Bikernet East – The Rolling Chassis
By Robin Technologies |
The competition has changed, expanded. Can home-built choppers fly to Sturgis? Can Jesse James build a chop and actually ride it, with all his tools, mechanics, equipment, lathes, milling machines, and money? Can Billy Lane from Choppers Inc. build a bike by hand while wanton women dance seductively around him daily in him Maimi based studio. Can two crazed fools from Bikernet build two chops in a small San Pedro garage with limited tools and no cash and make it to the Badlands? Another builder has entered the competition, Japanese Jay from the local motorcycle shop, Station 34 in San Pedro. He’s building a rat Shovelhead, I think. ![]()
While we’re damned low on time and still trying to recover property from West Coast Choppers, we’ve decided to get together two running choppers and ride them proudly to Sturgis. We’ve called in all our heavy clients, folks like RevTech, Weerd Bros., and Custom Chrome, Baker, Paughco frames, Headwinds, Harley-Davidson, and put them abreast of our situation and we’re receiving outstanding support as always. Our new goal for the Chop-off 2000, is to race to Sturgis, with back tire fires and heads full of fresh Jack on our custom, hand-built machines. Bandit and I are going back to our roots, building our own scoots, with our own hands, the way we like ’em, fast and simple, no bullshit, no backing out. These will be independence choppers, American-style, no bullshit politics, attitude, downtime, and loss of parts. We just want to ride. As for the vote to see which chopper the world of bikers like best? I’ll still kick Bandit’s sorry ass from here to Lead and back, I’ll have his woman, his whiskey, and he’ll have a view of my back tire all the way. May the best badass win. See you in Sturgis. Saddle up and ride. My Bandit-smashing nightmare is well under way and I’ve employed the assistance of the talented, albeit nuts, Chinaman and the master of horsepower, Wrench. At the moment, I’m way ahead of Bandit. Nothing new there. Billy Lane is hard at it. Jay’s engine is in the frame, and Jesse James, well, he’s in Europe being interviewed by the Pope. In just a few days we’re already working with a rolling chassis. The new horse is sitting on some good-looking chromed Thunderstar wheels from our bros at Harley-Davidson, 21 inches up front and 16 in the back. We chose Performance Machine brakes to stop the monster, once I get to Sturgis. Until then, they’ll get little if any use, since it’s a race. We have the Paughco frame resurrected from the Bandit II, plus a Paughco oil bag. We were going to use the rear axle and oil bag from Bandit’s other chopper, but West Coast Choppers seemed to have somehow misplaced them. The tank will be a Russ Tom Harley-Davidson/Seattle custom stretch. This is where I’ll keep the fuel that Bandit will breathe the fumes from as we streak north. For a front end, I’m going to use a Harley-Davidson narrow glide, which we’re planning to widen with new triple tits. Joel at Headwinds is the man behind the lighthouse-powerful headlamp system, to light my way. I know I can ride from L.A. to Sturgis straight through, because I’ve done it before, but I expect a great deal of whining and crying from the very soft-assed Bandit. The engine will be a beautiful new RevTech 88-inch CAD designed, fire-breathing whip-lashing, get-the-hell-out-of-my-way twin. The whole crew at Bikernet is pumped to test out one of these killer-tech twins as it’s the first RevTech we’ve gotten to try and we’ve got high hopes for her. The engine came complete with a RevTech carb, increased cooling fin surfaces, no head gasket, never-fail O-rings, high-performance, computer-controlled ignition, and it fits the custom frame with no modifications needed—we hope. Just bolt and scream, which is how we like it. And by the way, if you’re wishing you could get one of these fine RevTech monsters in a 100-inch, you can. To transfer all this power to the flypaper-sticky Avon in the back, we’ll be employing a Baker 6-speed tranny. I’ve not yet had the pleasure of running a Baker 6, but Bandit assures me they are as smooth and stout as a bottle of 20-year-old Jack. Can’t wait to marry it to the RevTech and watch them have some of the honeymoon torque sex. And Avon Tires, of course, will be providing the glue to keep me on the road all the way into South Dakota. If you’ve never owned a set of Avons, you’re missing out. |
Bikernet West – The Chop Lives
By Robin Technologies |
![]()
The speedometer arrived from the Dallas Easyriders with a little over 24 hours to kick-off. The cable was coiled in a cardboard box waiting and the drive unit was already bolted to the front wheel. Unfortunately, the cable was the wrong unit and a hunt began for the proper cap. A call from Phil, the Hamster painter, encouraged Bandit to send a young lady to see Jim at Drag Bike Engineering. He had the cable and, at three in the morning, Bandit was installing it. We will also follow this series with an article on the Weerd Bros. front ends. This is a ball-milled wide glide that, depending on what ruler you use, is approximately 14-over. According to Bandit, who is in the garage packing as I hit the keys, the front end is light handling with narrowed flat track bars due to the six degrees of additional rake. Even with an overall 44 degrees of rake, the front sliders are smooth and work effortlessly. Although this is a European-built front end with metric Allen head fasteners, it’s highly adjustable with removable fender mounts and brake caliper mounts that can be installed on both lowers or either one or none for the hardcore muthas.
![]() Bandit’s about to take his Blue Flame for a final test ride with his bed roll centered over the Weerd Bros. front end. Yesterday, during the heat of the harbor day, a small Fed Ex package arrived. It was from C.J., the old biker engraver. Inside was a Bikernet engraved point cover, a “Bandit” money clip, and a flamed mag light. When more photography is revealed of the Blue Flame, the Bikernet logo with our babe mascot will be revealed in all her nearly nude glory. Damn, when she walks into the sagging headquarters, everything stops, as if a contact high permeated the garage. In a daze we watch her every fluid move. By reader demand we will post a photograph of the lavish facility in the next couple of weeks.
![]() The bastard is rolling out in the wee hours of the morning and the race will be on for the Badlands. Agent Zebra will be heading out of Miami at noon on Saturday heading north and into Tennessee, as Bandit heads east across the border into Arizona where he will relieve his helmet of duty and ride on in freedom toward Phoenix.
![]() More reports are forthcoming. Live from the Bikernet World Headquarters in San Pedro, California. This is Renegade. Over and out.
|
Bikernet West – Electronics in a Weekend
By Robin Technologies |
![]()
Wiring is the nemesis of man, the puzzle of the best builders, the hornet’s nest of breakdown treachery. Bandit sat for hours drawing a wiring schematic for Agent Zebra’s Softail, only to rip it to shreds and toss it in the trash. He made lists while Sin Wu brewed strong coffee and baked peanut butter cookies. Bandit barked and growled for a couple of days with each run to the marine store for connectors, to the electronics store for switches, to the Custom Chrome catalog for components. The same formula fit his own West Coast entry in the Sturgis Bikernet Chop-Off. We knew as soon as he mentioned that the bike was ready to wire, that we should pack our shit and leave. We took the case of Jack fifths, the girls, and checked into the nearest fleabag motel. While we sat around the stanky pool and partied, Bandit thought about each wire, each connection, and each component. His mentor, Giggie from Compu-Fire, was his only sounding board and the only sonuvabitch big enough to snap back when Bandit growled about wire gauge or lost connectors. He wired the bike entirely with 14-guage wires. The only other sizes used were for the battery cables (stock units) and the wire that ran from the battery to the ignition switch (12-guage). Even when the sexually starved statuesque Asian roamed into the garage with cocktails, adorned in a sheer negligee, she was ordered back to the headquarters. Soon she found another plaything to keep her occupied, but that’s another story. Wiring, in the big guy’s mind, is a process of understanding what is happening with each component, where each component is located, watching for the safety of each wire, keeping the bike sanitary, and organizing each group of wires. Each wire is covered with shrink tubing, each connector supported with additional shrink tubing. Each bike had a minimum of wires carefully placed. Each bike had a minimum of components to keep the wiring process uncomplicated or enhance the reliability of the machine. No turn signals, no handlebar controls, and no micro switches. He used only millspec (military specifications) or marine quality switches. Vibration is a killer on motorcycles and much the same on boats, in addition to the moisture considerations. One additional component made wiring simple and risk free, the Custom Cycle Engineering starter mounted mechanical switch. (Check the article here in the Garage.) This unit eliminated the starter button, the starter relay, and all the associated wires. You must make sure you will have access to the switch, which is mounted directly on the starter, under the oil bag, (Photo 2) which can easily be interfered with by the position of the exhaust pipes.
![]() Photo 2
The concept is that you physically push the solenoid into contact with the starter gears and electrically engage the starter. We chose a Compu-Fire starter from Custom Chrome to kick this 98-inch monster to life. The key thing on fucking up starter motor installation is over tightening the brass lug wire fitting. It may turn the connection on the inside of the starter and ruin the contacts. Compu-Fire has designed a new line of starters which feature 6:1 gear reduction (Photo 3) and a 6-pole permanent magnet field to eliminate starter stall-out.
![]() Photo 3
These units deliver maximum cranking torque without overloading the battery. They also eliminate starting problems on fuel injected bikes. Only two switches were used and one 30-amp H-D (common at any electronic or auto parts store) circuit breaker. One on-off marine toggle for the ignition, which energized the Compu-Fire single-fire ignition system, the hydraulic brake switch, and the taillight. Since all the sweet parts like handlebar controls, foot controls, mirror, and taillight were Joker Machine components, he was in luck. Joker works the brake light switch into the body of forward controls, which eliminated the bulky hydraulic switch, the junction, and a two-piece rear brake line. Another wire went to the other switch, an on-off-on switch for the headlight (high/low beam). Two wires were run from it to the headlight. Daytec does a beautiful job of running guide tubes in the frame to hide the wires. Initially, if you chose to do so when ordering a Daytec frame, you can have two inserts welded to the frame seat post rail for electric box mounting. We ordered the certs for this frame but decided that with the simplified wiring program we could stuff switches and all the wires into the structure of the top motor mount. This was Giggie’s suggestion and Bandit readily agreed (a miracle). With careful measurements the switch holes were drilled with several bits until a 1/2-inch hole for each switch was attained. The only guide hole that the frame was missing was one for the headlight wires, but two wires were run through shrink tubing to the headlight and through a 5/16 hole in the motor mount. One wire was run from one side of the ignition switch to the circuit breaker, another, the 12-guage wire ran to the battery. From the circuit breaker a wire ran to the taillight down another guide hole along with the brake switch wire. From the brake switch another wire ran to the taillight, brake element. We also used a Compu-Fire regulator, which mounted to the front of the motor. One wire ran from the regulator back to the hot lead on the Compu-Fire starter motor. Bandit used the excess 12-guage wire to run from the battery to the hot side of the ignition switch. Giggie recommends that you use crimpers designed for Duetch connectors for a solid, vibration-handling connection. Bandit used water resistant connectors from a West Marine store. After some 20 hours in the garage, Bandit was finally lured into a well warmed King size bed by Sin Wu and her girlfriend Coral as the sun came up, but at that point the bike was ready to be fired to life. The question was, could Bandit be fired to life? –Wrench
|
Bikernet West – Amazing Progress
By Robin Technologies |
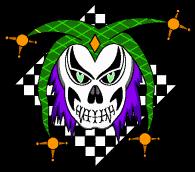
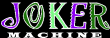
Late into the evening, Bandit, Nuut Boy, and my wonderfully-knowledgeable- self hammer, weld, bolt, space, and tear our beards out moving forward on Bandit’s rigid. The Weerd Bros front end is in place with the Roadwings 21-inch, 40-spoke wheel. The rear is a 180-18, both with Avon tires. The frame is stretched 6 inches up and 2 out. The trees on the clean front end are raked 6 degrees (photo 1). The S&S 98-inch stroker is bolted in place as is the 5-speed Sputhe trans.
We set the engine and tranny in place and then found a scrap inner primary to line everything up. With the stock 32-tooth pulley on the tranny, we put a 70-tooth narrow belt pulley from Harley on the back with a 134-tooth belt. It was too long. We tried to get a hold of the frame manufacturer for some guidance, but they wouldn’t get back to us, so we had to wing it. We had another option. Run a Harley Thunderstar 65-tooth wide pulley for taller gearing for the trip. We picked up a 130-tooth belt and it fit like a glove. The pulley on the wheel also felt good and afforded us plenty of tire clearance with the offset frame. With the rear wheel in the center of the adjustment axle slot and the tire centered in the frame, it was time to fit the rear fender. The rear fender was a Milwaukee Iron job, which took some time to mount up. First we centered the tire in the frame. Ignore the offset rear leg. Center it in the frame using the cross member behind the seat as a guide. We centered it then strapped chunks of 3/4-inch board (photo2) to the tire with green paint masking (low tack) tape.
Then we slipped the fender in place after the rear belt was adjusted. Again, make sure the fender is centered over the tire. The fender didn’t contour the tire completely, so you must decide what area you want contoured. We decided on the top, most visible area. Make sure the slot for the belt rides a good two inches above the belt and at least a 1/4-inch from the inside.
Then the Samson exhaust was removed from the box. They don’t build exhaust for rigids so natch the Dyna exhaust didn’t fit, since with rubbermount frames the engine sets higher in the chassis. They were also over 10 inches different in length. For performance we cut them to a more equal length (photo 4), about 27 inches.
We also ordered baffles and we cut them (guessing) to give the 2 1/4-inch exhaust some back pressure. Then we mounted them. The front pipe was way too close to the deck, so we cut 2 inches out of it and gas welded the pipe back together. During this process we were able to bring the pipe into closer alignment with the rear exhaust. None of the brackets would work so the madman with a torch went to work building brackets. The seat was also a trick. Bandit purchased an old cop solo with the plunger t-bar from 34th Station, a bike restoration shop on Pacific. After much contemplation he decided that he had to mount springs under the seat for something of a ride, but springs were a problem. He had some success with a set of valve springs on his dicey Knucklehead, “Made all the difference in the world,” Bandit said while pondering the ride. But the old Bates tapered 2- or 3-inch springs generally bottom out under any load. Then a bolt of lightening hit while attending the Harley-Davidson new model presentation to the motorcycling press. In addition to all the new models for 2001, they were showing off their new police bike, which had a sprung seat. Bandit drew the 4-inch crescent wrench he’s been carrying in his pocket for the last 32 years and began to take the springs off the new 2001 model. Seven factory executives struggled to pull him off the new demo bike. “But wait, guys. I just want to borrow ’em,” he screamed, pulling on his crescent wrench. Back at the top-secret massive 50-square-foot Bikernet testing facility, the gang was taking more measurements. It was determined that if he could narrow the seat one inch, all would fit, and the seat spring studs would line up with the center of the frame tubes. A call was made to California Harley-Davidson to order the springs, ASAP. Nuut Boy went to work stripping the seat to just the pan. With a die-grinder he cut a 1-inch strip out of the center of the pan then laid enough brazing rod into the jagged gap to sink a battleship. We decided not to use the old t-bar and with some standard 3/8-inch round stock, fashioned a triangle brace under the seat for support.
|
Bikernet West – Mikuni Carburators to the Rescue
By Robin Technologies |
With Sturgis 2000 looming over Bandit’shead we’ve been firing away at the getting the job done. Bikernet Eastmachine was well out in front in the competition when we wheeled the Agent’slow slung Softail onto a slick Gold Rush semi and said goodbye as the rig,packed with Ultra machines, Big Dogs and customs from the west coast, headedeast. Eddie Trotta from Thunder Design was more than happy to have thebike unpacked in his shop in Fort Lauderdale, so he could point a fingerat Bandit’s creation for Agent Zebra and bust out laughing, “You expectto ride that to Sturgis?” he said rolling on the floor of his shop. Weweren’t discouraged and neither was Bandit as we strapped the road wingswheels, the Weerd Brothers Front end on the Daytec rigid and went to work.
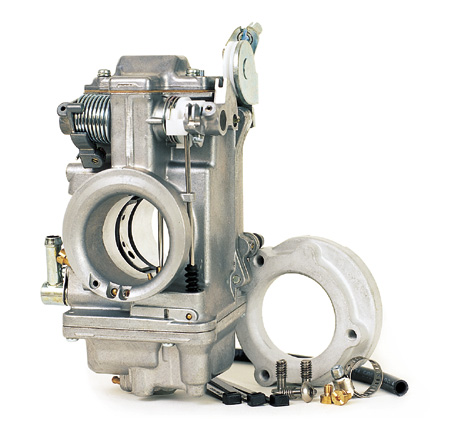
This was no ordinary installation. First,time was a factor, second it’s no normal, stock carburetor swap. The 98-inchS&S motor offered taller cylinders and improper intake manifold fitment.The stock Super E S&S manifold was too big for the 42 mm polished MikuniCarburetor. Stock manifolds shove the carb out too far and aren’t wideenough for the tall S&S cylinders so a quick call was made to JamesSimonelli of S&S who rushed the correct manifold to Mikuni. Lee alsowanted to explore an American Iron Horse manifold available for their customswhich pull the carb in closer to the engine and “L.T.” or James Littleof American Iron Horse moved equally fast and the parts were in hand inone day. The next hurtle: The cables. A call went out to Xavier at BarnettCables who turned about a set of Mikuni compatible cables which are setup the same as stock H-D cables, but cut to Bryan’s specifications forthe job. They also arrived in time.
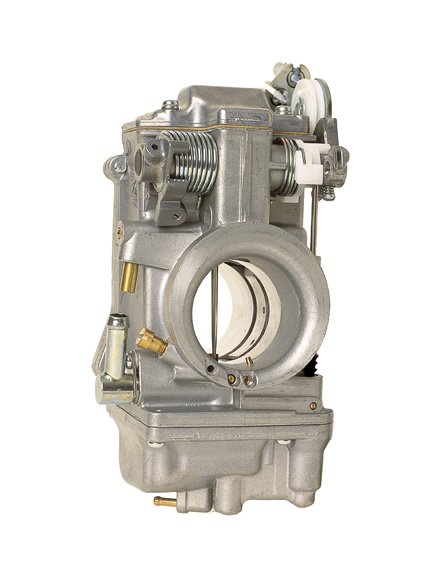
Bryan pointed out an adjustment on theleft side of the carb as you face it, a main jet air adjustment. He toldme to inform Bandit to turn it out a half turn in Denver for more compatiblerunning in altitudes. The bike immediately fired to life for the firsttime. Two weeks to go.
Bikernet West – The Blue Bomb Explodes
By Robin Technologies |
In a mad rush to build and break-in a monster Simms built S&S motor rigid before the long haul to Sturgis, Bandit makes an abrupt move. At the final hour he decided to take the frame to a local powder coater in Orange County who is capable of layering on a two or three stage powder coating process. After much deliberation with the entire staff, the decision to attempt a match between the frame and sheet metal was made. Nuutboy pointed out that the powder coated frame would be more resilient to wear and tear. Snake, in a rare lucid moment, noted that we wouldn’t be able to cover Bandit’s crappy welds with bondo, because powder coating is baked at such a high temperature that it melts the bondo. Overnight shipping would have been less than $100 to truck the delicate metal parts to Sacramento for Harold Pontarelli to paint. In contrast if we had the frame powder coated locally, we could have it back in three days and be working on the bike. On top of the concern for the various components being shipped, damaged, lost or dented- which would really set things back- there was the overall concern of time. We needed to be building a bike. Some of the Bikernet gang like Renegade, who was pissed that we weren’t working on his bike (he won’t ever let any of our mitts near it), Snake, Nuutboy, and my most informed self, huddled around a large bottle of Jack and a small bonfire in the junkyard rubble behind the Bikernet World Headquarters in San Pedro, California to take a vote. Bandit was somewhere inside the luxurious offices chasing a new female recruit, an oriental girl, whom he had failed to introduce to the rest of us. He was building a deep-seated resentment amongst the staff. “I say, fuck that bastard, let’s burn his frame,” Renegade said taking a hit on the freshly opened bottle of Tennessee champaign. “You say that every day,” Snake mumbled filling his large rusting flask with the bottle while guzzling the last remaining can of Bud from his 12 pack. No one else drinks beer. “We’re supposed to be deciding whether to ship or powder coat,” Nuutboy said standing on the edge of the fire holding a wad of tools in each hand. He doesn’t drink, but smokes joints incessantly and fidgets constantly. “We’re running out of time.” The evening went south from there. More riders showed up, Japanese Jay from the antique bike shop, 34th Station, came by. Chris from Hill Products wandered in and filled his boot flask, put in his two-cents worth and moved on. Nuutboy and I pondered the question until we heard the giggling stop from inside the Headquarters and the large thump of boots against rickety floors. Bandit appeared bleary eyed but content and placed his vote. If we could get a sample of the paint color on a separate rod we could ship it to Harold for a paint match. We went to work. We delivered the frame to Primo Powder Coating in Huntington Beach, California (714) 596-4242. They had a sample of the metallic blue we were after, waiting for us. We immediately took that sample to a mail box joint and shipped it overnight. The tank and fenders were carefully boxed up and shipped to Harold via UPS second day air. Then we delivered the chrome to Orange County Plating (714) 532-4610 where they immediately photograph the items and enter them into a computer. In four days we had the frame and chrome back and were in the process of building the bike. Harold moved on the paint quickly, but even with a simple flame job on the table, a couple of days was spent at the body shop, then paint prep and primer, then undercoats of silver base were followed by a matching blue candy with a hint of pearl, then drying time before the graphics could be laid out. Two weeks have slipped past, but the progress with the frame in hand is considerable. The engine and tranny are bolted in. The Weerd brothers front end is in place. The wheels and P.M. brakes are in place along with the Samson exhaust system. Wiring will begin this weekend. Then with the BDL 3-inch primary belt in place we will haul the bike to Mikuni for a Carb and go for a ride. Here’s a sample of the paint from Vacaville, California near Sacramento.
![]() –Wrench
|
Bikernet West Bogged Down In Pheonix
By Robin Technologies |
I knew it! The sonuvabitch couldn’t make it to the Badlands and back on that piece of shit. I knew it! The way Bandit mounted that tank was fucked from the beginning.
![]() I told him. Nuutboy told him. Harold Pontarelli told him. Shit, his 78-year-old mother told him. Did the big bastard listen? Nooo. So it jumped off the frame in Aspen, Colo., and landed in his lap.
![]() Yeah, they welded it up in Aspen with the help of Randy Aron from Cycle Visions in San Diego, and he limped into Sturgis, rode around the Badlands for the week and then the scoot was kidnapped from him by someone who knows what the fuck he’s doing, namely Paul Yaffe from Paul Yaffe Originals in Phoenix. Paul is working with Kyle of Independent Tanks, who hand makes steel tanks from heavy 16-gauge material. It’s about time someone grabbed that bike before it exploded into flames and scorched the ornery sonuvabitch.
![]() So we sent that fly-bitten claybrain to Phoenix for a welding lesson and instructions on how to properly mount a gas tank. If he wasn’t such a hasty-witted old fool, he would have put the bike together right the first time.
![]() Here are shots of the existing piece of shit with the new tanks recommended by Paul, who builds some of the most innovative bikes on the planet.
![]()
![]() Paul’s philosophy is to manufacture enough custom components to allow his customers to build something without doing a piece-meal job. “Instead of buying fenders from me that don’t fit the other guys’ frame properly and then mount a gas tank from so and so, and nothing fits properly, I want to give the customer half a chance to build a world-class custom on his own.” Paul’s positioning himself, unlike Bandit, to afford customers with frames, plus the fenders, tanks and billet components to match. Paul began his operation building LED taillight products. Unlike the slob who runs this joint, Paul is a young man of vast energy and talent who could not contain himself building bikes with existing components. He began building his own fenders, air cleaners, frames, etc. The young upstart with the flaming red hair does share one notion with Bandit: “If you’re going to build a new full-custom for a customer, I want the bike to be a reliable runner, of the newest technology, or how can you call it a new bike?” So all of Paul’s bikes are built with Harley-Davidson Twin Cam drive lines. “I use as much Harley stuff as possible,” Paul said. “Plus the factory is going crazy building more new accessories all the time. The selection is growing by leaps and bounds.” Damn, if I told that lunkhead Bandit once, I told him a thousand times, it’s time to move away from the Evolution shit into the real world of Twin Cams. But that motley-minded minnow is still out in the garage trying to put two Mikuni’s carbs on his ’48 Panhead. If you want to check true customs, built to ride, check Paul’s site http://www.paulyaffeorginals.com Finally, after much consternation, Bandit succumbed to one of Paul’s buddies, Kyle at Independent Gas Tanks. These are new, contoured tanks and here’s how ya do it right.
![]() Kyle has been building his own line of steel gas tanks for two years. Prior to ’98, he built tanks for Roger Borget for three years and before that he built Porsche 911 race cars. He won’t get near aluminum. “Not with the engine sizes that are bouncing around in these frames,” Kyle said. None of his creations are Mig welded, either. “I only Tig weld my tanks. I’m glad to work with builders and make suggestions.
![]() I’ve hand-built over 1,000 tanks for Harleys, and if told the brand frame, the stretch and rake, I usually know which tank works the best. I can go with one of my six to eight standard styles, or I can design something out of this world. I can make a bike blend into the crowd or stand out anywhere.” Kyle’s tanks come with mounting straps. Don’t just weld ’em on and go, though. “Depending on how the tank is designed to mount will depend on if the existing tabs will work immediately or need to be modified,” Paul said. In this case, he created some spacers to allow the tank to set on the frame perfectly to capture the look the big bastard wanted, then he cut the tabs and tacked them to the frame. Next he removed the tank and solid tacked the tabs. He put the tank back on and made sure everything was in place. These tanks are handmade and not manufactured with a jig, so no two tanks are alike.
![]() The tabs were finish welded and the tanks shipped to Harold Pontarelli for repaint. Paul welds everything with Tig because the Argon gas shield makes for a more controlled burn. It gives him better penetration and a less brittle weld than a Mig. Kyle had one other recommendation. He often gets calls from brothers requesting tanks after they have taken their frame to the powdercoater. Don’t do that. Make sure all the sheet metal is prepped and assembled before any finish work is undertaken. In fact, many builders ride scoots without paint for a hundred miles or so before tearing down for paint. Saves the headache, and makes for a much tighter custom.
![]() Of course the whole operation must have a photo finish. Two days before the Love Ride, the tank is floating into town via Harold and eight H-D Performance troopers. The bike is rumbling in on the back of Paul Yaffe’s custom trailer. The two will meet with Bandit in Woodland Hills for the install and road test for the parties to come that weekend. He doesn’t deserve this scoot. It should be mine. –Renegade
|
|
1928 Shovelhead Project Part 1
By Robin Technologies |

In an effort to stay tuned with the rapidly growing and ever changing industry the staff of Bikernet began a project Shovelhead several years ago in conjunction with Randy Simpson of Milwaukee Iron and Arlen Ness. It’s been a strange road, but we’re now rolling closer to completion with the assistance of Rick Fairless of Dallas Easyriders and his ace fabricator Jim.

The project began with the purchase of a slightly destroyed Mexican Police bike from Arlen a couple of years ago. He had scored some 300 1984 Mexican cop bikes that had been ridden through several revolutions and costly rebellions. The bikes were shot at, dragged, bombed and ridden harder than any V-twins on the planet. When we first purchased the Shovel complete with police sirens and blinkers, we assumed foolishly that we would restore it to it’s original fighting condition. Arlen even hand picked our unit specifically with our goal in mind.
Well it’s one thing to dream of a restoration, but when the cast iron triple trees are broken, the frame is bent, all the sheet metal destroyed we took a step back and said, Help! We pulled the Engine and sent it to JIMS Machine for a rebuild along with the Transmission. With the cases replaced along with the barrels and heads and all the internals replaced, the engine was ready to rock once more. A similar concoction was mixed for the transmission and a couple of us dressed all in black and prepared to bury the chassis in a shallow grave in the desert outside of 29 Palms, California when the Editor of “Biker” pointed out that we had a valid pink slip. Dean, salivating, over the dying chassis took the entire unit and paid us handsomely for the paperwork. We suspect that he made a rocking chair out of the frame and wheels. During one of our weekly Bikernet meetings we discussed what to do with the Shovelhead drive train, and in the process we started discussing various options and some of the customs we respected the most. Several suggestions were thrust onto the rusting boardroom table. First Randy Simpson had volunteered to help us build an old time looking bike from the remnants of the ’84. We voted unanimously to pursue this avenue, since we had always been impressed with the workmanship and design Randy injected into his own 1928 Shovelhead projects, and he had a desire to create a simple chassis kit to build one of these puppies to market to the public. We agreed to help him promote the concept. We also all agreed that a gesture to the community of San Pedro was a necessity since several members of the staff had been arrested and the headquarters were constantly under surveillance, so we decided that Bikernet needed its own private San Pedro Police bike. How else could we crash the local parades. Randy is a persnickety builder who takes great pains to build quality parts for the market. Two years passed and he still didn’t have the frame built. He was obviously so successful with his growing line of fenders that his chassis concept was slipping onto the back burner. Arlen Ness was also taking giant strides to build a similar machine and if you picked up a recent Easyriders you would have seen the fruits of his labor in his 50/50 Shovelhead. In addition Chrome Specialties with the assistance of Chico in Southern California had recently completed a similar project around a Sportster (It’s called Trick and is featured on Bikernet right now). The competition was stiffening. Randy dropped out, and we moved ahead, and with some research we discovered that a number of reproduction parts are being built in Europe for early Harleys. Early like in 1915.
Devoted to successfully completing this project we picked up a rigid frame from Paughco. This is a standard scale Paughco Rigid for Shovelheads. From there our old part contact was Fred Lange in Santa Maria California. Fred informed us that a European group is remanufacturing 1915 springer front ends, flat track tanks, headlights, fenders and Fred was making appropriate sprung seats for these models. We were in business. We ordered the flat track tanks, the fender for a side car so it could be used for the front and the rear, a hand leathered seat and snuck out of the hills over looking Santa Barbara.
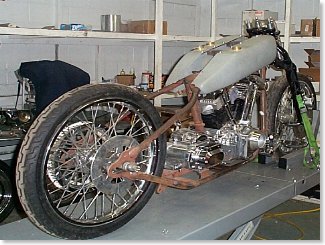
We had a Bad Boy front end, Wheels, etc. We’re in the market for some Custom Cycle Engineering lowering rockers. At that point we needed miscellaneous parts, pipes, etc., and we could get this puppy on the road. It was time to call in a favor. Rick Fairless had purchased the exclusive Bandit I Pat Kennedy Built bike from Bandit and part of the deal was parts and labor on a bike project in the future. It was time to call in that note. Then in a stroke of bad luck and good, Marty Ruthman decided to close his shop abruptly due to health problems and he had a massive sale.
–Wrench
Sturgis Shovel Part 9
By Robin Technologies |
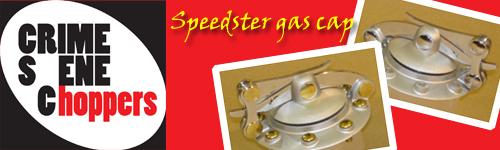
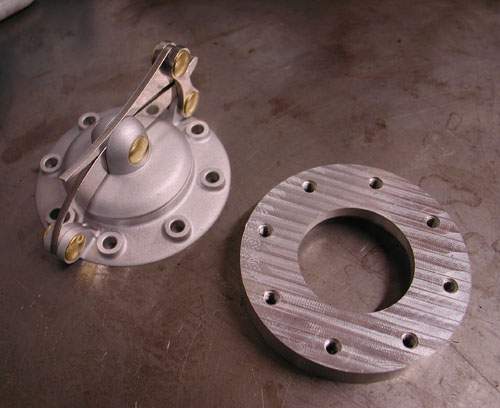
This is strange. I’m writing several Sturgis Chop Techs after I returned from Sturgis. I’ll try to remedy that in the future, but we were so damn busy trying to complete the bike and run Bikernet, we didn’t keep up on the techs. Many apologies.
This piece covers the installation of the hot Speedster cap from Crime Scene Choppers in the modified stock XR 750 factory tank. Later, you’ll discover, that this highly modified, strengthened and extra rubber mounted beast was my Sturgis nemesis. But more on that later.
We added rubber-mounted bungs to the back of the tank. I moved the petcock to the rear and filled the center for a 2.76-gallon gas capacity before it hit reserve. I doubt that it contained more than a quarter tank of reserve, so I’ll toss it a 3-gallon total gas capacity.

Oh, I need to thank Cyril Huze, who designs beautiful steel tanks for the opportunity to experience an aluminum tank once more. He suggested this classic for the Sturgis effort.
I’m not holding it against Cyril. He’s a master and I’m the bungler for attempting aluminum on a 93-inch rigid S&S hot rod. As you’ll see the vibration aspects came from several sources that I could have remedied. It’s all just a roll of the dice.
When I received the Speedster cap I drug the cap and tank down the street, about three doors, to Bill Hall’s Welding. He handles my aluminum welding, since I don’t have a TIG welding system. I’ve got the rest, but not TIG. I would highly suggest a TIG system for quality welding capacity and good looking welds. It’s much like welding with a torch, so you’re certain of the bead and depth of penetration.
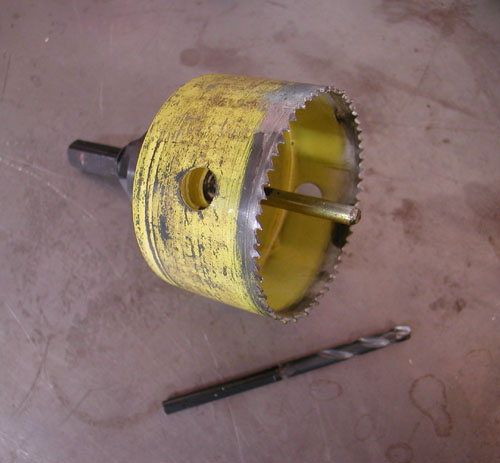
Bill’s a retired designer who enjoys welding and fuckin’ with his customers. “How are you going to drill the hole for the bung,” he asked?
I was thinking about die-grinders and files. I knew it would make a mess. Bill hooked me up with a 3-inch hole saw. He suggested that we hit a marine store for a tapered dowel pin (used for plugging holes in the leaking hulls).
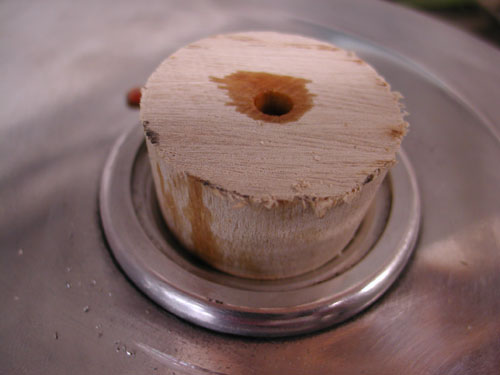
The key was to drill a perfectly centered ¼-inch hole to maintain a center approach to the cap bunghole. I drilled it and then ran the tapered wood dowel into the tank.
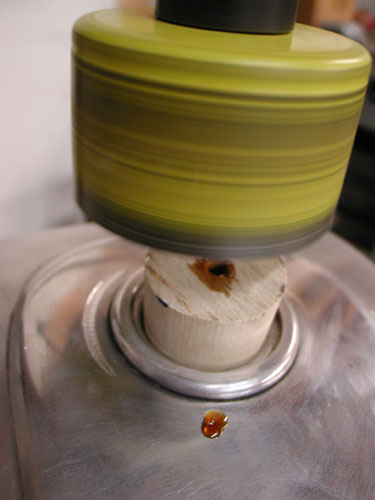
Then we set the tank on a pad on the drill press platform and lined up the hole saw. I used plenty of cutting oil on the edge of the blade and aluminum face to prevent the tank from snagging or catching. I knew how tender the surface of the tank was. We oiled the hole in the tapered wooden plug and carefully went to work. Bill’s formula worked like a charm.
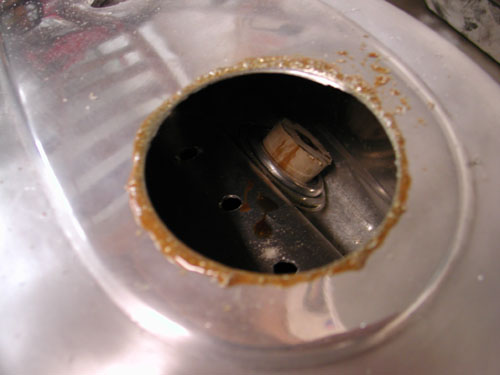
Next, we needed a tool to hold the Crime Scene Speedster bung in place. I grabbed a piece of strap, drilled a hole or two and mounted it with the supplied hardware, which was brass. You can order the cap with several styles of fasteners for your application.
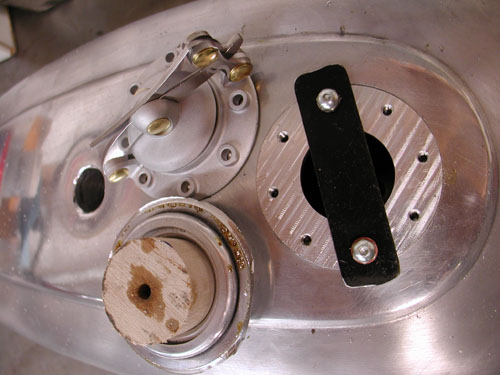
It was off to Bill’s for welding. While the gaping 3-inch hole was available I could have made a tapping tool and tapped out any imperfections in the tank walls. I dinged it way back in the beginning and never got around to fixing it. I left her be, as if it was the first injury and she needed to stay. I know it’s one of those wild superstitions.
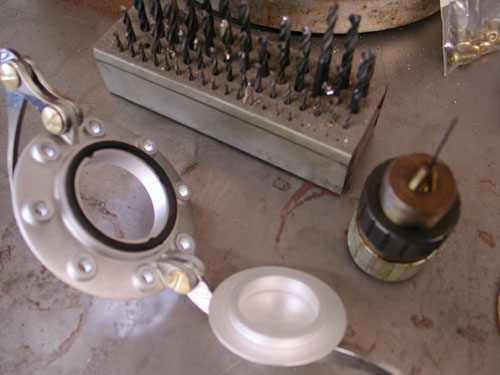
Okay, so during the “read the directions” phase, I noticed the bit about a non-vented tank. I would need to drill a tiny, cunt-hair hole in the cap of the tank. I discovered that I actually had such a tiny fuckin’ drill and dug it out. I had to find a chuck that pinched down to that size. Then I had a wise ass notion to drill the initial hole about 1/8 inch in diameter, since drilling with hair-thin bits causes easy drill bit breaks. The thinner the surface the better.
So, I initially drilled the inside of the cap with a 1/8-inch drill and drilled right through—Bummer. Ultimately I tapped the cap with a 10-32 then drilled the stainless Allen stud with the tiny drill bit. Then I screwed the stud into place and the job was finished.
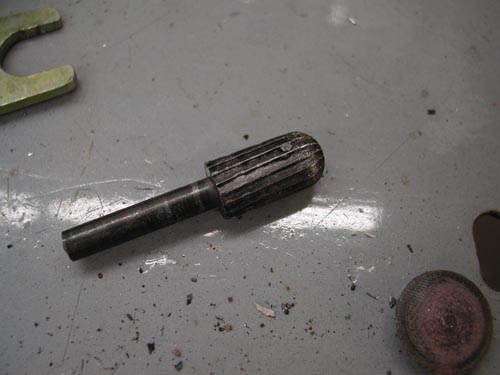
After Bill welded the bung into place it was my job to grind the welds down and ship the tank to Foremost Powder for a clear coat. I hit the big spots with a grinding tool. I tried my damnest to take only meat off the welds and not off the surrounding tanks surface.
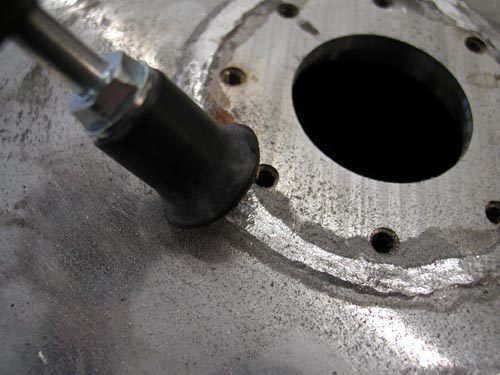
Next I used small emery discs to carve at the aluminum bead. I also smoothed some of the welds on the front of the tank where we filled the tunnel for additional gas capacity.

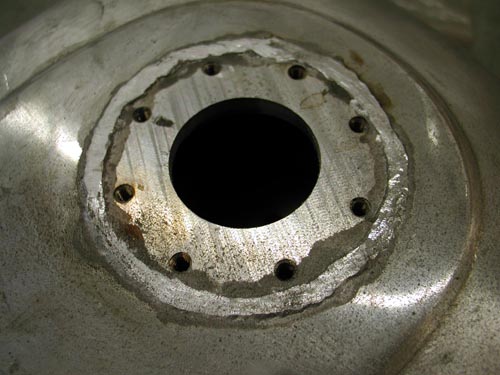
This shows the different grinding phases to reach a level that’s still strong with weld bead but handsome enough to live with. This was an interesting effort, since no bondo or thick urethane would be applied, covering a myriad of mistakes. This was the final stage before clear powder from Foremost in Gardenia, California.
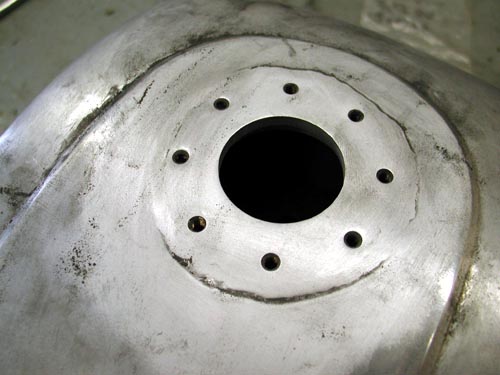
After this stage I polished the panels of the tank and hauled it off to the powder masters. There’s one other process I need to explain. I made every effort to clean the tank of debris and shavings. I also made sure to run a gas filter. I still had problems, which I will explain in my Sturgis Saga. They were easily remedied through Lee Chaffin at Mikuni. Just needed to dial the right number.
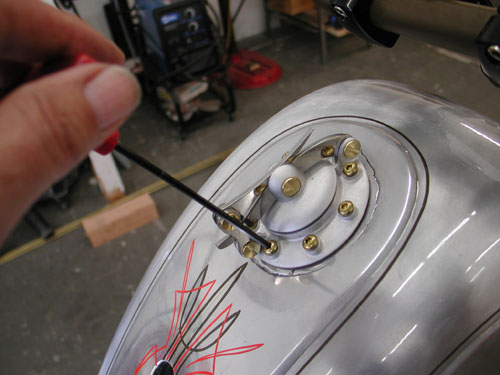
This shot was taken after powder and pin striping when I installed the gasket, decided which direction I wanted the cap to face and screwed the brass fasteners down. The cap worked flawlessly all the way to the Black Hills.
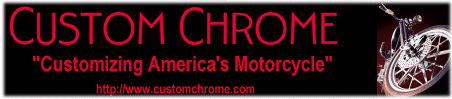
Sturgis Shovel Part 8
By Robin Technologies |
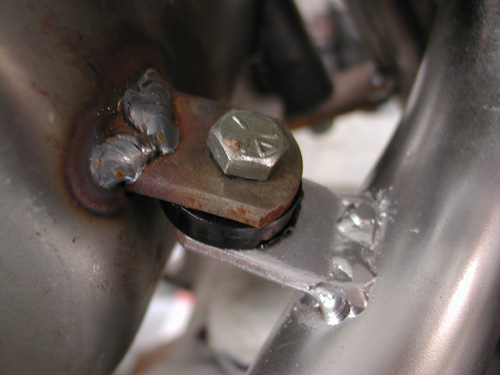
My first move began with a correction. I removed the exhaust pipe tab welded to the oil bag. The oilcan is rubber mounted, the exhaust pipe generated severe heat and the pipe system needs to be solidly mounted. It had to go. Actually Kent from Lucky Devil Metal Works in Houston tried not to mention the false move, but his frown gave it away. Or was it that question? “Is your rear pipe really mounted to the fuckin’ oil bag,” Kent said tentatively?
I discovered that the pipe exits the head close to the seat post and worked on a pipe connection there. There are a couple of rules in making pipes that I need to abide by. I needed to remove the pipe once in awhile, so I needed the pipe tab to be on the outside of the frame tab. Often mounting required slack, so I dug around for 1/16-inch washers to run between the tabs. That way when the fasteners are removed there’s some slack to pull the pipe free.
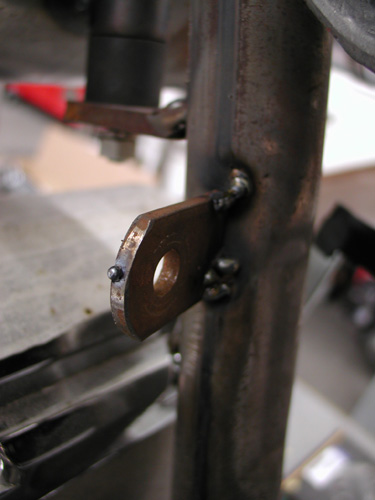
I worked with the pipe fully in place then tacked the seat post tab. Below is the tab tacked to the pipe. Then the tab welded in my shitty MIG welding fashion. I should slow down and clean the base metals more. I generally grind a bevel into the tabs for greater weld penetration. The welds are strong, just not handsome.
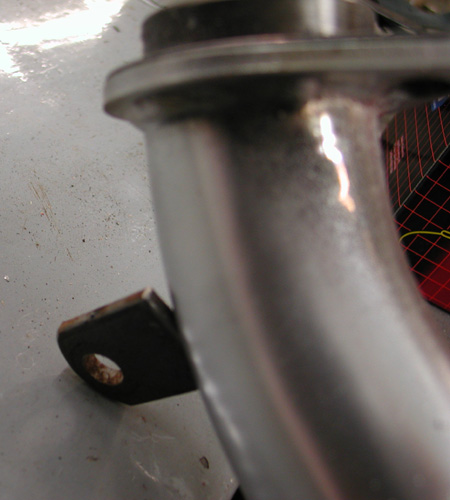
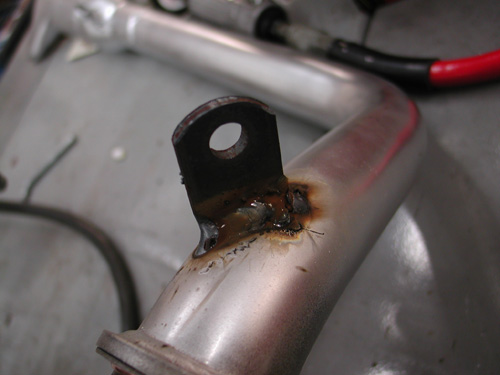

Next I needed to attach the Lucky Devil rear fender, align the rear wheel and cut the chain to fit. But first I needed to center the wheel in the frame, sorta. The custom Paughco frame is designed and manufactured to hold a belt pulley and a 180 Avon Tyre. That prevented me from measuring between the frame rails. I needed a straight line down the center of the frame backbone. It’s not incredibly accurate but close to draw a fabic or nylon line down the tube. Then with Doherty space kit and the seal spacers that came with the Custom Chrome aluminum and stainless spoke wheels, plus the Brembo brake caliper bracket, I aligned the wheel.
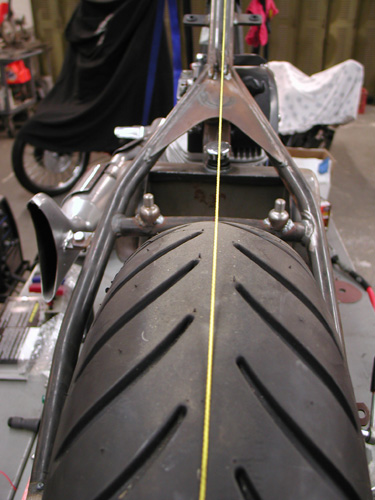
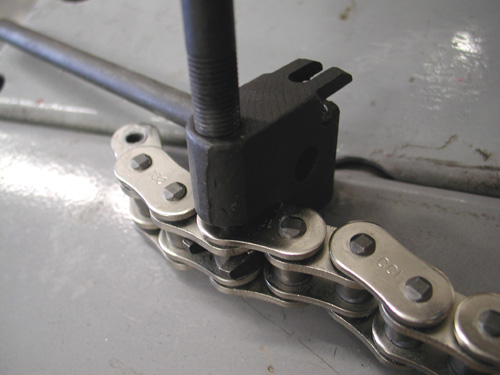
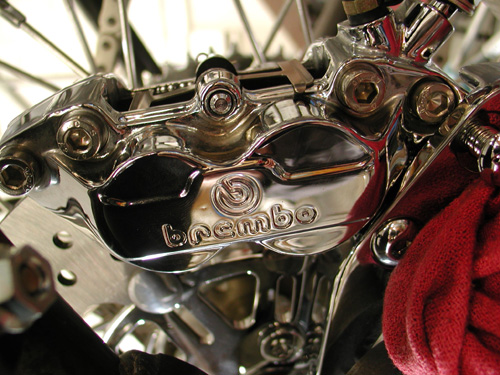
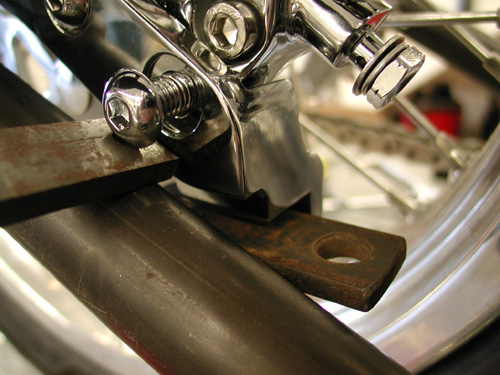
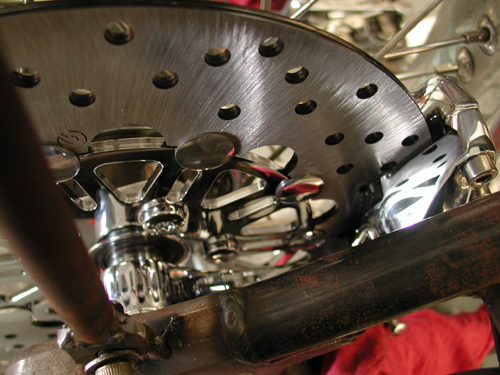
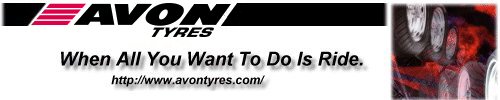
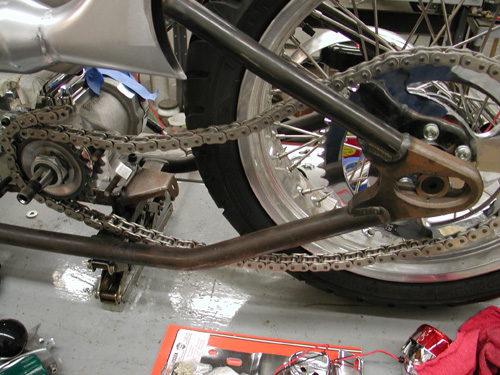
Before I cut the Rev Tech chain I installed the BDL Belt inner primary and pulled the engine and transmission into place which determined exact spacing. I know I covered this aspect somewhat a couple of chapters ago. There’s been some heavy drinking in the meantime, so if I lose track, it’s on Jack.
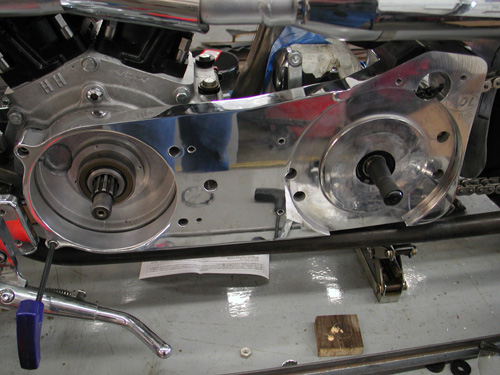
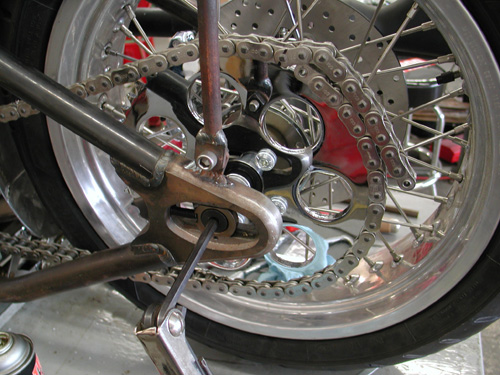
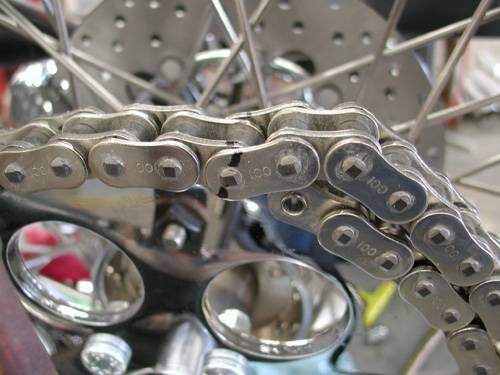
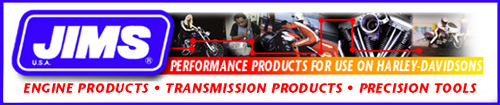
I centered the wheel in the chain adjustment slot to give me slack either way. Then I finally cut the chain with a JIMS tool.
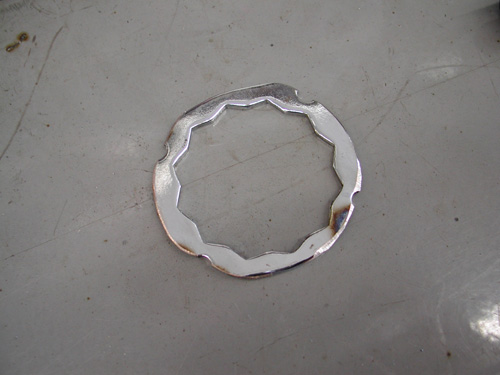
I spoke to a couple of guys about sprockets and was told that this contraption will hold a sprocket nut from coming loose better than simply Allen screws in the Custom Chrome sprocket. I may use it or not. Haven’t decided yet.

The reason this is altered is that it’s for a pulley and a different era. Add that to the fact that I flopped the dished sprocket over to space the chain away from the tire. That aspect worked perfectly.
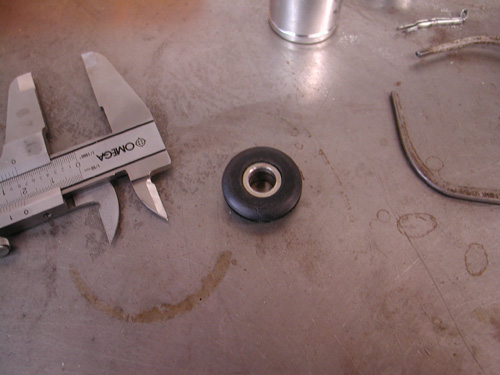
I decided that since the tank was rubber mounted and aluminum won’t flex as well as steel that I would attempt to rubber mount aspects of rear Luck Devil fender. Kent designed and handmade the fenders to match aspects of the XR 750 tank.
Cyril Huze sent me several grommets to work from and this pair are from some late model Sportster application. I measured the O.D. on the center portion and discovered that I needed ½-inch holes in the fender which I drilled after I had mocked up the fender in place, ground a clearance strip for the chain and stood back several times. Arlen Ness once told me that he used a chain wrapped over a tire to space a fender. I needed enough space for fasteners under the fender and some chain adjustment slack either way.
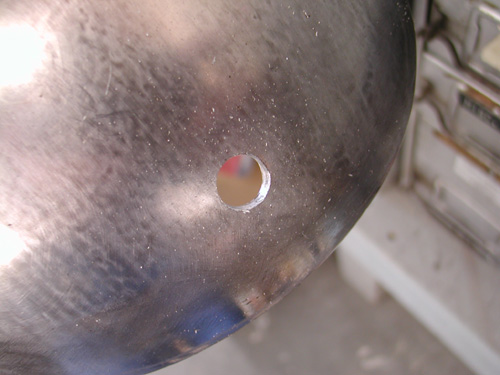
I moved the fender up and back, and side-to-side several times before making any hole-drilling marks. I was a nervous wreck. Ya don’t mess with the Devil’s fender. I finally drilled a half-inch hole, and smoothed the edges, in the bottom of the fender then at the crossover tube. I worked in the rubber with a dab of oil and bolted the bottom stainless bolt in place.
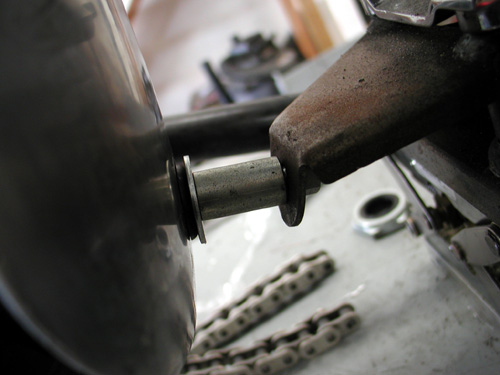
The Sportster grommets have metal inserts, which make them easier to install. With a couple of spacers in place the fastener held the center tab for tacking.
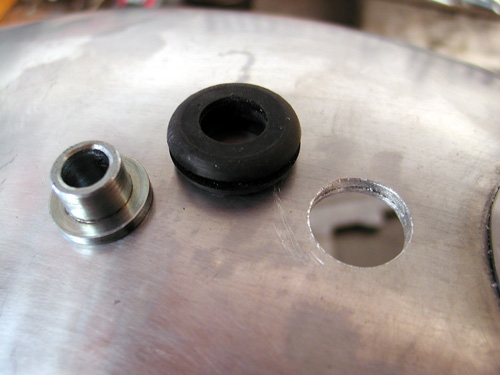
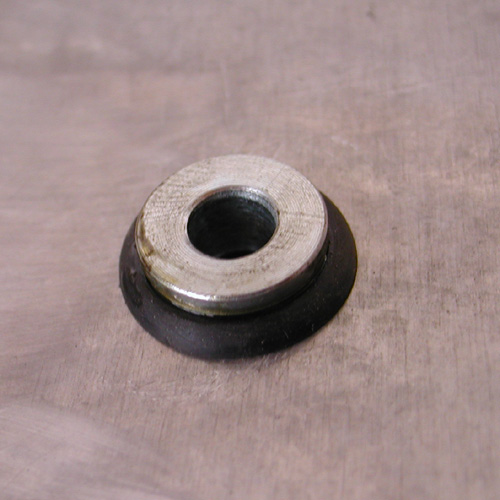
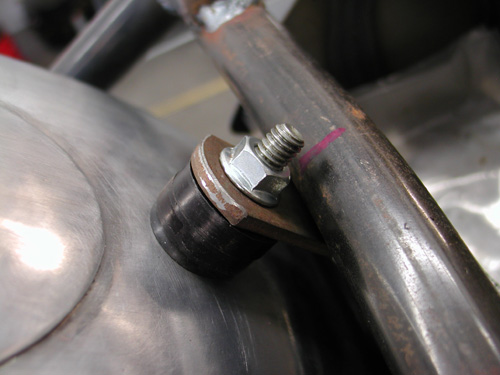
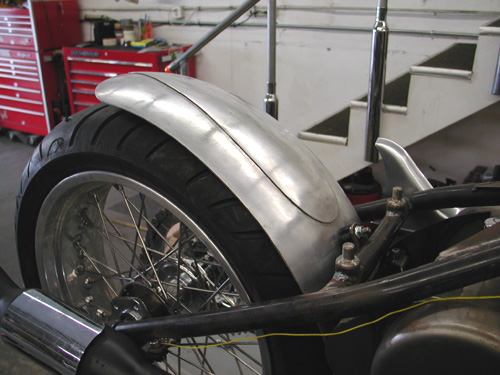

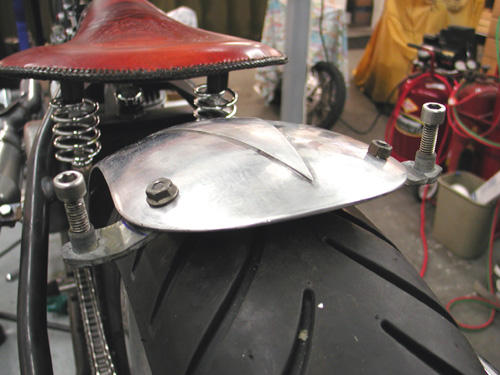
Here’s where it got tricky. I’ve been bending metal with a torch for years. Never improved my technique. Just the other day, a month after I built this fender rail system, I bought a small strap or tube-bending tool. Wish I had it when I went after this project.

First I built the fender strap out of a piece of exhaust pipe bracket. It came with two 3/8-inch coarse tapped inserts in each end. My plan was to build a fender rail system with tubing so I could adapt a couple of running lights on the tips. I carefully bent and drilled the strap and fender.
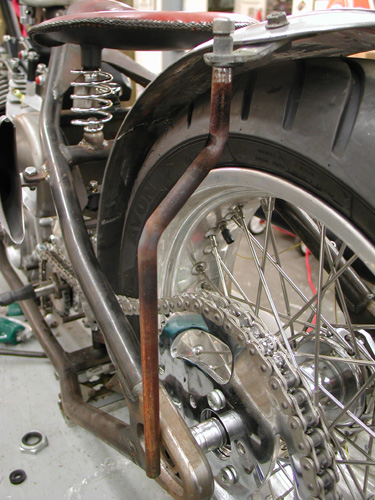
Then I bent the tubing fender rails to fit over the chain and tacked tab to the Paughco frame. One item I often attempt to use is a level. I’ll level the frame from side to side, then strive to keep all the other elements level. It helps.
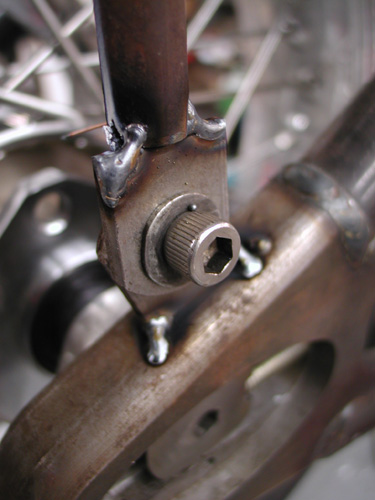
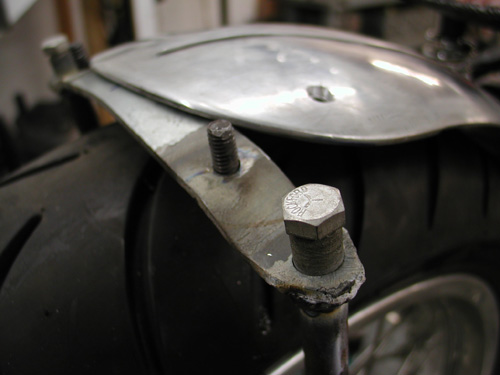
Here’s a perfect example. As I finished my welding chores, I got on a roll. I thought– wouldn’t it be cool to weld the fender bolts in place from the bottom. They would never come loose. Note the angle. There was no way they would ever return through their mounting locations. I was forced to grind them off and clean the holes.
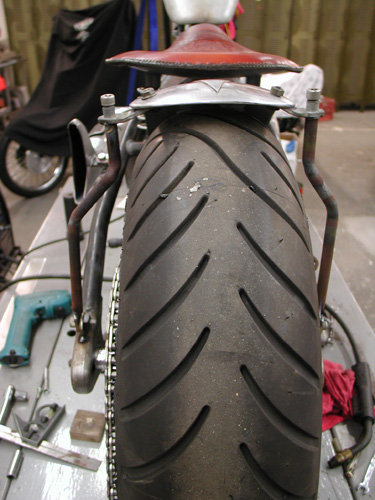
Here’s the finished fender rail system. I drilled holes in the frame and the rails to run wires. I still haven’t found the perfect running light style that rocks my boat and will afford me enough room to use the proper fasteners. Hang on!
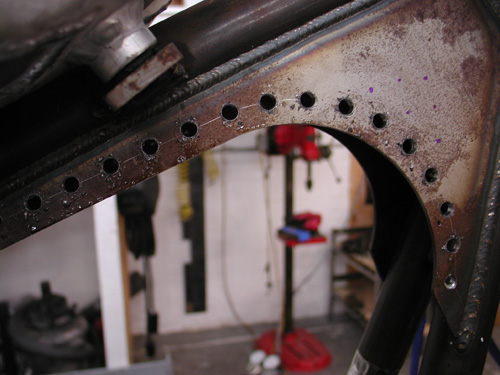
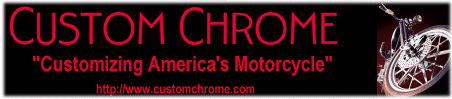