5-Ball Factory Racer Closing in on New Cam and Ignition
By Robin Technologies |
We were fortunate to hook up with Heather New, of New-Line Engraving several years ago. Since I was about to switch out my CrazyHorse engine ignition with a Blackhawk Motorworks cone cover I needed to come up with a classic point cover for the new unit and the 5-Ball Factory Racer. It was a natural choice to send her a chunk of aluminum, or I shoulda sent a piece of brass, but oh well. Either way I knew she would bring the project to life.
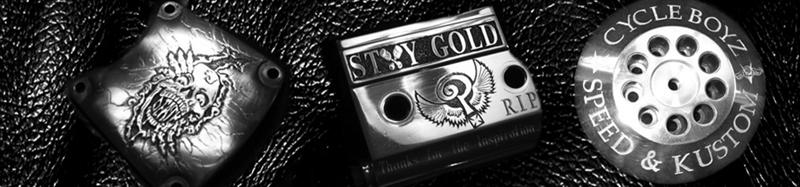
Heather started engraving in a small shop in downtown Edmonton in the Early 80’s, where she took care of over 100 jewelry stores. “I was engraving everything from I.D. bracelets to wine goblets to pocket watches, and more,” said the raving redhead, “items which other engravers said could not be done, I soon learned to do!!! This was when I first met Frank.”
Frank Gurney was (and still is) the best Hand-Engraver in Canada. “He is a true artist and craftsman, and along with the Alberta Apprenticeship Program, arranged for me to be his understudy,” Heather said. “I was thrilled!!! I learned so much from Frank in those years, confidence, trouble-shooting, and above all HUMOR!!!! We spent hours working and laughing (hoy-deedle-doy!!). He taught me so many things before he eventually retired out near Victoria, B.C.”
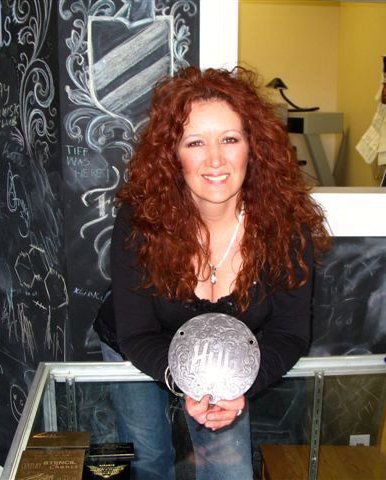
She then moved on to the largest Jewelry stores in Canada. “I was doing all of their machine engraving, as well as custom wedding bands, and one-of-a-kind jewelry pieces,” Heather said. “They treated me like gold, and I will always be thankful for the kindness I experienced there. I relocated near Calgary, Alberta, and began working for a gigantic company with more talent than I had ever seen gathered in one place. I naturally did the engraving there, and also moved on to operating CNC machines, and hand-carving moulds used in casting.” She became a programmer, writing the programs, which would later be used by the CNC machines to cut the actual moulds.
She started New-Line Engraving in the summer of 2005. “I hand-carved an inspection cover for my good buddy ‘Chicken’ and with her over-whelming encouragement, (she cried when she saw it) I decided to branch out into custom bike carving too (after all, a derby cover is just like a signet ring, only BIGGER.”
So here’s how the short, two-week process rolled:
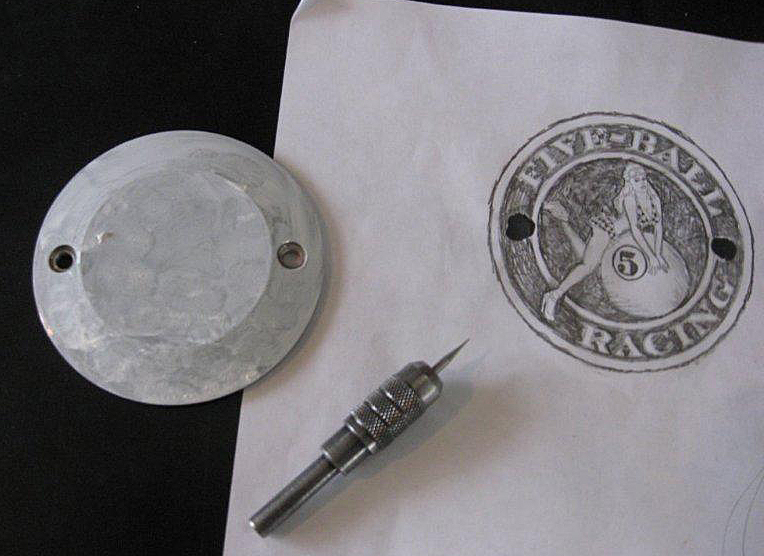
Cover the piece in white water-soluble paint, and transfer the artwork onto the surface
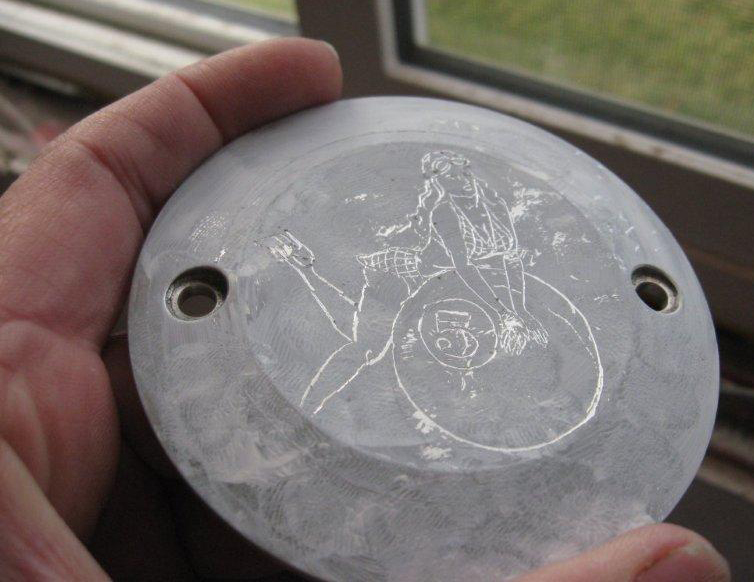
I highlight the general outline, scratching the paint leaves a more permanent mark than pencil, and you don’t rub it off as you work!
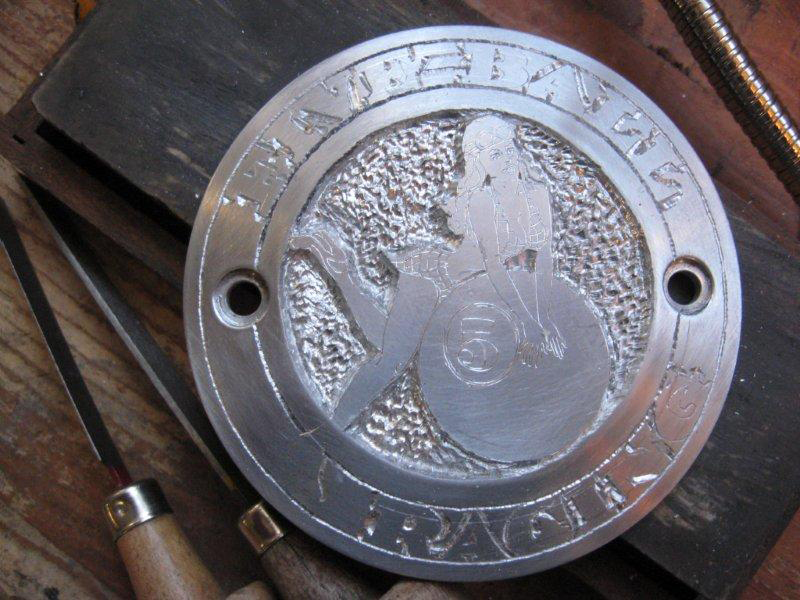
For removing large areas you can try a dermal, but they tend to vibrate too much for any fine work…I used small gravers hooked into a pin-vice to cut in between the letters,
as this cover was done mostly under a microscope.
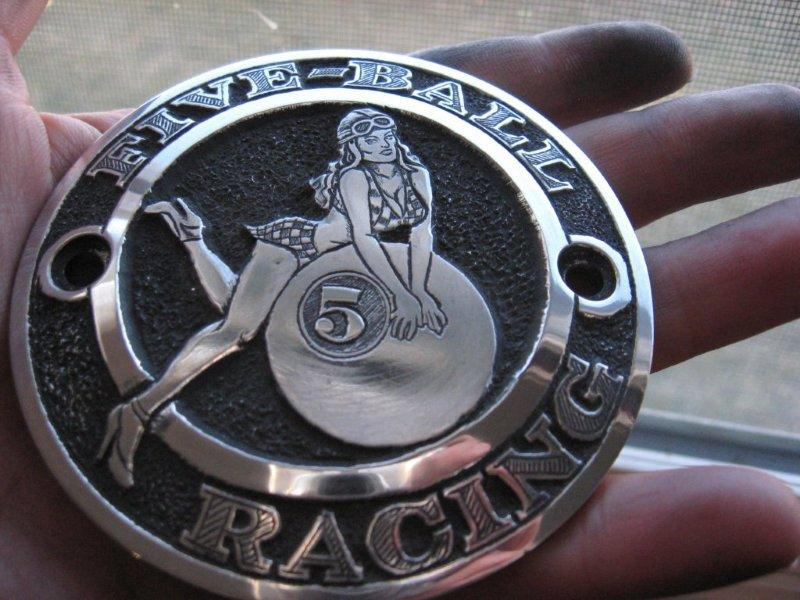
I also use fine sandpaper, jeweler’s files, and burnishers to “round-off” curves (as seen on her legs), and give some dimension to whatever artwork you are dealing with…
Details like hair, the features in the face, and fine shading are all done with fine gravers and files.
I then add an aluminum-oxidizing agent, which blackens the entire piece. When it is re-polished, the highest surfaces will become shiny again, while the black remains in all the nooks and crannies of the background. (I only do this by hand—a buffing machine can remove hours of work in a heartbeat!!)
“If anyone out there in Cyberspace wants to give it a whirl, I am always here with support and tips,” said Heather
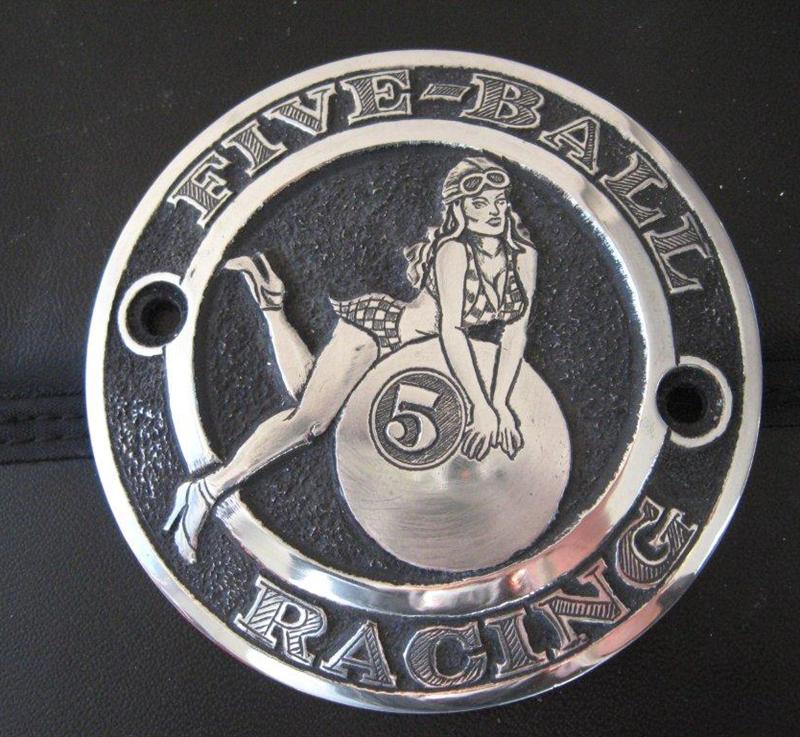
Sources:
NewLine Engraving: http://www.new-lineengraving.com/
Blackhawk Motorworks:
http://www.blackhawkmotorworks.com/
Compu-Fire Ignitions: http://www.compufire.com/
Custom Chrome:
S&S:
Sturgis Shovel Part 12
By Robin Technologies |

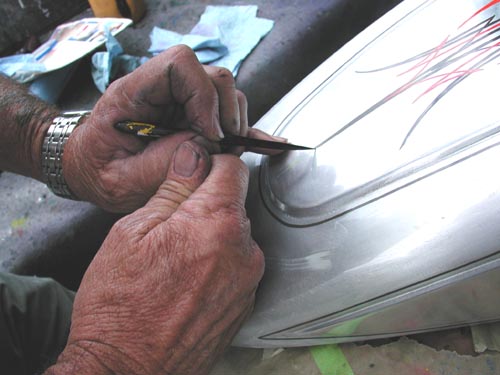
Hey, here’s quick bit on George The Wild Brush who handled the Pin Striping on the 2005 Sturgis Shovel project. He’s pin striped several other bikes for me in his 47 years behind the brush. Born in Hanford, California, a miserable military town, in 1944, he kicked tumbleweed while his mom worked on a base.
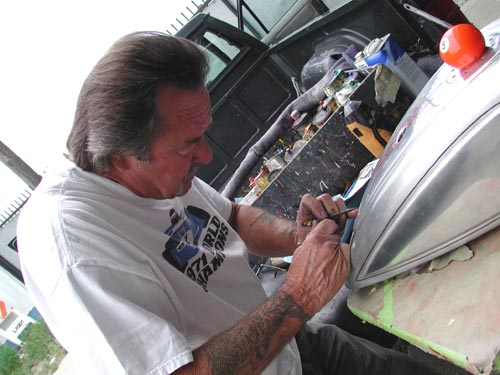
She moved to the safety of Southern California away from the miserable summer central Califa heat, to Long Beach then Lakewood (next door) where he went to school, but didn’t graduate.
He was warned that the fad would die so his vocation would fail. “The fad’s still rockin’,” George said. “My first car was a ’54 ford and I custom painted the driver’s side. I couldn’t afford enough paint to finish the passenger side, so I had the only cool side.”

He studied Von Dutch work, Larry Watson and George Barris. “I’ve striped refrigerators, toilet seats (new ones), and 50 and 110 Tom Gentry trans Atlantic ocean racing boats. He’s taught me a thing or two about striping. “It’s best to have the parts off the bike for the best quality art.”

It’s difficult to paint bare aluminum—“Paint won’t bond to it.” without a primer.” I worked at Gasoline alley for 15 years painting aluminum dragster bodies.
It’s also difficult to pin strip chrome—“It won’t hold up due to the lack of porosity.”
He only uses One-Shot enamel paints—“Can’t use any paint.”
With motorcycles it’s a good idea to clear over striping—“People don’t pour gasoline all over cars, but they do bikes.”
Cars don’t generally need to be cleared over striping work.
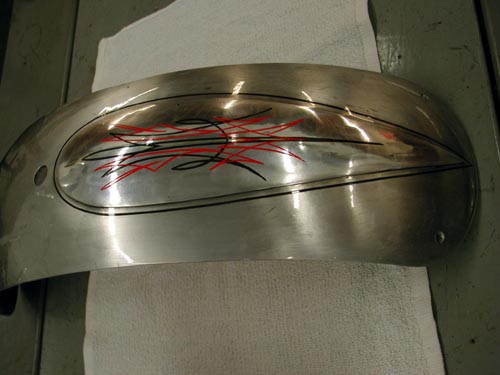
His number is (310) 488-5488 for classic pin striping and good stories.
George came to the shop just after I picked up the clear powdered aluminum sheet metal from Foremost Powder. He usually tells me what I’m going to have striped. I have a vote and initial color selection, then I best get out of the masters way.
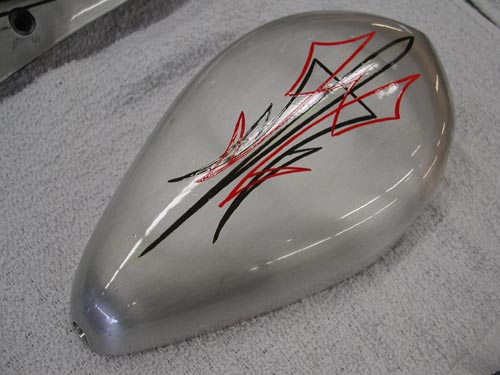
He striped the Goodsen Air Cleaner, which was treated to my holy treatment, then brushed with Scotchbrite to remove the polished appearance.
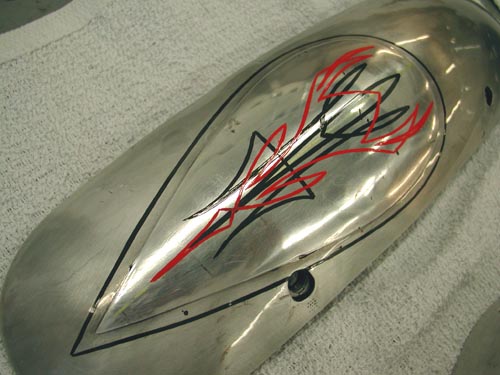
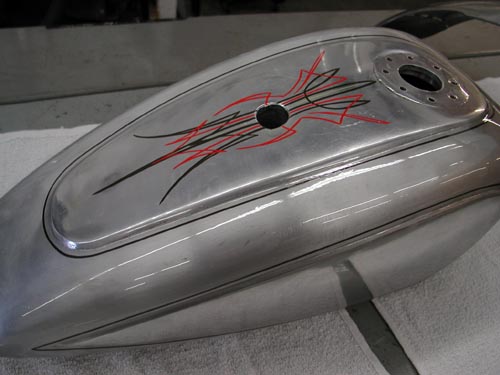
Then he striped the panel polished, highly-modified, XR750, Cyril Huze donated tank and Lucky Devil, custom made fenders. I polished the panels and brushed the rest for a two-tone effect. Not sure it worked, but George gave it a final touch.
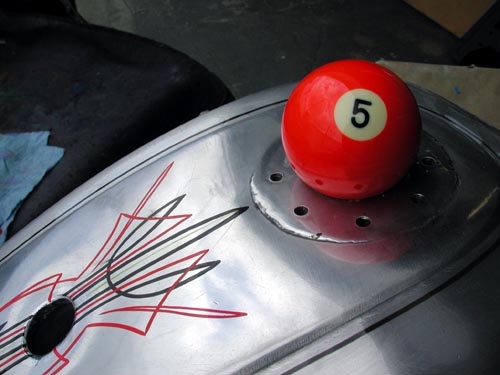
George suggested the 5-ball addition to the center of the tank. Not the gas cap. Ultimately I filled the center-mounting hole with a small 5-Ball to commemorate our company and all the women who put up with my shit over the years. In case you don’t know the story, I’ve been married five times, that’s five misses Ball.
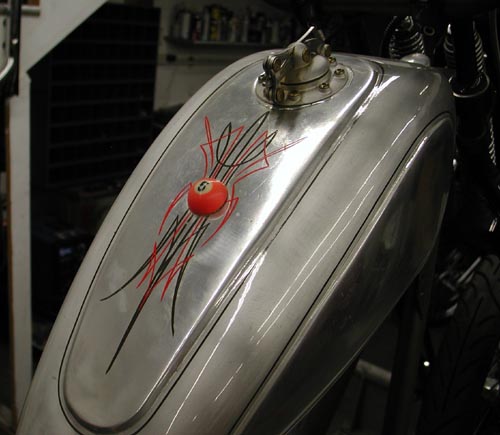
1928 Shovelhead Project Part II
By Robin Technologies |

In a dank dark corner of a dusty debris strewn shop behind the Strokers Saloon on Harry Hines Blvd in Dallas was a small stack of bike parts guarded by a massive starving pitbull with one eye and most of one ear chewed away. The beast was so vicious that it once chewed through a 1/2 inch tether cable, and ate four Avon tyres before it could be subdued and chained in place. No one had the balls to feed the animal and it ran off so many customers that a collective decision was made to relegated the dog to guarding our Shovelhead project. It was like a death sentence. The lovely Lena, the 14-year-old daughter of Rick and Tina Fairless, the owners, who was scheduled to be Bandit’s 6th wife had a fiery temper and told Bandit, in no uncertain terms that the bike would be completed until he left the other women behind and came to Texas to settle down. The Dallas crew surmised that it would never happen so the fuckin’ dog would starve to death waiting for Bandit to return to collect the fair Lena and complete his pact with the marriage counselor.
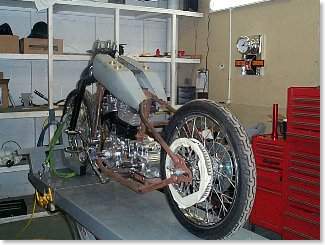
Unexpectedly during a freak Texas panhandle thunderstorm Bandit walked into the shop, carrying a turtle the size of a baby moon into and asked for the Lovely Lena. Upon presenting her with the turtle, her hardened resolve melted like a torch to a metal hanger and she swooned then demanded that her crew set to work on the project. We apologize for the long-winded explanation, but it’s important to understand all the delicate facets of this project to obtain a feel for the treacherous nature of this undertaking and the lives that hang in the balance.
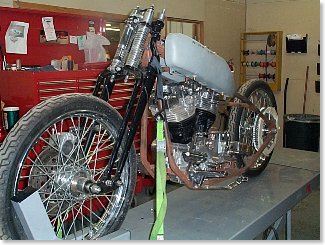
Just then the mega Dallas Easyriders store had a mass exodus of mechanics. Two were hospitalized trying to reach the parts, one died. Several were so pissed off at the shear audacity of Lena’s order that they started a competing business down the street. In reality they were so jealous of Lena’s affections for Bandit that they could no longer work and watch her dance through the shop on air. Enter Jim the transplanted fabricator from Florida who was hired before he knew what he was getting into. If you’re not from Texas, you won’t be familiar with the labor laws. Chain gangs are not exclusive to the Texas Penal system. They are a common phenomena in the work place. Jim hasn’t seen his family since going to work for the Fairless contingent. Between you and us, we have slipped Jim a note that once the project is finished we will spring him in the crate they plan to ship the bike, but that’s another story.
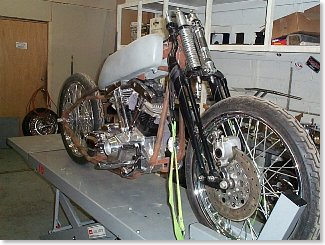
Jim has now modified the tanks for fit the Paughco rigid frame, mounted the engine and trans and front end. Randy Simpson is bending the bars for the project. Jim his building a box for under the seat for the battery since the oil will run from part of the gas tanks to the engine. If you note the belt pulley, we are now planning to run a chain for authenticity and since some other aspect of the bike forced us to go with a chain. We are still looking for the ultimate taillight to go with the project, and we hope to lower the front end enough to make the tanks more level, with Custom Cycle Engineering lower rockers. The front wheel is the stock Bad Boy 21 with an Avon tire. The rear will also be an 21-inch Avon with disc brakes. Pipes are scheduled to be reproduction stock early shovel pipes from Paughco.

Watch as this project comes together. All bets are that the San Pedro Police bike with never even see the border of California, unless she sees the coast before the bike arrives. Stay tuned.
–Wrench
Bandit 2006 Sturgis Shovel
By Robin Technologies |
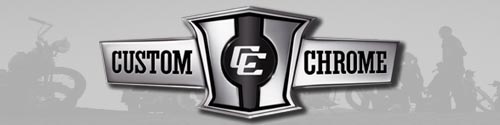
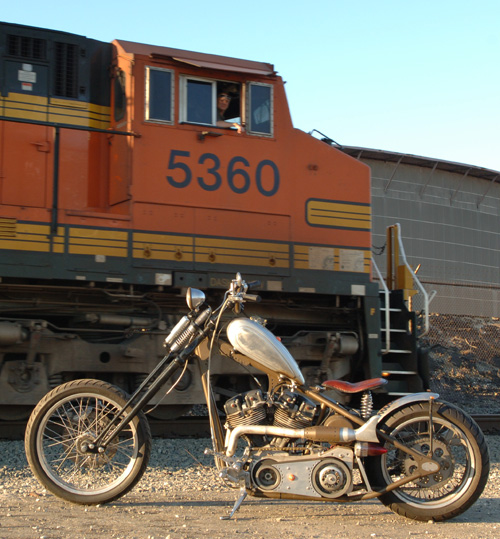
Editor's Note: You've seen the “American Iron” feature. Chris Maida, the editor, asked us to reshoot it, but we kept the original shots near the Wilmington, Califa, Port of Los Angeles rail road tracks. Just happened that a train rolled past in the middle of the shoot. Enjoy.–Bandit
I just did the Old School bit and rode this bike to Sturgis on our Bikernet.com 2005 run from the West Coast.
I cottoned to the pure machine marquee. I didn’t plan to paint it at all, unless absolutely necessary. I wanted to leave most components unblemished metals and incorporate as many iron types (for color) into the mix as possible. I wanted this mess to contain brass, copper, aluminum, steel, and stainless. Of course the steel corrosion dilemma dictated that we use some powder coating for a protective seal. The front end came in black to avoid chrome, so I supplemented the bike with a few additional black pieces, but the frame and some others were powdered to mimic a copper patina. Some aluminum parts were clear coated to prevent complete dulling and afford an acceptable pin striping surface. Some brushwork was applied.

It started with a Shovel engine that a brother gave me with a title. I loaned him a bike when he was down. Due to family illness he was forced to sell everything. There’s nothing better than an engine with a title. I took it from there and ordered a Paughco classic frame to fit me and handle like a midnight dream. Too many choppers today look good but don’t handle worth a damn. I wanted a bike to fit, handle well on freeways, yet be light in city traffic and parking lots. I spoke to Ron Paugh at Paughco and they built me a 4-inch up, 3-inch out, 35-degree raked rigid, wide enough to handle a 180 tire.
I don’t care for wide tire, fat-assed, beachball monsters. I decided to set my limit at 180 and run an O-ring chain for the traditional look. I stuck with a Paughco front end to top off the chassis. It’s one of their new tapered leg springers, 9-inches over with three degrees of rake in the trees. It worked out to be almost 5 inches of trail and handled as light as a dirt bike.
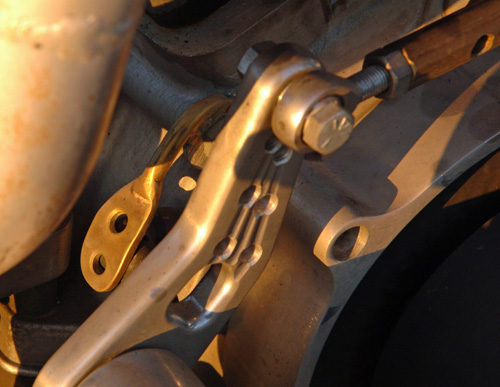
The engine had early stock heads, House of Horsepower cases and was a 105-inch stroker, too much for a rigid chassis. I wanted this bike to last, be a beater, but not be a dog. I contacted friends at S&S and they suggested 93 inches of street power for a balanced, reliable drive train. The stroke was reduced to 4.5 inch with 3 5/8 inch bore. The bike is fast but not a vibrating monster. I also spoke to Lee Chaffin at Mikuni and he suggested a 42mm, flat slide, Mikuni carb. “It will give you sharp throttle response,” he said. If I planned to run the Shovel on the salt flats he would have suggested a 45 mm venturi.
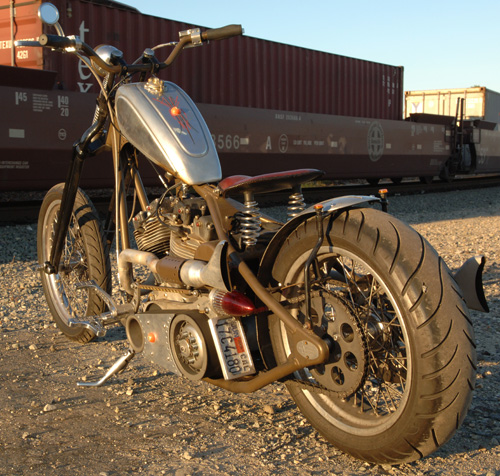
I have a couple of codes when it comes to building choppers. I like to keep them as simple as possible. On the other hand I like an oil cooler and filter to keep the drive train alive. I came across a system that bolted to the front motormount and doubled as a cooler while holding a spin-on filter (Rohm billet oil cooler mount). It was perfect. Other chopper codes include having enough taillight to prevent being run-over and enough gas to take you 100 miles before you hit reserve, or you’re looking for gas stations constantly. In this case I nearly broke the code a couple of times.
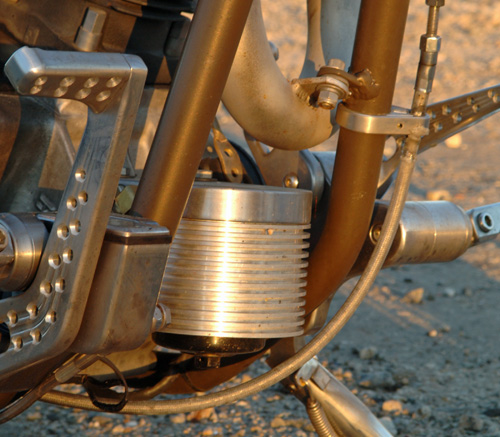
The Sportster gas tank originated on the verge of being beneath the acceptable fuel capacity, 1.75 gallons. It was an old Aluminum XR 750 race tank that we heavily modified. Get this: Some aluminum tanks are against the code, they’re too weak, notorious leakers. I broke the unwritten rule because it was a factory tank—cool right? Not so. “They broke during flat track races,” Berry Wardlaw, the Boss of Accurate Engineering, said at dinner in Deadwood, South Dakota, after I welded it twice on the way to Sturgis. “They ain’t worth the powder to blow ‘em to hell.”
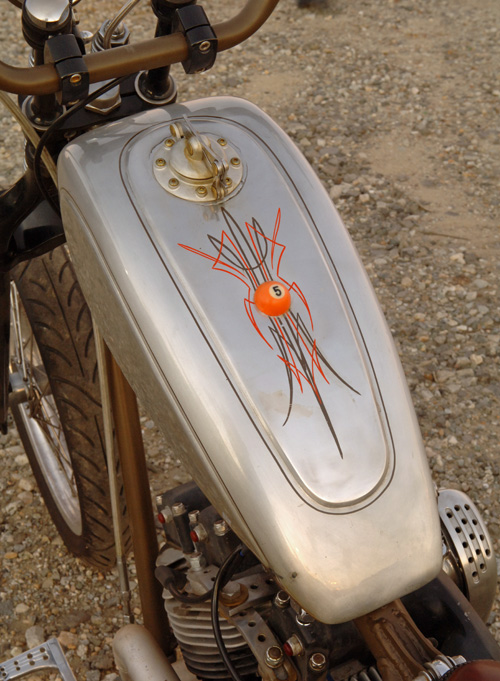
I put more work into that tank than the Martin Brothers pour into a set of one-off artistic sheet metal. First I added additional rubber mounted bungs to the base of the tank for added support, since I didn’t on the last Sturgis rigid. It broke twice. Because the tank would reside on a severe angle we moved the petcock to the rear, also for more fuel capacity. We drilled the tunnel and welded in a plate to allow the entire center section to augment petrol storage. Then I installed a Crime Scene speedster cap for an old school hot rod appearance.

Kent from lucky Devil Metal Works in Houston supported the aluminum theme by hand fabricating an aluminum fender to match the tank, front and rear. We scrapped the front job.
Back to the code. Remember the taillights, so a semi will at least recognize that it’s a motorcycle under his rip-roaring wheels. This is a tough one for me. I like the minimalist approach, but endeavor for some level of survival. The crew at Eye Candy Custom Cycles (.com) developed this hot looking, side-mount ’59 Cadillac taillight. I thought it was the cat’s paw and that I could mount it to glow through to both sides. I installed it to the BDL inner primary, so close and tight to the frame that no one could see it. I broke the code.
I also grappled with some elements of the wiring, but it worked out fine—that’s another story. I’ve been tinkering with bikes for 30 years, yet learned a tremendous amount with this build.
The bike continued to roll together like a dream with the Kraft Tech oil bag, hard copper oil lines, the Lucky Devil sprung seat and 5-speed Rev Tech Transmission. The wheels were Custom Chrome aluminum rims, stainless spokes and chromed steel hubs. This was the first time I ever used Brembo brakes, no problem and I’ve worked with Joker Machine controls for the last five years.
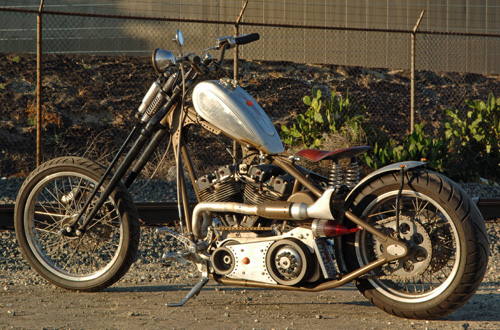
Let’s focus on mistakes I made, so you won’t make them in the future. The hard lines were cool, but I could have installed rubber hose and been finished in a half hour. Plus, since the Kraft Tech, round oil bag, was rubber mounted and the hard lines solid, the street vibration fucked with them and they cracked. I needed vibration resistant furrels. Let’s stick with the oil bag. It’s cool, solid and bolted right up, but battery choice is critical. There was very little space between the battery terminals and the frame. Ultimately, a Bikernet babe was called to the front, to stitch a rubber protective cushion to prevent shorts. That’s too close for everyday comfort.
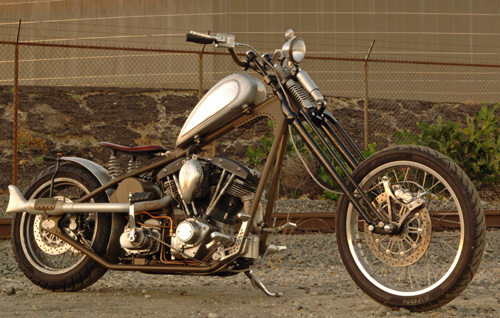
I broke in the bike using the Eddie Trotta formula for success, but missed one element, high-speed interstate travel. If I had put a few miles on the bike at 80 mph, which is against the break-in code, of 55 or less, I would have noticed the severe gearing. That’s where I went wrong. I started with a JIMS 6-speed and stock gearing. Then I discovered that the new Starter system from Compufire, that runs off the engine, wouldn’t be available for Sturgis, so I had to punt. I mounted the Dyna coils under the oil tank, which prevented a standard Compu-fire starter from being installed quick. A kicker was the answer. It fit with my hand made exhaust system using modified Samson mufflers, but I was forced to shift back to a Rev Tech 5-Speed transmission, because I needed the kicker. I should have considered a gear change at that point, but didn’t.

So what happened on the 1500-mile trek to the Badlands? The bike ran like a raped ape, strong and true. The handling was superb, everything remained in place except for the bullshit running lights I attempted to use for more visibility. They vibrated, spun, popped the bulbs and tore at the wires running through the fender rails. The ragged glitch in the road was the gearing. I ultimately replaced the running lights with these no-count reflectors and a H-D teardrop turnsignal under the right muffler.

The bike clocked 300 miles before I left town. Another 200 miles down the road toward Arizona, it had the mileage numbers to afford me enough break-in miles to drop the hammer and let her fly. At 90 mph I peeled past big rigs on Interstate10 heading out of the vast Los Angeles plague of concrete and stucco homes reaching dangerously close to the Arizona border. Crossing the state line, into the helmet-free state, I felt relieved to experience 100 degrees in the open desert flying toward Phoenix, another blight of concrete and southwestern architecture. I sensed the buzz in the frame and handlebar grips through Custom Cycle Engineering rubber mounted risers. The Shovel was over-revving and I needed that 6th gear release from extensive vibration, but I kept pushing for the love of speed, a light 520-pound, 93-inch chopper can deliver. She sliced the open road like a high-speed rotary knife through French bread.

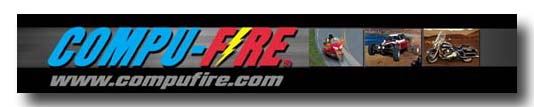


I was beginning to buzz my feet off the Joker Machine pegs and adjusted them at the next stop. Rubber inserts on rigid pegs are mandatory, but I flaunted that rule with impunity. Just 60 miles out of Phoenix with the temps cresting 104 degrees and our group, of a half dozen, barreling along at over 90, the Sturgis Shovel quit, pure dead in the fast lane. I reached for the plug wires, then the ignition key that hovered less than a ½-inch from the whirling BDL belt drive. Better not go there, I thought as I signaled to lean right into the slow lane then onto the rough texture of the emergency lane where my baby came to a stop. That’s when I noticed the terrible, over-flowing gas leak at the back of the tank, all over the rear head.
As if the devil knew, one more mile and I would burst into flames in the middle of the searing desert. He flipped my ignition off. I never found an electrical problem or mechanical woe. She turned herself off because the vibration had taken its toll on the aluminum tank.

The next morning I was back on the road after Nick and Charlie at Custom Performance, (Turbo builders for Harleys, in Phoenix), had my tank rewelded and Nick recommended larger, softer rubber mounts. We were back on the road, where I took care of the beast for the rest of the run to Sturgis (kept my speed down), or until I could change the gearing. As it turned out, as I pulled into Deadwood, gas dripped onto that rear plug again. Bad news. There are codes and builders who know which ones can be broken—none. You can check the entire Sturgis Shovel Project build in our Bikernet Tech Department. The tank was repaired in Rapid City, but just two weeks ago I was forced to have it welded for the third time in Los Angeles. When will I learn?
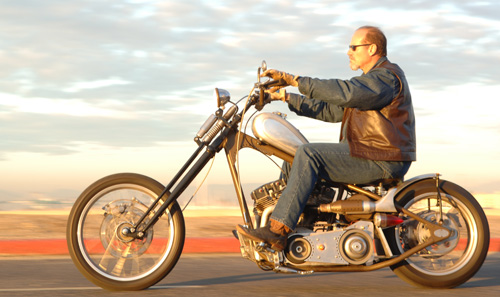
Ride Forever,
–Bandit
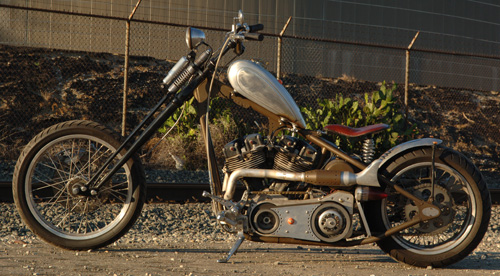
Owner: K. Randall “Bandit” Ball
Home: Wilmington, California
Builder: Bikernet.com
Year/model: 1956 Sturgis Shovel
Time to Build: 9 months
Color: Shit brown
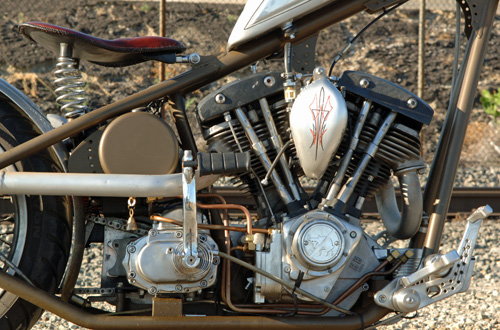
Engine/Transmission
Year/Model: 2005 S&S
Builder: Richard Kransler, Phil’s Speed Shop, and S&S
Displacement: 93 inches
Cases: House of Horsepower
Flywheels: S&S side-winder
Balancing: S&S, 1300 Bob weight
Connecting rods: S&S
Cylinders: S&S with longer skirts
Pistons: S&S forged, 8.2:1 compression
Heads: 1966 Shovelhead by Phil’s Speed
Cam: S&S
Valves: Black Diamond
Rockers: S&S rollers
Lifters: Custom Chrome
Pushrods: Custom Chrome
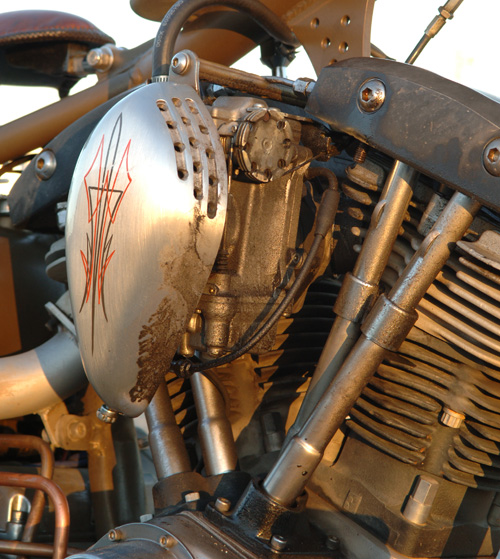
Carb: 42 mm Mikuni
Air Cleaner: Fantasy in Iron
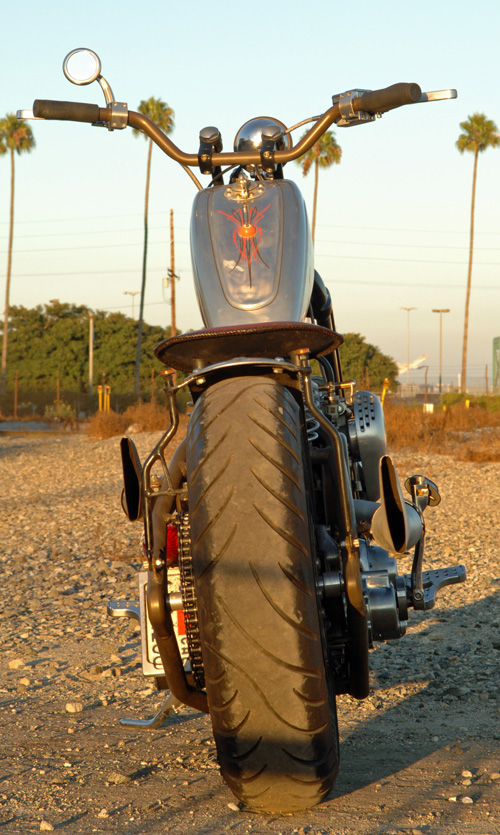
Exhaust: Bandit and Samson
Ignition: Compu-fire, single fire
Charging: Compu-fire
Oil Pump: S&S
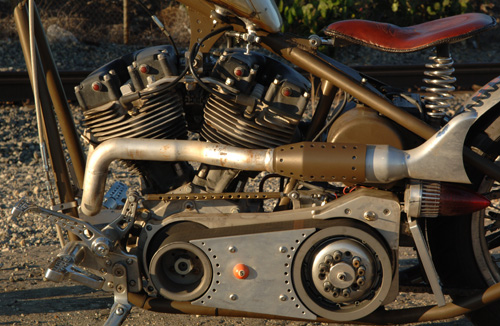
Transmission
Year/model: 2005 Rev Tech, 5-speed with kicker
Case: Rev Tech
Gears: Rev Tech
Clutch: BDL
Primary Drive: BDL open belt
Kick Starter: Rev Tech
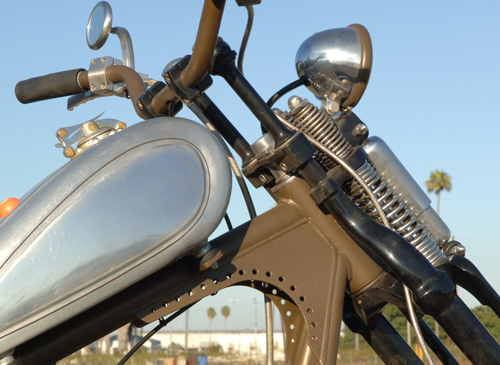
Chassis
Frame: Paughco Chopper
Rake: 35 degrees
Stretch: 3-out, 4-up
Front Forks: Paughco tapered-leg springer
Swingarm: none
Rear shocks: nope
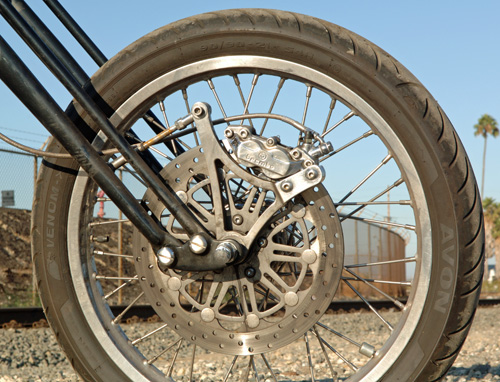
Front Wheel: 21-inch Custom Chrome
Rear Wheel: 18-inch Custom Chrome
Front Brake: Brembo Caliper and Springer Bracket
Rear Brake: Brembo Caliper and Softail Bracket
Front Tire: 21 Avon
Rear Tire: 18/180 Avon Venom
Rear Fender: Kent Weeks
Fender struts: Bandit
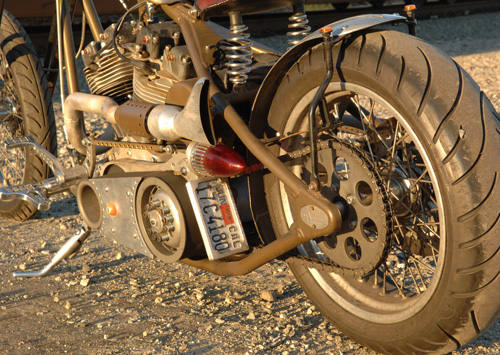
Headlight: Custom Chrome
Taillight: Eye Candy Custom Cycles
Fuel Tank: Aluminum 750 XR
Oil Tank: Kraft Tech
Handlebars: Custom Chrome narrowed
Risers: Custom Cycle Engineering dog bones
Seat: Lucky Devil Metal Works
License Bracket: Eye Candy Custom Cycles
Handlebar controls: Joker Machine
Foot Controls: Joker Machine
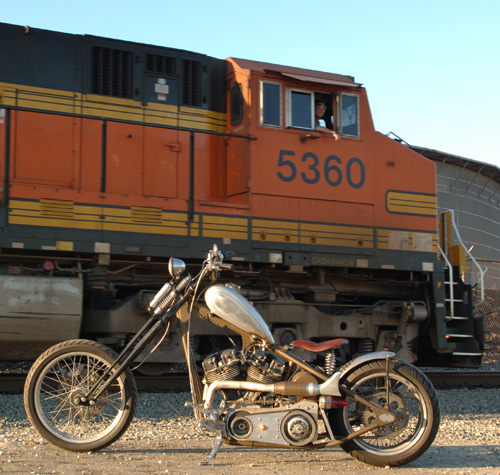
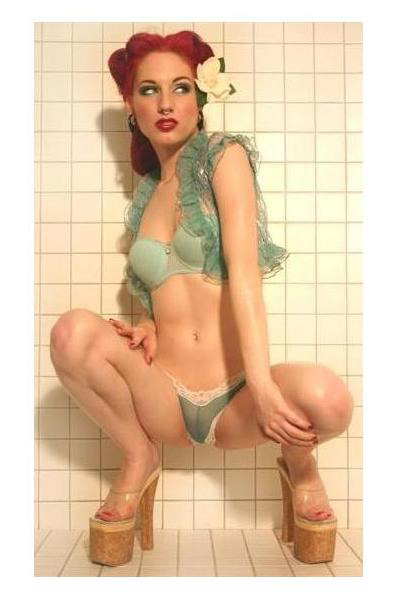
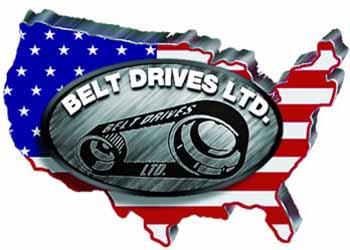
Mudflap Girl Part 1a
By Robin Technologies |

Back to Mudflap_Girl_Part_1_the_Concept
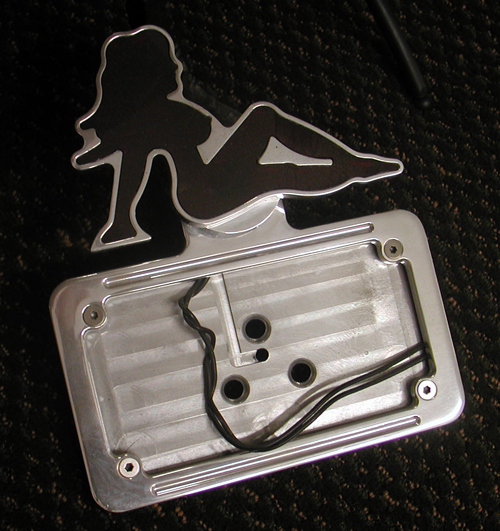
So we’ve collected a handful of mudflap girl products from Billy Lane, at Choppers Inc. , 2-wheelers in Denver, Sturgis and Daytona and Nick from New York City Choppers. Then we needed a fitting bike project, and one surfaced. Seems a Bikernet babe grew up in the San Pedro projects with eight brothers and sisters. The oldest one, and most supportive, hardest working, was Brad Olsen, a longshoreman crane operator in the LA Harbor.
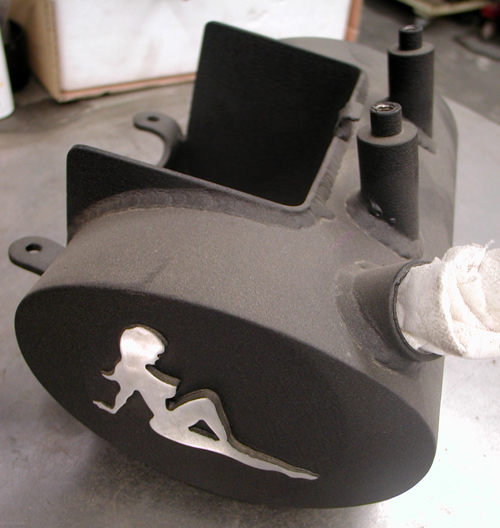
Those kids grew up on the tough side of the harbor and Brad took the brunt of the hard life, became a fighter and family member defender. He worked the ports, went to school, became a tugboat captain and ultimately, a crane mechanic. For eight years he trained under Richard Bustillo, who worked with Bruce Lee, and Brad became a master and owner of his own dojo, Harbor Kick-Boxing in San Pedro.
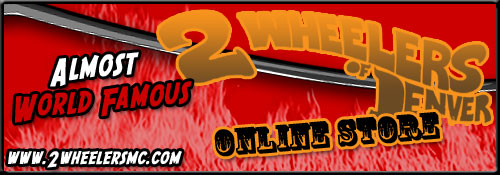
Brad fought for his brothers and sisters, and then worked with inner-city kids to build their self-defense abilities and self esteem. Brad has owned a 1961 Panhead for 25 years and keeps it pristine. It’s his baby, but his kicking knee is damaged and he needs a long-distance touring bike with an electric starter. That’s where the mudflap girl came into play.
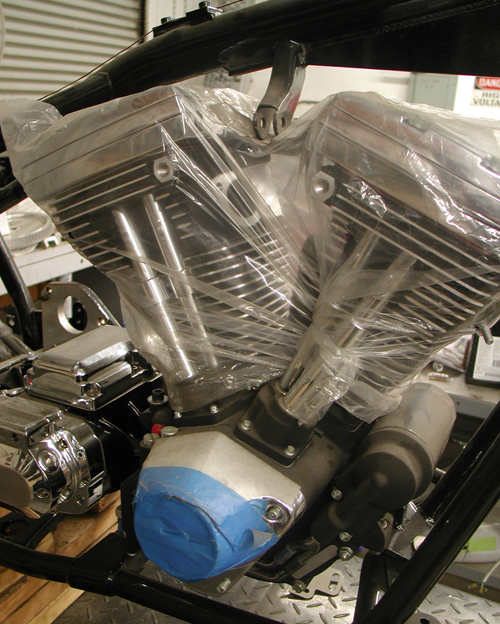
The project started with a salvaged 1998 Dyna Glide basket, which we tore apart. We sent the engine to Harley-Davidson for a re-man effort with the help of Fullerton, California H-D. The transmission was rough and we wanted a 6-speed for those long Mudflap Girl highways. I had a JIMS 6-speed, which I returned to the JIMS factory. We switched and twisted the Dyna Glide 5-speed transmission into a JIMS FXR, 6-speed and a Softail 5-Speed for another project (my 1915 5-Ball Factory Racer).
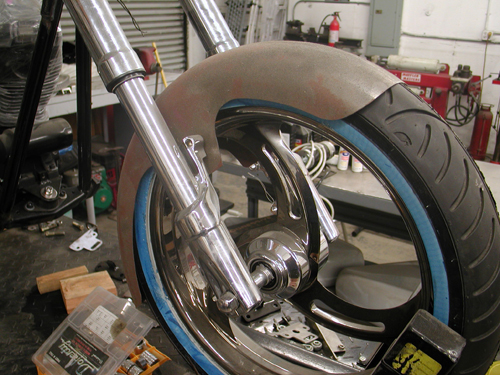
I’m not a big Dyna, fan so we dug out my last Quantum, Kenny Boyce styled Pro Street FXR frame and went to work finding parts. I bought a used Arlen Ness FXR swingarm from LA Chop Rods and dug out a wide Custom Chrome inverted front end with turn signals built in. The overall design element called for building a tough and reliable touring motorcycle for Brad.
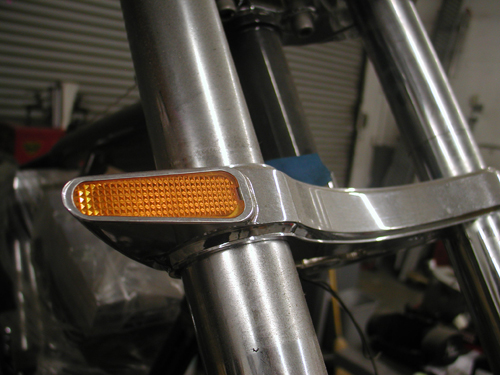
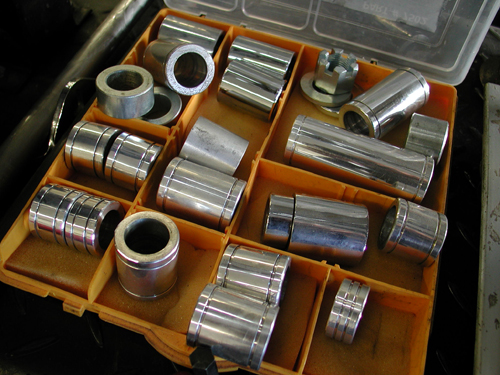
Another key element for the overall package was the bags we ordered from Redneck Engineering. Once we had a set of Renegade Wheels like we used on the Assalt Weapan, mounted to new Cobra Avon Tires we were ready to begin the mock-up stage.
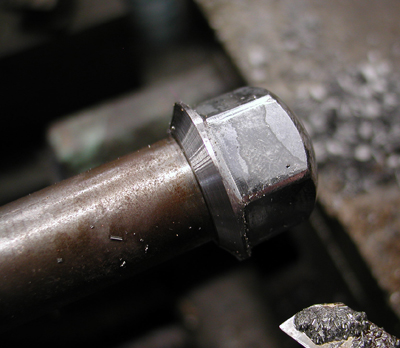
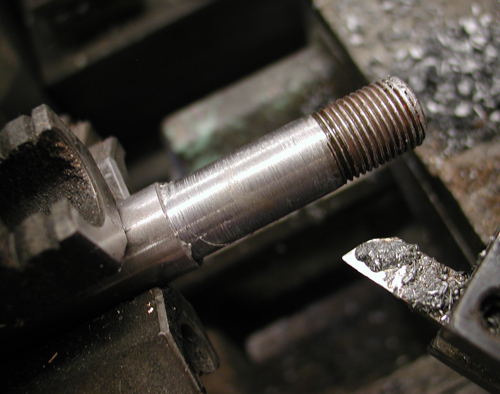
Of course, I used Doherty Machine wheel spacers to center the wheels and had to machine a stock axle to fit the Custom Chrome wide glide.
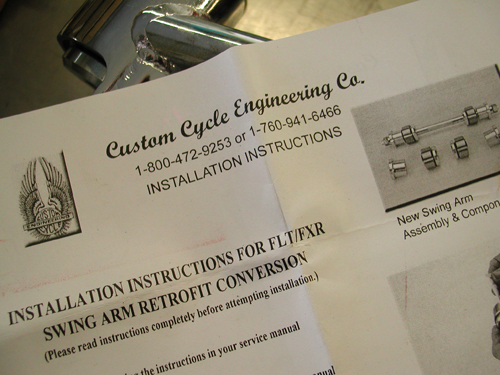
Handling is an issue with any rubber-mounted bike and we pressed in Custom Cycle Engineering swingarm bushings to tighten the ride. Plus I’m still trying to work with a tougher swingarm axle from www.Glide-Pro.com.
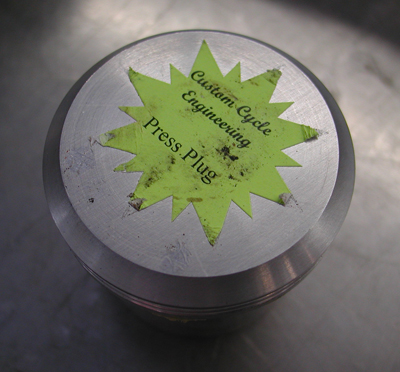
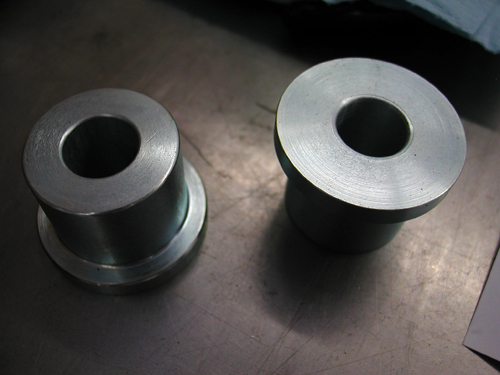
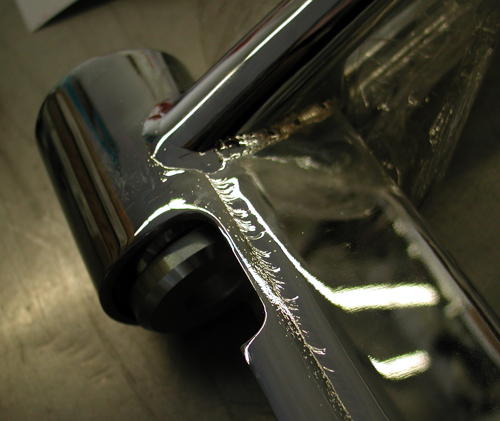
I spoke to a couple of builders about installing the driveline in a FXR frame and some bolt the engine and trans together, then lay them on their sides. They slip the frame over the top and install the swingarm, swingarm axle, rubber-mount biscuits and transmission to the frame. Unfortunately, I don’t care for that system. It’s against the Code of the West to lay a Harley engine on its side on the ground. Bad mojo.
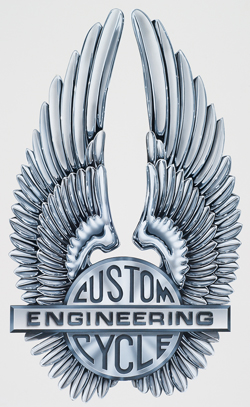


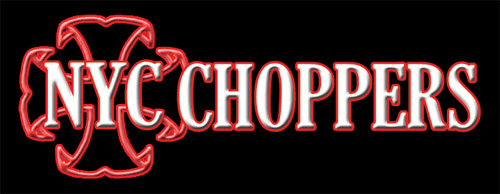
We mounted the front end and front wheel to the frame, then put a jack under the frame. Then we mounted the swingarm and transmission together in the frame with the axle. Next we installed the Renegade wheel. I moved the jack. with a chunk of wood to lift the transmission until it was level.
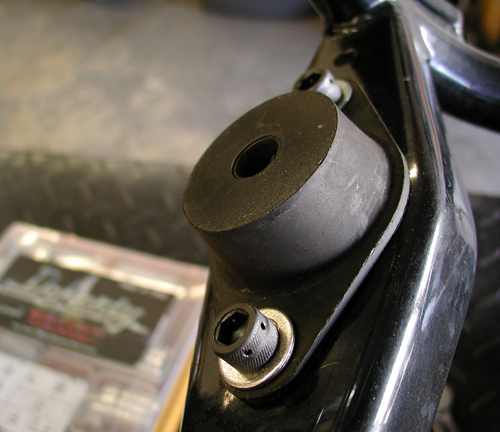
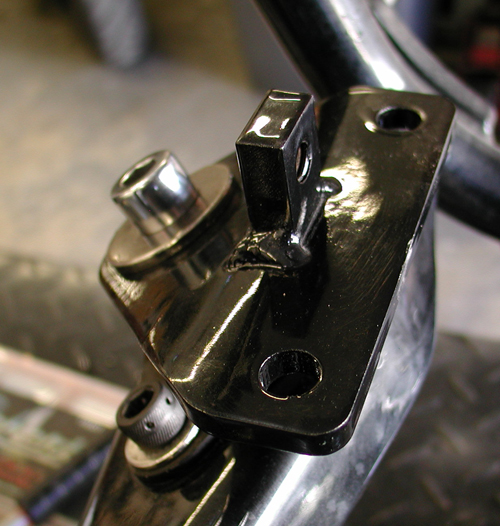
Then came the Quantum front motor mount, which was offset. We may replace it with a stock touring mount. Here’s what Rogue had to say about it:
No, they are not specific to the frames you have. They can be used with anyrubber-mount FXR frame to offset the engine 3/8ths of an inch to the left.We originally used them with the frames Kenny Boyce made for Quantum.
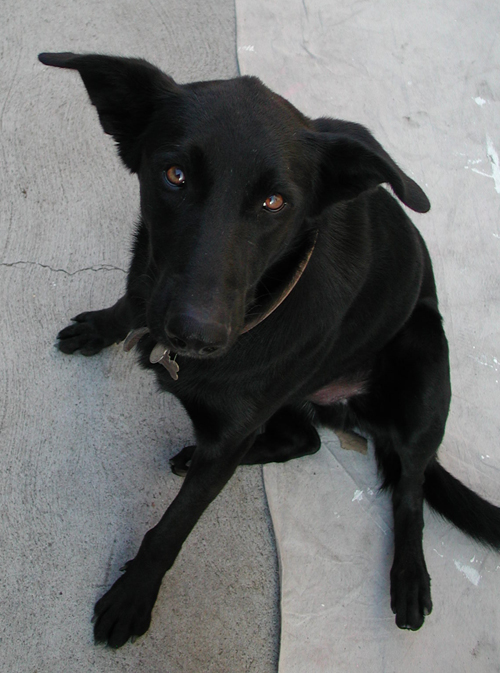
Looking back over some old paperwork it appears you got two blackpowder-coated Quantum frames that were made for Quantum by Kenny Boyce.
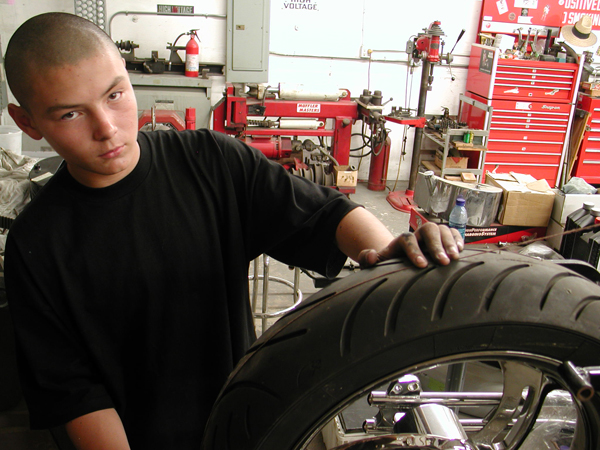
These frames were used with the front offset mounts and had the transmissiontail shaft modified by removing 3/8ths of an inch from the left side and useda spacer of the same size on the right. This moved the engine andtransmission equally to the left.
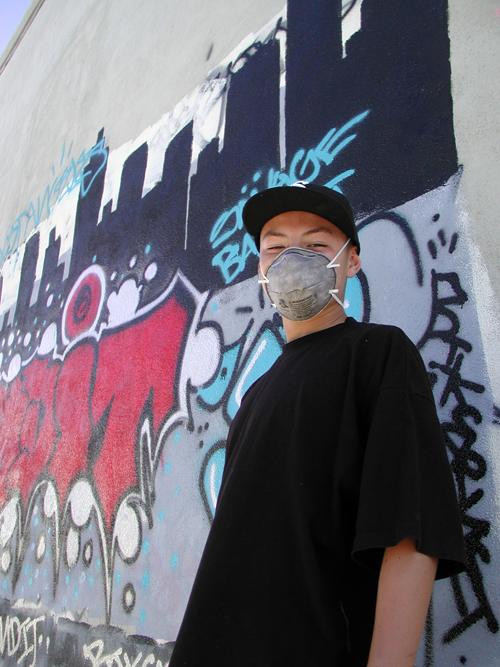
Later, Quantum used a set of offset rear swingarm end caps as opposed tomodifying the transmission. If a stock front motormount was used, no changes had to be made to the rear.
My notes say you also got a bare Quantum frame made for them by Kraftech. The mounts were usually used when using a fat tire on the rear.I had a bunch of them and figured you could use them for something. You donot have to use them!
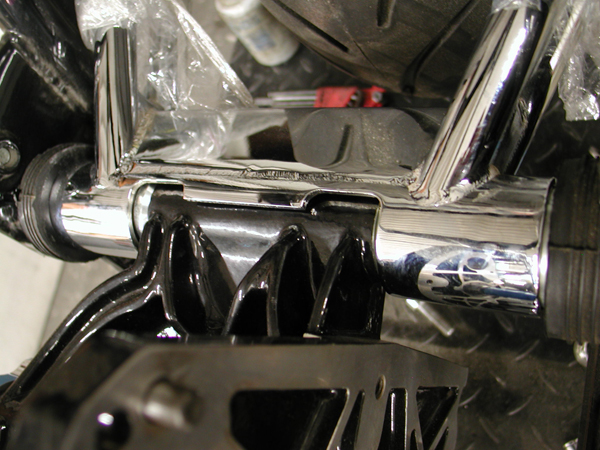
I was confused by the offset, so it’s always a smart notion to check with someone who knows. Rogue worked for Quantum back in the day. We will eliminate the offset front motormount plate as we roll forward.
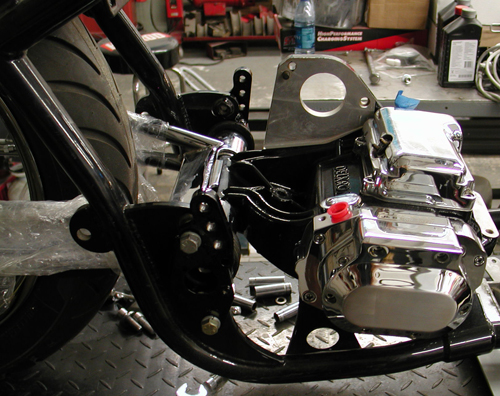
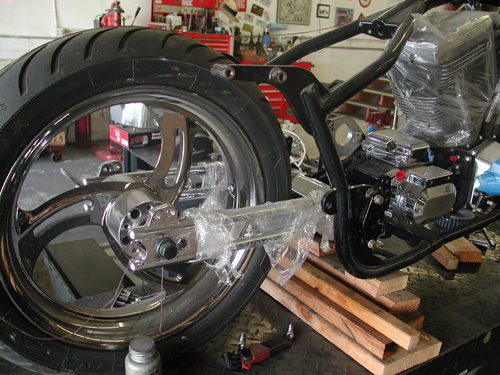
With the trans jacked level and the front rubber pad mounted loose with the front engine plate, mentioned above, snugged to the biscuit with a ½-inch bolt, we dropped the engine into place, like we would in a rigid or Softail frame.
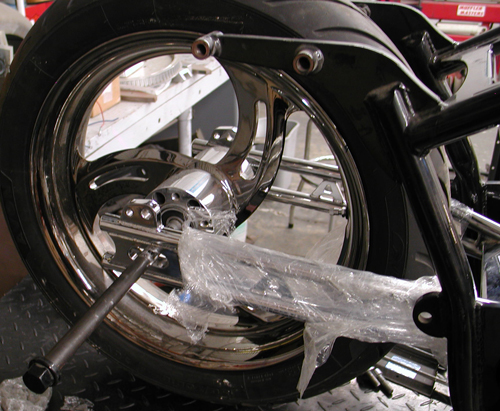
Next, we’ll replace that front motormount, shave off the existing tank mounts, start to mount a Custom Chrome gas tank and rear fender and prepare Redneck Engineering bag mounting brackets.
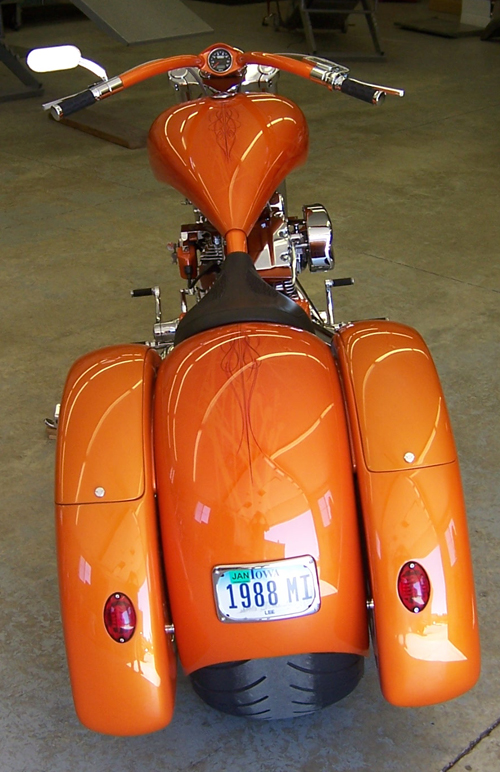

Above is a bike built by Don Hotop for his wife using Redneck Engineering bags. The fiberglass bags are designed, and come with mounting rails for Softails. We will need to cut the bags for Progressive Suspension shocks and build very sturdy basketry.
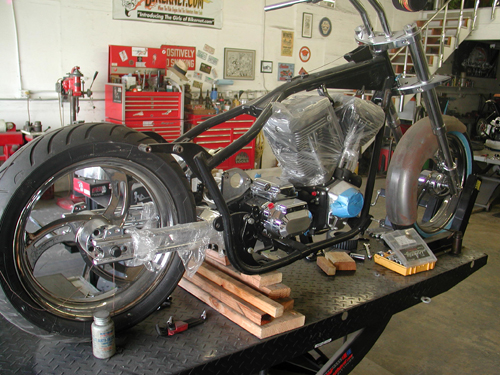
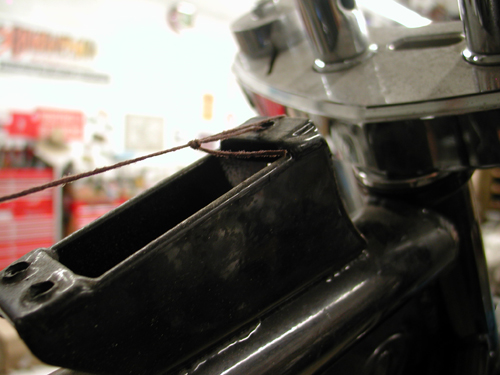
Click here for: Mudflap Girl Part 2, the Bandit Engine and Spitfire update
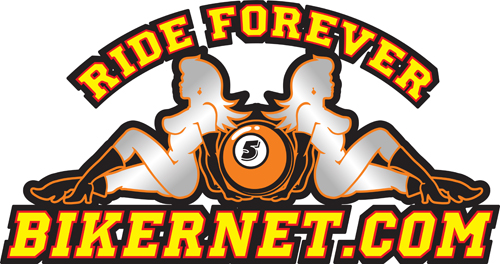
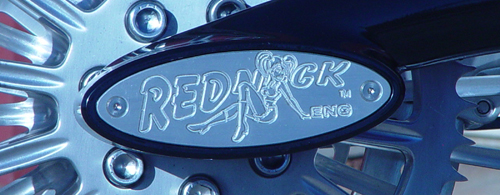
5-Ball Factory Racer, Part 6
By Robin Technologies |
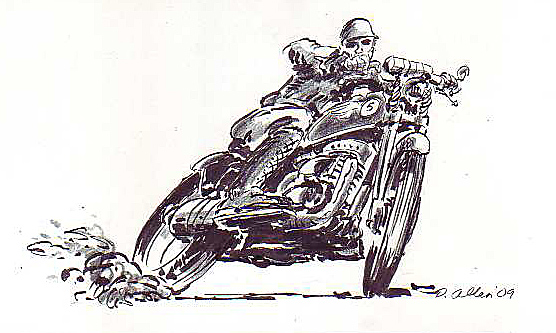
How do you feel about your computer? I could easily take my old .357 Smith and Wesson revolver and blow this sonuvabitch into the briny harbor Pacific waters. I'd set the smoking gun down, go find a job driving a trash truck, and be able to hang out with the bros and drink beer until my kidneys failed, then you could toss my carcass into the Pacific along with my IMac. Life is nuts.
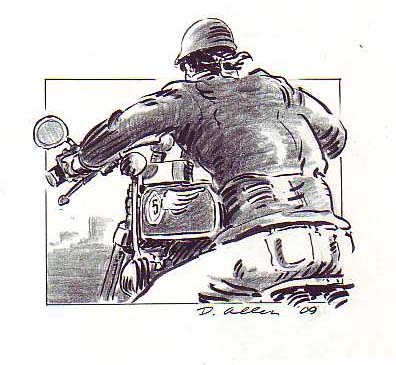
Ah, but the 5-Ball Factory Racer is coming right along. I hauled it down to Chica's for rear fender fitment, never thinking about the front fender. Should I? Chica makes his own wide ribbed fenders 5 and 6 inches wide. They're available for old tall 16-inch wheels and 18-inch wheels for an easy fitment to the tires. On my way south of Long Beach, California, I swung into Todd's Cycle. He was jammed with work. It's odd in this dour economy to see shops cookin'. Chica also was hustling to fill wheel orders, work on vintage bikes, and rebuild engines. I stopped in another shop on the edge of Long Beach, Richard Graves's car restoration facility. Damn, he does sharp work. He was working on a '50s Ariel square four.
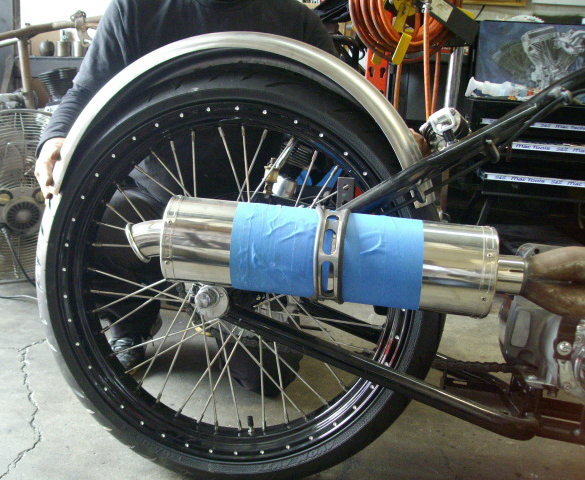
Graves was also jammed with work, so the world ain't all doom and gloom. We just gotta provide a valuable service and be honorable businessmen, and we'll survive, goddamnit. Like Dave Rash, of D&D Exhaust says, “Motorcycles are mechanical Valiums. The world can go to shit, and the brothers take care of their motorcycles.”
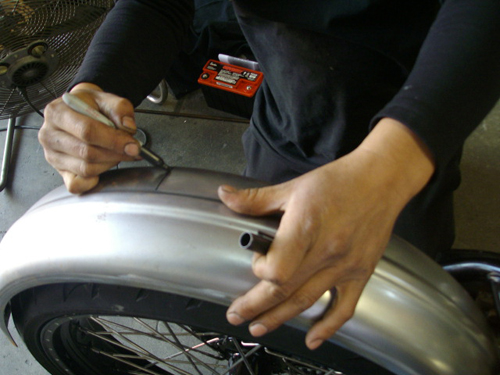
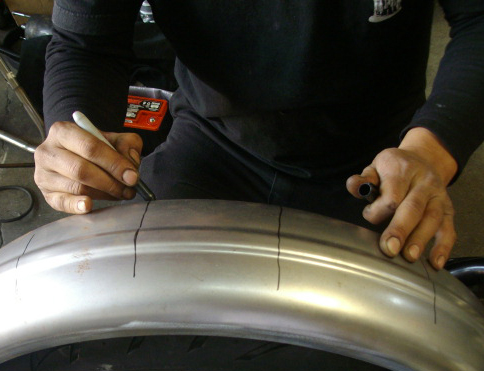
I like that notion. Chica marked my fender for stretching since his fender wouldn't wrap about a knockout Black Bike 23-inch wheel with an Avon Tyre. He indicated where the stretching would take place every 4-5 inches with a felt pen, then went to his machine. “You need to stretch it the same amount,” Chica explained, “and stagger the stretching maneuvers to prevent the fender from warping or twisting.”
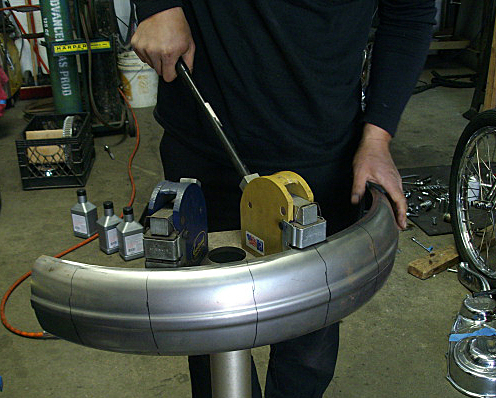
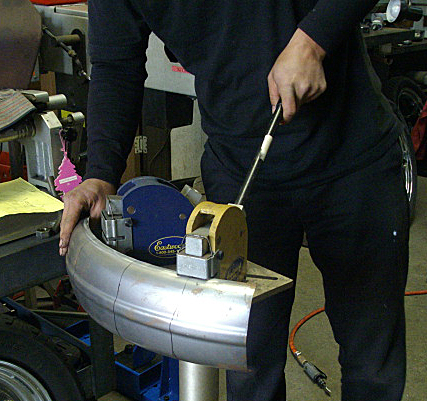
I asked Chica if his fenders needed additional support where the fender rails would be attached. He pointed out that the extreme contours and the ribs added extra structural strength. But he did recommend two fender straps over the frame cross-member.
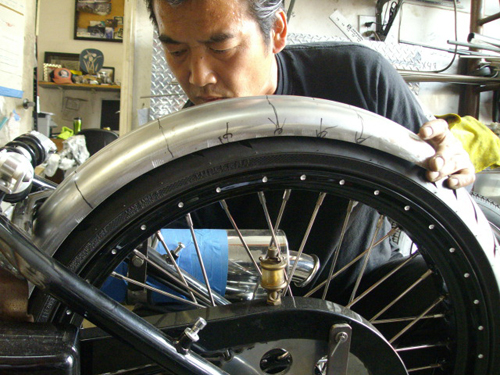
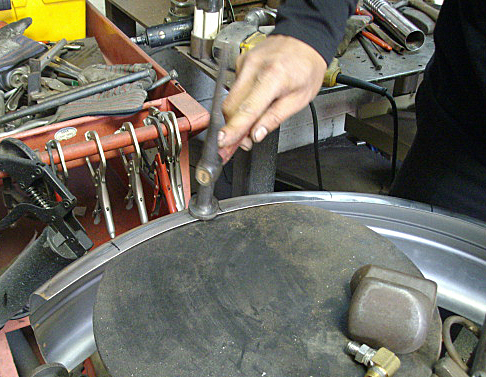
That did it, and Jeremiah and I loaded up the Racer for the return trip to the Bikernet Interplanetary Headquarters deep in the Wilmington ghetto. I started to work on the rear fender installation immediately. I bobbed it about 4 inches, but was grabbed by the rear wheel adjustment designed by Rick Krost of U.S. Choppers and manufactured by Paughco.

It's interesting, and I'm still getting the quirky hang of it. It automatically adjusts the ¾-inch axle back and forth, and up and down about ¾ inch. That element makes mounting the rear fender even more interesting. I was forced to don my patience- and-remain-flexible hat. Who knows if it's right, but I tried to work in several fender fluctuation means, so I could adjust it if necessary.
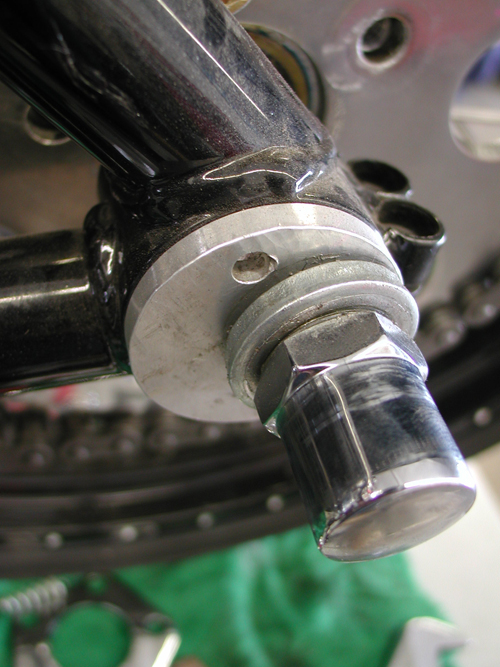
The fender was mounted with a single bolt at the bottom behind the battery case. Then, with the fender spaced evenly from the tire throughout the complete radius, I marked drilling holes for the fender straps. I drilled the holes, and the gods of stainless steel blessed my ass that day with a keen sense of accuracy. The holes and the fender straps lined up. I had to keep an eye on the axle adjustment, or the wheel was cocked right or left in the frame. “Ya gotta watch for the sweet spot,” Rick Krost said. I called him in the middle of the night to quiz him about wheel adjustment and alignment.
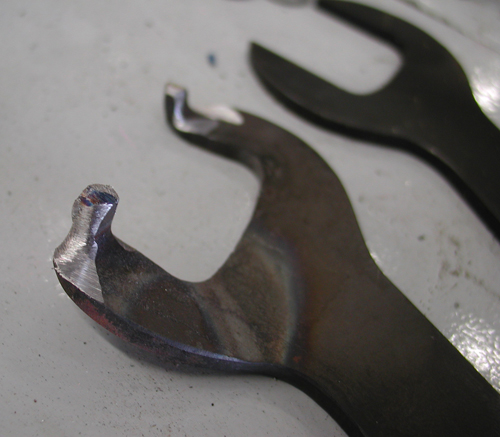

I also needed to make a spanner wrench for his axle adjusters. I was in a hurry one night and built a crappy one with some strange punched out flat open-end wrenches. I just heated, bent the tangs, and ground it to fit. It was sloppy, and ultimately, I built another one with brazed ¼-20 bolts to another wrench. It fits much better.
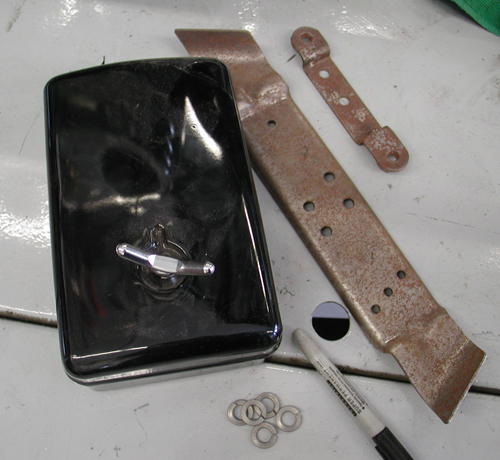
I also attached the Pauchco toolbox strap to the chain side of the bike, since the pipes would interfere on the right. It worked out perfectly for an additional installment point for the chain guard.
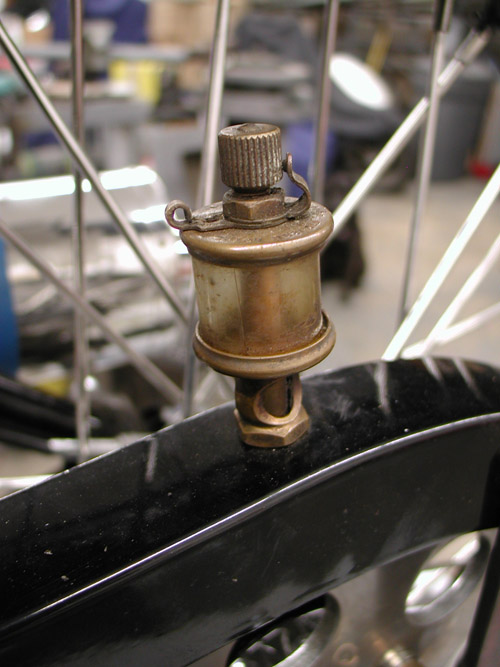
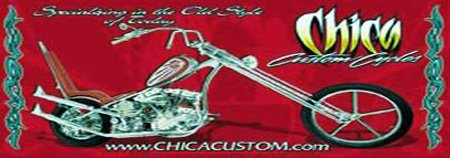
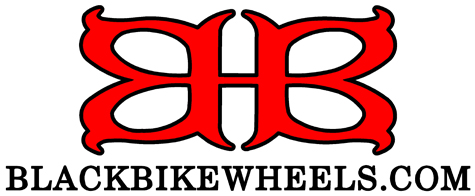

Next midnight run in the shop included grappling with mounting the Crime Scene taillight. It's a cool bastard, but I didn't have anything to mount it with. I dug through old boxes of parts, stock license plate rings, mounts, you name it, until I found an old rubber mount for license plate holders. It was already drilled for my three-point mounting taillight triangle. I found a thick license plate backing plate and went to work.
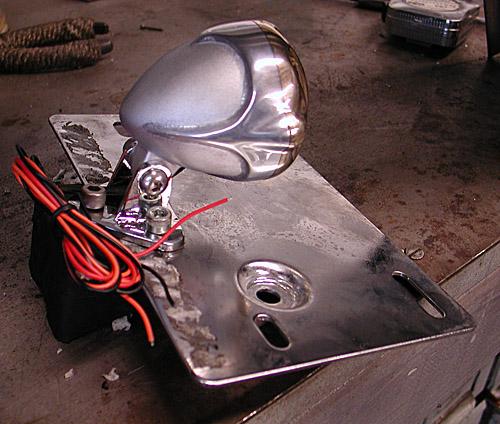
I drilled it to catch two of the Crime Scene holes and held the taillight over the license plate. I thought I had it made. I drilled the fender so the lip of the license plate will hang just slightly over it, for a proper, readable angle. Not sure I was successful. We'll see the first time I'm pulled over for speeding in Wyoming.
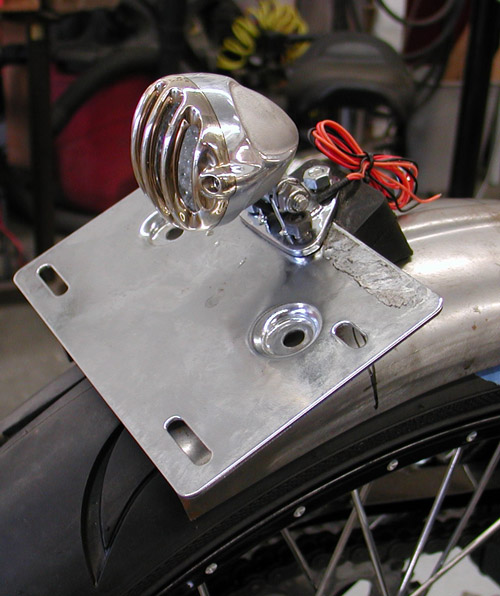
The one item I missed was the spacing for the bonaroo cool license plate ring. I'm not sure I didn't drill the holes too far into the plate, but I was thinking about strength and not bling. From that point, I moved to making fender rails. I can't do anything status quo. So I drilled corner holes in the backing plate, machined more brass, cloverleaf stock with 5/16 coarse threads and bent tabs and mounted them to the frame. Sorta crazy, but actually strong.
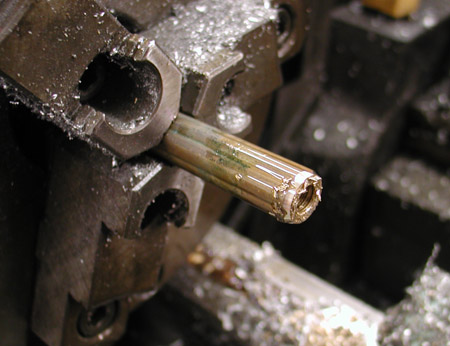
Evan at Power Plant Motorcycles on Melrose in Hollywood coached me on cutting threads in brass. “You need deep thick threads, so don't cut fine threads in brass,” Evan said. “It's soft.”
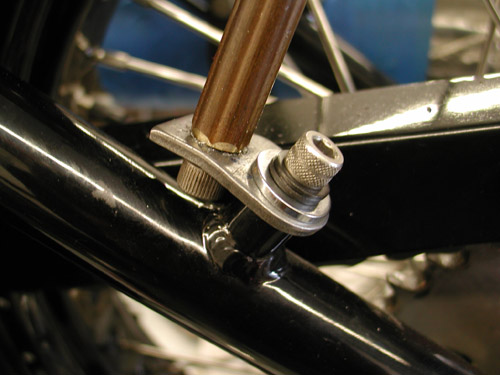
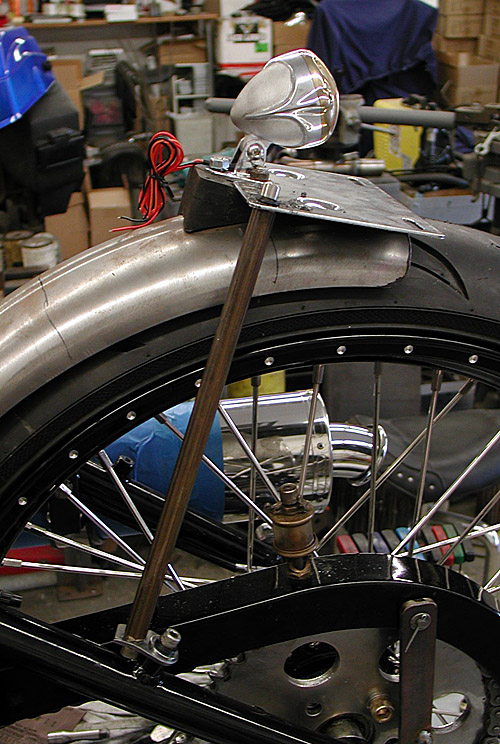
He also showed me a trick on his new antique lathe for centering cutting bits, which I'll never forget. I'll demonstrate in another tech in the near future. His shop was also busy, when I last stopped in. He builds vintage bobbers with very cool hand- made components. No CNC billet shit for Evan. Watch for his Chopper Challenge feature bike to show up on the pages of Cycle Source.
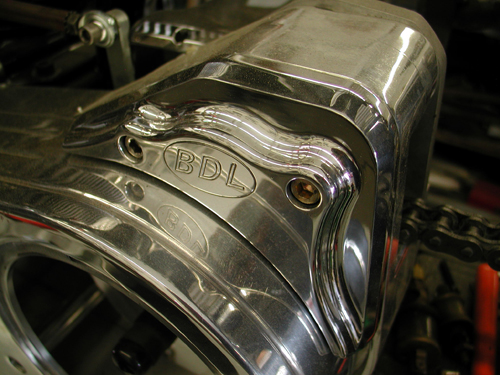
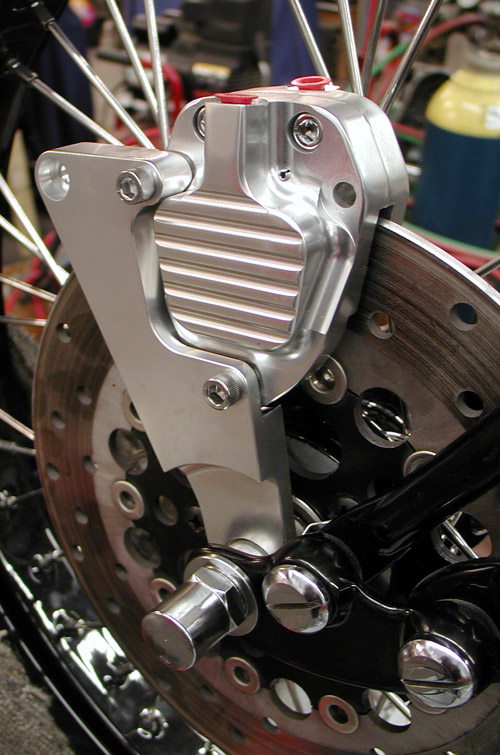
The guys at BDL helped with a super deal on a GMA front brake caliper, bracket, and hand lever. Unfortunately, they only make a springer bracket for the right side, so I modified for the left and built my linkage. Dealing with a narrow Paughco Springer and a front brake is a challenge to fit everything and center the caliper over the rotor. I still need to machine an axle spacer. I also need to deal with this billet bracket. I'm looking for some super cool art deco piece to bolt up front, like a hood ornament from an old Packard.
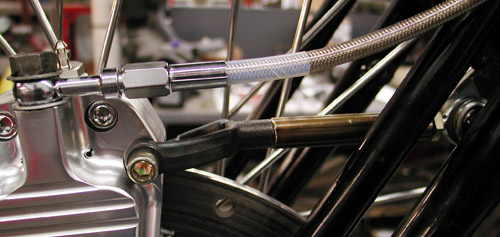
I had to deal with the suicide clutch situation. I had a vintage H-D rocker clutch system, minus the linkage and spring. I made the linkage with a spare Paughco toolbox-mounting bracket. Then while digging around, I discovered what I thought was a regulator mounting bracket. It would work perfectly for the regulator and had the space, and holes drilled for a clutch cable bracket. I went to work digging around for the perfect cable guide.
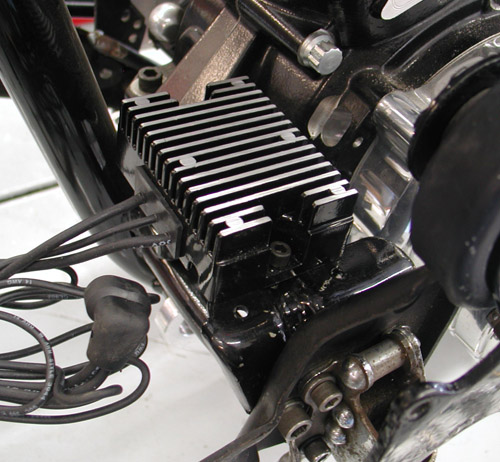
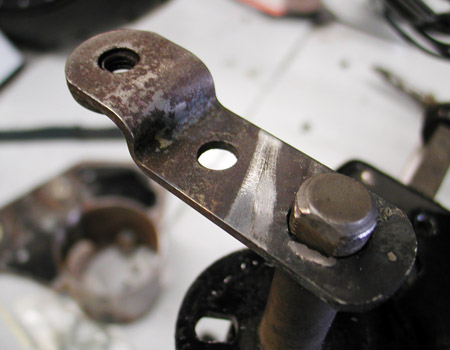
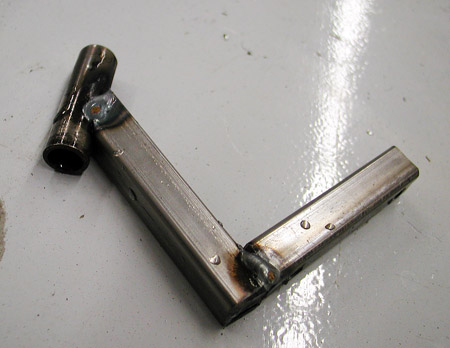
About this time, the Laughlin River Run surfaced and I rode my King into the desert. Two weeks later, I was called to duty on my Sturgis Shovelhead chopper to ride back into the desert to Cottonwood, Arizona for the Smoke Out. On the way I helped a couple broke down in the desert with a wiring problem. As we tinkered with his rigid Sportster, fulla devil tails welded everywhere like handles on wrought-iron furniture, I noticed his suicide clutch set up and his linkage and it gave me some good notions for a cable pinching system.
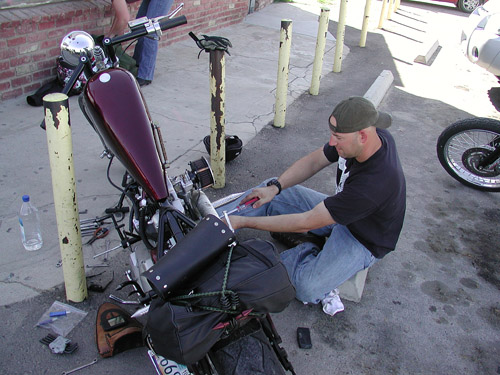
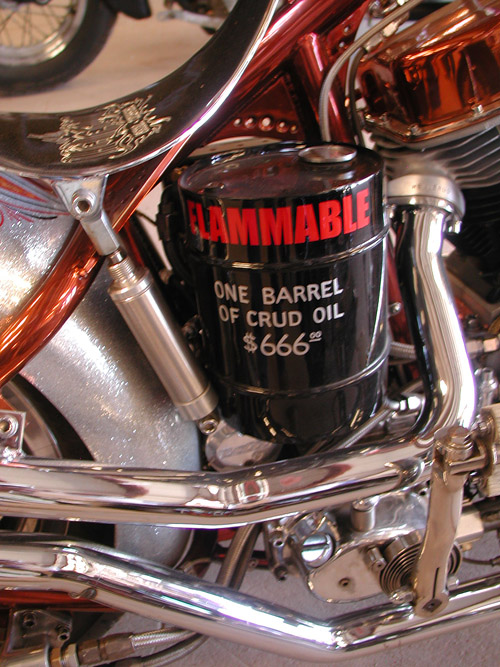


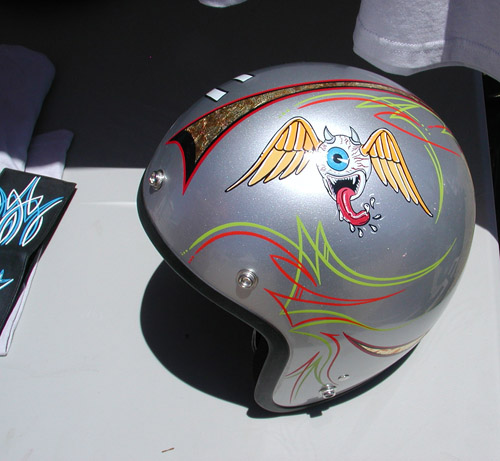
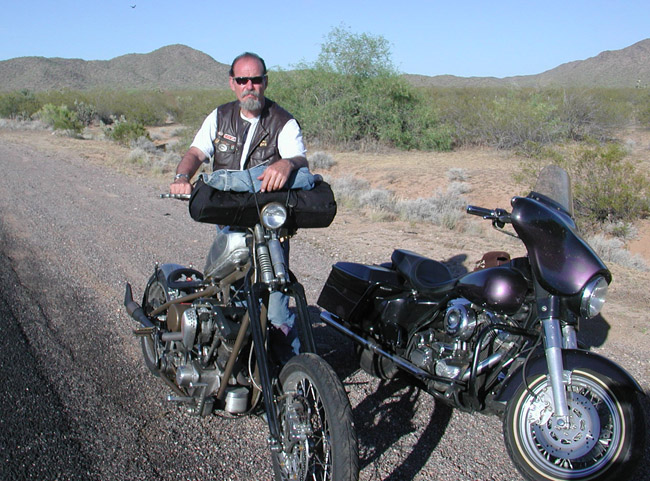
Between Laughlin and Cottonwood, I finally rolled around to cutting the front of the tanks to make room for fork stops with the Paughco narrow springer. As it stood the springer stops would smack the Factory Racer tanks, and my turning radius was shot. I went to work with a Makita cut- off saw and a plasma cutter to slice a new piece of 14-or 16-gauge steel for the replacement. The tanks were painted and that fucked with my MIG welding. Always clear the paint away from the welding area. The smoke from the heated paint messes with the pure oxygen and gas required for proper penetration. I'll work on that more with the next tank.
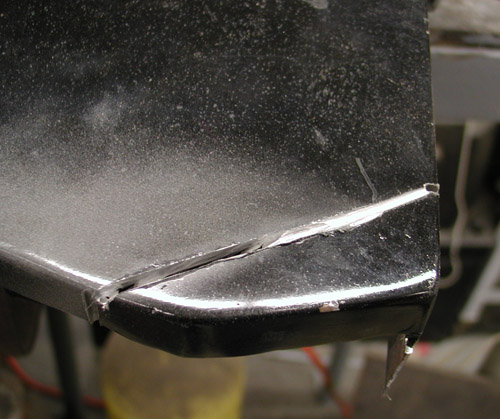
I'm getting close to making some final welds, while praying that a TIG welder will wander into my shop. But first, I needed to drop in the Baker N1 drum for 5-speeds. This is the simplest modification on earth. It's so easy even I could do it, amazing. These N1 drums… well I'll let Trish Horstman and James Simonelli tell you the facts:
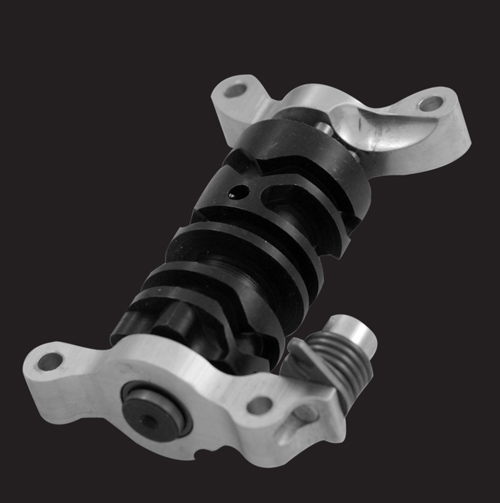
Five years ago we developed the N1 drum for drag racers and street racerswho used our 6-speed overdrive. The N1 shift pattern (Neutral-1-2-3-4-5-6) wasdesigned to prevent false neutrals during aggressive 1-2 upshifts by positioningneutral under 1st.
The jockey shift/foot clutch crowd soon discovered the benefitsof the N1 pattern. The big lever ratio of a jockey shift lever desensitizes the feelof the detents in the transmission such that finding neutral is a crapshoot withbad odds. With neutral on bottom (or all the way forward), the jockey shifter canmindlessly tap all the way down to neutral thus allowing him to put both feet onthe ground as he rolls up to the stop light.
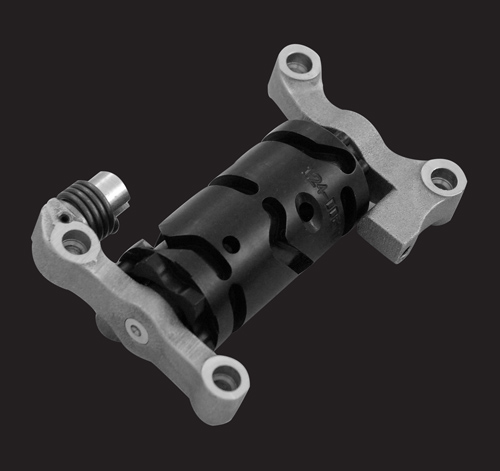
Today, a whole new crowd is realizing the benefits of the N1 pattern. Pingel’selectric shifter is slicker-than-snot and appeals to racers as well as those withrestricted movement in their left foot and left hand. Utilizing an N1 drum inconjunction with Pingel’s electric shifter makes finding neutral (with the solenoid)seamless, and yields a solenoid-actuated shift system that almost makes footshifting obsolete.
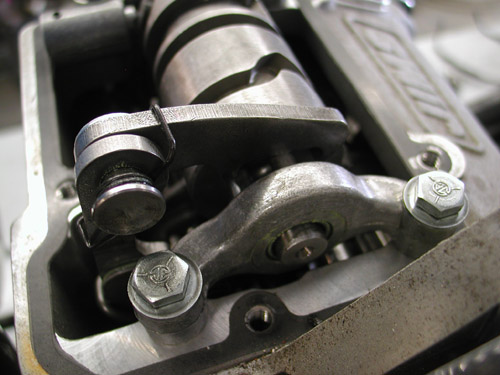
PN DESCRIPTION FITMENT
5-6QT-A N1 drum & pillow block assembly, 6-speed BAKER 6-spd overdrive except*
5-6QT-A1 N1 drum & pillow block assembly, 6-speed *Old 6-into-4 (S&S case) &Frankentranny
124-OD6RN1-A N1 drum & pillow block assembly, 6-speed RSD right-side Drive 6-speed, 2ndgeneration
124-DD6N1 N1 drum & pillow block assembly, DD6 DD6, all
2-5R-N1 N1 drum & pillow block assembly, 5-speed Single pole neutral switch 5-spds
2-5RL-N1 N1 drum & pillow block assembly, 5-speed Double pole neutral switch 5-spds
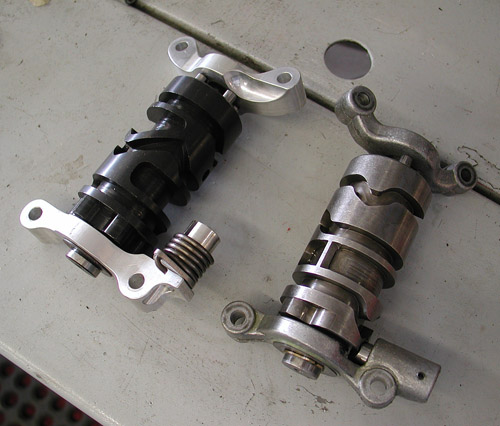
FEATURES/NOTES:
– N1 shift system option available at no additional cost with purchase of a complete transmissionor builder’s kit
– 5-speed N1 shift systems fit H-D 5-speeds and BAKER 5-speeds
– For aggressive shifting we also recommend the use of our anti-overshift ratchet pawl, PN555-56A for 5-speeds through 1999 and 555-56L for 5-speeds 2000-up. For example, this pawlmechanically prevents an unintended 1-3 up shift during an intended 1-2 upshift
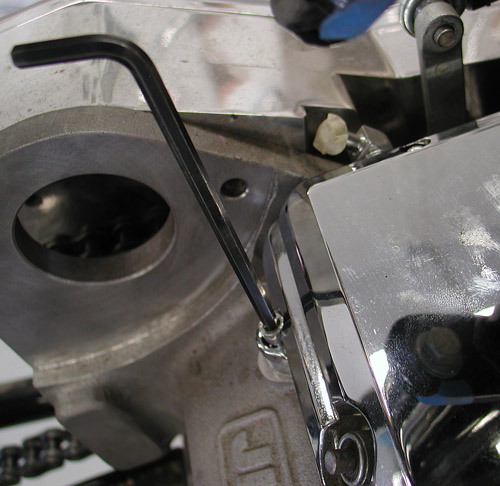
Okay, so I popped off the ¼-20 Allens off the top of the tranny cap. Since, within five fasteners there were three sizes, I placed them neatly in the battery pan to prevent mixing up the formula. The lid came right off.
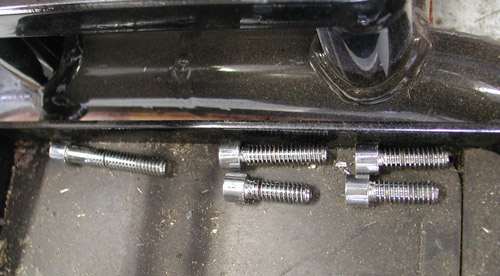
Then the four 7/16 hex heads need to be removed and the drum and pillow blocks came off as a single unit. Don't forget to lift the shifting arm, and keep it up when you replace the drum.
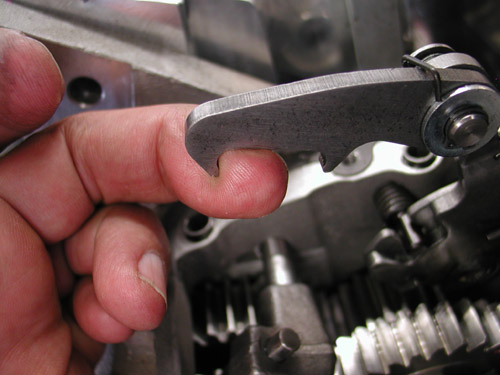
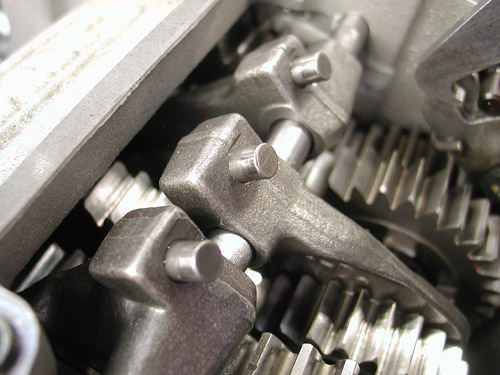
It might feel slightly snug to remove since there are guide inserts pressed into the case to hold the drum perfectly aligned. I studied the drum as I removed it and set it in exactly the same position on the bench to insure I put the new N1 drum back exactly the same way.
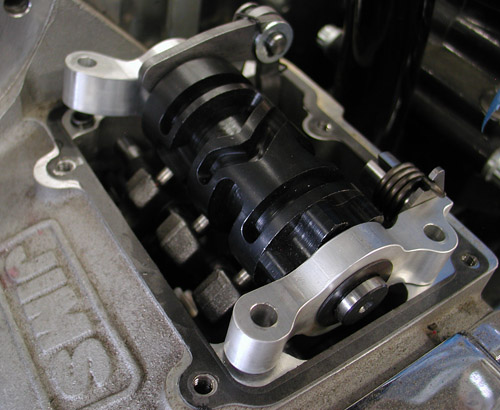
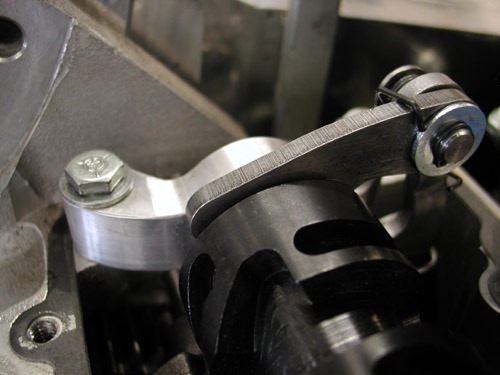
I told myself the old mechanic's rule as I replaced the drum and aligned the shifting forks: Don't force anything, jackass. I carefully aligned the shifting forks, then made sure the pillow blocks fit comfortable over the inserts before rolling the fasteners back into place and torquing them to 130 inch pound of torque or 10.8 foot pounds.
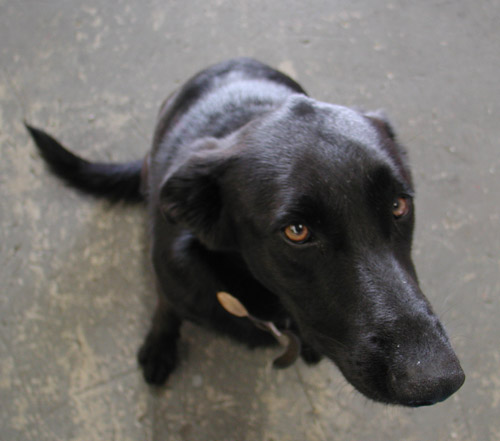
I smeared a dab of tranny oil on the lip of the transmission lid and slipped it into place, then tightened the fasteners to 130-inch pounds of torque. Oh, I forgot. I replaced the standard vent with something brass, mechanical, and vintage. What the hell. I'm going for that vintage appearance.
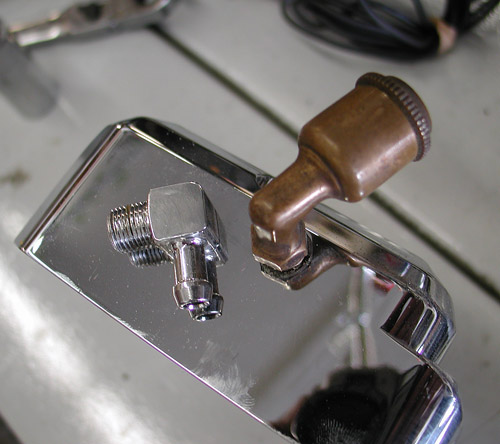
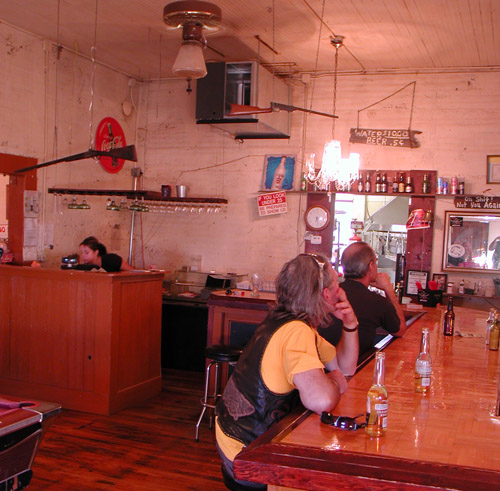
That's it for this installment. Next, I will install an Exile sprotor rear brake and 48-tooth sprocket. I'll finish all my welds, strip her down, and head to powder coating and paint. I have the color scheme down. It's going to be wild. I've also promised not to hit any more events between now and Sturgis for maximum shop time. We'll see if I run out of whiskey and women or not. Hang on.
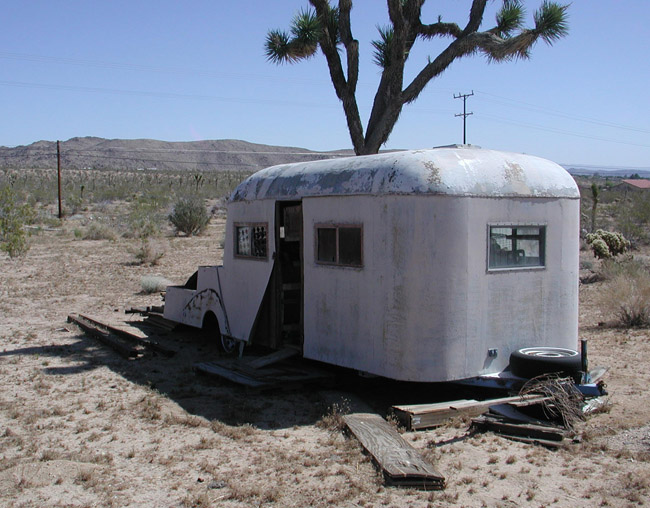
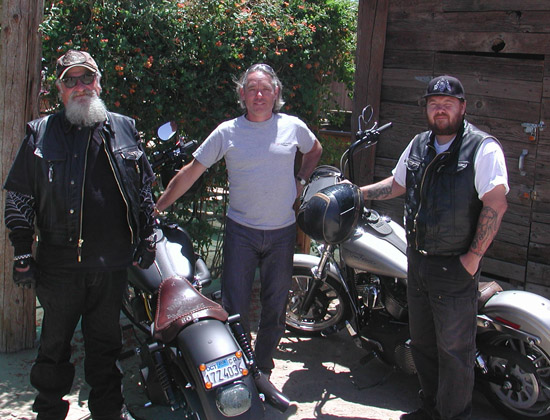
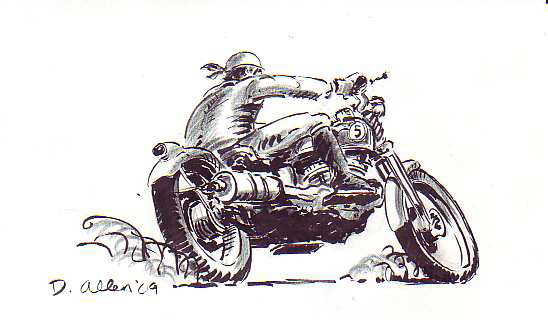
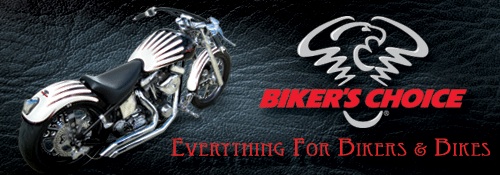
5-Ball Factory Racer, Part 5
By Robin Technologies |
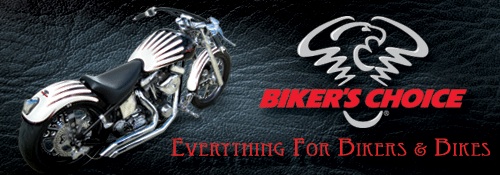

Last episode I was hit hard with life's bullshit obstacles to freedom and creative expression, but that's how it goes. I generally build at least one bike a year and each one represents a milestone of sorts. Or each one represents another year in the life and times of Bandit. I'm not unique. This notion applies to everyone and every project from building a new home, to building a boat or finishing a book. We're so damn lucky to have the freedom and resources to accomplish our goals, small and large. As you sit back and relish any accomplishment, you know it represents a moment in time–hopefully a good time.
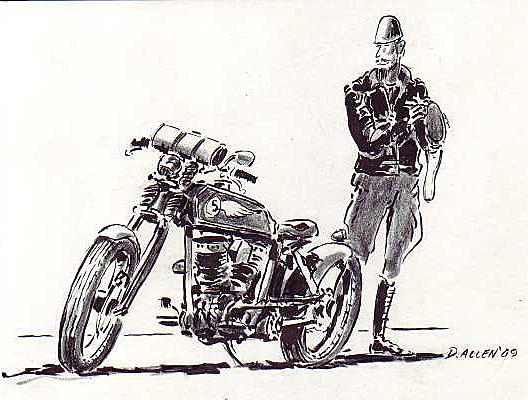
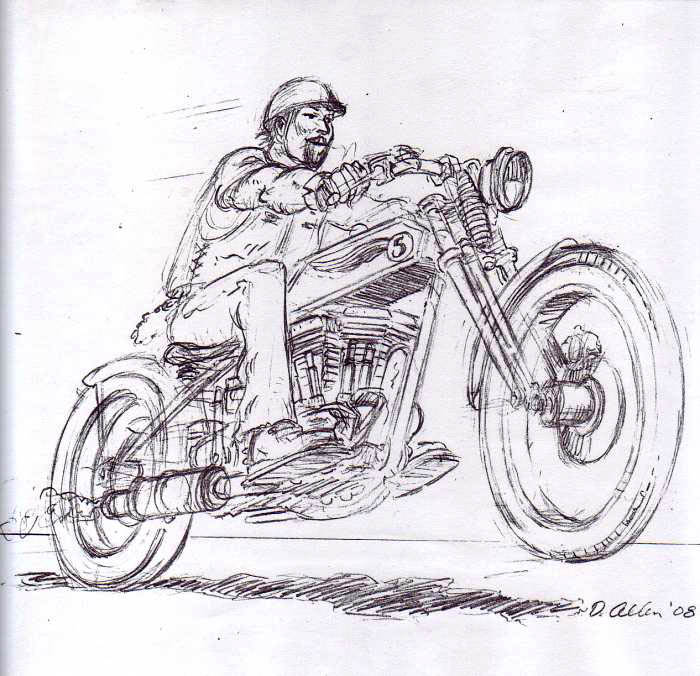
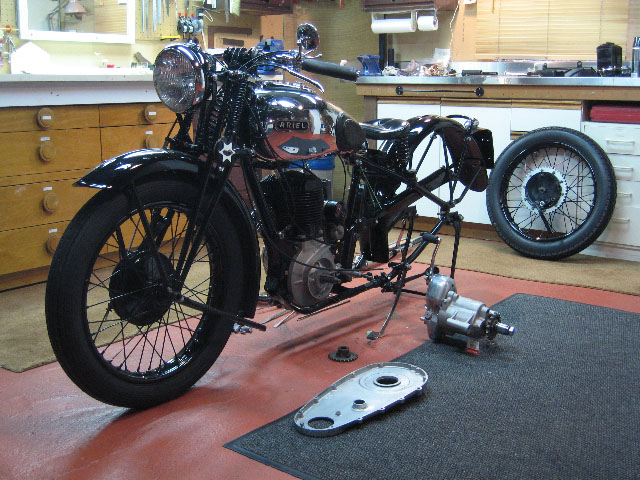
That's very kind of you to offer to runmy bio but honestly it makes me wantto take a nap just thinking about it.How about a pic instead of my stumppulling flathead single '40 Ariel? Wewere born in the same year and havebeen working together for about fifteenyears to keep my bank account drained.As the bike approaches completion itappears to be getting younger and youngerwhile I am definitely getting older and older!
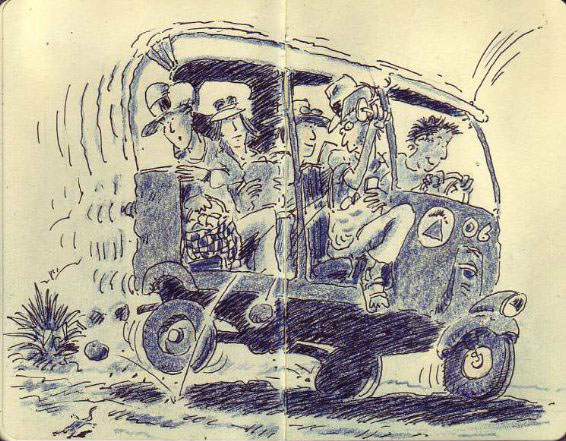
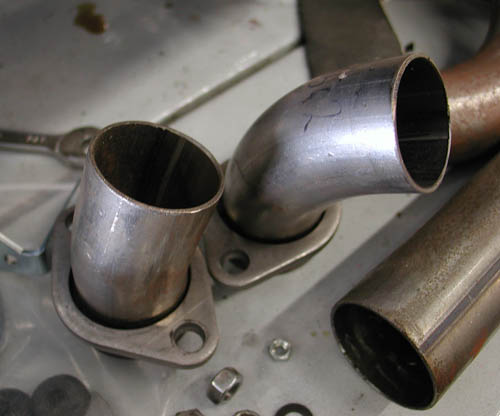
So, recently we tore the March page out of the Calendar and flew into April. A running Racer by the end of April–for the Smoke Out in May, is the goal. The pipes were a major obstacle, yet Jesse James, Illusion Cycles, and Roland Sands inspired me.
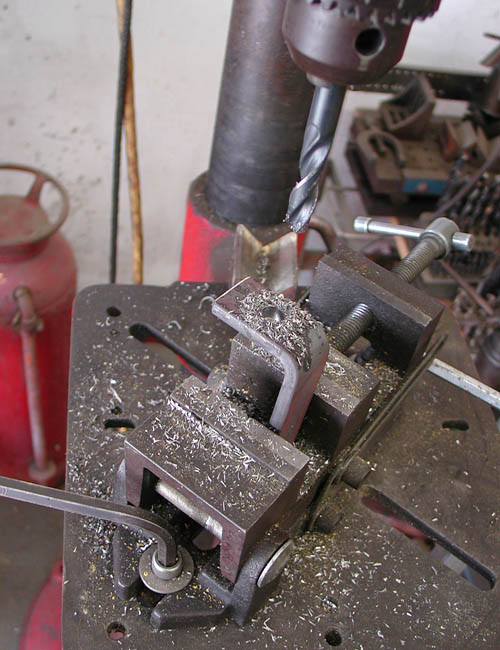
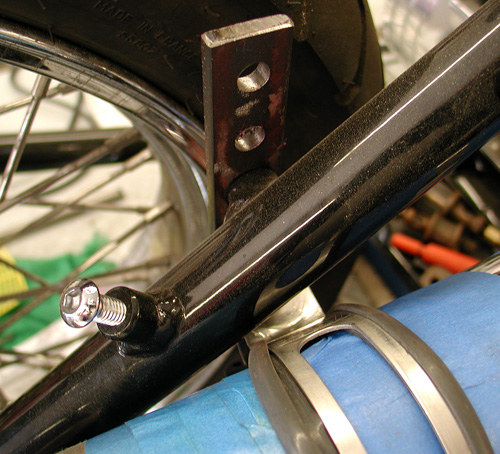
I spotted a tight shotgun system on one of Rusty Coones' Dyna Glide custom built in his Illusions shop. That's the direction I wanted to go for the racer look, not along the bottom of the frame in stock 1915 fashion. The muffler on Rusty's bike was a short/short Supertrapp developed with an exhaust guiding cone built by the Illusion team. The two-into-one pipe was designed at WCC, but I decided to give my own spin to the action for the Crazy Horse 100-inch engine.
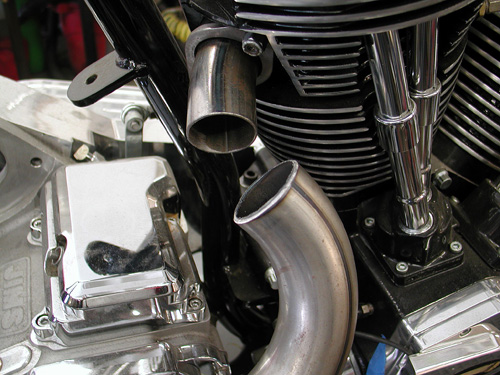
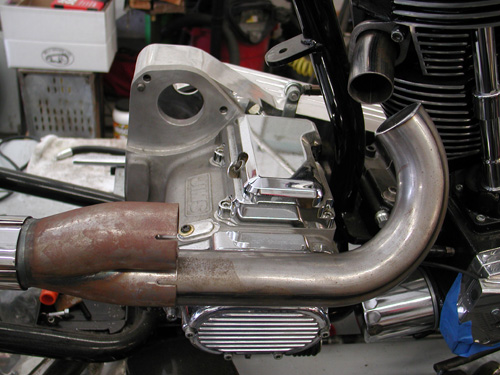
I also recently featured a bike built by Roland Sands with his own shotgun Vance and Hines system. Check it out. It also has a very short muffler system, but I had an all-stainless Scorpion sport bike muffler from the mad designer John reed.
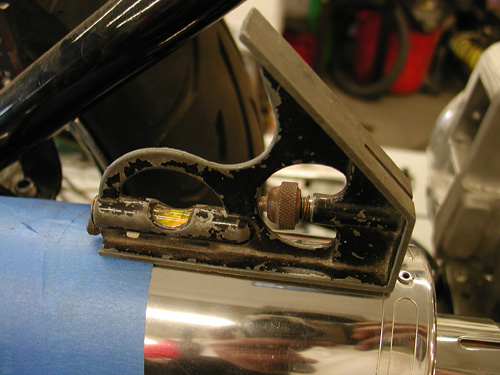
With Roland's design inspiration, I went to work. I had to make the system run tight to the bike, so ultimately I could install a Baker Drive kicker system to the JIMS 5-speed transmission. It had to run high enough not to mess with the rear axle and not too high for leg burning threats. I had one break; the Crazy Horse engine was designed with the intake manifold running out the left side of the engine. That allowed me to manufacture pipes as high as I wanted–watch the legs, damnit.
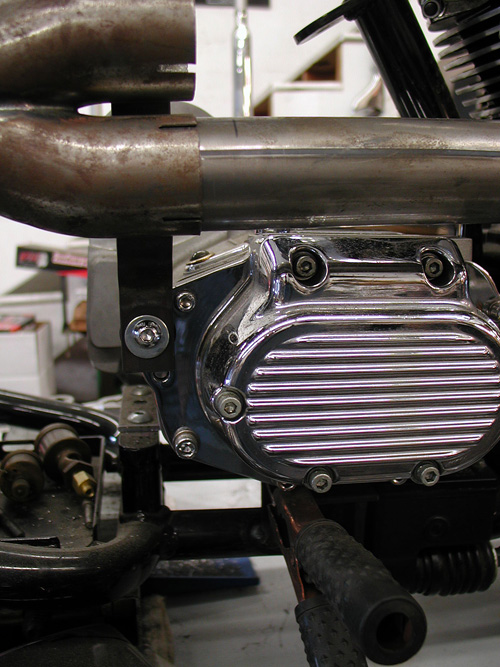
Making pipes is a tricky business. This system is teamed with lots of exhaust manufacturers, so I initiated a phone conference with D&D, and they supplied me with various ends and bends to give me a head start. Vance and Hines and WCC were involved with the design and inspirational aspects, and the Boys from Bassani stopped over for lunch and brought a hand full of bends and a chunk of muffler tubing for my speedometer mounts, a very diverse team. Plus nowadays, when you mess with pipes, the diameter fluctuates from below stock diameters to over 2-inch Bonneville racing exhaust performance demands. I took a day dealing with various sizes and ultimately decided on a 1 ¾-inch system to the two-inch muffler opening.
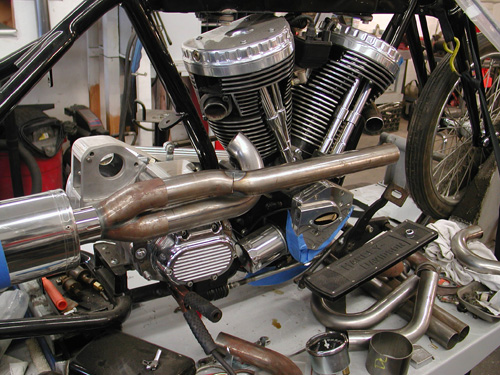
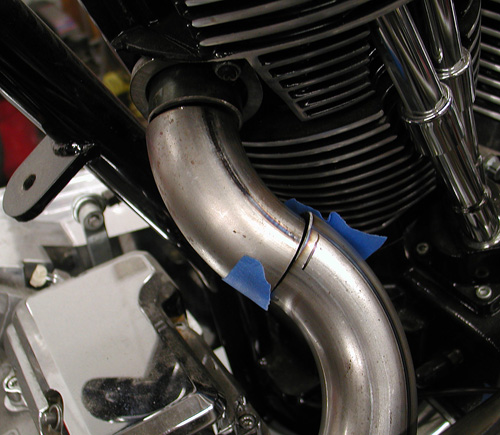
Then I had one of those calm and serene days in the shop–everything fit. It's a Zen thing, when the stars are aligned, and I drank just the correct carefully measured amount of Jack Daniels the night before. For some strange, inexplicable reason, I was tranquil with the dogs wrestling at my feet. The R&B Sirius station shop background music didn't spin any Michael Jackson tunes, and only the 4-tops and Jerry Butler lured me into a false sense of mechanical confidence. I patiently cut, ground chunks of pipes and brackets, then tacked them into place.
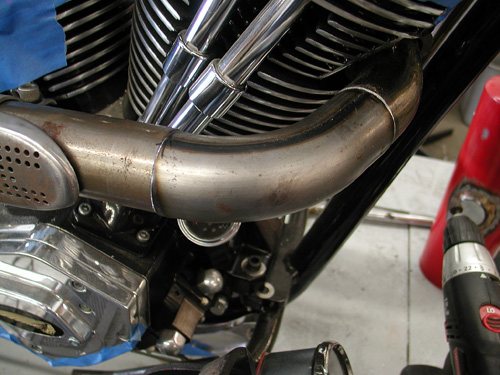
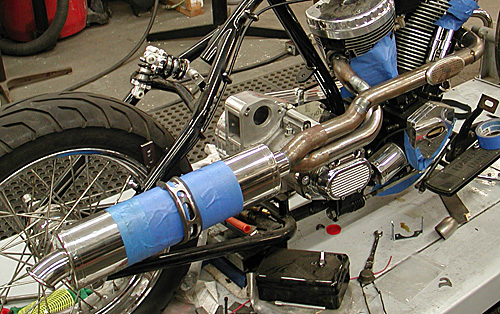
I've been making exhaust systems for about six or eight years, and each year I learn. For instance, I was through the roof to find Hooker Header alignment sleeves, only to discover they hinder performance. That meant I had to move more slowly, meticulously and make sure each segment fit perfectly. I also learned that exhaust wrap can also hinder ultimate performance, by being a heat transmitting barrier. Plus I'm still working on my MIG, pipe-segment welding skills. This year I'm going to clamp a bunch of pipe chunks together and weld them at different feed speeds and electrical settings. I'm determined to nail it down.
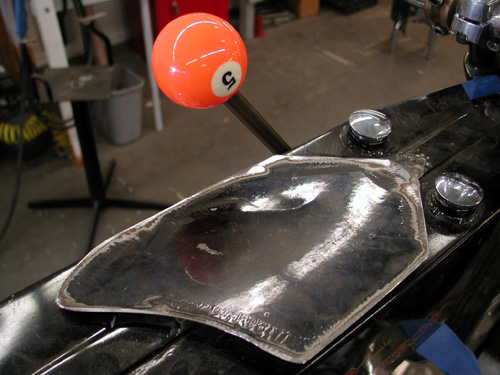
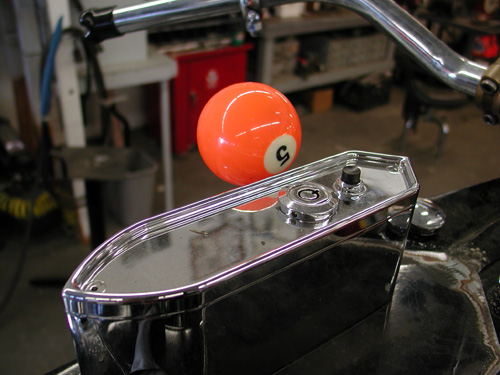



Next, I moved onto a dash plate, cut with a plasma cutter out of a chunk of 16 or 14 gauge sheet metal. My crazy thought was to install the Phil's Speed Shop ignition system onto this plate with the Bikers' Choice Speedometer. In 1915, Speedometers and the constant loss oil pumps were mounted to the top of the tanks, right out in the open, so I decided to follow suit.
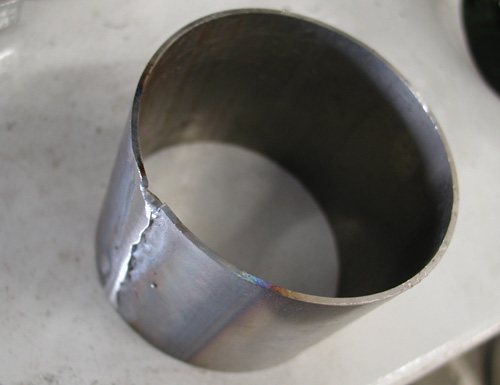
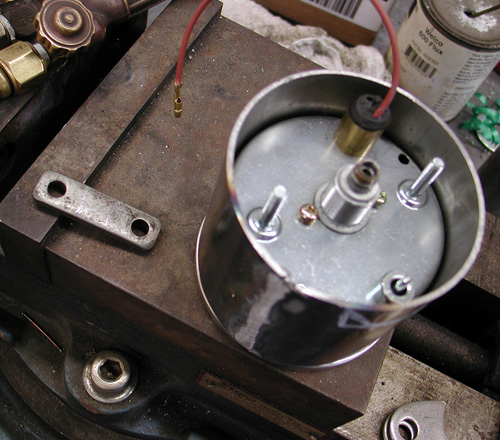
Bassini supplied the tubing for the Speedo, but I needed to be reduced the diameter a 1/2 -inch. I cut it with the Makita and pinched it down until the speedo fit in, and I could still wrap it with something to prevent vibration from beating it to death on the roads to the Badlands.


Phil's Speed Shop supplied me with a template so I could mark the holes and weld in studs to hold the ignition system down. It housed, circuit breakers, ignition switch, starter button, starter relay, neutral light and high/low beam switch.
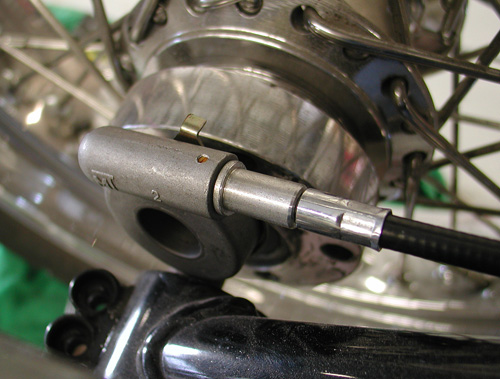
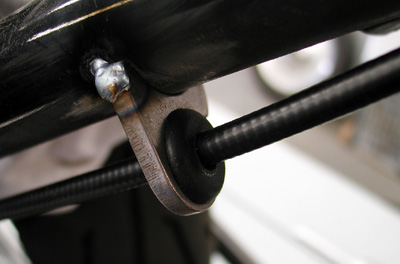
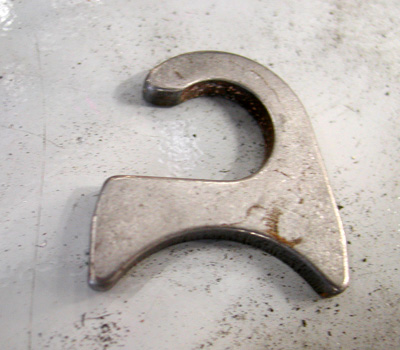
I ran the Biker's Choice speedo cable and drive off the rear wheel in 1915 fashion, but with late model components. I used LA Chop Rods cable guides and grommets tacked to the frame. I played with the plate and position for hours and hopefully got it right. I also cut a notch in the Bassani Speedo mount so I can hopefully reach the trip gauge adjuster. It's going to knat's ass close. In each perplexing case, I shot for functioning symmetrical positions, that don't interfere with other components, like turning the bars.
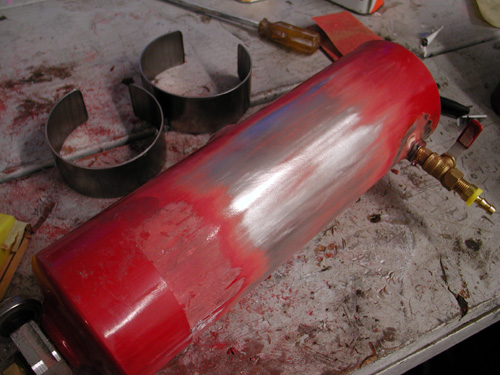
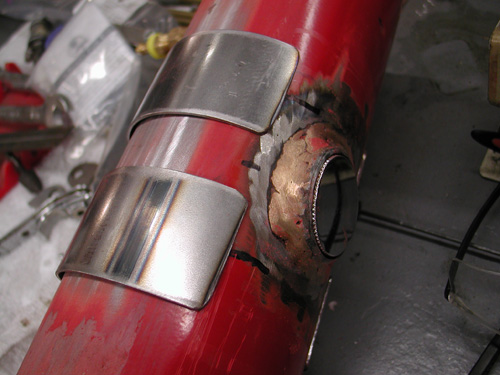
Next, I had the spare gas tank ready to rock, but needed to mount it above the bars. Talk about angst, I looked around for something to use for mounting, like other fire extinguisher clamps, then it dawned on me to use the an old set of handlebar risers, upside down. I found an old set of Jammer risers and bolted them to the bars between the DBBP bronze risers, so far so good. Then I cut them, estimating the height needed to clear the bars, but I was wrong. What happened with harbinger to my Zen aura?
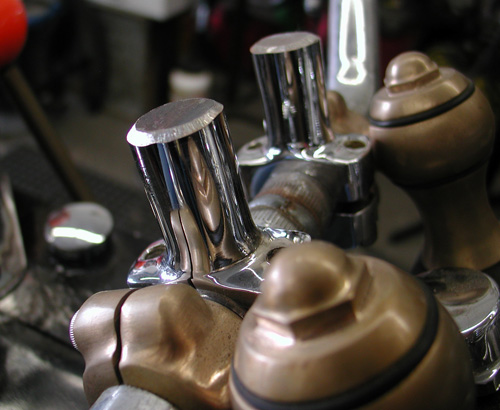
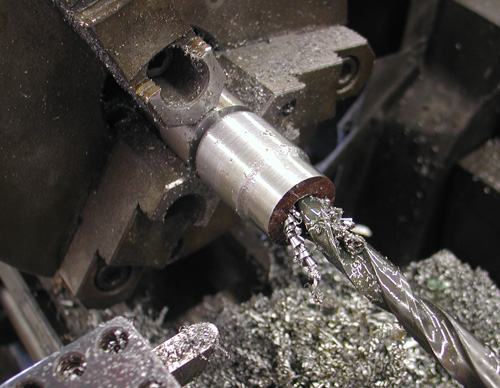
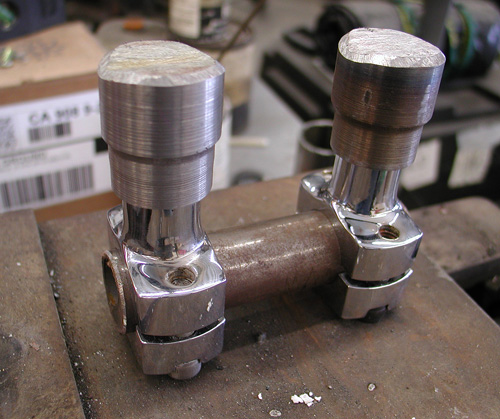
I don't know about other crazed builders, but often a glitch turns into an opportunity. I turned to my lathe to cut a couple of extensions. They widened the base for greater strength. I reached out to NICK Trumbo at Bassini exhaust for a couple of straps. My notion was to weld the brackets to the straps, so if something went wrong, it wouldn't crack the tank and create a dangerous gas leak. I've had my problems with gas leaks in the past.
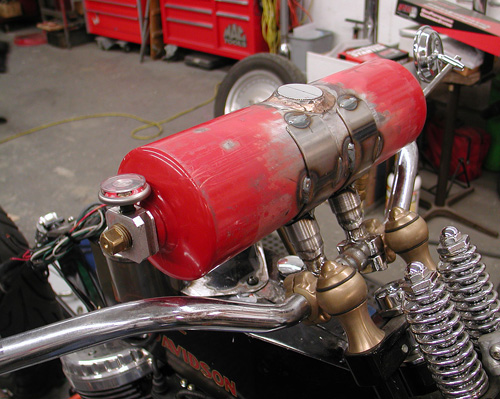
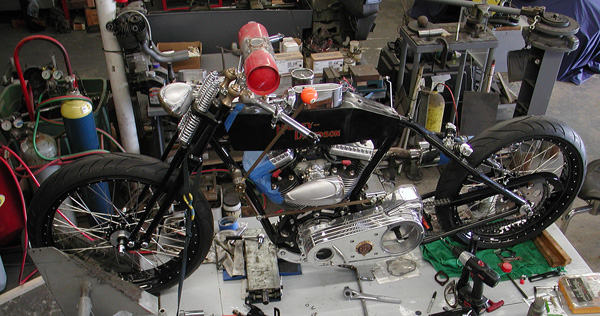
There you have it. Next, we'll mount the fantastic Black Bike Wheels (Avon Tyres), with GMA brakes from BDL, slice the Tanks for fork stops and Chica is going to build a Factory Racer ribbed fender. Rock and roll.
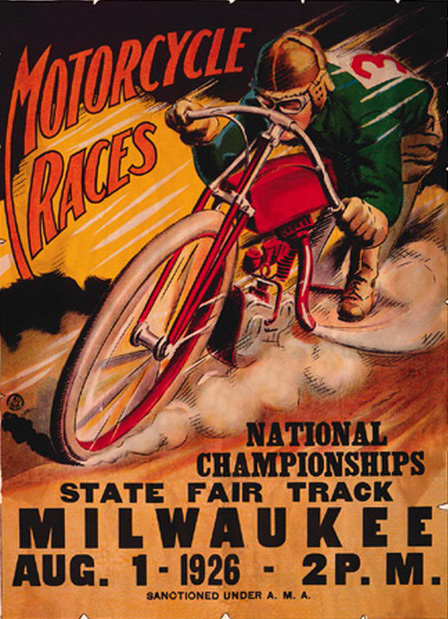
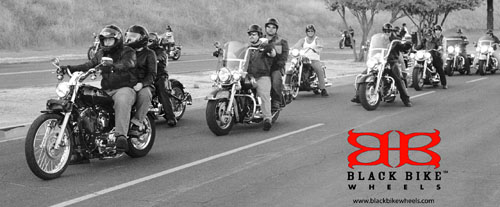

5-Ball Factory Racer, Part 9 Final Assembly
By Robin Technologies |
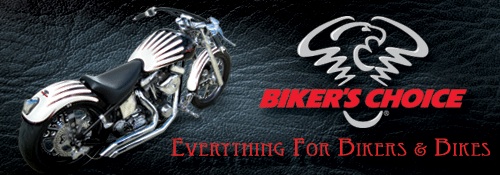
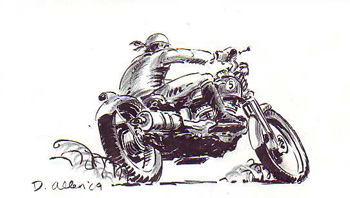
Every custom motorcycle build is an adventure. It takes me from one crazed time in my wild life to another. Fortunately, I'm not spilling my guts about another woman I lost during a knuckle-busting build. But this build did represent turning points. I'm about to step off into my 62nd year and sign up for Social Security. It also represented our stinky economy, and for the first time I pulled the plug on riding this bike to Sturgis.
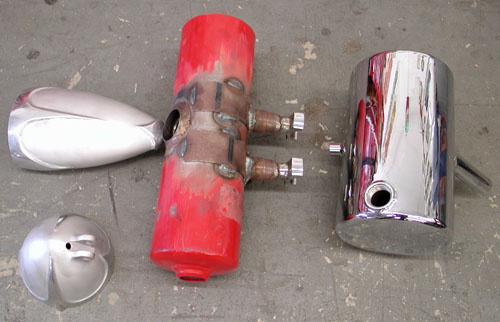
Imagine for a second, the middle of July. Days were long and hot, and the Bikernet shop boiled with activity. The Sturgis deadline was fast approaching. I needed to plan stops, hotels, food funds and a place to stay in the Badlands. Then suddenly we were forced to shift gears. Actually, we took the planning process out of gear. One day, I scrambled for the finish line; the next I coasted. I couldn't find the stress switch for a week and relieve the pressure.
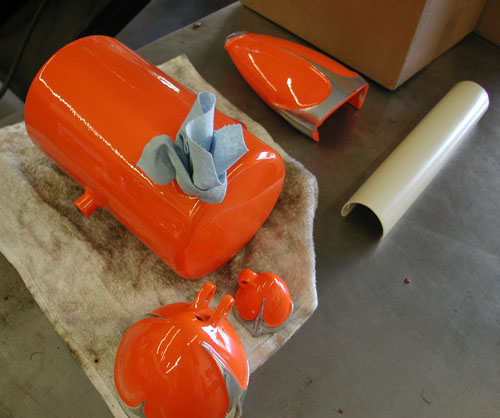
Most of my parts were baking in the Tony Pisano, Worco powder-coating ovens. It took me a week to realize the Sturgis Rally would survive without me, and I could relax. I was no longer under the gun to finish this build and risk my life riding an untested motorcycle halfway across the nation. Then it dawned on my feeble brain. I had a terrific opportunity to finish this bike and test it for a year before riding into the Mojave Desert and across several Indian reservations. Plus, I could kick back and enjoy the summer, pressure- free. I bought an ice-cold six-pack of Coronas, a couple of fresh limes and grabbed a sun tan. Not bad.
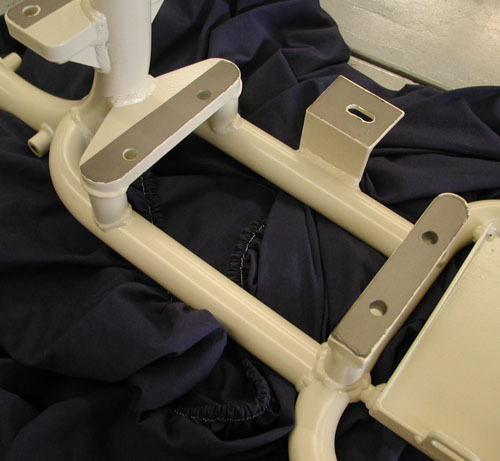
Tony is a pro powder-coater of the finest order and knows what it takes to tape off motor mounting plates and plug threaded holes. He saved long days under a grinding wheel. The powder work came out supreme. This year I tried something new. I powdered even the sheet metal, then asked a pro to paint panels on the tank and a flat black stripe down the Chica rear fender. He handled that aspect in a flash. Then I turned the job over to George the Wild Brush for the 5-Ball Racing logo on the tanks and pin-striping.
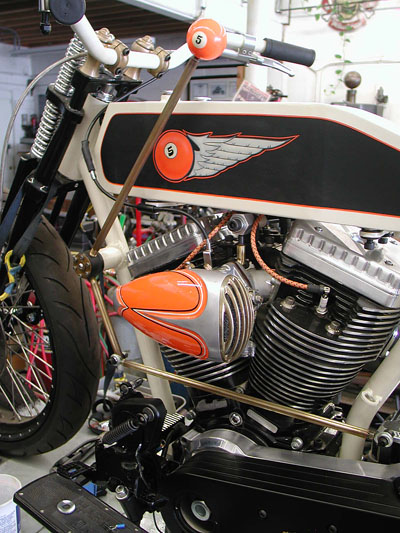
George drives around Los Angeles in an old Toyota truck with a camper shell, the home of paint headquarters. He folds down the tailgate, uncovers his vast, dripping assortment of paint and goes to work. He's old school to the bone. He pinstriped the giants' drag race funny cars in the '70s.
Here's where my fuck-ups began to surface. After the tanks were powder-coated, I decided to test them for leaks. I had planned to coat them with a sealer, and received Kreem tank sealer from Bikers Choice.
Here's the quandary: You can't seal tanks and then have them powder-coated. It might all go to hell in 400 degree ovens. So I held off. Then I decided to hit a local radiator shop for the test. We discovered one small leak where I welded in a rubber-mounting bung in the bottom. I ground it clear of paint and re-welded it. No problem. The painter touched it up for me. It was on the bottom of the tank and I was good to go. I thought.
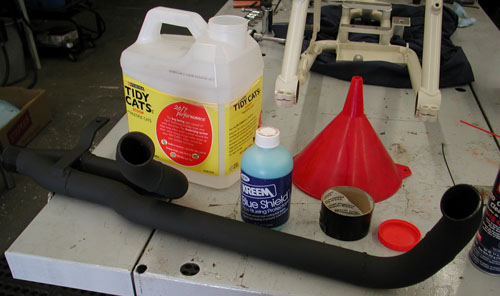
Next blunder: Instead of pressure-testing my handmade exhaust system, I decided to try another sealant available from Kreem and Bikers Choice. It's blue madness and can only be used on new pipes. I followed the directions, but it's a messy operation, and of course, I attempted this process for the first time, after I painted the pipes. What did I learn from these hiccups? Test tanks and pipes before you coat them with anything, period.
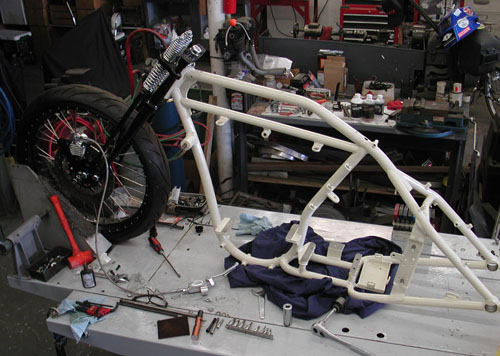
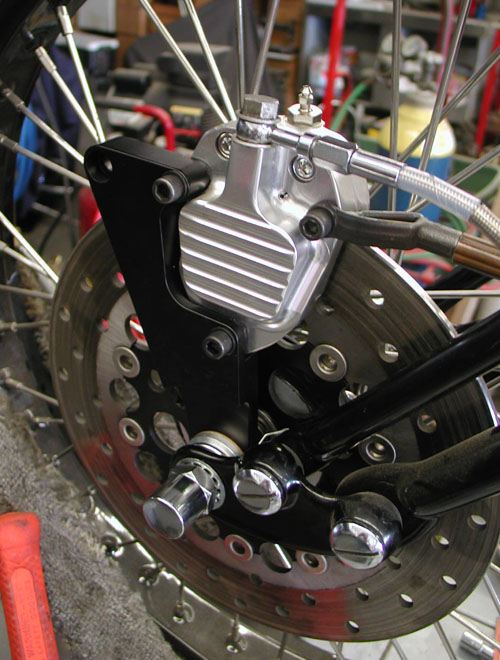
The first item to be installed was the new Paughco narrow, taper-legged springer front end. It slid right into place. If only I had four arms when I'm working in the shop alone. The front end already had the 23-inch Black Bike Wheel installed with a special Avon Tyre. I just needed to grapple with the front end, fasteners, bearings and top crown. No problem. I also installed the GMA front brake bracket and spaced the front wheel for the 14th time. It's a tight fit, and I need something art deco to mount on the front of the bracket. GMA, now owned by BDL, only builds a springer front brake bracket for the right side. I was forced to flip this one over. I could have machined the leading lip off, but I decided it could be used for some unique reflector, or quirky hood ornament. We'll see.
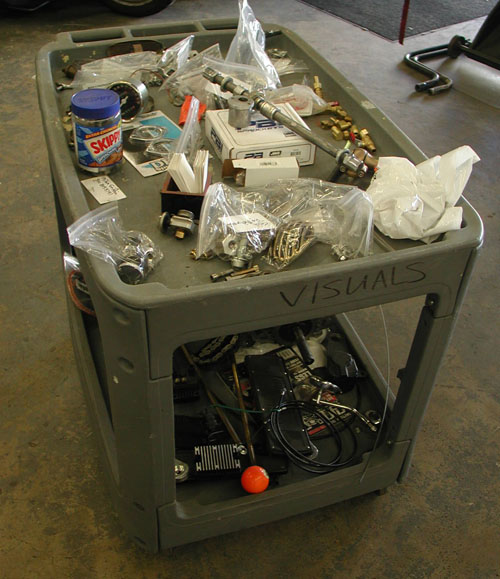
When I disassembled the bike, I carefully collected all the parts on this table. I also zip-locked all my fasteners and wrote their job descriptions on the back of each card. That was seriously helpful during assembly. Next, I dropped the Crazy Horse 100-inch engine in the Paughco frame, with the JIM's transmission and the Baker kicker system installed. Since the chain ran against a portion of the frame, I ordered a ½-inch 24-tooth tranny sprocket from JIMS and installed it with this special JIMS nut, designed with a built-in locking device. Unfortunately, no matter what I did, the holes wouldn't line up, so I safety wired the nut to the sprocket to prevent it from backing out.
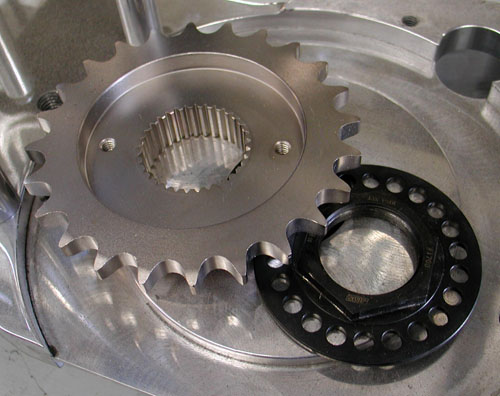
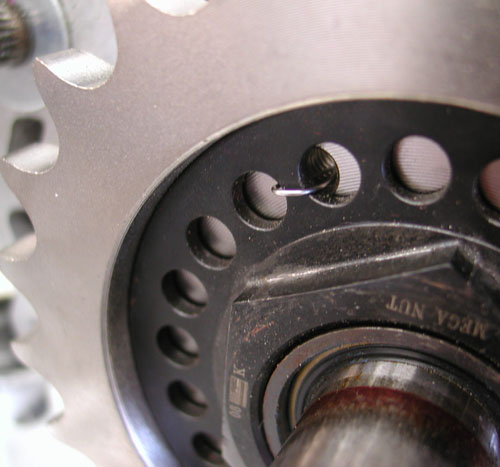
Then I faced one of the toughest assembly jobs, installing the Spyke alternator stator plug in the right engine case. It's easy and difficult at the same time. This time, I smeared the tunnel and the plug with Never Seize and tried to push the plug through the case tunnel. I also carefully backed out the set-screw and scraped any burrs of the case edges. That didn't help, but I ultimately wrestled it into place. I'm always careful of electrical connections, wiring, proper grounds, etc. Nothing leaves us alongside the road more often than electrical problems. So, I don't like pushing and prodding charging components.
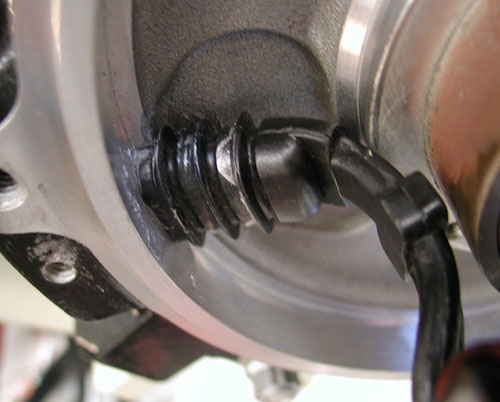
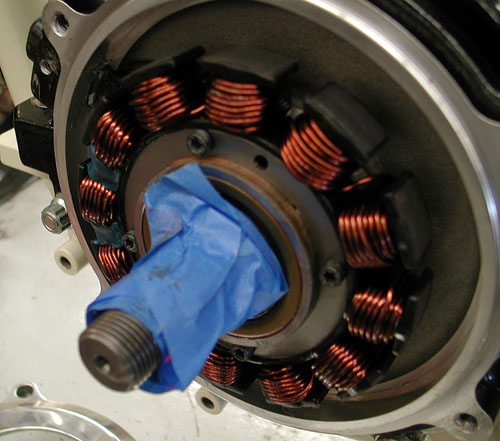
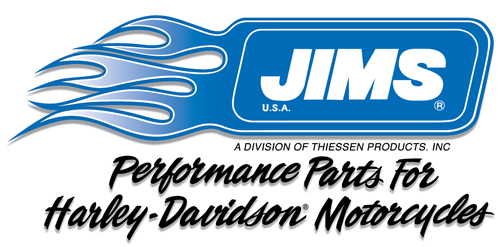

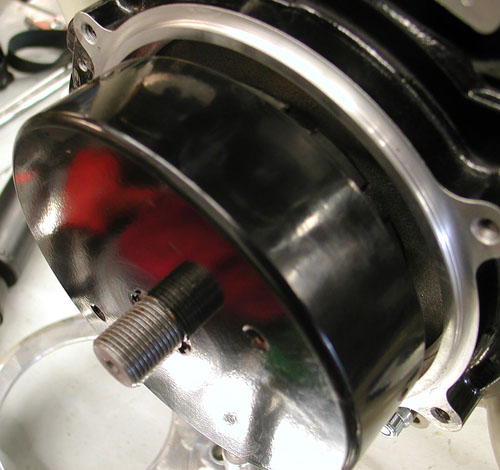
Once the stator was in place, I used self-locking fasteners from Harley-Davidson to fasten it down. Spyke is careful to supply all the proper assembly instructions, but it's always tough with aftermarket engines. Because it was somewhat of a guessing game, I installed the Spyke rotor a couple of times to make sure all the clearances were proper. Then I could move onto driveline alignment and the installation of the BDL narrow enclosed belt drive system.
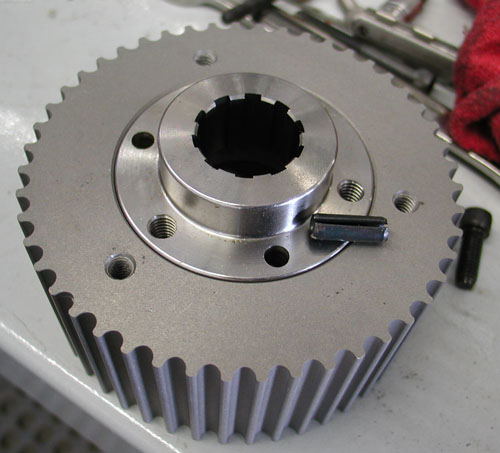
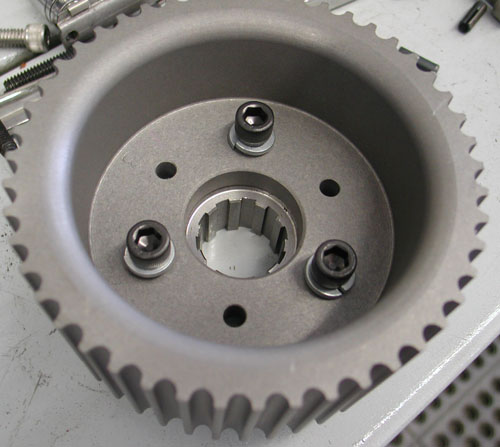

I've worked with BDL components for at least 15 years. They are solid as a rock. I used the inner primary to pull the engine and transmission into alignment. I left both major components loose in the frame until I pulled it up tight with the inner primary. Don't forget the John Reed Code. I use Never Seize on all bolts rolling into soft aluminum. John warned about damaging porous aluminum threads by running hardened steel against them over and over. Never Seize allows them to glide in and out of the cases without stress or abrasion.
With the driveline aligned, I tightened down the rear engine mounts and then checked the front ones for gaps. I shimmed the front motor mount perfectly, then tightened it down.
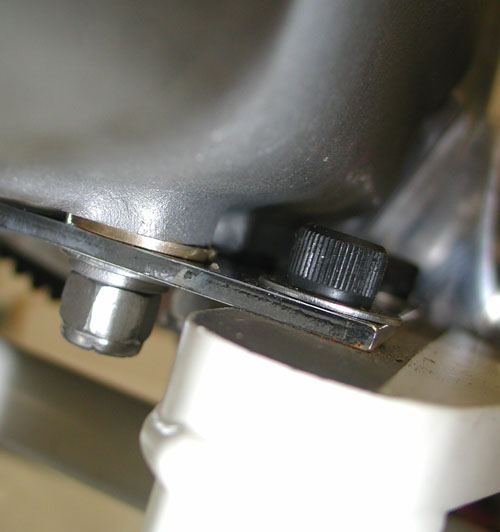
Next, I focused on the transmission. The Paughco mounting plate was tight and the JIMS trans case was fine in the rear, but slightly elevated in the front. I dug around until I found the correct shim washers and drove them under the trans and around the front tranny studs. It's key to go through these motions for proper alignment and to save problems with the belt. It's surprising how easy the BDL system slips together if the driveline is aligned.
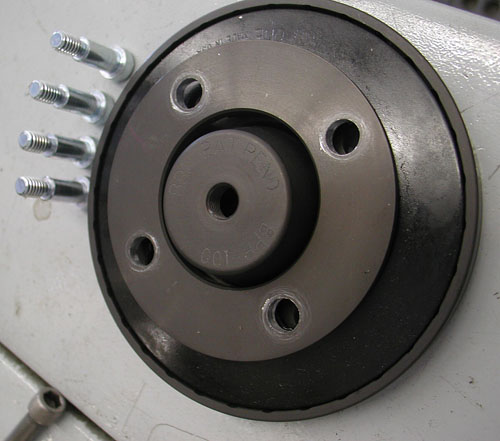
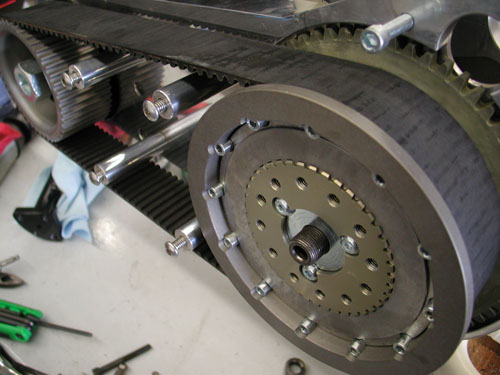
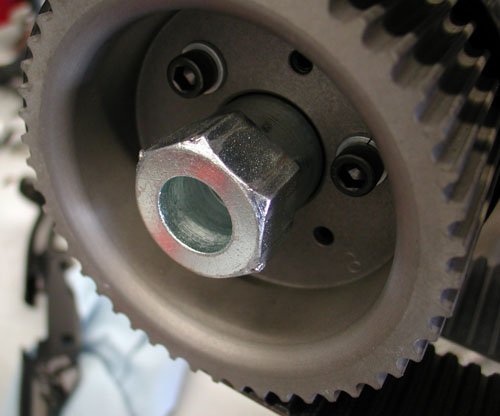
I followed the BDL instructions and bolted the engine shaft insert to the pulley then drove in the alignment pins and tightened down the Allen fasteners. I pulled the pressure plate pins out of the clutch and removed the clutch plates. With the clutch hub and the engine pulley holding the belt, I carefully slipped them on simultaneously. I attached the left-handed clutch nut and tightened it with an impact gun. I did the same with the engine main shaft nut. I turned over the engine and checked belt alignment and pulley alignment. I spaced out the front pulley slightly with a shim and was good to go.
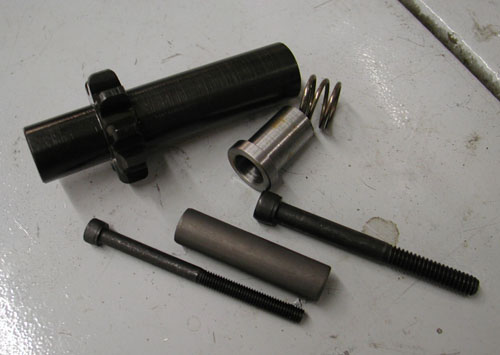
BDL TECHNICIAN NOTE:I received a call from BDL, “You fucked up, Bandit,” Dan said. He pointed out how I didn't mention using Loctite on the transmission mainshaft splines when I installed the clutch basket. “That's more important than many folks realize,” he said. Vibration from the spines can tear up the basket splines and ultimately the clutch plates.
I generally don't Loctite the mainshaft splines until the bike is tried and true, encase I need to remove the clutch. “Harbor Freight sells a cheap vintage steering wheel puller,” Dan said. “They work like a champ for pulling BDL clutches. If a hub is too tight a little heat does the trick, melts the Loctite.”
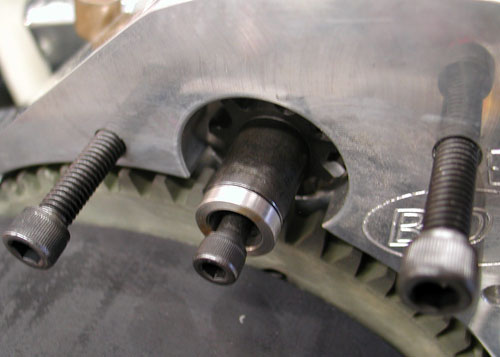
With the clutch back in place and all the elements tightened down I installed the Spyke starter and pinion shaft. Giggie, who just passed away the other day, told me years ago, how to check the spacing. To keep the starter strong and not fuck with the ring gear, the starter gear should rest about 0.150 back from the ring gear. Too close and it doesn't have the space to begin turning and jams against the ring gear. Too far receded and it won't make good solid teeth contact.
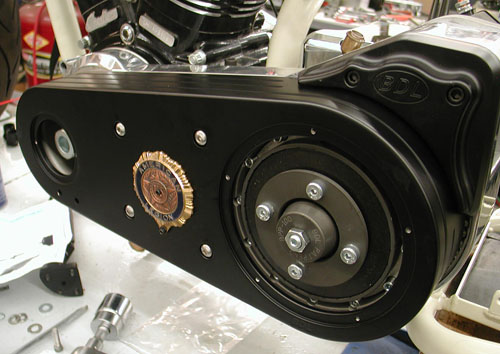
With the primary almost buttoned up, I moved to the LA Chop Rods new-fangled internal throttle installation. Internal throttles are cool but precarious. If a bike stumbles and falls over, the first damage is generally to the bars. It's easy to replace an external throttle or a grip. But what the hell. We're not building a bike to fall down.
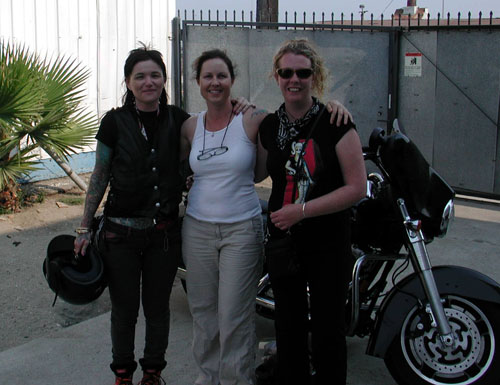
About this time, the Sturgis event hit the summer calendar, and folks arrived from Australia for the ride. Doc from Heavy Duty Magazine, in Australia, picked up a Victory for the run. Nicole Brosing, an Australian tattoo artist, flew to the coast, rented the same Road King she rode last year, grabbed her girlfriend and split north to San Francisco then east to the Badlands.
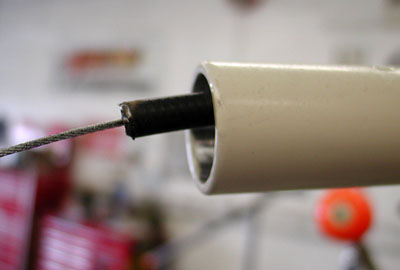
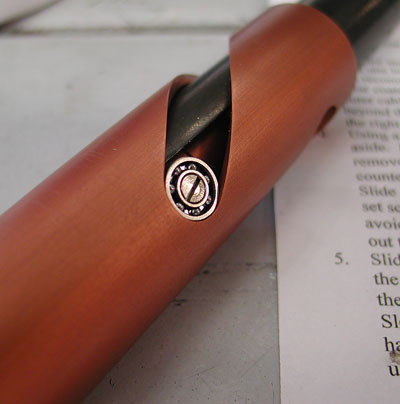
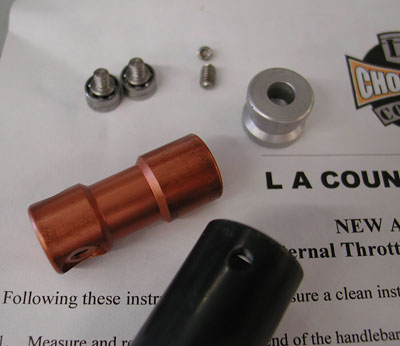


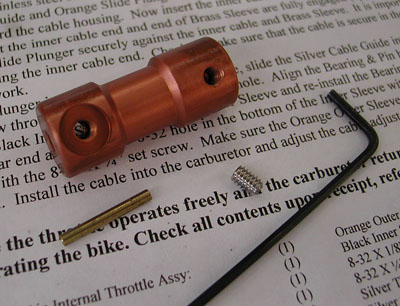
I wrenched in the shop, drank Coronas, smiled and caught a sun tan. Gard Hollinger from LA Chop rods slapped extra engineering into his internal throttle system. His instructions were detailed, but I was still nervous as I attempted to determine the proper length. It's always a sharp notion to take the bike off the lift so the bars can rotate for testing the overall length. It's actually a breeze to install, although I honed out the bars slightly, for an easy slip. Gard devised the cable lock-down with a brass sleeve to prevent damage to the internal cable and afford a solid grip for the set screw. This throttle, with extra bearings, is smooth as silk.
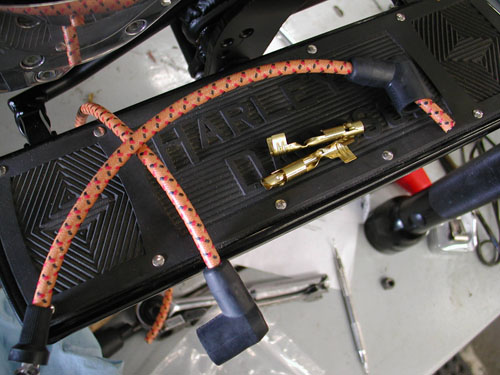
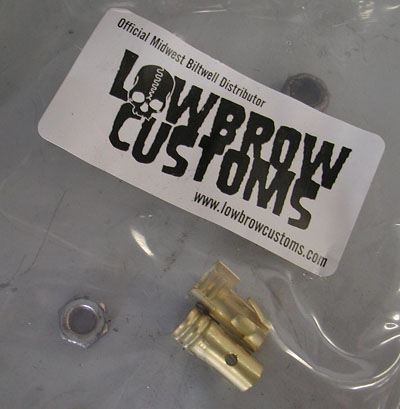
Then I turned to the classic spark plug wires from Low Brow. This is a cool system and adds class to any ride. They come in a kit form with all the elements needed, except a roll of solder, flux, and a gun. It was a simple operation, but I actually mounted the coil a tad on the tight side to the underside of the tank. Fortunately it all fit. Make sure to slip the boots onto the wires before you solder the brass fittings into place. Lowbrow attaches the other ends before shipment.
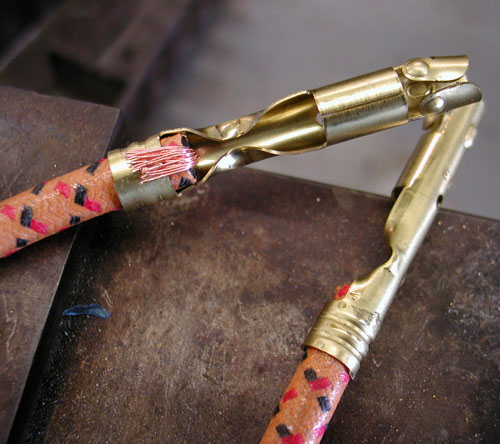
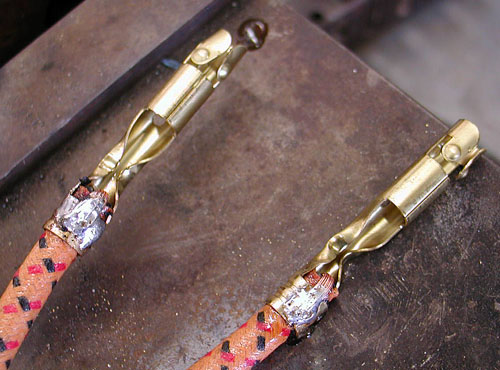
I simply attached the spark plug wire to the spark plugs, ran the lines out of harm's way to the coil, added an inch for safety, cut the wires, trimmed them back for soldering, and crimped and soldered the fittings into place. Frank Kaisler told me to make sure to wipe all the flux off after soldering. So I did as Commander Kaisler instructed. He uses alcohol or solvent to clean the area, preventing future corrosion.
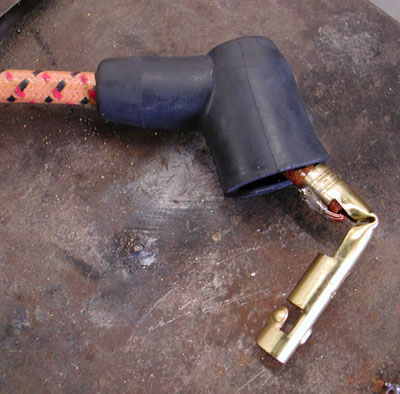
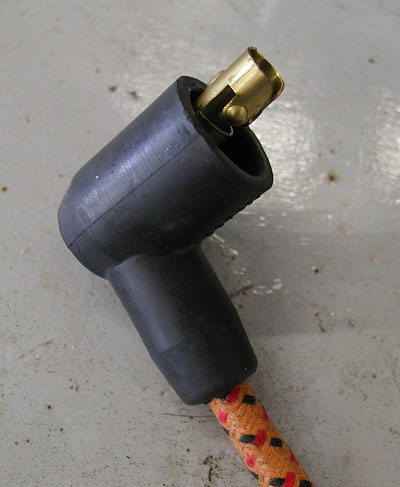
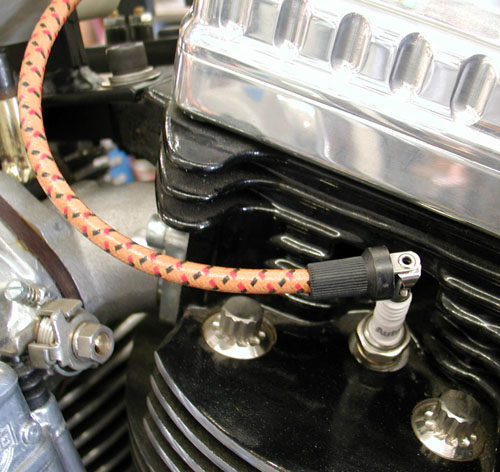
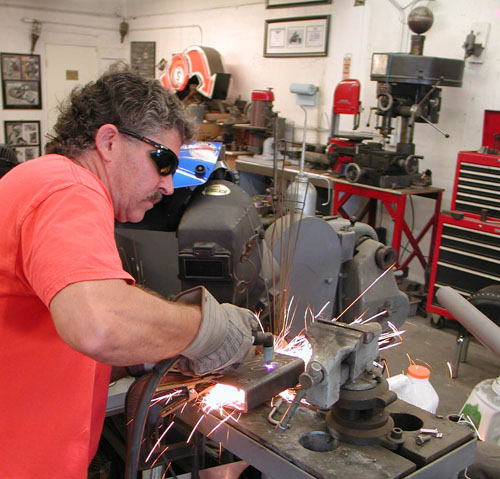
I took a day off to help Nyla's brother, Brad, build some diesel motor mounts for their 32-foot Cho Lee motor sailing vessel. They were smack in the middle of a complete restoration. It's a beautiful boat. I've sailed it to Catalina Island several times, when it belonged to an old friend of mine. Another deadline loomed. Less than a week away, the Easyriders Bike Show would rock the Broken Spoke Saloon in Sturgis. Bikernet sponsors the Panhead Class each year and I needed to create the trophy. Panhead Billy won the award. When I can reach him, we will feature his classic rat pan.

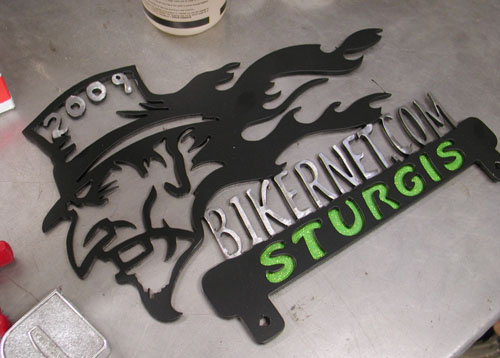
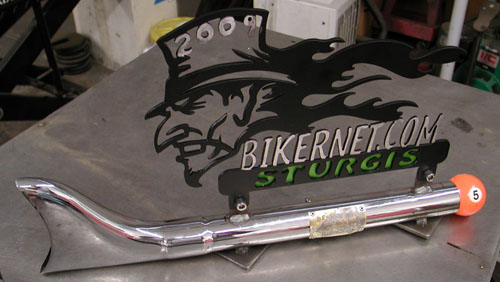

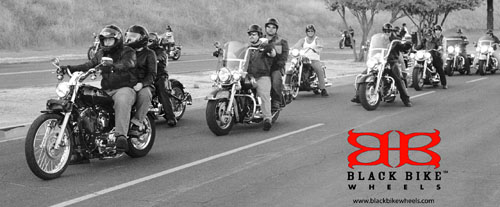
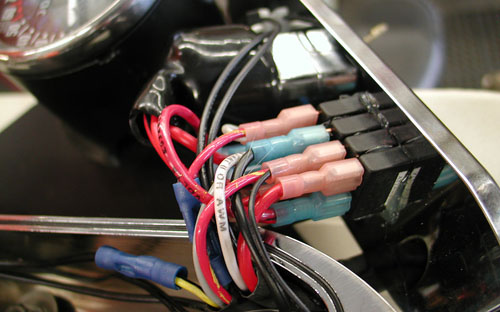
I shifted to the wiring. I used Phil's Speed Shop wiring system. It's designed for lots of custom applications and makes wiring a breeze. He includes instructions and a wiring diagram. The billet chromed box includes the ignition switch, the high-low beam switch, circuit breakers, starter relay, neutral light and starter button. I just ran the wires, used my Frank Kaisler soldering tool and ran the wires through the old H-D soaked canvas loom. I know that's not the correct term for it, but it's a close description.
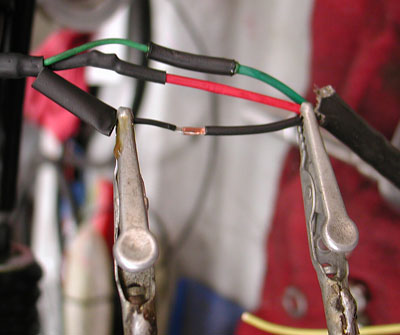
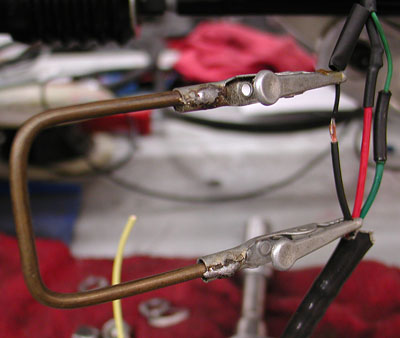
I ran into one problem that held me up for weeks. I like the CrazyHorse bottle cap engines. They offer three ignition alternatives. First, the original Thunderheart unit, an adjustable timing Thunderheart, and finally a cone motor system. Unfortunately, they don't tell you enough about the stock system. I thought it was like a Compu-Fire system in the cone. It's a one piece unit. I reached out to other Crazy Horse engine builders who told me I needed a Thunderheart ignition module. So, I ordered the system from Thunderheart, but when it arrived it didn't jive with any wiring diagram I received from Thunderheart or Crazy Horse. It was a riot. Every time I received a wiring diagram or a box from Thunderheart, I thought I was good to go. Then some goddamn thing wouldn’t match, and everyone had split to the Badlands. I paced the garage waiting for answers.
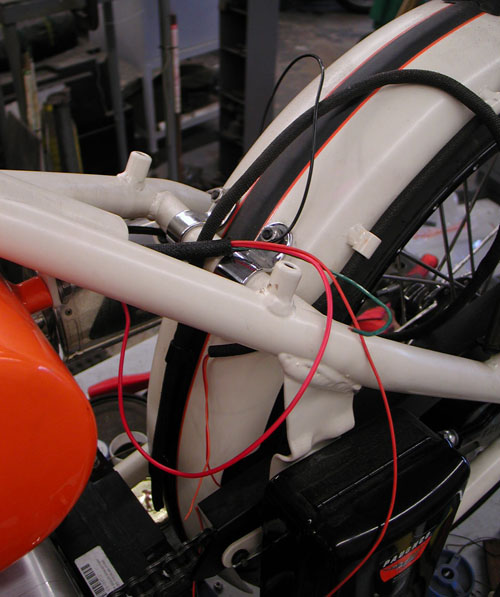
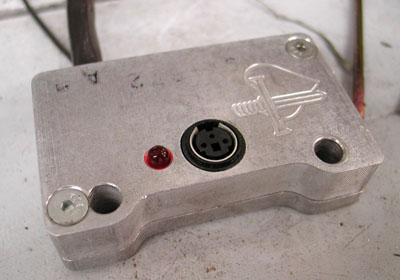
The Thunderheart tech guru sobered up after a week in the Broken Spoke swimming pool, doing belly shots with the lovely waitresses. He dropped me a simple e-mail: “There's only three wires goddamnit, black for ground, red for ignition and green to the coil. Go for a ride.”
That solved that mysterious issue and I moved on. Three more puzzling obstacles surfaced. I cleaned the Paughco oil tank with solvent and small nuts and bolts. I counted the fasteners before I slipped them into the tank. It was sorta rusty, and I didn't want to roll without cleaning it. I poured a cup of oil in it and flushed it out. I hooked up the oil lines, and Crazy Horse sent me very specific instructions, but this will blow your mind. I couldn't figure out venting. I'll get back to that.
I hooked up my gas lines. I filled the tanks and one leaked. I threatened to fire myself on the spot and another challenge surfaced. The pinhole at the front of the tank, where I cut away a section to allow for fork stops, stuck out like a sore thumb. It was obvious, but we didn't spot it during testing. I called Jim Murillo, a professional painter and cried for assistance.
“Don't use Kreem, it peels,” he said. “Use Casewell two-part Phenol Lovolac System.”
I ordered some and their customer service was supreme for a small $36 order. Some companies get it, when it comes to taking care of customers. This is where tank seals become terrifying. I needed to kick my ass into the middle of tomorrow. Make sure your tanks are sealed before any finish is applied, including powder coating. I suppose I was over confident. What the hell.
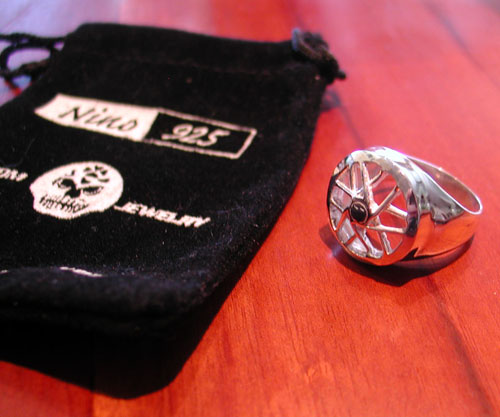
The directions called for cleaning the tanks with lacquer thinner, nuts and bolts, sand, you name it. I tried the lacquer thinner and immediately fucked with George's pinstriping. I called him, panicked and drank whiskey heavily. Fortunately a Bikernet reader shipped me a fresh bottle of Bulliet Whiskey, and Dusty, one of the 5-Ball Racing Team Salt Flat members, hand-stripped several pounds of walnuts and shipped them out.
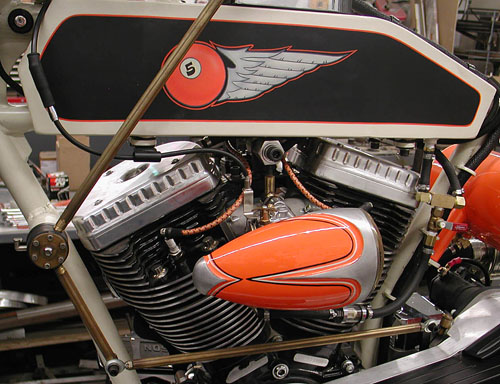
Incredible. I let the tank dry thoroughly, made up a small portion of the Casewell sealrant and poured it into the tank. I knew where the hole was, and fortunately it rested in an easy-to-reach corner. I tilted the tank in the sun and returned to the whiskey. George saved my ass once more.
With the tanks fixed and returned to the bike, all was well, and I put a key to the Phil's ignition switch for the first time. Here's another quirk. Crazy Horse doesn't tell you how to time your new 100-inch engine. It times itself. The bike didn't whine, growl, spit or cough. It fired immediately to life and purred. I checked the oil pressure, perfect. Then I unscrewed the cap off the oil bag to make sure the lubricant returned to the oil bag properly. Yep, it was returning, but the cap popped off into my hand. I wondered about venting. Everything was fine except for pressure in the oil bag.
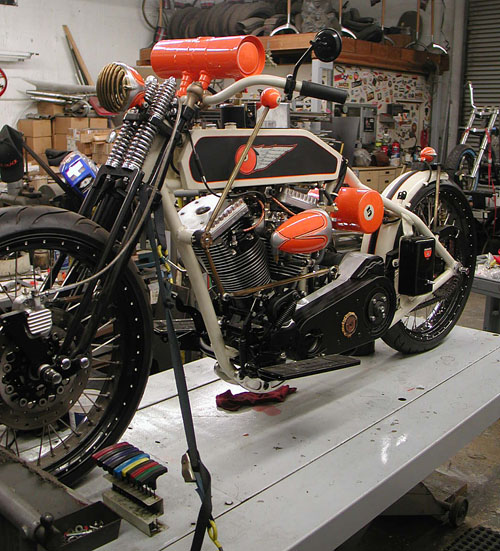
Again, I started a research project. The Crazy Horse installation material didn't mention a crankcase vent and I searched the engine. There are two 3/8-inch spigots between the heads, as if for a cross-over oil line. As it turns out they are designed as vents. I found out from Dar at Brass Balls that they just run a line under their gas tanks. I pulled one end, no oil flow. It had to be the vent, so I improvised and used another old machinery oil fitting to hold a screen to prevent crap from strolling back into the precious engine.
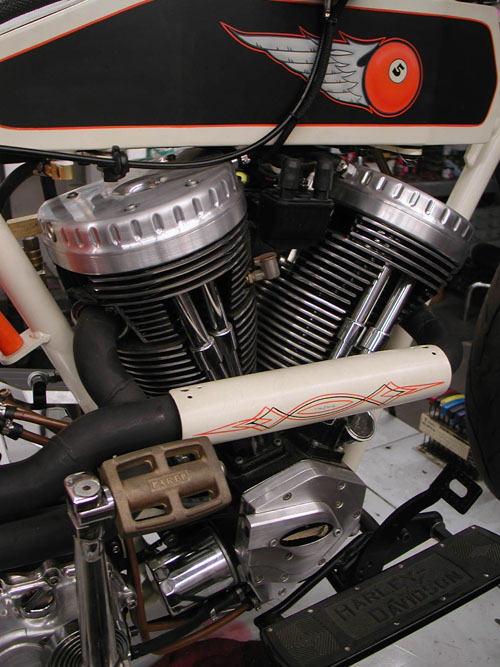
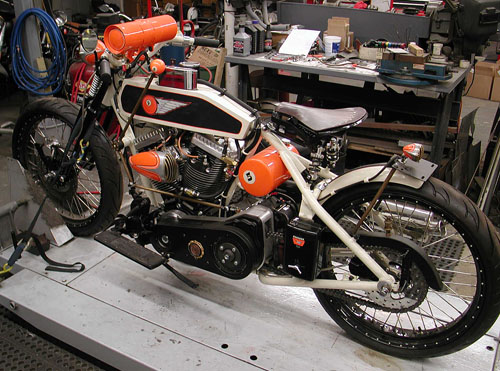
That solved that issue. I was ready to rock, but my seat hadn't arrived from Duane Ballard. It was a wild old sprung BMW seat he scored. When it finally arrived, it didn't fit. It was too high and too far back. I was faced with another quandary. If I moved the bars, I could barely place my boots on the footboards. I scratched my beard, looked at the box of walnuts, and then it dawned on me. Glenn Priddle, a leather seat master, who studied under classic saddle makers, made me a seat a couple of years ago for the 10th Anniversary of Bikernet. It was a wide, classic solo seat. I dug it out, dusted it off and it fit like a glove, dropped the seat height 2 inches and move the seat position forward 3 inches. It actually fit the frame better than the old classic from Duane. I dodged another bullet.
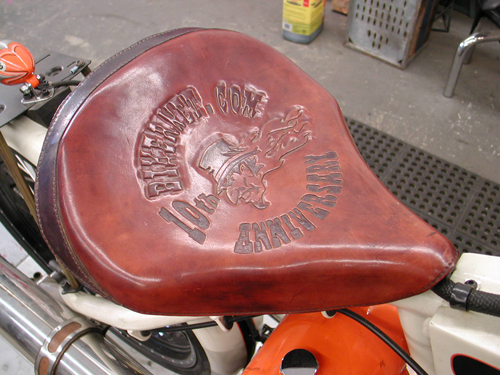
Every year when I build a bike, my mantra includes a solid, tough, rideable, unique bike that will last. But each year the unique project throws a few curveballs. It's part of my Zen education. Life is not meant for perfection. We need challenges to test our endurance levels and help us through the tough spots, find answers or solutions and persevere. Often my predicaments are caused by a lack of experience. For instance, if I ever use a Crazy Horse engine again, I'll know all the quirks and set-up issues.
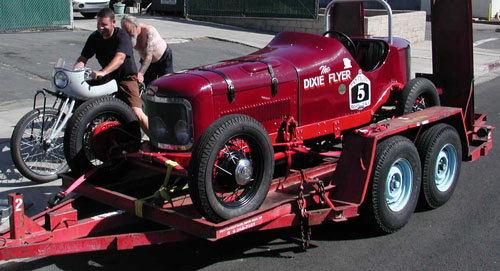

Now, let's see if I can ride it for any distance. I would love to ride it to the Badlands next year or to Arizona for our Too Broke for Sturgis Run.
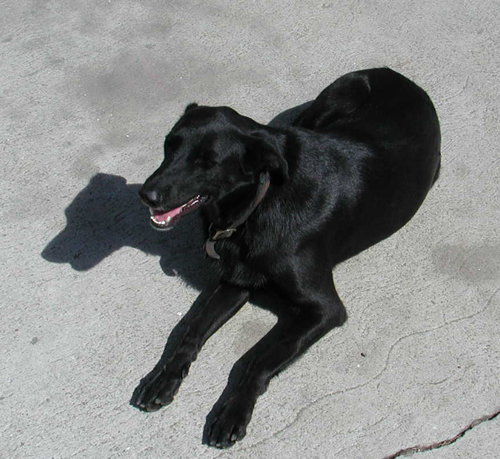
We'll see what happens next, as I take her through the Eddie Trotta break-in routine. Eddie starts a bike for the first time, let's her run and checks her over. Then he takes it out for a one-block jaunt, and checks it over again. Then he ventures forth for one mile and returns for another inspection, then 5 miles, then 25, then 50 and she's ready for a cross-country blast. Hang on!

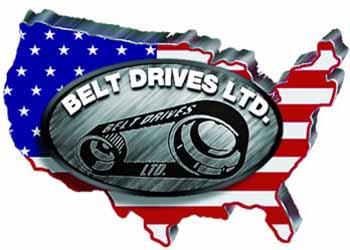
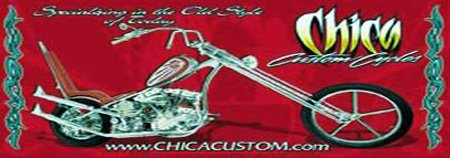
5-Ball Factory Racer, Part 7
By Robin Technologies |

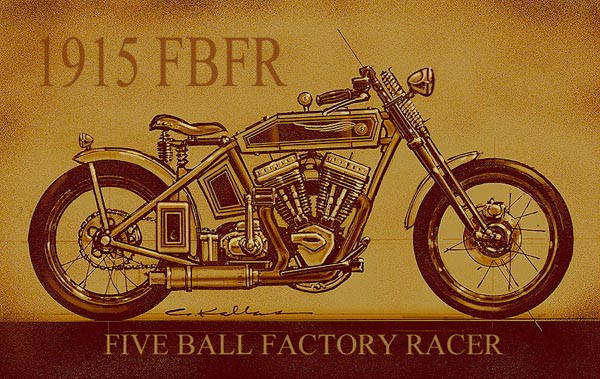
It's resting on the tail end of June and I'm riding to Sturgis on 27th of July. I'm burnin' daylight. Assembly will begin this 4th of July weekend, if I don't party the whole weekend away. This tech will take you through all the final preparations for shipment to paint, since I'm avoiding chrome. In this case, we're hauling down this old school road with only flat powder coating and pinstriping from George the Wild Brush.
No bondo, hand-rubbed lacquer, heavy clear coats, just some pinstriping and graphics from the master will insure this vintage Factory Racer peels to the badlands. Let's kick this tech square in the ass with the basics. We will cover an Exile rear brake mounting, Paughco footboard bracket gussets, welded pipes, final mods to gas tanks, fork stops, LA ChopRods wiring guides, and some fender-wiring guides.
This is the stage of bike-building that's frustrating. It's the notorious time of little bullshit obstacles hindering progress at every turn. I need to clean and seal the tanks. I must hunt down a couple of vintage parts and FlatheadFern.com is helping. I need the parts painted before I can begin my Phil's Speed Shop wiring, but I need to relax. It will all come together, I say, brimming with confidence as I drink more whiskey.
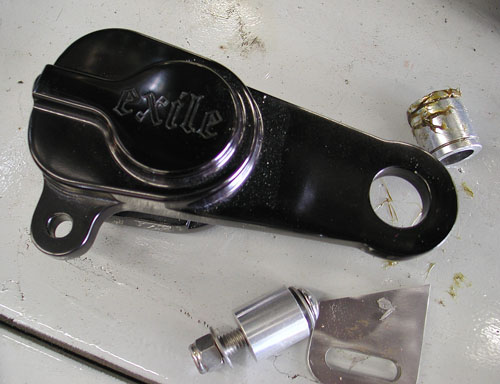
Let's get movin', so I can figure out what I'm missing as the weeks peel by, like deadlines to a Times sports writer. First, we installed the Exile black sprocket brake kit with a 48-tooth highly polished sprocket for the proper gearing.
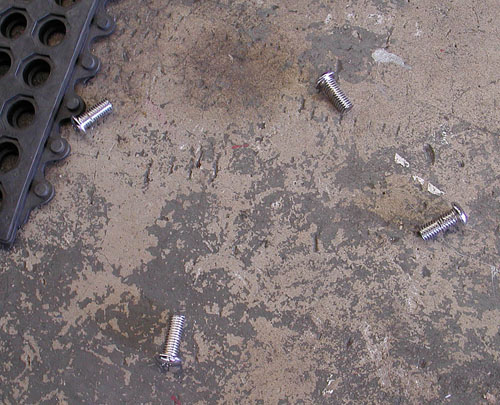
I dropped the special, chromed 7/16-inch supplied flathead screws on the deck. I bolted up the sprocket and prayed for alignment with the JIMS transmission sprocket, which was a ¼-inch offset. They distribute a number of trans sprockets with a variety of gearing and offsets from zip to 1 inch. I ordered another JIMS sprocket with ½ inch, since I feel it will afford me perfect alignment position. We'll see.
Russell Mitchell mentions in his Exile directions to consider a spacer between the hub and the Sprotor for alignment or tire clearance. The Black Bike wheel spacing seemed to be very cool.Next, Exile recommended machining the axle spacers so when the caliper and the bracket are installed and the axle nut is tightened, the caliper can run centered over the Sprotor.
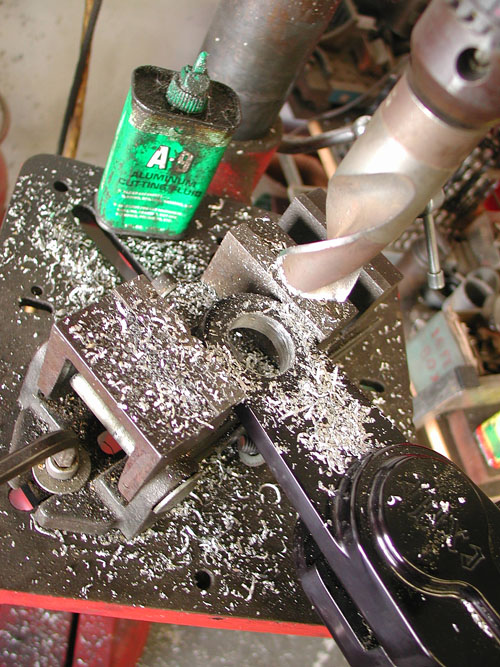
I bored out the caliper bracket to allow it to float into the proper position over the axle spacer. Then I positioned the steel anchor tab against the frame. Exile supplied a fastener and a spacer for mounting, but I was able to weld the tab on the inside of the frame, very close to the caliper, which had its drawbacks. I also made sure there was some space and some chain adjustment space, so I wouldn't be caught without adjustment flexibility.
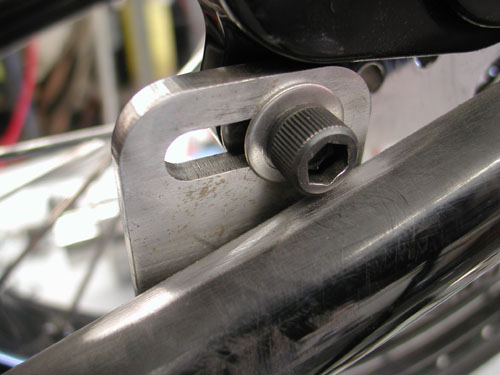
Russell made certain to point out that the tab needed to be absolutely parallel to the caliper, or braking efficiency will be hindered. He also pointed out the need to bleed the caliper before it was installed, but lifting it, so air could escape. I often take a file and slip it between the pads, to mirror the rotor surface. We'll get to bleeding over the weekend, I hope.
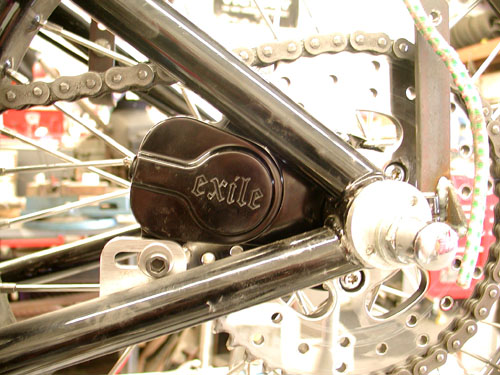
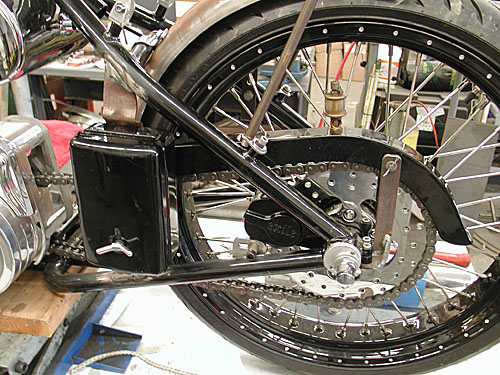
Moving right along, I spoke to Gard Hollinger like a panhandler at a coin convention. He offered a couple of his cable guide bungs for the project and I took him up on the notion. The code is to build a bike without using tie-wraps.
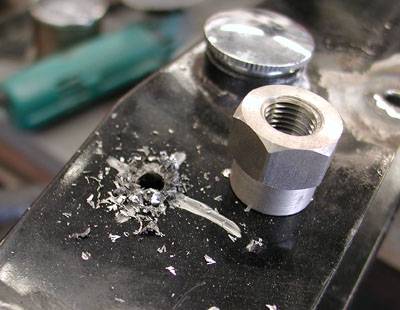
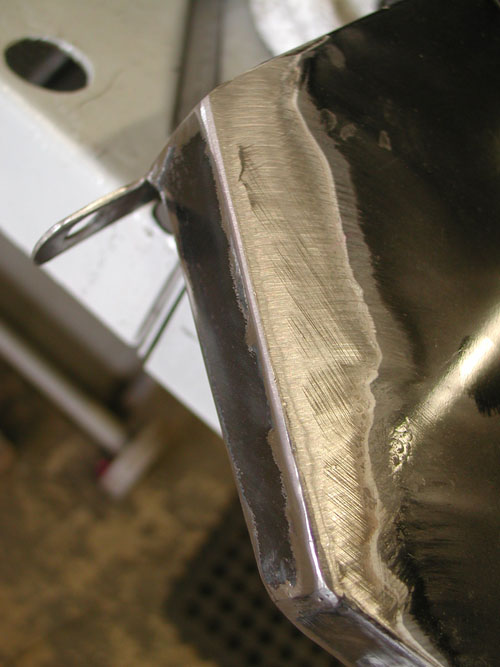
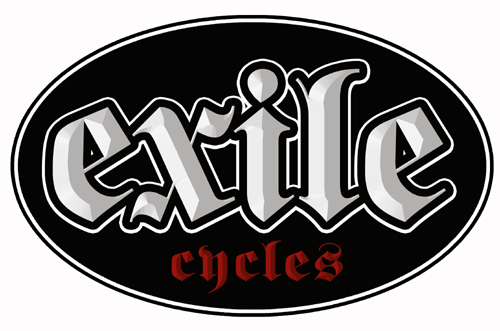

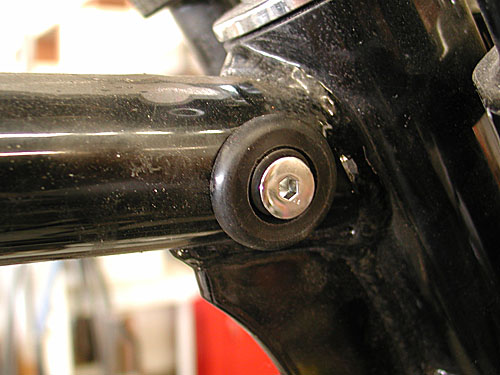
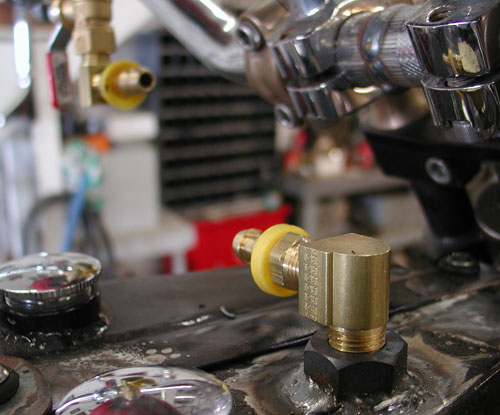
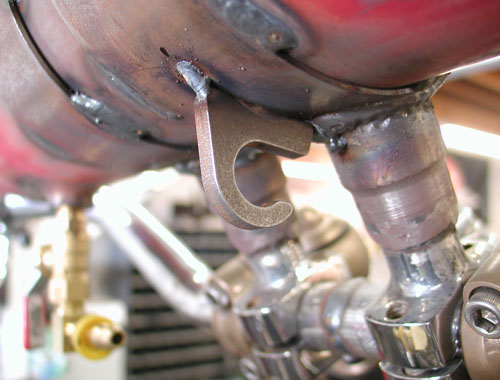
Gard makes a terrific product line of cable guides, tank bungs, and wiring loom guides. I crept through his shop slipping this guide and that runner into my pocket, and then I slithered out the back door.

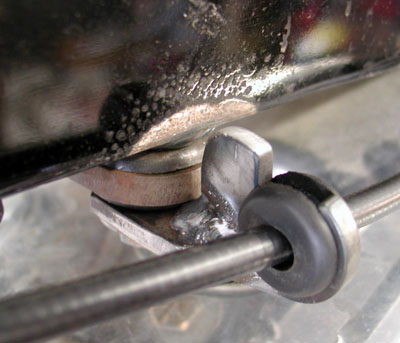
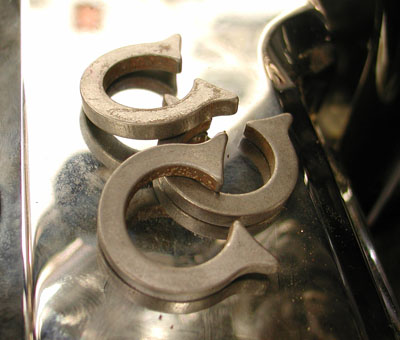
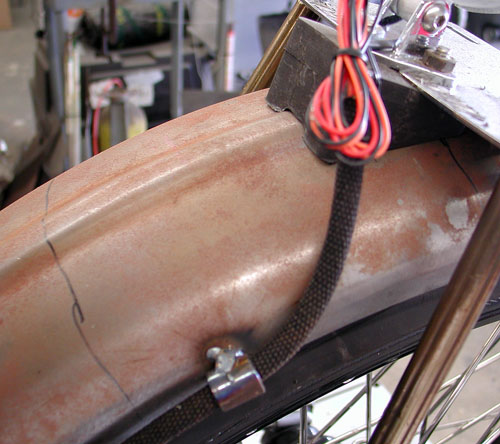
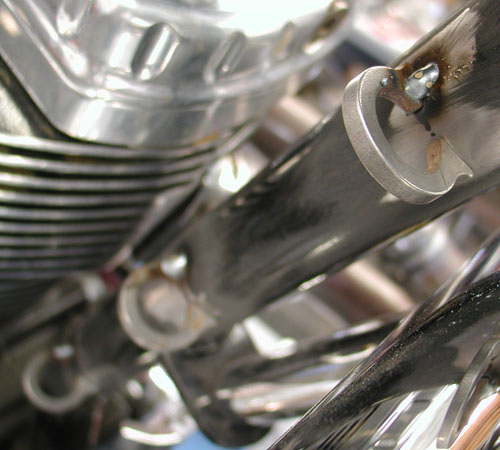
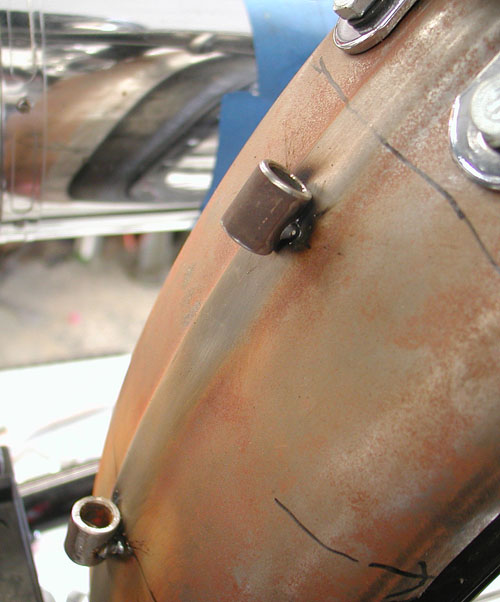
I made a final speedo guide runner and tried to figure out my wiring system with the Phil's Speed Shop wiring harness. I tacked several loom runners and made some tubing runners for the fender.
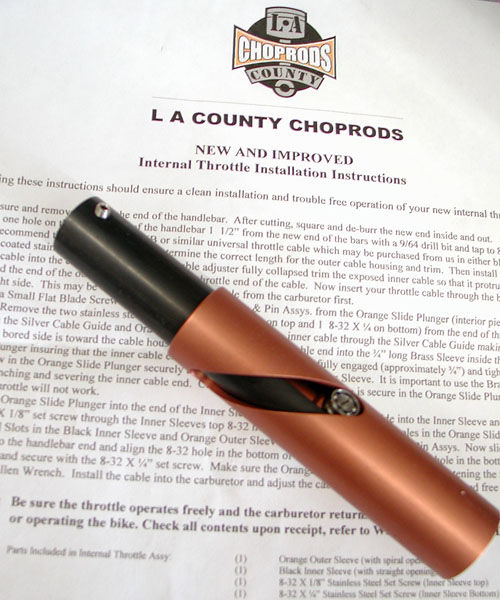
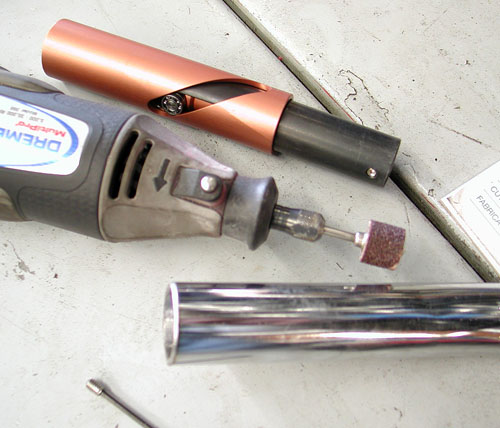
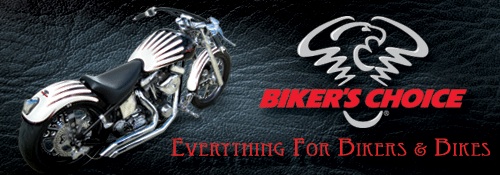
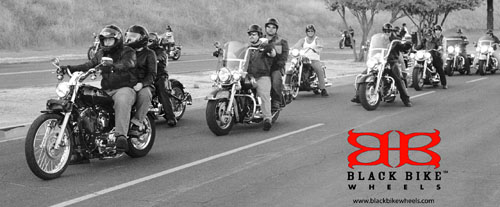
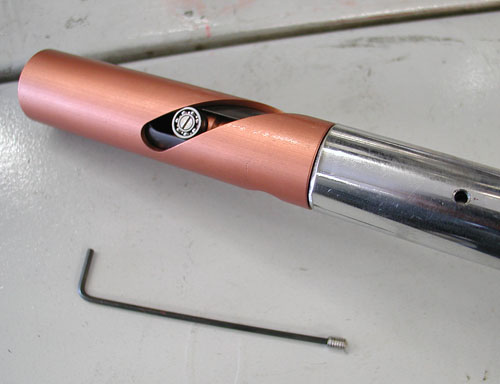
Then I moved onto installing the new and improved LA ChopRods internal throttle. They simplify handlebars and since no clutch lever was in the mix, my bars were destined for cleanliness. Gard, the boss of La ChopRods, the designer, welder, and janitor, went out of his way to redesign the LA ChopRods internal throttle with builders in mind. It has double bearings that won't fall out during installation. All the measurements were clean and simple, such as you cut a simple 4 inches off the bar and drill a tiny 9/64-inch hole just 1.5 inches in from the end and tap it to 8-32 thread. It was finished in a hot flash. I used an emery grinder on the inside of the bars to allow the internal throttle to slip in easy.
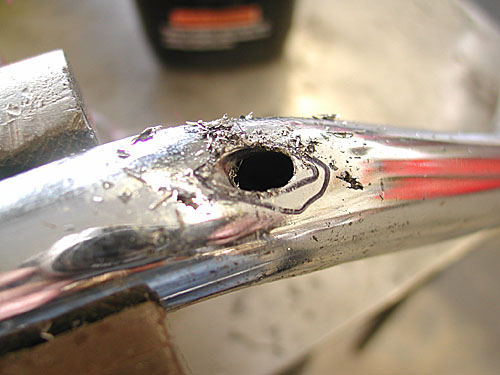
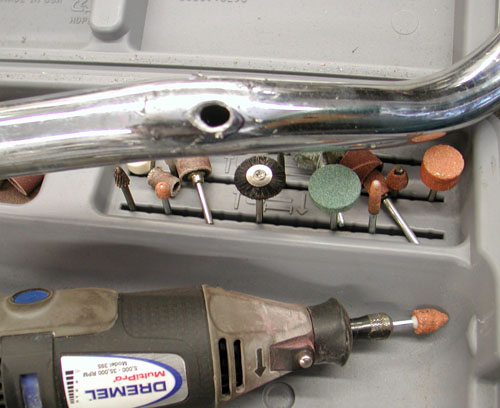
You can order the throttle cable from LA ChopRods. They recommend a Barnett 6B or similar universal throttle cable. They sell them in black vinyl or clear-coated stainless steel braid. In case I'm too harried to shoot the assembly, Gard suggests that the adjuster be collapsed and the cable installed in the carb first. He pointed out that the inner cable needed to protrude 1 11/16 inches beyond the outer cable.
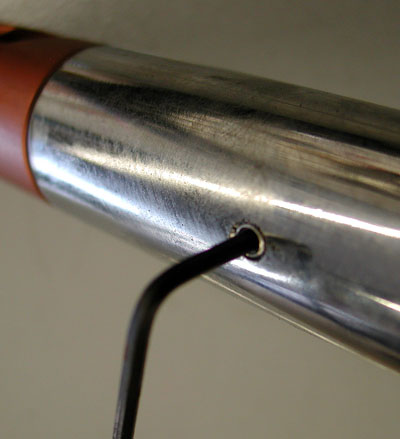
Insert it into your bars and out the right end. Remove the screws holding the bearings in place and disassemble the ChopRods internal throttle. Gard designed a 3/4-inch brass sleeve to grab the internal cable and not damage it. In the past, I was concerned about screws coming loose and finding myself alongside the freeway. It happened to me on my way to the Exile open house. Gard made sure all the fasteners have no place to escape. And the handlebar fastener can be secured by running my GMA front brake lever clamp over the Allen 8-32 set screw. Done deal.
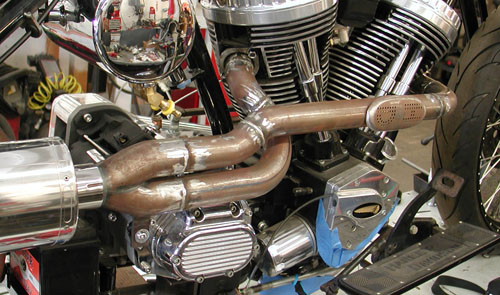
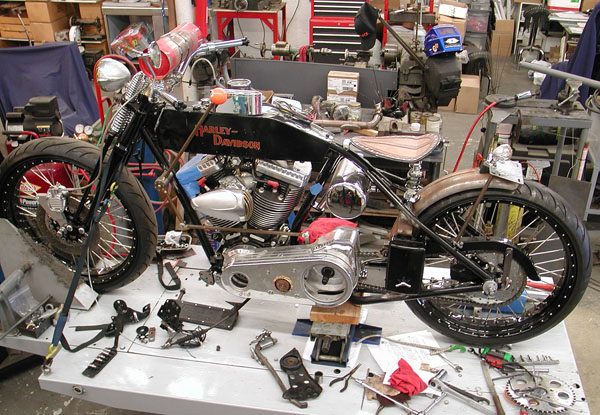
I ripped the Factory Racer apart after thoroughly thinking through the oil line placement, wiring, brake lines, and battery cables. I made a throttle guide and guesstimated it the best I could. With the bike in pieces, I finish-welded all the tabs and bungs in my sloppy MIG welding fashion. I drilled the frame for fork stops and busted the fender tab off the Paughco battery box. Positioned too close to the battery, I made another tab and welded it 3/16-inch closer to the fender. The head of the fastener won't rub against the battery. So far, it's the only item I forgot to weld completely. I missed the inside weld. Not sure what I will do, maybe panic. Maybe I'll grind away the fine Worco Powder Coating and weld it anyway. Or perhaps I'll just go for it.
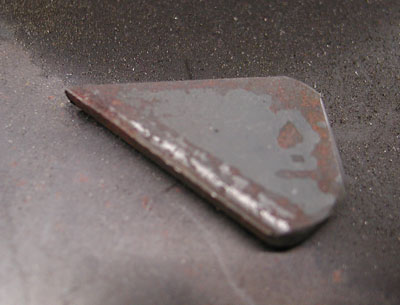
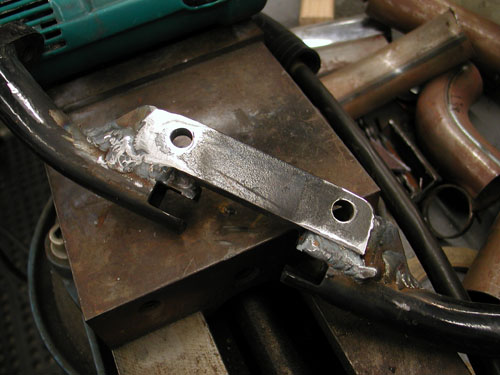
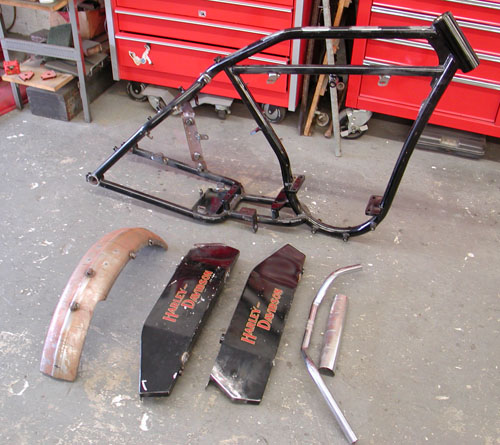
In the next couple of weeks, I'll deliver on the Baker kicker system installation. What a fine piece this puppy is. Then you'll witness George “the Wild Brush” pinstriping various components and final assemble. Of course, you'll also experience the ride to Sturgis. Hang on.
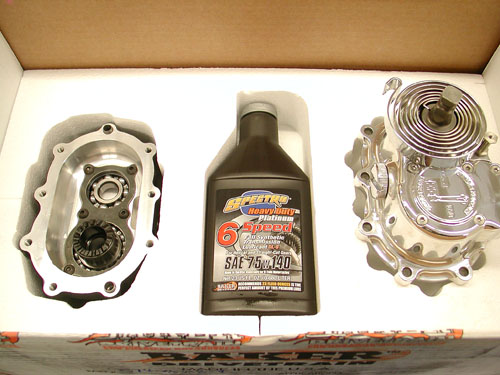
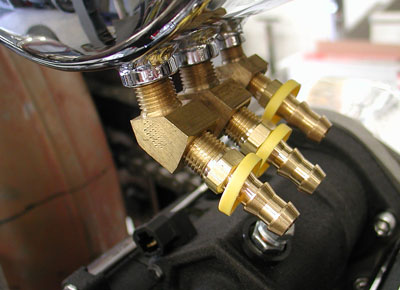
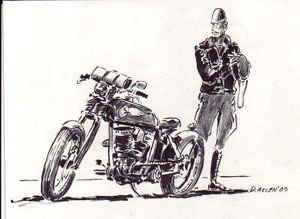

5-Ball Factory Racer Part 3
By Robin Technologies |


I'm in a daze this morning. Too much Quervo Gold last night and too many discussions about the sinking economy. It's a bastard when they lay off port crane operators. What does that tell you? I don't want to go there on this dank gray morning. It's warm outside, but even the dogs, Tank and Cash, feel the gray skies. They look hung-over, droopy and drained. I haven't shaved in a couple of days, need a shower and a kick-my-butt workout.
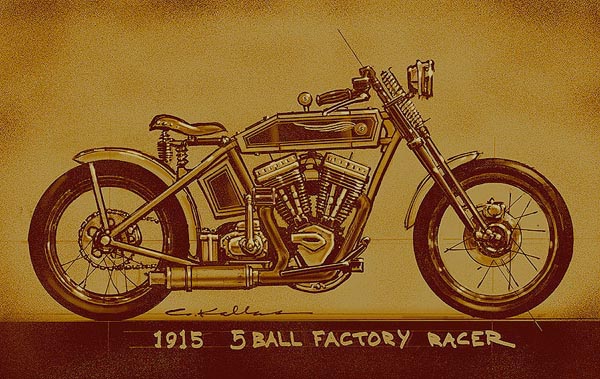
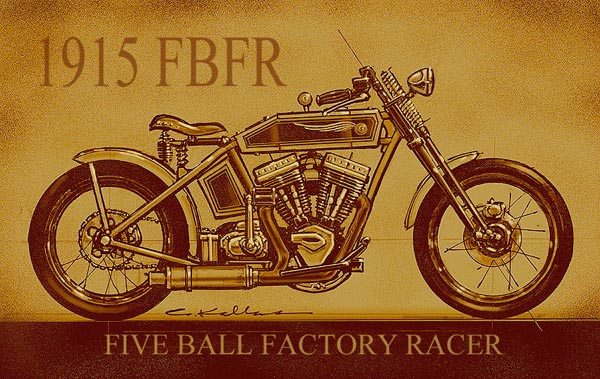
All the women left me and ran off to the mountains this weekend. I know why Sin Wu needed a break. Have you ever tried to maintain a 10,000 square-foot, old dilapidated building, clean and care for two lumbering, sloppy dogs, two house cats, and a stray that wanders through and bitches if the food supply isn't consistent with her desires? The Macaw needs to be fed and moved into and out of the sun at the end of the day and now we have a fuckin' fish.
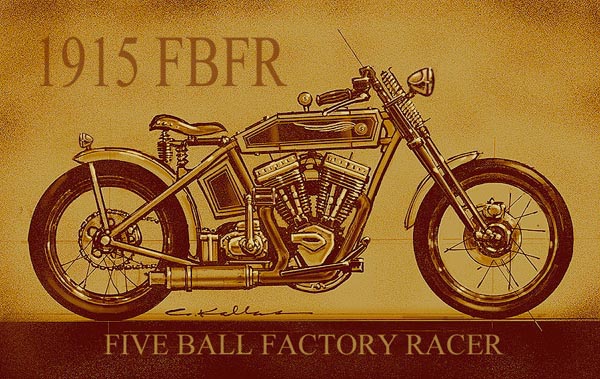
There are also construction workers, electricians and plumbers to deal with. It's never a dull moment around here. I'm a big proponent of running off all the costly pets, who can't do except shit and care for a half dozen concrete gargoyles. At least they keep the evil spirits at bay and involve zero upkeep.
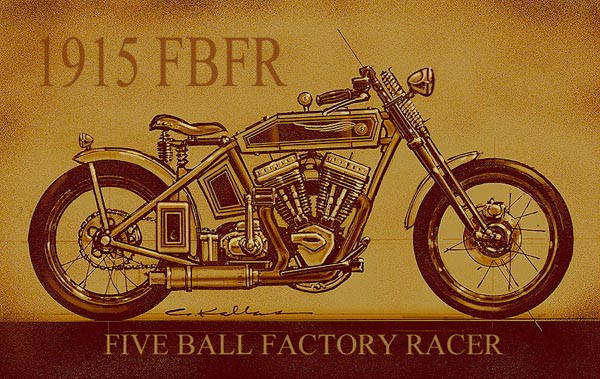
Okay, I'll get to the tech. I was on a hunt for a vintage seat and Duane Ballard stopped by with this vintage BMW seat. I used chunks of wood to hold it in place while I pondered the little Hispanic girl who works at Shamrocks, the Mexican fish market two blocks away. Since the seat was made with a number of springs incorporated in the structure, I didn't feel additional springs were necessary. I played with my options, but nothing – graceful, stylish, art deco or vintage – came to mind. Then I grabbed the springs that came with the prototype Paugho frame and voila, it all came together using the existing frame bungs, the mini-seat shocks and a slight modification to the BMW seat.
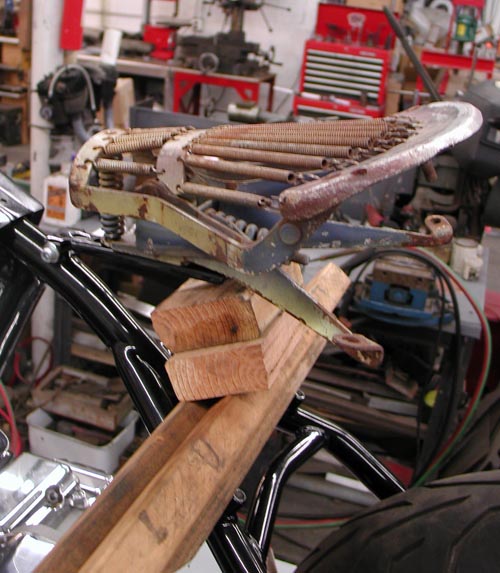
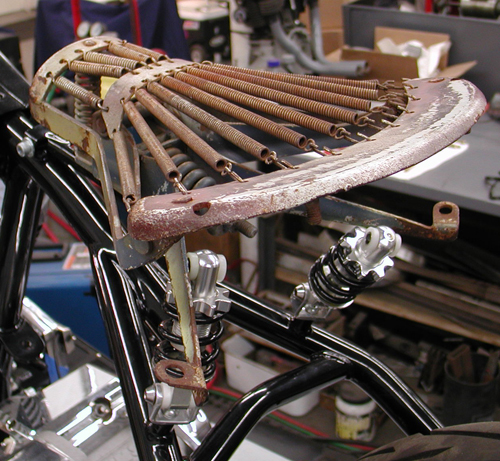
I drilled new holes in the brackets and cut about 4 inches off the arms. The front of the seat bolted directly to the Paughco seat hinge and I was good to go. Duane stopped by again, blessed my creation, and took the seat for top-notch leather upholstery action. He's the best.
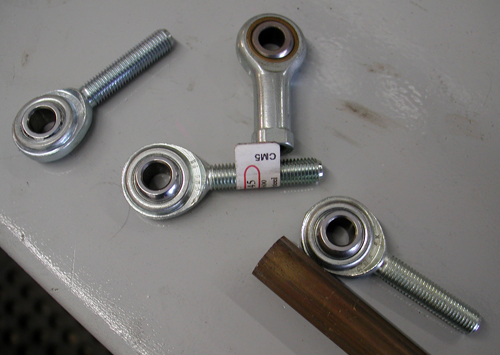
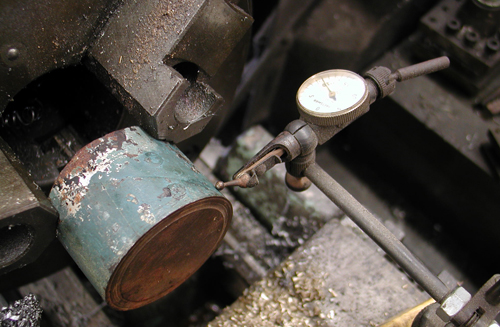
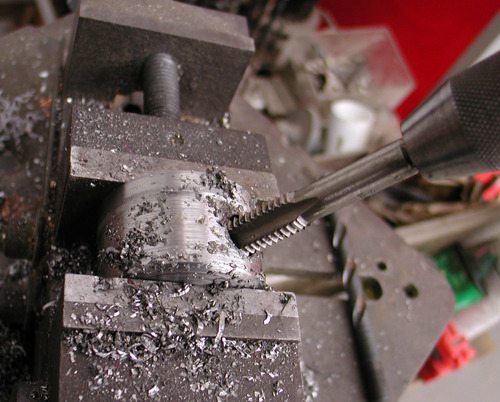
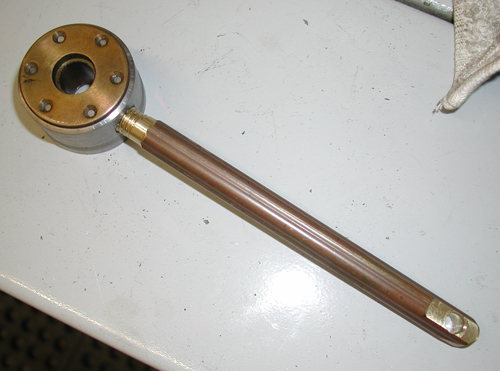
I shifted to my shift linkage system and called Jeremiah for the mathematical configuration from the system we build for his bobber. I wanted a tank shift and had several strange components, plus heavy, solid cloverleaf brass rod to use. I don't have any idea how I come up with this shit, but what the hell. It has class.
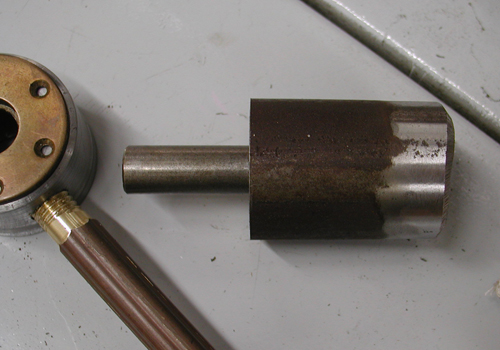
According to Jeremiah, from the pivot point down, the shift arm was about 6 inches in length, and the distance to the shift knob up was almost three times that length. That made for a vast throw and I needed to make sure I was clear, fore and aft, for shifting without smacking the bars or anything else. I checked my '48 Panhead with stock jockey shifting and the ratio was closer to two to one. In addition, jockey shifting is a different animal. There's no back and forth spring action on vintage tank-shifted bikes. The shifter banged through one gear after another from first to fourth, done deal.
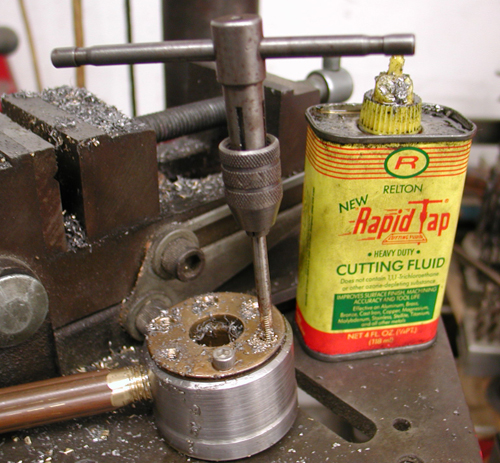
That's the reason jockey-shifted bikes are best with jockey top transmissions. If you need neutral, just pop it out of any gear and you're back in neutral. Ratchet tops force you to bang through one gear after another down to the only neutral between first and second, often missing it. In our next tech, we will install a Baker 5-and-1 drum in this transmission to afford neutral at the bottom for easy reach.
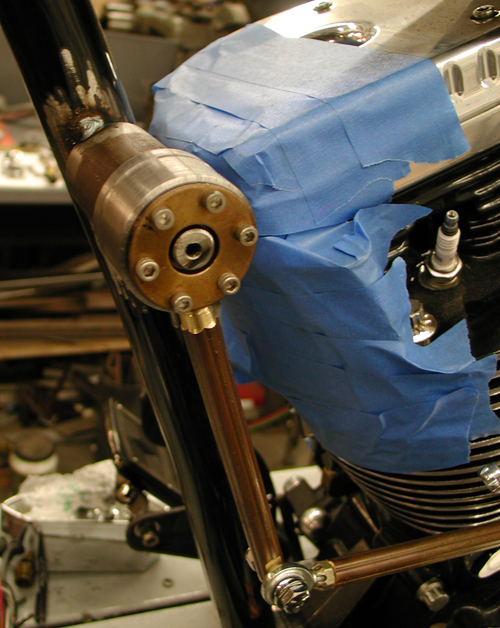
Okay, so back to the job at hand. I'm trying to use as much brass on this bike as possible, so I dug through drawers and boxes of old machined parts and trinkets and came up with these brass-bearing supports. Then I machined a piece to fit these, then the axle piece to mount to the frame. Then I had to bore and tap the pivot, drill and tap to anchor the brass bushing, drill and tap to create a pivot stop and machine and thread the brass rods, plus machine an end to fit a heim joint connection to the transmission shift linkage. I spent hours tinkering and figuring, drilling, tapping and testing, and I'm reasonable sure I have a tough, working shifting system.
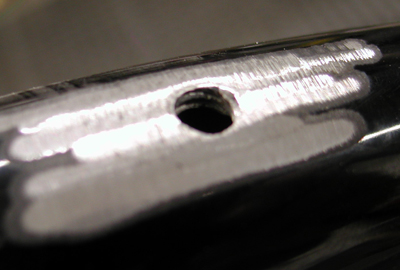
Then I shifted to the dreaded tanks. The tanks are fine, but more involved than normal one-piece, bolt-on tanks, ready with bungs for rubber mounting. Since this was a prototype Paughco Factory Racer frame, the first one of the batch, they bolted the tanks to the frame by drilling and tapping the top frame tube. Problem is, that afforded each 5/16 coarse bolt about three threads in mild steel tubing. In just a matter of time, those threads would fail, the tanks would rattle and come loose.
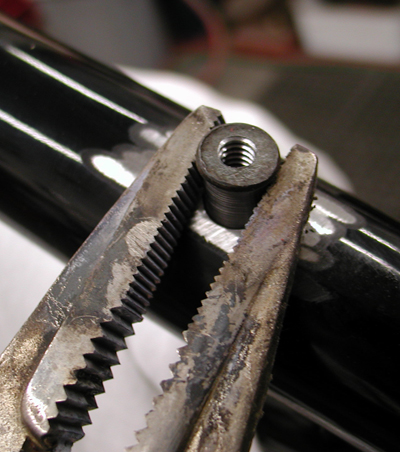
I decided I wanted to strengthen the tank mounting for the long road. I ordered some ¼-inch bungs, ¾-inch deep for a lasting hold. Later, I discovered that since the mainframe strut was 1.5 inch tubing, I could have used the 1.5-inch deep bungs from the Bung King (check their site for all available variations). I needed to re-drill the holes to a larger diameter for the bungs to slip into the frame. Adding the bungs and welding them enhanced the strength of the frame. At first, I though about machining a bung with a lip on it, but the tanks didn't have the clearance above the frame for a lip.
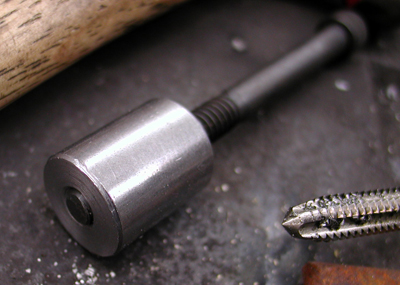

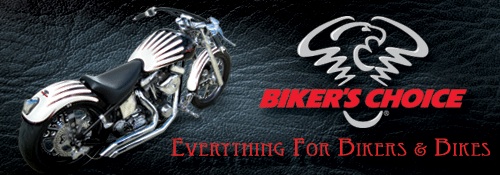
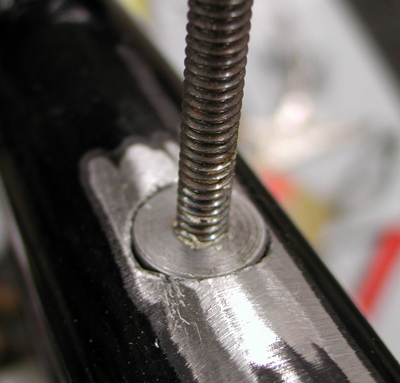
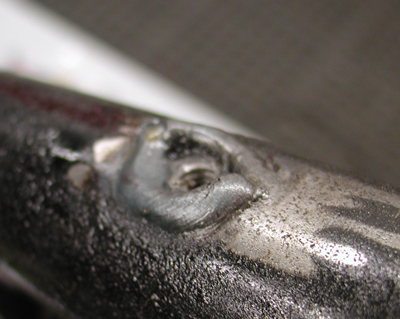
After drilling the frame holes, I tapped the bungs into the hole and as far below the surface as possible for the strongest, deepest weld. I would also need to grind off any protruding weld so the tanks would fit again. One tank protruded into the frame and rubbed at the back, so I moved it as far forward as possible for clearance, which amounted to about ¼ inch.
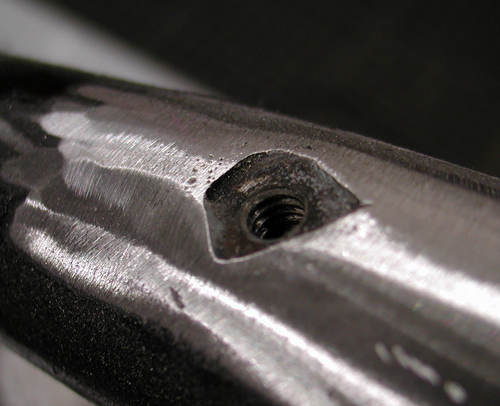
With the bungs in place, welded and ground, I grappled with the tank mounting holes. I thought I had it made, since I was dropping from 5/16-inch bolts to ¼-inch, but not so. Only one hole lined up. I grappled with these bastards for hours. Then I gas-welded the hole slots, refilled them and ground them to a reasonable size.
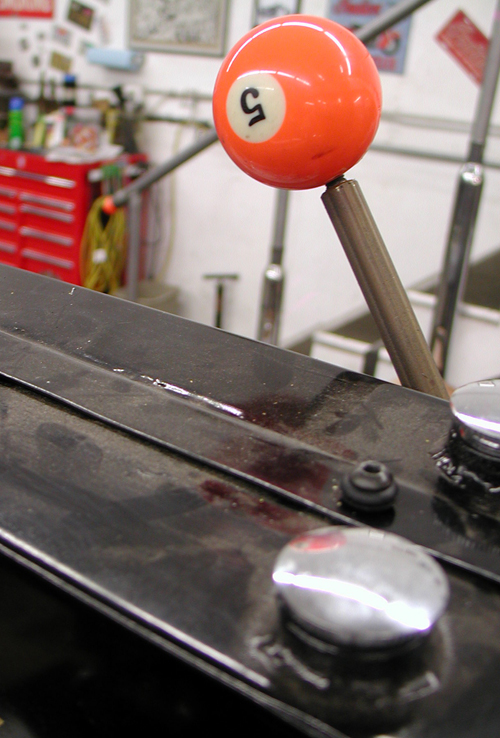
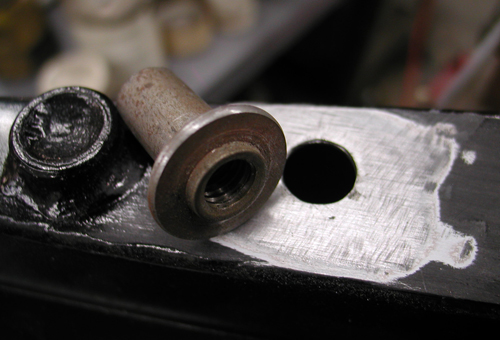
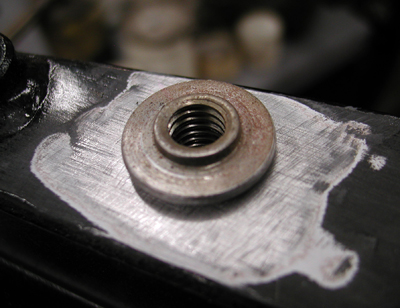
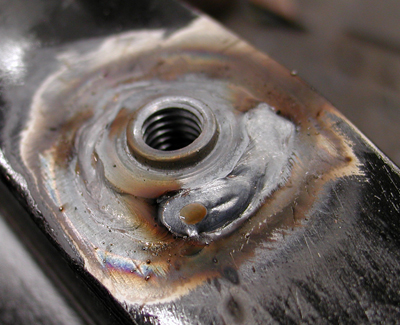
Next, I welded bungs, I believe from Lucky Devil, into the bottom of the tanks and used the Bung King’s rubber mount kits with straps and rubbers to attach it to the frame. In a sense, this was overkill, but I've experienced leaky tanks and poorly mounted tanks on my way to Sturgis a couple of times. One time, Randy Aaron from Cycle Visions saved my ass and my tank paint job. Later on, Paul Yaffe replaced my piece-of-shit Blue Flame tank with a properly rubber mounted Independent tank. So, goddamnit, this needs to be right the first time. I ran rubber mounts front and rear.
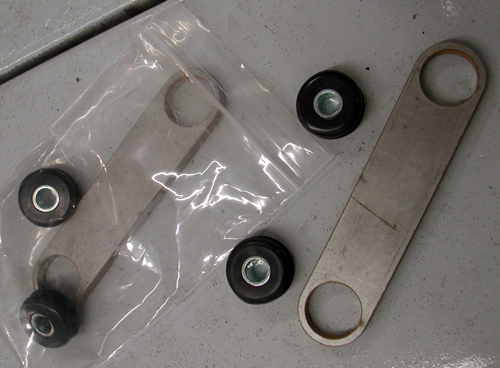
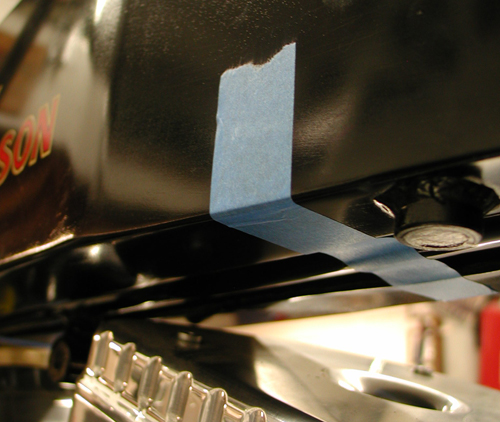
There's a trick to this operation. You need the rubbers in place to make proper measurements, cuts and tack welds. Ah but, too much heat will destroy your rubbers and sink the process. I've done it during mad welding spurts. This time I kept my Bonneville salt sprayer handy, so I could tack near the rubber insert and cool the strap before I damaged the insert. I removed the inserts before final welds.
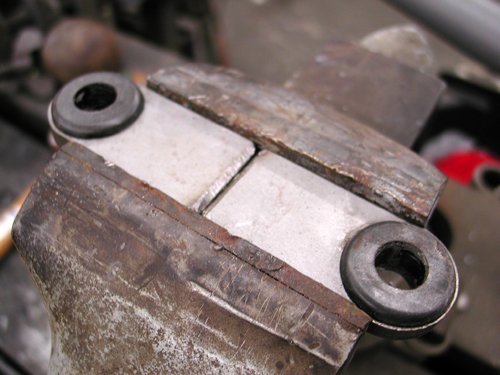
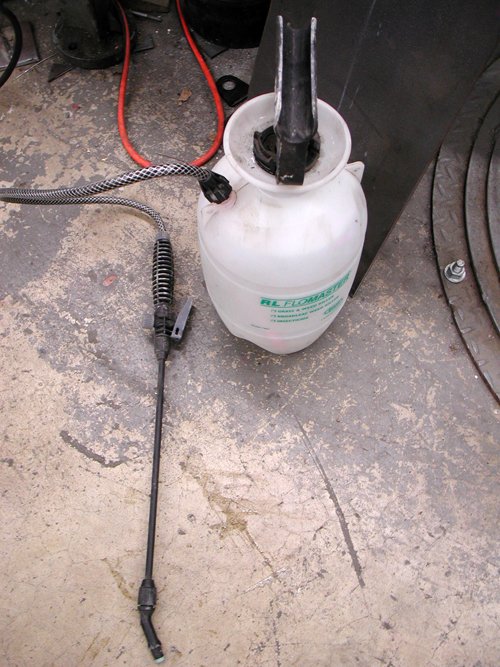

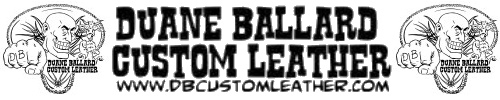
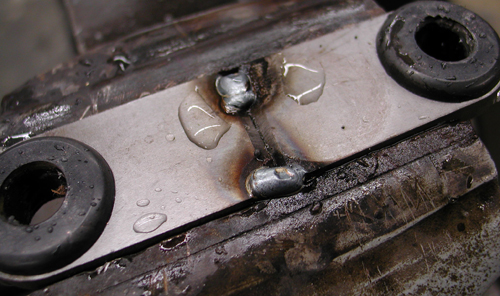
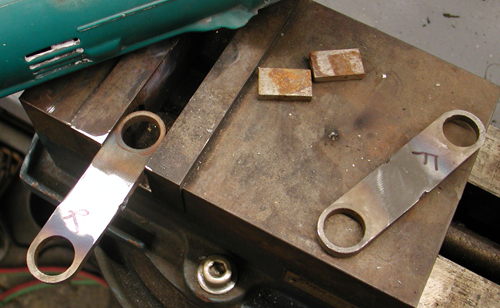
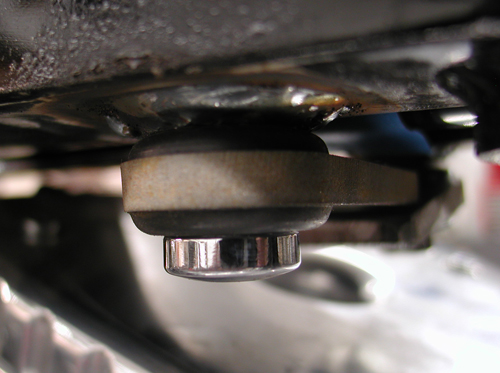
With the tanks securely mounted, I was confident, except for one aspect: capacity and turning radius. I needed to pull the bike away from the lift clamp and flop the Paughco taper-leg springer from side to side. As I suspected, it was going to hit the tanks. Over the next couple of weeks, I will operate again, slicing the tanks for turning.
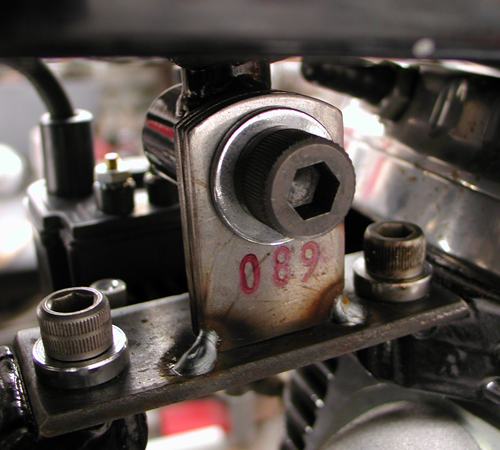
I shifted to making a top motor mount, which worked out like a champ. I made a strap from one Crazy Horse head to the other, then discovered a couple of tabs that would give me the strength and position I needed to hook up with the frame. Top motor mounts are also tricky. They need to be flexible and somewhat adjustable. I made sure the engine was positioned correctly with my BDL primary backing plate, but you never know if something might shift slightly during final assembly, and the top motor mount must be flexible and iron strong.
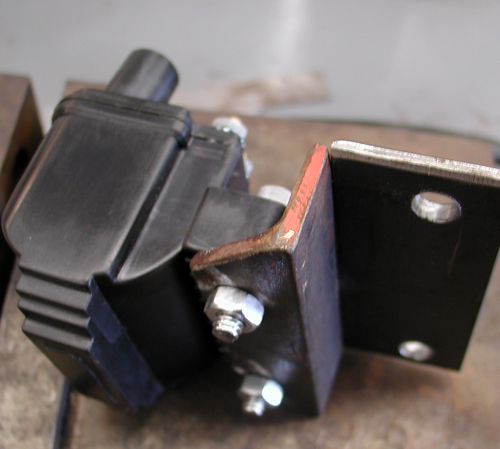
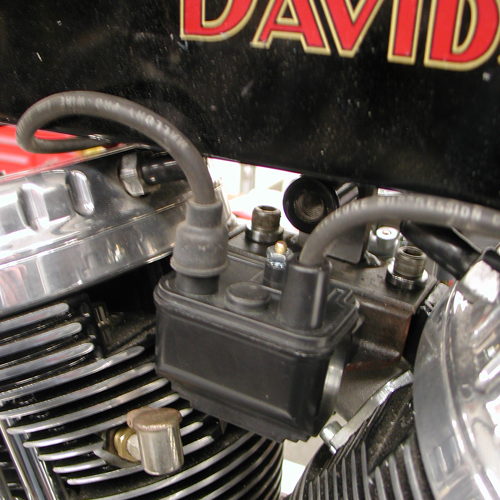
Without too much fanfare, I attached a piece of modified angle iron to the right side of the motor mount for a coil hanger. I angled it slightly so the spark plug wires wouldn’t bang or rub against the tank.
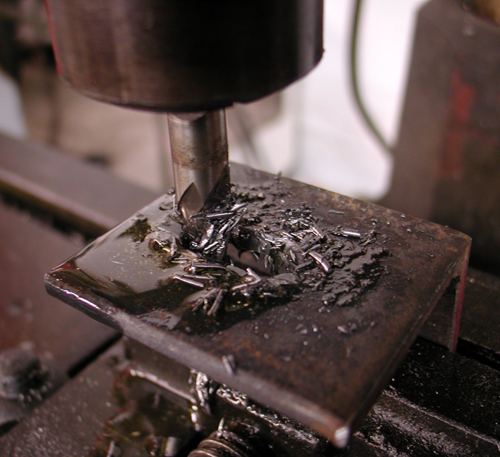
It just happened that I'm building a railing for my mom's house. She's getting feeble, in her old age and needed some additional support. That meant a trip to the local steel supply house, where I stumbled onto some small chunks of angle iron. I didn't like my original number 5 transmission mount, so I decided to remanufacture it with a heftier piece of angle iron that also reached the frame without a problem. It also allowed me a tad more positioning flexibility for the master cylinder and pedal adjustment.
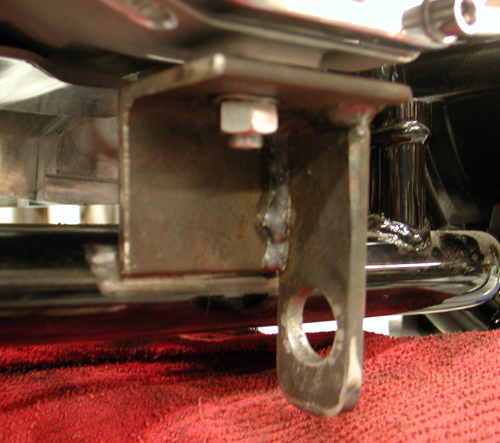
In the next segment, I'll run the progression of Dick Allen illustrations, so you can see the progress. It's as if I'm building the motorcycle, while Dick and Chris Kallas develop the visual story.
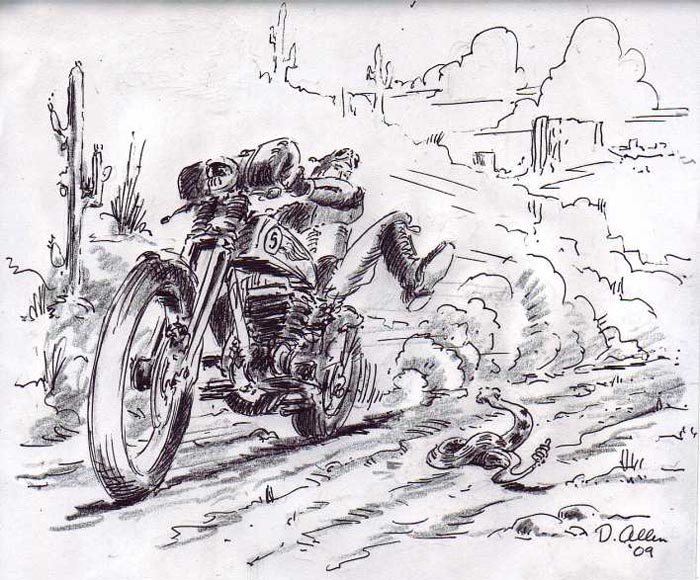
I don't know about you, but these illustrations give me hope and inspiration throughout the build process. Next, I will modify the tanks once more for enhanced Paughco Springer turning radius, then we'll mount the Phil's Speed shop ignition and wiring system to a plate I'll make that will bolt to the top of the tanks behind the gas caps.
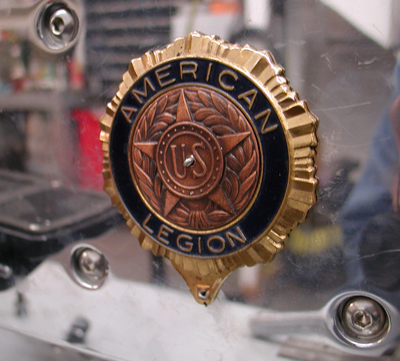
Also mounted to same plate of steel will be a manual, vintage Sportster replacement, Bikers Choice speedo driven off the rear Black Bike wheel. Hopefully, the wheels will roll in, I'll find some 23-inch tubes and Larry Settle will mount and balance the Avon tires. I'll set up the wheels in the frame and springer, and then haul the bike to Chica in Huntington Beach. He's going to help me with fender design and mounting. In the meantime, I'll watch the inauguration unfold and stay away from tequila. There's more coming, though. I'm going to modify the trans with a 5-1 Baker drum, and build a set of exhaust with D&D bends and pieces. Hang on for the next installment.
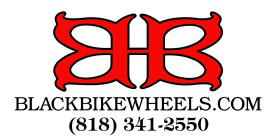