We found ourselves lost in the Holidays, but fortunately Kevin Kahl returned from Kansas after a surgery to relieve the pain in his legs. Most of my homework assignments were completed. He didn’t recuperate for a couple of days after the long drive but immediately came to the shop with his compact car packed with tools.
I helped him unload the tube bender, mandrels and a small Harbor Freight TIG welder. We went to work trying to determine whether we needed more rod and we did. I had a TIG welder and a tank full of Argon gas, but we considered another, smaller tank.
He needed to recuperate, so off he went to his swaying boat. Besides all the welding shops were closed on Saturday and H-D dealerships were closed on Mondays. It was a sinister plot to slow us down.
A couple of days passed and Kevin felt up for action. We made runs to True Value Hardware, Matheson Welding, and Phillips Steel the next Friday. They were having their Christmas party. Their boss had told me his Jesse James stories, but I will leave them in the dust of the past. The staff Christmas party wound down and the shop closed at noon. We arrived at 3:00, but a couple of staff members, one who worked there for 23 years, held on and helped us with some tubing chunks we needed. It wasn’t easy but we found them.
We cut away more sections of the Paughco touring frame. I installed the JIMS Fat 5 Transmission, with Custom Cycle Engineering spherical bearings, and dug the JIMS 135-inch Twin Cam out of its crate. It had been locked down for four years. It was time to feel the sun and progress.
Kevin is a confident and experienced frame builder. I was sketchy about cutting too much of the frame away. I didn’t want to lose my foundation before I was confident in the outcome.
I also needed an oil pan and started to scramble. I want to go back to the Evo days when shit was simple. There are even several versions of the oil pan now with the new M-8. The crew at JIMS didn’t know what transmission case I had. It took some digging and I need to learn to look for part numbers. They answer everything. I needed a 99-05 oil pan and Mike O’Brien had one. He also had the 39 mm front-end axle we needed for Frankie’s FXR. I scored and jammed home.
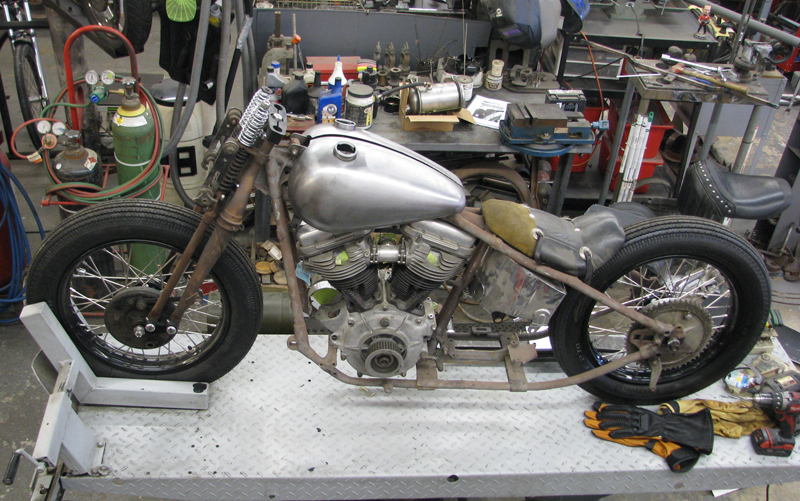
I was also cleaning up shop stuff and thinking about Dr. Hamster’s bobber. I moved the Paughco bars off the 1928 Shovelhead and made studs to hold them on the Panhead bobber project.
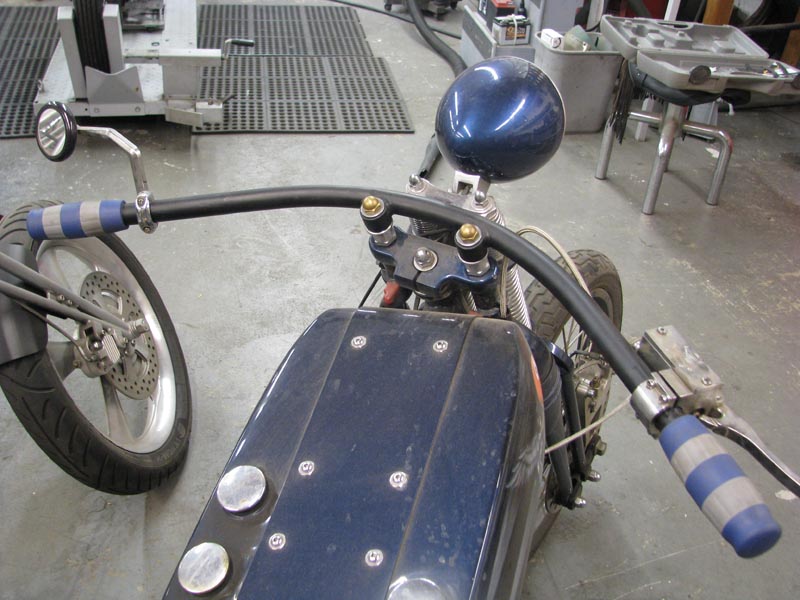
I had the oil pan I needed and cleaned the shit outta it before installing it. JIMS is now making a high capacity oil tank, but I’m not sure we need it. We will see. With the chain hoist, we installed the JIMS engine in place with a Paughco heavy-duty front motor mount system and plate.
I’m now asking lots of late model questions and working with BDL on a primary drive and clutch system. I also need some parts and an offset sprocket for the transmission.
We need these pieces in place to determine Torpedo body fitment. We are trying like hell to stuff all the elements in the smallest body tank available. So far so good.
One of our first missions was to level the lift, and then level the frame with the driveline in place, and finally level the belly tank bottom. Kevin worked on that, while I worked on shortening the swingarm an inch. We needed more flexibility inside the body. We finally cut the last chunks of the Paughco exhaust pipe out of the body of the belly tank.
We took the front axle and frame plate out and I trimmed it some more, while Kevin started to bend frame members. He also didn’t like the dragster seat pan I bought. It was still too wide and tall. He wanted to build a new one. Kent had narrowed the one I bought, but it could be even narrower.
We looked hard at the seat position and how close we could get to the engine.
In the meantime, Jeremiah constantly complained about his rattling D&D carbon fiber muffler. The aluminum rivets started to fail. He asked for a new muffler but the boss wouldn’t talk to him. He added new and additional rivets, but that only lasted a while. The clamp cracked and he welded it. I suggested we could fix it.
He tried one more time with D&D but the service guy didn’t know anything about Dynas and offered to talk to the boss, but the boss never responded. The service guy admitted that the baffles were popping loose, which added to the muffler failures.
We told him to go to Phillips steel and buy a chunk of 4-inch tubing, thin wall, like 16-gauge and make the muffler solid again. He did and finally tore the muffler apart. The baffle mesh holding the glass packed material was tacked to the tapered sleeve and all the tacks were busted. I told him to shit-can the glass pack material, but he saved every little burnt piece and put it back after I tacked the mesh back into place.
Kevin TIG welded the tube in place and re-welded the clamp, and off Jeremiah went to the store to buy VHS heat paint.
As Christmas approached, Kevin started coming to the shop every other day at noon. He needed to rest and heal. We made wooden guides to hold the body level and I made a frame jig, with his guidance, to hold the frame level. He started to bend tubing.
On Xmas day, Kevin felt up for action. The Redhead and a gang of wharf rats had made cookies and cooked for a couple of days. My son and grandson came over, and I couldn’t find a football game on television, so we were kicking back but itchin’ for action.
Kevin came over and tacked some of his frame rails. We installed the front section, and we felt compelled to see if he could fit inside.
That’s when we ran into measuring issues, but after measuring and re-taping several times, we got close. I hole-saw-drilled the corners and cut the fiberglass with a jigsaw.
What a kick. We made a thick, cardboard seat pieces and I dug out a brand new XRV Harley full-faced helmet. Kevin, who is about 5’10” fit with room to spare.
Next, we will bend roll bars after studying the FIM specs manual, which is sorta vague, but I’m also in constant touch with Denis Manning, the master of streamliners. Hang on to the next report.
JIM’S Machine
Hot Rod Underground
Paughco
Strictly Hawgs
MetalSport Wheels