Bikernet West – Electronics in a Weekend
By Robin Technologies |
![]()
Wiring is the nemesis of man, the puzzle of the best builders, the hornet’s nest of breakdown treachery. Bandit sat for hours drawing a wiring schematic for Agent Zebra’s Softail, only to rip it to shreds and toss it in the trash. He made lists while Sin Wu brewed strong coffee and baked peanut butter cookies. Bandit barked and growled for a couple of days with each run to the marine store for connectors, to the electronics store for switches, to the Custom Chrome catalog for components. The same formula fit his own West Coast entry in the Sturgis Bikernet Chop-Off. We knew as soon as he mentioned that the bike was ready to wire, that we should pack our shit and leave. We took the case of Jack fifths, the girls, and checked into the nearest fleabag motel. While we sat around the stanky pool and partied, Bandit thought about each wire, each connection, and each component. His mentor, Giggie from Compu-Fire, was his only sounding board and the only sonuvabitch big enough to snap back when Bandit growled about wire gauge or lost connectors. He wired the bike entirely with 14-guage wires. The only other sizes used were for the battery cables (stock units) and the wire that ran from the battery to the ignition switch (12-guage). Even when the sexually starved statuesque Asian roamed into the garage with cocktails, adorned in a sheer negligee, she was ordered back to the headquarters. Soon she found another plaything to keep her occupied, but that’s another story. Wiring, in the big guy’s mind, is a process of understanding what is happening with each component, where each component is located, watching for the safety of each wire, keeping the bike sanitary, and organizing each group of wires. Each wire is covered with shrink tubing, each connector supported with additional shrink tubing. Each bike had a minimum of wires carefully placed. Each bike had a minimum of components to keep the wiring process uncomplicated or enhance the reliability of the machine. No turn signals, no handlebar controls, and no micro switches. He used only millspec (military specifications) or marine quality switches. Vibration is a killer on motorcycles and much the same on boats, in addition to the moisture considerations. One additional component made wiring simple and risk free, the Custom Cycle Engineering starter mounted mechanical switch. (Check the article here in the Garage.) This unit eliminated the starter button, the starter relay, and all the associated wires. You must make sure you will have access to the switch, which is mounted directly on the starter, under the oil bag, (Photo 2) which can easily be interfered with by the position of the exhaust pipes.
![]() Photo 2
The concept is that you physically push the solenoid into contact with the starter gears and electrically engage the starter. We chose a Compu-Fire starter from Custom Chrome to kick this 98-inch monster to life. The key thing on fucking up starter motor installation is over tightening the brass lug wire fitting. It may turn the connection on the inside of the starter and ruin the contacts. Compu-Fire has designed a new line of starters which feature 6:1 gear reduction (Photo 3) and a 6-pole permanent magnet field to eliminate starter stall-out.
![]() Photo 3
These units deliver maximum cranking torque without overloading the battery. They also eliminate starting problems on fuel injected bikes. Only two switches were used and one 30-amp H-D (common at any electronic or auto parts store) circuit breaker. One on-off marine toggle for the ignition, which energized the Compu-Fire single-fire ignition system, the hydraulic brake switch, and the taillight. Since all the sweet parts like handlebar controls, foot controls, mirror, and taillight were Joker Machine components, he was in luck. Joker works the brake light switch into the body of forward controls, which eliminated the bulky hydraulic switch, the junction, and a two-piece rear brake line. Another wire went to the other switch, an on-off-on switch for the headlight (high/low beam). Two wires were run from it to the headlight. Daytec does a beautiful job of running guide tubes in the frame to hide the wires. Initially, if you chose to do so when ordering a Daytec frame, you can have two inserts welded to the frame seat post rail for electric box mounting. We ordered the certs for this frame but decided that with the simplified wiring program we could stuff switches and all the wires into the structure of the top motor mount. This was Giggie’s suggestion and Bandit readily agreed (a miracle). With careful measurements the switch holes were drilled with several bits until a 1/2-inch hole for each switch was attained. The only guide hole that the frame was missing was one for the headlight wires, but two wires were run through shrink tubing to the headlight and through a 5/16 hole in the motor mount. One wire was run from one side of the ignition switch to the circuit breaker, another, the 12-guage wire ran to the battery. From the circuit breaker a wire ran to the taillight down another guide hole along with the brake switch wire. From the brake switch another wire ran to the taillight, brake element. We also used a Compu-Fire regulator, which mounted to the front of the motor. One wire ran from the regulator back to the hot lead on the Compu-Fire starter motor. Bandit used the excess 12-guage wire to run from the battery to the hot side of the ignition switch. Giggie recommends that you use crimpers designed for Duetch connectors for a solid, vibration-handling connection. Bandit used water resistant connectors from a West Marine store. After some 20 hours in the garage, Bandit was finally lured into a well warmed King size bed by Sin Wu and her girlfriend Coral as the sun came up, but at that point the bike was ready to be fired to life. The question was, could Bandit be fired to life? –Wrench
|
Bikernet East Installment 5
By Robin Technologies |
629 E. Sunrise Blvd
Ft. Lauderdale, Fl 33304
“I’m thinking of having a painter do up the bottom of the bike with some radical paint design because the fucker is so damned fast with this S&S 113 that it brings the front end off the ground in second gear. I’m not kidding. I had to switch it back to a chain from a belt, because the belt would just sit there and whizzzz, spin like crap and fry.”
“The customer is completely nuts,” Eddie Trotta continues, as he closely examines a gorgeous, low-slung chopper which he hand built for a local Fort Lauderdale, Florida client. “The fuckin’ guy, he walks in here, I let him take a ride, he comes flying back in and says, ‘Jesus Christ! That’s the best running motorcycle I’ve ever ridden! How much?!’” “I tell him ‘$40,000, he writes a check and then, then the crazy motherfucker spends the next half an hour, eeeeeeeeeeeeowww! ZZZZZoooooommmm! Back and forth, roaring up and down the street out front like he wants to kill himself on this fast damned scoot. We’re all in here watching with our jaws on the floor and this guy’s outside going completely nuts. Finally, he comes back in grinning like a lunatic, the thing’s smoking like crazy, the back tire’s fried and he laughs and says, ‘I gotta let you guys know, I ride pretty hard. This thing has to be bullet proof.’ I asked, ‘Can I give you your money back right now?’ And he says, ‘Hell no! I love this thing! It’s tough as shit!’” Eddie lets out a casual laugh as he pulls a massive hunk of turf out from under the bike. “What’s this?” he asks incredulously looking at what appears to be golf course sod wedged under the bike. “What the hell? I think he’s taking this thing off road! That crazy bastard. He came in here the other day with a tiny crack in the back fender. Turns out he JUMPED the sonofabitch with his old lady, some broad who’s huge and he actually cracked this fender. Feel how thick this thing is! That’s the heaviest fender made in the business. I gotta get this guy a slower bike or a lighter old lady. Or a shorter ramp. He’s totally nuts.” I feel the metal and it is a really heavy fender, a beauty. “He jumped it?” I ask, thinking I must have heard wrong. “Yes! I’ve fixed this tiny running light down here behind the pipes at least 15 times. That’s a $100 light. I’m going broke off this one light!” Eddie says laughing, examining the light closely. “I don’t know how the hell he’s doing it, probably has flames shooting out of the pipes and he’s melting it or something, shit I don’t know. The guy owns 53 businesses, he’s my roughest riding customer. Totally nuts. I fix it all for him for free. I stand behind my choppers. Once in a while he puts up a new gutter at my house. It evens out.”
Good customer service? You be the judge, but by my standards, that’s going above and beyond. Stands to reason. If you want a gorgeous custom chopper and I mean gorgeous by the most rigorous show standards, a no-nonsense, built to ride, powered by beat-the-motherloving-crap-out-of-it equipment like RevTech engines and Baker trannies, Eddie Trotta at Thunder Cycle Designs is the man. Eddie’s is one of the nation’s premier custom motorcycle builders, specializing in one-of-a-kind choppers. He started building in the 70’s and opened his shop, Thunder Cycle Designs in Fort Lauderdale, Florida in 1990. Currently he has around 50 custom bikes for sale on his showroom floor at any one time and there is nothing that he can’t build for a serious customer.
“My bikes average about $40,000,” Eddie tells me as he cranks up a gorgeous new chopper with a stunning paint job. The big S&S 113 rumbles to life. “Sit on it, tell me what you think of this shape.” I gladly get on and the long, elegant monster fits like a high-speed glove. This is what it must feel like for a fighter pilot to slip into the seat of a well-oiled F-16, I think. “I try not to price my motorcycles into dumbass numbers,” Eddie says.
“Which some other builders do. My goal is to make an incredible, unique chopper for my customer and sell it to them at a reasonable profit and have them ride the crap out of it. These bikes aren’t built for trailers. I build them to ride. Sure, they look pretty, but they run like motherfuckers. I have some customers who trailer from show to show and that’s okay, but I still build them with the components to ride and ride hard. These are motorcycles, not art. They might look like art, but first and foremost, they’re hardcore machines.” “And now we come to Zebra chopper,” Eddie says, winking. We walk up to my new chop, the Great Northern Steamer, my entry into the fierce Bikernet.com Chop-Off competition for Sturgis 2000. This will be the horse, which I try to beat the mighty Bandit with, out on the West Coast. Taking on the Godfather of motorcycling isn’t an easy task which is why I’ve called in the master, Eddie. “I’ve taken the fender off and re-cut it. It was okay the way you had it, but we made it better, hugs the tire tighter. Eddie Meeks, at Hardly Civilized is painting in the artwork (5437-A Church St., Greensboro, NC 27445, 336.545.9064) now,” Trotta says. Eddie Meeks, one of the top painters around, was kind enough to light up his spray gun and blast off a paint job in just under a week, including curing and shipping time. “I put on a different kickstand, rear passenger pegs, we’re going to raise the bike a bit as well. I might change out these brakes on front, put on two small calipers instead of the one big one. Not sure yet. We’ve taken off the back tire, checked all the alignments, double-checked all the rear end, it looks good. This is the seat. It’s a custom job, made from a nice tan leather that fits perfectly and matches your paint.” Eddie shows me my new seat, a hand built beauty, which ends in a fine dovetail over the bobbed fender where the lass will perch. “You’ve got a great tranny with this Baker six-speed,” Eddie continues, “which is what I use on my bikes. These RevTech 88’s are beauties, too. They’re strong and smooth. I’ve had no problems with either the Bakers or the RevTechs, and you know how my customers ride,” Eddie says, rolling his eyes. “You don’t plan to jump the motorcycle, do you?” “Not voluntarily,” I tell him. “But of course, it is Bikernet, so it would be foolish to rule out such things entirely.” Eddie chuckles and shrugs. “That’s true,” he says, “I’ve known Bandit for a long time and I know better than to put anything past that damned outlaw.” Look for more tech tips coming down from Eddie Trotta and his boys at Thunder Cycle Designs as they finalize the Zebra Great Northern Steamer and the break-in process begins. Eddie Trotta’s Thunder Cycle Designs is located in Fort Lauderdale, Florida. Their web address where you can see Eddie’s entire line of incredible choppers and his full catalog of custom parts (if you don’t see it, call, he can make it), is http://www.thundercycle.com. You can call Thunder Cycle at 954-763-2100. Or, visit Eddie and his metal magicians by taking I-95 to Fort Lauderdale, to Sunrise Blvd, exit, head east over the tracks to 629 E. Sunrise Blvd, which is on the north side of the street, you can’t miss it and you don’t want to. It’s well worth the trip.
Thanks to Eddie Trotta and his boys at Thunder Cycle Designs, RevTech, Burt Baker at Baker Transmissions, Ken Gold at Gold Rush, and Eddie Meeks at Hardly Civilized. Couldn’t do it without you. Bikernet recommends all these businessmen for your biker needs. They’re tried and true. Gear up, grease up and gas up, all you bros out there. The big run is fast approaching. We’ll see you in Sturgis. Ride hard, |
Bikernet West – Zebra’s Chop is in the Lead
By Robin Technologies |
In his sullen mood, he continues to assist his brother Agent Zebra, although some of the parts he’s now bolting on the Agent’s Paughco/Custom Chrome monster look suspiciously familiar. Could it have been an inside job? Could he need cash to pay the rent? Could another psycho girlfriend have taken him for more than his heart? –Snake
|
Sturgis 2000 Project Bike – Bandit II Lives
By Robin Technologies |
![]() |
Each custom motorcycle has a story. That’s one aspect of this treacherous world that sets it apart from stock bikes. Stop any rider of a chop and ask him about his bike and he’ll either punch you in the face or tell you how he started to build his bike, lost his wife and family in the process, and had to sell his home and move into a rented garage in order to complete the project. There’s a story of romance, heartbreak, hard work, and struggle behind any bike. This one is no different.
Now comes another saga, equally terrifying, equally fraught with intrigue and heart. This tale of woe begins five years ago with a project conceived with Ron Simms of Bay Area Custom Choppers. The plan was to build a bike as a tribute to the ’30s. But times changed and attitudes became harsh as the unit came together. The more we worked, the farther the project ventured from the reality of the hard-riding world. |
|
Ultimately, the bike was finished and featured in the February issue of VQ magazine. As a tribute to all who worked on it, we will feature the entire list of talents that it took to complete (…see the partial list of the crew). The sad part of the story is that the bike was ultimately unrideable. Hell, we couldn’t even trailer it to shows without damaging the chassis, and the bike was put up for sale with less than a couple of miles on it.
But we don’t like the idea of selling something that our brothers helped us build and a suggestion was made to turn it into the ultimate ground-pounding, coastal-bar-hopping bastard. We pondered the thought. We kicked around the years it took to build it in its current form, the times we went through, the love that was lost and gained, the adventures, the rides, and the wild times to come. We thought about Sturgis 2000 and what to ride. I spoke to my brothers. We had considered riding old bikes. So the gauntlet was tossed into the ring. Build a rigid flyer from the pieces of the Bandit II and keep it alive, or put dual carbs on a ’48 Panhead and take our time? Ah, but the Bikernet staff can’t proceed with anything that’s status quo, we’ve got to tear the whole enchilida to the ground and start over, and do it with a vengence. At another meeting at Harold’s dive bar in San Pedro while tossing back stout glasses of Jack, a contest was conjured up. Bikernet East (the chicken-shit Agent Zebra who couldn’t hold a job in Los Angeles and escaped to Miami with his European nymphet) against Bikernet West (Bandit himself, riding a Daytec Rigid). Since the homeless, jobless bastard of Barstow doesn’t have a dime to his name, but still writes vile stories about the upstanding members of Bikernet, we voted to build him a bike to ride to Sturgis. Bandit was already tweeking the drawing board with parts from the Bandit II, hence a contest. Bikernet East rides against Bikernet West to the Badlands and we’ll take a vote as to who has the coolest bike that makes it. Yeah that’s right – gotta make it there to be voted on. |
|
![]() Photo One |
As it turns out, we will be able to use the entire driveline from the Bandit II for the Bikernet West rigid chop, including the 98-inch S&S, Simms-built motor (photo 1) and Custom Chrome transmission. It will be placed into one of Daytec’s 4-inch stretched, wide-tire rigid. |
The Harley-Davidson narrow glide (photo 2) will stay with the original Paughco frame for the Bikernet East project and a new long front end will grace, perhaps a Weerd Brother glide, the Daytec chassis. | ![]() Photo Two |
![]() Photo Three |
Two Road Wings 60-spoke wheels have been laced and mounted to Avon tires. The front will be a 21 with a 5-inch wide 18 on the rear. And Bandit picked up a Yaffee sidemount license plate/taillight. All the brakes and controls will remain Performance Machine (photo 3). |
Harold Ponterilli will paint the reincarnated Bandit II cobalt blue with ’60s metal flake silver flames touched off with white pinstriping. The Bandit II will live to fly through the streets of Long Beach, Pedro, and L.A. And perhaps, if all goes as the Lord of Choppers dictates, across the desert into the Badlands this year.
You’ll see the entire saga unfold on bikernet, good, bad or ugly. |
|
Ride Forever, –Bandit |
Bikernet East – An Eagle in the Garage
By Robin Technologies |
Custom Chrome introduces the world’s first rocket-powered Zebra. The power plant of the Great Zebra Northern Steamer for Bikernet Chop-Off 2000 by Special Agent Zebra 05.22.00. The Great Zebra Northern Steamer is to be a biker’s bike. No fantasyland Hollywood bullshit in the way of $80,000 paint jobs or diamond encrusted spokes, no chop-shop hoopla, the Zebra Steamer is going to the root of American bike building, tight, right, fast, and reliable. It’s being built by the rider, with help from Bandit, Wrench, the Chinaman and the torque kings at Casa El Horsepower, in an anonymous garage in San Pedro, California.
These suckers come complete with carb and ignition system. It is literally bolt-in ready when it comes off the truck with any OEM or custom frame that will hold an Evolution. The RevTechs aren’t a cheap amalgamation of aftermarket pieces. The entire system is designed on a CAD (computer assisted design) system, just like the ones used at the big automotive plants. This means you get the latest in engine technology available. Every component is created from new tooling techniques in a state-of-the-art ISO manufacturing plant. But high-tech engineering manufacturing equipment and techniques aren’t any good without great concepts to use them on. Again, Custom Chrome has put its money where its product is and created some revolutionary new thinking in big twins. The RevTech engines use no head or base gaskets. Why? Because they leak and they blow. Instead, CCI uses ultra-high temperature O-rings, which are hard as hell itself. Ignition is computer controlled. They come in 88 and 100-inch displacement. The 88s have 4 1/4 flywheel stroke with a 3 5.8 bore. The 100s boast 4 3/8 stroke and 3 13/16-inch bore. The cases are cut from 356T6 cast aluminum. Every stress point contains added materials for increased strength (read: you don’t walk across the Mojave Desert in August). They also have removable press-in/bolt-in bearing inserts on both the left and right sides of the cases and removable bottom sump-plate permits internal inspection. RevTech’s cylinders have increased fin surface in high-heat areas, for advanced cooling (Fourth of July runs, anyone who rides in New Orleans on the I-10 during rush hour or Miami before or after Christmas day). Steel liners are Perma-locked into the outer aluminum castings. The pistons are cast for controlled expansion, which reduces engine noise and wear.
Special Agent Zebra |

|
Mudflap Girl Part 2, the Bandit Engine and Spitfire update
By Robin Technologies |
Okay, you have the story behind this build, and Chris Kallas is refining the concept drawing. My engine arrived from the factory, and Eric Bennett immediately noticed the return address, in Viola, Wisconsin.
As it turns out, the factory hired the S&S crew to assemble their Evo line of engines. What a natural. I liked that notion all the way around the block. First, it means more American hands in my new engine. Plus, what could be better than to have the best performance engine company on the planet working with the factory on the last and most refined V-twin configuration?
For this crew, and lots of riders all over the world, the FXR Evo is the best of the best. So, for Bikernet, this became the year of the FXR and the Evo engine. I asked the factory about their Evo engine program and received the following information.
A Modicum of Harley Engine History
The first 74 cubic-inch V-Twin engine on the JD and FD models was introduced in 1921 and the 45 cubic-inch side-valve V-twin engine (later to be known as the Flathead) on the D model debuted in 1929. The Flathead engine proved so reliable that variations of it were available on Harley-Davidson motorcycles as late as 1973 (servi-car trikes).
In 1936, Harley-Davidson introduced the EL model with an overhead valve, 61-cubic-inch engine. With increased horsepower and bold styling changes, the motorcycle earned the Knucklehead nickname, due to the shape of its rocker boxes.
New features were added to the 61 and 74 overhead valve engines in 1948, including aluminum heads and hydraulic valve lifters. New one-piece, chrome-plated rocker box covers shaped like cake pans earned this engine the nickname Panhead. The engine introduced on the Electra Glide models in 1966 to replace the Panhead became known as the Shovelhead, again due to the shape of its rocker covers.
1340CC Evolution Softail Engine – Silver and Polished SPECS
Type: 4-cycle, 45 degree V-twin
Bore X Stroke: 3.498 X 4.250
Displacement: 80 cubic inches or 1340 cc
Compression: 8.5:1
Torque ratings at 3,500 rpms: Touring with fuel injection, 83 ft./lb.
Touring w/carb 77 ft./lb. @ 4000 rpm
Dyna/Softail 79/76 ft./lb.
Miles per gallon: 50 hwy/ 43 city with a touring model using a carb
55 hwy/ 43 city Dyna or Softail
Variety and sales info:
1340CC Evolution Softail Engine – Silver and Polished
Since the first single-cylinder built in 1903, engines have been the heart and soul of Harley-Davidson history. Each motor has made its unique contribution, and the V2 Evolution engine is no exception. With the Smart Start Engine Program, buying a new Evolution engine has never been easier. When replacing your Evolution motor, Smart Start offers brand-new, factory-tested engines at an unbeatable price. Choose the standard silver and polished Evolution, sinister black, the classic black and chrome or the silver and chrome finish. Either way, you won’t just be making a new start; you’ll be making a smart start.
16161-99
IN-STORE PURCHASE ONLY, Contact dealer for pricing and availability.
Fits all ’99 Softail models. Does not include carburetor, manifold or timer cover.
MSRP US $3,295.00
1340CC Evolution Softail Engine – Black and Chrome
16160-99
IN-STORE PURCHASE ONLY, Contact dealer for pricing and availability.
Fits all ’99 Softail models. Does not include carburetor, manifold or timer cover.
MSRP US $3,995.00
1340CC Evolution Softail Engine – Silver and Chrome
16177-99
IN-STORE PURCHASE ONLY, Contact dealer for pricing and availability.
Fits all ’99 Softail models. Does not include carburetor, manifold or timer cover.
MSRP US $3,495.00
When my engine arrived, I immediately hauled it in the Bikernet Hearse to Bennett’s Performance for a slight performance upgrade. I needed to let that puppy breath without messing with the reliability aspect. Sharing the same building on the edge of Signal Hill, California is the headquarters for Branch O’Keefe. John O’Keefe worked for Jerry Branch for decades and ultimately bought the business when Jerry Branch decided to retire.
We’re looking at several options for stock engines and for rebuilds. We have three touring models coming together right now, and they are all 80-inchers. One for my son, my factory motor, and Dr. Hamsters 200,000-mile Evo rebuild by Bennett’s.
I’m running the brand-new factory plain Evo engine with the Andrews EV-27 cam and Andrews chrome-moly adjustable pushrods for less flex, a new cam bearing and the Branch flowed stock heads, for 8.9:1 compression, 78 cc Branch-flowed chambers, and 75-80 horses at 2,600 rpms.
The next higher upgrade step from Branch is the EV-51 cam and additional headwork and shaved heads for a 10:1 compression and 85 horses at the same rpms. And finally, a customer can run with an EV-59 Andrews cam and 10.5:1 compression and 90-95 horses. Not bad for never taking the barrels off.
“I like rpms,” John O’Keefe said, “and the new ignitions allow these engines to burn more fuel and bring out the horses.”
The key to all this performance is the headwork set to match the cam, and John O’Keefe has studied this science for most of his life. The key is building a mid-range hot rod without sacrificing reliability.
The first move was to strip the engine and deliver my fresh factory heads to the Branch team. Eric Bennett set my beautiful, plain H-D Evo engine on his clean room bench and removed the top motormount, the top rocker box that came off with the middle ring. We noticed much improved, one-piece factory Teflon gaskets. We won’t mess with them. Then Eric removed the rockers, the pushrods, pushrod tubes and rocker boxes. We also retrieved the new base gaskets to reuse.
Then he removed the head bolts, the front head, and the rear head. I had already purchased the Andrews EV-27 cam from Branch O’Keefe, and Eric and I started to prepare for installation. He removed the point cover, ignition, and cam sensor.
He had a terrific Trock tool for removing the cone cover. It’s always a bastard to try to carve around the narrow gasket surface with a screwdriver or a knife, hoping to find opening and risk damage to the cases or create a leak by scratching the gasket surface.
“We always replace the new factory cam bearing,” Eric said, “with a full compliment Torrington bearing. The factory ran the good ones from ’55 to ’92, then they shifted to a cheapo brand. It’s also not a bad idea to replace the factory plastic breather gear with a solid JIMS unit.”
I scrambled to take notes and photographs while Eric peeled into my engine. He popped a factory set of magnetic tools into the lifter stools to hold the lifters up during cam removal. I wish I had a set of those puppies.
“It’s interesting,” Eric said. “Virtually every stock cam is .060 longer than any aftermarket cam.”
Eric pre-measures the cams and adjusts the thrust washers before replacing the cam, which you will see in the next report, when we study the Branch recipe for performance, the headwork, and modifications. He replaces the valve seats for larger valves, then ports and polished the chambers. You won’t believe the long-lasting components Branch uses.
Then we will watch Eric replace the stock cam with the Andrews unit and adjustable pushrods, and put the whole Evo puppy back together. “Don’t forget to order a top end gasket set,” Eric reminded me as the rain cut loose outside and I wondered if this winter season would ever end. I need a ride.
Then Eric grabbed a JIMS tool and a couple of wrenches and in 30 seconds pulled the cheap cam bearing from the new cases.
“I’ve seen these go south in 10,000 miles,” Eric said. “I’ll never understand why they replaced a perfectly good quality bearing with this junk.”
Just as quickly Eric took an aluminum guide and a mallet and tapped the new bearing in place, another 10 seconds passed, and we were finished.
A couple of days passed and I thought, just maybe my frames and front ends would be completed at Spitfire. On a hunch, I peeled 57 miles away from the coast in the hearse while listening to KJazz on the radio.
It was quiet as I wandered into the vast machine shop, welding shop, bike assembly area and ran into Joe Cavallo, Paul’s dad, who was hunting around the shop for Softail brake anchor brackets. He greeted me and said something about shop organization. The Spitfire and American Made business model has faced serious transformations over the last couple of years.
As I mentioned before, Paul was the partner and manufacturing arm of Hellbound Steel motorcycles. American Made manufactured fast moving products for a bunch of now defunct companies such as WCC. At one time, they were building hundreds of choppers each month, and thousands of products in a much larger facility. During the last year, they adjusted their business model and tightened their facility. They rewired their building, replumbed it with compressed air lines, and kept building products.
It’s tough to stop everything and regroup, scour through boxes of tools, base material, parts, and junk. With a skeleton crew they are still building any frame a customer needs, including big twins, rigid Sporty frames, British custom frames, and even frames for Yamaha 650s and Honda fours. They also build an entire line of forward controls, gas tanks, handlebars, girders, and glide front ends (bowling pin), pegs, oil tanks (a variety of styles), trees and taillights. Paul is the mad scientist of the group. As a kid, he manufactured exotic gun cases.
He’s the kind of guy who will catch a notion in a cup of Starbucks coffee, in the morning and by the evening, he has a new product. It’s not a one-off either. It’s fully designed and configured for multi-manufacturing.
Some of his crew have been working with Paul and his dad for decades, including Larry, who is their master motorcycle assembly guru. He knows it all. “Pull the alternator rotor off that engine before you run it,” Larry told me. “Check the wires for twists or tears.”
I made a note. Then we made our way into the frame jig area to see the FXR frame progress. The FXR fever caught on and there were at least five FXR frames in the making. The first was based on the pro-street configuration with additional gussets, the squished wishbone, for the single-loop notion and 36 degrees of rake for a 2-inch longer girder front end.
They discovered some issues with my request for a V-style frame in keeping with the stock FXR configuration. I also hoped for less rake and a shorter Frisco style girder front end style. Paul was working on my unit with a 30 or 33 degree rake, but he also started building a couple of drop seat FXR frames, including one for himself.
We are also going to try a slightly longer swingarm suggested to us by Dar, the boss of Brass Balls for his FXR configuration. He wanted to pull the rear tire out of the frame some, and I was willing to try it. They are hot after these frames, since Paul plans to ride one on the Diablo run that kicks off on May 5th in Temecula, California and rolls toward the border. Don’t know if we will make it.
The plan for now is to pick up the frames, swingarms, axles, and Spitfire girders, on Friday April 8th. Between now and then, hopefully we will wrap up the engine and bring that puppy home to the headquarters. We are trying to match up these Mudflap Girl FXRs wherever possible, but not always. We are going to run long and short dogbone risers from Custom Cycle Engineering, but we’ve ordered a new set of Raw 2-into-1 performance pipes from Bub for Frank’s FXR, and I’m running a D&D 2-into-1 system. I’m running a Frisco’d and stretched tank and he’s running something completely different. He’s running a Klockwerks rear fender and I’m running something bobbed. I’m getting seriously ahead of myself. See you in a couple of weeks with the next report.
–Bandit
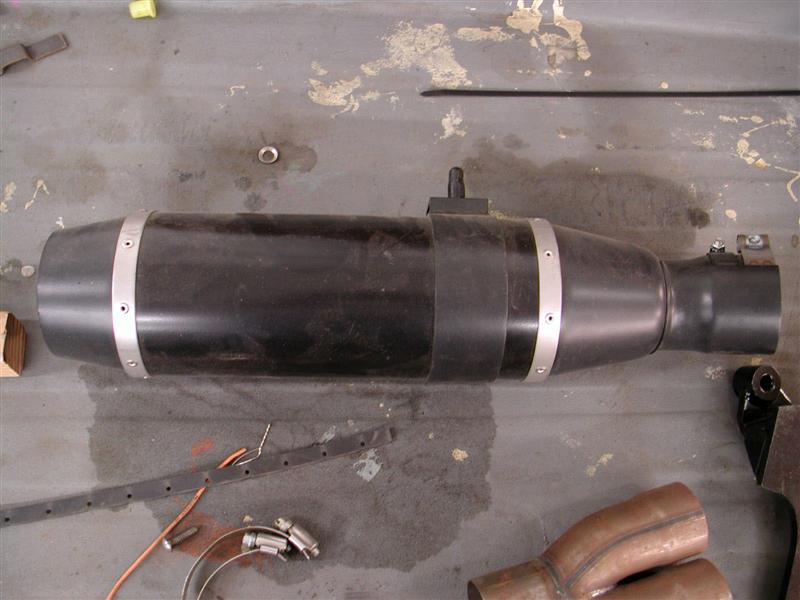
Sources:
Bennett’s Performance
Branch O’Keefe
JIMS
Spitfire
Custom Cycle Engineering
D&D
Harley-Davidson
Rivera Primo Inc.
Belt Drive Unlimited
Metal Sport Wheels
Sturgis Shovel Part 7
By Robin Technologies |
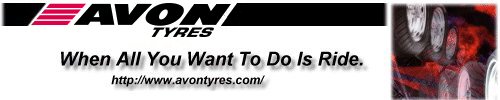
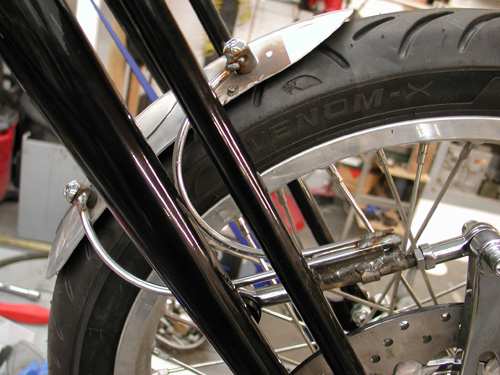
Brembo has a solid worldwide reputation, and I ran into a hot looking Brembo representative at an illustrious bike function and decide I’d give them a try. They’re hot and ready to rock. The only items I needed were the locking nuts for the back of the rotors bolts and the springer axle spacer. This set-up was designed for a stock springer replacement.
Because of the wild, light, taper-legged Paughco Springer my hiem joint link wasn’t long enough and I bastardized two fine bolts together temporarily. At that point I wasn’t considering a front fender. There are two aspects of chopperdom that I have a tough time working around. Bikes need front fenders and brakes. Can’t ride ‘em much without those two bastards. Even in the old days I ran front fenders, Avon Tyres and front brakes.
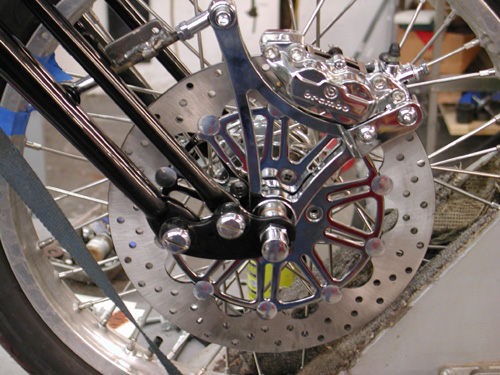
Chris Kallas came over at just the right moment. He’s as old at riding as I am and an artist. We’ve featured his work in special reports. He knows his bike shit and I’ve been trying to convince him to see Jim Murillo about a job. Jim has a paint shop in Torrance, but he’s not the graphics guy, Chris is.
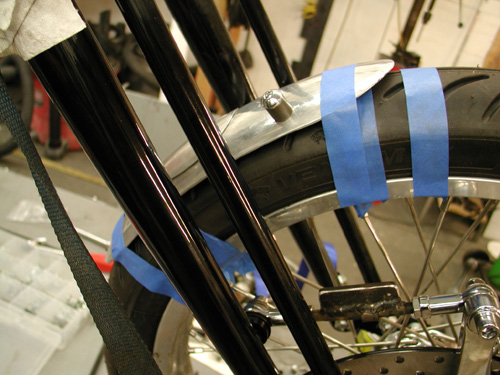
As usual, about the time I think it’s going to be easy, the devil pops up on my shoulder. Kent, from Lucky Devil Metal Works in Houston called, “What are you going to do about a front fender,” he said? “Yeah, that’s what I thought. I’ll send you some shots of my springer front fenders.” He hung up and Chris looked at me sorta strange.
”Who the hell was that,” he said?
”Never mind,” I said flipping my computer on. Kent developed a system of mounting springer front fenders that’s clean as a whistle and odd as only the devil would make it. An engineer wrote Bikernet when I first featured his wild notion and chewed us out. “That idea’s not worth the powder the blow it to hell,” he shouted.
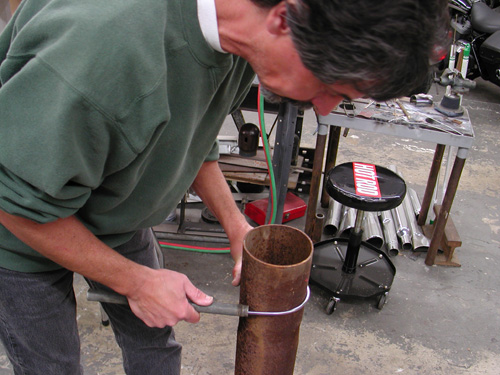
At first I thought he was correct, but the more I considered it, the more I determined that he was wrong. The caliper follows the line of the rotor, so the fender will follow the circumference of the Avon tire. Of course when I stepped into the ring to create a similar configuration I couldn’t do it like the Devil does. The Brembo caliper runs too far ahead of the rotor to mount the fender so we ran carefully designed struts off the brake linkage. Chris drew up the plan, then bent struts out of coat hanger for a guide.
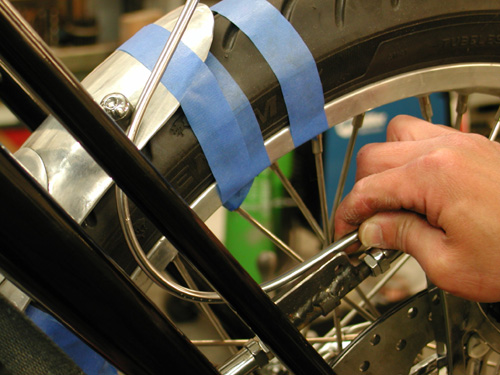
We constantly tried fitment again and again before tacking them into place. I wouldn’t recommend this configuration to anyone. If you run struts off the caliper they’re solid. The heim joints allow the fender to fluctuate, especially side to side. I had to find a concave washer that would allow the heim joints to work up and down but not side to side.
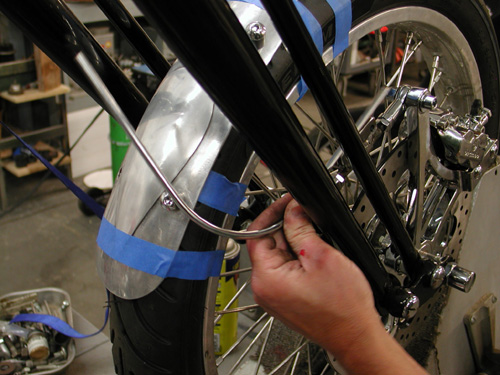
Chris bent each rail to match in pure artistic form. Then I tacked them.
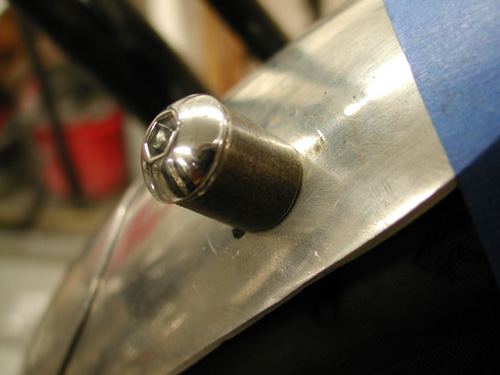
Kent built the front fender with threaded aluminum bungs underneath. I figured out some slender spacers to fit on top of the fender and tacked the rails to them. I must have welded them a dozen times trying to grab just enough rail, weld and spacer to prevent cracks.
There you have it. It’s wild, but will it last to the Badlands?
–Bandit
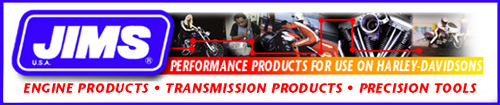
Mudflap Girl Part 1, the Concept
By Robin Technologies |
Life is nuts, or is it just me? Fortunately, we have motorcycles and women to chase. And this year became the year of the Evo, the FXR, and the mudflap girl. I’m scratching the back of my head and wondering how to kick off this build for 2011. There’s a lot on the plate this year and it’s a tad difficult to explain. First, I must fess up. I’m turning 63 this year and no more riding rigids to Sturgis, or even chasing young broads. Ah, but the adventure continues. It’s actually a blessing not to be hassled with women troubles. I’ll let my son, who just turned 37, deal with the addiction to soft curves. I’ll hide out and watch…
The solution for my missing long distance rider was an FXR, and I have one, the John Reed V-Bike that I took to Bonneville in 2006 and set a 141-mph record with a top speed over 150. Unfortunately, I have a hip problem and can’t ride mid-control bikes anymore. I even modified that puppy, but that didn’t do the trick. I love that bike. So, what the fuck was I going to do?
Okay, so I started to piece this bike together. We factory re-manufactured a ’98 Evo engine and JIMS rebuilt the transmission into a six-speed. I had a couple of Renegade Wheels and Progressive Suspension shocks. Then I had a conversation with Kenny Boyce, the man who designed the Pro-street FXR frame. He wasn’t happy with now-defunct Quantum. I also found out that some of these frames break in front of the seat area at the backbone. The project was moving forward with a Custom Chrome, super-wide, upside down front end, Aeromach risers, and we added super wide, Burly bar highbars.
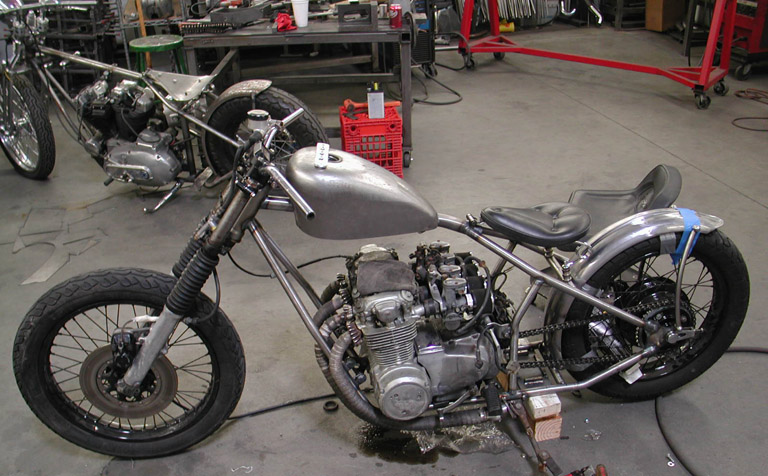
I even had an aluminum mudflap girl oil tank I ordered from Nick at New York Choppers. The bike was leaning toward a pro street touring model with a set of Redneck Softail fiberglass saddlebags and a Klockwerks touring bike rear fender.
I was rolling when Kim Hottinger called and asked if I could haul my old ass out to the American Built/Spitfire manufacturing facility in Rancho Cucamonga, California. Paul Cavallo was the engineer/manufacturing guru behind Hellbound steel. As we watched the production chopper industry dry up, in the wake of a floundering economy, only the diehard survived, and I wanted to support anyone who understood the code of the west.
The brothers who love motorcycles, choppers, bobbers, and custom parts continued to jump up every morning and do what they adore, work on motorcycles. Some went from building hundreds of bikes every month to a handful, but they kept building. Paul downsized and kept rolling with his father at his side. When I saw what he was up to, I was inspired. He can build any frame, for any motorcycle configuration, so my mind went wild. We could build a Frisco’d and stretched, single-loop FXR, and I dragged an old Durfee girder out to his facility so Paul could see how the master built the originals. Imagine an FXR with a state-of-the-art girder.
Paul is a wild man when it comes to building and manufacturing anything. He re-engineered the girder and refined the looks, and added two shock mounts to incorporate a state-of-the-art front suspension. Over the next year, you’re going to witness Paul’s Spitfire abilities with features in several national magazines, and you’ll begin to see his products pop up in Custom Chrome catalogs.
The more we moved forward with this bike, the more inspired I became. This was a bike for me, maybe the bike for my old-guy riding future, now that my Road King was down the road. So I went to Paul with the deal of the century: build two of these frames and front ends. I spoke to Paul, then to my son.
There had to be a goal behind this effort. We would ride to Sturgis together. Shit started to happen fast and I ran into a TV producer who wanted to follow the build, and Leomark studios got involved.
Next, I reached out to Chris Kallas and we started to work up a concept drawing. Here’s some of the e-mail that flew back and forth.
Here’s my initial description:
Frank’s bike: classic black mag wheels from Metalsport. Klock Werks rear dresser fender on Frank’s, might bob it. Both wheels will be mild width. Mudflap girl theme on my bike and Hardball tattoo on Frank’s. Paint reversed from Frank’s bike to mine. Forward controls on my ride, Frank’s will run mid controls. Rubber pegs, grips. dog bone-style tall rubber mount risers. Shotgun pipes. One Redneck bag on the left of Frank’s bike. We also talked about a small front fender.
–Bandit
Some questions?
Black and chrome or silver Evo engine?
Your wheels? Mag or spokes, what kind?
Style/brand of headlight, tail light?
The risers are the type with rubber mount at top?
Carb/aircleaner?
Shot gun pipes, staight, no mufflers?
Style of seat?
Your fender the same not bobbed?
Brakes? Dual or single up front? What brand of rotor/caliper?
If any of these things aren’t specific yet, they could be semi generic on art.
If you can send any photos or links to of fenders, wheels, bags, brakes or controls, it would be helpful.
As for paint, just a thought.
It looks good with lots of black or aluminum, and chrome.
It also looks good with your signature orange accents or striping. Since I’m not crazy for white frames, they could both have blue frames and just flop the two-tone paint on the tanks and fenders.
— CK
Here’s the basic FXR platform showing the frame modifications.
This is with a 3″ extended swing arm.
I need to go back and recheck some measurements but it will give you a
rough idea of the stretch up front.
Is this the type of exhaust setup you were thinking of?
When you said shotgun and 2-into-1, I wasn’t sure.
— Chris K.
I think we should go with this type of exhaust, if we plan to pack passengers. I’m going to ask Dar about that swingarm, but my tendency is to extend it about 1.5 inches, not 3. The stretch looks great. Let’s fuck with those fender rails, arch them, or make them disappear and bob the fender slightly. Plus I think we will need to lower the rear at least an inch, with shorter shocks.
–Bandit
Hey, here’s my first crack at putting it all together. Overall the stance looks good. Since it’s a rough draft without much decoration, I just threw a couple
of mud flap girls on it. I thought I’d try a traditional Sportster/FX headlight with it’s rubber- mounted bulb to stay with the theme of using rubber pegs, grips, and
rubber mounted-risers…. not to mention a rubber-mounted engine, plus I like them.
The frame tube behind the shocks creates a challenge for curved fender struts. I’ve included a couple of photos of some frames so you can check out that area, plus for general interest I tried mounting the tank higher (Frisco style) but thought this looked better.
You might use a semi-later model Sporty tank (when they first started making them larger but still had a carb).
I don’t know at what angle or how Spitfire plans to deal with the secondary neck brace under the tank, so just drew it how I thought it might go.
When you said a Fantasy in Iron tear drop air cleaner I took that to mean a plain Goodson (no rib), for engraving. (We now have a Roger Goldammer air cleaner for Frank’s bike)
Since you need to run a front fender, I made it small. I like when they show most of the top of the tire.
Questions:
Who’s handlebar and foot controls do you plan on using?
How about brake calipers?
–CK
Hey, Chris,
I feel like I want more attitude. How about the tank mounted in line with the bottom of the top bar and stretched a tad at the back to more of a point? Take out the stress bar and add a gusset there with a mudflap girl cut out.
Check the news. I ran a shot of the air cleaner, but you nailed it. Did you check out the heavy green flake and silver bike? I like that theme. My bike will have a plain engine. I thought that style worked well with the plain silver, driveline. And I liked the green springer to match the frame.
We don’t need to go with green. It could be almost anything and silver, then reversed for Franks, with a silver frame, and colored sheet metal.
–Bandit
If the Redneck bags wouldn’t fit, we looked at what Bob T. runs on his fantastic RT.
Part number for bags:
’87-90 FXRS conv bags
H-D 90702-89 left
90703-89
As you can see we are flying at this effort. Don’t miss the frame build in the next segment. As it turns out Frank and I will be running the same drivelines: JIMS six-speed transmissions and Harley-Davidson Evo engines.
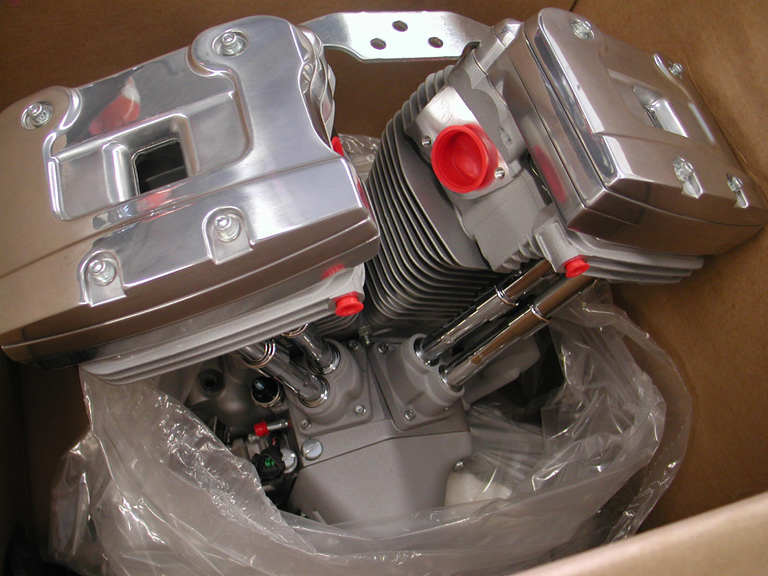
Sources:
Motorcycle Mania And Hugh King
By Robin Technologies |
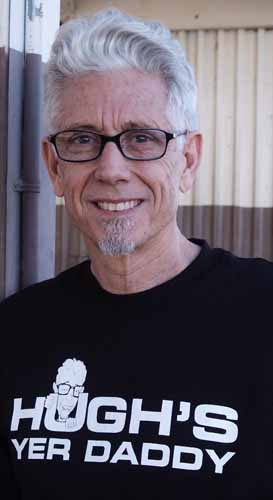
What hit the American Motorcycle industry like straight pipes and tire sizzling burn-outs, at 4 in the morning? Television, in the form of Motorcycle Mania one and two. The introduction of chopper building skills and rebel attitude, unleashed broadband, to citizens all over the country, rocked the biker world. Then chopper heaven in the form of Biker Build-offs struck with round two. Who was responsible for this Tsunami boon to our lifestyle? It was Hugh King, the producer/director/writer and editor at large of Original Productions.
Hugh felt the crisp freedom and wild wanton wickedness of the chopper industry in 1947 as a Milwaukee youngster, with his nose pressed against his living room window. An older neighborhood wildman, Billy Brody, screamed down the street on a bobbed ’46 Indian Chief. He tore across his folk’s lawn and slid to a stop on the front porch ignoring the driveway and garage alongside the house. That scene, on the Oak shrouded street, was emblazoned in Hugh’s expanding creative mind for years to come. In fact he added a wild black and white scene of a biker burning into a bar, to his documentary resume while living off grants and making social action films.
Through the reams of vast, rough-shot, motorcycle footage he learned the Harley biker industry, from event coverage, to land speed record attempts. Hired by Original Productions he produced reality shows. Then one fateful day, while warm California rays graced his small Original Productions, office, Tom Beers, his boss, wandered in.
“Discovery Channel called,” he said. “They want a feature on the custom motorcycle industry. You’ve experienced the motorcycle world. It’s your assignment.” Since the offices were located in Burbank, California, Hugh investigated valley shops and called motorcycle mag editors. A mystery connection was made, and an old crocked finger pointed toward West Coast Choppers. “And the rest is history,” Hugh said.
By Motorcycle Mania two, Jesse became a star. “Viewers wanted to talk to him,” Hugh said of growing audience. “We filmed it for the average Joe and sensed immediately that people wanted to reach out and touch tools. There was a deep longing for the ability to make something out of nothing.”
Jesse smacked a cord in young American viewers with a ballpeen hammer against a flat sheet of aluminum. Fans witnessed pure raw alloy shaped into sleek gas tanks. “The footage of metal being annealed was graphically inspiring,” Hugh said. At that stage he was the producer, director, writer and editor (Tom Beers was the executive producer).
Discovery was rocked and wanted more, so Hugh directed the first four Monster Garage segments, then kicked off the Build-Off series.
Life kicked into high gear for Hugh and again Original Productions was approached by Discovery Channel to make Motorcycle Mania III or “Jesse James Rides Again” starring Jesse James and featuring his buddy, Kid Rock. Jesse worked with wheelwright, Fay Butler, in Massachusetts to learn the intricacies of copper fabricating. Fay manipulates old yoders like an artist’s brush shaping copper. Yoders were used in WWII to fashion sheets of metal for fighter fuselages and wings. Jesse and Fay worked together to shape the copper chopper gas tank.
The MMIII film endeavor raised the bar for Hugh. “I had the opportunity to work with high def film and top quality camera equipment,” he said. “We got to use the highest standard automobile commercial equipment like a Shot Maker and Chapman cranes for dramatic rolling angles.” His life hit overdrive as he filmed the building of the Copper Chopper for Jesse, American Bad Ass Chopper for Kid Rock, and they hit it to Mexico. “Nothing went according to plan,” Hugh said. “We changed the itinerary constantly. The people of Mexico were terrific as we shot from El Paso, Texas and Juarez, Mexico, in 125 degrees, through 350 miles due south to Chihuahua.”
Hugh filmed spectacular footage of the two riders passing smoldering sand dunes, sweeping vistas and lumbering Iguanas crossing the rugged roads toward Copper Canyon.
Having the time of their lives they rode south to Chihuahua, a growing city, and searched through the old market place. Riding west they climbed 6,000 feet to Copper Canyon, in the middle of the Sierra Madres, which is six times longer than the Grand Canyon. They slept in a small village on the lip of the gorge, in a town of 65.
Jesse and the Kid accomplished their goal of escaping fame and fortune as they continued West toward the coast over torturous curved roads through blinding lightening storms and over a territory where the only vocation is hijacking. “We slept in the camera van,” Hugh said, “since there was no place to stay, until we reached the white sand beach on the Sea of Cortez. It was a transcendental experience.”
Motorcycle Mania III will experience limited theatrical release later this year, followed by Discovery Channel airing. Hugh has a year and a half invested in the film while directing Biker Build-offs with Billy Lane, Dave Perewitz, Roger Borget, Paul Yaffe, Indian Larry and currently with Yank Young, Chica, Eddie Trotta, Russ Mitchell, Arlen and Cory Ness. “Choppers have turned my life upside down,” Hugh said. Although the family man doesn’t own a bike, he rides constantly. “I’ll jump anything the builders let me straddle,” Hugh said. You can see the motorcycle mania fever boiling in his gaze.
What’s the future hold for Hugh King? The Biker Build Off series is rockin’ through another chrome and flamed season and even hotter segments are headed for next year. “We kicked off the series with Billy Lane and Roger Borget,” Hugh said. “Initially it was intended as an elimination competition, but no builder can manufacture one ass-kickin’ bike after another, every 30 days. We currently pick builders by regions and diverse styles.” In 2005 he hopes to throw a massive live finale in Las Vegas and take the bike voting interactive.
At 65, Hugh ramped into an all-time high with custom bikes. He’s riding it for all it’s worth and the entire industry benefits.
HUGH KING SIDEBAR:
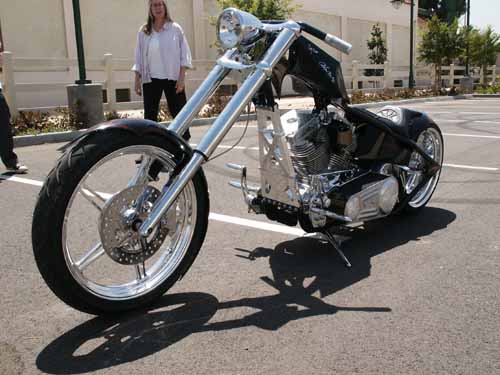
THE LAUGHLIN BUILD-OFF– On April 20th ten of the world’s greatest bike builders thundered into Laughlin, Nevada. For 72 hours in a secret desert shop they worked non stop to create BBO X, a one-off 124 cubic inch, rigid, right side drive, black and chrome, spear-like chopper. Then they presented it to Hugh King, producer of Discovery’s Great Biker Build Off. The geniuses who came together to make this awesome steed were Arlen Ness, Cory Ness, Russell Mitchell, Eddie Trotta, Mitch Bergeron, Kendall Johnson, Matt Hotch, Joe Martin, Chica and Hank Young.
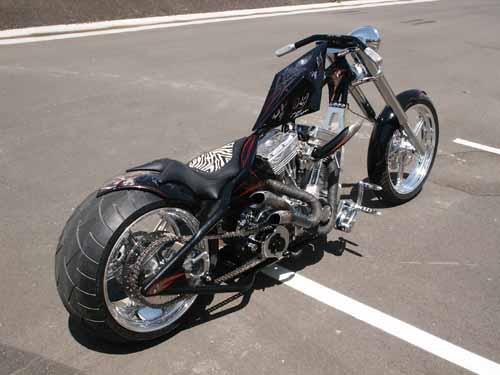
Chica hand fabricated the gas tank. Hank Young made the oil tank. Kendall Johnson was responsible for assembling and tweaking the 124 cc. S&S motor and the Baker 6 speed transmission, Mitch Bergeron was responsible for the frame and the billet down tube (in which was cut in the Roman Numeral X and the Discovery planet), Matt Hotch fabricated the fenders, Joe Martin built the pipes and did the pin striping, Russell Mitchell and Eddie Trotta built the front end and Arlen Ness and Cory Ness were responsible for the paint and the overall supervision of the project.
A special guest appearance was made by legendary seat maker, Danny Gray who fabricated a black leather seat with a zebra stripped manta ray inset.
On Saturday night, April 24th, before thousands at the Laughlin River Run, BBO X was unveiled and formally presented to Hugh King.
Each of the ten builders had competed in Bike Build Off before. Their ten bikes were on display at the Discovery both where the people voted on which motorcycle they thought was best in show.
Matt Hotch’s low slung, blue beach cruiser took the prize. Watch every Monday night for a new Build-Off on Discovery.
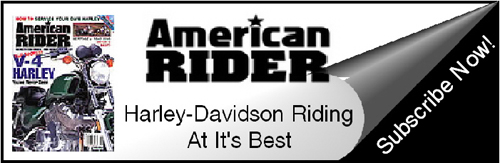
Sturgis Shovel Part 11
By Robin Technologies |
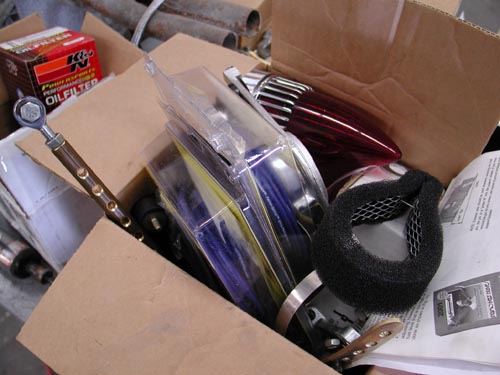
I’m not sure if I’m keeping everything in line. But this segment took us to Foremost Powder Coating in Gardena California. I was at that point when these shots were taken. I’ve had a Powder Coating Sponsor for years, Custom Powder Coating in Dallas. They’re good people and know how to handle custom work. They’ve handled jobs for Strokers Dallas, our custom for American Rider and even the 1928 Shovelhead for Bikernet.com.

Powder coating costs have dropped and it doesn’t make sense to ship a frame to Dallas. It would cost less to have it Powdered in LA than to pay for the shipping. So I looked around the area and was recommended to Foremost Powder Coating (877) We-Coat-it, 1608 W. 139th, Gardena, CA 90249. These people have their shit together and the girl who runs day-to-day operations, Esmeralda, is a delight on the eyes and to work with.
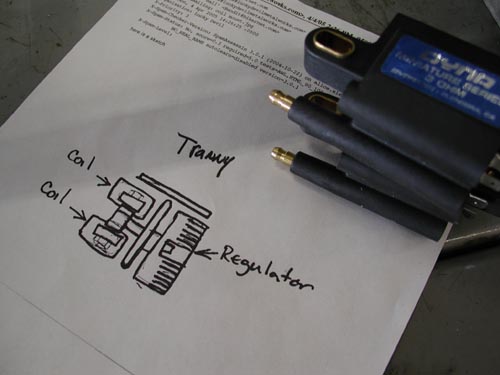
Let’s back up, though. Just before teardown for Powder I needed to think electrics. Kent from Lucky Devil Metal Works in Houston sent the above illustration for mounting the Compu-Fire voltage regulator under the tranny with the small Dyna Coils from Custom Chrome. I pondered that drawing and decided that I didn’t like the notion of putting my coils at ground level. What if I ran through a rain puddle? He’s built bikes using this technology several times and so has the guys at WCC, so it must work in most circumstances.
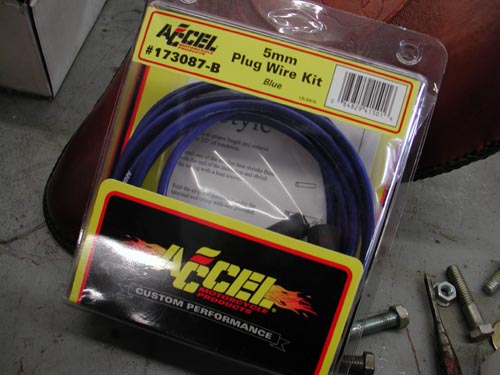
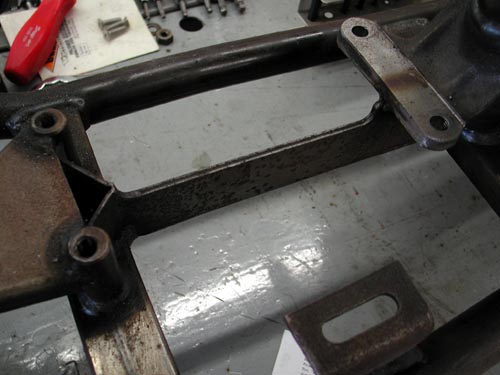
I decided that since I was going to run the Compu-Fire engine based electric starter that I had room under the oil bag for the coils. I still installed the sealed voltage regulator under the tranny on a 3/16 sheet of aluminum. But then welded brackets under the Craft Tech Oil bag to hold the two coils apart.
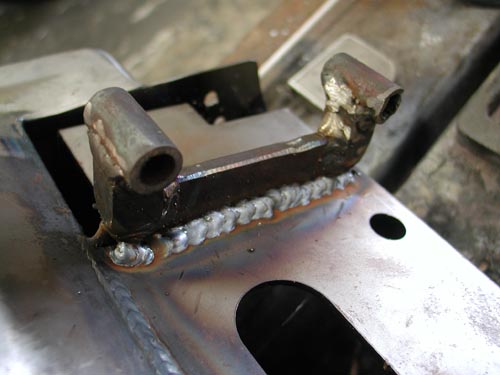
This was a delicate operation and ultimately the new Accell Sparkplug wires run right across the top of the RevTech Tranny. I also had just enough room behind the coils to house the wiring for the single-fire Compu-Fire ignition system. I thought through most every aspect of this motorcycle right up to the wiring business, then came up with a nuts notion, which I will explain during the final assembly process. It actually worked out fine with a handful of scary moments.
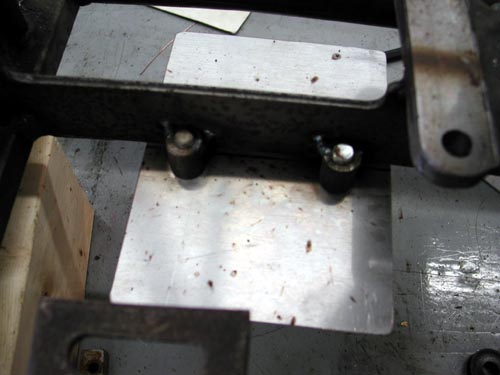
I welded four bungs that housed 3/8 fine threads to the frame with my Miller MIG welder. Ultimately I mounted the Compu-Fire voltage regulator to the pipe side (right) and it worked out fine.
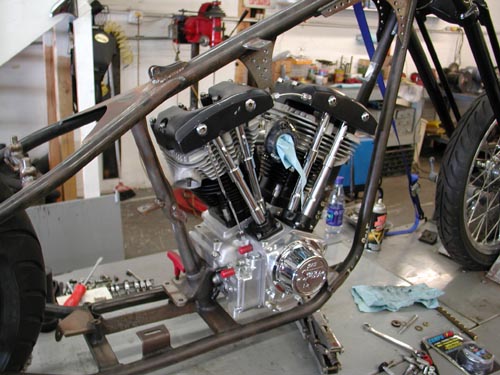
It was time to strip the Engine out of the frame, complete final welds, grind the welds and ship the parts to Foremost Powder. I needed to create a temporary engine stand to hold the S&S 93-inch Shovel in place. I used a RevTech engine stand and mounted it to a junk metal table leg. It worked perfectly and I shoved it in a corner for future use.
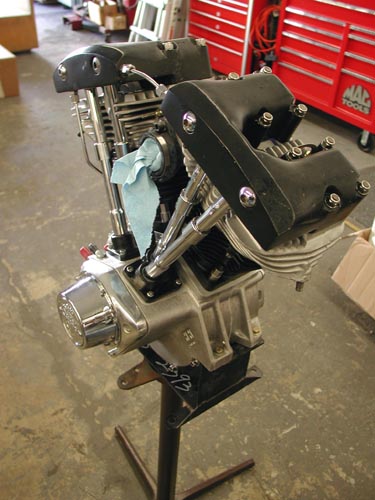
As I tore portions of the bike down I formed zip-lock bags with labels to hold the fasteners. You’d be surprised how fast you forget which spacer fit what, unless you organize. Mike Egan told me years ago that he takes photos of every part and organizes his assembly with photographs to demonstrate how components matched or were fastened. Since I try to take shots constantly I had an archive of various aspects. Hell, I just need to turn on Bikernet and look up the tech.
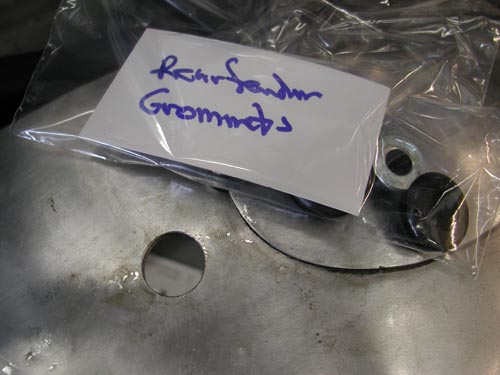
The next move was to finish welding any tab or bracket that had been tacked or partially welded. MIG welding is a breeze, but not as dead certain as TIG and I’m after a Lincoln TIG welder.
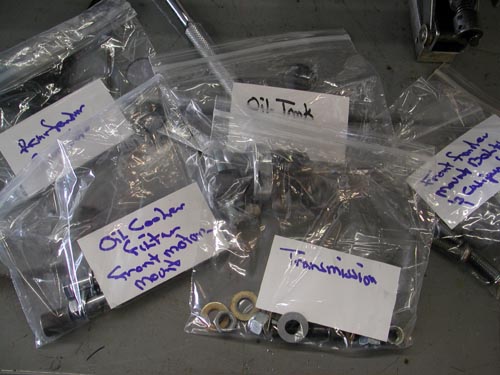
Here’s all the fasteners, grommets and spacers in bags with biz card labels. It works like a champ although I replaced some of these fasteners with stainless Allens wherever possible.
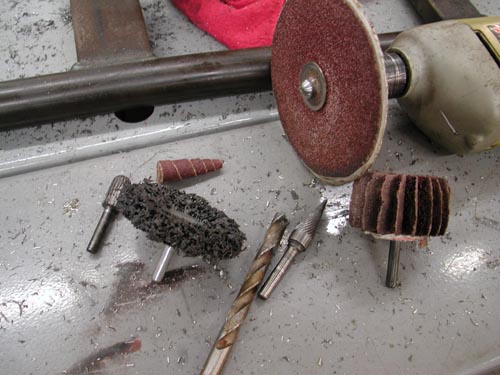
Next I dug out all my tools for grinding welds and went to work. This level takes a great deal of patience and artistic style, which I don’t have. The more time and patience, the better each weld will look. There is actually a process for bondo filling powder now, but it’s more costly. If you don’t want welds to show ask about it. If you don’t mind the look of a clean weld, just powder. I wanted the look of a machine, nothing slick.
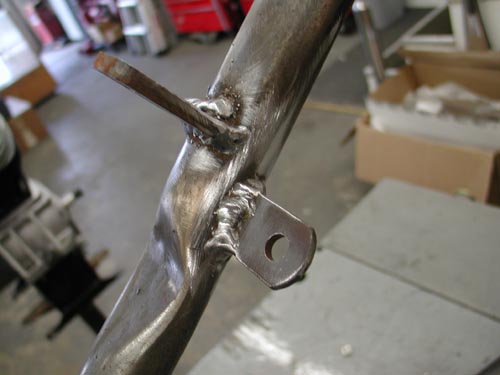
There’s one more consideration. Try to make each weld look the same as the next one for consistency. In my case that was tough. Some of my welds were decent, others sucked. I did my best, but my welds didn’t compete with the Paughco paid professional beads.
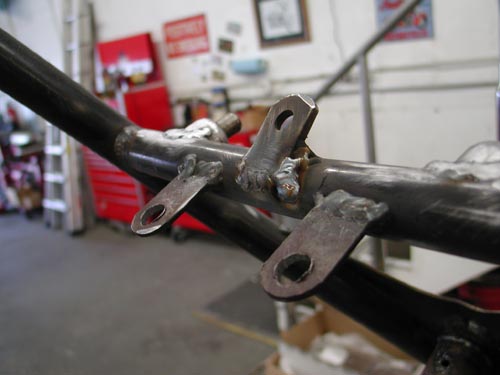
As I finished grinding and drilling holes in the frame for wiring I separated each group of powder finish parts and took a shot for the Powder guys at Foremost. It was a lifesaver to be able to hand them a shot of each group of parts since some had to be sand blasted before the finish was applied.
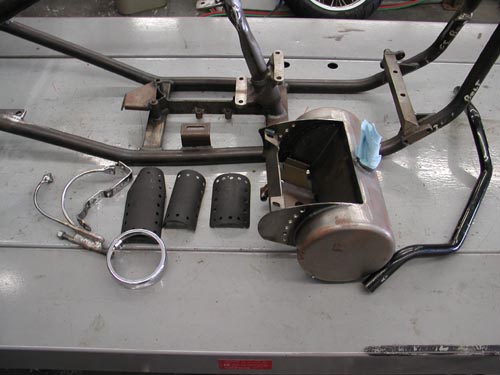
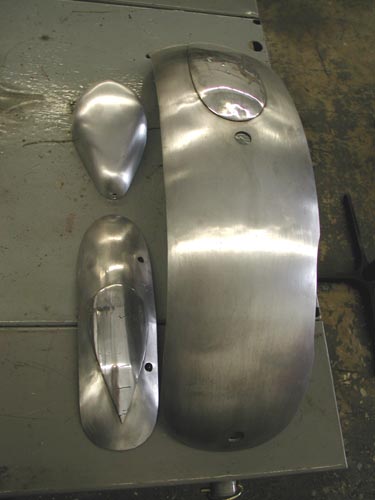
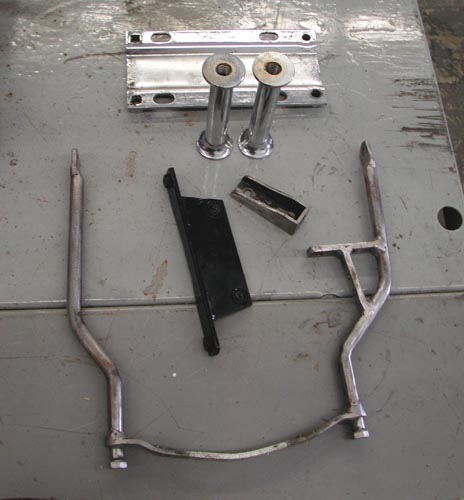
One more comment on drilling holes for wiring. This was one of the first times I drilled plenty of wiring holes. Remember Frank Kaisler’s rule? Drill the hole. Ream it out on a taper to prevent cutting your wires. Then with emery cones make sure there are no razor-sharp burrs in the tubing. Frank ran the emery paper then he’s twisted a Kleenex and shoved it in the hole. If it caught he’d sand the edges more. If not it was good to go. Let’s hit it to the next chapter, we’re burnin' daylight.
