We are chopper riders, fun loving souls who dance with the devil by the pale moon light, risk our lives behind a bottle of Jack Daniels and the next redhead. To others this is a creative nirvana. It’s a form of artistic expression, and fortunately we have the freedom to express ourselves. Yet there is still another level to this expression and Gard Hollinger is standing on it.
Unlike many custom builders, Gard is taking what is generally an annual creative expression for the likes of Arlen Ness, Dave Perewitz, or Roger Goldammer, and mixing two-wheeled art with form, function, performance, technology, and pure guts. It’s not to say Arlen or Roger don’t consider these elements, but Gard is no longer faced with one-off considerations. He is also considering the manufacturing process, serviceability, and long distance performance.
Gard always had a knack for function and handling within his bobbed custom creations. He met Keanu Reeves in 2007 through Keith Oliver, who was working with Bill Wall and making Keanu a seat for a Dyna. When Keith looked at Keanu’s accessorized stock motorcycle, Keanu commented, “It’s bad isn’t it?”
Rather than criticize his efforts, he offered him a source for a more functional custom effort, through LA Choprods and Gard Hollinger. The first creative challenge included turning the new Bartels’ H-D Dyna into a street club bike, with saddlebags, two-up seating, and long ride capabilities.
Gard recently started to work with DBBP.com in the Netherlands on 3D designs while working with Saxon motorcycles on a special edition chopper, which became their best selling motorcycle.
Gard and Keanu collaborated on an extreme custom effort during an almost four-year process. By year two, they had a rolling chassis while working closely with Danny at Frame Works Racing.
“I saw Keanu maybe three times a year,” Gard said, “plus we worked consistently with DBBP and other CAD companies long distance, which created obstacles.”
Another year passed and Keanu said, “Think I’m disturbing your design essence with the notion of saddlebags?”
All the saddlebag drawings, modeling, CAD programs and blueprints went into the trash. “But can I take a girl to lunch?” Keanu continued.
Gard designed a flip-up rear section containing a slim passenger seat and a sissy bar. He made Keanu promise to lower the backrest anytime a passenger dismounted.
Another stretch of time slipped by with numerous drawings, long distance 3D programing efforts, and sketched changes and suggestions until Keanu finally caved, “It’s my bike. Let’s go solo.”
In 2011 this complete one-off custom creation was meticulously finished, and after the first ride, Keanu recognized something very visceral in the handling characteristics, the unique styling, and the mass of thought-out workmanship, and asked, “Could we make some more of these?”
Gard created a one-off custom capable of high-speed road racing runs, long distance touring, and according to Keith, “It’s a lane slasher.” The suspension worked like a dream with the semi-rubber mounted configuration, the mono-shock, and the state of the art upside down front end. Plus, it was suited for the big power of an H-D motor built by the Bennett’s Performance (106 cubic inch).
Like any world class custom builder, or even backyard builder, when the job was finished he stepped back and immediately saw refinements, but you can imagine the checklist to build a production bike grew like a meteor induced tsunami over a small island in the Pacific. Suddenly in a giant wave of world class ingenuity Arch Motorcycles was born, but…
First, there were stylistic adjustments.
All modifications must be laced to a myriad of production considerations.
How will his KRGT-1 fit into the competitive dynamics of the world of exotic motorcycles?
Massive vendor considerations.
Manufacturing considerations—every part would be re-engineered.
Facility considerations—the team would need more space, equipment, folks, shipping, and receiving.
The lists rolled on and on…
He wanted to build a magnificent artistic custom motorcycle capable of keeping up with Ducatis, and not stopping at every gas station, but being a rider for long distance or cross-country.
There were trademark considerations, patents.
CARB and EPA restrictions.
Gard started working on motorcycles as a kid. He couldn’t stand the notion he faced all of his life when a new customer’s motorcycle rolled into the shop and he grappled with a small fix turned ugly because of mounting or positioning. He wanted the KRGT-1 to make absolute serviceable sense from stem to stern.
He also witnessed another big wave of technology engulfing the auto industry and rubbing off on motorcycling, including computer-operated suspension systems, proportioning brakes, ABS, and computer-generated tuning capabilities. He was forced to etch his own design mantra in the back of his mind.
He wanted to give it the best of the best from a handling prospective, performance, and technology where he saw fit, but this work of art still must remain a solid minimalist scooter with elegant styling, panache, and class. As you will see, Gard succeeded in hiding much of his workmanship, so it takes a second, more in-depth look to appreciate.
Over the next couple of months, we will tear into every element of the KRGT-1 and explain each design notion and production challenge. This first report will delve into the seemingly stock S&S 124-inch engine configuration, and the all-special construction Baker transmission configuration.
He picked the S&S 124 for its monster performance configuration and the history with S&S as the dominant engine and performance manufacturer in our industry. Plus he wanted a solid warranty program. One of Gard’s design challenges was to build this motorcycle to be almost 4 inches narrower than stock for comfort and handling. One of his first challenges was to aim the intake manifold directly up, so there would be no throttle body or air cleaner hanging off the right side of the motorcycle.
Without much trouble, he turned the intake manifold nearly due north, but that’s where the minor elements ended. He worked with K&N for months on the position of the air cleaner, the capacity, the mounting (rubber-mounted engine), the eliminated frame member, the design of the tanks to afford enough space for the air cleaner, yet maintain at least a 5-gallon fuel capacity and more air capacity than required by S&S for the monster engine.
It cost over $5000 to design just the rubber bellows, mounting boot connecting the S&S throttle body to the K&N filter canister while allowing the engine to move. After 20 different configurations and adjustments, the final air box gave the engine 40 percent more air capacity than recommended by the S&S factory.
One of the fuel cells acts as an actual stress frame member. Each set of gas tanks takes 60 hours of CNC machining, but when complete take only one weld and holds 5.3 gallons of gas.
Several materials for the plates holding the air cleaner in place were considered, including carbon fiber, machined from aluminum, and stampings. After exhaustive research, Gard found a company capable of low number-run stampings in steel. Another hurtle satisfied. Then he faced throttle cable rerouting and manufacturing a new throttle cable wheel on the throttle body, which required heat-treating.
Gard wanted to add an appearance-enhancing element to the engine. Unlike Harley-Davidson, S&S engines cam covers function. Gard designed and worked with S&S to change the external appearance of the cam cover, but wanted S&S to manufacture it, not to infringe on the existing warranty.
Harley-Davidson fuel pumps are installed through a door in the top of the gas tank. Gard didn’t want a massive hole in the top of the gas tank, so he researched if the pump could be mounted on an inside wall. It could, as long as it was submerged in fuel some of the time for cooling. Also, moving the pump to the inside helped with the design to keep the bike as narrow as possible. He moved the thermistor switch, and set the fuel pick-up and filter in the best possible location in the tank.
One of his constant goals included making each element simpler, which entailed making everything contain multiple functions, and it made each component more difficult to manufacture. Here’s an example:
The air feeds directly to the air cleaner from the front of the billet gas tanks. The airflow is enhanced with two shapely CNC-machined cowlings behind the headlight on the front end. They added an artistic metallic synergistic connection to the forks, plus functioned as the headlight mounts.
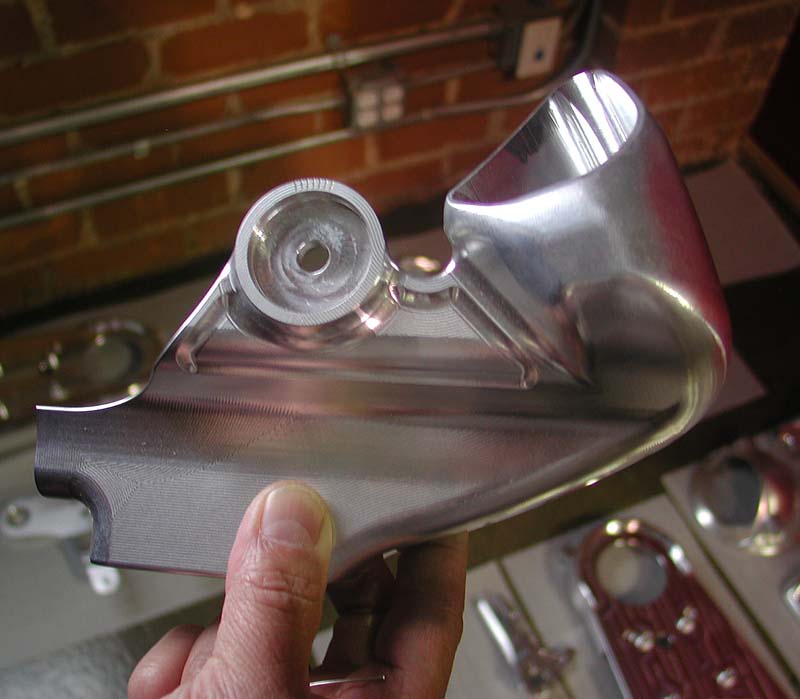
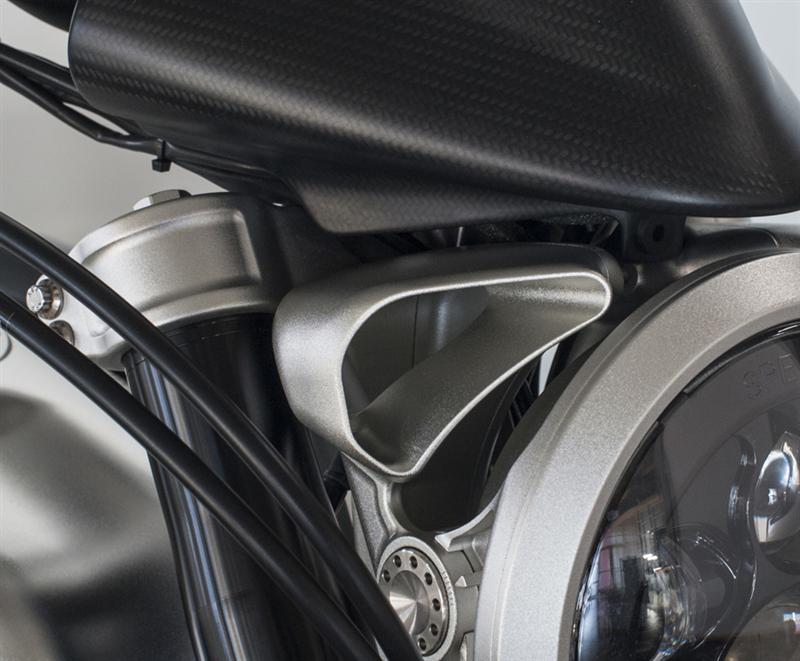
Gard also purchased aluminum machined AB Tech pushrod covers and had them delivered to S&S for install. The engines can be ordered in two different finishes. Gard requested three different parts to be raw machined, from S&S and not polished or plated. They include his cam cover design, which forced Gard to pay for a separate S&S QC process, oil filter mounts, and lifter blocks.
I will attempt to explain the transmission modifications, but bet I’ll miss something. Gard started with the notion of a solid Twin Cam unit philosophy, but in a Softail configuration. He went to Bert Baker, who recently designed a modular transmission case system to allow builders serious transmission mounting variations. This was the perfect start for Gard.
Gard designed his own oil tank system, which performed multiple functions, made the bike easier to service, narrower, and have a larger oil capacity than stock H-Ds and even surpassed S&S requirements of 3.5-4 quarts. The KRGT-1 holds over four quarts, but there’s much more.
First, the forward portion of the oil bag would act as an integral driveline component mounting the transmission to the engine. Gard designed it with a sight glass for ease of oil capacity measuring. The oil bag is mounted directly to the engine and eliminates the use of any feed line. Gard machined in guides so returning oil never comes in contact with the oil feed side for maximum cooling, and eliminating foaming oil from feeding back into the engine.
He designed the oil bag so the oil can be removed with the bike on the side stand and virtually every drop of oil can be drained and replaced with fresh lubricants.
The return line to the oil bag is just over an inch long for the shortest possible line for less chances of failure. The oil containment system does not hang below the frame. Plus all the drain plugs use the same Allen wrench for service ease.
One special tool is required and supplied by Arch for the swingarm axle nuts, which connect the frame and swingarm to the transmission. The same tool works on the steering neck.
The trans main shaft is shortened at the Baker factory by almost two inches, which narrows the primary system and clutch, again to narrow the bike’s overall platform and lift the clutch, primary and rear chain for handling.
The clutch is operated by a hydraulic slave system, which is widely used, but modified by Arch to use a Baker wafer, throw-out bearing, piston, and pushrod, and then Gard’s team designed the sprocket support, which works with the right-side chain guard.
Are you beginning to recognize the vast amount of work, design, thought, resources, and time put into every element of this machine? Believe me, after I sat on one and discussed each element with Gard, I scrapped my notion of buying a house in Deadwood and considered ordering a KRGT-1.
We have just scratched the surface. I’ll be back in a couple of weeks with the next chapter, taking us into the inner working of the Arch motorcycle design temple in Los Angeles.
Don’t miss chapter 2: http://www.bikernet.com/pages/The_Magnificent_ARCH_Motorcycle_part_2.aspx