Bikernet West – Mikuni Carburators to the Rescue
By Robin Technologies |
With Sturgis 2000 looming over Bandit’shead we’ve been firing away at the getting the job done. Bikernet Eastmachine was well out in front in the competition when we wheeled the Agent’slow slung Softail onto a slick Gold Rush semi and said goodbye as the rig,packed with Ultra machines, Big Dogs and customs from the west coast, headedeast. Eddie Trotta from Thunder Design was more than happy to have thebike unpacked in his shop in Fort Lauderdale, so he could point a fingerat Bandit’s creation for Agent Zebra and bust out laughing, “You expectto ride that to Sturgis?” he said rolling on the floor of his shop. Weweren’t discouraged and neither was Bandit as we strapped the road wingswheels, the Weerd Brothers Front end on the Daytec rigid and went to work.
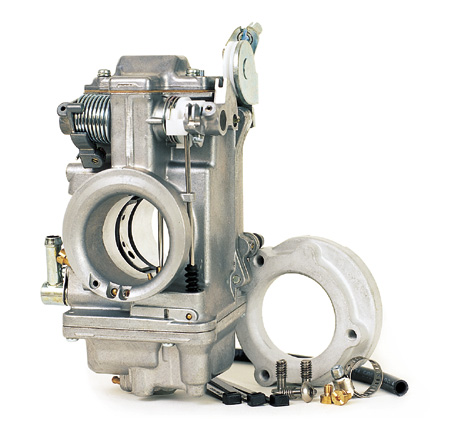
This was no ordinary installation. First,time was a factor, second it’s no normal, stock carburetor swap. The 98-inchS&S motor offered taller cylinders and improper intake manifold fitment.The stock Super E S&S manifold was too big for the 42 mm polished MikuniCarburetor. Stock manifolds shove the carb out too far and aren’t wideenough for the tall S&S cylinders so a quick call was made to JamesSimonelli of S&S who rushed the correct manifold to Mikuni. Lee alsowanted to explore an American Iron Horse manifold available for their customswhich pull the carb in closer to the engine and “L.T.” or James Littleof American Iron Horse moved equally fast and the parts were in hand inone day. The next hurtle: The cables. A call went out to Xavier at BarnettCables who turned about a set of Mikuni compatible cables which are setup the same as stock H-D cables, but cut to Bryan’s specifications forthe job. They also arrived in time.
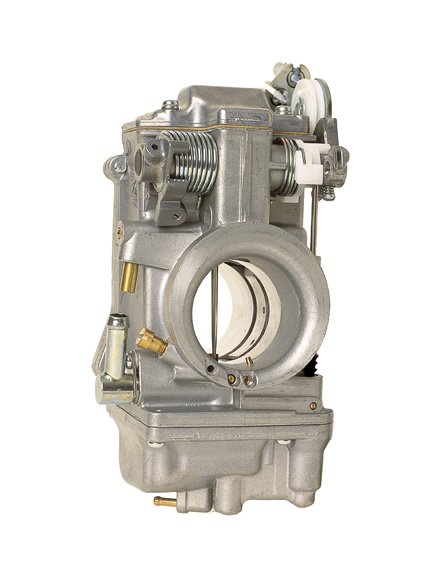
Bryan pointed out an adjustment on theleft side of the carb as you face it, a main jet air adjustment. He toldme to inform Bandit to turn it out a half turn in Denver for more compatiblerunning in altitudes. The bike immediately fired to life for the firsttime. Two weeks to go.
Bikernet West – The Blue Bomb Explodes
By Robin Technologies |
In a mad rush to build and break-in a monster Simms built S&S motor rigid before the long haul to Sturgis, Bandit makes an abrupt move. At the final hour he decided to take the frame to a local powder coater in Orange County who is capable of layering on a two or three stage powder coating process. After much deliberation with the entire staff, the decision to attempt a match between the frame and sheet metal was made. Nuutboy pointed out that the powder coated frame would be more resilient to wear and tear. Snake, in a rare lucid moment, noted that we wouldn’t be able to cover Bandit’s crappy welds with bondo, because powder coating is baked at such a high temperature that it melts the bondo. Overnight shipping would have been less than $100 to truck the delicate metal parts to Sacramento for Harold Pontarelli to paint. In contrast if we had the frame powder coated locally, we could have it back in three days and be working on the bike. On top of the concern for the various components being shipped, damaged, lost or dented- which would really set things back- there was the overall concern of time. We needed to be building a bike. Some of the Bikernet gang like Renegade, who was pissed that we weren’t working on his bike (he won’t ever let any of our mitts near it), Snake, Nuutboy, and my most informed self, huddled around a large bottle of Jack and a small bonfire in the junkyard rubble behind the Bikernet World Headquarters in San Pedro, California to take a vote. Bandit was somewhere inside the luxurious offices chasing a new female recruit, an oriental girl, whom he had failed to introduce to the rest of us. He was building a deep-seated resentment amongst the staff. “I say, fuck that bastard, let’s burn his frame,” Renegade said taking a hit on the freshly opened bottle of Tennessee champaign. “You say that every day,” Snake mumbled filling his large rusting flask with the bottle while guzzling the last remaining can of Bud from his 12 pack. No one else drinks beer. “We’re supposed to be deciding whether to ship or powder coat,” Nuutboy said standing on the edge of the fire holding a wad of tools in each hand. He doesn’t drink, but smokes joints incessantly and fidgets constantly. “We’re running out of time.” The evening went south from there. More riders showed up, Japanese Jay from the antique bike shop, 34th Station, came by. Chris from Hill Products wandered in and filled his boot flask, put in his two-cents worth and moved on. Nuutboy and I pondered the question until we heard the giggling stop from inside the Headquarters and the large thump of boots against rickety floors. Bandit appeared bleary eyed but content and placed his vote. If we could get a sample of the paint color on a separate rod we could ship it to Harold for a paint match. We went to work. We delivered the frame to Primo Powder Coating in Huntington Beach, California (714) 596-4242. They had a sample of the metallic blue we were after, waiting for us. We immediately took that sample to a mail box joint and shipped it overnight. The tank and fenders were carefully boxed up and shipped to Harold via UPS second day air. Then we delivered the chrome to Orange County Plating (714) 532-4610 where they immediately photograph the items and enter them into a computer. In four days we had the frame and chrome back and were in the process of building the bike. Harold moved on the paint quickly, but even with a simple flame job on the table, a couple of days was spent at the body shop, then paint prep and primer, then undercoats of silver base were followed by a matching blue candy with a hint of pearl, then drying time before the graphics could be laid out. Two weeks have slipped past, but the progress with the frame in hand is considerable. The engine and tranny are bolted in. The Weerd brothers front end is in place. The wheels and P.M. brakes are in place along with the Samson exhaust system. Wiring will begin this weekend. Then with the BDL 3-inch primary belt in place we will haul the bike to Mikuni for a Carb and go for a ride. Here’s a sample of the paint from Vacaville, California near Sacramento.
![]() –Wrench
|
Bikernet West Bogged Down In Pheonix
By Robin Technologies |
I knew it! The sonuvabitch couldn’t make it to the Badlands and back on that piece of shit. I knew it! The way Bandit mounted that tank was fucked from the beginning.
![]() I told him. Nuutboy told him. Harold Pontarelli told him. Shit, his 78-year-old mother told him. Did the big bastard listen? Nooo. So it jumped off the frame in Aspen, Colo., and landed in his lap.
![]() Yeah, they welded it up in Aspen with the help of Randy Aron from Cycle Visions in San Diego, and he limped into Sturgis, rode around the Badlands for the week and then the scoot was kidnapped from him by someone who knows what the fuck he’s doing, namely Paul Yaffe from Paul Yaffe Originals in Phoenix. Paul is working with Kyle of Independent Tanks, who hand makes steel tanks from heavy 16-gauge material. It’s about time someone grabbed that bike before it exploded into flames and scorched the ornery sonuvabitch.
![]() So we sent that fly-bitten claybrain to Phoenix for a welding lesson and instructions on how to properly mount a gas tank. If he wasn’t such a hasty-witted old fool, he would have put the bike together right the first time.
![]() Here are shots of the existing piece of shit with the new tanks recommended by Paul, who builds some of the most innovative bikes on the planet.
![]()
![]() Paul’s philosophy is to manufacture enough custom components to allow his customers to build something without doing a piece-meal job. “Instead of buying fenders from me that don’t fit the other guys’ frame properly and then mount a gas tank from so and so, and nothing fits properly, I want to give the customer half a chance to build a world-class custom on his own.” Paul’s positioning himself, unlike Bandit, to afford customers with frames, plus the fenders, tanks and billet components to match. Paul began his operation building LED taillight products. Unlike the slob who runs this joint, Paul is a young man of vast energy and talent who could not contain himself building bikes with existing components. He began building his own fenders, air cleaners, frames, etc. The young upstart with the flaming red hair does share one notion with Bandit: “If you’re going to build a new full-custom for a customer, I want the bike to be a reliable runner, of the newest technology, or how can you call it a new bike?” So all of Paul’s bikes are built with Harley-Davidson Twin Cam drive lines. “I use as much Harley stuff as possible,” Paul said. “Plus the factory is going crazy building more new accessories all the time. The selection is growing by leaps and bounds.” Damn, if I told that lunkhead Bandit once, I told him a thousand times, it’s time to move away from the Evolution shit into the real world of Twin Cams. But that motley-minded minnow is still out in the garage trying to put two Mikuni’s carbs on his ’48 Panhead. If you want to check true customs, built to ride, check Paul’s site http://www.paulyaffeorginals.com Finally, after much consternation, Bandit succumbed to one of Paul’s buddies, Kyle at Independent Gas Tanks. These are new, contoured tanks and here’s how ya do it right.
![]() Kyle has been building his own line of steel gas tanks for two years. Prior to ’98, he built tanks for Roger Borget for three years and before that he built Porsche 911 race cars. He won’t get near aluminum. “Not with the engine sizes that are bouncing around in these frames,” Kyle said. None of his creations are Mig welded, either. “I only Tig weld my tanks. I’m glad to work with builders and make suggestions.
![]() I’ve hand-built over 1,000 tanks for Harleys, and if told the brand frame, the stretch and rake, I usually know which tank works the best. I can go with one of my six to eight standard styles, or I can design something out of this world. I can make a bike blend into the crowd or stand out anywhere.” Kyle’s tanks come with mounting straps. Don’t just weld ’em on and go, though. “Depending on how the tank is designed to mount will depend on if the existing tabs will work immediately or need to be modified,” Paul said. In this case, he created some spacers to allow the tank to set on the frame perfectly to capture the look the big bastard wanted, then he cut the tabs and tacked them to the frame. Next he removed the tank and solid tacked the tabs. He put the tank back on and made sure everything was in place. These tanks are handmade and not manufactured with a jig, so no two tanks are alike.
![]() The tabs were finish welded and the tanks shipped to Harold Pontarelli for repaint. Paul welds everything with Tig because the Argon gas shield makes for a more controlled burn. It gives him better penetration and a less brittle weld than a Mig. Kyle had one other recommendation. He often gets calls from brothers requesting tanks after they have taken their frame to the powdercoater. Don’t do that. Make sure all the sheet metal is prepped and assembled before any finish work is undertaken. In fact, many builders ride scoots without paint for a hundred miles or so before tearing down for paint. Saves the headache, and makes for a much tighter custom.
![]() Of course the whole operation must have a photo finish. Two days before the Love Ride, the tank is floating into town via Harold and eight H-D Performance troopers. The bike is rumbling in on the back of Paul Yaffe’s custom trailer. The two will meet with Bandit in Woodland Hills for the install and road test for the parties to come that weekend. He doesn’t deserve this scoot. It should be mine. –Renegade
|
|
Motorcycle Mania And Hugh King
By Robin Technologies |
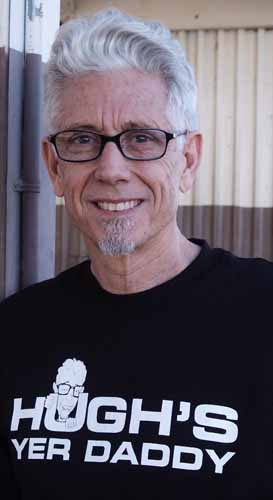
What hit the American Motorcycle industry like straight pipes and tire sizzling burn-outs, at 4 in the morning? Television, in the form of Motorcycle Mania one and two. The introduction of chopper building skills and rebel attitude, unleashed broadband, to citizens all over the country, rocked the biker world. Then chopper heaven in the form of Biker Build-offs struck with round two. Who was responsible for this Tsunami boon to our lifestyle? It was Hugh King, the producer/director/writer and editor at large of Original Productions.
Hugh felt the crisp freedom and wild wanton wickedness of the chopper industry in 1947 as a Milwaukee youngster, with his nose pressed against his living room window. An older neighborhood wildman, Billy Brody, screamed down the street on a bobbed ’46 Indian Chief. He tore across his folk’s lawn and slid to a stop on the front porch ignoring the driveway and garage alongside the house. That scene, on the Oak shrouded street, was emblazoned in Hugh’s expanding creative mind for years to come. In fact he added a wild black and white scene of a biker burning into a bar, to his documentary resume while living off grants and making social action films.
Through the reams of vast, rough-shot, motorcycle footage he learned the Harley biker industry, from event coverage, to land speed record attempts. Hired by Original Productions he produced reality shows. Then one fateful day, while warm California rays graced his small Original Productions, office, Tom Beers, his boss, wandered in.
“Discovery Channel called,” he said. “They want a feature on the custom motorcycle industry. You’ve experienced the motorcycle world. It’s your assignment.” Since the offices were located in Burbank, California, Hugh investigated valley shops and called motorcycle mag editors. A mystery connection was made, and an old crocked finger pointed toward West Coast Choppers. “And the rest is history,” Hugh said.
By Motorcycle Mania two, Jesse became a star. “Viewers wanted to talk to him,” Hugh said of growing audience. “We filmed it for the average Joe and sensed immediately that people wanted to reach out and touch tools. There was a deep longing for the ability to make something out of nothing.”
Jesse smacked a cord in young American viewers with a ballpeen hammer against a flat sheet of aluminum. Fans witnessed pure raw alloy shaped into sleek gas tanks. “The footage of metal being annealed was graphically inspiring,” Hugh said. At that stage he was the producer, director, writer and editor (Tom Beers was the executive producer).
Discovery was rocked and wanted more, so Hugh directed the first four Monster Garage segments, then kicked off the Build-Off series.
Life kicked into high gear for Hugh and again Original Productions was approached by Discovery Channel to make Motorcycle Mania III or “Jesse James Rides Again” starring Jesse James and featuring his buddy, Kid Rock. Jesse worked with wheelwright, Fay Butler, in Massachusetts to learn the intricacies of copper fabricating. Fay manipulates old yoders like an artist’s brush shaping copper. Yoders were used in WWII to fashion sheets of metal for fighter fuselages and wings. Jesse and Fay worked together to shape the copper chopper gas tank.
The MMIII film endeavor raised the bar for Hugh. “I had the opportunity to work with high def film and top quality camera equipment,” he said. “We got to use the highest standard automobile commercial equipment like a Shot Maker and Chapman cranes for dramatic rolling angles.” His life hit overdrive as he filmed the building of the Copper Chopper for Jesse, American Bad Ass Chopper for Kid Rock, and they hit it to Mexico. “Nothing went according to plan,” Hugh said. “We changed the itinerary constantly. The people of Mexico were terrific as we shot from El Paso, Texas and Juarez, Mexico, in 125 degrees, through 350 miles due south to Chihuahua.”
Hugh filmed spectacular footage of the two riders passing smoldering sand dunes, sweeping vistas and lumbering Iguanas crossing the rugged roads toward Copper Canyon.
Having the time of their lives they rode south to Chihuahua, a growing city, and searched through the old market place. Riding west they climbed 6,000 feet to Copper Canyon, in the middle of the Sierra Madres, which is six times longer than the Grand Canyon. They slept in a small village on the lip of the gorge, in a town of 65.
Jesse and the Kid accomplished their goal of escaping fame and fortune as they continued West toward the coast over torturous curved roads through blinding lightening storms and over a territory where the only vocation is hijacking. “We slept in the camera van,” Hugh said, “since there was no place to stay, until we reached the white sand beach on the Sea of Cortez. It was a transcendental experience.”
Motorcycle Mania III will experience limited theatrical release later this year, followed by Discovery Channel airing. Hugh has a year and a half invested in the film while directing Biker Build-offs with Billy Lane, Dave Perewitz, Roger Borget, Paul Yaffe, Indian Larry and currently with Yank Young, Chica, Eddie Trotta, Russ Mitchell, Arlen and Cory Ness. “Choppers have turned my life upside down,” Hugh said. Although the family man doesn’t own a bike, he rides constantly. “I’ll jump anything the builders let me straddle,” Hugh said. You can see the motorcycle mania fever boiling in his gaze.
What’s the future hold for Hugh King? The Biker Build Off series is rockin’ through another chrome and flamed season and even hotter segments are headed for next year. “We kicked off the series with Billy Lane and Roger Borget,” Hugh said. “Initially it was intended as an elimination competition, but no builder can manufacture one ass-kickin’ bike after another, every 30 days. We currently pick builders by regions and diverse styles.” In 2005 he hopes to throw a massive live finale in Las Vegas and take the bike voting interactive.
At 65, Hugh ramped into an all-time high with custom bikes. He’s riding it for all it’s worth and the entire industry benefits.
HUGH KING SIDEBAR:
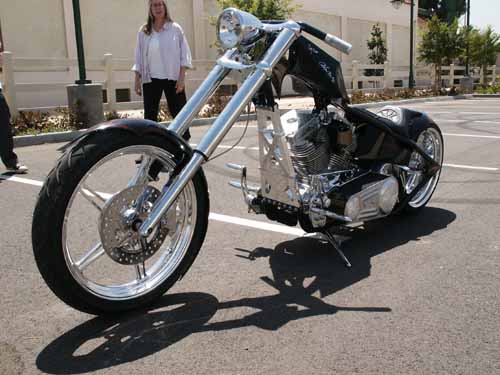
THE LAUGHLIN BUILD-OFF– On April 20th ten of the world’s greatest bike builders thundered into Laughlin, Nevada. For 72 hours in a secret desert shop they worked non stop to create BBO X, a one-off 124 cubic inch, rigid, right side drive, black and chrome, spear-like chopper. Then they presented it to Hugh King, producer of Discovery’s Great Biker Build Off. The geniuses who came together to make this awesome steed were Arlen Ness, Cory Ness, Russell Mitchell, Eddie Trotta, Mitch Bergeron, Kendall Johnson, Matt Hotch, Joe Martin, Chica and Hank Young.
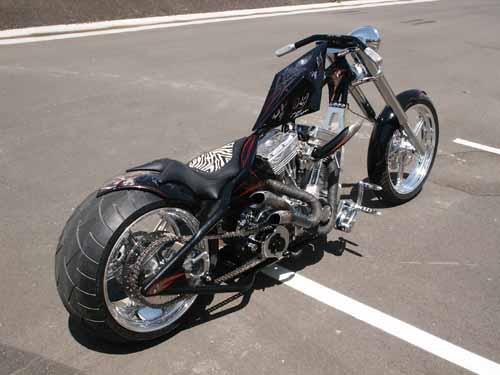
Chica hand fabricated the gas tank. Hank Young made the oil tank. Kendall Johnson was responsible for assembling and tweaking the 124 cc. S&S motor and the Baker 6 speed transmission, Mitch Bergeron was responsible for the frame and the billet down tube (in which was cut in the Roman Numeral X and the Discovery planet), Matt Hotch fabricated the fenders, Joe Martin built the pipes and did the pin striping, Russell Mitchell and Eddie Trotta built the front end and Arlen Ness and Cory Ness were responsible for the paint and the overall supervision of the project.
A special guest appearance was made by legendary seat maker, Danny Gray who fabricated a black leather seat with a zebra stripped manta ray inset.
On Saturday night, April 24th, before thousands at the Laughlin River Run, BBO X was unveiled and formally presented to Hugh King.
Each of the ten builders had competed in Bike Build Off before. Their ten bikes were on display at the Discovery both where the people voted on which motorcycle they thought was best in show.
Matt Hotch’s low slung, blue beach cruiser took the prize. Watch every Monday night for a new Build-Off on Discovery.
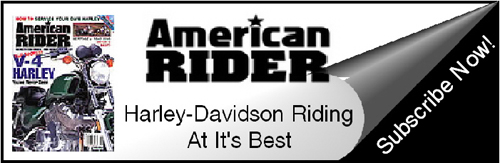
Sturgis Shovel Part 8
By Robin Technologies |
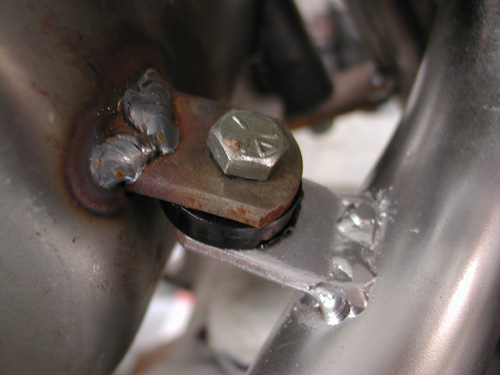
My first move began with a correction. I removed the exhaust pipe tab welded to the oil bag. The oilcan is rubber mounted, the exhaust pipe generated severe heat and the pipe system needs to be solidly mounted. It had to go. Actually Kent from Lucky Devil Metal Works in Houston tried not to mention the false move, but his frown gave it away. Or was it that question? “Is your rear pipe really mounted to the fuckin’ oil bag,” Kent said tentatively?
I discovered that the pipe exits the head close to the seat post and worked on a pipe connection there. There are a couple of rules in making pipes that I need to abide by. I needed to remove the pipe once in awhile, so I needed the pipe tab to be on the outside of the frame tab. Often mounting required slack, so I dug around for 1/16-inch washers to run between the tabs. That way when the fasteners are removed there’s some slack to pull the pipe free.
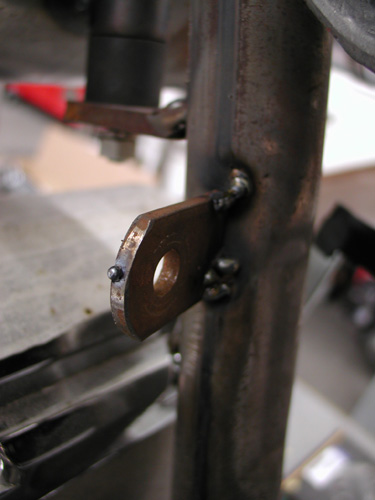
I worked with the pipe fully in place then tacked the seat post tab. Below is the tab tacked to the pipe. Then the tab welded in my shitty MIG welding fashion. I should slow down and clean the base metals more. I generally grind a bevel into the tabs for greater weld penetration. The welds are strong, just not handsome.
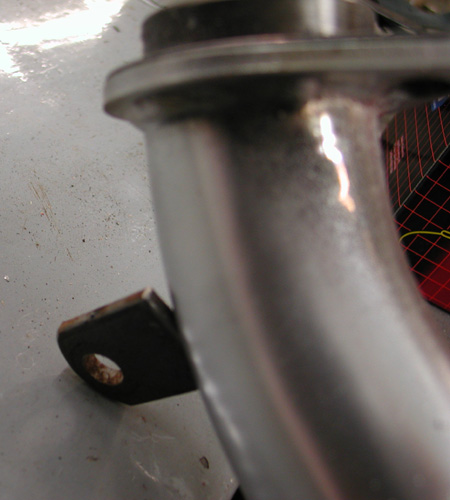
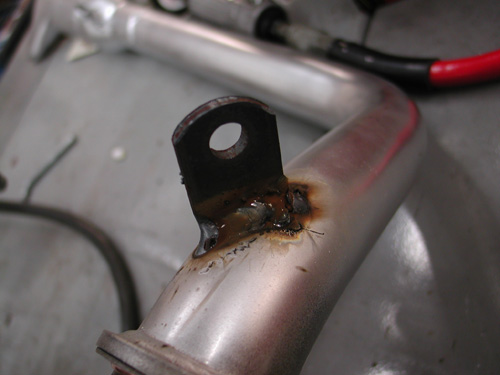

Next I needed to attach the Lucky Devil rear fender, align the rear wheel and cut the chain to fit. But first I needed to center the wheel in the frame, sorta. The custom Paughco frame is designed and manufactured to hold a belt pulley and a 180 Avon Tyre. That prevented me from measuring between the frame rails. I needed a straight line down the center of the frame backbone. It’s not incredibly accurate but close to draw a fabic or nylon line down the tube. Then with Doherty space kit and the seal spacers that came with the Custom Chrome aluminum and stainless spoke wheels, plus the Brembo brake caliper bracket, I aligned the wheel.
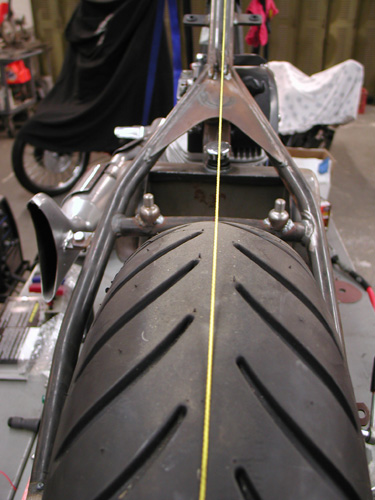
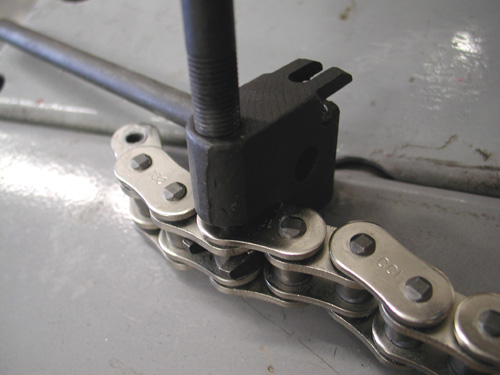
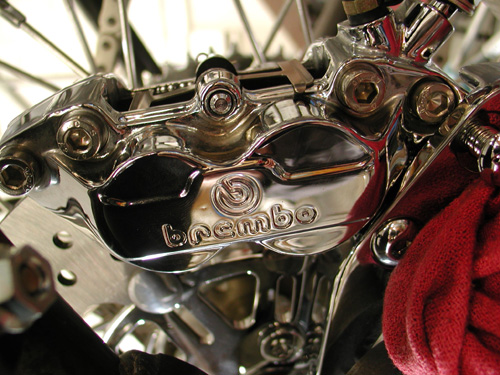
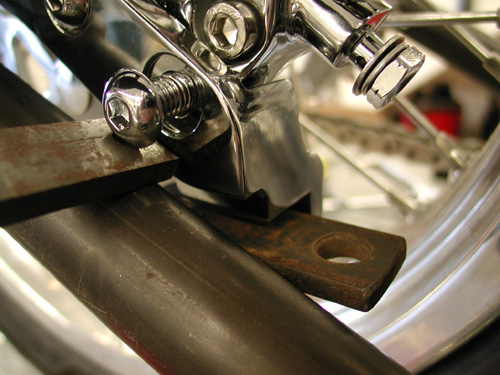
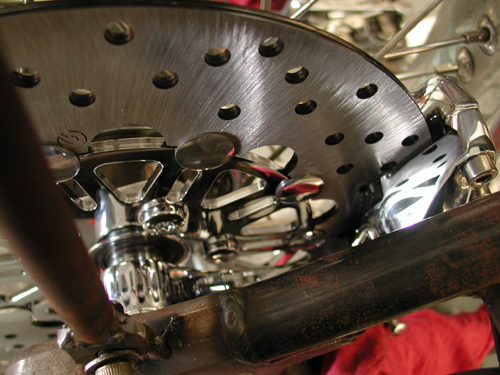
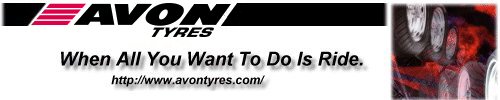
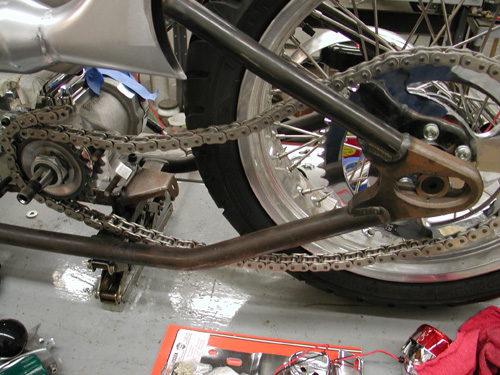
Before I cut the Rev Tech chain I installed the BDL Belt inner primary and pulled the engine and transmission into place which determined exact spacing. I know I covered this aspect somewhat a couple of chapters ago. There’s been some heavy drinking in the meantime, so if I lose track, it’s on Jack.
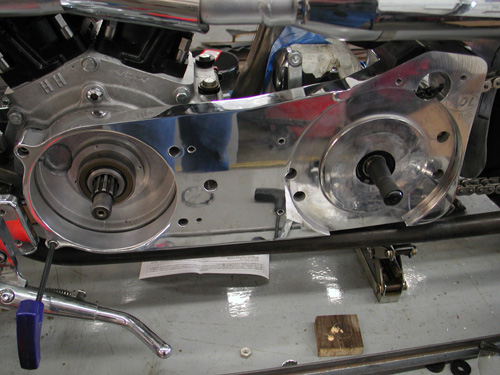
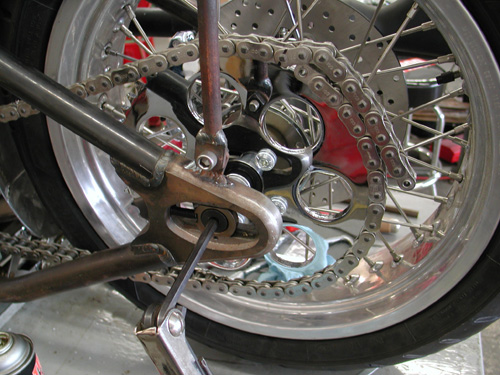
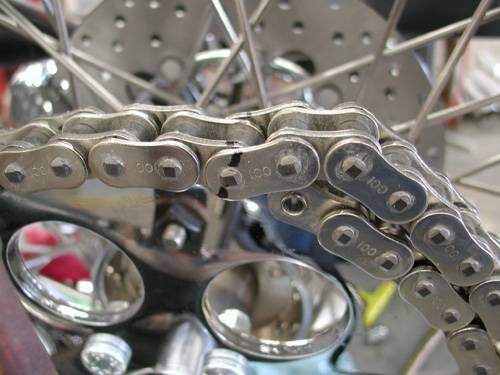
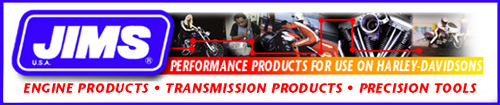
I centered the wheel in the chain adjustment slot to give me slack either way. Then I finally cut the chain with a JIMS tool.
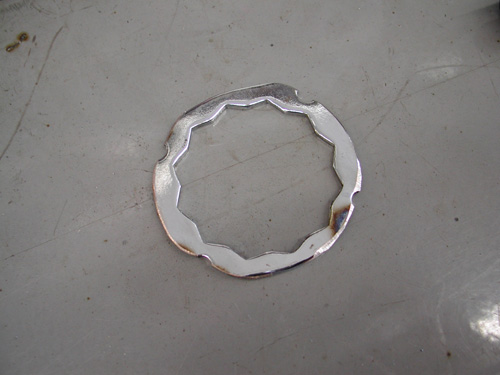
I spoke to a couple of guys about sprockets and was told that this contraption will hold a sprocket nut from coming loose better than simply Allen screws in the Custom Chrome sprocket. I may use it or not. Haven’t decided yet.

The reason this is altered is that it’s for a pulley and a different era. Add that to the fact that I flopped the dished sprocket over to space the chain away from the tire. That aspect worked perfectly.
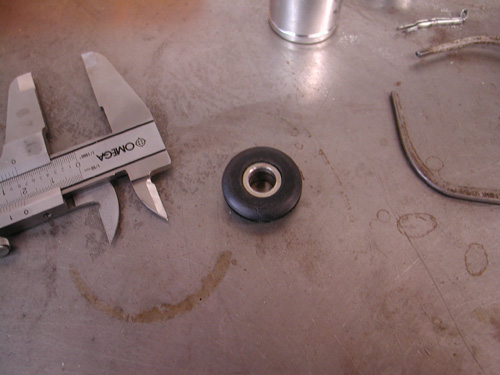
I decided that since the tank was rubber mounted and aluminum won’t flex as well as steel that I would attempt to rubber mount aspects of rear Luck Devil fender. Kent designed and handmade the fenders to match aspects of the XR 750 tank.
Cyril Huze sent me several grommets to work from and this pair are from some late model Sportster application. I measured the O.D. on the center portion and discovered that I needed ½-inch holes in the fender which I drilled after I had mocked up the fender in place, ground a clearance strip for the chain and stood back several times. Arlen Ness once told me that he used a chain wrapped over a tire to space a fender. I needed enough space for fasteners under the fender and some chain adjustment slack either way.
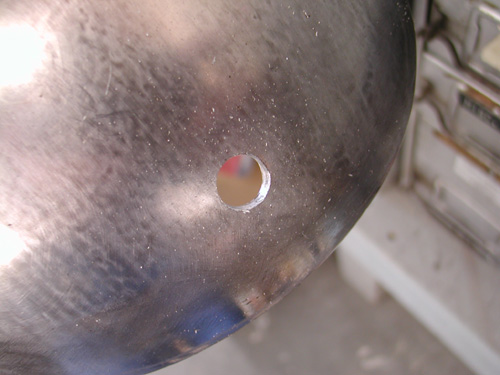
I moved the fender up and back, and side-to-side several times before making any hole-drilling marks. I was a nervous wreck. Ya don’t mess with the Devil’s fender. I finally drilled a half-inch hole, and smoothed the edges, in the bottom of the fender then at the crossover tube. I worked in the rubber with a dab of oil and bolted the bottom stainless bolt in place.
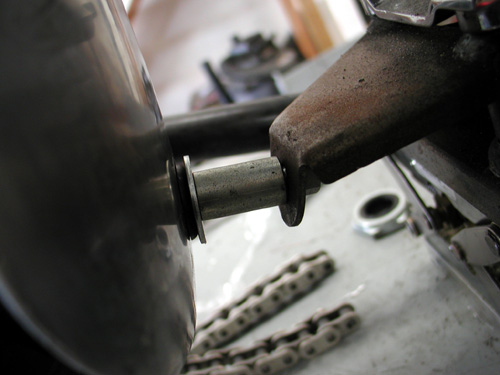
The Sportster grommets have metal inserts, which make them easier to install. With a couple of spacers in place the fastener held the center tab for tacking.
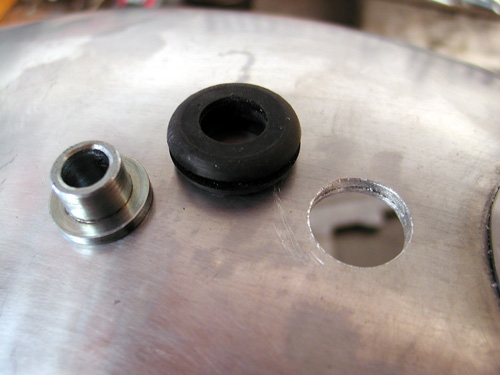
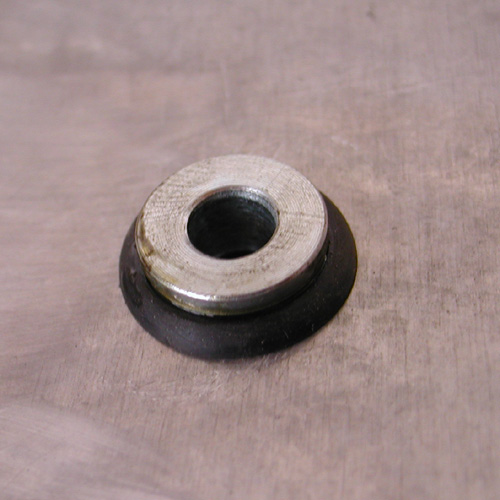
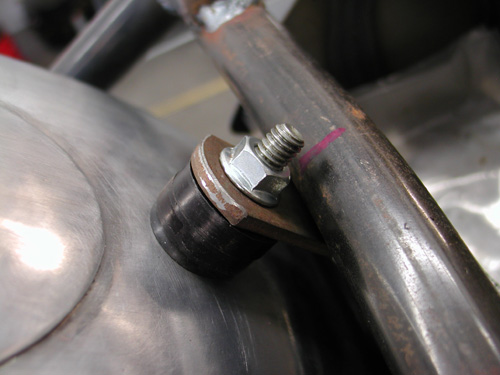
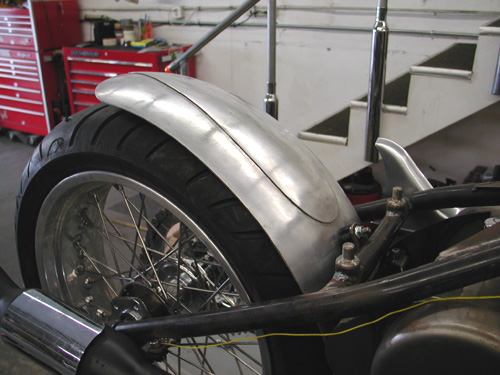

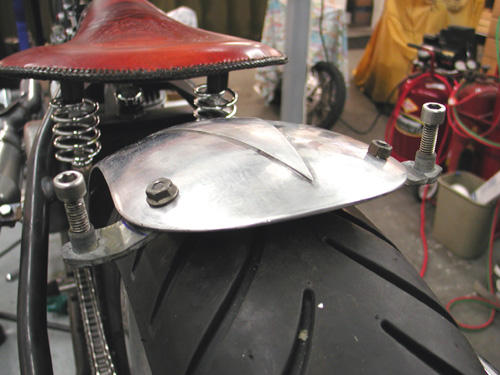
Here’s where it got tricky. I’ve been bending metal with a torch for years. Never improved my technique. Just the other day, a month after I built this fender rail system, I bought a small strap or tube-bending tool. Wish I had it when I went after this project.

First I built the fender strap out of a piece of exhaust pipe bracket. It came with two 3/8-inch coarse tapped inserts in each end. My plan was to build a fender rail system with tubing so I could adapt a couple of running lights on the tips. I carefully bent and drilled the strap and fender.
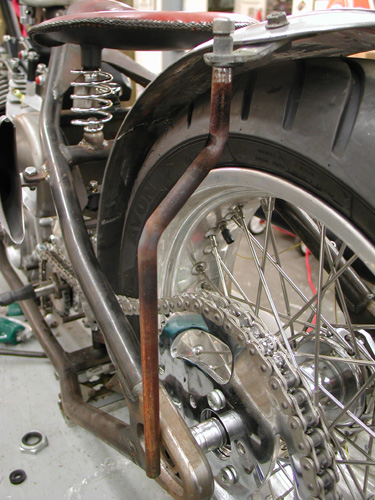
Then I bent the tubing fender rails to fit over the chain and tacked tab to the Paughco frame. One item I often attempt to use is a level. I’ll level the frame from side to side, then strive to keep all the other elements level. It helps.
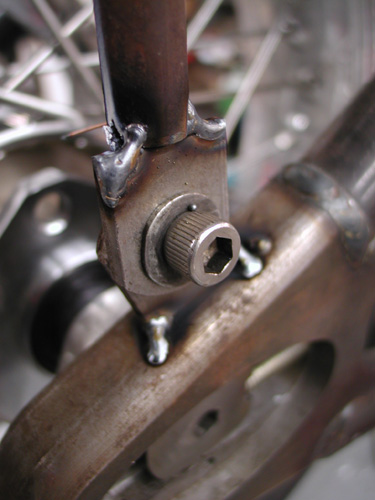
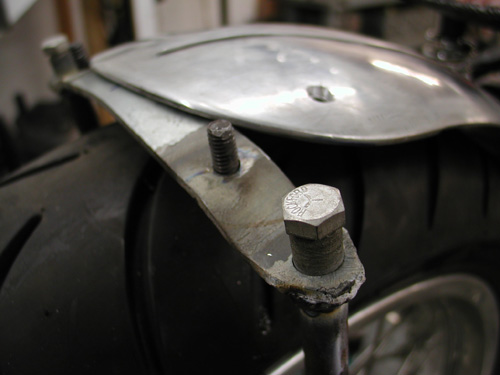
Here’s a perfect example. As I finished my welding chores, I got on a roll. I thought– wouldn’t it be cool to weld the fender bolts in place from the bottom. They would never come loose. Note the angle. There was no way they would ever return through their mounting locations. I was forced to grind them off and clean the holes.
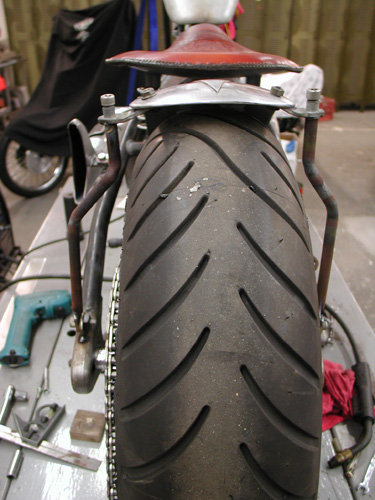
Here’s the finished fender rail system. I drilled holes in the frame and the rails to run wires. I still haven’t found the perfect running light style that rocks my boat and will afford me enough room to use the proper fasteners. Hang on!
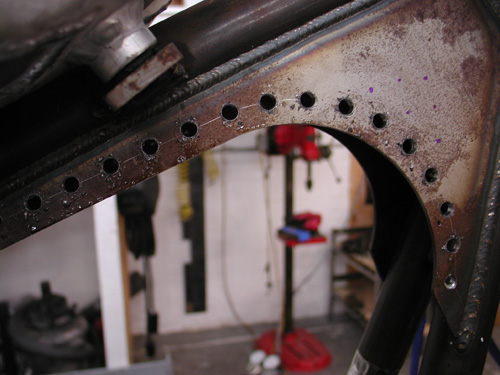
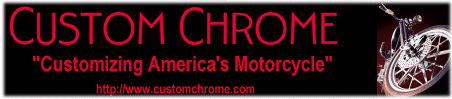
Sturgis Shovel Part 9
By Robin Technologies |
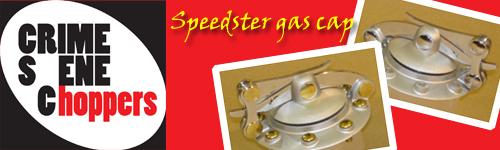
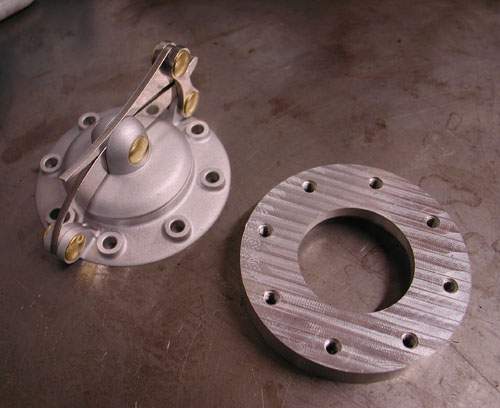
This is strange. I’m writing several Sturgis Chop Techs after I returned from Sturgis. I’ll try to remedy that in the future, but we were so damn busy trying to complete the bike and run Bikernet, we didn’t keep up on the techs. Many apologies.
This piece covers the installation of the hot Speedster cap from Crime Scene Choppers in the modified stock XR 750 factory tank. Later, you’ll discover, that this highly modified, strengthened and extra rubber mounted beast was my Sturgis nemesis. But more on that later.
We added rubber-mounted bungs to the back of the tank. I moved the petcock to the rear and filled the center for a 2.76-gallon gas capacity before it hit reserve. I doubt that it contained more than a quarter tank of reserve, so I’ll toss it a 3-gallon total gas capacity.

Oh, I need to thank Cyril Huze, who designs beautiful steel tanks for the opportunity to experience an aluminum tank once more. He suggested this classic for the Sturgis effort.
I’m not holding it against Cyril. He’s a master and I’m the bungler for attempting aluminum on a 93-inch rigid S&S hot rod. As you’ll see the vibration aspects came from several sources that I could have remedied. It’s all just a roll of the dice.
When I received the Speedster cap I drug the cap and tank down the street, about three doors, to Bill Hall’s Welding. He handles my aluminum welding, since I don’t have a TIG welding system. I’ve got the rest, but not TIG. I would highly suggest a TIG system for quality welding capacity and good looking welds. It’s much like welding with a torch, so you’re certain of the bead and depth of penetration.
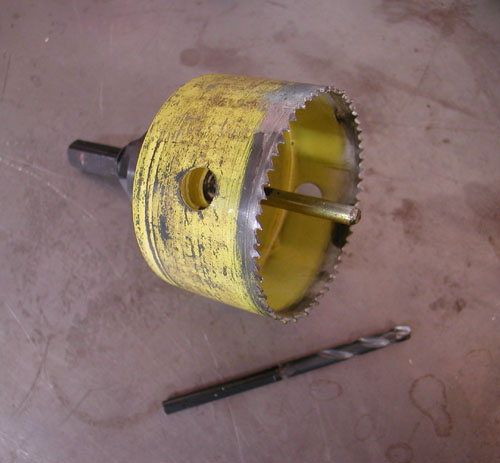
Bill’s a retired designer who enjoys welding and fuckin’ with his customers. “How are you going to drill the hole for the bung,” he asked?
I was thinking about die-grinders and files. I knew it would make a mess. Bill hooked me up with a 3-inch hole saw. He suggested that we hit a marine store for a tapered dowel pin (used for plugging holes in the leaking hulls).
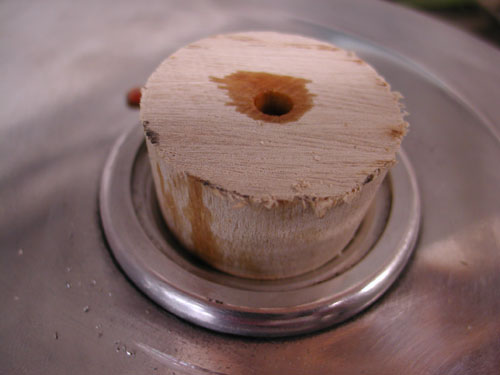
The key was to drill a perfectly centered ¼-inch hole to maintain a center approach to the cap bunghole. I drilled it and then ran the tapered wood dowel into the tank.
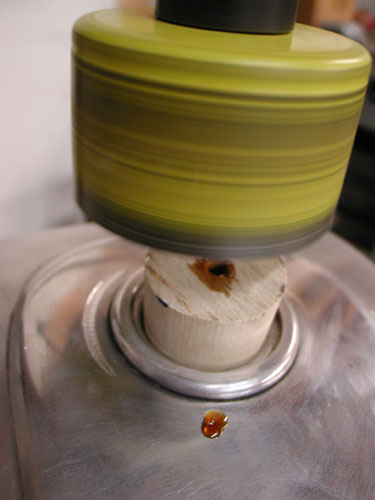
Then we set the tank on a pad on the drill press platform and lined up the hole saw. I used plenty of cutting oil on the edge of the blade and aluminum face to prevent the tank from snagging or catching. I knew how tender the surface of the tank was. We oiled the hole in the tapered wooden plug and carefully went to work. Bill’s formula worked like a charm.
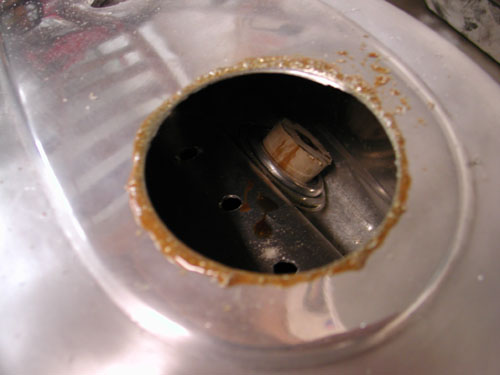
Next, we needed a tool to hold the Crime Scene Speedster bung in place. I grabbed a piece of strap, drilled a hole or two and mounted it with the supplied hardware, which was brass. You can order the cap with several styles of fasteners for your application.
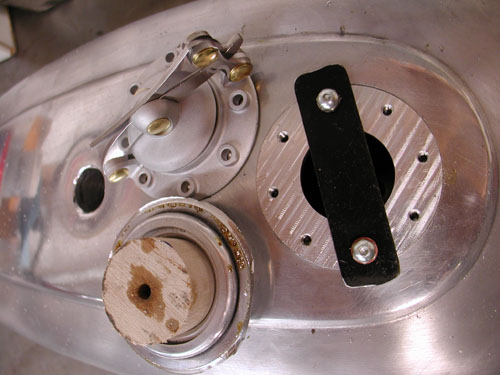
It was off to Bill’s for welding. While the gaping 3-inch hole was available I could have made a tapping tool and tapped out any imperfections in the tank walls. I dinged it way back in the beginning and never got around to fixing it. I left her be, as if it was the first injury and she needed to stay. I know it’s one of those wild superstitions.
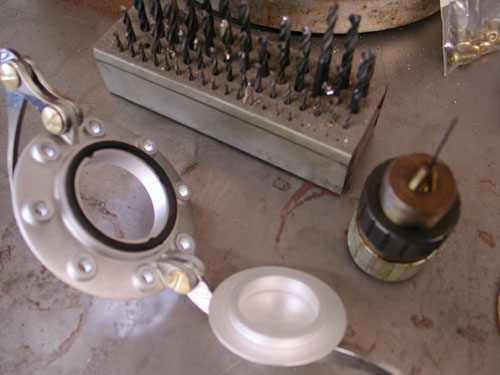
Okay, so during the “read the directions” phase, I noticed the bit about a non-vented tank. I would need to drill a tiny, cunt-hair hole in the cap of the tank. I discovered that I actually had such a tiny fuckin’ drill and dug it out. I had to find a chuck that pinched down to that size. Then I had a wise ass notion to drill the initial hole about 1/8 inch in diameter, since drilling with hair-thin bits causes easy drill bit breaks. The thinner the surface the better.
So, I initially drilled the inside of the cap with a 1/8-inch drill and drilled right through—Bummer. Ultimately I tapped the cap with a 10-32 then drilled the stainless Allen stud with the tiny drill bit. Then I screwed the stud into place and the job was finished.
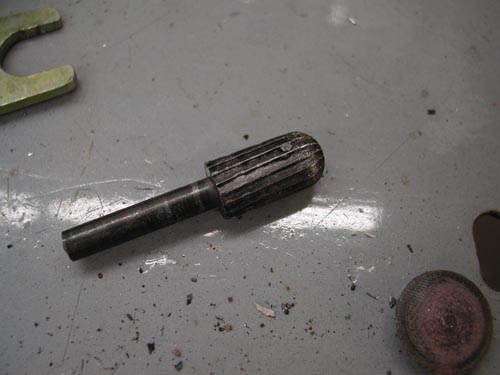
After Bill welded the bung into place it was my job to grind the welds down and ship the tank to Foremost Powder for a clear coat. I hit the big spots with a grinding tool. I tried my damnest to take only meat off the welds and not off the surrounding tanks surface.
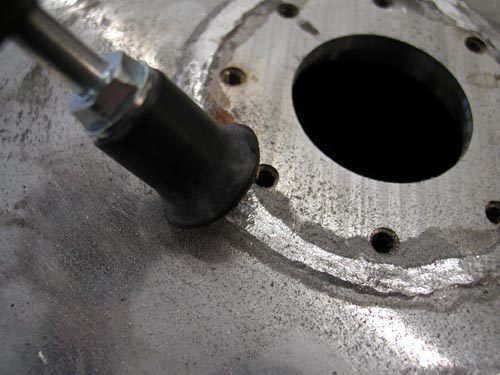
Next I used small emery discs to carve at the aluminum bead. I also smoothed some of the welds on the front of the tank where we filled the tunnel for additional gas capacity.

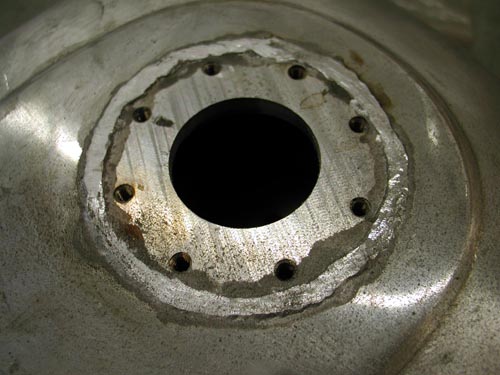
This shows the different grinding phases to reach a level that’s still strong with weld bead but handsome enough to live with. This was an interesting effort, since no bondo or thick urethane would be applied, covering a myriad of mistakes. This was the final stage before clear powder from Foremost in Gardenia, California.
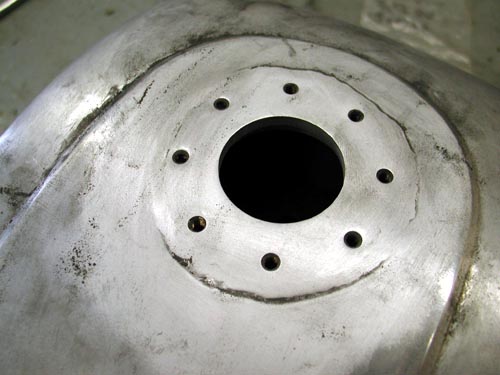
After this stage I polished the panels of the tank and hauled it off to the powder masters. There’s one other process I need to explain. I made every effort to clean the tank of debris and shavings. I also made sure to run a gas filter. I still had problems, which I will explain in my Sturgis Saga. They were easily remedied through Lee Chaffin at Mikuni. Just needed to dial the right number.
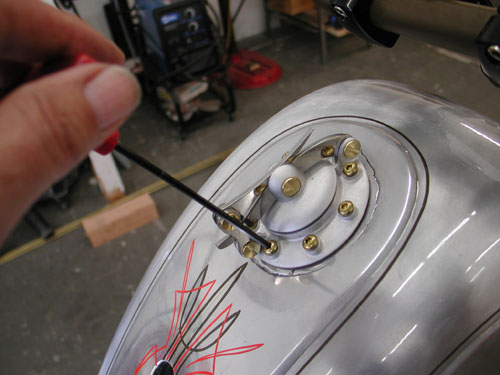
This shot was taken after powder and pin striping when I installed the gasket, decided which direction I wanted the cap to face and screwed the brass fasteners down. The cap worked flawlessly all the way to the Black Hills.
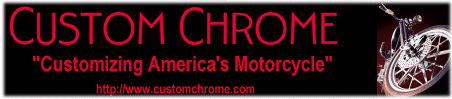
Sturgis Shovel Part 1
By Robin Technologies |

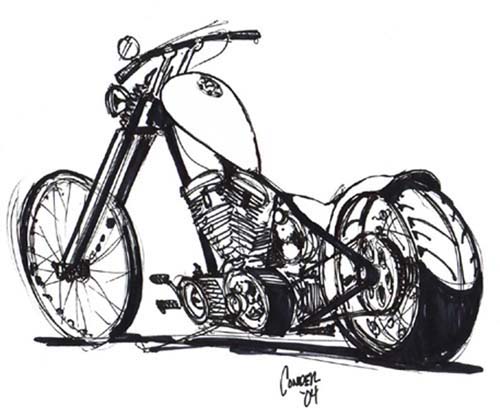
We're starting another project at Bikernet, the Ultimate Chopper. I dediced that title was bullshit. I look at some of the bikes built nowaday and mine pale by comparison, so screw it. It's the Bandit/Sturgis 2005 Chop. It's been a couple of years since I built a bike for myself. Hell, I can't ride the shrunken FXR, it's too small. Besides I need a rigid chopper for everyday flying. I gotta tell ya, I love choppers, like women. They're sleek, slim and move with an indescribable grace.
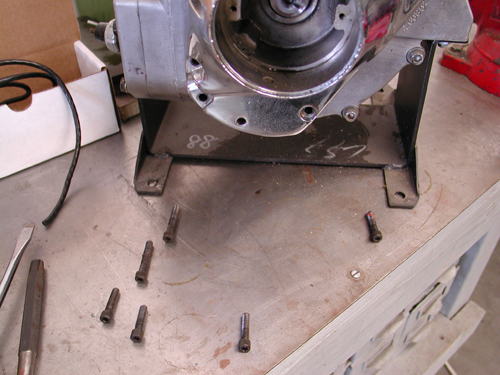
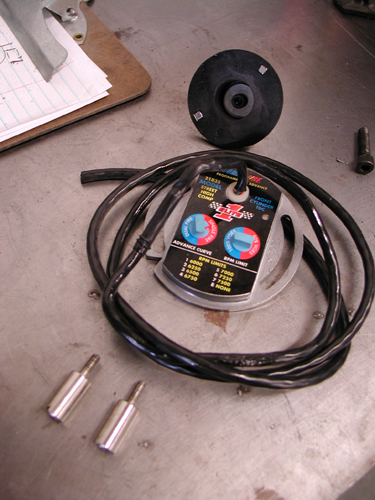
Here's the design notion. No we're not trying to compete with the Martin Brothers, Paul Yaffee or Matt Hotch, who are all master craftsmen and artisans in the custom motorcycle world. They are incredible and I have the utmost respect for each one of them. I'm sorta Indian Larry West. I want to build a light agile chopper for the ride. I'll attempt to explain. I've been riding choppers most of my life. I've tried out many styles, but consistently come back to the mighty light weight chopper.
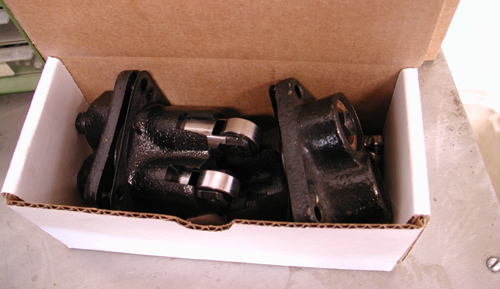
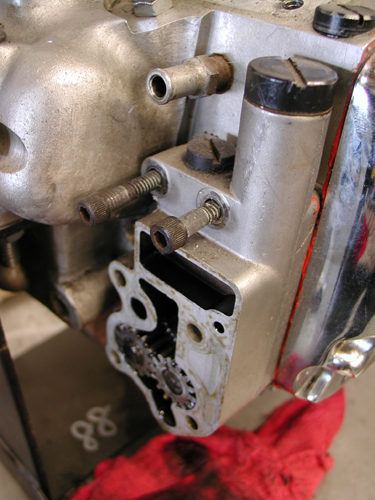

Let's get specific. I needed something stretched to fit my 6-foot, 5-inch frame so were going with a stretched Paughco Rigid with 4 inches in the downtubes and 3 in the backbone. But I'm sticking with a very moderate rake of 35 degrees for handling. I'm running a 9-over light tapered leg Paughco springer for class and city handling. I'll run my traditional Custom Cycle Engineering risers for limited handlebar vibration and traditional appearance.
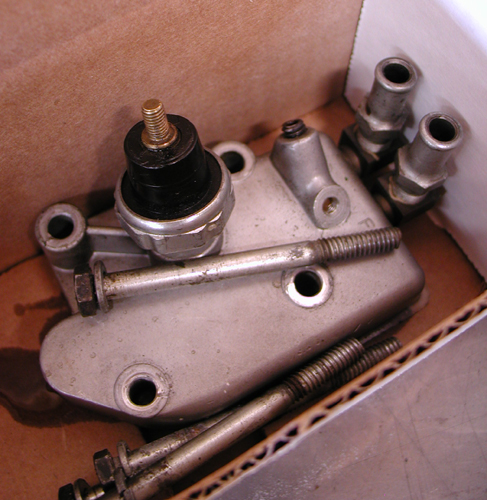
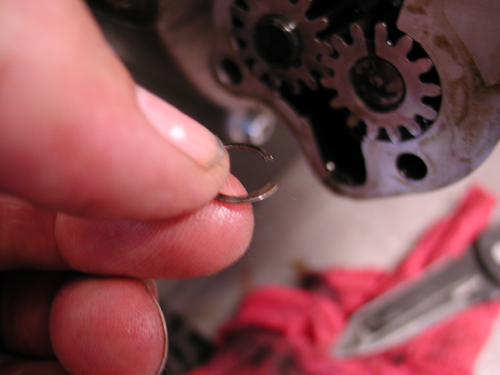
One of the notions is to make this bike a very reliable, rideable chopper for long hauls, maybe to Sturgis next year. I would generally run a 96-inch Evo to fit the rule, but this time a brother, Richard Kransler cut me a deal on a Shovelhead engine with 3 5/8 bore and 5-inch stroke. That over 100-inch monster would tear this bike apart in short order so I called S&S for advice.
We're going to roll with a tried and true S&S formula for street power, reliability and balance–same bore with 4.5-inch stroke will give me 93 inches of grunt. I tore the engine down for modifications last week and shipped the lower end to Viola, Wisconsin for a S&S blessing.
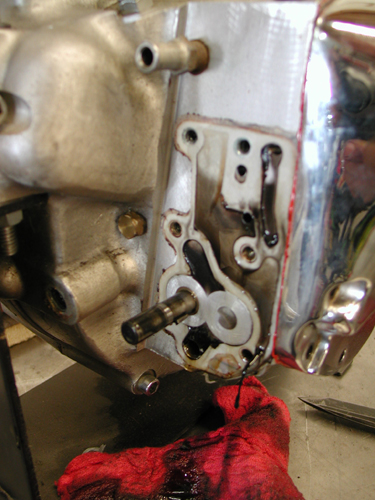
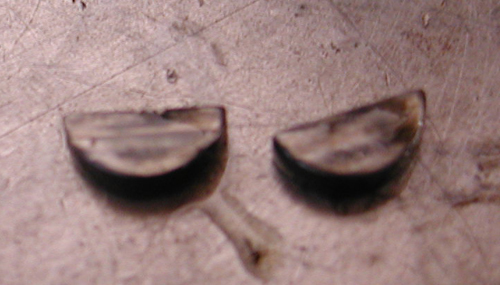
In keeping with the chopper code of the west, no fat assed tire will cramp the handling. I'm going with only an Avon 180/18 and a 21 on the front. No wild billet wheels but clean Custom Chrome polished aluminum rims and 40 stainless steel spokes. This bike will have a touch of chrome, but not much. I'm going to start a bin of Stainless Allen fasteners to take care of assembly.

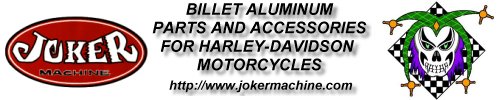
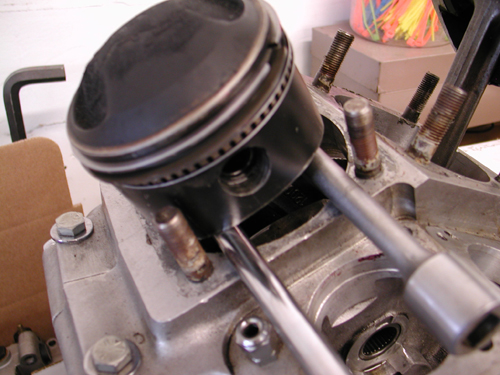
I'm not going to run anything that sticks out from this bike, no sidemounted license plate bracket or wide bars, just tall risers and what I call TT bars that I will narrow for splitting lanes on LA freeways.
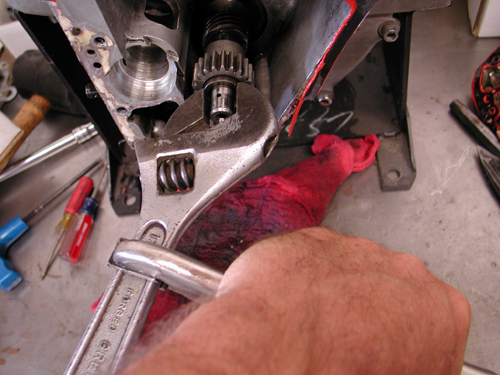
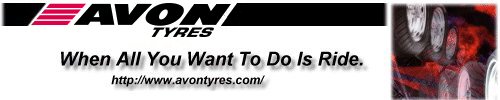
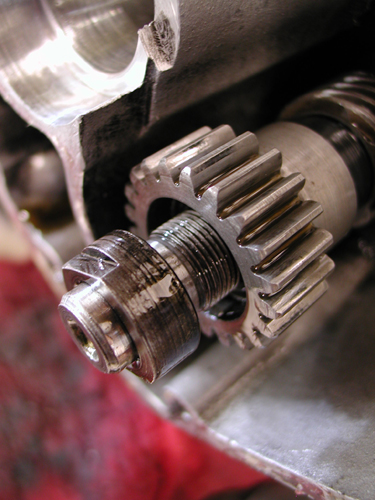
I may use a flush mount Sporty tank, or perhaps a Cyril Huze job like the one on the Shrunken FXR. What a sharp tank. I'll use a BDL belt, Compu-Fire alternator/ regulator and single fire ignition for reliability. We're mounting Kraft Tech fenders and oil tank, making our own pipes and brackets. Dewey's custom pegs will be used because they're light and contain just enough rubber to keep vibration away from feet and hands. The foot and hand controls are all Joker Machine for true reliability and simple clean design.
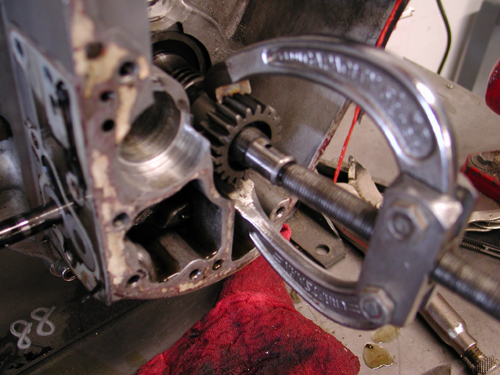

The Jim's 6-speed overdrive tranny is waiting a Custom Chrome Sprocket and Rev Tech O-ring chain. Finally I'll research the best possible sprung seat for comfortable, vibration free ride.
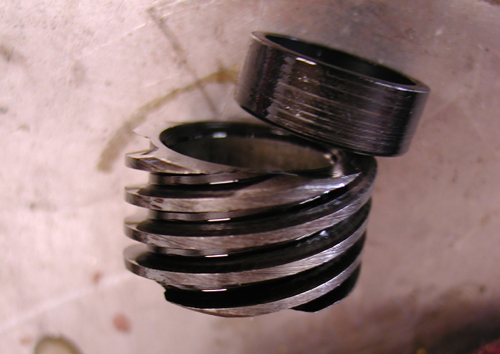
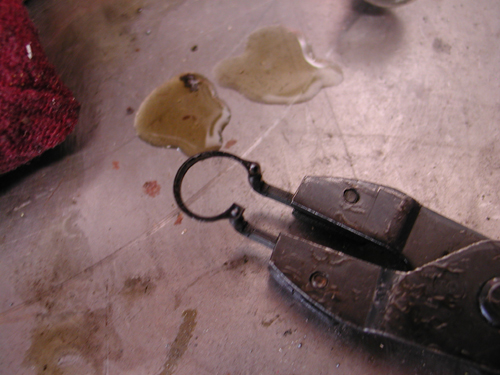
We're shooting for a bike that will be solid for the long run. It'll run strong, won't vibrate to shit, be reliable enough to ride to Sturgis, a street fighter in the old school fashion. Not a lot of flash, but tremendous class. Watch as it comes together right hear on Bikernet. Oh, I've got a couple of tricks up my sleeve that will be revealed as we turn this pile of parts into a running gargoyle.
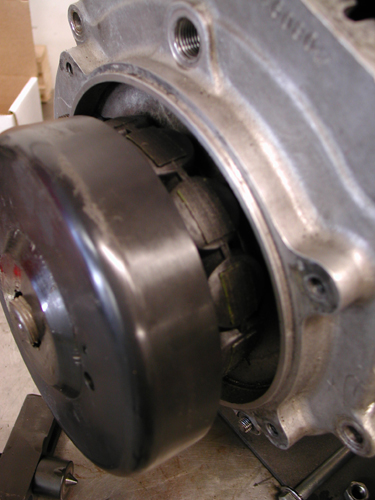
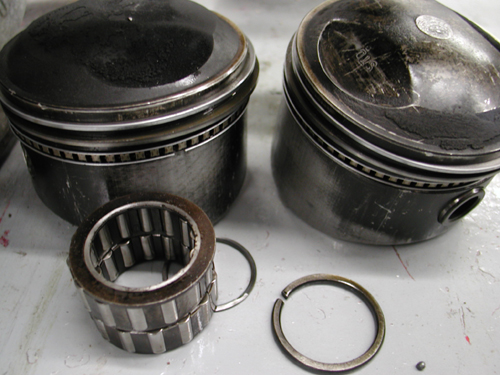
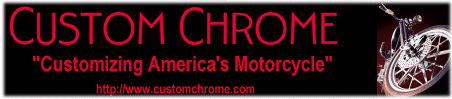
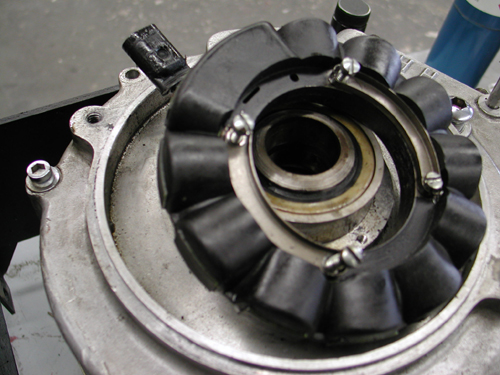
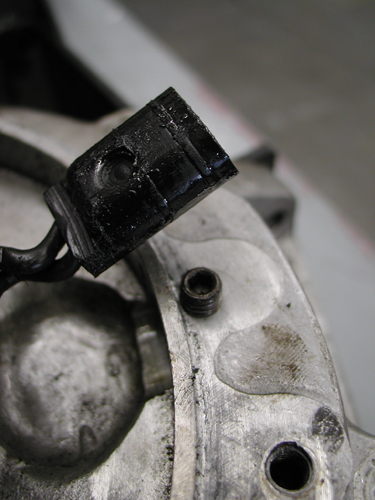
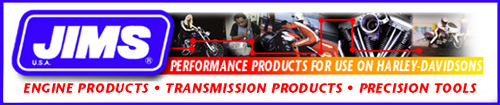
1928 Shovelhead Project Part IV
By Robin Technologies |

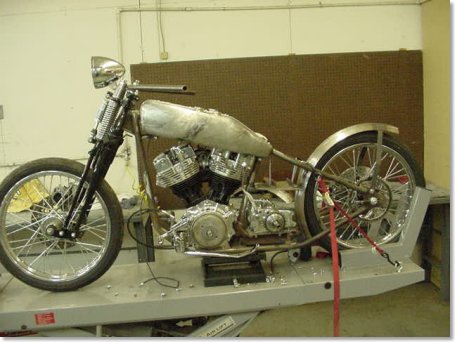
One of the best aspects of building bikes nowadays is the integrity of the components. If you get the right mixture of components together and take care with the wiring and assembly, you’ll have a bike as reliable as factory stock. That’s one of the reasons Bandit has moved to using Compu-Fire electrical components on most of his bikes. First, because even he can install them, and most of all, because Compu-Fire has been building electrical components for years. The stuff doesn’t break.
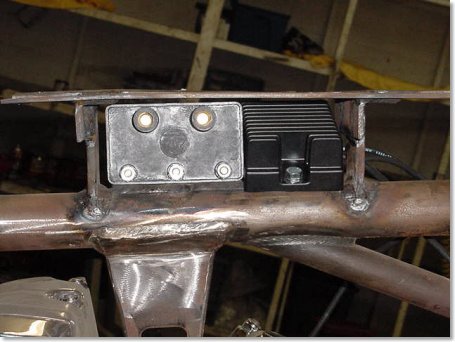
Take, for instance, this charging system. The stator slips firmly in place over the engine sprocket shaft race area and Compu-Fire suggests that you use the stock fasteners with a drop of red Loctite to ensure it won’t ever come loose. Compu-Fire alternator plugs are the protruding variety from the late-model design. Carefully oil the plug and slip it into place, then replace the plastic bridge and fasten it with blue Loctite. If you have new cases, make sure there are no sharp edges on the plug opening. File if necessary. Then with the shaft seal .090 shim in place, use a wire feeler gauge to determine that you have at least .060 of clearance between the rotor and the case.
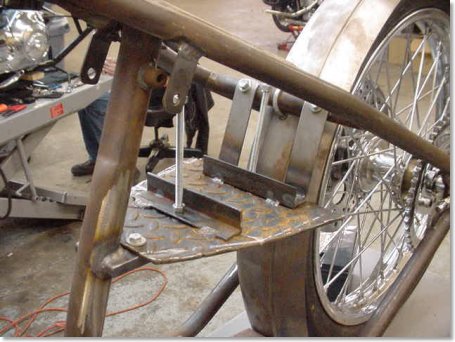
With each Compu-Fire charging kit for Shovelheads or Evolutions comes a thrust washer that goes on the outside of the rotor on chain primary systems. It may not be necessary on belt drive primaries. Mr. Gillihand from Compu-Fire recommends that you have a direct ground to the engine cases. Compu-Fire charging systems are the series type, unlike the shunt variety. The difference is that a shunt type drives the charge to ground if the battery is satisfied, causing the alternator to heat up and constantly work. The series type shuts the stator off when the battery is satisfied, which allows the unit to cool. The hot wire goes directly to the battery through a circuit breaker, or to your ignition switch on the hot side. In this case, the regulator was positioned with the coil between the tanks so the plug wire had to be extended.
That covers the basics of installation. Now here are the specs: Compu-Fire manufactures two versions of its charging kit, a 32 and 40 amp. From 1970-’75, stock charging systems were rated to 15 amps; from 1976-’80, they were 17.8 amps; between 1981 and 1988, they jumped to 22 amps; and finally, in 1989, skyrocketed to 32 amps. Now fuel injected models run 38-amp systems. So the two systems cover the lot.
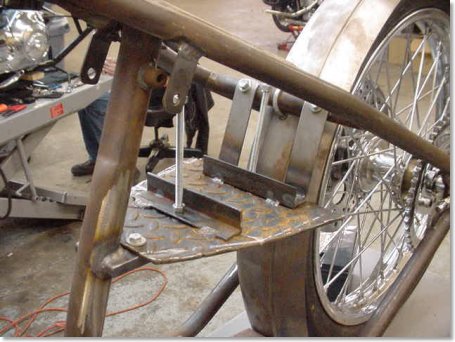
We’ll get into wiring after paint and chrome. The ignition system is Power Arc. The timing module is in the nose cone and the coil is also positioned under the seat with a chunk of angle iron. This system is about as clean as you can find.
Next week we’ll hit the final sheet metal as we close in on paint and chrome, and the lovely Princess Lena, daughter of the rich and powerful Rick Fairless, king of the Strokers Ice House plantation, makes her move on the hapless Bandit. –Wrench
Mudflap Girl Part 1, the Concept
By Robin Technologies |
Life is nuts, or is it just me? Fortunately, we have motorcycles and women to chase. And this year became the year of the Evo, the FXR, and the mudflap girl. I’m scratching the back of my head and wondering how to kick off this build for 2011. There’s a lot on the plate this year and it’s a tad difficult to explain. First, I must fess up. I’m turning 63 this year and no more riding rigids to Sturgis, or even chasing young broads. Ah, but the adventure continues. It’s actually a blessing not to be hassled with women troubles. I’ll let my son, who just turned 37, deal with the addiction to soft curves. I’ll hide out and watch…
The solution for my missing long distance rider was an FXR, and I have one, the John Reed V-Bike that I took to Bonneville in 2006 and set a 141-mph record with a top speed over 150. Unfortunately, I have a hip problem and can’t ride mid-control bikes anymore. I even modified that puppy, but that didn’t do the trick. I love that bike. So, what the fuck was I going to do?
Okay, so I started to piece this bike together. We factory re-manufactured a ’98 Evo engine and JIMS rebuilt the transmission into a six-speed. I had a couple of Renegade Wheels and Progressive Suspension shocks. Then I had a conversation with Kenny Boyce, the man who designed the Pro-street FXR frame. He wasn’t happy with now-defunct Quantum. I also found out that some of these frames break in front of the seat area at the backbone. The project was moving forward with a Custom Chrome, super-wide, upside down front end, Aeromach risers, and we added super wide, Burly bar highbars.
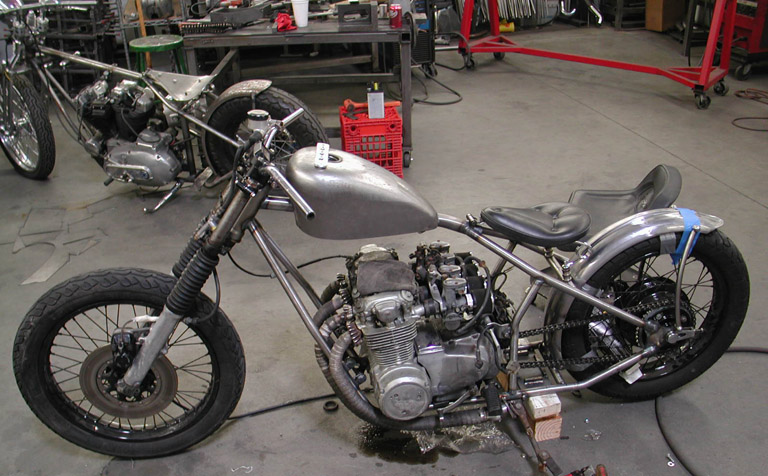
I even had an aluminum mudflap girl oil tank I ordered from Nick at New York Choppers. The bike was leaning toward a pro street touring model with a set of Redneck Softail fiberglass saddlebags and a Klockwerks touring bike rear fender.
I was rolling when Kim Hottinger called and asked if I could haul my old ass out to the American Built/Spitfire manufacturing facility in Rancho Cucamonga, California. Paul Cavallo was the engineer/manufacturing guru behind Hellbound steel. As we watched the production chopper industry dry up, in the wake of a floundering economy, only the diehard survived, and I wanted to support anyone who understood the code of the west.
The brothers who love motorcycles, choppers, bobbers, and custom parts continued to jump up every morning and do what they adore, work on motorcycles. Some went from building hundreds of bikes every month to a handful, but they kept building. Paul downsized and kept rolling with his father at his side. When I saw what he was up to, I was inspired. He can build any frame, for any motorcycle configuration, so my mind went wild. We could build a Frisco’d and stretched, single-loop FXR, and I dragged an old Durfee girder out to his facility so Paul could see how the master built the originals. Imagine an FXR with a state-of-the-art girder.
Paul is a wild man when it comes to building and manufacturing anything. He re-engineered the girder and refined the looks, and added two shock mounts to incorporate a state-of-the-art front suspension. Over the next year, you’re going to witness Paul’s Spitfire abilities with features in several national magazines, and you’ll begin to see his products pop up in Custom Chrome catalogs.
The more we moved forward with this bike, the more inspired I became. This was a bike for me, maybe the bike for my old-guy riding future, now that my Road King was down the road. So I went to Paul with the deal of the century: build two of these frames and front ends. I spoke to Paul, then to my son.
There had to be a goal behind this effort. We would ride to Sturgis together. Shit started to happen fast and I ran into a TV producer who wanted to follow the build, and Leomark studios got involved.
Next, I reached out to Chris Kallas and we started to work up a concept drawing. Here’s some of the e-mail that flew back and forth.
Here’s my initial description:
Frank’s bike: classic black mag wheels from Metalsport. Klock Werks rear dresser fender on Frank’s, might bob it. Both wheels will be mild width. Mudflap girl theme on my bike and Hardball tattoo on Frank’s. Paint reversed from Frank’s bike to mine. Forward controls on my ride, Frank’s will run mid controls. Rubber pegs, grips. dog bone-style tall rubber mount risers. Shotgun pipes. One Redneck bag on the left of Frank’s bike. We also talked about a small front fender.
–Bandit
Some questions?
Black and chrome or silver Evo engine?
Your wheels? Mag or spokes, what kind?
Style/brand of headlight, tail light?
The risers are the type with rubber mount at top?
Carb/aircleaner?
Shot gun pipes, staight, no mufflers?
Style of seat?
Your fender the same not bobbed?
Brakes? Dual or single up front? What brand of rotor/caliper?
If any of these things aren’t specific yet, they could be semi generic on art.
If you can send any photos or links to of fenders, wheels, bags, brakes or controls, it would be helpful.
As for paint, just a thought.
It looks good with lots of black or aluminum, and chrome.
It also looks good with your signature orange accents or striping. Since I’m not crazy for white frames, they could both have blue frames and just flop the two-tone paint on the tanks and fenders.
— CK
Here’s the basic FXR platform showing the frame modifications.
This is with a 3″ extended swing arm.
I need to go back and recheck some measurements but it will give you a
rough idea of the stretch up front.
Is this the type of exhaust setup you were thinking of?
When you said shotgun and 2-into-1, I wasn’t sure.
— Chris K.
I think we should go with this type of exhaust, if we plan to pack passengers. I’m going to ask Dar about that swingarm, but my tendency is to extend it about 1.5 inches, not 3. The stretch looks great. Let’s fuck with those fender rails, arch them, or make them disappear and bob the fender slightly. Plus I think we will need to lower the rear at least an inch, with shorter shocks.
–Bandit
Hey, here’s my first crack at putting it all together. Overall the stance looks good. Since it’s a rough draft without much decoration, I just threw a couple
of mud flap girls on it. I thought I’d try a traditional Sportster/FX headlight with it’s rubber- mounted bulb to stay with the theme of using rubber pegs, grips, and
rubber mounted-risers…. not to mention a rubber-mounted engine, plus I like them.
The frame tube behind the shocks creates a challenge for curved fender struts. I’ve included a couple of photos of some frames so you can check out that area, plus for general interest I tried mounting the tank higher (Frisco style) but thought this looked better.
You might use a semi-later model Sporty tank (when they first started making them larger but still had a carb).
I don’t know at what angle or how Spitfire plans to deal with the secondary neck brace under the tank, so just drew it how I thought it might go.
When you said a Fantasy in Iron tear drop air cleaner I took that to mean a plain Goodson (no rib), for engraving. (We now have a Roger Goldammer air cleaner for Frank’s bike)
Since you need to run a front fender, I made it small. I like when they show most of the top of the tire.
Questions:
Who’s handlebar and foot controls do you plan on using?
How about brake calipers?
–CK
Hey, Chris,
I feel like I want more attitude. How about the tank mounted in line with the bottom of the top bar and stretched a tad at the back to more of a point? Take out the stress bar and add a gusset there with a mudflap girl cut out.
Check the news. I ran a shot of the air cleaner, but you nailed it. Did you check out the heavy green flake and silver bike? I like that theme. My bike will have a plain engine. I thought that style worked well with the plain silver, driveline. And I liked the green springer to match the frame.
We don’t need to go with green. It could be almost anything and silver, then reversed for Franks, with a silver frame, and colored sheet metal.
–Bandit
If the Redneck bags wouldn’t fit, we looked at what Bob T. runs on his fantastic RT.
Part number for bags:
’87-90 FXRS conv bags
H-D 90702-89 left
90703-89
As you can see we are flying at this effort. Don’t miss the frame build in the next segment. As it turns out Frank and I will be running the same drivelines: JIMS six-speed transmissions and Harley-Davidson Evo engines.
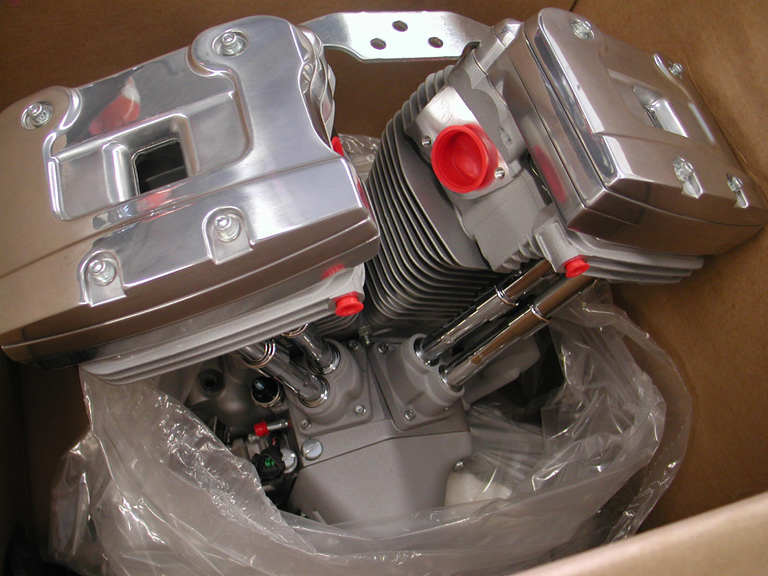
Sources:
1928 Shovelhead Project Part 1
By Robin Technologies |

In an effort to stay tuned with the rapidly growing and ever changing industry the staff of Bikernet began a project Shovelhead several years ago in conjunction with Randy Simpson of Milwaukee Iron and Arlen Ness. It’s been a strange road, but we’re now rolling closer to completion with the assistance of Rick Fairless of Dallas Easyriders and his ace fabricator Jim.

The project began with the purchase of a slightly destroyed Mexican Police bike from Arlen a couple of years ago. He had scored some 300 1984 Mexican cop bikes that had been ridden through several revolutions and costly rebellions. The bikes were shot at, dragged, bombed and ridden harder than any V-twins on the planet. When we first purchased the Shovel complete with police sirens and blinkers, we assumed foolishly that we would restore it to it’s original fighting condition. Arlen even hand picked our unit specifically with our goal in mind.
Well it’s one thing to dream of a restoration, but when the cast iron triple trees are broken, the frame is bent, all the sheet metal destroyed we took a step back and said, Help! We pulled the Engine and sent it to JIMS Machine for a rebuild along with the Transmission. With the cases replaced along with the barrels and heads and all the internals replaced, the engine was ready to rock once more. A similar concoction was mixed for the transmission and a couple of us dressed all in black and prepared to bury the chassis in a shallow grave in the desert outside of 29 Palms, California when the Editor of “Biker” pointed out that we had a valid pink slip. Dean, salivating, over the dying chassis took the entire unit and paid us handsomely for the paperwork. We suspect that he made a rocking chair out of the frame and wheels. During one of our weekly Bikernet meetings we discussed what to do with the Shovelhead drive train, and in the process we started discussing various options and some of the customs we respected the most. Several suggestions were thrust onto the rusting boardroom table. First Randy Simpson had volunteered to help us build an old time looking bike from the remnants of the ’84. We voted unanimously to pursue this avenue, since we had always been impressed with the workmanship and design Randy injected into his own 1928 Shovelhead projects, and he had a desire to create a simple chassis kit to build one of these puppies to market to the public. We agreed to help him promote the concept. We also all agreed that a gesture to the community of San Pedro was a necessity since several members of the staff had been arrested and the headquarters were constantly under surveillance, so we decided that Bikernet needed its own private San Pedro Police bike. How else could we crash the local parades. Randy is a persnickety builder who takes great pains to build quality parts for the market. Two years passed and he still didn’t have the frame built. He was obviously so successful with his growing line of fenders that his chassis concept was slipping onto the back burner. Arlen Ness was also taking giant strides to build a similar machine and if you picked up a recent Easyriders you would have seen the fruits of his labor in his 50/50 Shovelhead. In addition Chrome Specialties with the assistance of Chico in Southern California had recently completed a similar project around a Sportster (It’s called Trick and is featured on Bikernet right now). The competition was stiffening. Randy dropped out, and we moved ahead, and with some research we discovered that a number of reproduction parts are being built in Europe for early Harleys. Early like in 1915.
Devoted to successfully completing this project we picked up a rigid frame from Paughco. This is a standard scale Paughco Rigid for Shovelheads. From there our old part contact was Fred Lange in Santa Maria California. Fred informed us that a European group is remanufacturing 1915 springer front ends, flat track tanks, headlights, fenders and Fred was making appropriate sprung seats for these models. We were in business. We ordered the flat track tanks, the fender for a side car so it could be used for the front and the rear, a hand leathered seat and snuck out of the hills over looking Santa Barbara.
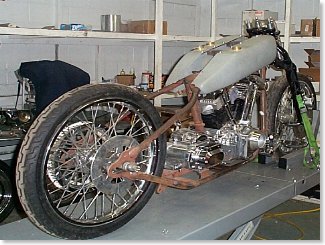
We had a Bad Boy front end, Wheels, etc. We’re in the market for some Custom Cycle Engineering lowering rockers. At that point we needed miscellaneous parts, pipes, etc., and we could get this puppy on the road. It was time to call in a favor. Rick Fairless had purchased the exclusive Bandit I Pat Kennedy Built bike from Bandit and part of the deal was parts and labor on a bike project in the future. It was time to call in that note. Then in a stroke of bad luck and good, Marty Ruthman decided to close his shop abruptly due to health problems and he had a massive sale.
–Wrench