Road King 4/15/09
By Robin Technologies |
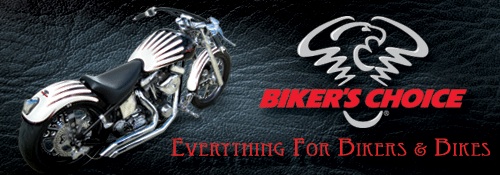
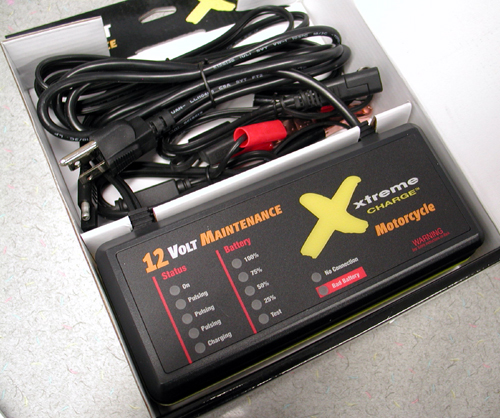
We decided to take a run at an electrical article, since about 90 percent of problems and breakdowns come from the electrical component. Besides, it’s riding season and we all need to check our electrical connections before we ride off into the sunset. This is especially true of bikes stored in moist or seaside climates. Besides, I’m riding the King to Laughlin and need to check it out. It’s been awhile. Here’s the lastest upgrade to the king: King Meets Zippers and D&D
This article will cover some basic electrical checks, since being forced to charge your battery indicates deficiencies in your charging, or wiring system–or you left the goddamn lights on.
This rambling will also cover all the aspects of the latest battery charger from Biker’s Choice, the Xtreme 12-Volt battery maintenance charger. If you find it necessary to charge your battery, take it out of the bike and place in on a wood or fabric surface, not steel or concrete (draws battery charge). Make sure the terminals are clean. A loose or corroded terminal will prevent the battery from accepting a charge. No shit, just that will leave you along side the road.
Corrosion, or bad grounds cause most electrical problems, especially in dense humidity climates. Check your grounds annually; clean the connectors and the ground surface.
Batteries are nasty dangerous bastards. Make sure to protect yourself around them. Don’t mess with a battery near flame, extreme heat or next to your custom painted Ferrari. If the bastard explodes, you could lose your eyesight and that $5,000 paint job. And that acid crap is super nasty. Don’t get it on anything. There is a cure. Mix some baking soda and water and have it standing by to clean anything with battery acid splashed on it. This is no jive. If you get battery acid on anything, it’s toast. Believe me. I have a number of holy shirts from acid meetings.
Wear eye protection and don’t fuckin’ smoke around batteries. Fortunately, for incased batteries, we don’t have to mess with acid as much anymore, but I’m still building choppers and using bullshit little batteries with acid requirements. Whatta mess. Make sure the area used for charging is clean and well ventilated. Okay, enough for the safety procedures. The Xtreme Charger comes with complete safety warnings.
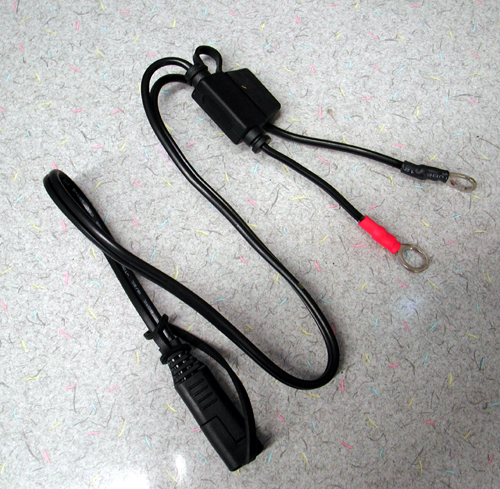
For years I liked Battery Tenders, because they monitored the charging process and dropped the charge level automatically, when the battery was completely charges. If the charge level dropped, the automatically kick into gear again. This Xtreme charge handles those tasks and more to keep your battery strong and charged. Below is the full description of the Xtreme capabilities. The kits also come with a lead set you can bolt directly to the battery for easy access at anytime. Check this out, then we’ll give you some testing, trouble shooting electrical tips:
The Xtreme Charge is ideally suited for AGM and Maintenance-Free Batteries. The combination of PulseTech’s patented pulse technology and proprietary charging algorithm allows it to charge these high-performance batteries more fully while maintaining a safe charge profile for traditional batteries.
The Xtreme Charge Battery Maintenance charger comes in variety of colors, which may suite a particular need. If your looking for the best battery maintenance charger for use on any 12v battery rated from under 10Ah to over 150Ah, pick your color, and get one today.Includes fuse-protected quick-disconnect battery clamps and lugs, Important Safety Instructions and Quick-Start Guide. The Xtreme Charge is fuse-protected, spark-proof, and is UL and CE certified.
Comes with a Five-Year Warranty
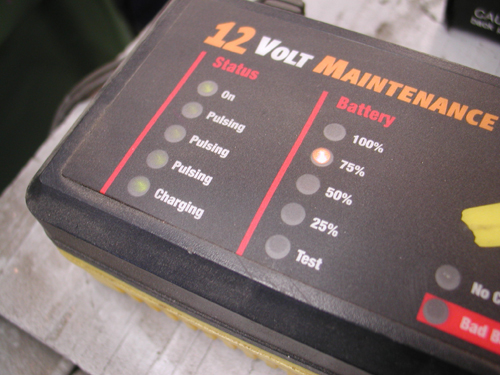
Xtreme Charge Maintenance and Charging
The Xtreme Charge is a microprocessor controlled maintenance and bulk charger for any type of 12-V lead-acid battery. It features PulseTech’s intelligent circuitry, which imposes only the correct amount of charge rate as determined by the continual evaluation of the battery’s condition. By using only the appropriate amount of charge rate, the battery is maintained safely at its proper operating voltage indefinitely. Conversely, if the charger is connected to a discharged battery, its bulk charge capability (2.5A actual/5A effective) will re-charge the battery rapidly and safely so it can be put back into service quickly. Charge rates may be as minimal as 0.2A during typical float up to the full 2.5A for more deeply discharged batteries. This variable float charge ensures optimal charge rate is applied to the battery at all times.
PulseTech’s unique and patented PULSE technology increases the duty and life cycles of your battery by minimizing the size of the lead sulfate crystals. This allows a battery to accept as much charge as possible. PULSE technology helps ensure that your new batteries will stay in like-new condition while improving older batteries dramatically. Duty cycles are typically extended from three to five times for all types of lead-acid batteries!
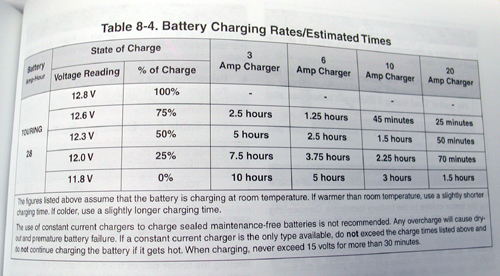
PulseTech’s ReNew-It Pulse Technology
Twelve years ago, PulseTech applied its technology to a full line of innovative and unique products designed to make batteries stronger so they will work harder and last longer than ever before.
To get an idea of exactly how important PulseTech’s technology is to the performance of all your powersport toys, consider this: The main cause of vehicle failure is battery failure. The main cause of battery failure is sulfation buildup on the battery plates. And ReNew-IT Pulse Technology prevents sulfation buildup.
When it comes to a dead battery, chances are it is still good. You just can’t reach the energy due to sulfate buildup. That means you have to buy another battery even though the one you have may still be useable. Xtreme Charge helps prevent this problem.
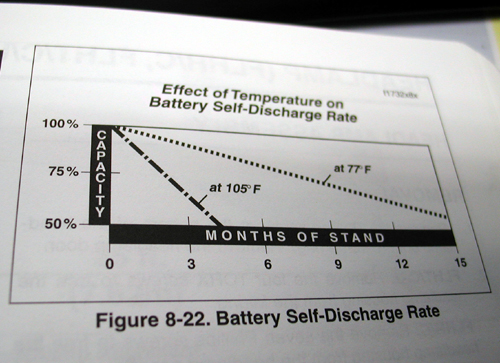
How Renew-IT Pulse Technology Makes Batteries Stronger
PulseTech’s Xtreme Charge connects directly to the battery. The Xtreme Charge emits a pulsating DC current that removes the sulfate deposits from the plates and returns them to the battery acid as active electrolyte.
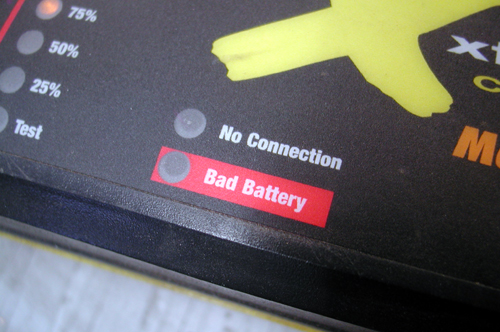
Here is how it works:
1. Lead-Acid batteries work by releasing energy through an interaction that occurs between the positive and negative lead plates and the lead sulfates in the electrolyte.
2, Sulfation buildup occurs as lead sulfates form on the battery plates during the normal charge/discharge cycles. During this process, some of the sulfates enlarge to the point where they won’t accept energy so they stay on the plate. Over time these sulfates can build up until efficiency is reduced and finally the battery dies.
3. ReNew-IT Pulse Technology works to prevent sulfation buildup by removing the sulfate deposits from the plates through a unique Ion Transfer process.
4. The lead sulfates then return to the battery acid as active electrolyte. When connected on a regular basis, our battery maintenance systems will also keep the sulfates from building up again.
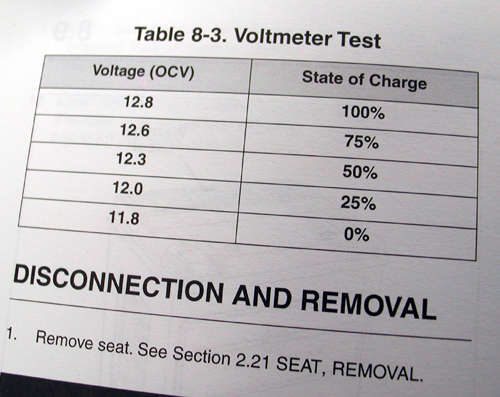
Get True Battery Power
PulseTech’s technology works with all types of lead-acid batteries including sealed, gel cell & AGM. By keeping the plates “clean”, batteries charge faster and deeper so they work harder and last longer than you ever thought possible. They also have greater charge acceptance so your battery will recharge faster and release all of its stored energy. With more available energy so your vehicles last longer between recharges and your electronic accessories work better. You get the true power of your batteries.
Some of our patented products also prevent the normal loss of battery power on stored vehicles and equipment no matter how long they sit unused—even months at a time.
They even help protect the environment. Since batteries last longer, it reduces the danger of contamination caused by lead and sulfuric acid dumped from prematurely discarded batteries.
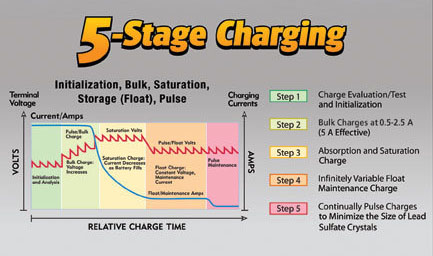
Xtreme Charge 5 Stages of Charging
1. Initialization: Xtreme Charge’s unique test feature evaluates the battery thoroughly during initial connection to determine the appropriate charge rate based on its size and condition. It tests the battery continually for as long as it its connected to the charger to maintain the optimal bulk or float charge rate. This test step incorporates a “Bad Battery” indication if it determines the battery is faulty and can not be charged.
2. Saturation: A proprietary computer-integrated technology measures both the voltage and current to determine the appropriate amount of charge the battery is able to accept at any given time. As the pulse and saturation charges improve the battery’s condition, the charge rate is increased safely to an optimal level. This proprietary algorithm protects the battery from the risk of damage due to overcharging.
3. Storage(Float)
4. Pulse(De-Sulfation)
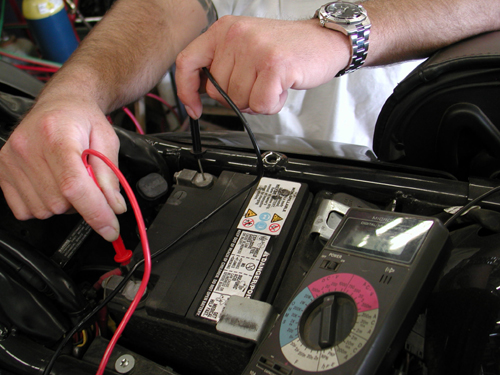
Testing Tips
I reached into a couple of Harley manuals and to Pablo, our Bikernet Harley factory trained technician for additional info. If you suspect a problem with your charging, you’re experiencing sparking when you hit the starter, or the battery needs to be charges, here’s some tips.
First, check all your grounds and battery posts for connection and cleanliness. Then take a voltmeter and run it across the batter whiled the bike is idling. It should indicate 12 volts (see chart). Now run the throttle up to about 2,500-3,000 rpms. The indication should jump above 14.1 volts, indicating that the charging system is working.
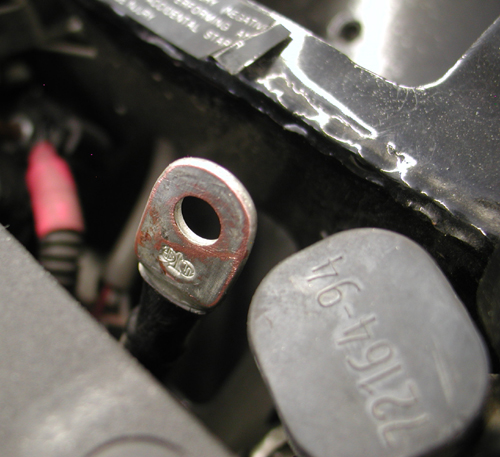
Before you toss the regulator and replace it, you need to check the connections with the alternator. Make sure you haven’t lost a ground or run over a speed bump and ripped through a wire running along the bottom of your frame, which is against the code of the west. Don’t run wires under frame rails. Keep them up and out of harms way.
To check the alternator, here are a couple of tips. Pablo suggests that you take an old regulator plug, with the wires and create a testing lead. If you check the resistance to ground on each lead, they should be open. “But if you take the derby off your primary and run into that burnt electrical smell,” Pablo said, “the alternator is toast.” There’s also an AC test. Start the bike and run it up to 3000 rpms. Attach your alligator clips to your alternator leads and it should read over 40 volts or 16-20 volts per 1000 rpms.
“With the newer models, we have seen some issues with the bikes having batteries going dead after a couple of days,” Pablo said. “A milliamp draw test and total current draw test is the first things you check in the H-D flow charts. Corrosion on the system relay on some models can cause this.”
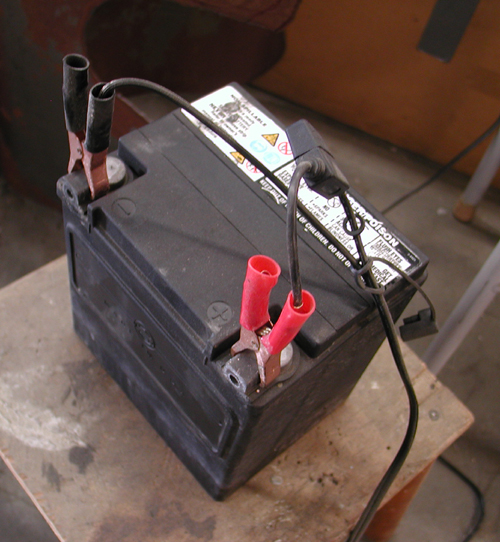
“The service manual, including the electrical diagnostic manual are a must on the new models. You basically have to be a Circuit Head to work on these things nowadays. The H-D Digital Tech we use at the dealership also helps with the serious hard to find electrical gremlins.”
“Fuck, I’m just a old Seabee resistant to change. Man invented technology to frustrate himself you know. Just look at what we have done to a motorcycle over the years. Seriously though, one can, with a cheap DVM (Digital Volt Meter) do allot of trouble shooting on the H-D charging system. Like checking the stator for AC volts output. A grounded stator, continuity checks, etc.”
One more addition from Pablo: DC Voltage output at the battery with the bike running is also a quick check. The system should be putting out over 14 volts but not more than 15 volts at 3000 RPM. Usually, you will see like 14.1 to 14.4 volts or so, that is if the regulator is good and shunting excess voltage to ground.
So, with the Xtreme Charger and a volt meter, you can check your battery, the charging system, the alternator and check for bad grounds and busted wires. That’s all you’re gonna get from the Bikernet tech staff today. Let’s go to the Cantina for a beer.
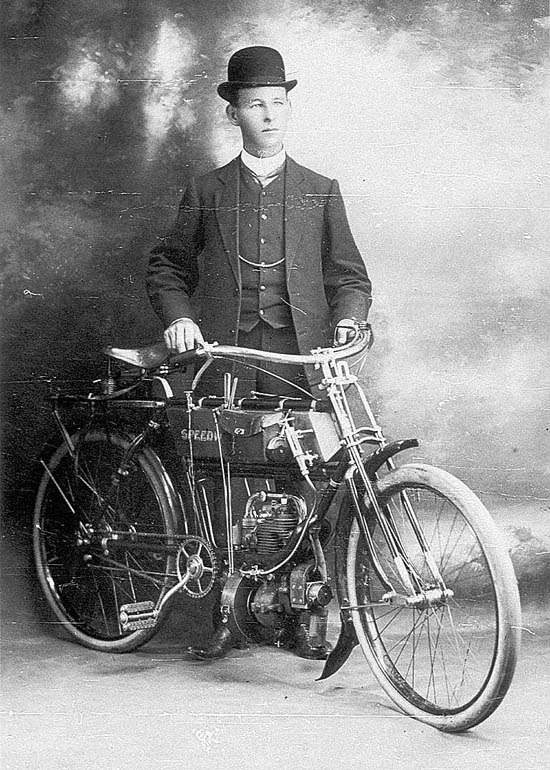
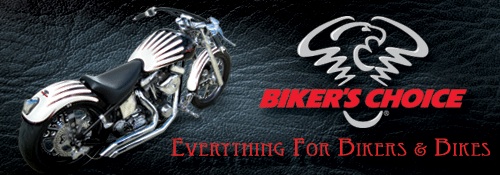
Sturgis 2000 – Part 4-3
By Robin Technologies |
That last 25 miles were the worst of the trip. It rained off and on as the traffic became thick as mud on your boots. Lane splitting is not allowed and when we attempted to play ignorant travelers, motorists tried to hit us. As the sun broke over the parking lot of cars, the humidity rose with the mercury. Of course we got lost at one point, found the Two-Wheelers shop and ultimately the hotel. There was a major party planned for the 25th anniversary of the shop, but the threat of rain and the 450- mile trip to Sturgis the next morning forced us to take it easy and hit the hay early. We tried a local restaurant for grub, but they still didn’t serve peach pie. The next morning, Myron and I were on the road by 4:30. An odd feeling swept over us as we rode Highway 25 in the dark. In the rolling fields and wide open spaces of Colorado, it was as if we were lodged on the brink of the city. There wasn’t a row of houses or an industrial park once we turned north and it felt good. We rumbled for 90 miles until we arrived at Cheyenne, Wyo., for breakfast. We hit the road for another 75 miles and pulled off in Wheatland where we refueled and had one of Myron’s safety meals and coffee. He works out constantly and feels that his success in the gym is attributable to his intake of protein. He doesn’t eat a lot or poorly, but often and bushels of protein. As we walked out of the restaurant, we were met by Cheryl. Tom’s bike had a broken shift lever and he was working on it. “How the hell did you get here?” Myron asked. “Uh,” Cheryl muttered, not sure what to say. “What time did you leave?” I asked. “6:30,” she said. We looked at each other in dismay. Myron jerked on his gloves. “Let’s ride,” he shouted, “We’re burnin’ daylight.” We spit dust and rocks as we blasted out of the gravel lot and onto the highway. Suddenly he was hell bent for leather. We stopped just for gas in Orin and headed east on 20/18, blasting toward the small town of Lusk, Wyo.
![]() At the end of town we stopped for another safety meal. We had 130 miles to go to get to Sturgis, but the roads would narrow and we’d have to slow down. Across the street the bikes were lined up in front of the western bar. I liked this town. It’s small but has some action going for it. As we turned toward the door of the Del Rey Cafe, Milo strolled out the door pickin’ his teeth with a tooth pick. “Damn!” Myron said and almost abandoned his safety meal stop. “What the fuck are you doing here?” Milo shrugged, straddled his all-black dresser and took off. The waitress would melt a good man’s bones with her silky, fair complexion, even lighter hair and brilliant blue eyes. My words were stumbling when I asked for peach pie, but I lost all interest when I discovered that she had just run out. “You mean you didn’t save me a slice?” I shouted, throwing my tan gloves on the table. In Newcastle we stopped momentarily for gas, but as we paid our ticket we noticed Hamster Jeff pull into the station. Myron grabbed his gloves and headed for his Dyna. “Fuck the peach pie,” he shouted again, “Let’s ride.” I tried to holler to Jeff as we headed out of the station and hit the highway toward Four Corners. We were in a race now, and although Myron said to most riders as we left them in bars and gas stops, “Keep it under a hundred,” this time it was different. If we had open straight roads ahead, throttles would be pegged to the stops. He couldn’t figure out how these bastards who left the motel two hours after we did were catching up. Hell, we were rumbling along at 85 plus, but we had 14 meals to their one cup of coffee. What the fuck? Now we were in narrow canyons weaving through packs of bikers heading to their homeland. Again the chopper handled the curves as if I were on a rice rocket, dipping and bending with each bank. Each gas stop was spoke to spoke with lines of motorcycles to refuel. Each bar looked like a popular biker hangout from Southern Calif. on a Sunday afternoon.
![]() They were coming from all directions. The rumor of afternoon thunderstorms had us pushing the envelope. Our bikes were a mess, but they were running and we were ready to hit the home stretch for our abode in the Bad Lands. Finally, in Spearfish Canyon 15 miles from home, we slowed and enjoyed the Jack Pines and the bustling brooks that bordered the winding road. We were home. Home to the biker, the outlaw, the bandit and to every fucking rider in the world who enjoys open roads, beer, broads and peach pie. Now if we could only find the girl, or at least a piece of pie.
![]() –Bandit PS. Zebra had arrived four hours earlier. We immediately gathered up the boys and found the only bikini bike wash in town. Following is a couple of miscellaneous shots from Sturgis 2000. It was a helluva year.
|
Sturgis 2001 Buell
By Robin Technologies |
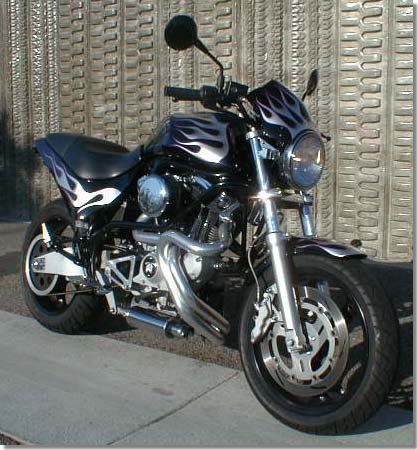
It’s part of our job as moto-journalists to try what’s outthere in the American market and report back. The ultimate test is to take a bike, customize it and ride it to Sturgis. What could give you a truer test of a bike’s ability to look cool and endure a long run? I’ve been fortunate enough to customize and ride everything from nearly bone stock bikes to ground-up customs. Each trip is an adventure. Each run has varying characteristics, and with each journey there’s a new woman, but that’s my problem.
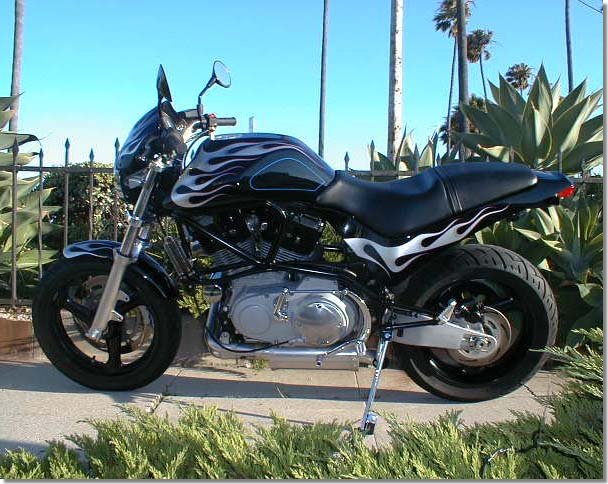
This year we needed to make a choice. I had a Kenny Boyce ProStreet frame that I planned to load a Twin Cam engine into and rideto the Badlands. I also had a 2000 Buell M-2 and I had recentlyinstalled dual Mikuni carb heads on my ’48 Panhead. Since I’m alsoworking on a Pro Street custom for Dr. Ladd Terry, the Bikernetmorale officer, I decided to hold onto my Pro Street project for nextyear. Another doctor, Dr. Hamster, had been working on his 34 VL andwas excited about riding it to Sturgis. We both knew that the antiqueride would be a long shot.
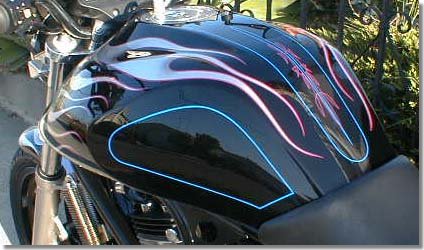
On top of the time/money consideration, I enjoy riding the M-2. It’s the hotrod of Harleys, light, agile, brakes like a madman and hauls ass. The guys at Harley like to refer to Buells as their street fighters. I have to agree. So I decided that I needed to put some miles on it and experience its ability for distance. Like last year when I told folks that I was going to ride a rigid toSturgis, I got the same reaction to the Buell. I rode it toLaughlin with a passenger and soft saddlebags. The bike handled likea dream. At 100 mph, it was more stable than most Big Twins, andacceleration was always at hand. There’s no hesitation from zip to 100 mph, and that’s my riding range.I was advised at one point to put a smaller pulley onthe rear for lower rpms while cruising. Later I found that themodification had its glitches. I found that the bike was glass smoothat 100 and still zippy and that was good enough for me. We began aseries of mild mods with a cam change to the Screamin’ Eagle raceversion and added the stainless race header. My partner to Laughlinhad a blast and was so comfortable she passed on several rest stops.We kept going and ran out of gas in the desert. So you can understandwhy there’s a new woman each year. She’s still out there somewhere.In the final analysis the decision was made to ride the Buellto the Black Hills Rally.
If you’ve read the techs, you know what wedid to this puppy, so I’ll go beyond the build to a few conceptionsabout Buell. First, there is no fairing to speak of, but I actuallyfound the bike extremely comfortable to ride. The little chin fairingkeeps the big blast off your chest and I didn’t need anymore. I mayregret those words as I hit the Colorado monsoons, but so far, sogood. Some guys complained about the sitting position, but I found itcomfortable once I knew how to sit. Like any bike, you need to findthe groove. The brothers talked about leaning on the bars and toomuch weight on the wrists. I found that if I leaned over the bars Iput excessive weight on my grip, but if I sat on my ass, it was nodifferent than other bikes, although under hard braking situationsyou are thrust forward.
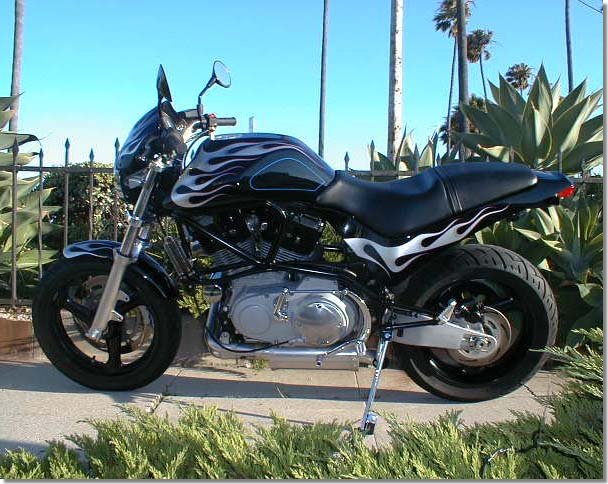
Some felt the ride on a Buell would be rough, yet most wereunaware that the bike is basically a rubbermounted Sportster, andincredibly smooth, especially at 80-100 mph.
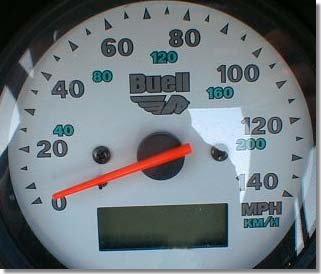
Others thought I mightlook ridiculous, and I told them I look ridiculous all the timeanyway. What difference would this year make? Others don’t like midcontrols. If you’re not used to them, you may find that you need toadjust, but once you get the hang of them, you’ll find less pressureon your back.
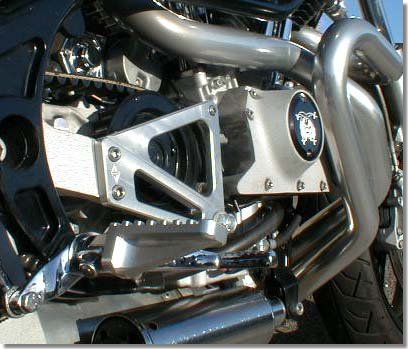
Alright enough perceptions and conceptions, let’s get readyto ride. The Buell has 400 miles on it since we made thecosmetic changes and cured some rocker box leaks.
This last week weinstalled Joker Machine billet and anodized turn signals on it and hidthem as much as possible.
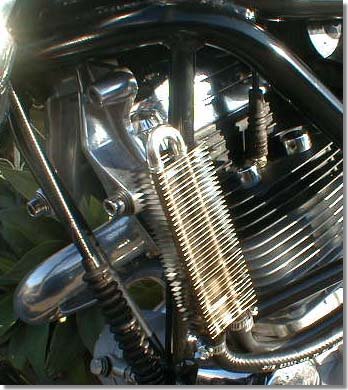
We picked up a small oil cooler from ChromeSpecialties and installed it with longer oil lines at the front ofthe bike. The oil capacity is about 2.5 quarts, which always makes menervous, so we changed oil and plugged in the largest Dyna oil filterwe could find. The filter and cooler combination allowed us to squeakin 3 quarts and take some precarious kinks out of the lines. I alsostopped by Joker Machine and they liked the mods so much they told meto run one of their point covers or die.
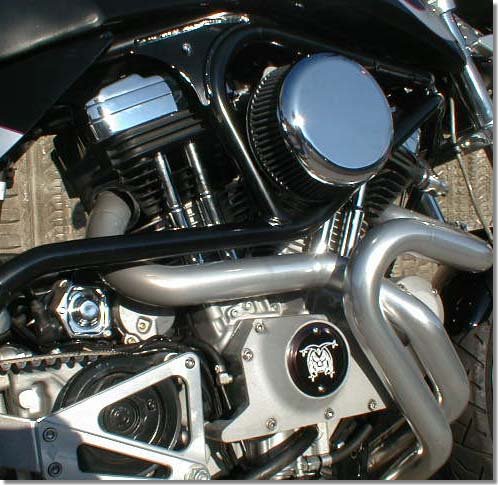
Dewey’s Custom Pegs makes thecleanest air cleaner cover on the market and it fit like a dream.Finally we ordered a chrome hardware kit for the rear pulley. While disassembling the rear wheel, we polished the right wheel spacerand the belt adjuster guides–not bad touches.
So Sturgis 2001 is one week away. If I collect enoughaluminum cans off the beach I’ll have a pile of quarters for spendingmoney. The woman in my life is the best candidate to run Bikernetwhile I’m on the road, and I’m ready.
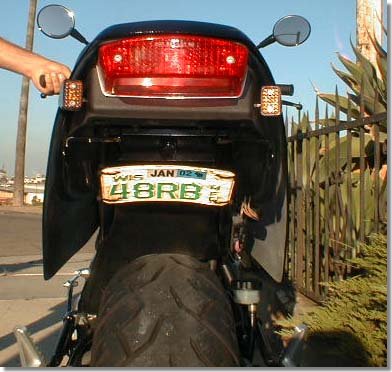
This is our quest each year,to build a vehicle and make it to the Badlands to talk about it. I’llhave a full report upon my return. Hang on.
Sturgis 2000 – Part 3
By Robin Technologies |
The next morning, after breakfast at Stan’s diner in Scottsdale, we rolled north toward Payson on our way to Holbrook. Stan’s is a small joint in a dull rectangular building downtown, that Stan tried to spruce up with adobe chairs and tables. A skinny waitress came to take our order but since this was Myron’s regular digs, he went directly to the chef in back and nodded. That was enough. The chef knew what to do. Karl and I attempted to order with smiles on our unshaven mugs but the waitress was dry as toast, and edgy. The cactus twig of a woman could not comply. We had been trying the low carb regimen and Karl had lost 40 pounds, but she couldn’t allow us to substitute potatoes for tomato slices or cottage cheese for toast. We ended up ordering everything a la carte. At first our easy-going hackles were raised because we wanted to hit the road early and slice away some dusty miles, then eat in some strange hole-in-the-wall joint in nowheresville, Arizona. But the more we irritated her, the more fun we had. She was spitting in our scrambled eggs by the time we finished with her, but it was worth it. Phoenix is a strange city. Surface streets are straight and packed with stoplights. We headed out a country road through one boulevard stop after another. Suddenly we were out of the flat city and into the country, winding into the Mazatzal Mountains on Highway 87. At one point we pulled off the highway at an All-Bike junkyard Rye, Ariz., a town with a population of 300. There were acres of bikes rotting in the elements.
![]() At this point there were four of us. Myron was riding his black, detailed 2000 Dyna with a 95-inch kit, stretched tanks and a custom windshield. As usual, his bike was immaculate with chromed Harley mags and diamond cut cylinder fins. He had soft bags beside the rear wheel and a bolt-on sissy bar with bags attached. He was one comfortable mutha as we cut through the canyons. The man generally wears a long sleeved T-shirt with a regular T-shirt over it and his HAL vest, plus a scarf. He rides fast and tight. Myron has always reminded me of longtime friend George Christie, the president of the Ventura chapter of the Hells Angels. Although Myron is a massive weight lifter, and George trains in martial arts, the two men are similar height with jet-black hair (graying some, now). Both men are born leaders and strong riders. Karl was on his lowered Softail with drag pipes and drag bars, with his buoyant wife of 25 years at his back. The couple have raised three gigantic kids, consequently Karl doesn’t have new bikes yearly, custom paint jobs and chrome. He’s saddled with a non-working mother and three money-soaking monsters to raise and he’s proud of every minute he can keep the clan in college, clothes and wheels. I respect the fact that Cheri stays home with the kids. It’s a full time vocation and perhaps the most important job on the planet.
![]() The mountains were striking and I’m constantly amazed at the Arizona beauty. The state is diverse and open. No wonder people are lining up to move there. It’s a killer place to live. The diversity is unreal, from the arid, open, hot-as-a-mutha desert to the rolling, pine-strewn mountains and the Grand Canyon area. We stopped in Payson for gas. I had clocked 87 miles and took 1.9 gallons. I was still rolling along even in erratic terrain and getting 45 mpg. I bought a cheap tire gauge and checked my tire pressure. Brownie had jacked it up per the tire specs, but I was more flexible and had another priority — the ride. The front tire being on an extended front end didn’t need 50 pounds of pressure and the rear 180-18 Avon needed to be as soft as possible, so I dropped the 40 pounds to less than 30. As I stood there, Cheri chatted away about one thing or another, constantly making sexual references to the most absurd articles. She somehow found honey mustard dressing sexual, or elevators, though I could understand her phallic reference to pickles. As we moved into the hills, the incline felt good to the 98-inch S&S motor. Rumbling up a winding incline, we found ourselves behind several motor homes and a logging truck. When we hit a passing lane, two tourists melded to the right and the logging truck and one camper stayed to the left as if in a 1/4 mile they could pass the other dog-slow travelers. I down shifted and poured the fuel to the stroker, which climbed on the other vehicles like they were standing still. The lumber truck was barely reaching the rear bumper of the motor home when I split between them. I blasted over the rise ahead and began a high-speed decline. I slowed slightly to let the others catch me, but they didn’t come. I slowed some more, then suddenly noticed a thundering 18-wheeler bearing down on me. I had upset the trucker and he planned to flatten my ass. The rigid Blue is light, and I was discovering lightning-fast throttle response. I bolted forward. I spun the throttle, again, and it came alive like the crack from a high velocity .22. Then I noticed a new vibration. It was coming from the tank. The truck was trying to gain on me again, and I slipped the polished 42-mm Mikuni more fuel and she responded like a tongue to a sensitive clit. The bike jumped and roared ahead. Again, a rattling screamed at me from the top of the frame and I pulled my gloved hand off the left grip and put it on top of Harold’s paint work, which glistened in the sun. My teeth immediately responded to the touch. Something was wrong, but I had a semi barreling down on me and I couldn’t stop. I didn’t want to pull over and give him an open target so I pressed on the tank with my left hand and pushed harder on the throttle with my right. I raced past the signs indicating a dangerous decline ahead and warning truckers to check their brakes. The guy behind me had no notion of using his as he sped to catch me. Fortunately, I could outrun him, if I were riding a bike built for mountain riding. This was my first opportunity to test the handling of the 38-degree raked frame with the 6 degrees in the Weerd Bros. front end. I had specifically built in plenty of ground clearance by cutting the Samson pipes and lifting the front header. There was nothing on the left to interfere with the road and I had a solid six inches of ground clearance underneath the frame. As I leaned I felt the bike want to tumble so I poured more fuel and the front wheel tracked the corner smoothly. The next corner was well marked for speed and curvature. I dipped low and accelerated. Although the rake generally, with speed, wants to force the bike to go straight, the additional rake in the triple trees minimized the trail and the front end adjusted easily to the turn, but I was trying to hold on to my vibrating gas tank at the same time. Another series of turns were dead ahead and the screaming logger was shifting gears 30 feet from my rear Avon. He knew the road better than I did. I took the shift as a signal of manageable turns ahead and turned the throttle. The bike jumped forward and I released the tank to handle the curve. To my left were open oncoming lanes through sliced mountains. To my right was a sheer precipice and a majestic valley a couple thousand feet below. I pushed the Blue Flame and it responded like a thoroughbred. It felt strange. I had ridden choppers for years, but in the last decade I hadn’t ridden a bike with this length of front tubes. The Jesse James touring chopper had a severe turning radius restriction with the bags, but this machine seemed to have no bumpers, no drag, no pegs that prevented me from leaning it closer to the asphalt, so I pushed. The only thing that would hold me back from making the next turn was Avon traction, a flexing Daytec frame or a squirrely front-end. I seemed to handle turns to the right easier than to the left, and I dipped as the curve unveiled itself. The truck was right on my ass as I hit the 35 mph turn at 60. The most terrifying aspect of any turn is the visual. Can you see the chamfer and the complete arch? Is there a mountain on the inside preventing visibility? Are you heading downhill? Downhill racing is the worst. You can let up on the throttle and the bike won’t slow down. That’s the last thing you need when you realize that your bike cannot make the corner. I needed deceleration and it wasn’t there. I had pulled away from the truck, but the tank was singing a violent tune. I ignored the horrible vibration and dipped the machine to the right. To my amazement, it went over easily. Nothing scraped, skipped, twisted or jiggled. The tire remained firmly planted to the road’s surface and I accelerated through the turn and into the next one. The truck loomed behind me except it wasn’t barreling after me this time. The postings along the side of the mountain warned of the steep slope, brake testing and slow trucks. The driver had chosen to ignore the warnings and careened after me, but now in the rearview mirror the trucker’s load seemed out of balance. The massive logs were jostled. The truck leaned at an odd angle. The driver had abandoned the pursuit in favor of saving his own neck. Smoke poured from the brakes as he tried to control the 80,000-pound vehicle before he encountered another curve along the perilous slope. I glanced at the valley below and decided he was more of a threat now than when he was pissed and in control. I turned up the heat and headed quickly away from the collision-bound truck. We had several junctions ahead, including 377 to Holbrook, 277 to Snowflake and 260 to Show Low. With each curve I was forced to test, I became more confident in the Daytec chassis and long Weerd Bros. wide glide front end. I had never owned a chopper that handled with this much ease. I seemed to be able to dip the flaming scoot over so far that my calf was parallel with the pavement. I hit the town of Heber where we had planned to stop for a piece of peach pie, but I blew right through. I passed the 377 turn off and prayed that the trucker survived, but was on his way to Snowflake. I split off on 260 toward Show Low and quickly found a safe place to pull over to check my tank and wait for the others. The rear tab on the tank had broken and the vibration between the remaining tab was eerie, but with the 3M weather stripping holding the tank to the frame backbone and the front tab in place, all appeared secure. Myron pulled up with Karl and the emotional Cheri shouted, “That truck was after your ass.” We only had another 30 miles to go but we hit a hardware store and, based on expert breakdown recommendations from Karl and Myron, I picked up more 3M stripping, JB Weld, sand paper and some grommets. I rode carefully for the final 30 miles into Holbrook where we copped a couple of rooms and prepared to operate on the Blue Flame.
![]() I almost had to pry the tank off. The rear tab was toast and I spent an hour cleaning it. I mixed and spread the JB weld, put down new 3M weather stripping and reinstalled the tank. It was time for happy hour and we walked to the local cowboy/sports bar across the highway. There’s an odd sensation that comes over a rider with a busted machine. It’s as if you know you must hike to the top of the hill, but you’re bleeding. You know you’re going for it, but not sure how you’ll make it. Still you keep moving forward. Holbrook was our stopping point about 250 miles out. The bar was cool and for some reason, perhaps the unrelenting heat, we ordered margarita after margarita, then chicken wings, chicken tenders and more wings. Those little puppies were smoldering but went down like chips at a Mexican restaurant. We munched as if we weren’t going to eat for a week, then went in search of peach pie. Why is it that once out of California, fresh vegetables and fruit seem impossible to come by. If I couldn’t have sex, I wanted peach pie, and for some odd reason, it seemed as rare as a whore in church.
|
Sturgis 2001
By Robin Technologies |
Buells are the Harley-Davidson street fighter. They are inexpensive,sharp-handling machines that give the American rider something toshout about, something to fuck with and something to race.
This bike won’t compete with the 200 mph Japanese sportbikes, but it will handle like one, and brake like one. So we gothold of one and evaluated it for the Sturgis 2001 run. Since I come from a custom bike or chopper background, I wasn’t sure the Cyclone would do the job for me. If you ask a guy who rides a custom bike what style of bike he enjoysand why, the answer might be strange. I want something distinctiveand bad. I want it fast and cool. I need it to handle, but be achopper. Perhaps an oxymoron of conditions, yet there’s a mixture offactors that go into any ride and machine. Last year I rode astretched rigid with a 14-over front end. What a machine. For a rigid,it rode like a dream. For a 14-over front end, it handled well and Ipassed everyone I dared to pass, generally because I had the groundclearance to shove it close to the pavement and the raked tripletrees allowed me to turn the front end where I needed to go.
Each year the trek to the Badlands takes on a differentdemeanor, and this will be no different. After a week, I discovered a serious sense of enjoyment about straddling the M-2 Cyclone. It’s light, fast, a nimble handler that stops on a dime. I needed to learn to ride it like a race bike with my toes on the soft rubber pegs to enhance turning radius and ground clearance. There is also a notion that in the sportbike position, you’re forcing too much weight on your wrists. I discovered quickly that if I put my ass down,the weight on my wrists was not a problem. The force is substantial, however, when braking with a passenger on board. Ultimately, after riding two Buells, I decided that this motorcycle deserved a shot at aSturgis trek. It had class, felt sporty, even nasty, and I could makeit rumble. So I stood back and thought, “Can I make it even cooler?”It didn’t take long to discover that I could strip it down evenfurther than stock. I picked the Cyclone over the model with hard bags because of its bare bones feel. The crew here at Bikernet.com developed a five-pronged approach. One, we wanted toenhance the Harley-Davidson marriage with Buell and downplay thelittle-known name Buell for the time being. We also wanted to enhance the Sportstermotor and bring out the looks of the Harley-Davidson power plant, andchop it in a Buell way without altering the geometry of theframe, the front end length or lowering it, which is a tradition withour custom bikes. There’s more. We wanted the bike to sound more likea Harley and we wanted to enhance the performance without disturbingthe long-range reliability.
Our team included myself, Professor NuttBoy, consulting fromPaul Davis of Charlotte, Gene Tomasen Jr. from the Harley-Davidson fleet center, and a number of Bikernet readers who knew about and were testing Buells. This is the first of several techs on the modifications and the experiences we have with the M-2. We collected and ordered parts, then ran to the fleet center to get thejob done. The initial plan was to unleash the natural performance ofthe bike without breaking down the engine. We started by removing thecarburetor.
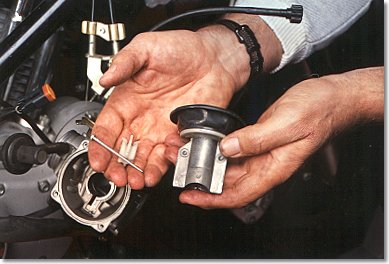
We replaced the needle in the slide with an ’88 Sportsterneedle, and drilled out the carb body above the idle adjustplug.
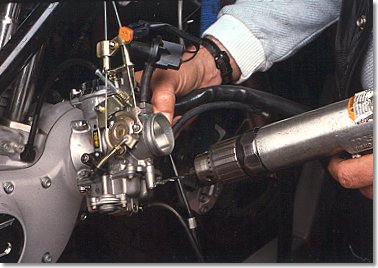
That allowed us to knock out the plug and back outthe idle adjuster 2.5 turns.
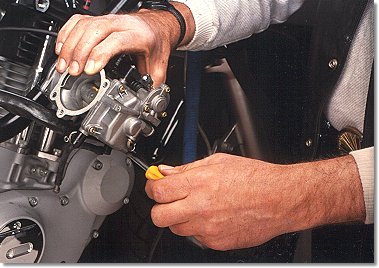
Stock carburetors are adjusted from thefactory to a very lean condition. Usually they are so lean that warmup takes a long time and you get an occasional cough through thecarb.
Others have recommended drilling directly through theplug, but Gene warned that if you slip, you will drillinto the adjuster screw and possibly damage it. Gene also recommendedhead work ultimately coupled with a 44 mm CV carb, manifold androller rockers in the future. I had a Screamin’ Eagle air box for a BigTwin, which I modified for the carb with an open K&N filter. We alsodropped the float bowel and replaced the 42 pilot jet with a 48. Becareful not to strip the screws holding the float bowel in place.Treat them with respect or they’ll cause you nightmares.
We set the carburetor aside and began to remove the timingcover to replace the cams. It’s important to take a scribe to thetiming plate so that you can duplicate the timing once you havereplaced the cams. Then pull the plate and the rotor cup, which isscrewed into the No. 2 cam. Before you go any further, remove the rockerboxes and the rocker arms to unload the tension on the non-adjustablepushrods. Now you can remove the cam cover, but don’t forget todrain the oil first.
At this point we decided to add a racy feature to theappearance of the bike by shaving the cam cover plate. First removethe oil line. Unplug the timing plate wire, dismantle the connectorand pull it through the plate.
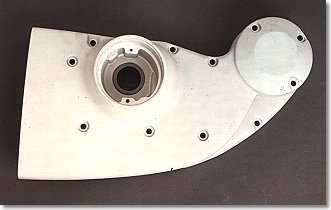
Gene used a Sawzall and a grinder toremove the aluminum underneath the bolt holes.
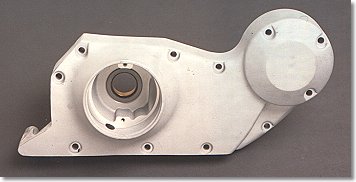
You will note that there is a series of seemingly endless webbing in this area which is for noisereduction.
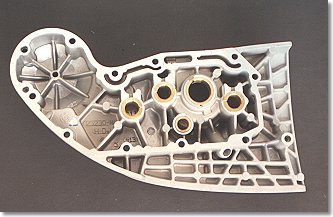
Notice that in the lower left hand corner, there is a dowelpin. Gene chose to leave it in place as a wiring guide and carve thecover around it.
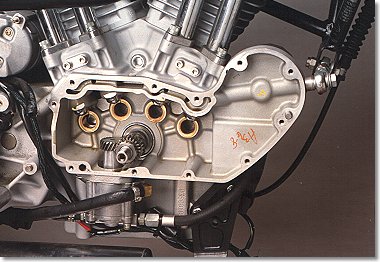
The pushrods are color coded: pink or red forexhaust and brown for intake. The cams are numbered like you readfrom left to right, or back to front, 1 to 4. Make sure you pull theplugs for ease in turning the motor over. Install No. 4 first with redline assembly lube; No. 3 has two index marks. Slip No. 1 in next andNo. 2 last. It has three index marks to line up the cam with the pistonposition and the other cams with an index mark that aligns with aslot on the pinion gear.
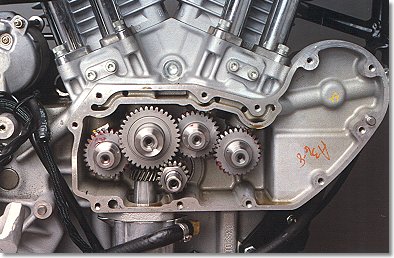
This is where we noticed that the pitch onthe Screamin’ Eagle race cams was different than the new pinionshaft gears. An emergency run to Bartels H-D was in order for partNo. 24055-91, or No. 24061-91. The factory changed to a new pitch in ’99.When replacing the cam cover, keep in mind that there are fourdifferent length Allens holding it in place. Make sure you have theright length in the right hole. The torque setting for the cam coverAllens is 17 foot pounds. After the cover went back on, it was timeto reinstall the rotor cap and the timing plate.
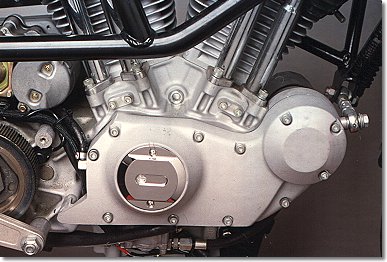
These modifications will help it run better. Buells usually run hot from the factory because of hotter cams and ThunderstromHeads. At this point we re-ran the wiring to the regulator behindthe oil pump for a cleaner appearance. We only had to extend onewire, to the oil pressure switch. Gene Jr. handled it with solder andshrink tubing. Removal of the gastanks is a breeze and access to the heads and top end is easy. But ifyou need to remove the engine, the fact that it is an integral partof the frame and suspension creates unruly problems. The entirechassis must be supported.
At this point we replaced the pushrods from the top of theengine and replaced the stock rockerbox covers with chrome units.Don’t use anything on the self-sealing gaskets except a dab of greasehere and there to hold them in place.
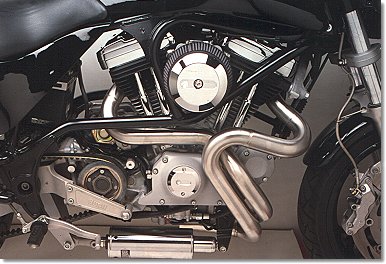
With the engine assembled, we replaced the stock exhaustwith a Buell race header kit and module. While Gene Jr. was out oftown, I spoke to the Buell tech of the demo fleet, Alan Varsi, who hasworked at Bartels Harley-Davidson for more than 11 years. The Buell racemodule retards the timing 5 degrees and eliminates the rev limiter.The stainless steel header is 11 inches longer than stock, which makeseach exhaust runner equal in length. The muffler is an aluminumcanister type that is high flow with low resistance for additionalperformance at the high end.
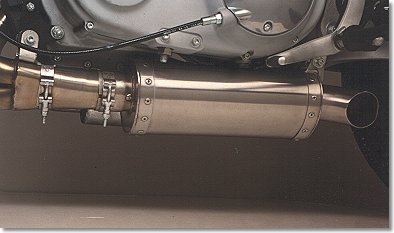
That’s it. Laughlin is right around the corner, along with our firstlong ride on the Harley-Davidson Street Fighter. We’re lookingforward to every desolate mile. We’ll report upon ourreturn. A new paint job is in the wings, along with some cosmetic modsto brighten the look of this bad-ass bike.
Sturgis 2000 – Part 4-2
By Robin Technologies |
![]() The Harley shop in Green River didn’t have it, nor did any of the other bike shops in the valley, but there was a shop in Aspen. It wasn’t in the phone book and couldn’t be reached by directory assistance. I called the Harley shop back and was given the number for Aspen Custom Motorcycles. I dialed and there was only an answering machine. Tired and dejected, we rambled back toward town. During one of our last installation attempts, we broke off the stud that held the rear tab in place. Now we needed an auto parts store for a large hose clamp and some rubber insulation to prevent the clamp from tearing through the durable powder coating finish. We pulled up in front of a Napa auto parts store and parked beside a blue and silver pickup with Krylon letters across the back window, “Aspen Custom Motorcycles.” Inside, a thin man with dark hair and youthful features leaned over the counter wearing a black Aspen Custom Motorcycles T-shirt. I introduced myself and he asked us to follow him. Two blocks away, this guy had his shop set up in a single storage unit stall (970) 544-9419. His undercover shop was complete with three stage creme sealer and we bought his only kit, thanked him and hauled ass for the Swank Hotel. In front of our room was an outdoor corridor leading to the bar and outdoor pool. I picked up several towels, borrowed a large bucket and we went to work. The first stage was a mixture of water and a strong detergent that was supposed to soak in the tank for four hours. We didn’t have the time and let it set for an hour. In the meantime, the guys in Randy’s room where having trouble with the plumbing. After I flushed the toxic mixture into a bucket, I poured it down the toilet in Randy’s room. I knew I should have stopped, but I was beyond the point of no return. I returned to the bike for stage two – flushing the tank with a strong solvent. Again the remnants of the explosive liquid were drained into the toilet. Meanwhile, hotel maintenance men and managers descended on Randy’s room, where a couple of riders had set up their joint rolling station. Plungers, tools and snakes were moved from room to room. Four rooms were effected and they were going to have to snake down from the roof. Randy shook his head. “Won’t work,” he said and poured the final stage of thick milky fluid into the tank. This process included sloshing the creamy liquid around the tank for 10 minutes, letting it set for 20, then sloshing again before draining. Randy sloshed and coated the lining of the tank for what seemed to be hours, making sure every crevice received its fair share. By this time evening was upon us. The tank was supposed to dry for 24 hours. I didn’t have time and Randy suggested that we use a hair dryer to speed up the drying process. The instructions specifically warned against the use of hair dryers because the final process was extremely flammable. Randy continued draining the thickening substance back into the bottle it came from, as we pondered the question. At one point, we tried putting the tank in front of the air conditioner to augment the flow, but there had to be a better way. Finally someone hit up the maintenance crew for a shop vac. As the sun sank, we started sucking the fumes from the tank outside our room.
![]() At one point, two girls showed up, one 22 and the other 27. They wanted to smoke a joint and party some, but the fumes held them at bay. Both were wearing shorts and tank tops and carrying shopping bags. One included a couple pairs of spiked heels that they quickly unwrapped and promised to sport for us. One had on a top buttoned up the front over no bra, and her tits were pressed so hard against the mint green fabric that the heavenly mounds creased the material. When she leaned over to slip on the shoes, we gasped in unison. Whatever it is that makes a woman’s body magic to a man, is a wonderful thing unless abused by either party. If a woman minds that a man gawks at the flesh exposed by too little clothing, she should cover herself. These girls didn’t mind. In fact, they enjoyed it and wanted more. We could have given in to them except we had a mission and a deadline. After the girls asked some probing questions and we didn’t respond appropriately, they rolled themselves a doobie and departed. There was another problem with nubile girls finding their evil ways into our lives. We were staying with 100 of our closest, most gossipy friends in the same goddamn hotel. Speaking of gossip, I hadn’t heard from Zebra for two days. He was supposed to hook up with a pack of riders in Tennessee, and perhaps they roasted him instead of a pig. I didn’t know his whereabouts, but I kept calling his cell phone hoping to hear the number had been permanently disconnected. At 6 a.m. Friday, the phone rang. Larry the mobile mud slide maker was leaving his room to meet me in the parking lot to lend me gas. I was hoping to sleep in, but noooo. I wrestled my ass out of bed and out to the bike with the tank. After setting it on the bike, it was difficult to tell that it had been through hell the previous day. I mounted it, hooked up the lines and went back to bed. I told Larry never to call me at 6 a.m. again and to keep his gas. I wanted to let it air for a couple more hours. At 9 a.m. we put gas in it for the first time from Howard’s truck, just a quart. We loaded up and hit the first station. We were Denver bound. Some of the guys were heading into the pass above, but rumor was that the straight shot was down to Green River, over to the 70 Freeway and into Denver. It was 30 miles out of the way, but we chose the straightest shot. The freeway is only two lanes wide but it meanders along railroad tracks and rivers toward Vail. We stopped for gas in Eagle and were passed by 30 Hamsters blasting onto the freeway. How they beat us I will never know, but I sent my navigator his walking papers the next day. We caught the furry beasts outside Vail. Traffic began to bunch up and we kept riding faster, splitting lanes and running the gauntlet between the very fast cars and extremely slow trucks. Treachery was all around us as we crested a pass and could see the dots of a pack of bikes in the distance. The tank was holding and the bike hadn’t burped, coughed or sputtered. It could handle anything I dished out. I turned the throttle and it responded. About 25 miles outside Denver we blew past the guys in yellow and another couple miles down the road it began to rain, then hail. We ducked off the freeway, pulled on our slickers and found a log cabin watering hole.
![]()
|
Road King 1/7/04
By Robin Technologies |
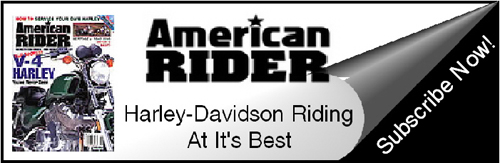
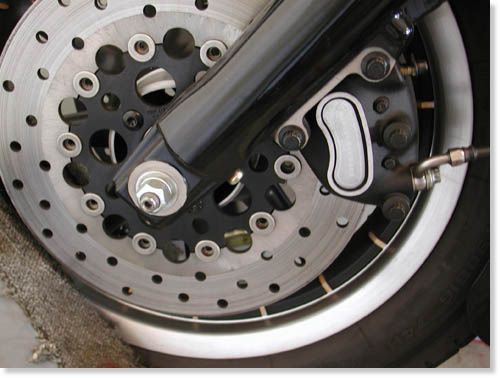
I had a bad feeling about this mod. First, I don’t like to pack anyone, any time. If you want a ride on my Panhead, carry a hand-towel and a bungie cord. I avoid giving a girl a ride home from the bar, even a babe with gigantic hooters. I would preferred to follow her home. I’m not the kind of rider to take a woman on a long run. I would rather have a variety of women in various towns and cities. Okay, I’m a bastard.
Okay, so the pressure’s on. Sin Wu want’s to ride once in a while, and I want to get laid daily. Gotta give up something. I kept the stock Road King classic seat for additional passenger comfort. It’s covered with dust, in the corner, but that quick change aspect is covered. I ordered the custom billet tab for the rear of the stock seat, and had it powder coated black, so both seats were ride-ready. When you purchase a new saddle, it doesn’t always come with the rear tab. The base is plastic and screwing fasteners in and out will wear out the threads.
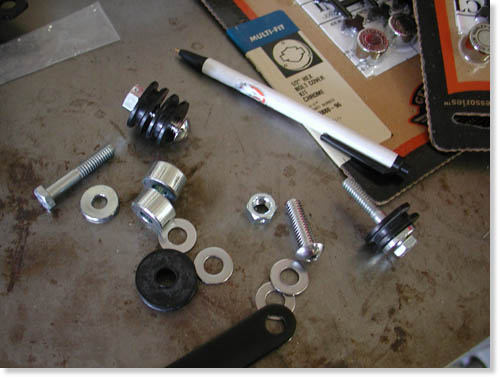
Here’s a handful of the fasteners and bag bracket spacers.
I ordered the front and rear detachable docking hardware kits, but be careful. I leaned toward the new lower backrest/sissybar for styling, which wasn’t in stock, but the pad was. I bought it, then the backrest was back-ordered so we bought the taller sissybar for immediate gratification, but when we got home the pad didn’t fit and we were forced to buy the tall pad. Watch out for this dilemma when ordering. Make sure to check all the installation instructions to make sure you have the correct puzzle pieces. There are several back rest options so watch that aspect when ordering.
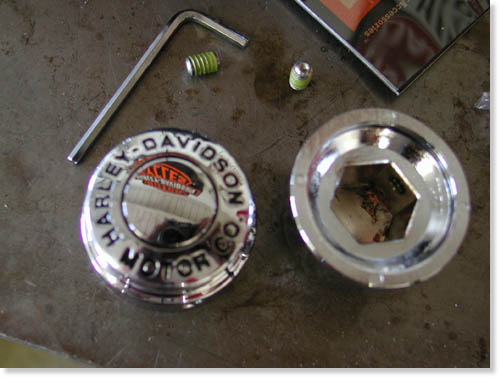
Here’s the massive chromed Classic H-D axle dress hardware.
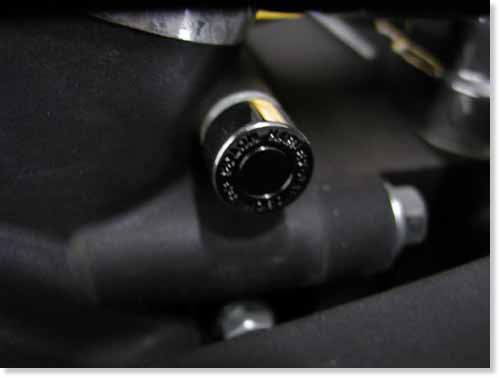
This is simple installation. Slip on the plastic wedge and the cap grips over it. Push them into place–done deal.
We also ordered some classic hex bolt covers and stainless Allen caps to begin an engine detailing process. We purchased chrome caps to detail the front brake calipers and classic chromed front axle covers. We didn’t use the plastic chrome caps ultimately but brush painted the raised edge of the calipers black. I’ll tell you why in a bit.
This was supposed to be one of the easiest mods we undertook, but we learned quickly, that wasn’t the case.
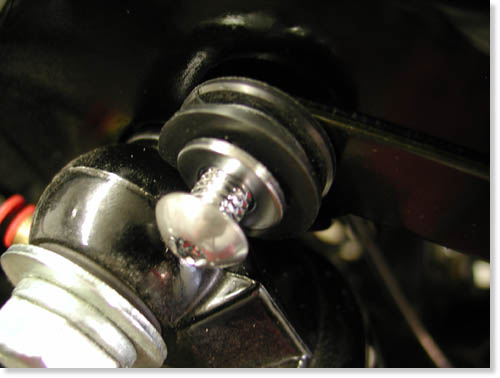
This is the front docking port in place, but not tightened.
When we black powdered a ton of components previously, we assembled the bike securely with Loctite and care. That was our undoing. The Phillips-head beside the shock needed to be replaced with the front docking hardware. Take one bolt out and replace it–no problem, right? The Phillips screws wouldn’t budge and we proceeded to strip the heads. First, I wished I had an impact driver.
I discovered an aerosol spray by Chemsearch called Yield in the auto parts store that loosens rusted bolts instantly. It worked like a charm, with a little patience the bolts came lose. An American Rider reader complained that this product isn’t available in retail stores. That’s true. My longshoreman connection hooked me up. You may need to find a factory worker or mechanic who has a connection.
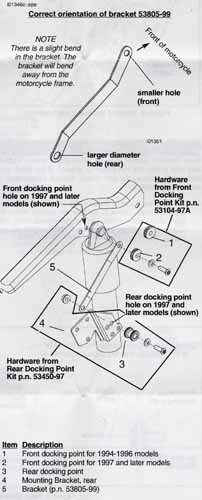
After reading the Low Detachable Backrest kit info that came with the taller kit, the Backrest Docking Hardware kit directions, the Front Docking Point kit instructions and the 100th Anniversary FLHT and FLHR Backrest Pad kit directions, I guzzled my first Corona.
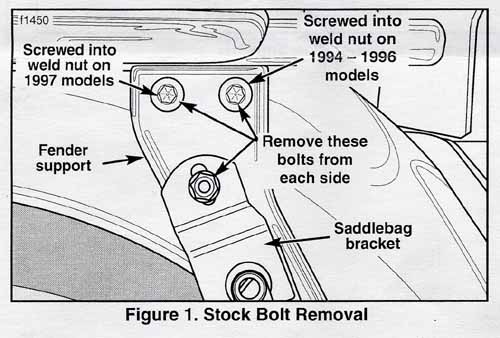
I opened the next Corona. The operation would have been simple if the directions were. I read them over and over. There were too many variations between years and configurations to sort through. The Front Docking port directions confused me with illustrations involving rear bag support spacers designed to bounce out the saddlebags and clear the release button on the backrest.
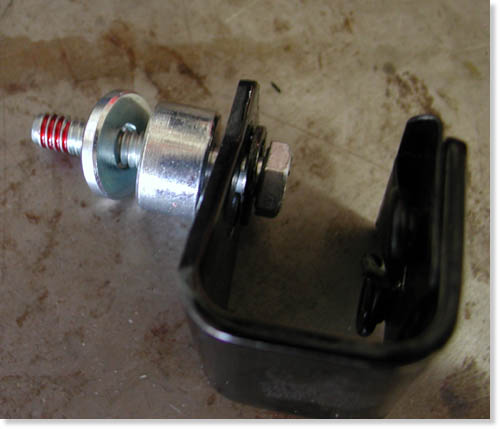
This was a matter of trial and error.
If you’ve built choppers as long as I have, there’s always a way to make anything work, so ignoring the confusion, we spanked our asses in gear. I ignored the spacers, installed the front docking rubber that was designed specifically for the King with a notch for the shock.
There’s a bracket that runs from the front docking station to the rear, but first the rear docking port bracket needed to be installed. On some models equipped with air shocks the shock filler bracket must be removed. The directions said I didn’t need to remove it on the 2003, bullshit. It was directly in the path of the docking bracket, so off it came.
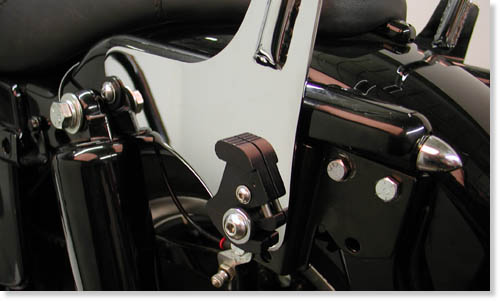
This shot shows the bracket in place, with the shock air port moved. Note the single empty hole in the bottom of the bracket. That’s where the rear bag mount bolts into place. The trick of the night.
Three lousy bolts had to be removed, the rear bag bracket 1/4-20 fastener and the two 5/16s fender support bolts. First the 1/4-20 spun the thin, tin clamp that holds the nut in place. Then the 5/16, once removed, could hardly be replaced. Nothing aligned properly. My lovely assistant had to squat and lift the tip of the fender, and in one case we were forced to remove the lower bag rail to align the top bolts.
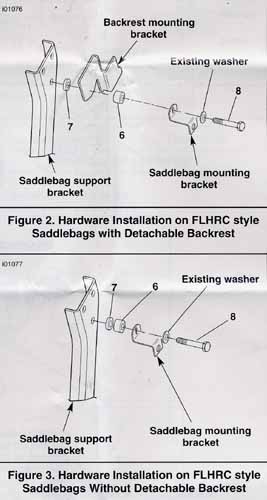
This still doesn’t totally jive. Actually washers had to be fed behind the top Backrest mounting bracket also.
“Can I let go of the fender, now?” Sin Wu asked grunting. The top docking port bolts are packaged in two sizes, 1 inch and 3/4 inch. The directions warn that if the rear inch-bolt comes too close to the fender, replace it with the 3/4. We replaced both and used the 1-inch jobs in the front holes on both sides.
Without the rear fender rack detachable bracket, another option, two washers were thrust under the rear docking port bracket to make up for the thickness of the rack bracket.
Part of the confusion was the numerous detachable elements available for various models. There’s also the two-up detachable rack front docking kit that surfaced from time to time.
That’s all there was to it. We bolted all the elements in place and tested the back rest and bags. Sure enough the King Classic bag lid smacked into the backrest latch when opening. We ultimately spaced the rear back bracket out only about an 1/8 of an inch and we were good to go.
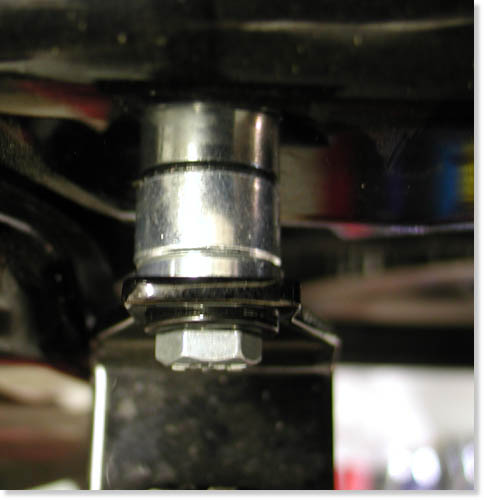
We tried it with the spacers, without, then with smaller spacers that worked perfectly.
Sin fed me chips and salsa and dabbed my sweating forehead with a bandanna, while I slipped the saddlebag bracket, 1/4-20 nut, into place using a long magnet. It worked on the right side. On the left we unbolted the entire fender support, replace the nut, adjusted the thin, tin tabs, and bolted the sucker all back together, only to have the nut fall out again. In this case we squeezed a slim square 1/4-20 nut behind the docking bracket and bolted the back bag bracket on with a spacer. It worked like a charm.
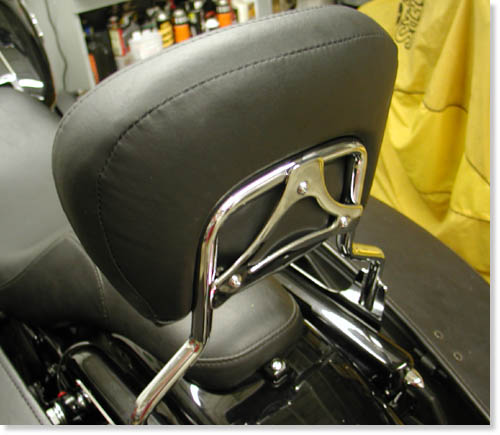
“Can we ride?” Sin cooed. I told her to gear up. We were just about ready to roll.
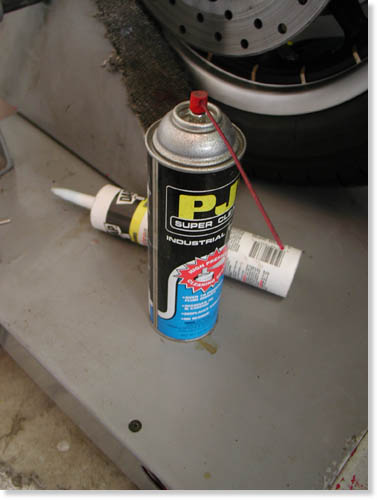
I used electrical contact cleaner to loosen the tin insignia plate, but discovered that wasn’t the intended plan. Leave it be, goddamnit.
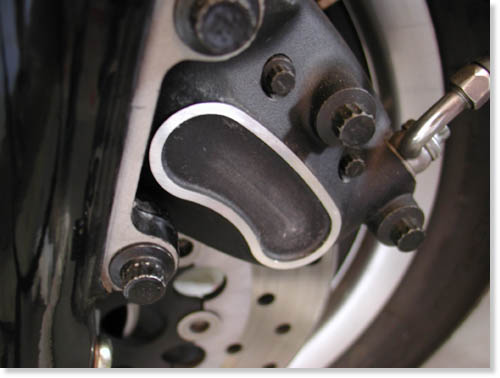
Here’s the totally clean caliper. Big mistake.
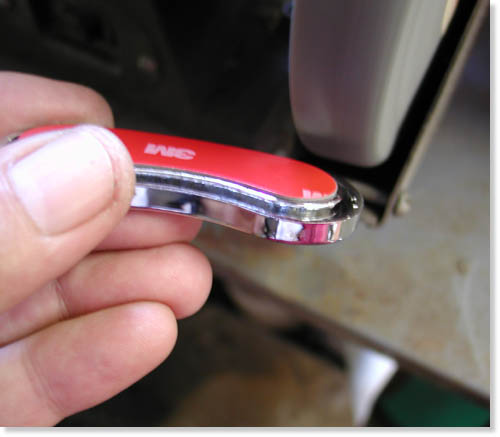
I ground the lip unevenly, but it then fit into the recessed slot on the caliper.
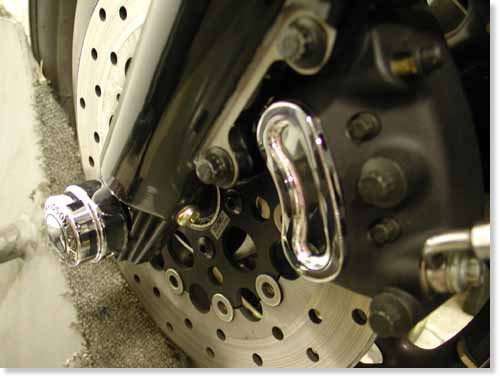
After grinding, all was well. Sorta.
The air in the garage eased as I warmed to her company. For an easy half-hour we played with the details of the bike by installing nut caps and front axle caps which I snugged down against a coating of silicon to prevent vibration.
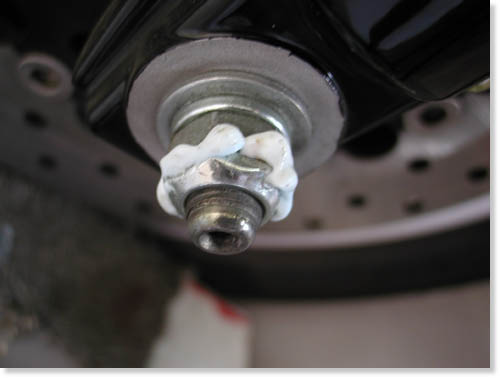
Some silicone on the axle nut will prevent vibration that may loosen the cap.
I discovered that the front chrome caliper caps stuck directly against the existing tin insignia. I took one off and cleaned the area thoroughly with electrical cleaner then the self-sticking surface didn’t reach the base.
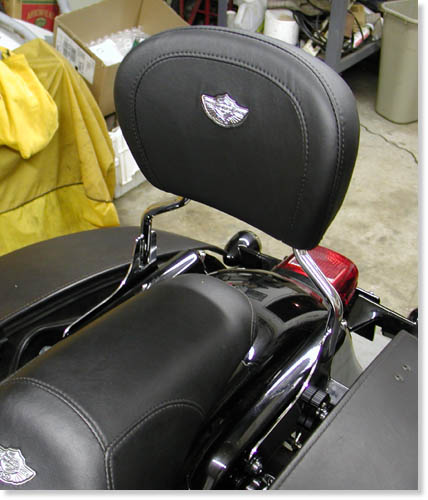
Here’s the 100th Anniversary backrest that will not fit on the short back rest bracket. We sent the short unit to Custom Powder Coating, in Dallas, for a coating of black.
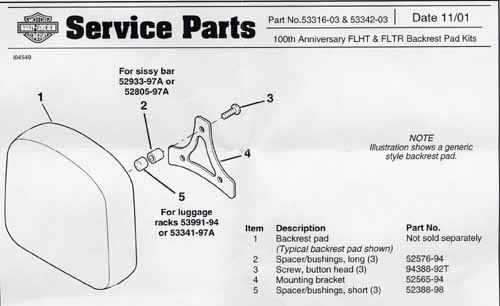
Note that there are various pads and various fasteners and spacers for different applications. Don’t try using common sense.
I ended up with 1/2 pint can of Rust-oleum paint and a small brush for touch-up details. I sent Sin Wu in the house to prepare for the ride. That meant striping out of her threads and waiting for me in bed. It’s the code. We must workout before we ride.
–Bandit
Editor’s note: I’m sniveling through this, but I’m sure with some experience this would have been a breeze. I suppose that’s what dealerships are for.
Road King 4/18/03
By Robin Technologies |

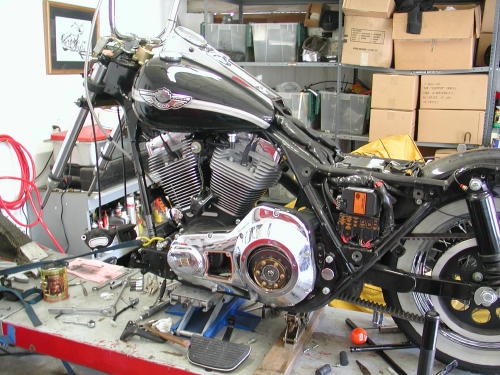
The King stripped for powder coating.
The plan was to strip the bike of all the brackets, tabs and accessories we could get our hands on and have them black powder coated by Custom Powder Coating in Dallas a Bikernet Sponsor.
We ordered additional accessories to enhance the clean black effect. First we ordered the Harley-Davidson black mag wheels and floating rotors with black centers. We pondered the front fender and trying to black out all the trim. During research we discovered, in the Winter P&A catalog, brackets to allow a Fatboy fender to be bolted in the King front end. The Fatboy fender is a cleaner unit, but it still has rivets and ribs. We opted for a solid black Street Stalker fender that’s clean as a whistle and light as a feather.
We also decided to switch the rear turnsignals out for the new Screamin’ Eagle teardrops and the narrower light bar. When they arrived we had to tear the lights down. We cut the two plug wires in a staggered fashion. The light bulb was then removed and we used a coat hanger tool to hook the plastic base and pull it out of the shell. Lastly we ordered the Harley-Davidson fender, license plate mount.
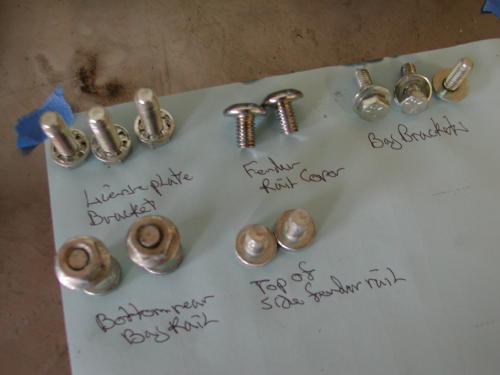
The first thing we did was to clear off our bench and tape down a couple of large sheets of paper. We organized every nut and bolt, screw and spring.
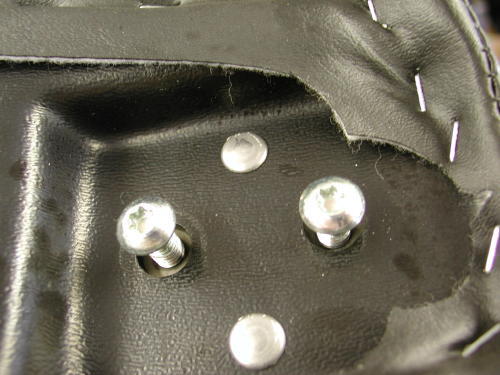
I ordered the billet seat tab from the catalog in the Multi-fit area. When I ordered a slim seat it didn’t come with a tab so I had to move the tab each time I switched seats. I powder coated both for more simple assembly in the future.
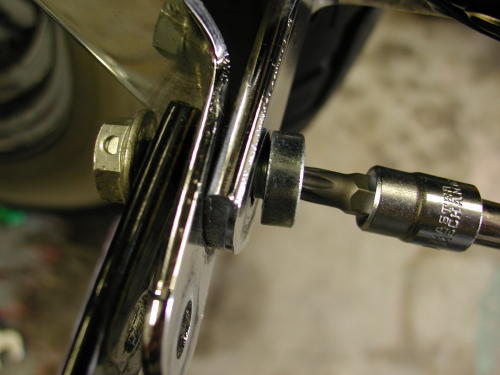
Nuttboy and I started the process removing the bags. I began the process of removing all the bag brackets and roll bars. Each time we removed a fastener we set it on the sheet of paper and wrote a description.
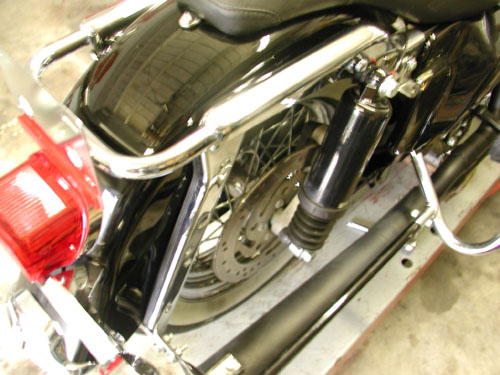

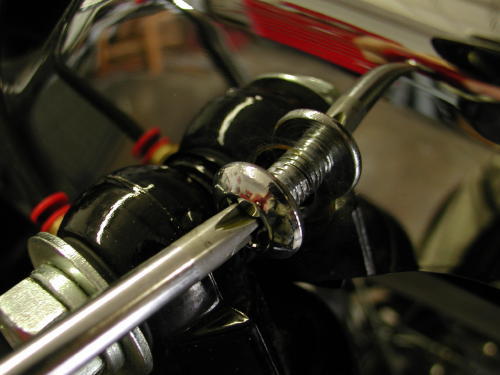
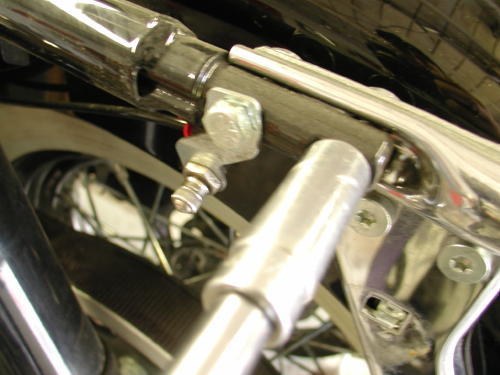
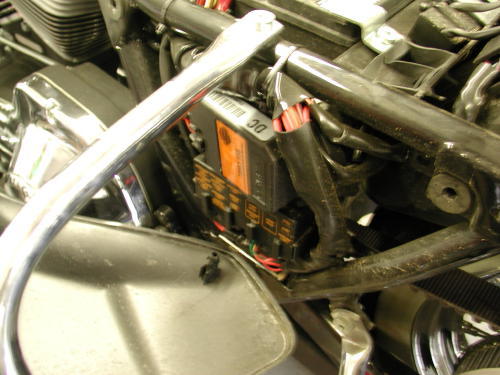
We had to pop the plastic side panel loose and take the seat off to get at the roll bar fasteners.
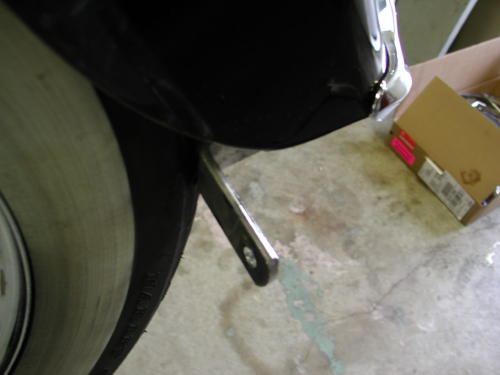
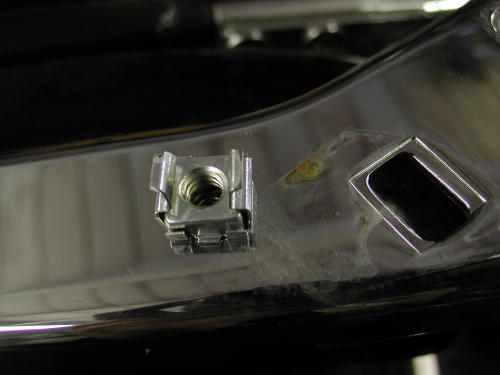
This shows one of the bag bracket fasteners that are inserted into the bag rails. I thought about pulling them for fear that the heat from the powder coating process would weaken the spring tension. We tested the theory by leaving some in place. We didn’t have a problem, either way.
On the left side I had to remove the passenger footboard to take the derby cover off. With each note on the sheet of paper we listed the number of fasteners for each application. The more information the better. I had to remove the seat and the King side panels to take the bag roll bars off. Many of these items were held on with Torx bolts. It’s a good notion to buy a set.
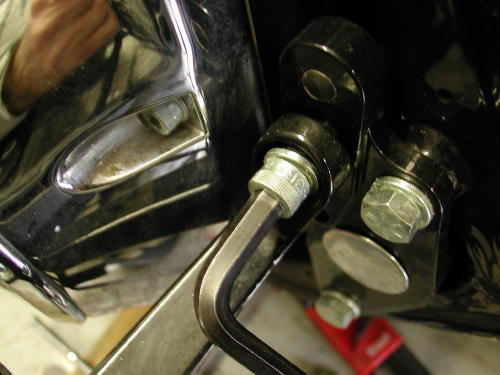
This footboard had to go to reach the derby fastener.
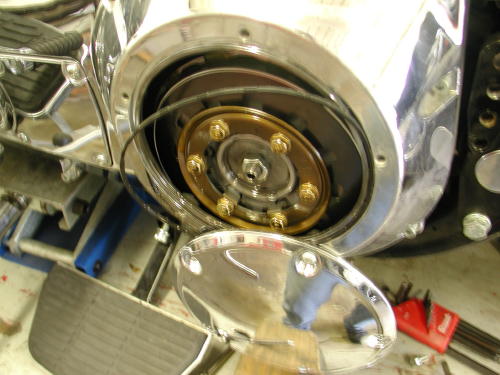
I started to remove the shift levers and discovered that I had to remove the footboard to reach the inspection cover Torx fasteners. I wasn’t sure if the footboards would have black in their future. At first I reviewed the area of the black board that would show, just the rim. Then we turned the board over and studied the way the rubber suspended pads were installed. We discovered that the pads are removed easily with a punch to the edges of the bottom protruding rubber lips. The boards went into the box for powder.
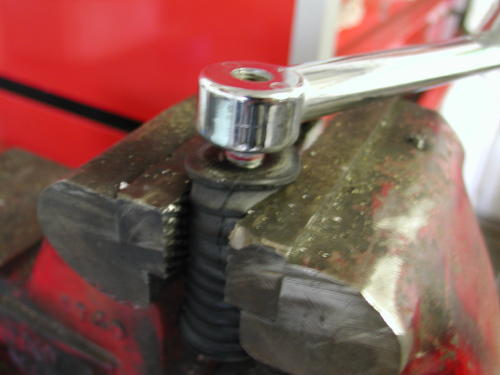
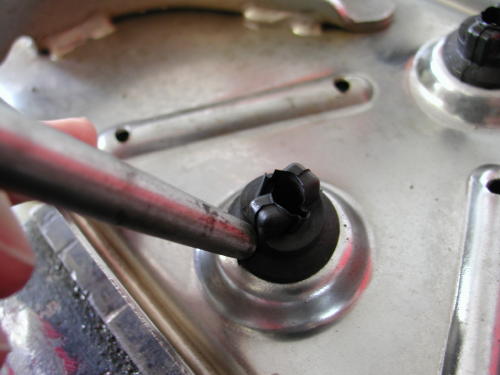
This was a simple process to tapping the edges of the rubber with a large tap and rubber hammer. We tried driving them out with the tap first, through the center. That didn’t work.
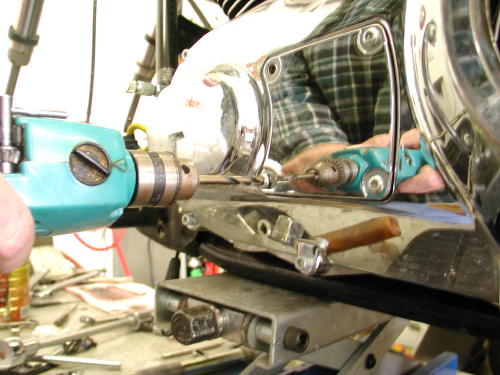
The mechanic’s law calls for one screw or fastener to seize every time. We had to drill out one of the inspection cover screws.
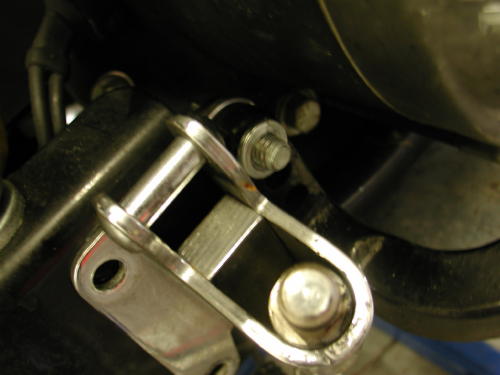
I tried to take off the kickstand the old fashioned way by removing the tooth then pivoting the arm forward. The spring wouldn’t come loose. I had to remove all the fasteners.
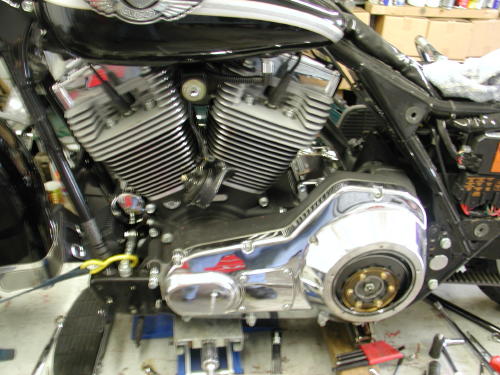
Metric fasteners haunted me from time to time, including the red Loctite touched horn fasteners which were #10 metric sockets. The Showa front end was covered with metric 12 point fasteners. It forced us to hit a commercial tool shop for 12-point metric sockets.
As the last of the fender rail parts came off we marked the loop that carried the license plate. We planned to replace the license plate holder with a fender-mounted job that attached below the taillight. We cut off the existing license plate loop, then I brazed washers and nuts so we could screw small orange reflectors in place.
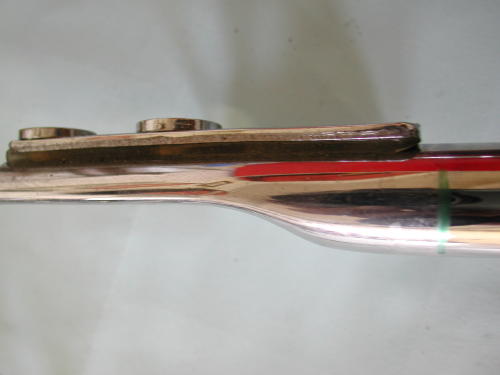
We marked the old license plate rail with a felt pen so the cut would fall just under the fender rail cover.
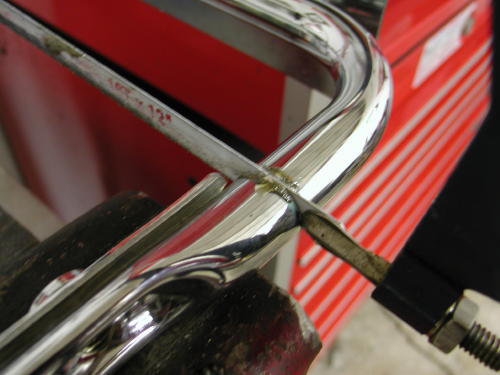

We didn’t use these reflectors. We were looking for Harley orange reflectors with steel backs.
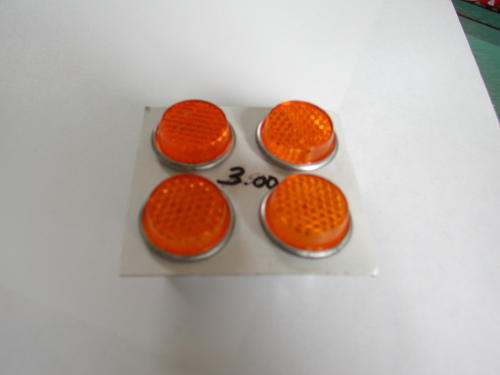
After a swapmeet run we had the right stuff for the job.
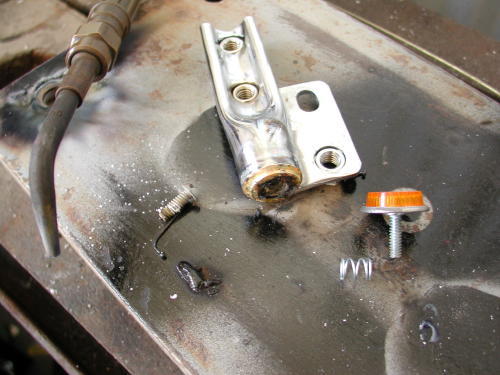
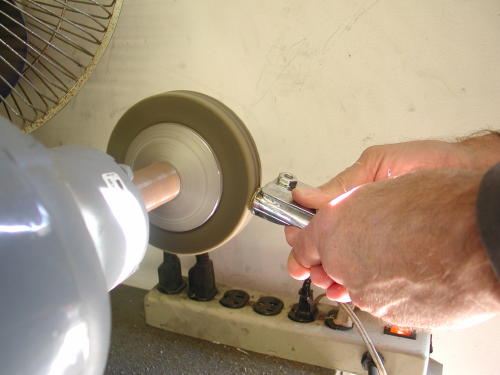
Sin Wu wandered into the garage just as I turned off the torch. She shuts down productive activity wherever she goes. She had a couple of alloy knitting needles that she offered us. I discovered in short order that the long alloy knitting needle worked perfectly for removing the hard-to-reach cotter key behind the brake pedal.
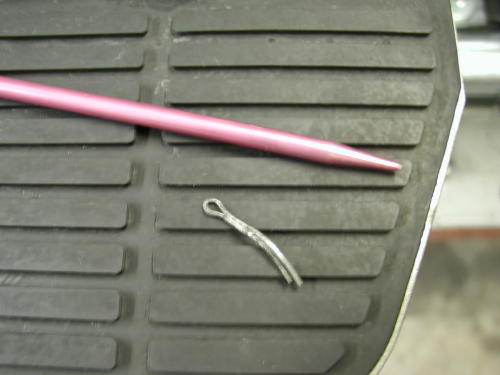
I had the toughest time retracting the clevis pin from of the pedal that hinged on the master cylinder piston. Finally it was removed with a punch from under the frame. The brake pedal caused me so much pain it didn’t make it into the powdercoating box. We painted it with a rattle can after prepping.

Continued On Page 2
The Amazing Shrunken FXR Part 5
By Robin Technologies |
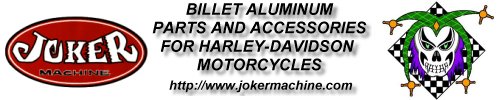
You’ve been there. You handed the Makita cordless drill toyou’re drunken buddy, and he drilled a hole in your big screentelevision. You tried to wrap the extension cord around his neck andfinish him off. We came close to blows in the garage a couple ofmonths back. I spent days carefully welding chunks of Samson exhaustpipes together to form a one-of-a-kind exhaust system.
All the welds were performed with gas and hanger rod. Thepipes weren’t perfect, but they fit the bill. They were actuallyintended to be prototypes, to be duplicated by a paid professional.After the first pass was completed the pipes fit like a glove,although they were artistically rough around the edges. Nuttboy cameby on his Wednesday afternoon escape, and I handed him a highspeedgrinder and instructed him to round off the welds. I worked onanother project and paid no attention while sparks flew. When he wasfinished he tapped me on the shoulder and said humbly, “Not sure thisis what you had in mind.”
He had ground right through the pipes and left gapingholes alongside most of the welds. In addition, I discovered to myteeth-grinding dismay, that there were still large sections of thepipe ground so thin, that as soon as the torch tip came within 6inches of the surface the pipe melted away. I spent another whole dayfilling the gaps. Who knows what will happen when the struggling bikefires to life. We’ll have the only exhaust system on earth withbaffles throughout.
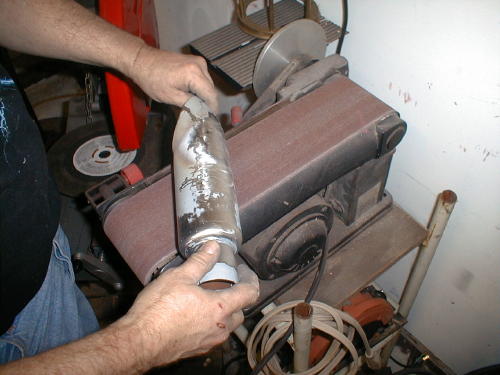
That’s not all. The grief continued. I hand made a mufflerusing a portion of a Samson baffle. We purchased a chromed, truckfender tip from San Pedro Muffler and went to work, but after hoursof screwing with the shiny metal we almost shitcanned the unit. Thefender tip was made out of a strange metal, almost pot metal, thatdidn’t seem to take to the gas welding and wouldn’t respond tobrazing. For every hole I filled, another crack lurked. I welded,then smoothed on a bench grinder only to find cracks and holes tofill again. The shorty muffler probably weighs 50 pounds due to thevast layers of welding rod. As it stands, this is a pure prototypeexhaust system. We should use it for testing then shitcan the rankpiece of shit and start over.
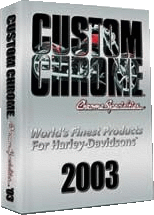
Click to order Catalog!
Frustrated, but pleased with the overall look we were readyfor final metal work. This bike is being built by inexperiencedhands, not professionals, in our backyard garage. Sure, I’ve builtsome bikes, but I wouldn’t consider myself a metal fabricator. I cameup with the initial design and we roughed out elements, but we neededa master metal worker to finish what we started. There are preciousfew, true metal craftsman, who I know. One is Billy Westbrook,another is Jesse James and recently, in the news, we displayed metalwork by Roger at Goldammer (Goldammer Cycle Works Ltd.,www.goldammercycle.com ,1-250-764-8002). High quality workmanship.
They’re out there but not on every corner. I stumbledonto another super-slag artist under my nose. James and LarryFamighetti are Hamsters and own a corrugated steel metal shop inHarbor City, California, called Fam-Art. You’d be tweaked to rumbledown Narbonne Street and stumble across this rusting corner buildingthat’s got to be the oldest swaying dump on the block. Theyspecialize in structural steel (you could never tell it from theircreaking tin shed) for homes and buildings. Large chunks of steel,massive shredders, presses and welders are scattered around the funkylocation that’s reminiscent of the first shack Harleys were built in.
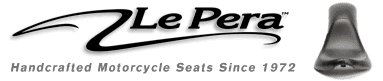
Nuttboy and I darkened their doors a couple of times toask them to flame-cut a couple of chunks of steel for our fenderbrackets. The more I hung around the more quiet-James began to showme steel components he had fashioned for some of the local riders. Herebuilt and reformed Harley taillights to eliminate all the edges andgrooves, then welded them to fenders so that ultimately there were noseams. The more I gawked at the sculptured parts, that demonstratedhis ability, the more I knew we had discovered a man capable of BillyWestbrook fabrication qualities. We hauled the entire FXR to Jamesthe next week.
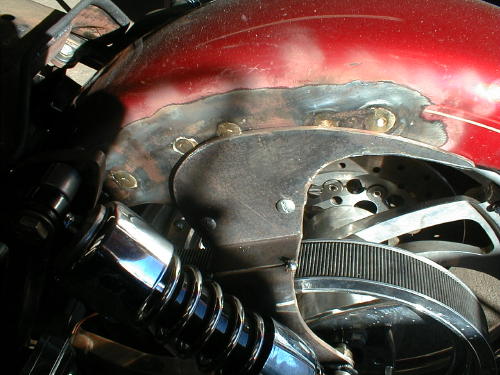
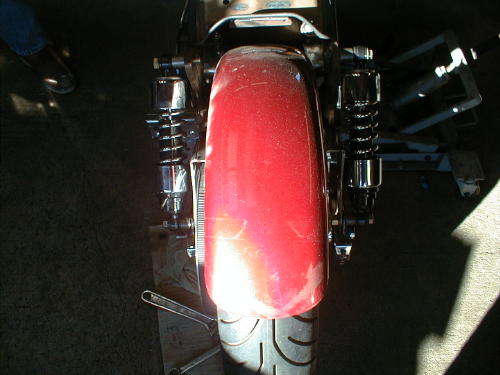
James relocated the straps in such a way to narrow the shockplacement keeping that shrunken look in mind.
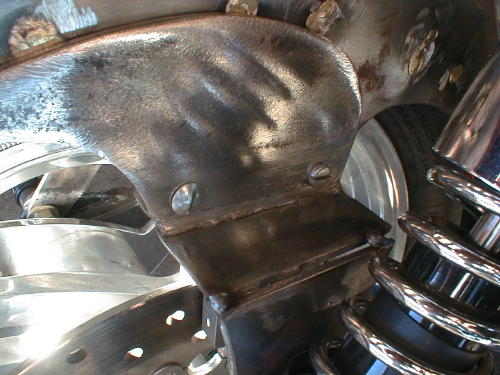
This is a close-up of the right fender strap. It’s beencorrected, reformed and readied for final welds.
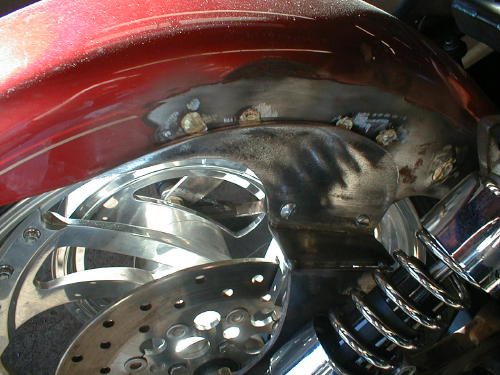

We cut and fitted the tank and made the mounts, butJames filled the underside, rear section for a perfect fit.
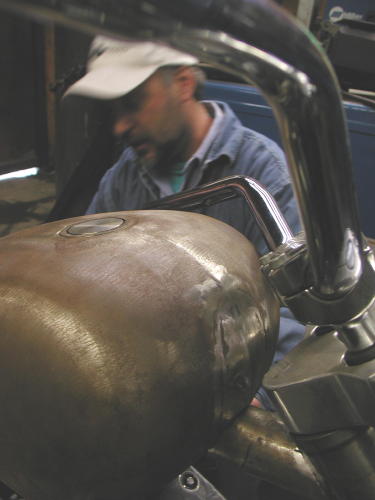
We jacked up the front of the tank and mounted it, butJames filled it and formed the front of the tank to match the customridge along the top. He even made paint work suggestions that I foundinteresting. “If you paint a ridge like this with a light color,”James said, “The ridge will disappear.”
We decided to paint the bike a light House of Kolors pearland create a dark teardrop panel on the top of the tank. He alsocreated and welded fork stops to the neck.
As we rolled out of the shop that day James still hadfinal welds to complete. He straightened out our seat pan, but neededto figure out a mounting arrangement. Finally we needed the CyrilHuze front fender brackets checked and welded into place.
We should have the Shrunken FXR back in our clutches inthe next couple of weeks. We need to finish our rear brake andshifting mechanisms with Giggie from Compu-Fire, fire it up for atest ride and tear it down for paint.
Oh, I need to untie Nuttboy. I need that extension cord.
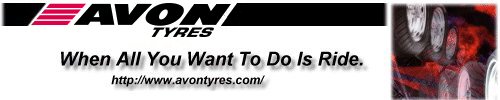
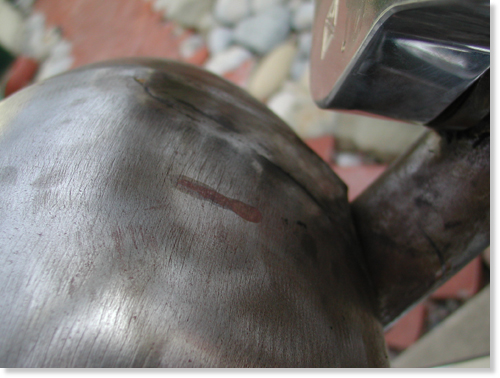
The Shrunken FXR returned recently from Fam Art, in HarborCity, California (310-326-2141). They welded, shaved, mounted theseat, manufactured fork stops and saved our poor- construction asses.James Famighetti mounted our Cyril Huze front fender, welded andformed the tabs and informed us that the Avon Venom was too large forthe narrow glide front end. It was our turn to work on it.
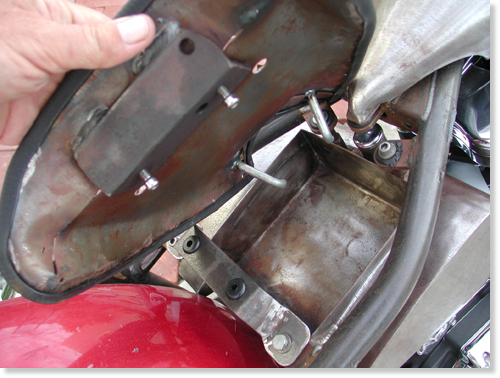
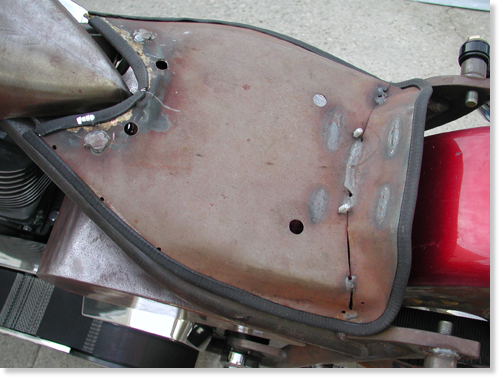
Note that James mounted the seat pan so that the edges wouldnot touch the frame paint in the future.
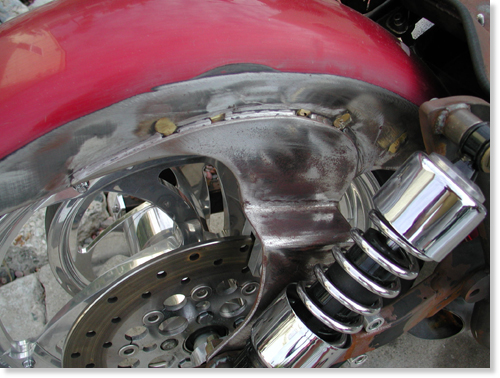
Like any self-respecting bikers we hate to have a bike, oreven components out of our mistrusting mitts. We had another dilemmathat needed handling. The bike still didn’t have a kick stand, and weused two 2 by 4’s, to hold it upright, when not perched on the lift.There’s a trick to this maneuver. If I backed the Pro Street FXR outof the garage and wasn’t hauling the wood planks, I was screwed. Ifalone, I could stand there for hours waiting for someone to strollpast carrying two 2 by 4s–unlikely. After a couple of unsteadyoccurrences, the bike didn’t move without the wood chips on the seat.You can imaging the major pain in the ass this caused.

We ordered a weld-on, Sportster style, kick stand fromCCI, and it arrived complete, with all chromed hardware and thebracket to be welded on the frame. There was one problem indetermining the position. The front Avon was a 100/100 18-inch, andwe planned to replace it with a 90/90. We needed to have the finishedPerformance Machine wheel in place.
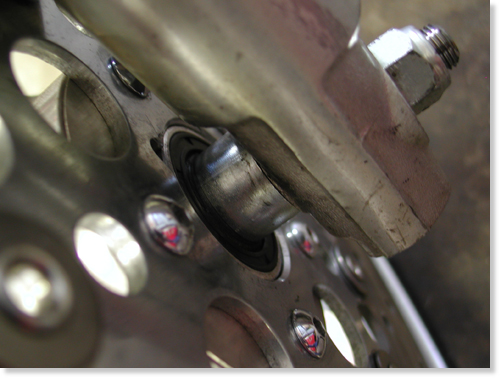
The Avon Road Runner tire arrived, and we had it installed at thelocal Yamaha dealer. James pointed out to us that our front tirespacing wasn’t perfect so I sliced a spacer to give us about a1/4-inch spacer on the right side of the wheel and about a 3/4 inchspacer on the left. The tire, almost centered, now had clearance, andthe wheel floated effortlessly under the modified Cyril Huze frontfender.
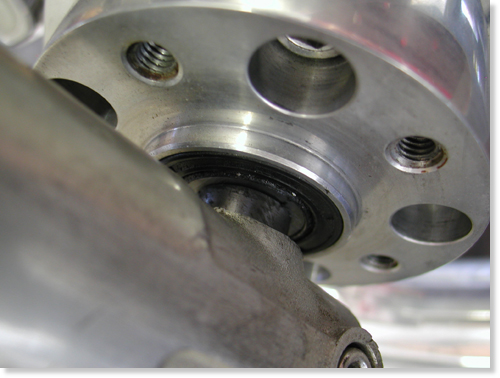
Now we were cleared to install the Hot Match weld-on kickstand.This is a tricky assembly process. First, you need to be absolutelysure you don’t plan to change the front wheel, to a 21, or extend thefront forks. If you do, the kickstand will need to be bent ormodified to fit. It’s not the end of the world, but it will destroythe chrome.
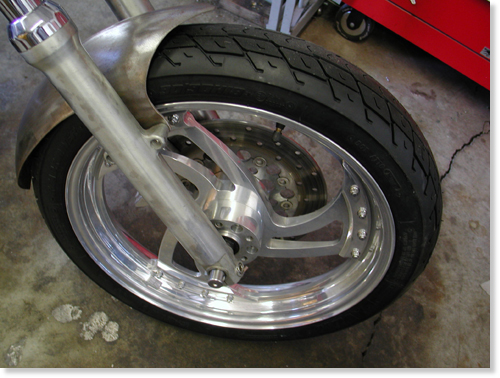
The other trick is determining the right position. Here’swhat my feeble brain told me, since the directions with the Hot Matchdidn’t cover positioning, except to recommend that you take yourtime–no shit. First I stood my Road King straight up and lifted theside stand until it was locked in place. Then I measured from thepoint that would touch the pavement to the ground. It varied fromaround 2.5 inches to 3 inches. I noted that the Hot Match lever wasnearly 3 inches shorter from the point of contact to the center ofthe pivot point. I took that into consideration. I also noted that Ihad lowered my King with shorter shocks, then added a larger Avontyre (a 150). Ground clearance was also a consideration.

Then we picked a placement area on the frame. Our designcalled for little or no forward controls. I kept the tab under theBDL belt drive system and hidden as much as possible, without beingso far back as to create a balance problem. If the weight is forwardof the kickstand, sometimes it can topple the bike. One otherconsideration. When the stand pops up you need to be able to reach itwith a toe, and it better not ride on the belt, or you’re toast. Makesure to check all that, before you burn any rod.
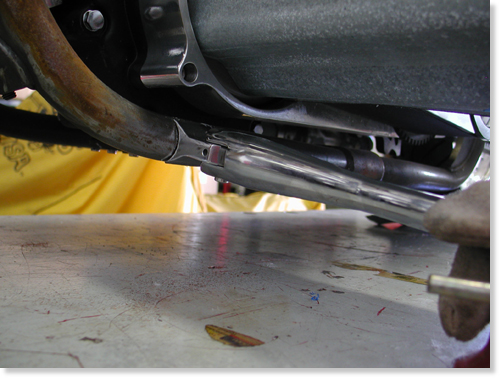
I sprayed the frame rail and the components with asilicone splatter preventative. It obstructs slag from sticking tocomponents. It also made the frame a slipper bitch. I tried settingthe stand end on a socket nearly 3 inches off the deck. Then Iconsidered the differing lengths of the stands and shifted to 2.5inches. Sin Wu was called, from the bedroom, to hold the stand firmlyin place. I marked it, with a grease pencil, then ground the edges ofthe bracket to be welded to the frame. Extra grinding took place toform a snug, metal to metal fit. In order to make all this work weneeded to partially assemble the kickstand without the ball andspring.
The easy-to-read directions called for disassembly, but we left ittogether and used it to hold the bracket in place for tacking. Beforetacking I backed the bike out of the clamp, holding it upright,positioned the bracket in the white grease pencil marks and leanedthe bike carefully until the stand rested on the flat surface. Itlooked cool, so we re-clamped the bike securely, held the stand inplace, protected the belt from hot slag and tacked the sucker withour Millermatic welder. Then we took the stand arm off the bracketand welded it some more. That would hold it securely until we torethe bike down for paint.
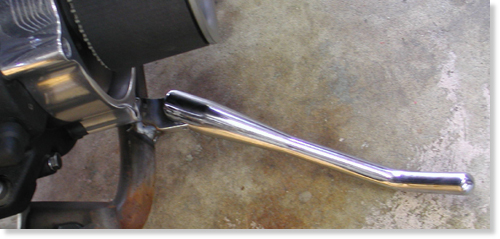
The Hot Match unit from Custom Chrome is a well madeprecision unit delivered show chromed. The instructions includedrecommendations to apply anti-seize to the spring and ball. Theyendorse using Red Loctite on the pivot pin threads. We didn’t becausethe bike would be torn down for paint in the near future. The armneeds to be placed firmly over the bracket and pushed into placebefore the pin will ease into the hole from the bottom. It doesn’thurt to have a spare set of hands and someone holding the bike.There’s also a pivot pin set screw to prevent losing that preciouspivot pin and kick stand arm, on a desert highway, in the middle ofArizona.

That’s it, except to mention that when we head to thepaint shop, we need to tape off the chrome bracket, so the painterwill paint over the welds but not the chrome tab.
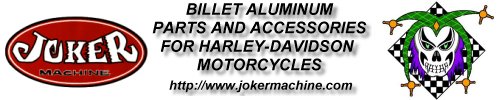
As you can see this bike is damn close to the spray booth.I need to coerce Giggie, from Compu-fire, to ride his FXR out to theBikernet Headquarters with our mid-controls. Once the Joker Machinehandlebar controls are bolted to the modified bars, we’re ready for atrial run, then off to paint. Stay tuned.
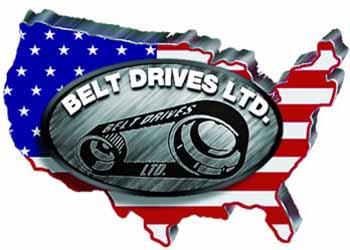
–Bandit
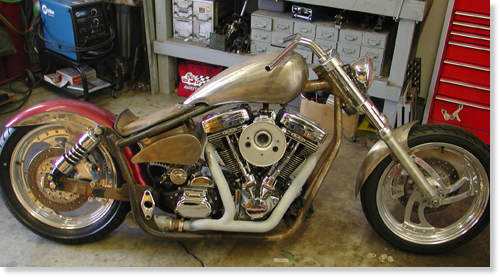
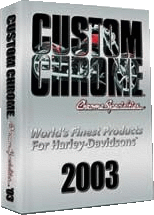
Custom Chrome ® and Chrome Specialties ® have joinedforces to bring you the most comprehensive product offering in theHarley-Davidson ® aftermarket! At over 1,400 pages and over 25,000part numbers, our 2003 Catalog features everything from nuts & boltsto HR3 bike kits, and sets the NEW industry standard.
ONLY $9.95 + 6.95 Shipping**
–Bandit
Back to Part 4…
Sturgis 2001 Part 2
By Robin Technologies |
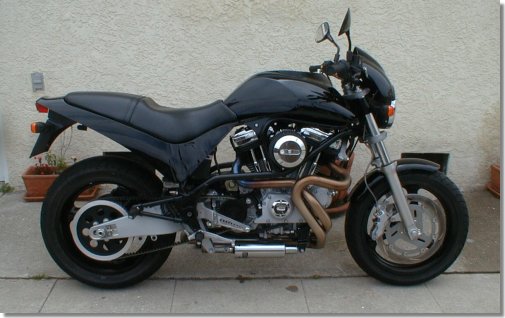
Here’s a couple of shots of the Bikernet Street FightingBuell for Sturgis 2001. This is how it currently stands with ahandfull of minor modifications and a lot of plastic removed. Let meknow what you think.
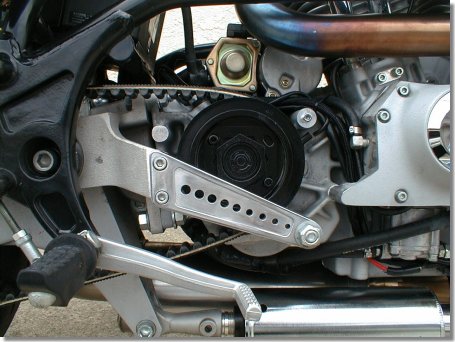
Note the pulley guard. We had the notion to take levers andbraces like this off, lightening-drill polish and replace. Not sureif that’s going to be the bit, now, but this brace was the test. Ithink we’ll powdercoat rather than polish.
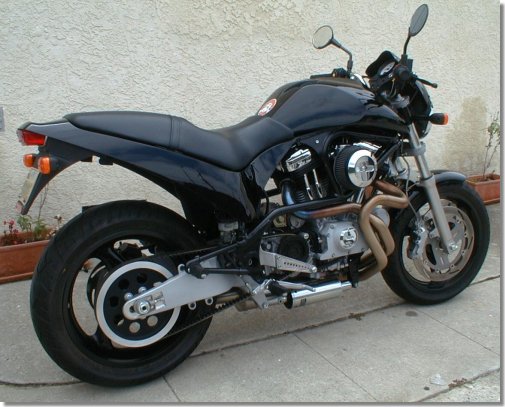
Trying to keep polishedaluminum up on a bike that’s well ridden is a pain in the ass. Haveyou seen a polished engine after a ride to Sturgis? We plan to removethe triple trees and swingarm. The tabs for the plastic dust shieldsneed to be removed and then the parts need to be polished to removethe ribs and casting marks before we decide on a finish.
Let us know what you think. I think I should black powercoatthe swingarm and maybe the trees and lower legs. We’re looking for apainter for the sheetmetal, and we’ll be ready to rock.
–Bandit