warping might become an issue.
We spent hours grinding, hammering and fitting until we thought we were close. I would love to find an English wheel and make the time to take a sheet metal class. Then we tacked the pan to our extension, and worked on it some more. I didn’t want to send it back to Le Pera’s historical shop looking like shit, so we worked over the pan extensively, and then drilled additional rivet holes to match the traditional pattern of Le Pera holes.
Le Pera is the home of the chopper seat, the cool, low, stylish, bare bones butt pads. “We can’t make ‘em fast enough,” Christine said. They have also shifted to more dresser seats, and seats for tall guys are popular.
This is their 40th anniversary in the seat-making business, and their focus for this year is new products, not parties. They constantly study new fabrics, threads, and embossed products. While in Italy at a dealer show, a customer approached Christine and told her, “Le Pera is the Ferrari of custom seats.”
When I spoke to Christine, my first question was regarding my seat pan. “How did we do?”
“You did a good job,” Christine said. “According to Bob, it was easy to cover.”
After they inspected our Bikernet shop handy work, she sent the pan out for powder coating. Then they installed a tough rubber edging molded over a metal insert. The metal grabs the pan securely, and the rubber clings securely to the metal. Together they protect the cover fabric.
While the pan is prepped for padding, the Le Pera liquid foam formula spilled into the standard Silhouette foam mold and was clamped into place while it cured.
Bob Le Pera, Christine’s brother, glued the foam figure of the seat to the pan and started hand-shaving the foam. “He’s the artist,” Christine said. Once shaped, the seat was ready for the fabric cover.
Bob chose a long-lasting comfortable fabric, but the master of seat patterns, Gus, a 32-year member of the team, laid out and customized the seat template, extending the standard Silhouette pattern, which he transferred to the resilient fabric, cut out the various pattern segments, and sewed the pieces together with upholstery-grade, ultraviolet-light-resistant bonded polyester thread. The color selection is vast.
Another long-term veteran member of the Le Pera team, Rick, with 27 years under his leather belt, completed the seat. He attached the stitched cover over the hand-shaped foam, made sure all the lines were symmetrical and tacked it in place with a couple of rivets, starting at the rear with a rivet gun.
With the completed seat in hand, Rick carefully glued a protective template of carpeting on the bottom.
I asked Christine about ordering custom seats from them, and they are open to a variety or requests. It’s often best to work with a knowledgeable dealer who can give you tips and knows how to speak the lingo to the Le Pera staff. You can always e-mail the staff and hit them up for info. Try to nail down a style before you reach out. Styles range from thin, low, and sleek, to touring, or tall guy seats. Check their catalog for ideas, and once you’ve nailed the basics down, you can discuss custom stitching, inlays, fabrics, leathers, and or embossing, and of course an affordable budget.
With the seat in hand and the Spitfire forward controls mounted and dialed it, Frank’s Mudflap Girl FXR is ready for a ride. He just needs a plate, registration, and insurance documents, and we will begin the Eddie Trotta break-in routine.
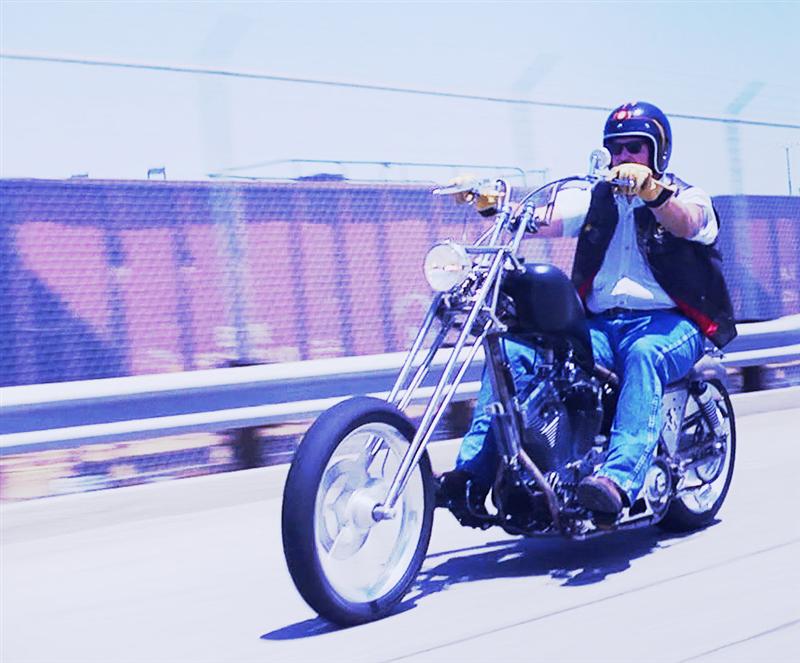
Le Pera Seats
D&D Exhaust
Biker’s Choice
JIMS Machine
MetalSport
BDL/GMA
Wire Plus
Branch O’Keefe
Bennett’s Performance
Custom Cycle Engineering
Saddlemen
Bub
Progressive Suspension
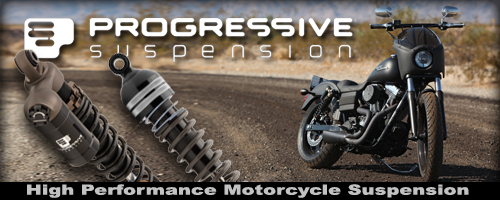
Check out my road test in the next chapter: http://www.bikernet.com/pages/Mudflap_Girl_FXRs_part_11_The_First_Road_Test.aspx
Bikernet/Cycle Source Sweeps Build Part 7 Sponsored by Xpress
By Robin Technologies |
Hang on. We are two weeks away from running out to Vegas for Bikefest and pulling the winner of this most magnificent custom motorcycle, specifically built for Bikernet and Cycle Source fans, readers, and subscribers. You need to sign up, if you haven’t, or come to the Cashman Center in Vegas to grab a card and sign up for the drawing. You don’t need to be on site to win. After Bikefest, the scooter will return to Kustoms Inc. near Detroit, for final tuning and break-in before being shipped to the winner.
So here’s the update in a flash, after Bonneville, and heading smack dab against a Cycle Source Deadline. “I’m way behind,” said Chris Callen, the esteemed Editor da Emperor, in Chief, in Charge, in Trouble. This year has turned into the scrambling year. We are scrambling to finish projects; builders are scrambling to finish bikes. Chris scrambles every month to finish a magazine. It’s bananas.
The bike was displayed in Sturgis at the Broken Spoke. Then it returned to Grand Ledge, Michigan, down the street from Ron Finch, for final manufacturing and paint by the master of Chop Docs, Ron Harris, but let’s finish the pieces first.
“I kill batteries no matter what I do,” Gary Maurer said as we started to discuss the battery box. “When I carefully rubber-mount the bastards, they vibrated enough to rip the battery cables to shreds.” So now he puts a small rubber lining under the battery and bolts the unit down hard with Jules-made steel battery straps. He is now using Brail and Ballistic batteries with some luck. This is where I started to learn more manufacturing processes from Gary and Jules, again.
It’s interesting. I don’t consider myself a builder, and when I work with someone with the manufacturing knowledge of the Kustoms Inc. team, I know I’m just an enthusiast, not anywhere near a pro builder. This story contains a couple of fine examples of their expertise. The battery straps are easily bent after marking the position for the bend on the top corner edge of the battery. Jules made the hand bend with a solid bar of steel, and then noted the amount of metal used in the radius and worked it into the formula for the next bend so the strap fit the battery perfectly.
“There is a mathematical formula for this process,” Gary said. “You need to add or subtract material from the next bend, but we bend one side and then adjust the other.”
I also noted how perfectly the fender edge fit the line of the tire, since most fenders do not align with the tire radius. “We often scribe the radius of the tire on the fender and cut it to match perfectly,” Gary said.
He uses thick welder ground cable stock taped to the fender to give him the proper fender clearance. “Sometimes we use chunks of busted rear drive belts,” Gary said. “Sometimes, if need be, we can double the belt, or mesh the teeth for a slightly larger space.”
They break the chain to be as close to the center of the adjustment path as possible, with the engine, primary and transmission in place. Then they adjust the chain to be bowstring tight, and then they tape the spacing material to the tire and start mounting the fender.
This Bare Knuckles fender was bobbed and channeled on both sides by Jules. She often cuts with a plasma cutter, and then works the edge with Matabo grinder with flap wheels. Bare Knuckle fenders are made with solid, thick spun steel. They are as strong as a battleship hull and easy to work with. “Our plasma was toast,” Gary said, “so she used a high-speed cut-off wheel, then the Matabo and flap wheels.
I like the exhaust system he built with D&D components and a carbon fiber muffler. I asked how he held the components accurately together for tacking. “I start generally, but not always, with the muffler in place and move forward,” Gary said. “I hold the chunks in place with three fingers and tack them.” If his weld pulls away from the joint, he adds a small ball of rod to one piece, then holds them together, and heats the ball until it flows to the other tubing piece.
Note how Jules fashioned the lower fender mount to the frame so it acted as a battery strap mount and fender mount.
Then Gary built the sissy bar by hand-bending the steel rod. He machined each chunk of bar stock for the frame rails, and drilled them ½-inch so the rail would simply insert into the welded boss. Then he drilled and tapped them for setscrews. On the top, he welded a machined bung to the bar, and a drilled and tapped the bung to the fender, so the fastener simply slips through the sissy bar tab and screws into the solid bung on the fender.
With all the components tested and brushed with flapper wheels, Ron Finch stopped by and picked up the components for the trip to Ron Harris, a third generation paint and body shop guy. “I couldn’t touch a paint gun until I could bump a fender,” Ron said of his granddad. Back in the day, bodywork was hammered and filled with brazing and lead.
“My dad called Bondo Chinese lead,” Ron said. Then he ran down the Chop Docs custom paint process. From the photos, paintwork slides along like ironing an old pair of Levis (who the hell does that anymore?), but any top-notch painter has the talents of a concert violinist. It may look easy, but there’s a refined eye and level of perfection that turns any steel surface into a perfectly smooth piece of art.
As soon as Ron Finch dropped off the components and peeled out, Ron Harris cleaned the welds with a cookie wheel, and then scuffed all the surfaces with 80-grit for a world-class bonded protective coating. Initially, paint was used solely to protect a surface. Now it protects and adds the final illustrious finish.
Then he coated all the sheet metal surfaces with a filler Bondo skin coat and block-sanded the surfaces. This is where perfection and talent come into play. I’ve been there. I couldn’t Bondo a baby moon hubcap and make it look like new. There’s an eye for sanding just the right level of Bondo to capture the perfect slick surface.
He followed the Bondo coating with a skim coat of putty to capture imperfections, and then tested his eyes with various levels of Emory paper from 80-grit, to 150, to 320, so he can minimize his primer usage.
“I’ve been working with Stage 5 Coatings for two years,” Ron said.
Stage 5 Coatings was established in 2008 and is the newest and one of the fastest growing coatings suppliers in the United States. We are committed to selling jobber direct and establishing an exclusive territory for anyone that carries our lines. We strive to offer the best values available in the market. We are a small company that is personal and ethical. We build a personal working relationship with every customer, whether they are our largest or smallest. We believe when a customer buys from us, a partnership is formed, and is not just another customer. We have the industry experience to put ourselves in your shoes and understand the everyday struggles in the body shop business. From us to the jobber to manufacturing, we have the personal hands-on experience in all areas of the aftermarket coatings industry.
States with Stage 5 or Technico:
Michigan New York
Illinois Missouri
Texas Oklahoma
Wisconsin Oregon
California Arizona
Washington Georgia
Maryland Caribbean
Virginia
Ron is working with Ken Dudley on a line of Chop Docs candies. After he primed all the surfaces, he used a black spray bomb dusting to cause imperfections to surface. After any pits or surface maladies were dealt with, he water-sanded everything with 400 grit wet and dry, and then hand-sanded with 600 grit and finished off with Scotchbrite.
With the components hung in a booth, he primed them with two coats of sealer, and then hit them with the silver base coat and inner clear before taping off for the black pearl inlay. Then everything was cleared again and sanded with 600-grit.
This was Ron’s first attempt with green variegated leaf* using Mona Lisa glue to attach it to the paint surface. “It’s like a very thin, watered-down Elmer’s glue,” Ron said. “The leaf is so thin, it’s like dust in your hands.”
Once the leaf was glued into place and the area cleaned with a cotton ball or a brush, Ron hit it with another coat of inner clear, which locks the base down and leaves sort of a satin surface to adhere any art to, such as pin striping by John Harrow, who used a one-shot enamel sign paint called Kansas City Teal.
Now for the final six layers of gloss clear coats and 1500 grit wet sanding, followed by 3000 grit with water, and then buffing with polishing compound, finishing glaze, and spit shine. It’s Saturday, and by Monday, all the elements will be returned to Gary and Jules and Kustoms Inc. for final assembly. Ron volunteered to help. Unfortunately, he’s 140 miles away, but he drove out and spent all day, Sunday, helping with assembly. “It’s 80 percent there,” Ron said on his way home.
Speaking of volunteer efforts, this has been an amazing build with efforts from a variety of sources, all to create a bike we are giving away. No one made a dime off this puppy. It’s all American-made, and the whole gang pulled together to offer Bikernet and Cycle Source readers a shot at a world-class custom motorcycle—thanks. Chance of a lifetime, goddammit.
Dimensions: 5½” x 5½”
Xpress
http://mysmartcup.com/
Crazy Horse
http://www.crazyhorsemotorcycles.com/
Texas Bike Works
www.TexasBikeWorks.com
Kustoms Inc.
KustomsInc@hotmail.com
Chop Docs
www.Chopdocschoppers.com
3 Guyz
www.3Guyz.com
Accel
Accel-ignition.com
Fab Kevin
http://www.fabkevin.com/home.htm
Evil Engineering
www.evil-engineering.com
D&D Exhaust
http://www.danddexhaust.com/
Wire Plus
http://www.wire-plus.com/
Barnett
Barnettclutches.com
Rocking K Custom Leathers
howard.knight@montana.com
Rivera Primo
www.RiveraPrimoInc.com
Spectro Oils
www.Spectro-oils.com
Bell
www.moto@rcn.com
Metzeler Tires
www.metzelermoto.com
Hawg Halters
Handy Industries
www.HandyIndustries.com
Grip Ace
www.gripace.com
Biker’s Choice
www.bikerschoice.com
Aeromach
www.aeromachmfg.com
Ride Wright Wheels
www.ridewrightwheels.com
Biker Pros
www.BikerPros.com
Bare Knuckle Choppers
www.bareknucklechoppers.com
Doug Coffey’s RetroMod Panhead Part 2
By Robin Technologies |
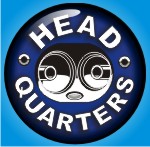
Bennett’s Performance 2004 Dyna Build 106-Incher
By Robin Technologies |
Eric Bennett grabbed the shop door chain and hoisted the roll up door for the first time, in 2000. He started his mechanical career as a certified diesel mechanic with 60-weight always flowing through his blood stream. Finally, he gave into his entrepreneurial spirit and his desire to make motorcycles his life—he opened his own shop on Signal Hill. The rest is motorcycle history, much of it spent at the Bonneville Salt Flats with his dad, Bob.
He recently owned a modified twin cam FLH, but a customer made him a deal he couldn’t refuse, so he let it go. Then a deal on a Dyna surfaced and he made a quick move to snatch it. This time, he decided he would take it to the concrete and rebuild every aspect of the bike to be moderately fast, ultimately reliable, precise, and built with absolutely all the best mechanical intentions and components in mind. You get to see the 106-inch project unfold before your very eyes right here.
One of the benefits of running a service center in the largest city in Los Angeles County includes encountering every possible mechanical malady and the ability to research whatever solution might be necessary. Since LA is also the motorcycle media hub, he has constant opportunities to test anything new on the market. After working on Twin Cams since their introduction into the market in 1998, Eric has watched every configuration, modification, performance recipe, and model roll in and out of his shop.
With this build he could pour every lesson and improvement into his own ride. It started as a bone stock 2004, 88 cubic inch TwinCam. Eric could choose from any hot rod configuration in the world, but he chose to roll with a 106-inch kit from S&S and Branch re-tuned heads. He started the process by installing a JIMS Timken conversion into his left case and welding his crankpin into the S&S lower end after it was balanced.
“With superior S&S flywheels, I didn’t need to monkey with the cases,” Eric said.
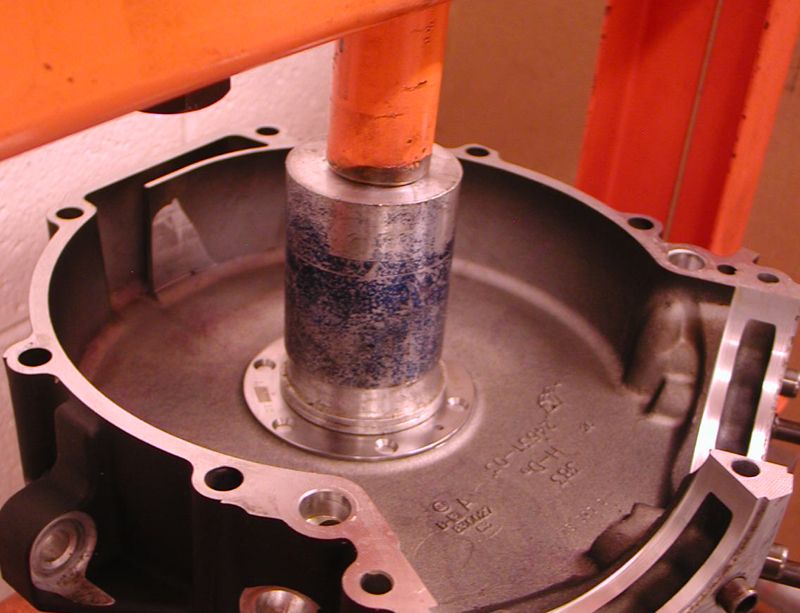
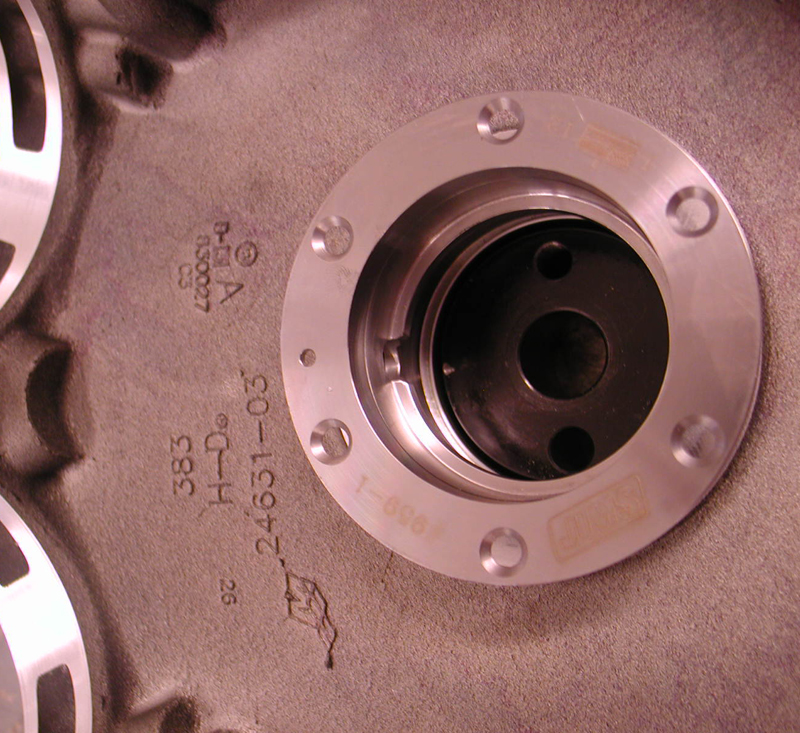
He bored the stock barrels from 3 ¾ to 3 7/8 inches and increased his stroke from 4 inches to 4.5. With JIMS tools he pressed in the JIMS race (using green Loctite) (9-59-1) while keeping his fixture perfectly flat and the hole in the race at 12 o’clock.
Using a JIMS fixture tool, he was able to drill guide holes in the case for Timken bearing and race oiling. The JIMS tool holds the drill and guides it. The drills are set to indicate the depth. Otherwise, he would need to use transfer punches and a milling machine. Then he used another JIMS tool to drill for the race fastener holes, and used tap guides to prevent misalignment.
“I’ve made tap guides for every size tap,” Eric said.
One of the benefits of the higher quality Timken lower end bearings is their ability to lock the lower-end into place.
“I have never seen a Timken bearing fail,” Eric said. Until recently Timken’s were used since 1957. “I’ve seen dozens of roller bearing failures!”
The cost saving shift to roller bearings started in 2003 during the 100th anniversary season. “The best Twin Cams were built in 2002,” Eric confirmed. “Better engines, still carbureted and with 1-inch axles for strength and stability.”
Eric used red Loctite on the race screws. He uses a tool for installing both Timken races at the same time. Kelly McKernnan, an amazing machinist out of Portland, Oregon, manufactured it.
The next phase included welding the S&S flywheels. Anytime Eric has a twin cam lower end out of a customer’s bike, he welds the crankpin in place with stainless TIG rod. It doesn’t create much heat and is not a structural weld; it just cements alignment and prevents shifting. He always checks the true after welding.
Next, he installed the Timken bearing by heating the race to expand it, and it slippped over the shaft easily. There is very little endplay in the shaft, just .001-.002-inch. Eric cinched down the top bearing with another JIMS tool, then pressed in the main seal and spacer with yet another JIMS tool.
At this point, we shifted to pressing the new S&S cam bearings into the new heavy-duty Screamin’ Eagle cam plate for hydraulic cam tensioners, but Eric chose to shift to an S&S gear drive system, so he blocked off the oil passages to the hydraulics.

He installed Torrington cam bearings in the right case prior to installing the new cams. His plan called for installing a D&D Bob Cat exhaust system, which is 20 pounds lighter than a stock exhaust. D&D pipes come bolted together with all spring clips, flanges, and heat shields in place. “They take like two minutes to install,” Eric said.
“It’s the easiest system I have ever installed,” Eric said. “It comes with the all the components needed and the heat shields in place. No shimming is necessary or egg shaping holes.”
Day 2
We took a break for the day and grabbed a beer. But the next day, Eric installed a heavy duty Harley-Davidson pinion shaft bearing kit using a JIMS pinion bearing tool and it was time to slip the cases together with Yamabond on the case edge, while applying assembly lube on the pinion shaft. The case bolts were torqued to 18-22 ft. lb.
“Don’t forget the new oil pump O-ring when installing the high flow H-D pump,” Eric pointed out. Eric has an engine-building quirk. He continually turns the engine over, while rolling through the build process, and constantly tests for changes. “I want to catch anything that might bind early on,” Eric said. We actually ran into a small glitch while installing the cam plate.
But first, he installed the oil pump return gears, and then the separation washer and the spring, before the feed gear. He bolted the cam plate in place with ¼ -20 fasteners torqued to 120-inch- pounds. He used guide pins to help align the oil pump, and turned the engine over while tightening the pump so it would seat itself properly. He tightened two oil pump bolts, then removed the guide pins, and then tightened the other two Allens.
While aligning the cam drive gear dots, he installed the cams and used red Loctite on the drive gear Allen bolts, but used assembly lube on the washer for more accurate torque values and to prevent the bolt from galling against the washer surface for a false torque reading.
As we wrapped up the operation for the day, Eric installed the lifter with the oil holes facing the cam cover, then the guide pins, caskets and covers. No more lifter stools.
Day 3
Eric sub-leased a portion of his Signal Hill building to Branch O’Keefe, perhaps the best head porting business in California. I don’t want to put down any performance heads, but Jerry Branch, who is now about 82, built a helluva business around head performance.
Here’s a description of their heads from the Branch-O’Keefe site:
This is where is all began. Branch-O’Keefe is known throughout the industry for legendary cylinder head modification service. Our extensive reworking of stock Harley-Davidson cylinder heads begins with removal of the stock valve seats and guides. Next, the combustion chambers are heliarc welded to add additional aluminum alloy in the combustion chamber and around the valve seats for re-machining.
The valve seat pockets are then machined for larger nickel-chrome valve seats, and the combustion chamber is cut from the stock low compression rectangular shape to the legendary Branch “bathtub” chamber. After cutting the combustion chamber, new oversize valve seats and performance-quality valve guides are installed to tighter than stock tolerances.
The heads then advance to the porting room where the ports are fully hand-ported, blended and polished to Branch’s exacting specifications as proven on the dyno and flow bench. The head’s gasket surface is machined an additional 0.050-inch, which raises compression slightly. Finishing up, new oversize intake and exhaust valves (hard chrome stainless steel with stellite tips, polished face) are installed in bigger seats with a machined race-quality valve job and then hand-lapped. New seals and a high quality high-lift radius spring kit complete the installation.
The Branch O’Keefe head components are damn impressive from the titanium upper collars to the single oval wire spring with more travel and a larger diameter spring material. They have developed heads for JIMS big inch motors that produce 132 horsepower and ft-lb of torque, at an absolutely stock reliability level, even on a B motor. So natch, Eric had John O’Keefe and his master right-hand man, Paul go through his heads. Actually they used a formula they call the Dave Thew head. It’s a nickname for a performance formula. Dave beat everyone with these Branch O’Keefe head configuration. I will outline the different formulas next week.
We started the day installing S&S pistons with wrist pins first, since the oil rings pass over the wrist pin holes. Seems odd, but it’s the nature of the short-skirted piston. “Actually it allows for more skirt on stroker motors and does away with stroker plates,” Eric said. “This piston configuration will keep a stroker running longer.” The oil ring must be positioned with the dimple in the wrist pin area in a particular location to prevent rotation. The S&S pistons use four-piece oil rings with a removable ring land.
Eric installed the bottom compression ring so that the opening faced the exhaust port area. “No gaskets are used on the bottom of the cylinders,” Eric said, “just O-rings.” He compressed the rings carefully, lubed the inside of the freshly bored cylinder and slid the cylinder into place. Then Eric spun the motor over to check for binding. “I can’t wait to hear the D&D pipe.”
Eric started to install the heads using Cometic gaskets. The heads were torqued to Cometic specs and then he set to installing the rocker boxes and the fasteners, which were torqued to 22 foot-pounds. He started from the inside and worked out. Then he slipped in the S&S Quickee-Install intake pushrods for maximum valve opening. “I run premium S&S lifters with travel limiters,” Eric said. “They become solids at high RPMs.”
He tightened each pushrod until the valve slipped off the seat, and then let it bleed down, for about 10 minutes. He backed off the adjustment until he could spin each pushrod (one at a time). Then he backed off just one complete turn or six flats.
These shots were taken before John O’Keefe came up with a crazy notion to machine Twin Cam cylinder fins in a round configuration. Eric was knocked out by the procedure and pulled his barrels for the process.
In the next episode, Eric will slip the beautiful 106-inch Twin Cam into the stock frame, and we will discuss JIMS tools, while replacing the inner primary bearings, the slightly modified Dyna D&D pipe, and then and the new Rivera Primo clutch, the S&S G carb, and a new S&S high flow air cleaners.
Sources:
Bennett’s Performance
S&S
JIMS
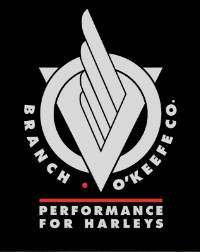
Bikernet/Cycle Source Sweeps Build Part 4 Sponsored by Xpress
By Robin Technologies |
This segment will demonstrate again the level of quality craftsmanship and passion for our industry guiding this magnificent motorcycle project. We have some fun with these articles, but the level of talent and engineering directed at this motorcycle is impressive. Take for instance this Crazy horse engine from John White’s factory in Kent, Washington.
American Piledriving Equipment (APE) is the number one provider in research and development, production and sales of foundation construction equipment. APE has branch offices in Asia, Europe and every corner of the United States. But a big part of this man’s heart has been devoted to keeping the Indian heritage alive. When the Gilroy Indian factory stumbled in 2005 he purchased the remaining bottle cap Indian engines from the defunct facility. He began to study and refine this sharp looking air-cooled 45-degree V-twin.
Crazy Horse Motorcycles LLC, based in Kent, Washington, is the manufacturer of the “V-Plus” V-Twin motorcycle engine. They are an OEM supplier of this engine to individuals and custom bike builders. Each engine is proudly made in America with American components. They are basically built around the Evo platform and will fit any Evo model. The only quirky aspect is the carburetor facing out the left side of the engine, which I like, and it creates no obstruction for the rider of any bike with fatbob tanks; otherwise it is a minor consideration. Any Evo exhaust system will fit the Crazy Horse format.
“Our goal is to provide a distinctive, powerful, and reliable V-Twin American made engine. By using superior grade components and craftsmanship, along with a generous warranty, we intend to be considered among the best engine manufacturers in the industry,” said John White, the boss.
Paul Jr. Designs has recently teamed up with Microsoft to produce a unique configuration for Paul, a Trike! It is a very exciting design inspired by the new game, Gears of War. The bike features a Crazy Horse Motorcycle Bottlecap V-Plus engine, which Paul has been using for many of his more recent projects.
John secured the rights to build these unique engines, enhanced the oiling system, the cylinder cooling capabilities, and they even purchased Ramsden foundry castings, which are semi-permanent steel tooling, so even the cases are no-longer sand-casted. In fact, this 100-inch V-Plus addresses some of the problems when pushing the size of standard Evo engines, with heavier cases and barrel material for stronger head bolt connections, so this 100-inch configuration based around 3 5/8-inch bore and 4 ¼ stroke is built to last with 9.5:1 compression from Keith Black hypereutectic pistons.
The original Gilroy oil pump was an external bypass pump, which had a problem feeding excessive oil. Then they shifted to an internal bypass oiling system, which also failed. Crazy Horse ditched the old bypass pump and replaced it with a True Internal Bypass (TIB) oil pump. It reduced internal engine oil foaming and did away with all the old oiling issues.
This engine affords builders the use of any conventional Evo ignition system, including Compu-Fire, Crane Hi-4, or Daytona Twin-tec systems, you name it. The need to correct the carb mounting came up in a discussion in a dark alley behind Bandit’s Cantina. There was a drunken vote for moving it to the conventional right-hand position, but I disagreed and have a lump over my left eye to prove it. I like the unique aspects of the left-hand carb, and the fact that it doesn’t leave the left side bare. Plus, it’s classic, goddammit. I’ll fight for it again.
This is now a complete world-class unique 100-inch engine platform used by Paul Jr. on many of his projects, on Brass Balls Bobbers, and by custom builders over the globe. The components are all the finest available including JIMS sprocket shafts, and all the engines are assembled with JIMS special tools, as the lower end run-out is trued to .0001 tolerance. Can’t get much better.
Crazy Horse Motorcycles “V-Plus 100” engine
All brand new components,
NOT A REBUILD
Durable and reliable
Hand assembled
True Internal Bypass oil pump (T.I.B.) superior to other “improved” pumps
Viewable timing marks
Premium aerospace quality gaskets and fasteners
Standard Big Twin mounting points, fits most frames with minimal fuss
Available either carbureted or fuel injected
Several styles of ignition triggers available including conventional cone-type
Optional Retro-Gray color scheme
Left side intake
Either a Mikuni 42mm or an S&S Super E carburetor can be installed. The latter requires removal of the rubber flange adapter and enlarging the two bolt holes.
Every Crazy Horse engine is test-run on their engine stand through several heat cycles, and checked for potential leaking problems. Gary and Julie received the Crazy Horse engine in a proprietary molded heavy plastic, high-security engine shipping case, perhaps the most secure engine shipping device I’ve ever seen. No worries.
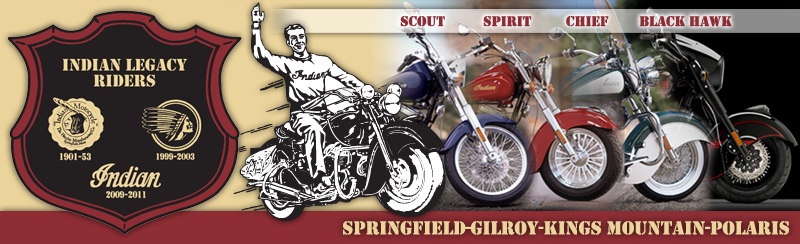
This website constantly collects data on all Indian motorcycles. This data is then titled and posted in the appropriate section for the benefit of all riders. John welcomes any data you wish to contribute.
Check the roller. In the next episode we will start the sheet metal fabrication process by cutting up a set of Biker’s Choice fat bob tanks. You’ll begin to see the true talents of the Kustoms Inc. fabricating and body work team. Hang on and don’t forget to enter to win this puppy. The odds are terrific. Hell, you only go around once.
–Bandit
BIKERNET/CYCLE SOURCE BUILD SOURCES
Xpress
http://mysmartcup.com/
Crazy Horse
http://www.crazyhorsemotorcycles.com/
Texas Bike Works
www.TexasBikeWorks.com
Kustoms Inc.
KustomsInc@hotmail.com
Chop Docs
www.Chopdocschoppers.com
3 Guyz
www.3Guyz.com
Accel
Accel-ignition.com
Fab Kevin
D&D Exhaust
http://www.danddexhaust.com/
Wire Plus
Barnett
Barnettclutches.com
Rocking K Custom Leathers
howard.knight@montana.com
Rivera Primo
www.RiveraPrimoInc.com
Spectro Oils
www.Spectro-oils.com
Bell
www.moto@rcn.com
Metzeler Tires
www.metzelermoto.com
Hawg Halters
www.HawgHalters.com
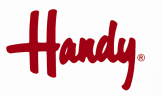
Handy Industries
www.HandyIndustries.com
Grip Ace
www.gripace.com
Biker’s Choice
www.bikerschoice.com
Aeromach
www.aeromachmfg.com
Ride Wright Wheels
www.ridewrightwheels.com
Biker Pros
www.BikerPros.com
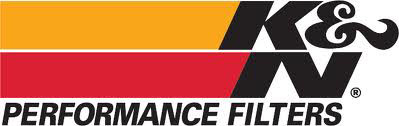
Timbo’s ’64 FL Restoration (Part One)
By Robin Technologies |
Not too long ago, my good friend Timbo approached me with a proposition, restore his 1964 Harley FL, I agreed. Problem was, it’s in a box, literally! So after a brief discussion on exactly what we wanted to do, how much it would cost and the possible value at the end of the rainbow, I started the Hard Ride back from Hell with the old ’64. I picked up the bike, basically a roller and all the boxes of parts that came with it. As you probably expected, this will be a frame up restoration as close to factory specs as I can get it.
There will be some minor changes, which I’ll talk about as we go along. First thing was to lay it all out and take inventory to see what was missing. After some research, I found replacing parts for the ’64 surprisingly easy thanks to J&P Cycle, Biker’s Choice, and the internet. I ordered the Vintage catalog J&P Cycle puts out and started researching parts I needed to replace.
I also found a local polishing company and chrome hardware supplier (needmorechrome.com) to make life easier. Tear down was a snap. Make sure you bag or box all your parts as you go and label what they are, and in some instances what order they go in. It’s not a bad idea to take lots of photographs for future reference. Sometimes a parts manual comes in handy.
After tear down, I started the fun stuff, going through each and every part, each nut and bolt and cleaning them. Some parts and hardware will not be salvageable, so you’ll have to replace them with either new, or good condition used. I found that there is a tons of vendors on line for just about everything you need. Buying new parts from the catalog is not always the best answer, especially if you’re on a budget like I am.
So shop around, do some research, you may be able to save as much as 50% sometimes. You will also need repair manuals and a few restoration guides like the one my friend Bandit sent me for reference from Wolfgang publishing, thanks Bandit. It has been very useful so far. This is the first of many articles on this restoration project. As the months progress, I’ll try and give you a detail look at what’s involved with a full-blown restoration.
Tail Gunner out for now, see ya next month!
1964 Pan Head part 4 (frame)
By Robin Technologies |
Oil tank and lines were next on my agenda. I opted for a more modern spin on oil filter adapter, it looks nice and makes oil changes a snap. I kept the original oil filter that was polished just in case the owner wants to go all original some day.
The front forks have been completely rebuilt with all new modern seals, I had them polished also, looks nice! My customer decided he wanted a old school look on the wheels like they did in the ’30s and ’40s, so we blacked out the spokes and hubs leaving the star bearing plates and lug bolts the original parkerized coating.
Just about everything that is aluminum was polished like chrome. We kept to the OEM look on the primary and oil tank, which was black with touches of chrome.
As for the clutch shift linkage (mouse trap), it also was completely gone through and restored, polished and looks like new. I did find out why they call it a mouse trap! Got my Fuckin’! finger snapped twice while trying to adjust it, IT HURT BAD!
The brakes have all new shoes, lines and fittings. Front brake is mechanical and rear is hydraulic, all juiced, adjusted and ready to go. Tires we picked are replicas of the day. They are Shinko reproduction white walls. Not the best, not the worst, but fit the budget just right. They have all new tubes, rim belts and have been balanced and trued by me.
The new exhaust went on comfortably with new head clamps. We kept the original muffler. It was salvageable. All the footboards have been rebuilt with new rubber and rivets and foot controls were installed.
The original generator in chapter 3, was a no go, it had a bad armature and wasn’t cost effective for a rewind. So I ordered (cust. request) a new 6v generator with built in voltage regulator, it too looks very nice. Just a quick rundown, the electric system although all 6v, has all new solid state components i.e. electronic dual breaker distributor with a solid state voltage regulator, no mechanical parts.
The electrical has all been installed and wiring is complete less the head light and tail light. Both electrical junction boxes have been rebuilt with new insulators and wiring harness.
There’s a lot of little things like the $5 chrome chain guard I found at the swap meet and some odds and ends I also found in good condition cheap, at the swap meet. You can see them in the photo’s if you look hard. The steering head lock was a nightmare. It took me months to track one down on eBay. Shortly after I purchased the one on eBay, JP Cycles informed me that they finally had one in stock, go figure!