Sturgis 2000 – Part 4-2
By Robin Technologies |
![]() The Harley shop in Green River didn’t have it, nor did any of the other bike shops in the valley, but there was a shop in Aspen. It wasn’t in the phone book and couldn’t be reached by directory assistance. I called the Harley shop back and was given the number for Aspen Custom Motorcycles. I dialed and there was only an answering machine. Tired and dejected, we rambled back toward town. During one of our last installation attempts, we broke off the stud that held the rear tab in place. Now we needed an auto parts store for a large hose clamp and some rubber insulation to prevent the clamp from tearing through the durable powder coating finish. We pulled up in front of a Napa auto parts store and parked beside a blue and silver pickup with Krylon letters across the back window, “Aspen Custom Motorcycles.” Inside, a thin man with dark hair and youthful features leaned over the counter wearing a black Aspen Custom Motorcycles T-shirt. I introduced myself and he asked us to follow him. Two blocks away, this guy had his shop set up in a single storage unit stall (970) 544-9419. His undercover shop was complete with three stage creme sealer and we bought his only kit, thanked him and hauled ass for the Swank Hotel. In front of our room was an outdoor corridor leading to the bar and outdoor pool. I picked up several towels, borrowed a large bucket and we went to work. The first stage was a mixture of water and a strong detergent that was supposed to soak in the tank for four hours. We didn’t have the time and let it set for an hour. In the meantime, the guys in Randy’s room where having trouble with the plumbing. After I flushed the toxic mixture into a bucket, I poured it down the toilet in Randy’s room. I knew I should have stopped, but I was beyond the point of no return. I returned to the bike for stage two – flushing the tank with a strong solvent. Again the remnants of the explosive liquid were drained into the toilet. Meanwhile, hotel maintenance men and managers descended on Randy’s room, where a couple of riders had set up their joint rolling station. Plungers, tools and snakes were moved from room to room. Four rooms were effected and they were going to have to snake down from the roof. Randy shook his head. “Won’t work,” he said and poured the final stage of thick milky fluid into the tank. This process included sloshing the creamy liquid around the tank for 10 minutes, letting it set for 20, then sloshing again before draining. Randy sloshed and coated the lining of the tank for what seemed to be hours, making sure every crevice received its fair share. By this time evening was upon us. The tank was supposed to dry for 24 hours. I didn’t have time and Randy suggested that we use a hair dryer to speed up the drying process. The instructions specifically warned against the use of hair dryers because the final process was extremely flammable. Randy continued draining the thickening substance back into the bottle it came from, as we pondered the question. At one point, we tried putting the tank in front of the air conditioner to augment the flow, but there had to be a better way. Finally someone hit up the maintenance crew for a shop vac. As the sun sank, we started sucking the fumes from the tank outside our room.
![]() At one point, two girls showed up, one 22 and the other 27. They wanted to smoke a joint and party some, but the fumes held them at bay. Both were wearing shorts and tank tops and carrying shopping bags. One included a couple pairs of spiked heels that they quickly unwrapped and promised to sport for us. One had on a top buttoned up the front over no bra, and her tits were pressed so hard against the mint green fabric that the heavenly mounds creased the material. When she leaned over to slip on the shoes, we gasped in unison. Whatever it is that makes a woman’s body magic to a man, is a wonderful thing unless abused by either party. If a woman minds that a man gawks at the flesh exposed by too little clothing, she should cover herself. These girls didn’t mind. In fact, they enjoyed it and wanted more. We could have given in to them except we had a mission and a deadline. After the girls asked some probing questions and we didn’t respond appropriately, they rolled themselves a doobie and departed. There was another problem with nubile girls finding their evil ways into our lives. We were staying with 100 of our closest, most gossipy friends in the same goddamn hotel. Speaking of gossip, I hadn’t heard from Zebra for two days. He was supposed to hook up with a pack of riders in Tennessee, and perhaps they roasted him instead of a pig. I didn’t know his whereabouts, but I kept calling his cell phone hoping to hear the number had been permanently disconnected. At 6 a.m. Friday, the phone rang. Larry the mobile mud slide maker was leaving his room to meet me in the parking lot to lend me gas. I was hoping to sleep in, but noooo. I wrestled my ass out of bed and out to the bike with the tank. After setting it on the bike, it was difficult to tell that it had been through hell the previous day. I mounted it, hooked up the lines and went back to bed. I told Larry never to call me at 6 a.m. again and to keep his gas. I wanted to let it air for a couple more hours. At 9 a.m. we put gas in it for the first time from Howard’s truck, just a quart. We loaded up and hit the first station. We were Denver bound. Some of the guys were heading into the pass above, but rumor was that the straight shot was down to Green River, over to the 70 Freeway and into Denver. It was 30 miles out of the way, but we chose the straightest shot. The freeway is only two lanes wide but it meanders along railroad tracks and rivers toward Vail. We stopped for gas in Eagle and were passed by 30 Hamsters blasting onto the freeway. How they beat us I will never know, but I sent my navigator his walking papers the next day. We caught the furry beasts outside Vail. Traffic began to bunch up and we kept riding faster, splitting lanes and running the gauntlet between the very fast cars and extremely slow trucks. Treachery was all around us as we crested a pass and could see the dots of a pack of bikes in the distance. The tank was holding and the bike hadn’t burped, coughed or sputtered. It could handle anything I dished out. I turned the throttle and it responded. About 25 miles outside Denver we blew past the guys in yellow and another couple miles down the road it began to rain, then hail. We ducked off the freeway, pulled on our slickers and found a log cabin watering hole.
![]() |
Road King 1/7/04
By Robin Technologies |
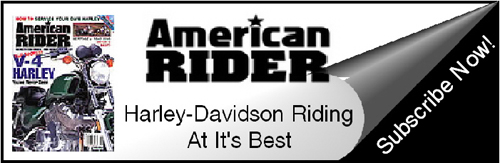
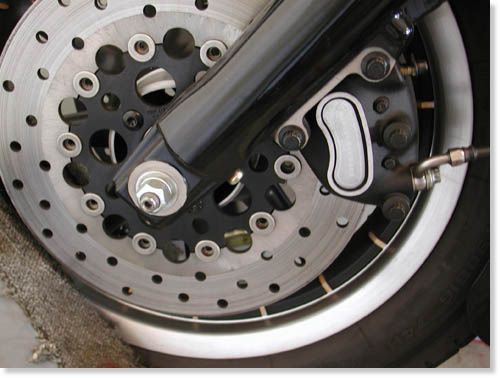
I had a bad feeling about this mod. First, I don’t like to pack anyone, any time. If you want a ride on my Panhead, carry a hand-towel and a bungie cord. I avoid giving a girl a ride home from the bar, even a babe with gigantic hooters. I would preferred to follow her home. I’m not the kind of rider to take a woman on a long run. I would rather have a variety of women in various towns and cities. Okay, I’m a bastard.
Okay, so the pressure’s on. Sin Wu want’s to ride once in a while, and I want to get laid daily. Gotta give up something. I kept the stock Road King classic seat for additional passenger comfort. It’s covered with dust, in the corner, but that quick change aspect is covered. I ordered the custom billet tab for the rear of the stock seat, and had it powder coated black, so both seats were ride-ready. When you purchase a new saddle, it doesn’t always come with the rear tab. The base is plastic and screwing fasteners in and out will wear out the threads.
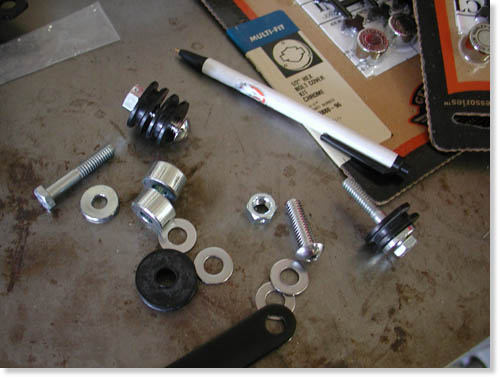
Here’s a handful of the fasteners and bag bracket spacers.
I ordered the front and rear detachable docking hardware kits, but be careful. I leaned toward the new lower backrest/sissybar for styling, which wasn’t in stock, but the pad was. I bought it, then the backrest was back-ordered so we bought the taller sissybar for immediate gratification, but when we got home the pad didn’t fit and we were forced to buy the tall pad. Watch out for this dilemma when ordering. Make sure to check all the installation instructions to make sure you have the correct puzzle pieces. There are several back rest options so watch that aspect when ordering.
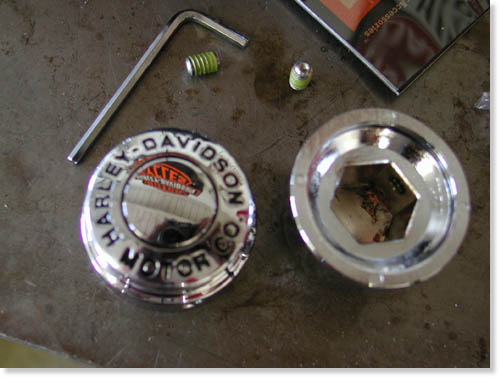
Here’s the massive chromed Classic H-D axle dress hardware.
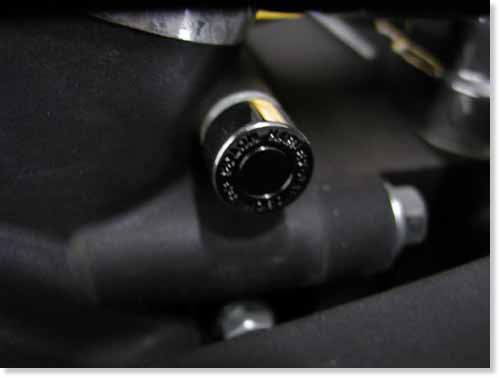
This is simple installation. Slip on the plastic wedge and the cap grips over it. Push them into place–done deal.
We also ordered some classic hex bolt covers and stainless Allen caps to begin an engine detailing process. We purchased chrome caps to detail the front brake calipers and classic chromed front axle covers. We didn’t use the plastic chrome caps ultimately but brush painted the raised edge of the calipers black. I’ll tell you why in a bit.
This was supposed to be one of the easiest mods we undertook, but we learned quickly, that wasn’t the case.
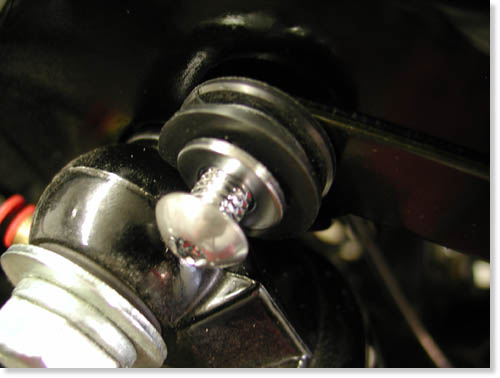
This is the front docking port in place, but not tightened.
When we black powdered a ton of components previously, we assembled the bike securely with Loctite and care. That was our undoing. The Phillips-head beside the shock needed to be replaced with the front docking hardware. Take one bolt out and replace it–no problem, right? The Phillips screws wouldn’t budge and we proceeded to strip the heads. First, I wished I had an impact driver.
I discovered an aerosol spray by Chemsearch called Yield in the auto parts store that loosens rusted bolts instantly. It worked like a charm, with a little patience the bolts came lose. An American Rider reader complained that this product isn’t available in retail stores. That’s true. My longshoreman connection hooked me up. You may need to find a factory worker or mechanic who has a connection.
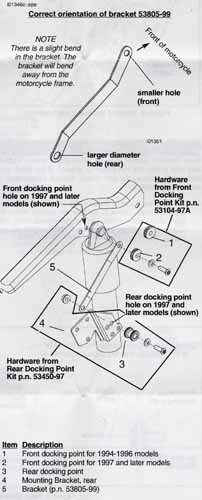
After reading the Low Detachable Backrest kit info that came with the taller kit, the Backrest Docking Hardware kit directions, the Front Docking Point kit instructions and the 100th Anniversary FLHT and FLHR Backrest Pad kit directions, I guzzled my first Corona.
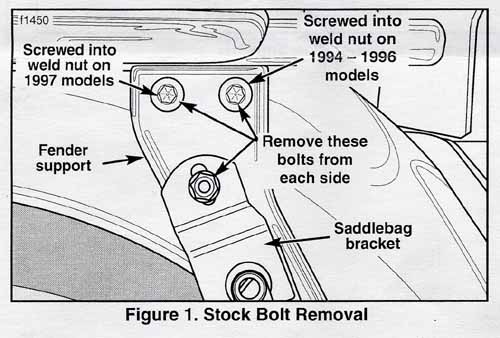
I opened the next Corona. The operation would have been simple if the directions were. I read them over and over. There were too many variations between years and configurations to sort through. The Front Docking port directions confused me with illustrations involving rear bag support spacers designed to bounce out the saddlebags and clear the release button on the backrest.
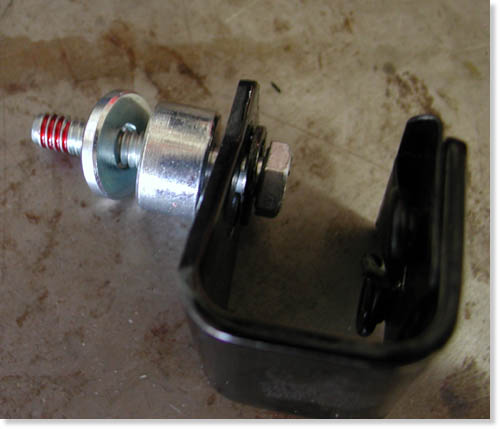
This was a matter of trial and error.
If you’ve built choppers as long as I have, there’s always a way to make anything work, so ignoring the confusion, we spanked our asses in gear. I ignored the spacers, installed the front docking rubber that was designed specifically for the King with a notch for the shock.
There’s a bracket that runs from the front docking station to the rear, but first the rear docking port bracket needed to be installed. On some models equipped with air shocks the shock filler bracket must be removed. The directions said I didn’t need to remove it on the 2003, bullshit. It was directly in the path of the docking bracket, so off it came.
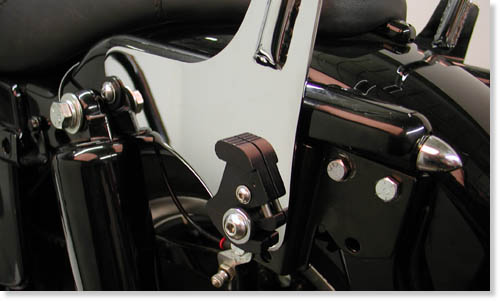
This shot shows the bracket in place, with the shock air port moved. Note the single empty hole in the bottom of the bracket. That’s where the rear bag mount bolts into place. The trick of the night.
Three lousy bolts had to be removed, the rear bag bracket 1/4-20 fastener and the two 5/16s fender support bolts. First the 1/4-20 spun the thin, tin clamp that holds the nut in place. Then the 5/16, once removed, could hardly be replaced. Nothing aligned properly. My lovely assistant had to squat and lift the tip of the fender, and in one case we were forced to remove the lower bag rail to align the top bolts.
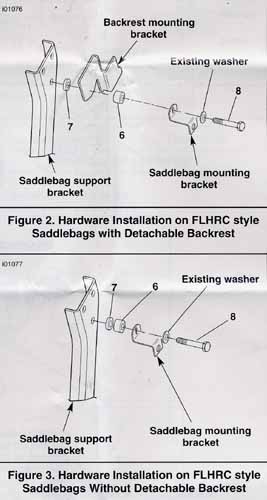
This still doesn’t totally jive. Actually washers had to be fed behind the top Backrest mounting bracket also.
“Can I let go of the fender, now?” Sin Wu asked grunting. The top docking port bolts are packaged in two sizes, 1 inch and 3/4 inch. The directions warn that if the rear inch-bolt comes too close to the fender, replace it with the 3/4. We replaced both and used the 1-inch jobs in the front holes on both sides.
Without the rear fender rack detachable bracket, another option, two washers were thrust under the rear docking port bracket to make up for the thickness of the rack bracket.
Part of the confusion was the numerous detachable elements available for various models. There’s also the two-up detachable rack front docking kit that surfaced from time to time.
That’s all there was to it. We bolted all the elements in place and tested the back rest and bags. Sure enough the King Classic bag lid smacked into the backrest latch when opening. We ultimately spaced the rear back bracket out only about an 1/8 of an inch and we were good to go.
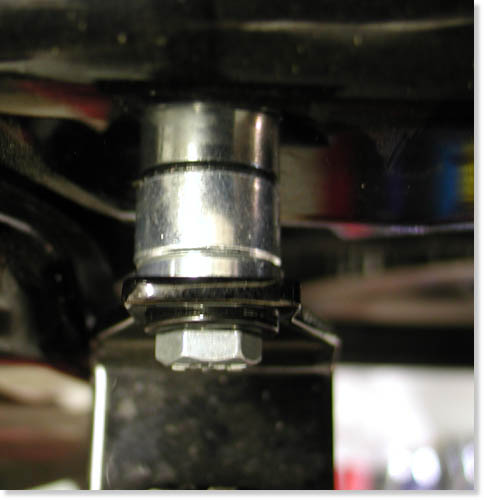
We tried it with the spacers, without, then with smaller spacers that worked perfectly.
Sin fed me chips and salsa and dabbed my sweating forehead with a bandanna, while I slipped the saddlebag bracket, 1/4-20 nut, into place using a long magnet. It worked on the right side. On the left we unbolted the entire fender support, replace the nut, adjusted the thin, tin tabs, and bolted the sucker all back together, only to have the nut fall out again. In this case we squeezed a slim square 1/4-20 nut behind the docking bracket and bolted the back bag bracket on with a spacer. It worked like a charm.
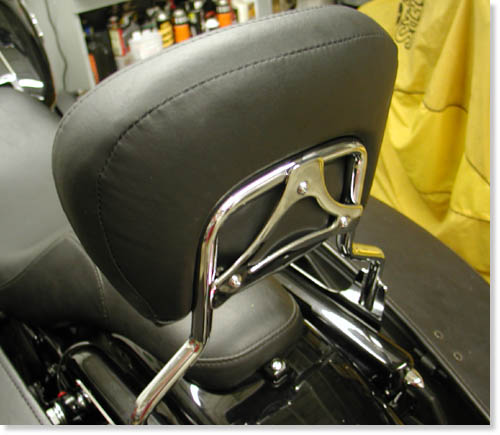
“Can we ride?” Sin cooed. I told her to gear up. We were just about ready to roll.
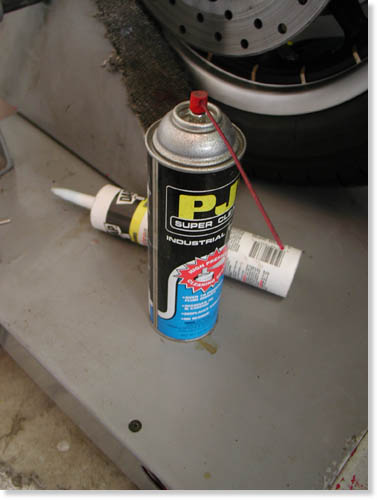
I used electrical contact cleaner to loosen the tin insignia plate, but discovered that wasn’t the intended plan. Leave it be, goddamnit.
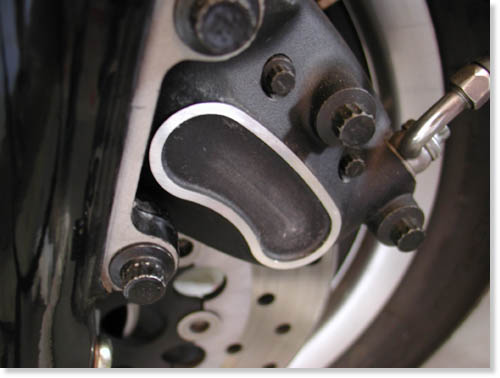
Here’s the totally clean caliper. Big mistake.
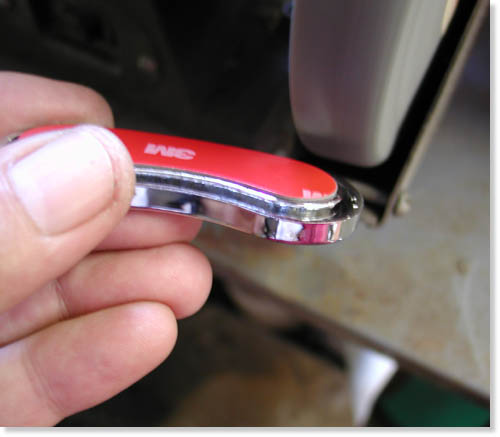
I ground the lip unevenly, but it then fit into the recessed slot on the caliper.
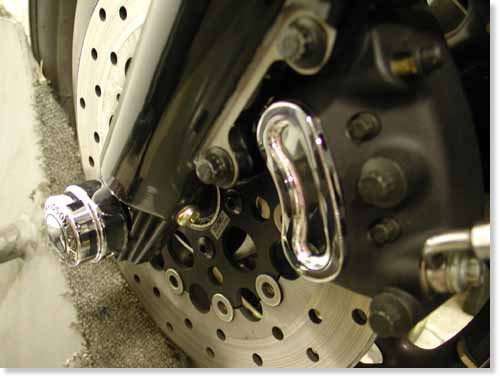
After grinding, all was well. Sorta.
The air in the garage eased as I warmed to her company. For an easy half-hour we played with the details of the bike by installing nut caps and front axle caps which I snugged down against a coating of silicon to prevent vibration.
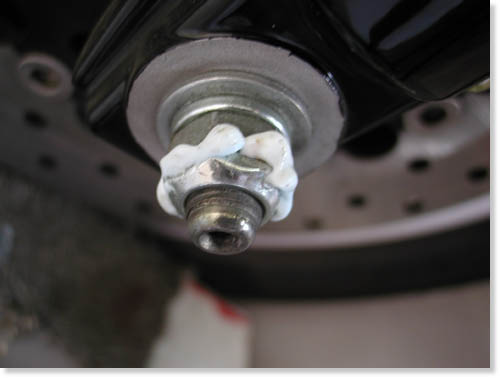
Some silicone on the axle nut will prevent vibration that may loosen the cap.
I discovered that the front chrome caliper caps stuck directly against the existing tin insignia. I took one off and cleaned the area thoroughly with electrical cleaner then the self-sticking surface didn’t reach the base.
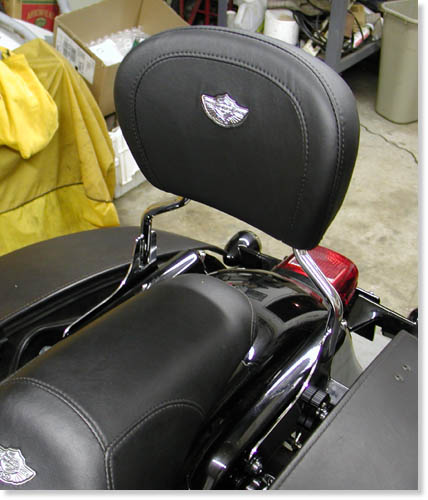
Here’s the 100th Anniversary backrest that will not fit on the short back rest bracket. We sent the short unit to Custom Powder Coating, in Dallas, for a coating of black.
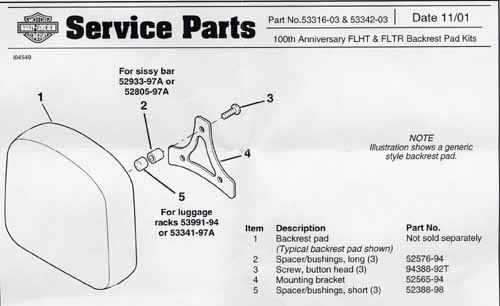
Note that there are various pads and various fasteners and spacers for different applications. Don’t try using common sense.
I ended up with 1/2 pint can of Rust-oleum paint and a small brush for touch-up details. I sent Sin Wu in the house to prepare for the ride. That meant striping out of her threads and waiting for me in bed. It’s the code. We must workout before we ride.
–Bandit
Editor’s note: I’m sniveling through this, but I’m sure with some experience this would have been a breeze. I suppose that’s what dealerships are for.
Road King 4/18/03
By Robin Technologies |

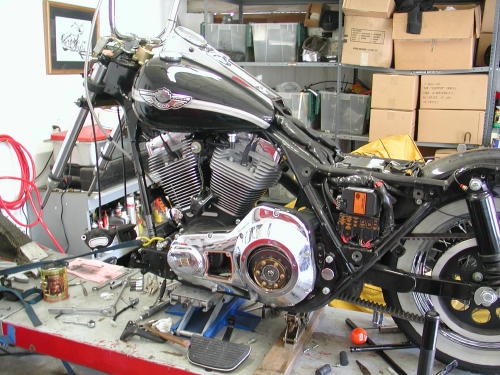
The King stripped for powder coating.
The plan was to strip the bike of all the brackets, tabs and accessories we could get our hands on and have them black powder coated by Custom Powder Coating in Dallas a Bikernet Sponsor.
We ordered additional accessories to enhance the clean black effect. First we ordered the Harley-Davidson black mag wheels and floating rotors with black centers. We pondered the front fender and trying to black out all the trim. During research we discovered, in the Winter P&A catalog, brackets to allow a Fatboy fender to be bolted in the King front end. The Fatboy fender is a cleaner unit, but it still has rivets and ribs. We opted for a solid black Street Stalker fender that’s clean as a whistle and light as a feather.
We also decided to switch the rear turnsignals out for the new Screamin’ Eagle teardrops and the narrower light bar. When they arrived we had to tear the lights down. We cut the two plug wires in a staggered fashion. The light bulb was then removed and we used a coat hanger tool to hook the plastic base and pull it out of the shell. Lastly we ordered the Harley-Davidson fender, license plate mount.
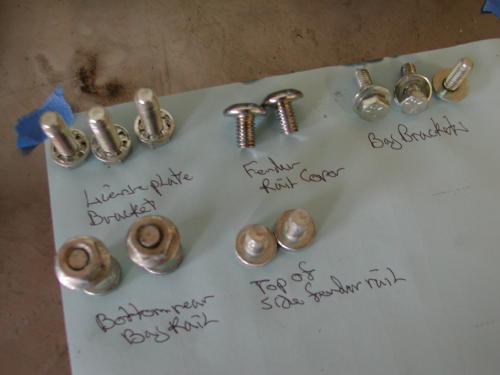
The first thing we did was to clear off our bench and tape down a couple of large sheets of paper. We organized every nut and bolt, screw and spring.
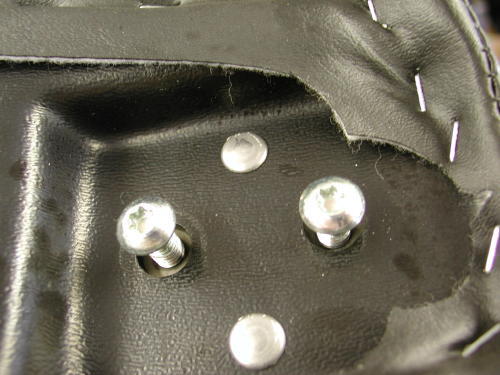
I ordered the billet seat tab from the catalog in the Multi-fit area. When I ordered a slim seat it didn’t come with a tab so I had to move the tab each time I switched seats. I powder coated both for more simple assembly in the future.
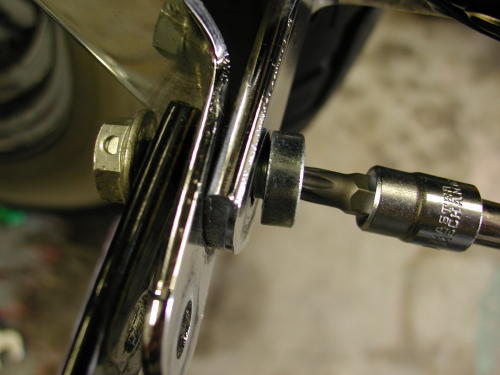
Nuttboy and I started the process removing the bags. I began the process of removing all the bag brackets and roll bars. Each time we removed a fastener we set it on the sheet of paper and wrote a description.
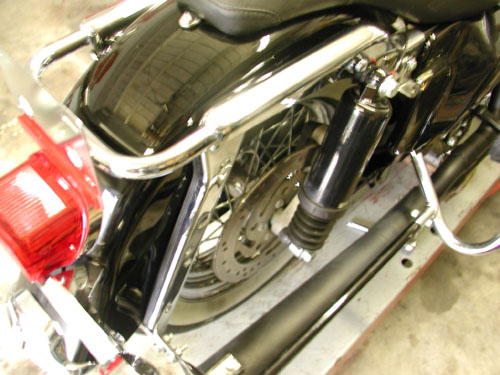

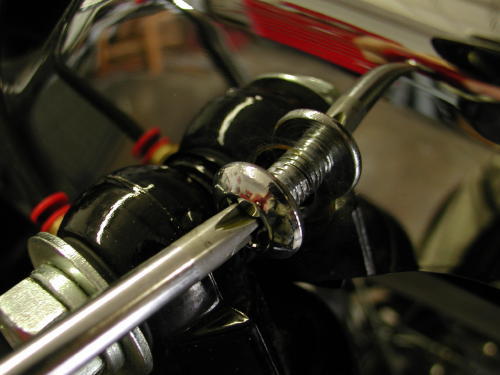
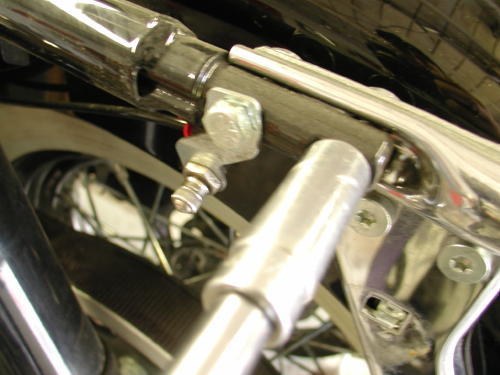
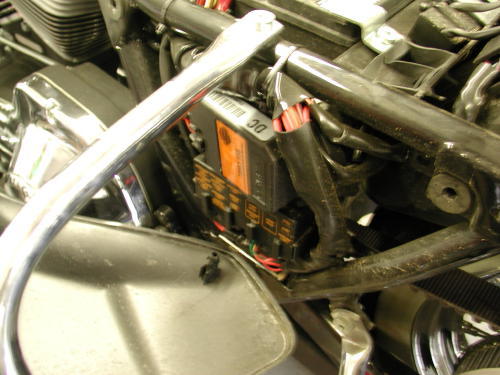
We had to pop the plastic side panel loose and take the seat off to get at the roll bar fasteners.
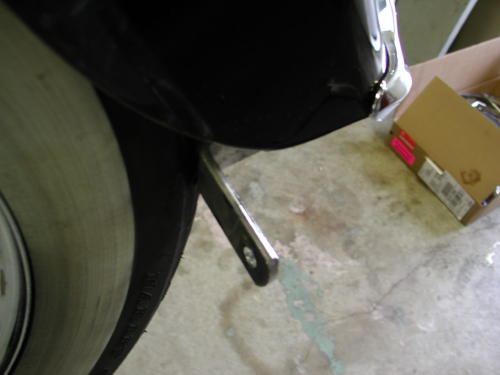
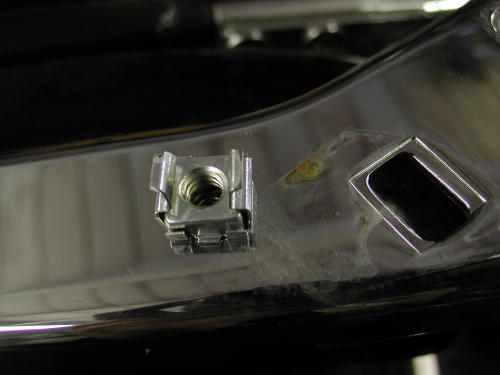
This shows one of the bag bracket fasteners that are inserted into the bag rails. I thought about pulling them for fear that the heat from the powder coating process would weaken the spring tension. We tested the theory by leaving some in place. We didn’t have a problem, either way.
On the left side I had to remove the passenger footboard to take the derby cover off. With each note on the sheet of paper we listed the number of fasteners for each application. The more information the better. I had to remove the seat and the King side panels to take the bag roll bars off. Many of these items were held on with Torx bolts. It’s a good notion to buy a set.
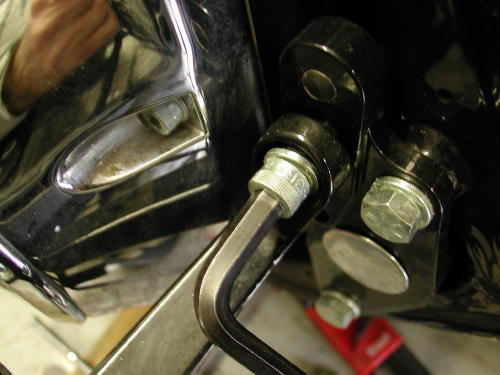
This footboard had to go to reach the derby fastener.
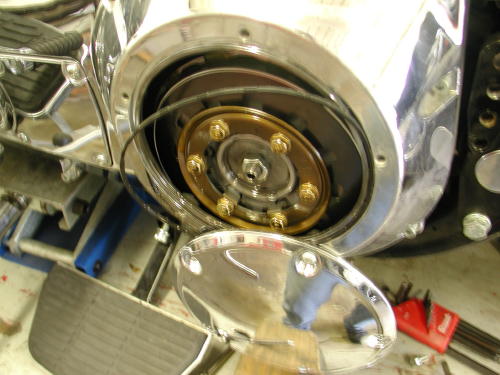
I started to remove the shift levers and discovered that I had to remove the footboard to reach the inspection cover Torx fasteners. I wasn’t sure if the footboards would have black in their future. At first I reviewed the area of the black board that would show, just the rim. Then we turned the board over and studied the way the rubber suspended pads were installed. We discovered that the pads are removed easily with a punch to the edges of the bottom protruding rubber lips. The boards went into the box for powder.
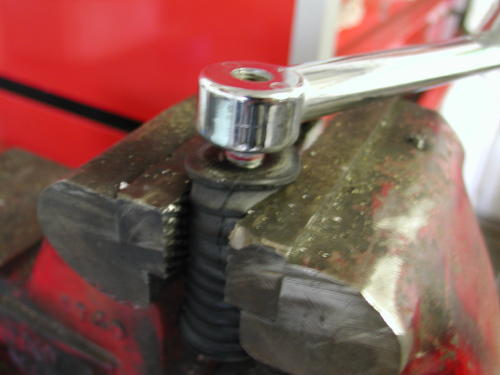
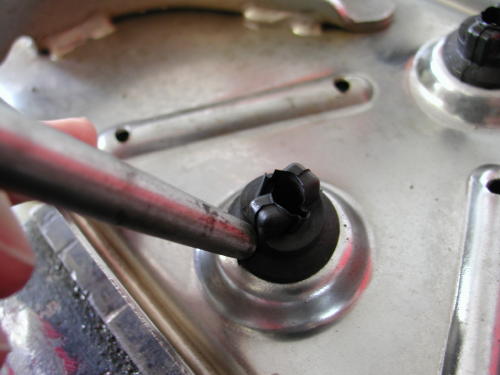
This was a simple process to tapping the edges of the rubber with a large tap and rubber hammer. We tried driving them out with the tap first, through the center. That didn’t work.
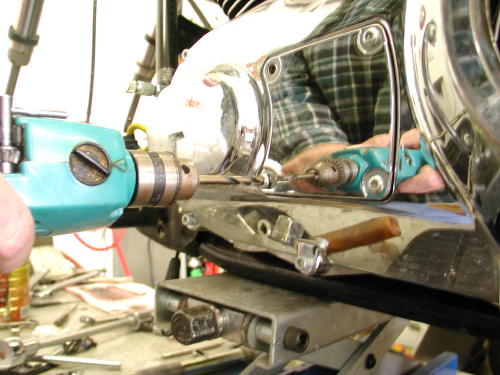
The mechanic’s law calls for one screw or fastener to seize every time. We had to drill out one of the inspection cover screws.
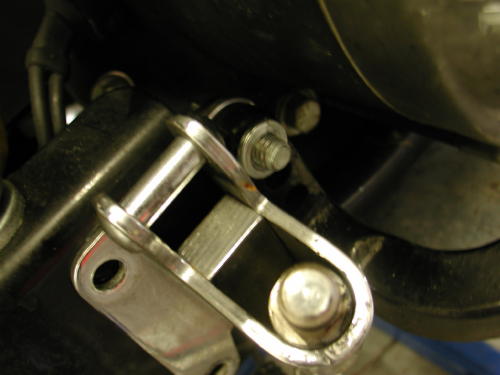
I tried to take off the kickstand the old fashioned way by removing the tooth then pivoting the arm forward. The spring wouldn’t come loose. I had to remove all the fasteners.
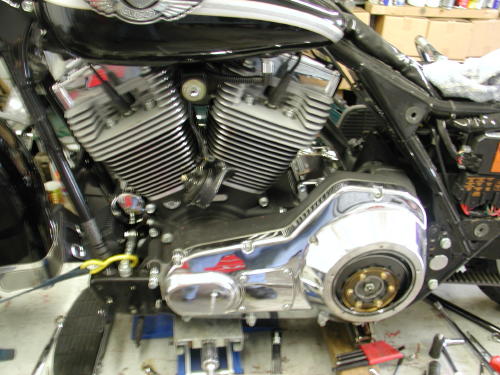
Metric fasteners haunted me from time to time, including the red Loctite touched horn fasteners which were #10 metric sockets. The Showa front end was covered with metric 12 point fasteners. It forced us to hit a commercial tool shop for 12-point metric sockets.
As the last of the fender rail parts came off we marked the loop that carried the license plate. We planned to replace the license plate holder with a fender-mounted job that attached below the taillight. We cut off the existing license plate loop, then I brazed washers and nuts so we could screw small orange reflectors in place.
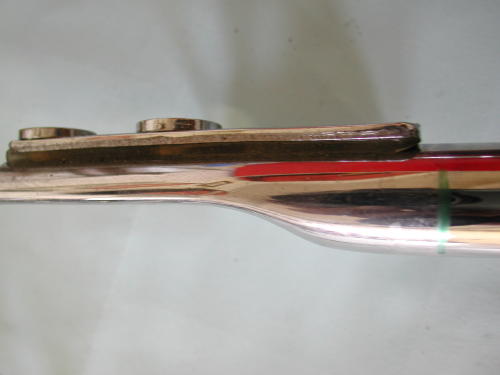
We marked the old license plate rail with a felt pen so the cut would fall just under the fender rail cover.
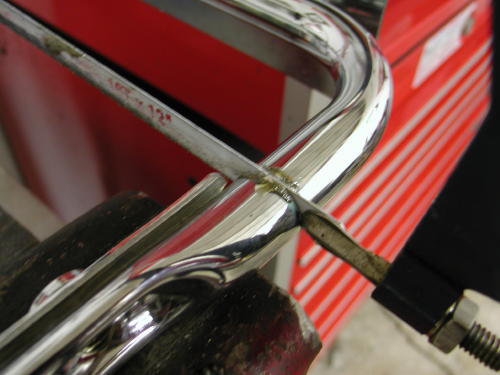

We didn’t use these reflectors. We were looking for Harley orange reflectors with steel backs.
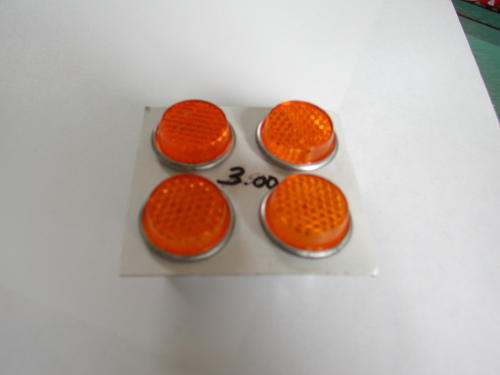
After a swapmeet run we had the right stuff for the job.
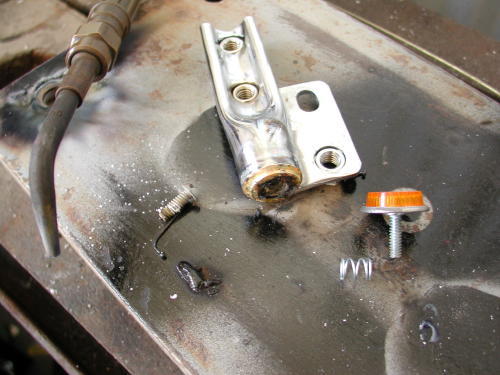
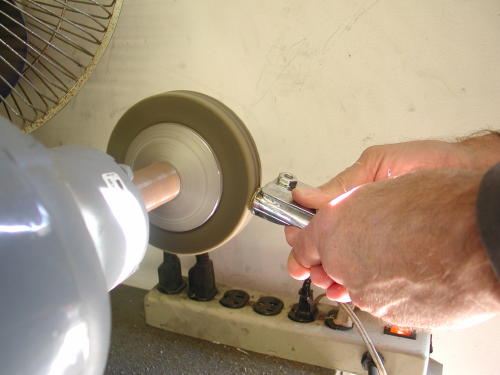
Sin Wu wandered into the garage just as I turned off the torch. She shuts down productive activity wherever she goes. She had a couple of alloy knitting needles that she offered us. I discovered in short order that the long alloy knitting needle worked perfectly for removing the hard-to-reach cotter key behind the brake pedal.
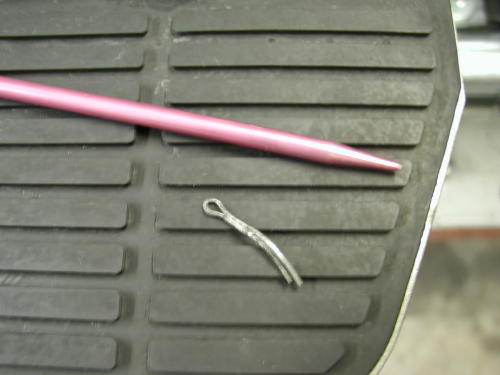
I had the toughest time retracting the clevis pin from of the pedal that hinged on the master cylinder piston. Finally it was removed with a punch from under the frame. The brake pedal caused me so much pain it didn’t make it into the powdercoating box. We painted it with a rattle can after prepping.

Continued On Page 2
The Amazing Shrunken FXR Project Part 3
By Robin Technologies |
Bandit and I were checking out the Amazing Shrunken FXR. “Thedamned thing,” referring to the shrunken FXR project we had beenhammering at, off and on, for almost two years, “has attitude,” hegrowled, “a bad-assed attitude.”
“Yeah, but will it have sound attitude?” I mused. “I want it toget attention. I want it to be felt in their chests before they seeit. I want them to hide their children from the evil they fear.”
The Amazing Shrunken FXR has developed into a mythic ethos. Froma cardboard box full of rejected, beat-up, and cast off parts, thebike has become a sculptured icon, a physical dream, and perhaps awrong turn down a bad dirt road, three miles back.The project began back in the spring of 2001. After a lot of fitsand starts, the Buell Project, the Sturgis Run, the Deer Gut stewadventure, Bandit’s painful recovery, the Red Ball prep, variousevents including a trip around the world and soiree’s, we slappedparts on, hammered steel into shape, welded this and that, cussed andfarted and got to where we are with the help of a RevTech driveline,Custom Chrome, BDL belt, Joker controls, Cyril Huze sheet metal andCompu-Fire electrics. The bike is raw boned, trimmed down, and meanlooking. That’s where it stands, inert and waiting for inspiration,up on the rack at the Bikernet garage.
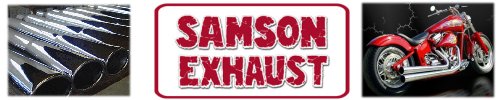
Bandit regarded the raw metal frame with squinty-eyed intensity.”What you thinkin’,” I asked, keeping my own gaze focused on thepotential of the bike. At my question he stretched out his gangly,egret-like frame to its full 6’5″. “It’ll be a loud mother fuckereither way you play it,” he intoned in his gravitas basso-profundodeep voice. “We’ve shortened the frame and rear wheel base so muchthat it’s barely a cunt-hair from the exhaust port to the rear wheel.”
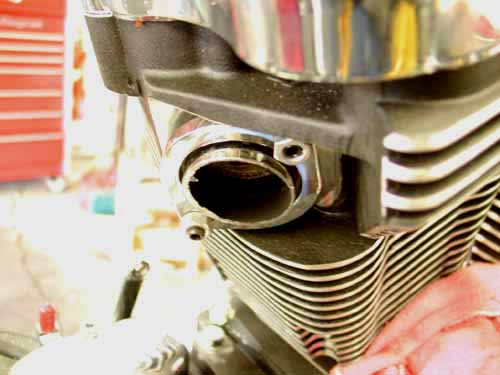
We cut a piece of an Samson Evolution system with a Mikita touse the exhaust port, then started welding other pieces in place. Wecut it back to make a tight turn and create space away from the oiltank.
“Fuck it,” I responded in my best Pancho Sanchezimprovisation, “let’s just start from the port and see what happens.”
We rummaged through a pile of Samson scrap exhaust pipes that wehad scavenged from a dumpster behind the Sampson factory. Flingingout fish tail tips, shot gun systems and swoopy cruiser exhausts,most of them dented and damaged so they couldn’t be re-used. Mr.Samson gave us only the best to modify. We eventually came up withenough pieces to fabricate a Frankenstein exhaust system.
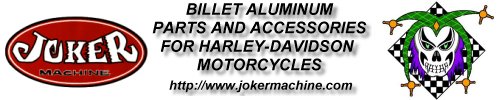
As I grabbed for a section 1 3/4-inch chrome pipe, Imistakenly grabbed a goodly chunk of fur. Bandit’s midget, crazeddemon of a feral cat yeowled in protest and sank his needle-liketeeth into the back of my hand.
“God damn that crazy bastard,” I screamed, “he’s as crazyas a peach orchard boar.” I’m sure Bandit has a mescaline salt-lickfor that freaked out feline.After I extricated my hand from the jaws of Bandit’s feline Cujo, Ireturned to the exhaust system at hand.
Our intent was to minimize the exhaust system as much as possible.We ran the pipe straight down from the front exhaust port, thenturned it to hug the bottom of the engine case. We had originallyhoped to put a flattened pipe under the frame, but reasonable roadclearance dictated a different path. So we tucked it in and aroundthe engine case, then inside the frame, coming out just at the edgeof the back wheel.
“Our first mistake,” Bandit spouted, “we needed a smallerdiameter chunk of exhaust to form guides when welding chunks ofexhaust together. If we had slipped it in one piece even a quarter ofan inch. it would have held each chunk in alignment. That’s onetheory to building pipes. The key to fabing your own pipes is havingenough scrap to slice and dice, then cutting and working each pieceuntil it’s as close to a perfect fit as possible. Finally the tackingprocess is critical. That’s were the guides didn’t come in. If we hadguides we wouldn’t have offset pipes tacked into place. That problememerged severely a week later during the grinding process.”
“It took two days of playing, cutting, fitting and welding toform a completely custom exhaust system in place,” Bandit added.”Make sure you wet towels and form a fire barrior around your tackingarea to protect the rest of the bike. I used a small 0-sized torchtip and common hanger to tack the segments of pipes together. I’m notconfident enough with our new MIG welder with thin sheet metal, so Istuck with the torch.”

” It wasn’t perfect, but it was ours,” Bandit added, “acompletely unique system that would be tucked under the transmissionand attached to the driveline solidly under the tranny backing place.Then we faced the muffler aspect. The pipes were too short to be openor we would have been arrested within a block of the headquarters.”
Needing some kind of ‘standardized’ muffler elements, we went toour local San Pedro Kragen Auto Parts store. With the clamp-on piecein hand, we found parts and pieces enough to create a 7″ mufflercase. “Most of the elements were too heavy and glass packed,” Banditspouted, “We couldn’t weld on a glass pack.”
Back at the garage, with torch in hand, Bandit cut out a sectionof baffles from some scrap Sampson muffler. Spot welding the bafflesinto our jury-rigged muffler, we produced something that may, likeJapanese Fart Wax, diminish the painful ‘Brap-rap-rap’ flutter ofunrestrained exhaust back pressure. A right-angle turn-out willdirect the dragon’s breath exhaust from the screaming 88cc Rev Tech,high-performance engine to an unsuspecting public standingslack-jawed and terrified at the curbed edge of civilization, theirhair-dos blasted straight by the sizzling after-burner of the AmazingShrunken FXR.
“He gets sorta twisted,” Bandit muttered shaking his head.”Actually with the baffle in hand we went to San Pedro Muffler Shopand looked at the myriad of tips and tubing alterations we couldmake. We found a tip and had a chunk of 1 7/8 tubing spread to matchthe tip. That formed the other end of the muffler. We just had toweld the three elements together.”
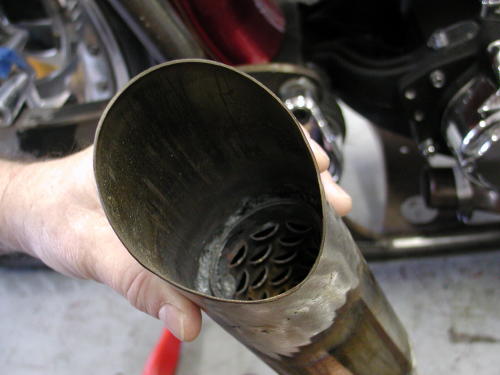
I welded the baffle in place, positioned as it was in theSamson System. I discovered that the two elements didn’t want to weldtogether. I have a feeling the tip was made of an inferior metal.
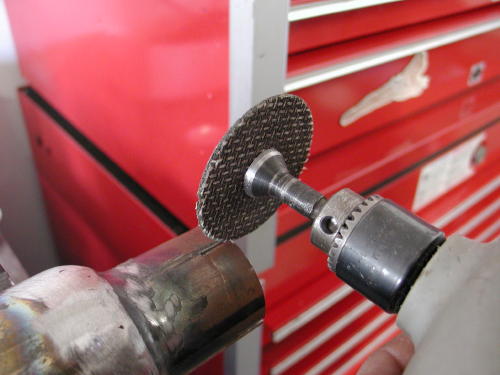
With the die grinder we cut notches for the muffler clamp.
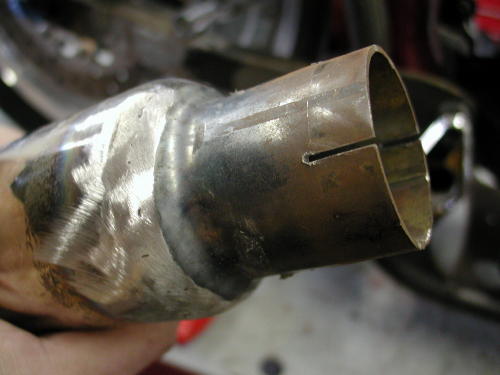
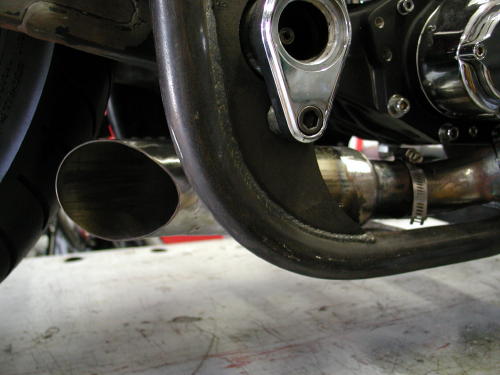
“After welding and fitting I stood back and was proud of ouruniquely tight system that would allow Giggie, from Compu-Fire, tomachine mid-controls for a final touch,” Bandit interupted. Theexhaust played perfectly into the Shrunken aspects of the project. Iremoved the tacked system and began hours of gas welding to make itwhole. That’s when all hell broke loose. While working on anotheraspect of the bike with my back turned to my partner, he began togrind the welds. The college art history professor sought perfectionwith each weld and ground right through the thin walls of the18-guage exhaust pipes. It was amazing. I was sure the system wasruined.”
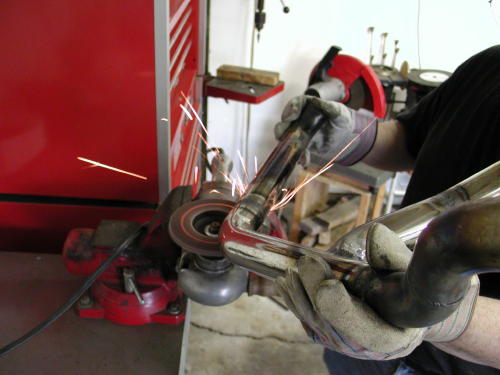

This shows the amount of area ground down so far we were forcedto fill it or destroy the system and start over.
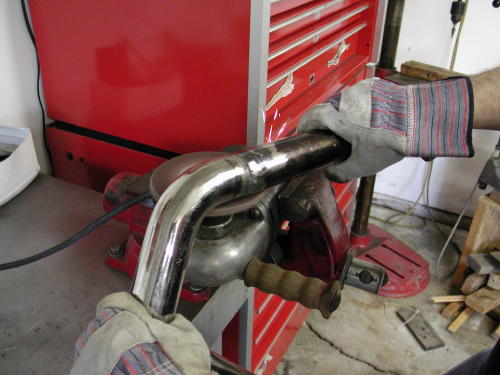
“Some builders tack systems together then take them tomuffler shops for professional construction. I thought that was mynext move. Unfortunately a regular muffler shop doesn’t have themandrels to make the tight bends we had proposed. I was devastated,but the man told me that he could fill the welds with his MIG welder.
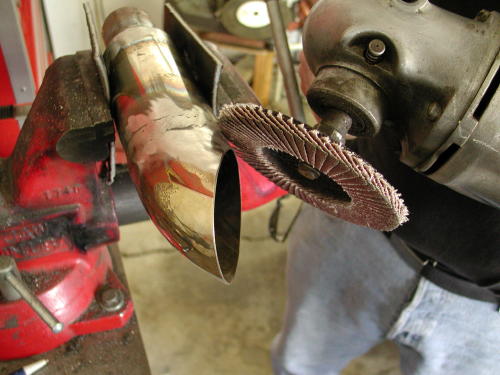
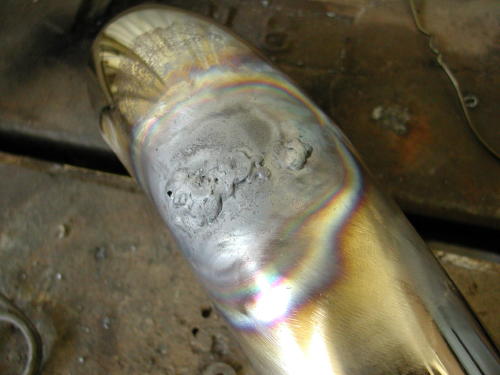
More welds to fill the mad grinder’s cutting work.
“Unfortunately each weld was now a 1/2 inch tall and wide zit atalmost each junction of the pipe. Nuttboy began the grinding processagain. More holes were found and I filled them with gas welding usinghanger rods. I joke now that if the bike runs like shit we blame iton the exhaust system. If it runs well, it’s the same roll of thedice. We’ll see.”
“Making your own exhaust system can be a blast, just don’tget heavey handed with the grinders. Pipe is thin and a little weldthat shows won’t matter much since we didn’t plan on chrome, butblack Jet Hot coating. I’ve sworn off chrome exhaust systems on mybikes for the future.”
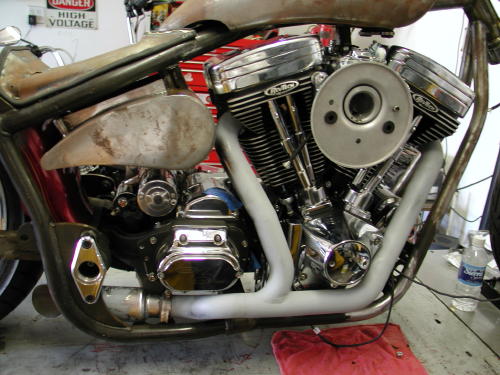
That big bastard just won’t shut up. The next episode in thismechanical adventure will feature Giggy’s attempt a electrifying thesteel monster. Next weekend, barring any new bike projects, Giggy’sinopportune finger damage at the power tools, splattered deer guts,San Pedro political insurrection, Sin Wu’s beguiling charms, a caseof beer, or any other form of diversion or chaos, we will be closerto cranking this monster over.
To Continue……..
Back to Part 2……..
Back to Custom Chrome on Bikernet……..
Back to Joker Machine on Bikernet……..
The Amazing Shrunken FXR Part 5
By Robin Technologies |
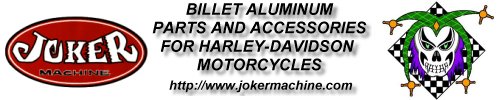
You’ve been there. You handed the Makita cordless drill toyou’re drunken buddy, and he drilled a hole in your big screentelevision. You tried to wrap the extension cord around his neck andfinish him off. We came close to blows in the garage a couple ofmonths back. I spent days carefully welding chunks of Samson exhaustpipes together to form a one-of-a-kind exhaust system.
All the welds were performed with gas and hanger rod. Thepipes weren’t perfect, but they fit the bill. They were actuallyintended to be prototypes, to be duplicated by a paid professional.After the first pass was completed the pipes fit like a glove,although they were artistically rough around the edges. Nuttboy cameby on his Wednesday afternoon escape, and I handed him a highspeedgrinder and instructed him to round off the welds. I worked onanother project and paid no attention while sparks flew. When he wasfinished he tapped me on the shoulder and said humbly, “Not sure thisis what you had in mind.”
He had ground right through the pipes and left gapingholes alongside most of the welds. In addition, I discovered to myteeth-grinding dismay, that there were still large sections of thepipe ground so thin, that as soon as the torch tip came within 6inches of the surface the pipe melted away. I spent another whole dayfilling the gaps. Who knows what will happen when the struggling bikefires to life. We’ll have the only exhaust system on earth withbaffles throughout.
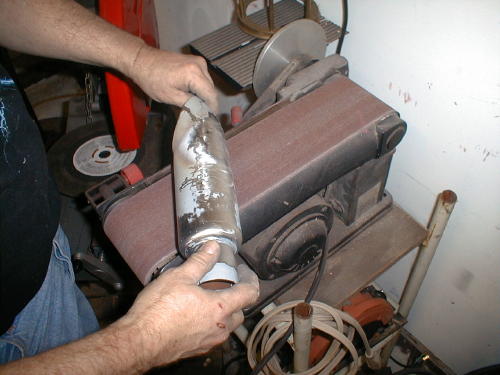
That’s not all. The grief continued. I hand made a mufflerusing a portion of a Samson baffle. We purchased a chromed, truckfender tip from San Pedro Muffler and went to work, but after hoursof screwing with the shiny metal we almost shitcanned the unit. Thefender tip was made out of a strange metal, almost pot metal, thatdidn’t seem to take to the gas welding and wouldn’t respond tobrazing. For every hole I filled, another crack lurked. I welded,then smoothed on a bench grinder only to find cracks and holes tofill again. The shorty muffler probably weighs 50 pounds due to thevast layers of welding rod. As it stands, this is a pure prototypeexhaust system. We should use it for testing then shitcan the rankpiece of shit and start over.
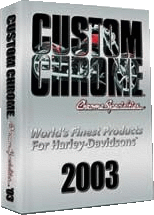
Click to order Catalog!
Frustrated, but pleased with the overall look we were readyfor final metal work. This bike is being built by inexperiencedhands, not professionals, in our backyard garage. Sure, I’ve builtsome bikes, but I wouldn’t consider myself a metal fabricator. I cameup with the initial design and we roughed out elements, but we neededa master metal worker to finish what we started. There are preciousfew, true metal craftsman, who I know. One is Billy Westbrook,another is Jesse James and recently, in the news, we displayed metalwork by Roger at Goldammer (Goldammer Cycle Works Ltd.,www.goldammercycle.com ,1-250-764-8002). High quality workmanship.
They’re out there but not on every corner. I stumbledonto another super-slag artist under my nose. James and LarryFamighetti are Hamsters and own a corrugated steel metal shop inHarbor City, California, called Fam-Art. You’d be tweaked to rumbledown Narbonne Street and stumble across this rusting corner buildingthat’s got to be the oldest swaying dump on the block. Theyspecialize in structural steel (you could never tell it from theircreaking tin shed) for homes and buildings. Large chunks of steel,massive shredders, presses and welders are scattered around the funkylocation that’s reminiscent of the first shack Harleys were built in.
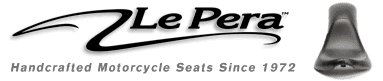
Nuttboy and I darkened their doors a couple of times toask them to flame-cut a couple of chunks of steel for our fenderbrackets. The more I hung around the more quiet-James began to showme steel components he had fashioned for some of the local riders. Herebuilt and reformed Harley taillights to eliminate all the edges andgrooves, then welded them to fenders so that ultimately there were noseams. The more I gawked at the sculptured parts, that demonstratedhis ability, the more I knew we had discovered a man capable of BillyWestbrook fabrication qualities. We hauled the entire FXR to Jamesthe next week.
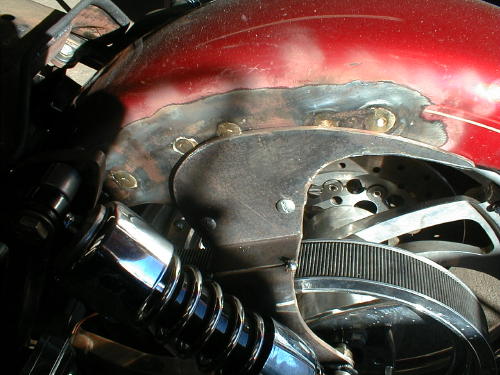
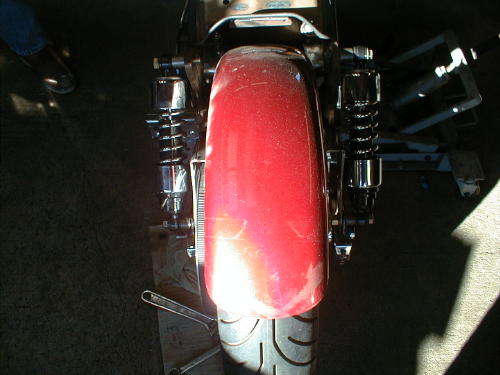
James relocated the straps in such a way to narrow the shockplacement keeping that shrunken look in mind.
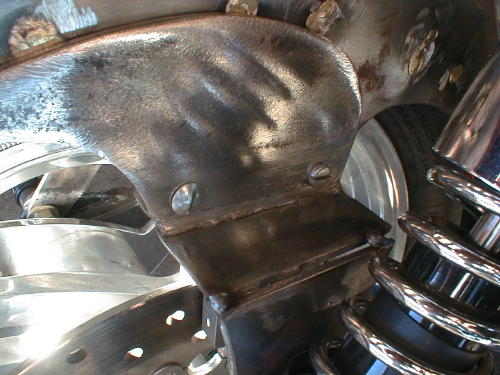
This is a close-up of the right fender strap. It’s beencorrected, reformed and readied for final welds.
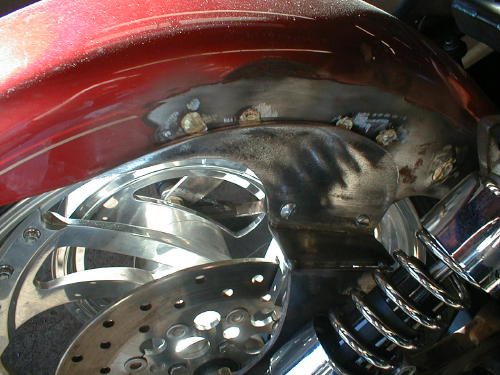

We cut and fitted the tank and made the mounts, butJames filled the underside, rear section for a perfect fit.
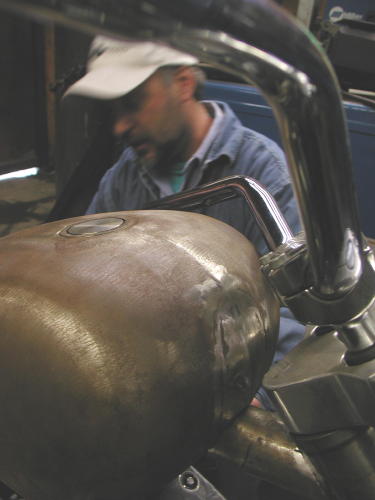
We jacked up the front of the tank and mounted it, butJames filled it and formed the front of the tank to match the customridge along the top. He even made paint work suggestions that I foundinteresting. “If you paint a ridge like this with a light color,”James said, “The ridge will disappear.”
We decided to paint the bike a light House of Kolors pearland create a dark teardrop panel on the top of the tank. He alsocreated and welded fork stops to the neck.
As we rolled out of the shop that day James still hadfinal welds to complete. He straightened out our seat pan, but neededto figure out a mounting arrangement. Finally we needed the CyrilHuze front fender brackets checked and welded into place.
We should have the Shrunken FXR back in our clutches inthe next couple of weeks. We need to finish our rear brake andshifting mechanisms with Giggie from Compu-Fire, fire it up for atest ride and tear it down for paint.
Oh, I need to untie Nuttboy. I need that extension cord.
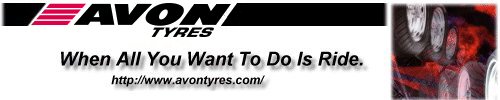
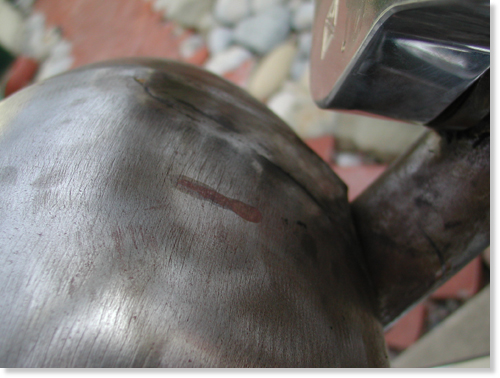
The Shrunken FXR returned recently from Fam Art, in HarborCity, California (310-326-2141). They welded, shaved, mounted theseat, manufactured fork stops and saved our poor- construction asses.James Famighetti mounted our Cyril Huze front fender, welded andformed the tabs and informed us that the Avon Venom was too large forthe narrow glide front end. It was our turn to work on it.
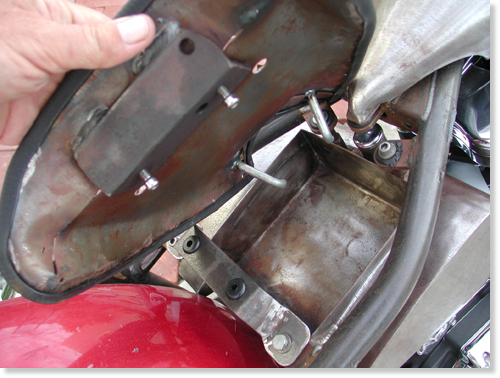
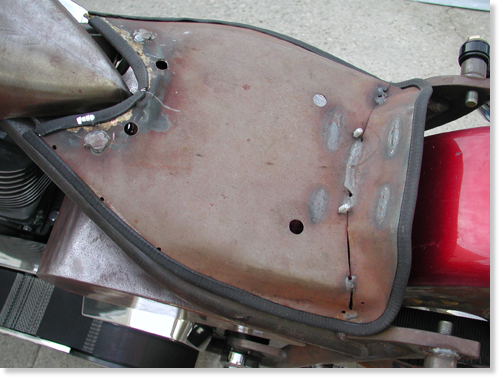
Note that James mounted the seat pan so that the edges wouldnot touch the frame paint in the future.
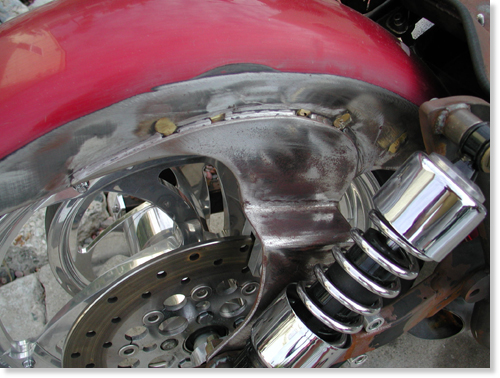
Like any self-respecting bikers we hate to have a bike, oreven components out of our mistrusting mitts. We had another dilemmathat needed handling. The bike still didn’t have a kick stand, and weused two 2 by 4’s, to hold it upright, when not perched on the lift.There’s a trick to this maneuver. If I backed the Pro Street FXR outof the garage and wasn’t hauling the wood planks, I was screwed. Ifalone, I could stand there for hours waiting for someone to strollpast carrying two 2 by 4s–unlikely. After a couple of unsteadyoccurrences, the bike didn’t move without the wood chips on the seat.You can imaging the major pain in the ass this caused.

We ordered a weld-on, Sportster style, kick stand fromCCI, and it arrived complete, with all chromed hardware and thebracket to be welded on the frame. There was one problem indetermining the position. The front Avon was a 100/100 18-inch, andwe planned to replace it with a 90/90. We needed to have the finishedPerformance Machine wheel in place.
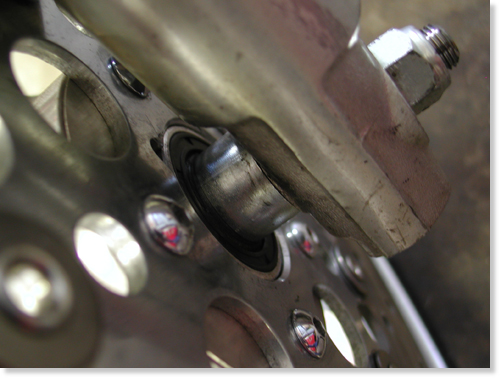
The Avon Road Runner tire arrived, and we had it installed at thelocal Yamaha dealer. James pointed out to us that our front tirespacing wasn’t perfect so I sliced a spacer to give us about a1/4-inch spacer on the right side of the wheel and about a 3/4 inchspacer on the left. The tire, almost centered, now had clearance, andthe wheel floated effortlessly under the modified Cyril Huze frontfender.
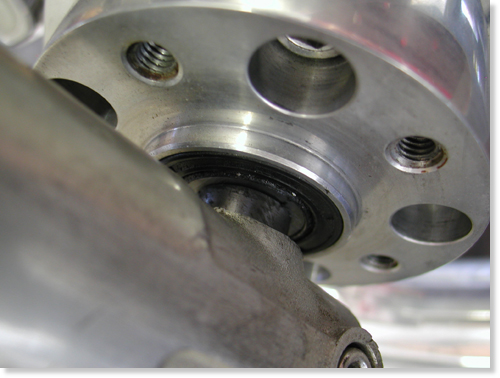
Now we were cleared to install the Hot Match weld-on kickstand.This is a tricky assembly process. First, you need to be absolutelysure you don’t plan to change the front wheel, to a 21, or extend thefront forks. If you do, the kickstand will need to be bent ormodified to fit. It’s not the end of the world, but it will destroythe chrome.
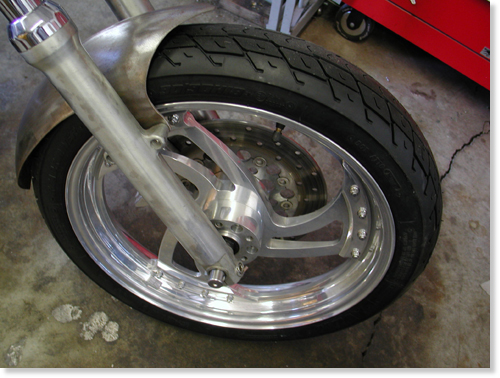
The other trick is determining the right position. Here’swhat my feeble brain told me, since the directions with the Hot Matchdidn’t cover positioning, except to recommend that you take yourtime–no shit. First I stood my Road King straight up and lifted theside stand until it was locked in place. Then I measured from thepoint that would touch the pavement to the ground. It varied fromaround 2.5 inches to 3 inches. I noted that the Hot Match lever wasnearly 3 inches shorter from the point of contact to the center ofthe pivot point. I took that into consideration. I also noted that Ihad lowered my King with shorter shocks, then added a larger Avontyre (a 150). Ground clearance was also a consideration.

Then we picked a placement area on the frame. Our designcalled for little or no forward controls. I kept the tab under theBDL belt drive system and hidden as much as possible, without beingso far back as to create a balance problem. If the weight is forwardof the kickstand, sometimes it can topple the bike. One otherconsideration. When the stand pops up you need to be able to reach itwith a toe, and it better not ride on the belt, or you’re toast. Makesure to check all that, before you burn any rod.
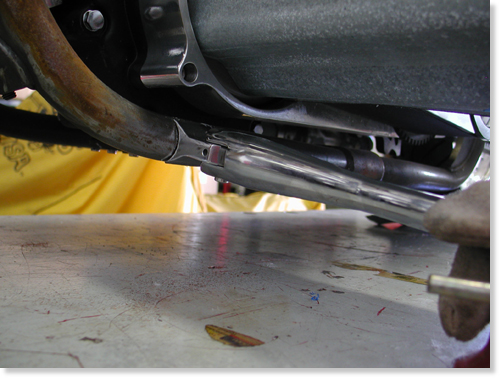
I sprayed the frame rail and the components with asilicone splatter preventative. It obstructs slag from sticking tocomponents. It also made the frame a slipper bitch. I tried settingthe stand end on a socket nearly 3 inches off the deck. Then Iconsidered the differing lengths of the stands and shifted to 2.5inches. Sin Wu was called, from the bedroom, to hold the stand firmlyin place. I marked it, with a grease pencil, then ground the edges ofthe bracket to be welded to the frame. Extra grinding took place toform a snug, metal to metal fit. In order to make all this work weneeded to partially assemble the kickstand without the ball andspring.
The easy-to-read directions called for disassembly, but we left ittogether and used it to hold the bracket in place for tacking. Beforetacking I backed the bike out of the clamp, holding it upright,positioned the bracket in the white grease pencil marks and leanedthe bike carefully until the stand rested on the flat surface. Itlooked cool, so we re-clamped the bike securely, held the stand inplace, protected the belt from hot slag and tacked the sucker withour Millermatic welder. Then we took the stand arm off the bracketand welded it some more. That would hold it securely until we torethe bike down for paint.
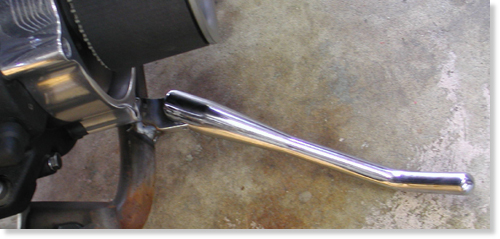
The Hot Match unit from Custom Chrome is a well madeprecision unit delivered show chromed. The instructions includedrecommendations to apply anti-seize to the spring and ball. Theyendorse using Red Loctite on the pivot pin threads. We didn’t becausethe bike would be torn down for paint in the near future. The armneeds to be placed firmly over the bracket and pushed into placebefore the pin will ease into the hole from the bottom. It doesn’thurt to have a spare set of hands and someone holding the bike.There’s also a pivot pin set screw to prevent losing that preciouspivot pin and kick stand arm, on a desert highway, in the middle ofArizona.

That’s it, except to mention that when we head to thepaint shop, we need to tape off the chrome bracket, so the painterwill paint over the welds but not the chrome tab.
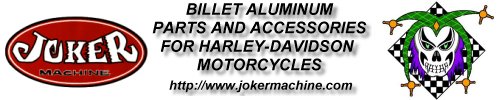
As you can see this bike is damn close to the spray booth.I need to coerce Giggie, from Compu-fire, to ride his FXR out to theBikernet Headquarters with our mid-controls. Once the Joker Machinehandlebar controls are bolted to the modified bars, we’re ready for atrial run, then off to paint. Stay tuned.
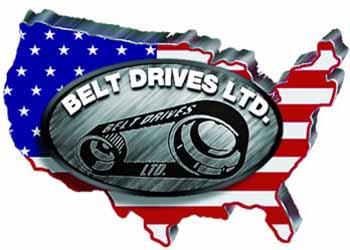
–Bandit
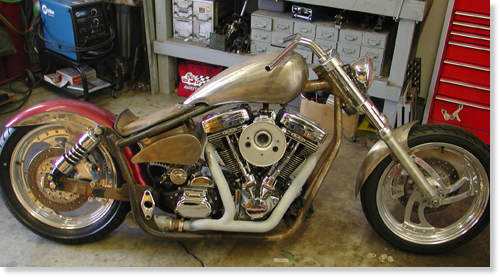
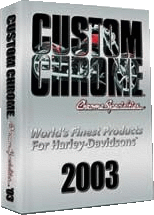
Custom Chrome ® and Chrome Specialties ® have joinedforces to bring you the most comprehensive product offering in theHarley-Davidson ® aftermarket! At over 1,400 pages and over 25,000part numbers, our 2003 Catalog features everything from nuts & boltsto HR3 bike kits, and sets the NEW industry standard.
ONLY $9.95 + 6.95 Shipping**
–Bandit
Back to Part 4…
Sturgis 2000 Project Bike – Bandit II Lives
By Robin Technologies |
![]() |
Each custom motorcycle has a story. That’s one aspect of this treacherous world that sets it apart from stock bikes. Stop any rider of a chop and ask him about his bike and he’ll either punch you in the face or tell you how he started to build his bike, lost his wife and family in the process, and had to sell his home and move into a rented garage in order to complete the project. There’s a story of romance, heartbreak, hard work, and struggle behind any bike. This one is no different.
Now comes another saga, equally terrifying, equally fraught with intrigue and heart. This tale of woe begins five years ago with a project conceived with Ron Simms of Bay Area Custom Choppers. The plan was to build a bike as a tribute to the ’30s. But times changed and attitudes became harsh as the unit came together. The more we worked, the farther the project ventured from the reality of the hard-riding world. |
|
Ultimately, the bike was finished and featured in the February issue of VQ magazine. As a tribute to all who worked on it, we will feature the entire list of talents that it took to complete (…see the partial list of the crew). The sad part of the story is that the bike was ultimately unrideable. Hell, we couldn’t even trailer it to shows without damaging the chassis, and the bike was put up for sale with less than a couple of miles on it.
But we don’t like the idea of selling something that our brothers helped us build and a suggestion was made to turn it into the ultimate ground-pounding, coastal-bar-hopping bastard. We pondered the thought. We kicked around the years it took to build it in its current form, the times we went through, the love that was lost and gained, the adventures, the rides, and the wild times to come. We thought about Sturgis 2000 and what to ride. I spoke to my brothers. We had considered riding old bikes. So the gauntlet was tossed into the ring. Build a rigid flyer from the pieces of the Bandit II and keep it alive, or put dual carbs on a ’48 Panhead and take our time? Ah, but the Bikernet staff can’t proceed with anything that’s status quo, we’ve got to tear the whole enchilida to the ground and start over, and do it with a vengence. At another meeting at Harold’s dive bar in San Pedro while tossing back stout glasses of Jack, a contest was conjured up. Bikernet East (the chicken-shit Agent Zebra who couldn’t hold a job in Los Angeles and escaped to Miami with his European nymphet) against Bikernet West (Bandit himself, riding a Daytec Rigid). Since the homeless, jobless bastard of Barstow doesn’t have a dime to his name, but still writes vile stories about the upstanding members of Bikernet, we voted to build him a bike to ride to Sturgis. Bandit was already tweeking the drawing board with parts from the Bandit II, hence a contest. Bikernet East rides against Bikernet West to the Badlands and we’ll take a vote as to who has the coolest bike that makes it. Yeah that’s right – gotta make it there to be voted on. |
|
![]() Photo One |
As it turns out, we will be able to use the entire driveline from the Bandit II for the Bikernet West rigid chop, including the 98-inch S&S, Simms-built motor (photo 1) and Custom Chrome transmission. It will be placed into one of Daytec’s 4-inch stretched, wide-tire rigid. |
The Harley-Davidson narrow glide (photo 2) will stay with the original Paughco frame for the Bikernet East project and a new long front end will grace, perhaps a Weerd Brother glide, the Daytec chassis. | ![]() Photo Two |
![]() Photo Three |
Two Road Wings 60-spoke wheels have been laced and mounted to Avon tires. The front will be a 21 with a 5-inch wide 18 on the rear. And Bandit picked up a Yaffee sidemount license plate/taillight. All the brakes and controls will remain Performance Machine (photo 3). |
Harold Ponterilli will paint the reincarnated Bandit II cobalt blue with ’60s metal flake silver flames touched off with white pinstriping. The Bandit II will live to fly through the streets of Long Beach, Pedro, and L.A. And perhaps, if all goes as the Lord of Choppers dictates, across the desert into the Badlands this year.
You’ll see the entire saga unfold on bikernet, good, bad or ugly. |
|
Ride Forever, –Bandit |
The Road King Report Installment 1
By Robin Technologies |
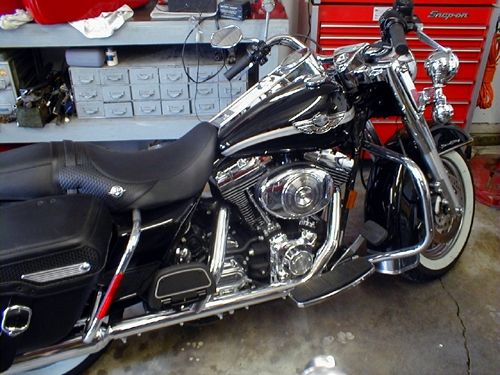
ROAD KING REPORT–Initially I had some questions regarding Road Kings. I wanted to know some about the frame geometry. I perfer a little trail over low speed, parking lot handling. I like to run fast and stable. Next I’m old school. I perfer a bike with minimun extras so I lean toward a carb model over the fuel injection, EFI models.
I immediatly spoke to an expert, Paul from Charlotte, H-D:First as you always say “What year is the damn thing”??????? If it’s a newer model why get rid of the EFI?? The new stuff works good. Harley has new sofware to tune the thing, just out from the dealer show. This will put a big hurt in the Powercomander II and any other after market add on stuff!!!! It’s in the new P&A book for ’03 in the Screamin Chicken (Eagle) section. I like the new Dephi stuff. Also BC Gerolamy has a new dual throat induction throttle body for the Delphi system that is kick ass!!
To take off the system, man it’s lot’s off work. The ECM has all this start up shit it goes thru. checking all the system’s and sensors. Again I have never done this. So to be honest I just don’t know for sure on this one. I can run it by Old Bob tomorrow and see what his thoughts are on both the frame/trees and removing the EFI.
On the frame, my first thought is no. Are you familiar with what they did to the trees? They are not like the old FL stuff at all. The stem is in front of the fork tubes. This makes it a self centering front end. One of the tests they have to do at Talledega on the track is to smack the handle bars hard at 80 MPH++ and see if the damn thing will straighten itself out!!!!
I’ve never thought about doing this so who knows maybe it could be done. Christ you come up some stuff man. Was Jack Daniels involved in all this brain storming??
A week later…
’03 is good year for the Road Queen. The EFI is much better than years past.My question to you is why do you want to loose the EFI?? What are your plans?? Pipes, Big Bore, Stroker kit?? We just did a 103 Stroker kit with cams, heads and a V&H 2-into-one pipe, megaphone, on a ’03 Road Queen for a salesman. He should have used a Thunder Header but most of these clowns want the magazine yuppy chrome look. Shine and billet are in I guess, drives me nut’s!!!!!
You can remove the fuel pump and that shit from the tank. You can put a regular fuel valve in the tank in place of the EFI fuel line. There are two bung’s on the left side of the tank, one is plugged. I did make an adapter for a fuel valve for a Softail EFI bike once. The guy bought these tanks at a swap meet and didn’t know they were for fuel injection.
I think maybe you might just need to change the ECM from EFI to a Carb. ECM. Disconnect the senor’s, eng. temp, crank pos., induction module stuff. Do the tank, install a carb and you might be just be down the road. That way you could leave all the stock wiring and shit in place if you ever wanted to go back to EFI.
On the trees I guess when they went to that style the early top tree was just turned around for that newer style configuration. Don’t know about the setup now. If you did a rotation of the top tree putting the fork tubes forward the bars would be in a different forward location. That would screw up all that headlight cover shit. You might be able to put a complete early FL front end on. Hey maybe even the adjustable sidecar trees. Remember them? The front fork’s are non-air assist now.
I’ll keep plugging away on this “Amazing Raked Road Queen” project for you. I can check out some front end’s and take a better look. Also will try to call tech services at H-D and see what won’t say!!!
–Later, PSD
Bikernet West – Mikuni Carburators to the Rescue
By Robin Technologies |
With Sturgis 2000 looming over Bandit’shead we’ve been firing away at the getting the job done. Bikernet Eastmachine was well out in front in the competition when we wheeled the Agent’slow slung Softail onto a slick Gold Rush semi and said goodbye as the rig,packed with Ultra machines, Big Dogs and customs from the west coast, headedeast. Eddie Trotta from Thunder Design was more than happy to have thebike unpacked in his shop in Fort Lauderdale, so he could point a fingerat Bandit’s creation for Agent Zebra and bust out laughing, “You expectto ride that to Sturgis?” he said rolling on the floor of his shop. Weweren’t discouraged and neither was Bandit as we strapped the road wingswheels, the Weerd Brothers Front end on the Daytec rigid and went to work.
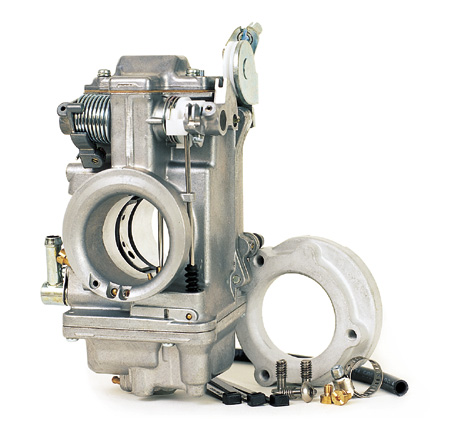
This was no ordinary installation. First,time was a factor, second it’s no normal, stock carburetor swap. The 98-inchS&S motor offered taller cylinders and improper intake manifold fitment.The stock Super E S&S manifold was too big for the 42 mm polished MikuniCarburetor. Stock manifolds shove the carb out too far and aren’t wideenough for the tall S&S cylinders so a quick call was made to JamesSimonelli of S&S who rushed the correct manifold to Mikuni. Lee alsowanted to explore an American Iron Horse manifold available for their customswhich pull the carb in closer to the engine and “L.T.” or James Littleof American Iron Horse moved equally fast and the parts were in hand inone day. The next hurtle: The cables. A call went out to Xavier at BarnettCables who turned about a set of Mikuni compatible cables which are setup the same as stock H-D cables, but cut to Bryan’s specifications forthe job. They also arrived in time.
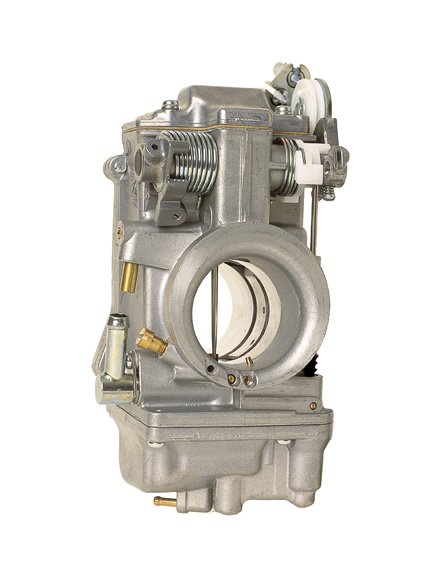
Bryan pointed out an adjustment on theleft side of the carb as you face it, a main jet air adjustment. He toldme to inform Bandit to turn it out a half turn in Denver for more compatiblerunning in altitudes. The bike immediately fired to life for the firsttime. Two weeks to go.
Bikernet West – The Chop Lives
By Robin Technologies |
![]()
The speedometer arrived from the Dallas Easyriders with a little over 24 hours to kick-off. The cable was coiled in a cardboard box waiting and the drive unit was already bolted to the front wheel. Unfortunately, the cable was the wrong unit and a hunt began for the proper cap. A call from Phil, the Hamster painter, encouraged Bandit to send a young lady to see Jim at Drag Bike Engineering. He had the cable and, at three in the morning, Bandit was installing it. We will also follow this series with an article on the Weerd Bros. front ends. This is a ball-milled wide glide that, depending on what ruler you use, is approximately 14-over. According to Bandit, who is in the garage packing as I hit the keys, the front end is light handling with narrowed flat track bars due to the six degrees of additional rake. Even with an overall 44 degrees of rake, the front sliders are smooth and work effortlessly. Although this is a European-built front end with metric Allen head fasteners, it’s highly adjustable with removable fender mounts and brake caliper mounts that can be installed on both lowers or either one or none for the hardcore muthas.
![]() Bandit’s about to take his Blue Flame for a final test ride with his bed roll centered over the Weerd Bros. front end. Yesterday, during the heat of the harbor day, a small Fed Ex package arrived. It was from C.J., the old biker engraver. Inside was a Bikernet engraved point cover, a “Bandit” money clip, and a flamed mag light. When more photography is revealed of the Blue Flame, the Bikernet logo with our babe mascot will be revealed in all her nearly nude glory. Damn, when she walks into the sagging headquarters, everything stops, as if a contact high permeated the garage. In a daze we watch her every fluid move. By reader demand we will post a photograph of the lavish facility in the next couple of weeks.
![]() The bastard is rolling out in the wee hours of the morning and the race will be on for the Badlands. Agent Zebra will be heading out of Miami at noon on Saturday heading north and into Tennessee, as Bandit heads east across the border into Arizona where he will relieve his helmet of duty and ride on in freedom toward Phoenix.
![]() More reports are forthcoming. Live from the Bikernet World Headquarters in San Pedro, California. This is Renegade. Over and out.
|
Bikernet West – Electronics in a Weekend
By Robin Technologies |
![]()
Wiring is the nemesis of man, the puzzle of the best builders, the hornet’s nest of breakdown treachery. Bandit sat for hours drawing a wiring schematic for Agent Zebra’s Softail, only to rip it to shreds and toss it in the trash. He made lists while Sin Wu brewed strong coffee and baked peanut butter cookies. Bandit barked and growled for a couple of days with each run to the marine store for connectors, to the electronics store for switches, to the Custom Chrome catalog for components. The same formula fit his own West Coast entry in the Sturgis Bikernet Chop-Off. We knew as soon as he mentioned that the bike was ready to wire, that we should pack our shit and leave. We took the case of Jack fifths, the girls, and checked into the nearest fleabag motel. While we sat around the stanky pool and partied, Bandit thought about each wire, each connection, and each component. His mentor, Giggie from Compu-Fire, was his only sounding board and the only sonuvabitch big enough to snap back when Bandit growled about wire gauge or lost connectors. He wired the bike entirely with 14-guage wires. The only other sizes used were for the battery cables (stock units) and the wire that ran from the battery to the ignition switch (12-guage). Even when the sexually starved statuesque Asian roamed into the garage with cocktails, adorned in a sheer negligee, she was ordered back to the headquarters. Soon she found another plaything to keep her occupied, but that’s another story. Wiring, in the big guy’s mind, is a process of understanding what is happening with each component, where each component is located, watching for the safety of each wire, keeping the bike sanitary, and organizing each group of wires. Each wire is covered with shrink tubing, each connector supported with additional shrink tubing. Each bike had a minimum of wires carefully placed. Each bike had a minimum of components to keep the wiring process uncomplicated or enhance the reliability of the machine. No turn signals, no handlebar controls, and no micro switches. He used only millspec (military specifications) or marine quality switches. Vibration is a killer on motorcycles and much the same on boats, in addition to the moisture considerations. One additional component made wiring simple and risk free, the Custom Cycle Engineering starter mounted mechanical switch. (Check the article here in the Garage.) This unit eliminated the starter button, the starter relay, and all the associated wires. You must make sure you will have access to the switch, which is mounted directly on the starter, under the oil bag, (Photo 2) which can easily be interfered with by the position of the exhaust pipes.
![]() Photo 2
The concept is that you physically push the solenoid into contact with the starter gears and electrically engage the starter. We chose a Compu-Fire starter from Custom Chrome to kick this 98-inch monster to life. The key thing on fucking up starter motor installation is over tightening the brass lug wire fitting. It may turn the connection on the inside of the starter and ruin the contacts. Compu-Fire has designed a new line of starters which feature 6:1 gear reduction (Photo 3) and a 6-pole permanent magnet field to eliminate starter stall-out.
![]() Photo 3
These units deliver maximum cranking torque without overloading the battery. They also eliminate starting problems on fuel injected bikes. Only two switches were used and one 30-amp H-D (common at any electronic or auto parts store) circuit breaker. One on-off marine toggle for the ignition, which energized the Compu-Fire single-fire ignition system, the hydraulic brake switch, and the taillight. Since all the sweet parts like handlebar controls, foot controls, mirror, and taillight were Joker Machine components, he was in luck. Joker works the brake light switch into the body of forward controls, which eliminated the bulky hydraulic switch, the junction, and a two-piece rear brake line. Another wire went to the other switch, an on-off-on switch for the headlight (high/low beam). Two wires were run from it to the headlight. Daytec does a beautiful job of running guide tubes in the frame to hide the wires. Initially, if you chose to do so when ordering a Daytec frame, you can have two inserts welded to the frame seat post rail for electric box mounting. We ordered the certs for this frame but decided that with the simplified wiring program we could stuff switches and all the wires into the structure of the top motor mount. This was Giggie’s suggestion and Bandit readily agreed (a miracle). With careful measurements the switch holes were drilled with several bits until a 1/2-inch hole for each switch was attained. The only guide hole that the frame was missing was one for the headlight wires, but two wires were run through shrink tubing to the headlight and through a 5/16 hole in the motor mount. One wire was run from one side of the ignition switch to the circuit breaker, another, the 12-guage wire ran to the battery. From the circuit breaker a wire ran to the taillight down another guide hole along with the brake switch wire. From the brake switch another wire ran to the taillight, brake element. We also used a Compu-Fire regulator, which mounted to the front of the motor. One wire ran from the regulator back to the hot lead on the Compu-Fire starter motor. Bandit used the excess 12-guage wire to run from the battery to the hot side of the ignition switch. Giggie recommends that you use crimpers designed for Duetch connectors for a solid, vibration-handling connection. Bandit used water resistant connectors from a West Marine store. After some 20 hours in the garage, Bandit was finally lured into a well warmed King size bed by Sin Wu and her girlfriend Coral as the sun came up, but at that point the bike was ready to be fired to life. The question was, could Bandit be fired to life? –Wrench
|