Exhaust Heat Wrap Installation
By Bandit |
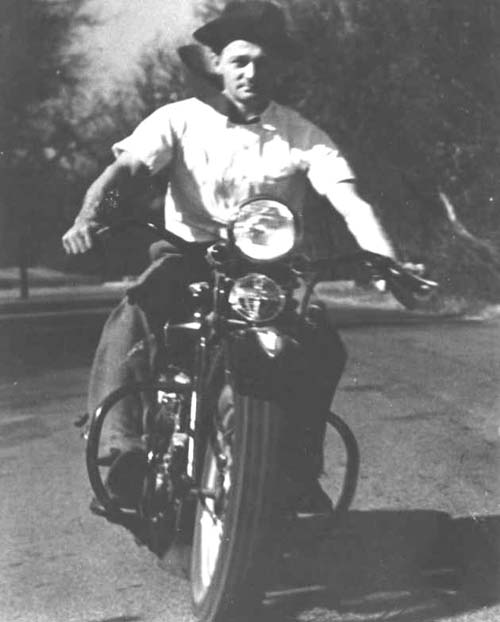
Editor’s Note: Sounds official, like I might tell you this guy is fulla shit before we get started. That’s not the case. We’ve wanted to bring you the skinny on using insulated exhaust wrap for a year or two. Larry Curik is a close friend and a classic custom bike builder. He offered and I decided to wait him out, since he’s been in the biz as long as I have. He’s starting his own shop, Lone Star Choppers, Inc. Gotta give a brother a break. Here is the long-awaited tech. Let’s get to it.

Note: It takes more material than you think so I wrap the pipe loosely andadd about ten feet to cover one pipe. You never want to come up short
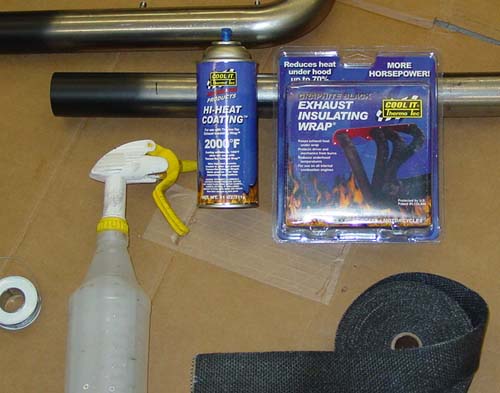
It’s a simple operation so Larry started by laying out everything that you will need(except the rubbergloves), water spray bottle, high heat paint (for the area left un-wrapped),stainless steel safety wire and Thermo-Tec insulating wrap.
Looks like you can buy this at any hot rod shop or Pep Boys.
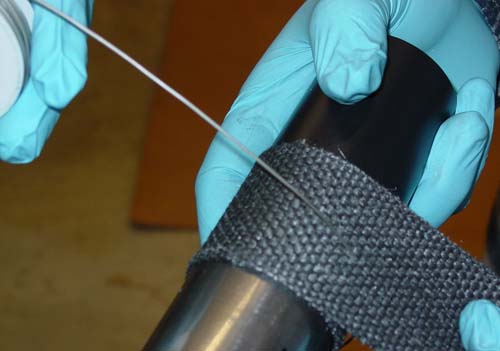
Take 1 full wrap and secure it with safety wire (position so as not toshow with next wrap, (insert through the wrap and twist wire tight). Use glovesbecause wrap is impregnated with graphite and contains fiberglass. It can makea big uncomfortable mess.
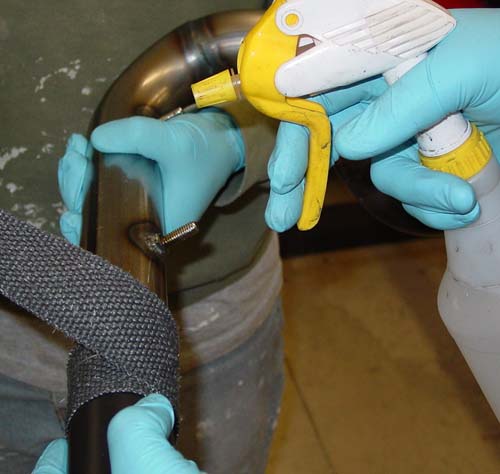
Continue to wrap, overlapping ½ of the last wrap with each turn. Spray the material lightly with water tohelp it conform to the shape of the pipe.

If you wet it down really good, it is very easy to pushmounting studs through the wrap.
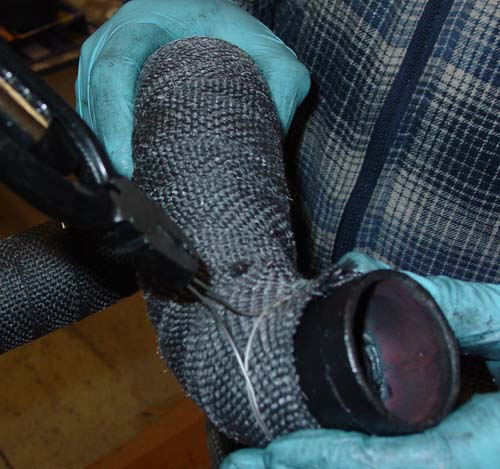
Tie the finished wrap with a double wrap of safety wire, or you canuse hose clamps. Larry starts wrapping from the end of the pipe, so the leading edge is not exposed and is clean as possible.
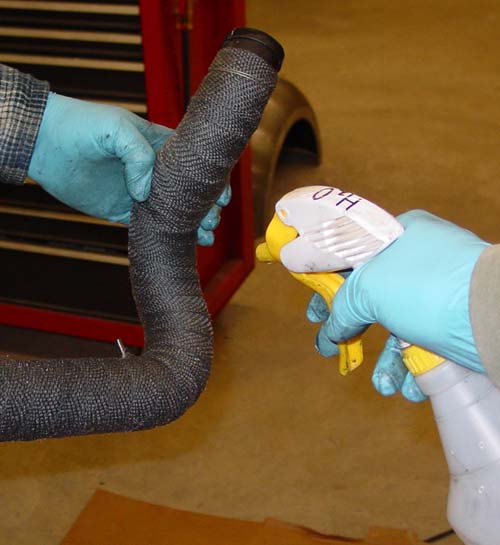
Lightly wet the entire pipe and “wring” (massage it), it to make the wrappingmold to the pipe. Set the pipe aside and let it air dry.
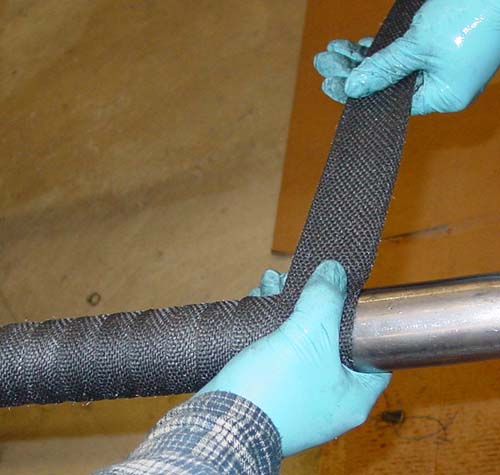
Four hands are better than two. Have a friend help for a tighter wrap.
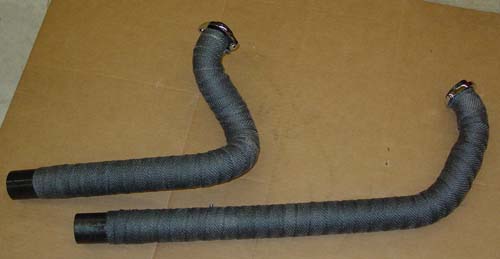
Here’s the finished pipes. Let them air dry and install the bastards.
Note: this stuff must cure, when you start up the first time, it’s goingto smoke and smell real bad. Let your scooter run a few minutes and shut it down. I prefer to cure it (let it set and cool) and then get in the wind to finish the curingprocess. Due to higher exhaust velocity, it is advised to check the jetting after you run it. You can go leaner with the wrap.
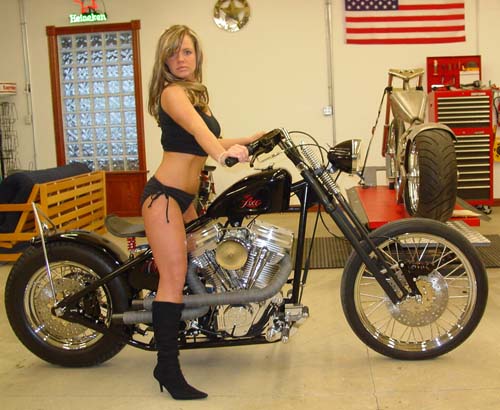

Larry Curik
Lone Star Choppers, Inc.
(618) 406-1554
Larry@lonestarchoppers.com
Lonestarchoppers.com
7858 Andy Road
Waterloo, Illinois 62298
PowerPacc EFI System From Doherty
By Bandit |

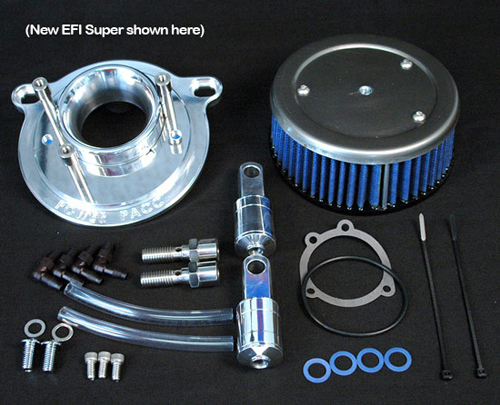
Doherty Machine has just released their latest version of the performance proven Power PACC intake system for all Delphi EFI equipped machines. This upgraded version incorporates numerous improvements that provide increased efficiency and longevity. Doherty's snap in venture has been updated and machined specifically for the EFI application.
This specially designed venturi creates an induction path which provides a 100% unobstructed air flow. The combination produces increases in both horsepower and torque with overall gains of up to 15%! Each system is CNC machined from solid billet and polished to a show quality finish.
All associated hardware is polished aircraft quality stainless steel. Easily installed the new POWERPACC EFI SUPER is compatible with stock or aftermarket, round and oval air cleaner covers.
For complete details call 800-956-9409 and be sure to visit them on the Web at www.dohertymachine.com
When you're after quick-and-easy to perform alterations that improve the performance on your Harley-Davidson, little compares with hardware designed to enhance the engine's breathing.
Just simple air intake and exhaust upgrades can provide gains in both torque and horsepower. In the vast majority of applications these mods can be handled with minimum of hands-on mechanical ability, specialty tools and time.
For years enthusiasts have recognized and realized the benefits of replacing the stock air filter element with a unit similar to K&N's. These high-flow filters provide the engine with a higher volume of air at a less restricted rate.
The most popular filter are easily cleaned for extended use with no loss in performance. Okay, so you've presented the carburetor with a larger mass of air to ingest. Is that it, or would manipulation of the swirling mass provide even greater benefit, hmm? That question was not lost on the ace engineering team at Doherty Machine.
Tim Doherty had long speculated that if the shape and movement of the air mass between the cleaner and carb could be controlled, engine breathing and performance would be enhanced.
To that end he developed a sophisticated, easily installed intake package known as the Power PACC, which Tim Doherty claims will produce real-time torque and horsepower gains you can feel.
Initially, Doherty developed this unique system as a means of controlling air between the filter and carb. Focusing on patented “snap-in” venturi extension, the unit provides predicable air management to the entrance of the carburetor. As one might expect, the extension increases air speed velocity while reducing turbulence.
Additionally, Tim found the new venturi configuration acts to collect and straighten out the air once it has cleared the air filter element. This in turn allows for a smooth and uninterrupted transition to the carb entrance. Unlike traditional velocity stacks, which can negatively affect low rpm performance, Power PACC's “short” venturi runner length offers increased torque on the bottom end.
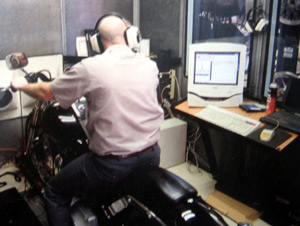
Benefits of the Power PACC system
The Power PACC system offers others significant benefits not to be overlooked.
Machined from a solid piece of 3/4-inch billet aluminum, Doherty's 1-piece backing plate provides a structurally sound, rigid platform for the entire intake assembly while eliminating all flimsy brackets. Furthermore, the Power PACC, as tested, incorporates Doherty's revolutionary Power Vent Twin kit.
Power Vent is a fast sealing, one-way valve that prevents air from being sucked back into the crankcase on the piston's upstroke. This venting method can increase horsepower and throttle response while eliminating rocker box and base gasket leaks often cause by excessive crankcase pressure. Power Vent is a convenient addition to the Power PACC kit since the highly polished billet aluminum vents bolt directly to the cylinder head breather outlets using the same stainless banjo bolts that secure the backing plate.
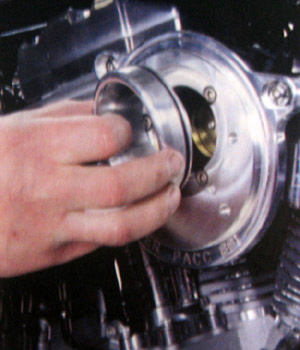
Quick and Simple Installation Process
Before we lay out the results of the Power PACC let's walk you through the installation process so you can see just how quick and simple it really is.
First off, let the engine cool and slip on some decent eye protection. This is a good time to familiarize yourself with the operation by reading the instructions.
Remove your stock air cleaner assembly including cover, filter, tin backing plate and breather lines. Clean up any lingering road grunge, taking care that nothing makes its way into the intake channel. This is not a good place to lay screws while doing an installation.
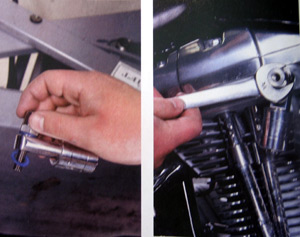
Take one of the nylon washers from the kit and place it over the breather bolt. Run the bolt through one of the Power Vents followed by a second nylon washer. Thread the bolt into the cylinder head breather outlet. Ditto for the other breather. Install the supplied gasket, with the adhesive side toward the carburetor/injector.
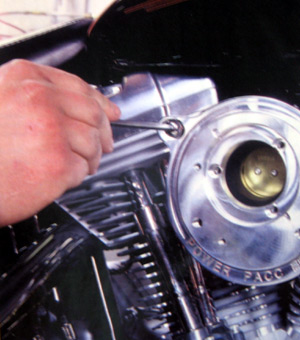
Using the three supplied Allen head screws, install the Power PACC backing plate. Align the two slotted holes in the backing plate with the breather botls and secure using the supplied button head screws and washers. Lubricate the O-ring fit to the velocity stack and then press into the backing plate.
Set the air cleaner onto the backing plate and secure using the three screws and touch of Blue Loctite. Reinstall the air clean cover and that's it. Installation takes only 20 to 30 minutes max using tools your ol' lady commonly throws at you. It's that simple.
Power PACC Performance Evaluation
For a completely unbiased evaluation of Doherty's Power PACC we fired up a new 2002 FXSTI and headed over to see Troy and Jim in the service department at Grand Canyon Harley-Davidson. Just prior to and right after installation the bike was put through its paces on the dynometer. We think the dyno graph and horsepower/torque readings speak for themselves.
Only 27 minutes separated the before and after runs, which is further evidence of how simple the installation is.
Our first dyno run with the bone stock Delphi inject Twin Cam produced a maximum of 63.1 horsepower and 72.8 foot-pounds of torque. The very same engine after installation of the Power PACC kit produced readings of 73.5 horsepower and 78.9 foot-pounds of torque.
Yeow! That's a whopping 10.4 horsepower increase and an addtional 6.1 foot-pounds of honest torque. Those numbers come straight from the dyno's mouth and are about as honest as you're gonna get. It appears that not only are Doherty's performance claims realistic, they may even be understated.
The complete Doherty Power PACC kit contents
The complete Doherty Power PACC kit includes their custom designed high-volume, high-flow air cleaner, with billet backing plate, patented snap-in venturi, a pair of highly polished Power Vents and all necessary mounting hardware.
Depending on your preference and application, you can run the factory cover or one of Doherty's custom air cleaner covers. Power PACC kits are available for all '92 and later Evolution, Sportster and Twin Cam 88 models, fit with Keihin, CV, S&S E or G, and Mikuni flat side carburetors as well as Delphi injection.
When you consider the benefits, it's one of the most cost-effective ways to sharpen up your engine's throttle response while increasing usable power from the bottom end through peak output. It's the real deal!

Bad Ass Seats Takes On An Indian Uprising!
By Bandit |
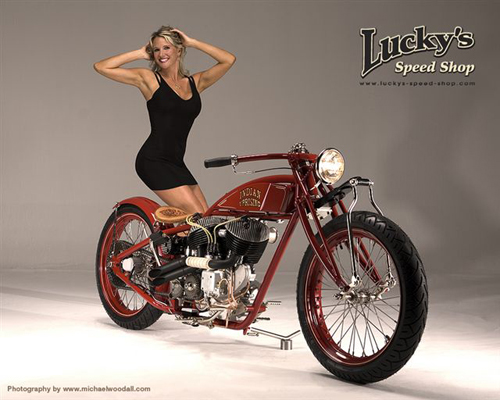
This is Shirley Zanelli’s latest leather seat creation. It was etched for an Indian restoration by “Lucky’s Speed Shop” out of Chandler, Arizona. It was designed by the owner, Don Yates, as a tribute to the Board Track Racers of the early 1900s. Mike Tomas, of Kiwi Indian, who’s responsible for building the engine, transmission, and the Springer front end, referred Don of Lucky’s to Shirley. The bike is being entered in the Laughlin River Run Bike Show, on Saturday, April 28th, ‘07.
The lovely Shirley, of Bad Ass Seats, in the Nevada desert, will describe every step below:
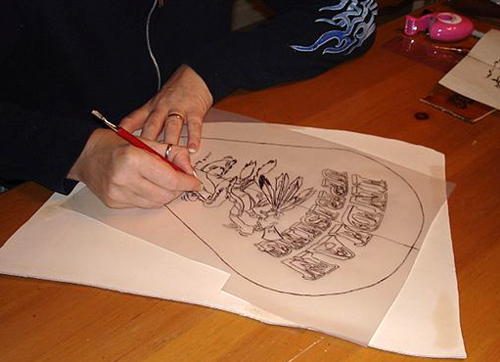
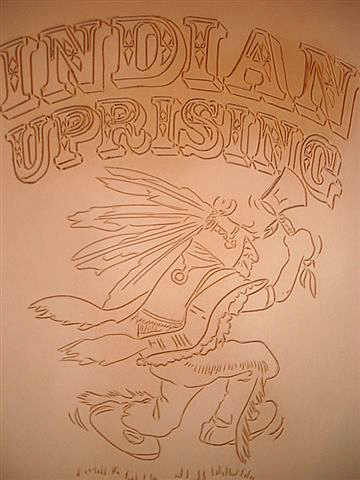
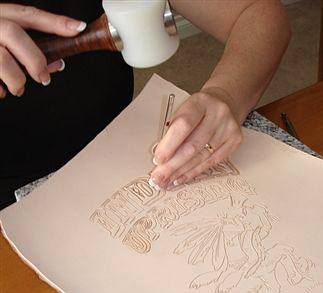
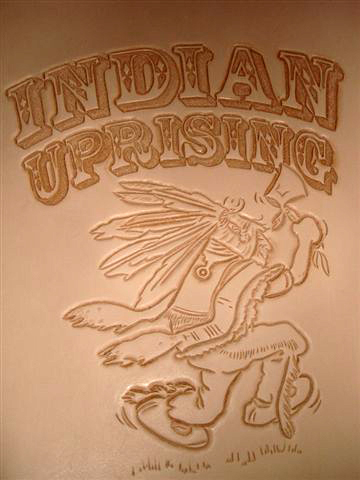
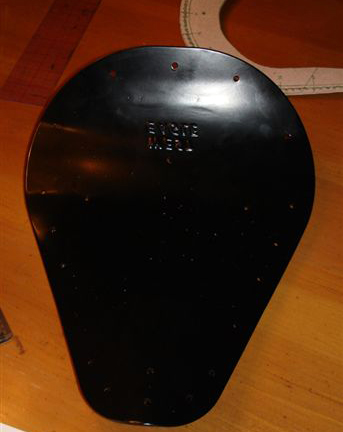
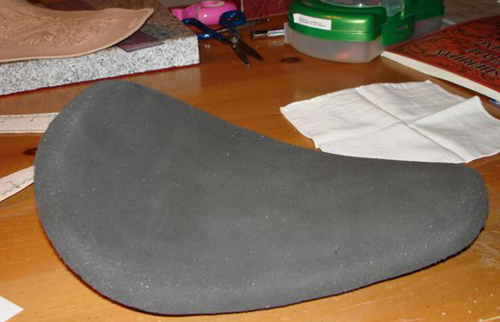
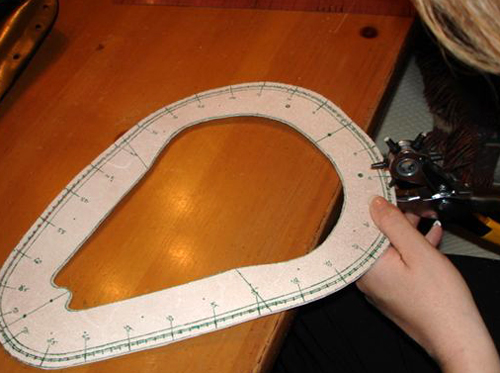
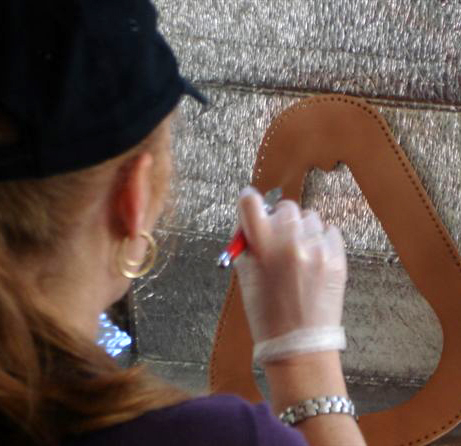
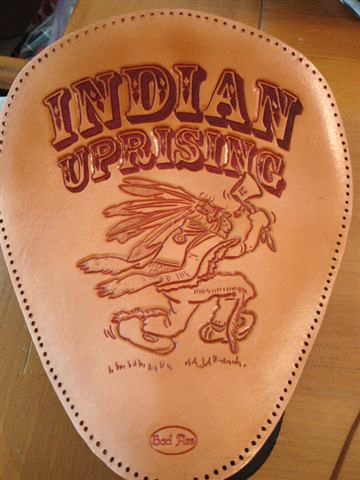
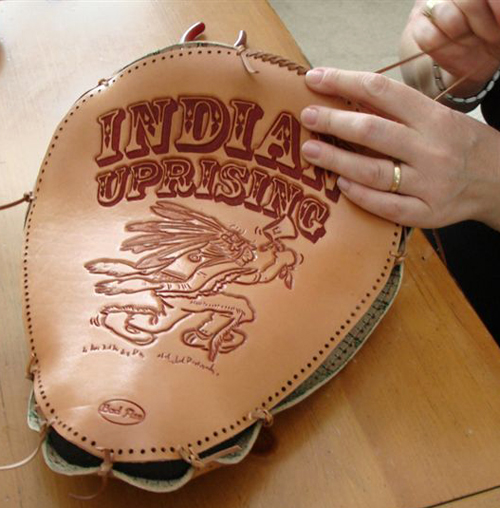
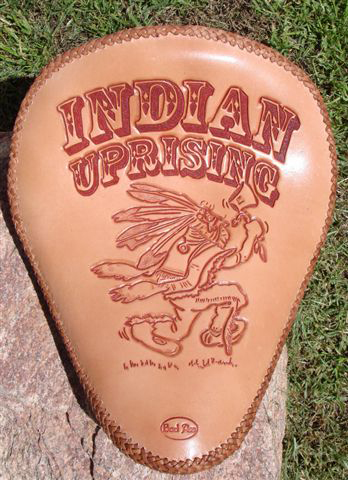
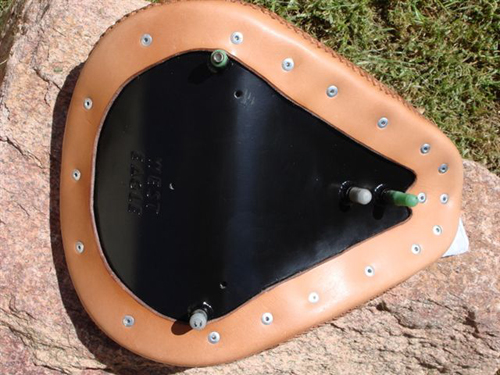

Shirley Zanelli
http://www.badassseats.com
702-325-3532
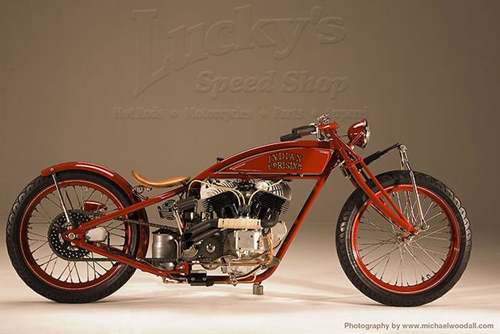
Don Yates, Lucky’s Speed Shop
http://www.luckysspeedshop.com
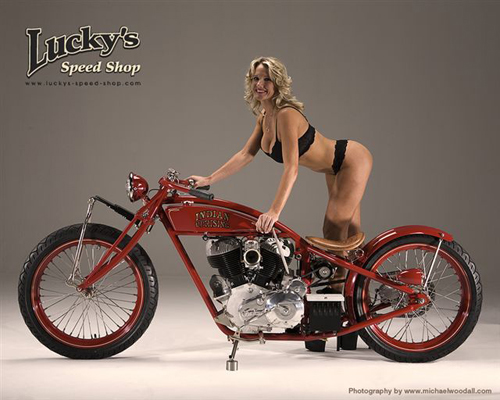
Mike Tomas, Kiwi Indian Company
http://www.kiwi-indian.com
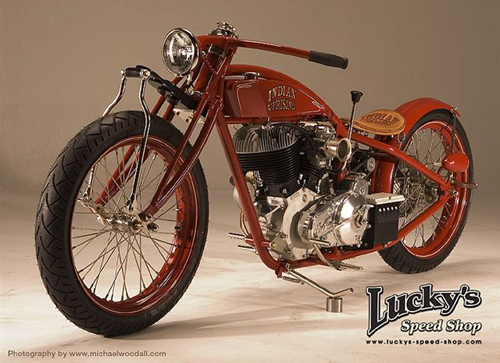

Extra Trans Support
By Bandit |
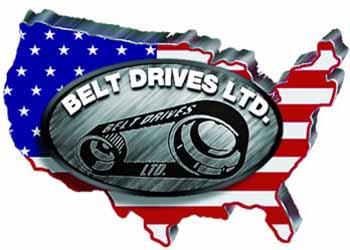
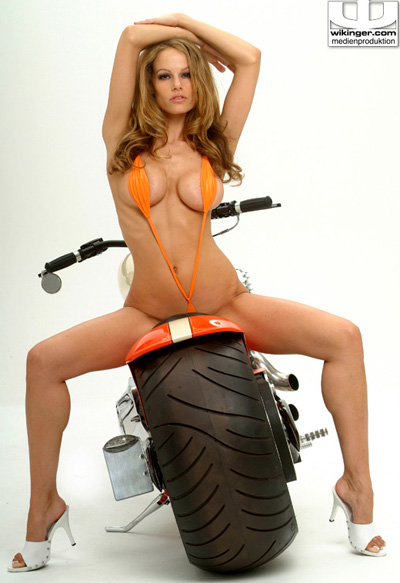
After breaking my transmission Mainshaft for the second time I decided an Outboard Support Bearing was my only hope. Sadly BDL does not have a direct fit “Bolt On” Outboard Support Bearing for a Shovel (a 3-inch open belt kit with EVO-10S motor plate). But I was able to re-engineer their EVO-3000 Outboard Bearing retrofit kit, which is intended for a Softail with the EVO-9S motor plate.
Since the distance between the Crankshaft and Mainshaft is the main difference, I was prepared to discard the outboard bearing on the Crank Pulley but it turns out that BDL has already abandon it because it was difficult to get all three points, (front pulley, stand offs, and clutch basket) in alignment correctly.
Predictably the position of the four stand offs on the Softail bearing support will not match the Shovel motor plate, not to mention apparently there is an old and a new version of the Softail bearing support, and those stand-offs are located even more differently.
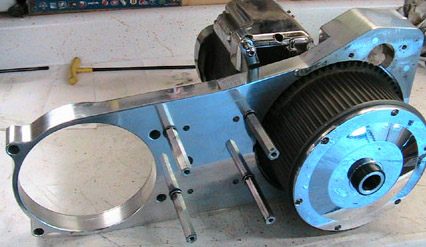
Another snag: the older BDL clutch basket (Part # 76-3E) is not made where it will accept the rear pulley cover derby and would have to be machined out, however a newer BDL Shovel basket (same Part # 76-3E Note the Shoulder) will accept it perfectly. Since the last clutch basket was destroyed in the aftermath of the shaft failure, (it passed me on the pavement) the new basket was a win/win.
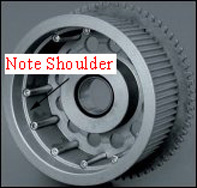
Also the Shovel basket is a larger overall diameter than the Softail, and the round stand offs that came with the kit might not quite clear the Ring Gear, so I decided against using them.
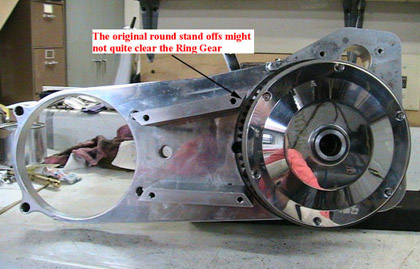
I used 5/8 x 4-inch flat aluminum bar. I had them milled down to 3.94 inches to match the length of the original stand offs. With the motor plate bolted to the tranny, and the clutch basket and cover derby all in place, I drilled and tapped my standoffs and bolted them to the support bracket. I then positioned the bearing & bracket onto the clutch basket derby. This would fix the location for the standoffs on the motor plate.
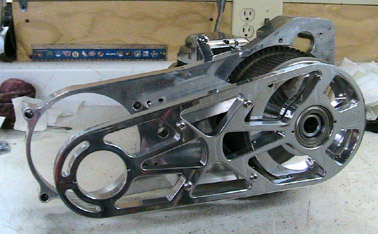
After marking the position of the standoffs, I drilled the motor plate, and then drilled and tapped my standoffs. Then with the standoffs attached to the support bracket, I mounted them to the motor plate.
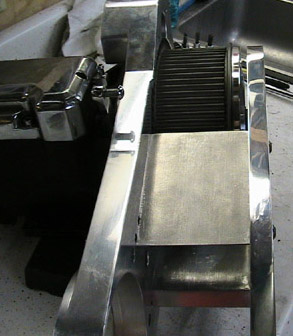
After making sure that everything was clear and square with nothing binding, I left the standoffs bolted to the motor plate and removed the support bracket.

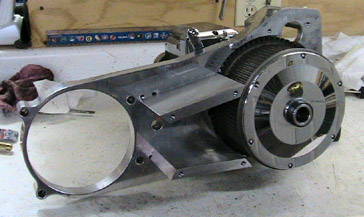
It all went back together on the bike perfectly.
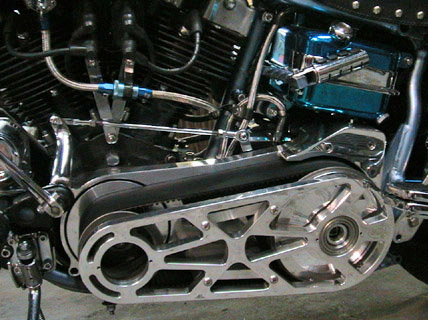
Four separate “post” could possibly twist or trapezoid. While not as pretty, I think that my two flat stand offs are far more rigid.
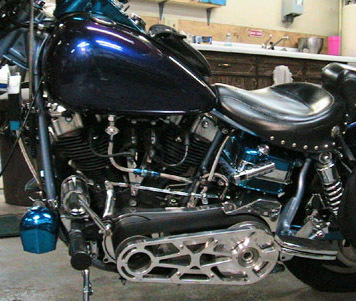
Special Thanks to Bandit for putting me in touch with the right people at JIM’s (transmission) and BDL, who both helpfully indulged my imagination.
–Jim Padgett
St. Clair, Missouri
jim.padgett@sbcglobal.net
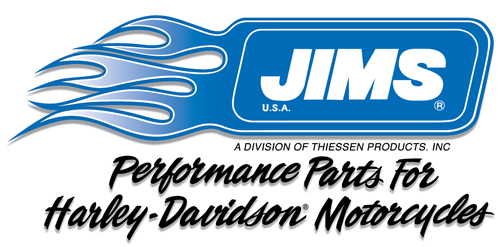
Enhancing Dresser Stability
By Bandit |

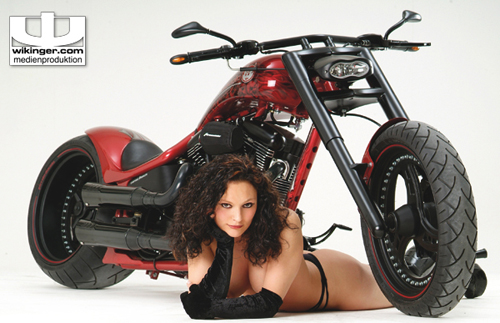
For those who know me, you all understand that I am an imperfect perfectionist. For those who do not know me, it means if there is something that is bothering me – then I have to fix that problem right away. Here is my latest conquest on the highway of life.
Lately I have been researching a solution to something that is dear to me – Why do the Harley touring bikes get so squirrelly at high speed (over 85 mph)?
When I first got the shop bike it had been neglected. It is a 1999 FLHTPI (or cop Electra Glide). After rescuing it from the attic of a local H-D dealer I began to test different ideas on the bike as far as performance. I soon found that it does not matter if you make the engine a hot rod monster, if the chassis cannot handle it. So my focus changed.
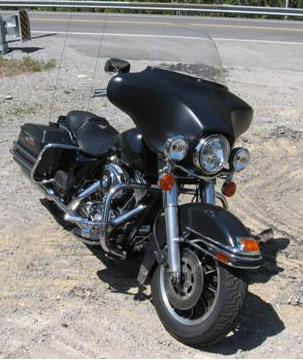
A few years ago I met the creator of the True-Track at the Cincinnati V-Twin show, Wil Phillips R.I.P. He demonstrated the dynamics involved with and without his product. I bought one and began with that.
Before installing the bike would start a wobble in curves at 40 mph, and after installing the bike could handle the same curves at 60 mph without a problem.
Soon after that was cured I began running with the big trucks on the interstate. I then found another wobble issue. At 90 mph if there was a semi truck ahead, there would be drafting turbulence that caused the bike to wobble from the front end; also when riding 90 -95 mph in a lean I discovered another wobble.
With this new problem came a thorough front to rear check. Everything was within specifications. So then I sought out other riders and found Road Glides allegedly did not have this front-end issue. I even met a H-D factory rep at a State Rally and pressed them, if they experienced wobbling with their Electra Glides. The only answer they could give was that the fork-mounted fairing had limitations. BIG SURPRISE!
So if the issue is the fairing, then I looked towards other manufacturers of motorcycles also featuring fork mounted fairings and could not find the same issue. So what is different about the Electra Glide? As I poured over the bike time and time again, I kept noticing the front forks on FLs are set up different than anything else on the road. The fork tubes follow the steering stem, but all the others have the fork tubes in front of the steering stem even if is a just slight amount.
So the closest front-ends to what FLs use are very similar to the front forks on sport bikes. Then I started looking at the sport bikes for what they did to reduce or even eliminate high speed wobbles.
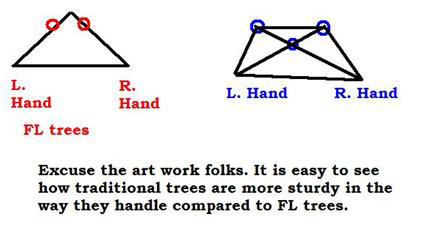
So most sport bikes have the swing arm tied to the frame. The FL swing arm is hinged to the rubber-mounted drive-train, and H-D drive-trains are coupled at three points to the frame. The next comparison was the front end. Many track operated sport bikes use steering stabilizers. In fact some manufacturers install them at the factory on some models. There was the key; a steering stabilizer might actually work.
Then began all the emails, phone calls, and online research. A fellow rider suggested I contact Wheelers Performance located on the famous Dragon, US 129. A call to them confirmed they did install steering stabilizers on Road Kings to help reduce wobbling when running the curves at high speed. As soon as I could get the time I threw a leg over my shop bike and rode full tilt over to their shop for a quick explanation of their installation and to order the parts.
After a few weeks I received the kit and went about installing, but not in the way they suggested. There were two reasons: 1. the original had the stabilizer placed with the adjuster going to my right and I wanted to have it on my left so that I can adjust it on the fly and 2. I wanted to retain the air baffle that the older FLs have to prevent the air from coming up in behind the fairing.
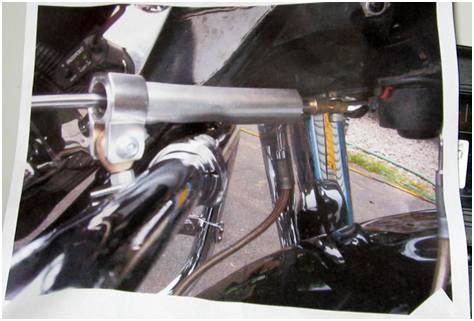
So as I began to tap the hole, I found that the tap handle could not rotate enough to reset for another grab. As I studied the tap it occurred that the drive end fit near perfect into the 1/8-inch drive of a socket. So after placing the two together, I used an Allen socket to fit in the business end of the socket and attached the socket wrench to the tap.
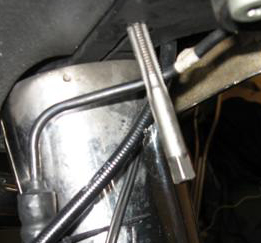
I carefully started the tap until I got a bite. Then I hosed the tap from the top down with WD-40. Carefully I turned the tap until an occasional bit of metal residue would stop the progress. A little backing out of the tap and then some WD-40 to flush out the residue would allow progress to continue. Then I would continue until at last the threading was complete.
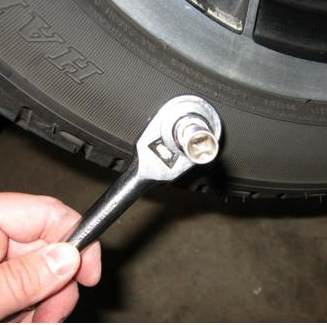
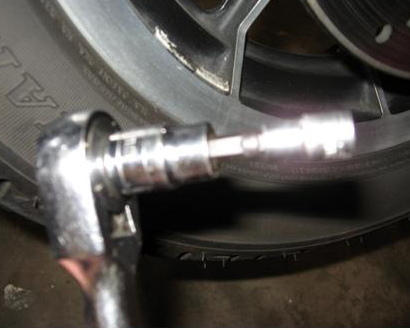
I installed the mounting tree end of the stabilizer as suggested, but found that the stabilizer passed over the crash bar and prevented the forks from turning enough to lock. Also the tree end was binding slightly. So I removed the bolt and installed a nut to act as a spacer so that tree end could move through its full range.
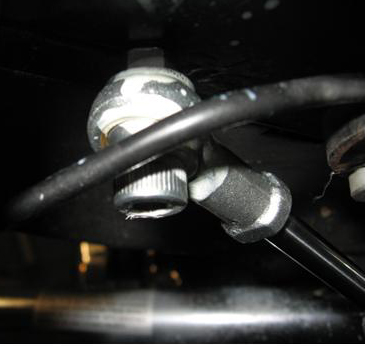
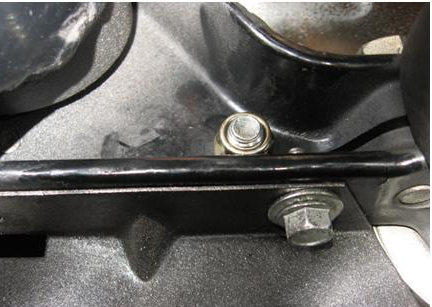
The crash bar mounting fixed itself at this point; the stabilizer could go under the crash bar and allow the air baffle to continue as intended. I checked several times about losing one inch from the fork travel. It did not seem to be problem in the shop so the real world would have to be the testing ground.
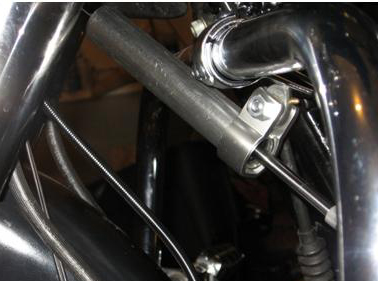
With the stabilizer installed, I began the real world test. I found that the curves that the bike went from handling at 60 could be taken at 70-75 mph without a problem. I also found that potholes and other surface irregularities were not a problem either. The front end stayed where I intended it to be. Even riding at 95 mph was no longer a hair-raising experience. Perhaps between prevent the driveline from moving side to side and adding the stabilizer the Electra Glide can be a true touring bike?
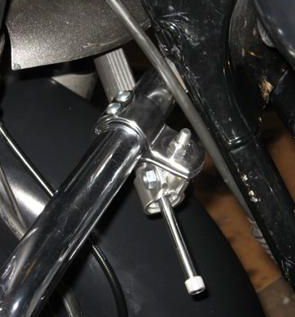
I sat down and drew out a sketch of what is involved both with and without the stabilizer as well as comparing the FL tree end to a more traditional tree so that other cans visualize the dynamics involved.
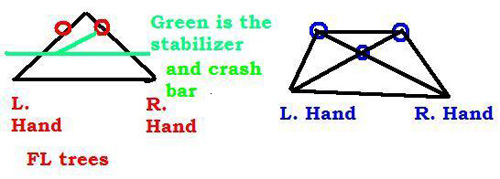
So I will be testing this as time goes on. Be sure to check out the Latest News on my shop’s website www.R-RatedCustoms.com for the progress. Once this setup proves itself worthy I will put together a complete installation kit so fellow FL riders can fully enjoy their motorcycles as I am now able.
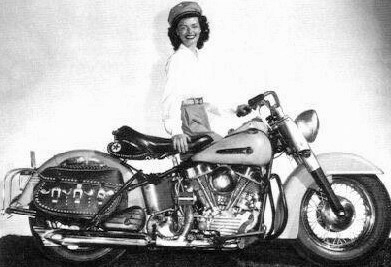
Feel free to contact me with any questions,
Anthony C. Roberson
R-Rated Customs
(931) 607-7399
rratedcustoms@bellsouth.net
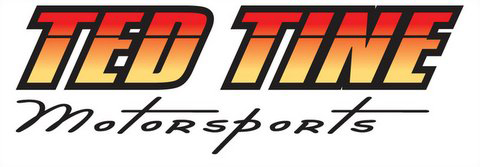
Brass Balls, Bikernet.com and Iron Works Sweepstakes Bike, Part 4
By Bandit |
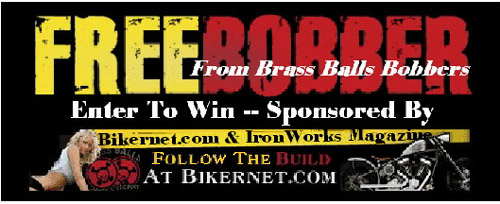
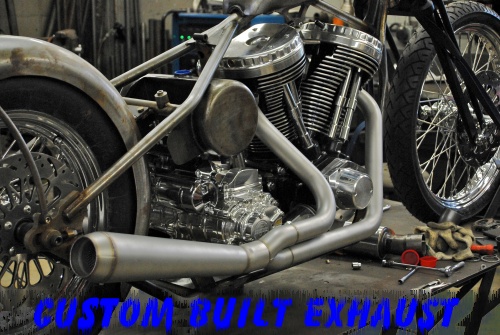
With apologies to a credit card company whose television commercial was popular a few years ago, our theme this month for our Brass Balls Bobber Giveaway Bike is “ownership has its privileges.”
So we’re privileged to share with you some first-time photos of products that have been only recently developed by Darwin Motorcycles (parent company of Brass Balls Bobbers) specifically for this bike. By the way, these same parts will become production items, available for future BBB bikes that Darwin Motorcycles will offer to the public.
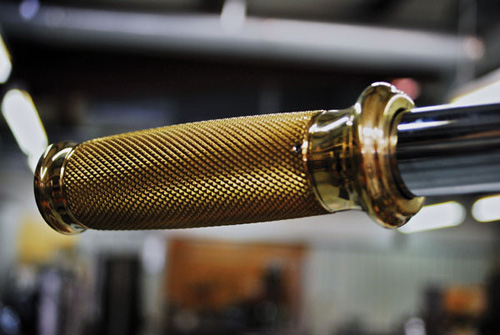
Enough about BRASS BALLS customer bikes, let’s talk about your new bike. You know, the one that you’ll win because you subscribed or re-newed your subscription to IronWorks Magazine or you’re a Bikernet.com reader.
This installment focuses in particular on the exhaust for the Crazy Horse 100 engine, the Rich Phillips custom leather seat, foot and hand controls by Todd’s Cycle, and a sneak peek at Brass Balls Bobbers’ first-ever billet wheels.
We’ll start with the exhaust, which, when it’s completed, will feature a new, exclusive finish by BBB, what they call the Faux Ti. This is essentially a finish to the stainless steel surface that, when completed, resembles titanium. Using a special bead-blasting technique BBB is able to make stainless steel tubing look like titanium.
“It has the strength of stainless steel, with the look of titanium,” said Dar Holdsworth, of Darwin Motorcycles/Brass Balls Bobbers.
Connection with D&D Performance Enterprises
Fact is, Darwin Motorcycles worked long and hard with D&D Performance Exhaust to develop this 2-into-1-style system that meets EPA regulations, delivers improved performance, looks great and offers customizable options for their customers. The new system includes a common header pipe design that accepts any of three muffler concepts.
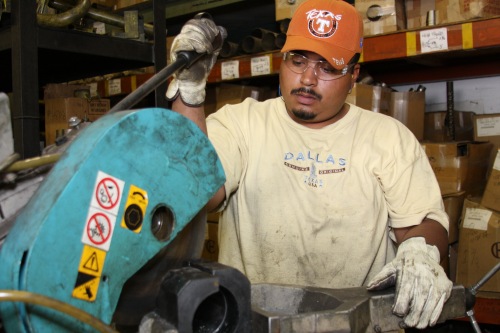
“We developed a set of headers that are common to each bike,” said Dar. “Then the customer can choose from a Fat Slash Cut, a Reverse Megaphone or a Sport Canister muffler.” The systems will be available with Faux Ti finish, or more conventional stainless, aluminized or black ceramic coatings. “We’ll unveil the Faux Ti finish for the first time on the IronWorks/Brass Balls Bobber Giveaway Bike,” added Dar, hinting, too, that the Bobber will sport the reversed megaphone system.
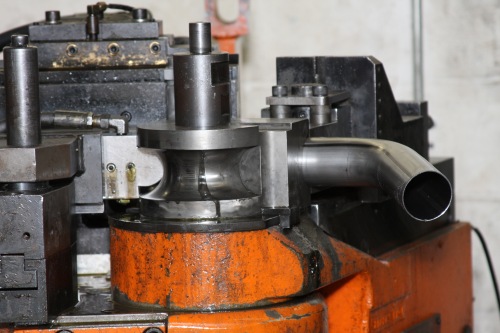
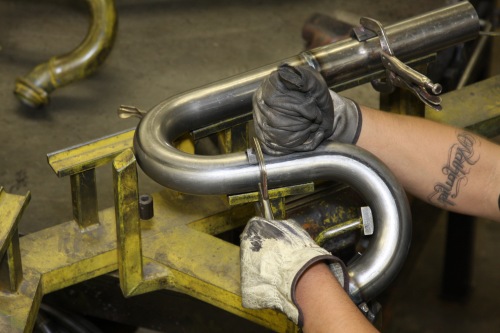
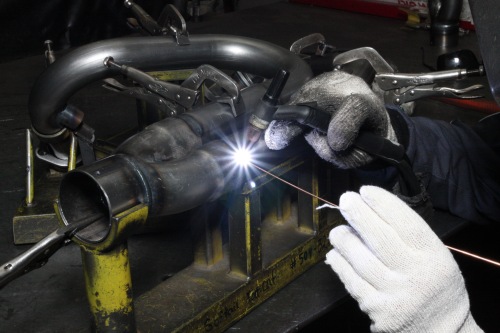
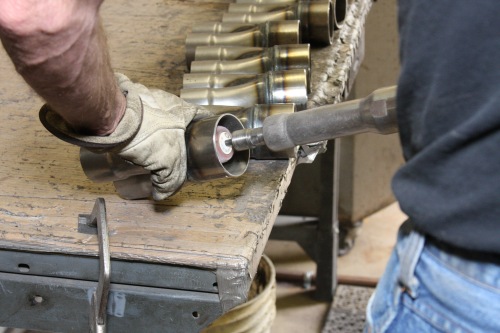
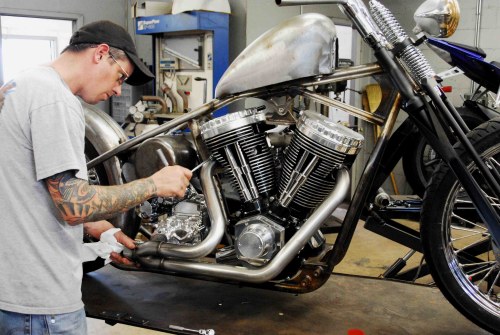
Now, Let's Talk Wheels
“Here’s a sneak peek at a computer rendering of our new billet wheel upgrade,” explained Dar. “After many hours and revisions, we’ve come up with a wheel that has great style, performance and uniqueness. Check back next issue to see the real thing.”
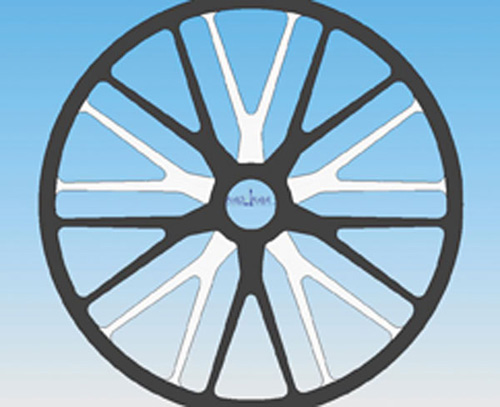
The “real thing” is the first-ever billet wheel on a BBB bike.In the meantime this issue shows the real deal in terms of the custom seat that Rich Phillips stitched for the bike, and the cool brass handgrips and foot pegs that Todd Sicilanto of Todd’s Cycle built for the bike.
“Both of these men are accomplished bike builders in their own right, and we’re glad to have them as part of this project,” said Dar.
Custom Hand-tooled Leather Seat from Rich Phillips
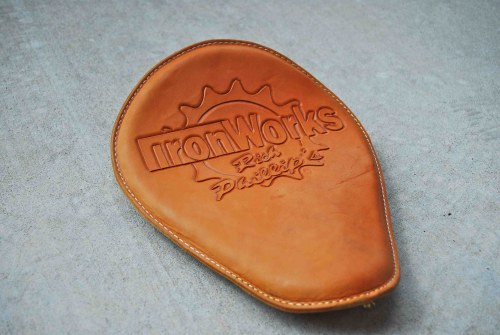
Rich started out doing this type of work at the of 15 when I went to work for my uncle at his upholstery shop. After years of apprenticeship he broke out and has never looked back.Rich's specialty is tooled veg tanned leather, with custom art work. The giveaway bobber seat is extra comfy because it includes medical grade gel pad.
Selecting a Winner on January 31, 2009So there you have it—seat, controls, exhaust and a first look at BBB’s first-ever billet wheels. Remember, we’ll select the bike winner on January 31, 2009. Who will that person be? Well, just keep in mind that old adage that says you have to enter to win. So if you’ve entered, it could be you. Good luck!
Brass Balls Bobbers Motorcycle Resources
Brass Balls BobbersOklahoma City, Oklahoma405-285-0808 http://www.brassballsbobbers.com”>www.darwinmotorcycles.com >
Rich Phillips CyclesHazelwood, Missour314-392-7841 http://www.bikersaddles.com”>www.bikersaddles.com >
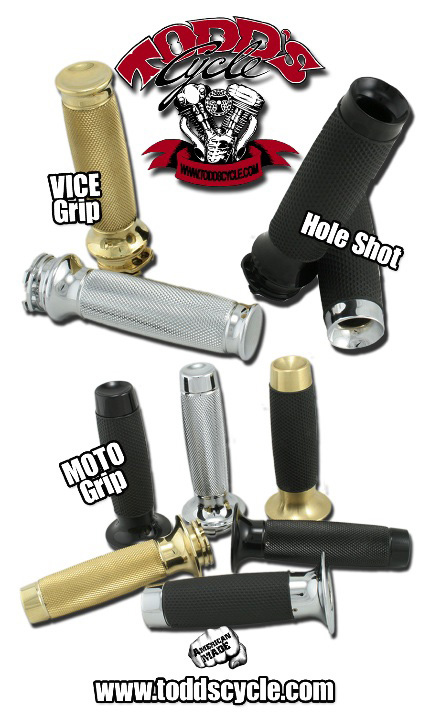
Todd’s CycleHuntington Beach, California714-901-4516 http://www.toddscycle.com”>www.toddscycle.com
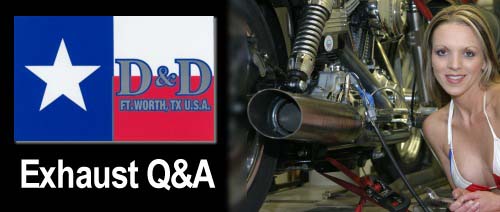
D&D Performance ExhaustFort Worth, Texas817-834-8961 http://www.danddexhaust.com”>www.danddexhaust.com >
Speaking of finished bike, we’ll be showing you some of the final build and paint prep photos in the next issue of Iron Works and shortly thereafter on http://www.Bikernet.com”>Bikernet.com >, then look for the build’s conclusion in the January/February issue.
You Are Eligible
Also keep in mind that if you start or renew your subscription to IW before January 31, 2009, you’ll be automatically eligible to win this bike. May the best subscriber win! up your mouse and register today to win the giveaway Digger.
Sponsors For Our Free Bobber


Darwin Motorcycles is a Registered & Licensed NHTSA Manufaturer and listed with Kelley Blue Book. Our bikes are easy to finance and insure. Call 405.285.0808 for more details.
Stay Up To DateStay up to date on our latest news by receiving our newsletter.
You can WIN this Bikernet / Brass Balls Bobbers / IronWorks Magazine giveaway by here for details.
You See How We Do ItNow it's your turn to build a Brass Balls Bobbers' Digger. Create your own custom sled by here. Return To The Giveaway Bobber Build Page.
–Jeff Najar
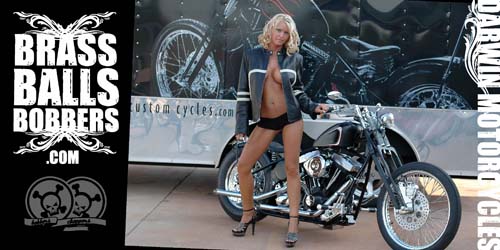
You Want To Be A Weldor?
By Ronnie W. Powell |
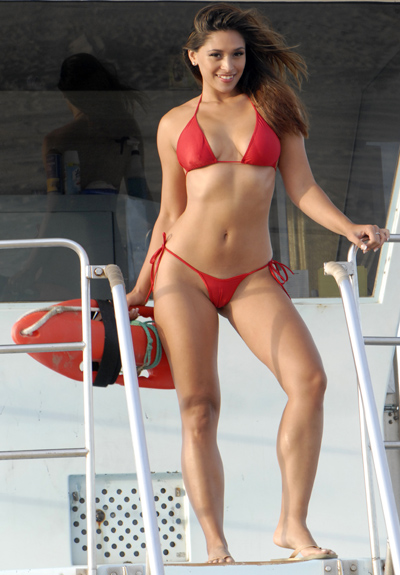
Master weldors make welding look so easy and so essential that many of us are tempted to rush out to the nearest tool store and buy a full featured TIG machine – even if we don’t know what TIG stands for, what it does, how it works, or how to use it. We’ve been lured by custom bike builders in magazine articles or TV programs where, without apparent thought, they grab an always handy, ready-to-go welding torch; snap down their welding helmet; and merrily fuse the seams of an aluminum gas tank. Their welds of orderly, evenly spaced, identical swirls are so perfect you think that’s the way the bead flows out of the stick.
Before you go on that shopping spree, let’s talk to a real world weldor and get a better idea of what this welding thing is all about. What is it? What is the difference in Stick, MIG, and TIG? How does it work? Is it that simple?
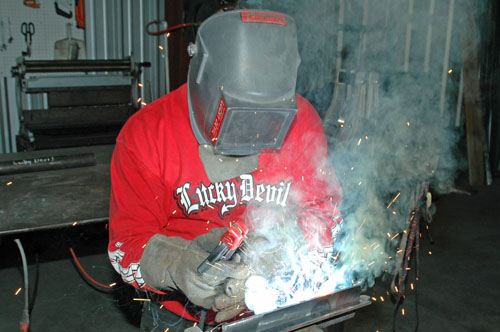
Let me introduce Mr. Kent Weeks (aka Mr. Devil) the master weldor at Lucky Devil Metalworks in Houston, Texas. He is definitely one of those craftsmen who really can make welding look easy.
Over Kent’s career he has worked as a professional fabricator and weldor on a wide variety of things from large industrial parts, handicap vehicles, elevators, wheelchair lifts to hot rods and custom bikes. He’s worked with exotic specialty materials, performed micro-welding, and operated machine shop equipment. But it’s Kent’s passion for welding that lead him to run The Best Little Fabhouse In Texas where he builds custom motorcycles and customizes stock motorcycles. Kent says he’s had the opportunity to learn how to use all kinds of equipment from different welding processes and fabrication tools but that he hasn’t done or seen it all. Good thing too ‘cause it would only make his head bigger.
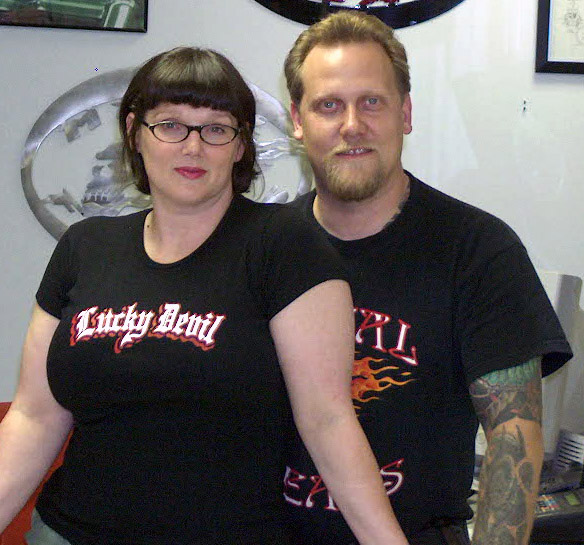
What is Arc-Welding?
Arc welding is a fusion process that joins metals by using an electric arc to apply intense heat at the joint between two pieces of metal. The metal is melted and caused to intermix usually with an intermediate molten filler metal. When cooled and solidified, the metals are permanently bonded together with the joint having the same physical properties as the original metals. For convenience, we’ll refer to arc-welding as just welding from here on out.
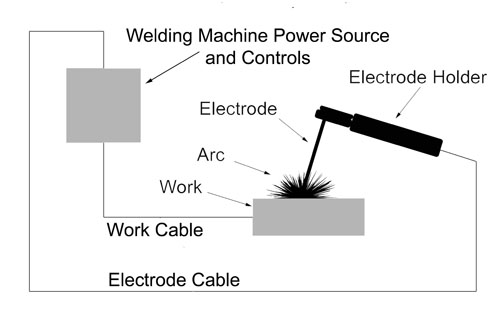
The basic welding circuit consists of a power source connected by a work cable (often called the ground) to the work piece and by a electrode cable (often called the hot cable) to a holder with a welding electrode. An arc is created with the electrode tip touches the work piece and is withdrawn a short distance. The arc produces a temperature of about 6500°F at the tip that melts the base metals at the joint.
Since metals at high temperature react to the oxygen and the nitrogen in the air, the molten pool must be shielded by an inert gas or slag. This shield prevents bubbles forming in the weld which would weaken it. The basic welding circuit is the same regardless of the welding process.
The three commonly used welding processes are:
1.Stick Electrode or Shielded Metal Arc Welding (SMAW)
2.MIG for Metal Inert Gas or Gas Metal Arc Welding (GMAW)
3.TIG for Tungsten Inert Gas or Gas Tungsten Arc Welding (GTAW)
Stick Electrode
Kent says that stick welding is perhaps the oldest form of arc-welding, having been around for decades, like his grandfather’s old cracker box. These simpler machines are common in many garages, home shops, and farms. While they aren’t used as much in the motor sports industry, the process still has a solid place for rough fabrication, repair work on fences and trailers, and especially in heavy industry such as oil field work, mobile welding, large equipment repair, building construction, and underwater welding.
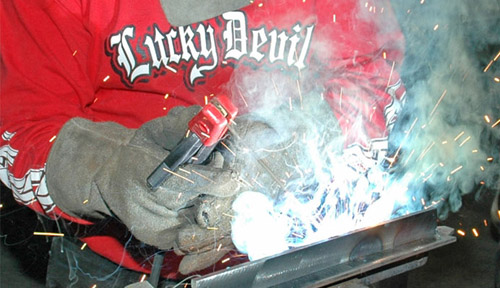
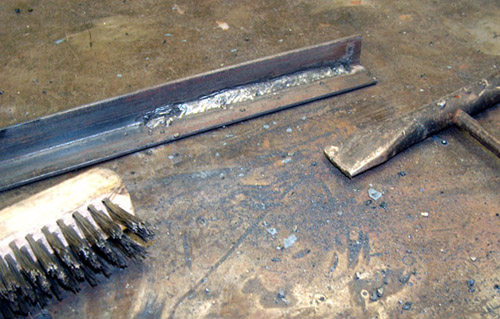
Stick or SMAW welding requires a holder for the replaceable welding rod (or electrode). The rod completes the electrical circuit and is consumed by the welding arc. The rod supplies both the filler metal for the weld bead and a chemical coating that when burned creates protective gasses to shield the molten metal. Since there is no need for a bottle of inert gas, the stick welding process is the simplest and requires the least equipment. Welding rods are available in a wide variety of sizes, materials, and coatings.
Stick welding can be used for almost any application. Its main disadvantage is that the slag leaves a messy weld and there is usually more spatter than other processes. The spatter and the slag must be chipped and cleaned away before painting. Also, starting the arc requires a light hand. Most beginners will burn up a lot of rods sticking them to the work material.
MIG
MIG or GMAW welding is a well established and easy to use process that’s also common in many home garages these days. MIG welding can be used in almost any application. It’s most useful for light to medium fabrication projects.
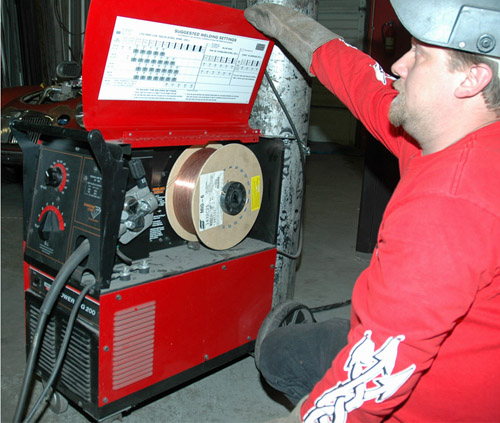
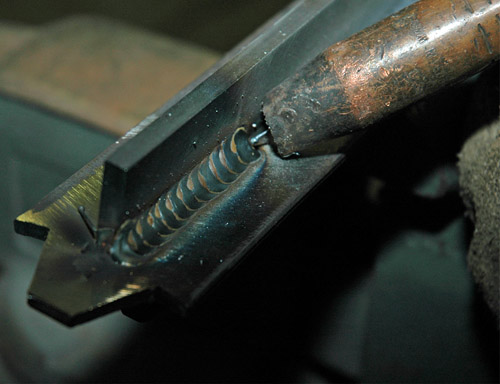
MIG welding uses an electrode cable that includes the circuit wire, a tube for the filler wire, and a tube for the inert shielding gas. The cable ends in a MIG gun with a trigger which activates the electrical circuit, the wire feed, and the gas flow. The filler material is fed by the machine from a spool to the gun.
Kent uses his 220 single-phase MIG welder mostly for welding fixtures and occasionally for use on light fabrication and automotive projects. In it he runs .035 thick ER70S-6 welding wire which is designed for welding mild steel material from 18 Gauge to ¼-inch thick material. He uses .025 wire for lighter sheet metal work. A variety of wire gauge sizes is available for use on thinner or thicker material as well as different alloys such as stainless.
Of course, each wire size and welding situation requires a change in the MIG gun tip, arc temperature (determined by voltage and amperage settings), and wire feed speed. You will find temperature and wire feed setting info on the back of the door to the spool compartment on most models regardless of the manufacturer. Kent recommends fine tuning your set-up by making a test pass on some scrap material before welding your work piece.
To shield mild steel welds, Kent uses a bottle of C25 mix made up of 75% argon and 25% CO2 (carbon dioxide). To shield stainless steel welding, you need to change your gas to ether pure argon or Blue max (90% helium, 7.5% argon and 2.5% CO2).
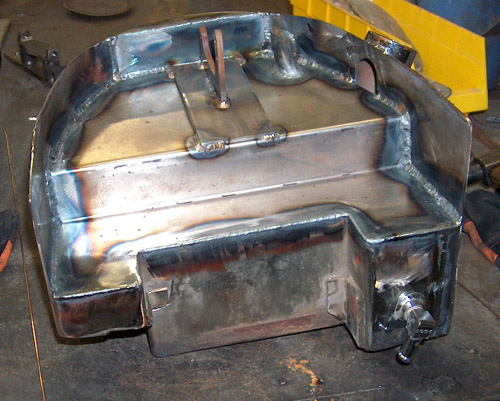
To use MIG to weld aluminum, Kent says you’ll need to use pure Argon gas and to purchase a spool gun to run aluminum welding wire. Spool guns are designed just like they sound; they hold a small spool of welding wire right in the gun itself. This is necessary because the aluminum wire is too soft to be pushed through the lead on a normal gun. This process is messy but it sure gets the job done in a jiffy.
Smaller MIG welders are a good option for custom bike projects in the home garage. A machine like the Lincoln Power MIG 140 is fine for mounting tabs and basic sheet metal work. It’s designed to weld from 24 gauge to 10 gauge mild steel in a single pass with .025 welding wire. If you have to weld thicker material then run multiple passes and pre-heat the work material.
TIG
TIG or GTAW (or for you really old guys, Heli-Arc) welding is a very powerful welding process because it gives the weldor almost complete control of all the welding elements to achieve welds of great beauty, strength, and quality. However, that control brings additional complications requiring a higher degree of knowledge and skill than either stick or MIG. While TIG can be used for almost any application, it is the number one process chosen by professionals in the motor sports industry. Why? Because TIG is a very good process for welding nonferrous metals (aluminum etc.) and stainless steel.
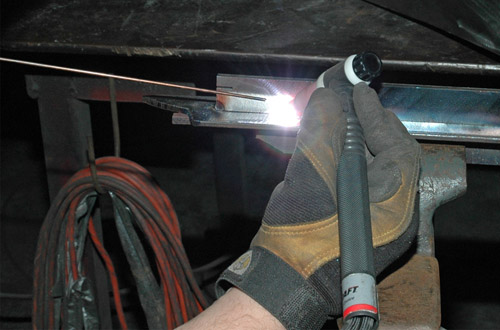
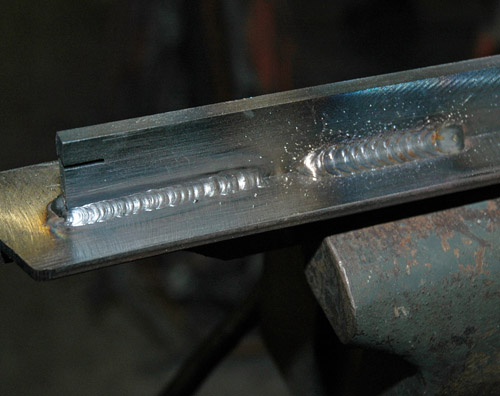
Mention welding to Kent and he will quickly inform you that TIG is his favorite; that he tolerates MIG as a useful, but distant, second, and that stick is at the level of cavemen pounding bronze ore with rocks. Kent has invested significant time and energy (as you would expect from a man following his passion) to learn the intricacies of the TIG process and to develop the expert skills with the equipment. And he’s not afraid to use it.
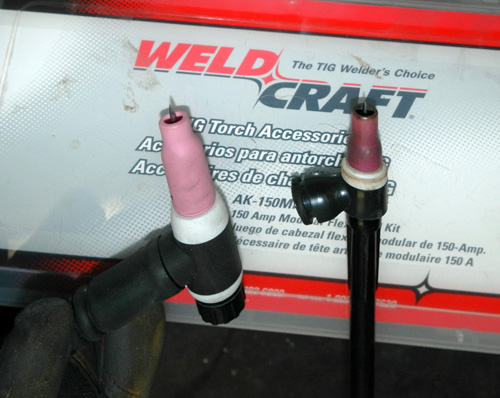
The controls on a TIG welding torch are a little more complicated than MIG gun. Instead of a trigger to turn on the flow of power, gas, and filler metal, TIG uses a foot pedal which variably controls the power output within the selected range. A tungsten electrode is used inside the torch to put the power to the work piece and a welding rod is used to manually feed material to the weld bead in a method similar to oxy-acetylene welding. Starting with MIG experience and learning to TIG weld is sort of like learning to drive a car with an automatic then switching to a manual. You realize you got a lot more to do but you have a lot more fun.
The pointed pin sticking out of the cup of the torch is the tungsten electrode. Its function is to create the arc between the work piece and torch. The tungsten electrode is a non-consumable part and it is important to keep it clean and sharpened to a fine point in order to make a nice looking weld. So if you take it for a dip in the base metal or slam your filler rod into it then you need to clean it up on a grinding wheel or belt sander.
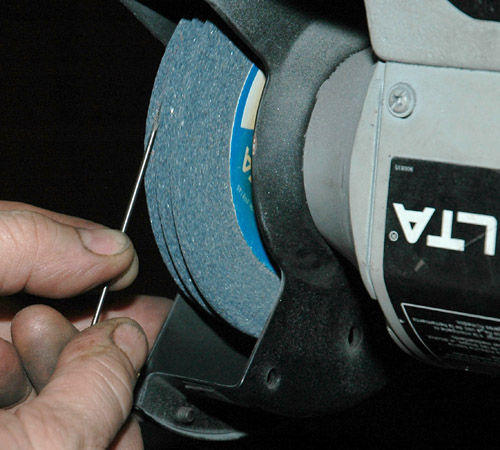
Tungsten electrodes come in many different sizes. Kent uses 3/32-inch the most. For thicker frame pieces he steps up to 1/8-inch and for thinner material he goes down to 1/16-inch. He also has even smaller ones for micro welding but doesn’t get many opportunities to use them. The tungsten electrode also comes in different tungsten alloys. Kent uses thoriated tungsten, which includes 2% thorium oxide, to weld mild steel, stainless steel, etc. and pure tungsten for welding aluminum.
For welding in tight spots, Kent ran across some new Weldcraft torches (the WP-150/200 Series and the WP-125 Micro-TIG Torches) which are designed for advanced projects. These styles are extremely helpful in a fast-paced welding shop or in the hands of a serious motorcycle fabricator.
First of all, the heads on these torches can be changed in seconds without the need for tools. This allows Kent to have a variety of head assemblies ready to go at all times. For all around projects on light sheet metal, he has a straight head, a 90-degree head and a special 90-degree head without a back-cap for extra tight spots. Then for thicker materials like framework, Kent keeps both a large style straight head and a 70-degree head ready. All these are set up with tungsten electrodes, cups and back caps – ready to weld at all times. This flexibility allows Kent to jump from one project to the other.
Secondly, these torches are available for air or water-cooled applications and they are compatible with WP-20 hoses, cables and handles. For those who don’t know (like me), WP-20 style torches are standard on most TIG welders, so chances are you can upgrade your existing power cable to get started and save a few bucks in the process.
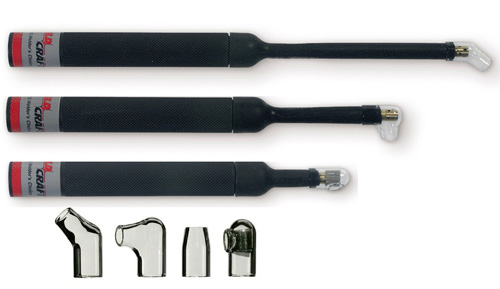
The WP-125 Micro-TIG Torches are great for super tight spots where even flex-heads can’t reach. This rascal can get down in a 5/8-inch diameter hole for nearly impossible welding work. These torches are rated for 10-125 amps (DCSP), 100% duty cycle with quarts nozzles. 3/32-inch chucks are available for increased capacity to 160 amps to weld 1/8-inch mild steel in a single pass.
While too many to adequately cover in this simple article, it’s worth noting that a large number of components and assemblies for the TIG torch are available depending on the welding situation. These include different sized gas cups and back caps; straight or angled torch heads; and air or water cooled heads. Check with your welding suppliers for configurations, which will fit your welding machine.
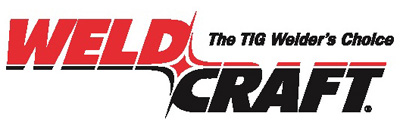
TIG Welding Examples
Kent insisted on throwing in a couple of extra TIG welding examples to illustrate and highlight his favorite welding pastime.
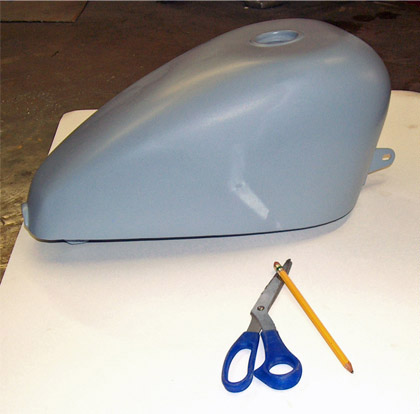
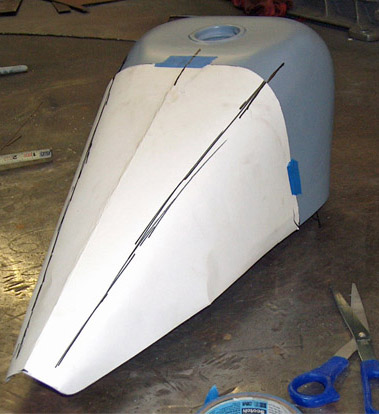
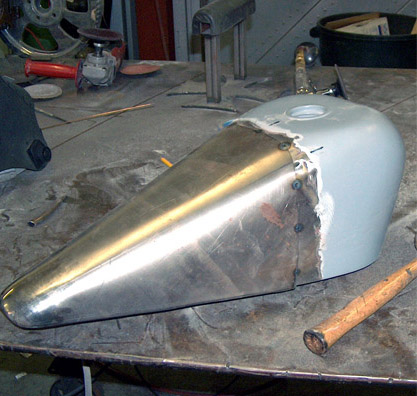
To illustrate a good home-style shop project using basic TIG equipment, Kent shows us how to stretch a gas tank. He used only basic tools and methods available to anyone. First, he used construction paper to make a template, which he carefully fit to the tank using alignment marks. He transferred the template outline and alignment marks to a sheet of 18-gauge cold rolled mild steel. To cut the steel sheet he used a cheap, limited duty electric sheer that he got from a local tool store for about twenty bucks. They work great for occasional projects, there’s no need to get the most expensive tools for every task. Next, he shaped the cut piece to the tank using a solid round bar with the end rounded off. Using the alignment marks and feeling the edges, he tacked the new piece to the tank.
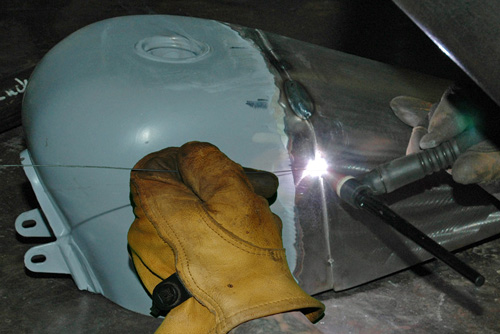
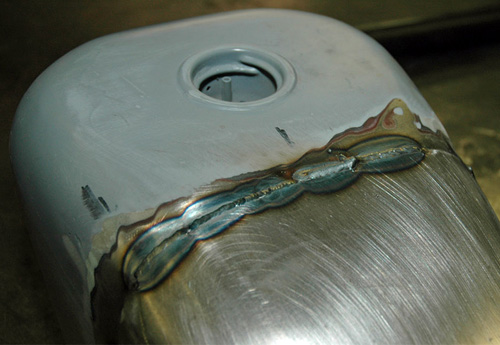
Here’s a Mr. Devil welding tip: On projects like this, use “skip welding” where you run one inch beads separated by two inch gaps, allow the base metal to cool, then make as many passes as necessary until all the gaps are filled. This method keeps the metal from getting too hot and warping. After the welding was complete, Kent sanded the welds to make the bodywork easier. This process takes a little work, but if you take your time and not force the work, you will end with a completed, sharp-looking tank.
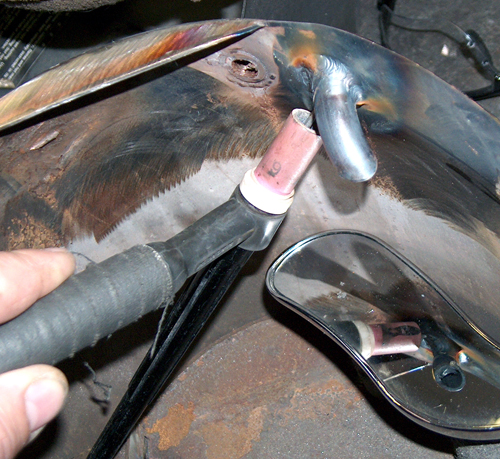
With this project Kent cut the top out of an oil bag to make a place to mount an air pump and the mounts for the air bags under a solo seat. He needed to add a tube for the vent next to the oil return. Not as easy as it sounds, because he had to use a mirror to see the underside of the tube while welding. This sounds funny, but you can get the hang of it if you try hard enough. Even Kent says that no matter how many times he tries this trick, he always sticks the tungsten tip at least once.
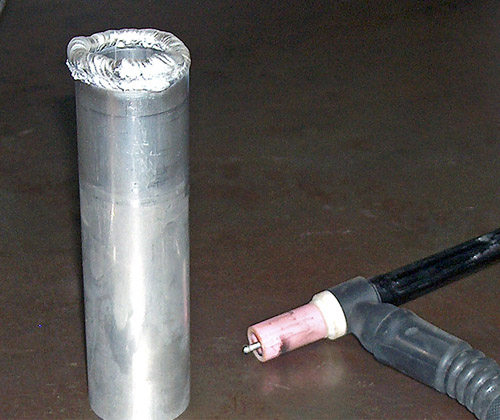
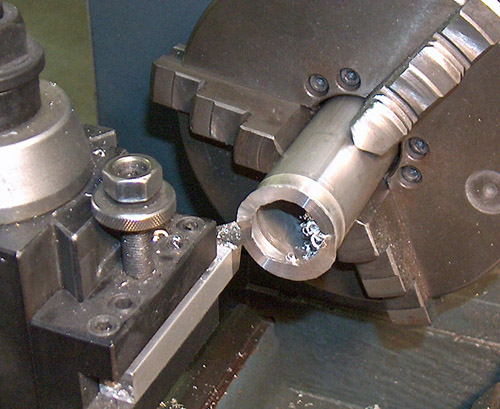
Here’s another of Kent’s, “why use a cheap shim when you can play with cool tools instead,” tricks. It’s very straight forward, to set the endplay on wheel bearings, Kent builds up the end of a center tube then turns it down to the proper dimension. Just think of the savings is shims.
This little exercise reminded Kent of another useful surface build-up application. It’s called hard surfacing. This is where you run continuous beads of a hard alloy (such as chromium-manganese stainless steel) over a cheaper stock material like stainless steel. This is done to provide the benefits of the hardened material without having to make the entire part from the higher cost alloy.
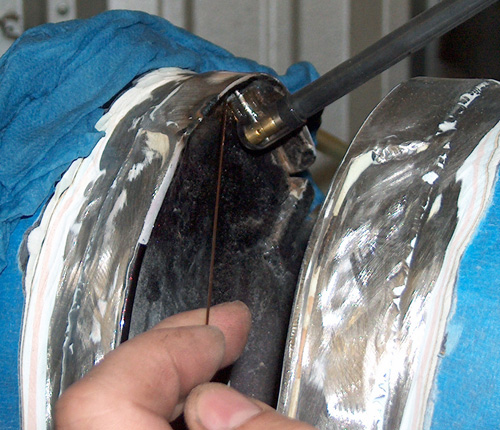
Nobody, not even Mr. Devil, likes to do unnecessary work, so Kent was pleased when he used his WP-125 Micro-Torch with a 90 degree head to reach into a narrow spot and repair a leak in steel gas tank. Normally, he would have to remove and replace the front part of the tank. But with the new torch, he could fit it into the tank channel where a normal sized TIG torch won't go.
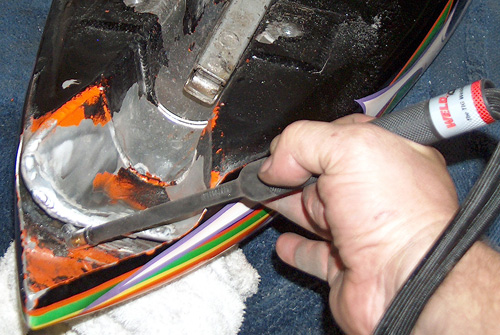
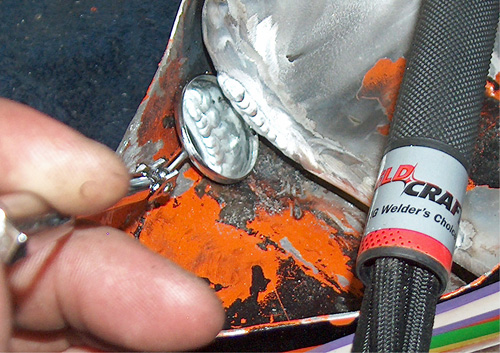
When Kent needed to repair a crack just under the rear stretch on an aluminum gas tank, he turned once again to his WP-125 Micro. This type of job is totally out of the question with a standard torch head.
Mr. Devil says, “That’s the bottom line!” By using the micro torch, Kent avoided major rework on the tank and thus saved some expensive artwork. Kent says he doesn’t keep the micro connected all the time but it sure is handy when needed. While Kent is leery about sounding like a Weldcraft commercial he truly believes this stuff is worth talking about.
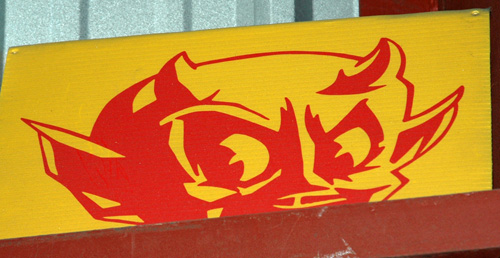
Safety, Equipment, and Shop Tips
Kent’s alter ego may sound evil but when it comes to shop safety, Mr. Devil follows the rules like they were the ten commandants. He strongly recommends you do the same.
He offers these sources for the latest in welding safety so you can decide what is right for you.
•OSHA Safety and Health Topics
•Lincoln Electric on Arc Welding Safety
In addition Kent offers the following comments on particularly important safety issues and throws in some comments on equipment and shop tips.
All welding processes produce toxic fumes which vary is severity based on the welding electrode, shield gas, project material, and any coating on the project material. Exposure standards have been established to protect weldors from over exposure to these fumes. There are different kinds of breathing filters and fume extractors on the market to reduce exposure to acceptable levels. Whether or not you choose to purchase a small portable fume extractor, Kent strongly suggests that you work in a well-ventilated area with an exhaust fan.
Safety glasses are standard protection in any shop and Mr. Devil says. “Use them; you only get one pair of eye balls.” In addition to those, a welding shop requires shaded welding lenses. While many people are familiar with the classic green lens in most welding hoods, there are many more choices. Kent uses #10 gold lenses in his hoods for both MIG and TIG welding and sometimes even a darker one for high heat projects. The gold reflective face is designed to provide a crisper view of the work without the discoloration of a green lens while also reducing temperature and infrared penetration generated from the electric arc.
One particular project that deserves special safety attention is welding on a gas tank. Unless you like bursting into flames, take extra care if you have to repair a tank. Just empting the fuel is not enough. You must also vent the fumes and flush out any residue. Washing out the tank with soapy water and purging with welding gas like argon will take care of fuel. But even if you get a tank that the owner claims is bone dry, they may have used a chemical solution to clean it out and remove moisture to prevent rusting. Flush it anyway. Finally, some tanks may have liquid liner materials that you’ll have to remove. Speaking of which, you may want to line the tank after your repair as extra insurance against leaks and rust.
Most welding shops (home or commercial) have some kind of gas torch to use for preheating, bending, and cutting metal. If so, the smart guys also have fire extinguishers rated for the types of fires they’re likely to encounter and they know how to use them. Mr. Devil relates from first hand experience, if you play with fire and brimstone you will get burned. So have extinguishers handy; and a really good first aid kit too!
Speaking of heat, if you do find yourself working on a project where you need to monitor pre or post heating, then you should have one of Kent’s favorite little shop tools: an infrared temperature gun with laser pointing. Yeah, Mr. Devil likes to use modern gadgets to know how hot it is in his place of worship.
With a home garage your biggest limitation may be your available power supply. Determine what kind of power supply you have or what can have installed. It’s probably best to have an electrician install a specific outlet for your welder. They will also check that your breakers are rated high enough and that the outlets are properly grounded. Have we mentioned fire extinguishers?
Conclusion and Final Thoughts
If you want to give welding a try there are several quality manufacturers to choose from, such as Lincoln, Miller, Hobart, Esab and Thermal Dynamics. In addition to the common welding processes mentioned here, there are a slew of different controls, options and settings that vary from one brand to another. You may want to shop a little and check them all out to find the right one for your needs and preference. Visit the local welding and fabrication shops, they’ll be happy to assist you.If you need welding lessons and you don’t have a weldor buddy to show you the ropes or help you take the next step in skill level then you check you local community college for training classes or metal workshops. Even if you already know how to weld, continuing education will fine-tune your skills and techniques to help make the most out of whatever projects you try.
Mr. Devil says there is more to welding, metallurgy, machining, and metal shaping than he ever thought possible. Go ahead, sell your soul, he did.

Many thanks to Lincoln Electric and Weldcraft for technical assistance with this article.
— Ronnie
Exclusive, First 250 Chopper
By Bandit |
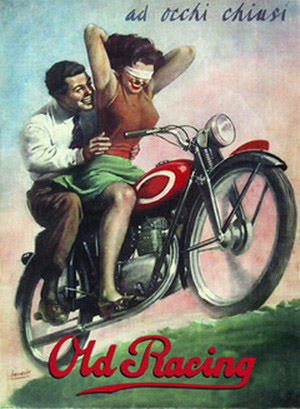
Veterans to the custom bike industry will know the name Johnny Pag, a Master Builder for some 30 years in Southern California, his show winning customs appearing in the leading bike mags. Now he’s about to chalk up a new milestone in the industry. Taking his expertise and designs to China, and working with one of the largest motorcycle/parts manufacturers (suppliers to the Big Four Japanese OEMS) at their 650,000 sq. ft. facility, he closely supervised the fabrication and assembly of the Spyder to American quality standards but with a price tag that will make your jaw drop.
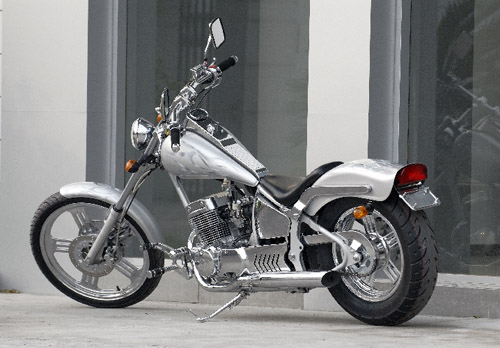
We’re not talking a downsized mini-bike, this is a full-scale, full framed motorcycle wrapped up in a package that includes front and rear disc brakes, custom candy paint, forward controls, beefy 1.25 inch handlebars and custom wheels, not to mention a 2-year, unlimited mileage warranty.
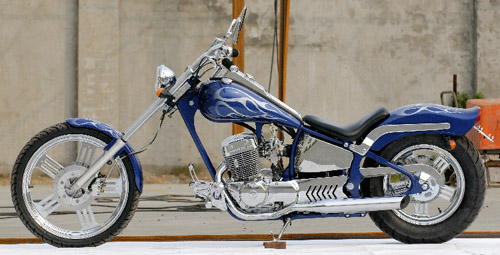
The Spyder 250 as the name implies features a 250cc twin cylinder, four stroke power-plant that brings the bike, as Johnny says, “comfortably up to speeding ticket speeds.” While not aimed at breaking land speed records, the custom chopper will cruise all day and sips gas at 65 mpg. Specs include a dry weight of 360 lb. and a 73-inch wheelbase, a Softail-type suspension with an adjustable seat height of 20-23 inches, chromed alloy rims, 21-inch front and 16-inch rear tires, rated load of 1000lbs., and a 4.2 gallon fuel tank. Colors include candy red, blue, silver and black all with silver flames and an all black model.
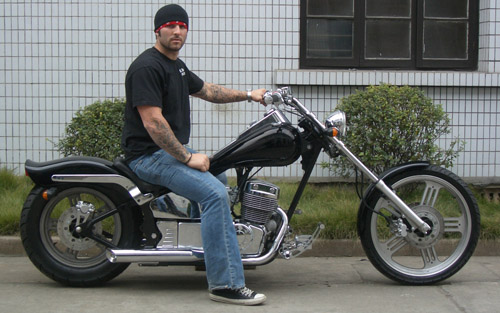
The Johnny Pag 250 Spyder is fully EPA-CARB certified and also carries $2 million in liability coverage that extends to its dealers while every nut and bolt, as far as replacement parts, is available from their warehouse on a 24-hour basis. To qualify as a Spyder 250 dealer, you need a showroom, a service department and a dealer’s license if required by your state. A minimum order of five bikes is also required. As of this writing, some 40 dealerships have signed up for the 250 Spyder, many reporting most models pre-sold. When you check the price tag, you’ll know why. Would you believe a MSRP of $3295?
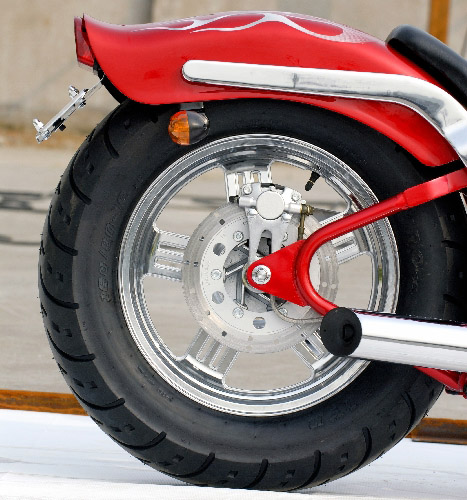
Says Johnny Pag, “We are the designers, we are the manufacturer, we have complete control of our products. We just do it overseas. What others imagined, we went ahead and accomplished. It did take two years of hard work, with me living there, but it was worth it. We pass on the incredible savings but with no shortcuts or scrimping on quality. It’s a great bike for the 18-year old, for the ladies, for the veteran biker looking for a fun around town bike with coolness factor, and a bike you can take home on a credit card. Take a look for yourself. Sit in the saddle of one of our Spyders and you’ll be amazed at the quality and especially the price.”
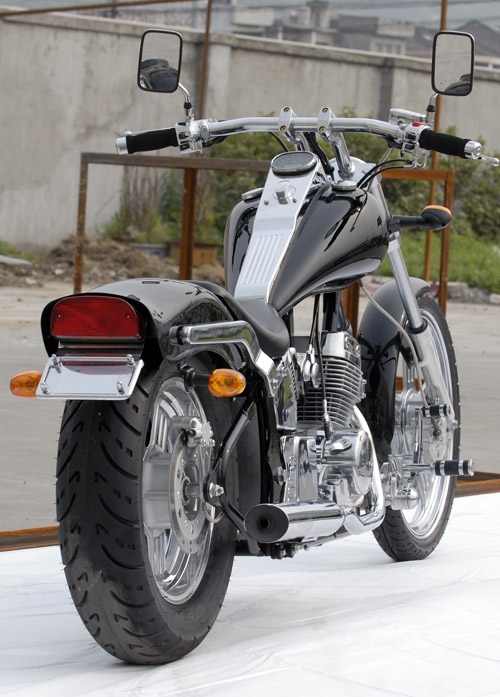
If you’re at Sturgis, you’ll find Johnny Pag Motorcycles with several Spyders on display at Glencoe Thunder Road. For more information log on to www.johnnypag.com or call 951-352-1300.
Enforcer Motorcycle Road King Line
By Bandit |
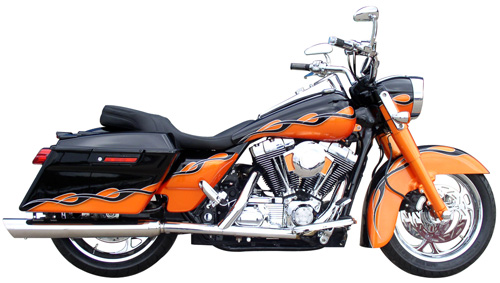
FT. LAUDERDALE, FL (August 30, 2006) – Rucker Performance announces a new collaboration with Bruce Rossmeyer’s Harley-Davidson and Daytona Boss to customize 120 pre-owned Police, Fire and Rescue Road Kings for its “Enforcer” line within the next year. Rucker Performance will start modifying the pre-owned Harley-Davidson Road Kings® this fall.
“Rucker Performance is stepping out of the box and providing high-caliber customization services for customers who want a cruiser motorcycle, the performance of a Harley-Davidson® motorcycle and the look and feel of a one-off custom.
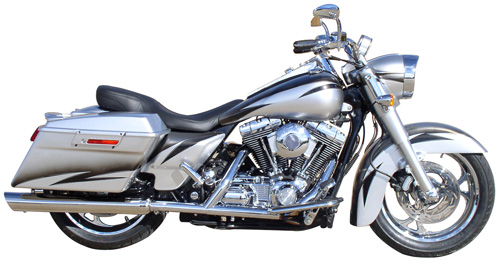
Pre-owned 2005 and 2006 Harley-Davidson Road King Police, Fire and Rescue motorcycles will undergo complete facelifts that include upgrades such as a wide tire 200 mm conversion kits (from the standard 130 mm), a strong performance Screamin’ Eagle Big Bore 96 cu. in. motor, chrome handlebar package (all handlebar components, grips, switches, housing, brake master cylinder and molded frame neck cover), chrome 18-inch wheels, customized fabrication work (extended fuel tanks, front and rear fenders and saddlebags), a custom fitted seat, painted front end, matched to the color of sheet metal, a headlight molding and graphics package with Toxic Paint upgrades.
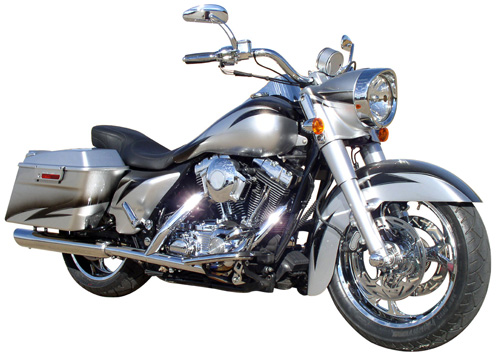
“I am excited about our collaboration with Daytona Boss, my internal customizing department and Bill Rucker of Rucker Performance to provide the world’s first wide tire production customized Harley-Davidson touring motorcycle,” said Bruce Rossmeyer, CEO of thirteen Harley-Davidson locations. “We will be offering our full bike care warranty, which is similar to the Harley-Davidson fender-to-fender warranty, with the purchase of each Enforcer.”
The pre-owned customized Enforcer motorcycles will be available for sale at all of Bruce Rossmeyer’s locations; Daytona Harley-Davidson in Daytona Beach, FL; New Smyrna Harley-Davidson in New Smyrna Beach, FL; Fort Lauderdale Harley-Davidson in Fort Lauderdale, FL; Pompano Harley-Davidson in Pompano Beach, FL; Sunrise Harley-Davidson in Sunrise, FL; Southern Thunder Harley-Davidson in Horn Lake, Mississippi, Grand Junction Harley-Davidson in Grand Junction, CO; Hollywood Choppers of Fort Lauderdale and Arlen Ness of Daytona Beach.

Founded in 2004 by Bill Rucker, Rucker Performance has quickly become a leading designer and manufacturer of custom American Muscle and Chopper motorcycles, high performance street rods and professionally restored vehicles. Log on to www.ruckerperformance.com for more information.
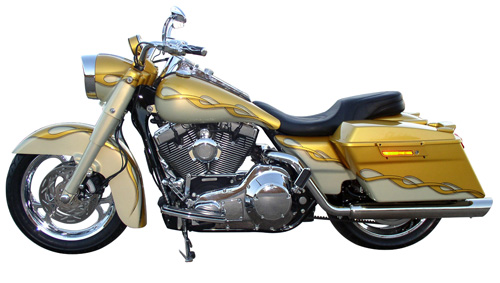
Bruce Rossmeyer’s World’s Largest Harley-Davidson dealership is located at 1637 North U.S. Highway 1, Ormond Beach, FL, 32174. Bruce Rossmeyer’s corporate offices are located at 2871 N. Federal Highway in Ft. Lauderdale. For more information, please call (954) 724-2800 or visit www.BruceRossmeyer.com.
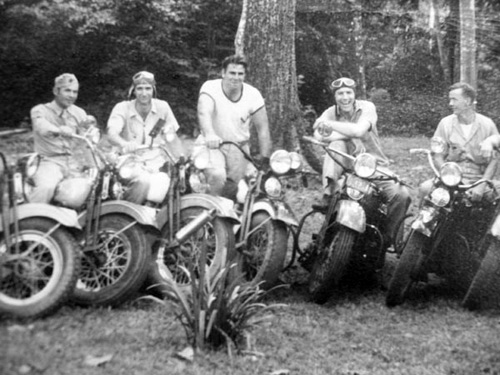
2009 Street Bob FXDB Road Test
By Jon Towle |
By JonTowle
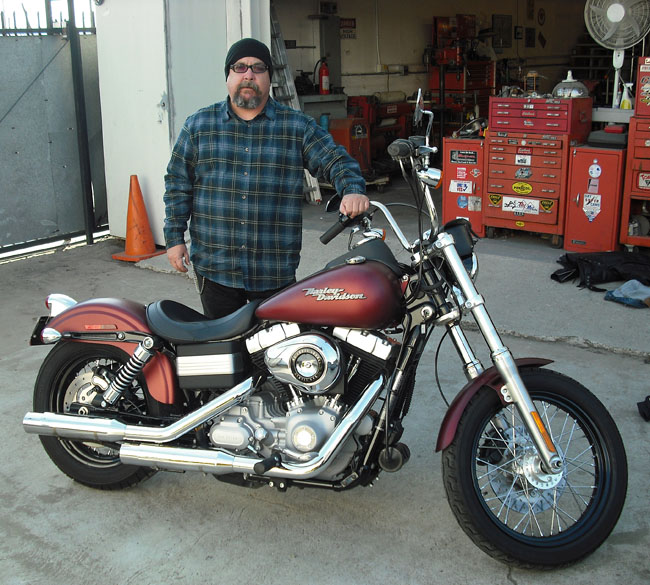
Editor's Note:We could fuck up a wet dream, and we do regularly. This is a helluva example. We should have published it six months ago before the new models slipped into the market place. I don't like making excuse, but Jon Towle, our esteemed test rider has endured family and physical hell. But that's okay, we'll give him hell throughout this feature anyway. I'll make comments in the photo captions–Renegade.
I've wanted to jump on this bike ever since I first saw it. I was strolling the Cycle World International Bike Show aisles a couple few years ago, in the Socialist Republic of California, when I saw the Nightster. Finally my time had come, same ol' routine, I jumped on the freeway from the H-D holding facility, and aimed for home. What a great fuckin' ride.
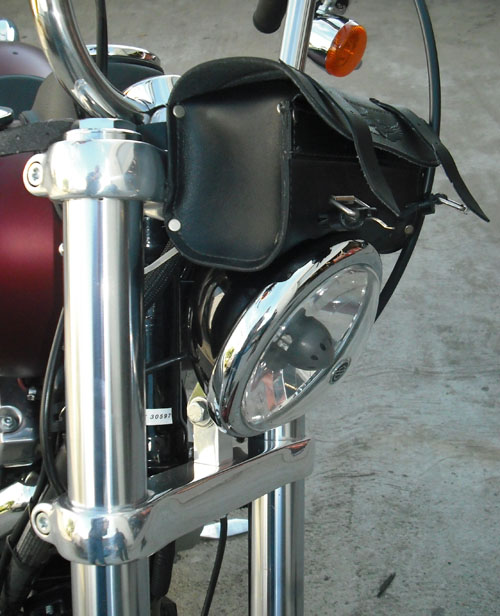
Very stable, really comfortable and she fit me like a glove. A beautiful rust-red color coated the sheet metal. It almost looked like I painted it with a spray can from Wal-Mart…very cool. Bare bones production bike, ya gotta love that shit. Semi high bars, solo seat (yes, there are times when the little lady must park her ass for a ride), bobbed rear fender with a great tail light/brake/turn signal combo! Plus those great rock solid forks like those on the Low Rider, which happens to be my most favorite bike in the line up…thick as the bullshit that comes out of Washington. But, all things must pass, so this baby is the winner for this moment, with a seat height of only 26.8 inches, and that's before my ton-age straddles the poor thing. Just about anyone with the exception of a squashed spider should be able to plant both dogs on the floor with ease while sittin' on this one.
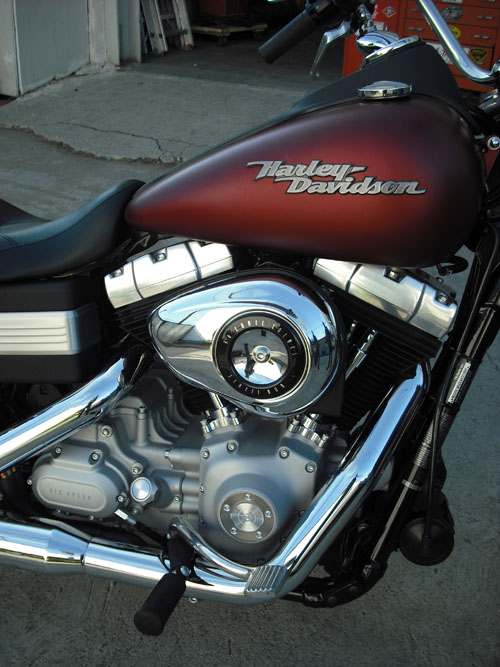
I've been in a constant debate over the Twin Cam engines. I still like the simplicity and classic refinement of the Evo, but as the need for more ridiculous, bone breaking power increases, the platform for 110 plus engines needed the solid infrastructure twin cams deliver. I may just end up being a rebel in favor of the classic separate, single-cam shaft, V-twin until the end.
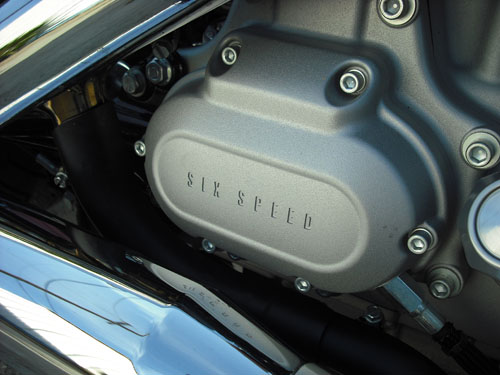
They say she chimes in at 634 pounds dry. It feels much lighter than that number. I wonder why they list the weight without all of the fluids and fuel introduced into the picture? Have you ever ridden a bike dry? Fucker won't even start! So, quit with the dry weight crap. Fill it up, top it off and then put it on the scale fer shit sakes. What, are we in grade fuckin' school here or something? Give the real weight. This has always drove me nuts.
Here's another listing, all of the manufacturers do, that make me crazy: Estimated/average M.P.G. They all (read the fine print) perform this test with a 180 lbs human, during perfect riding conditions. Who the fuck rides in perfect conditions 24/7? How about handling it real world. Perform one test with Mr. Perfect in perfect conditions. Then fire up another round with a fat fucker, riding in strong head wins, up a hill, in LA bumpe-to-bumper traffic, and then once more with a skinny dude in a rain storm. Do that kind of shit and then round it off. You know why that will never happen, because no manufacture would be able to collect those inflated numbers. Not the American bikes, the Japs, the Germans, Italians….none of 'em. We're all aware that bikes get way better mileage than a fuckin' cage…….stop it already!
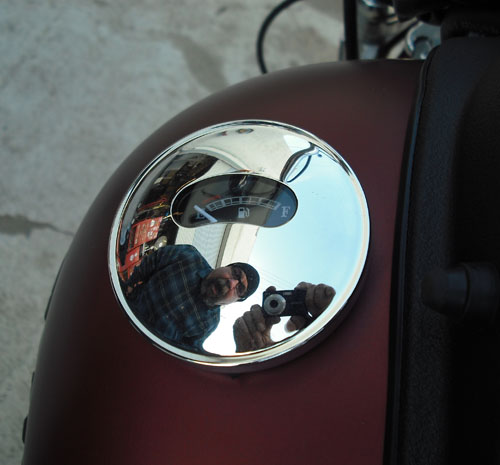
This bike reminds me of an old iron head sporty we will rebuild in the near future. It's sitting in my garage (ask a British cat how they pronounce that word, it's damn funny). They tried to make the Street Bob kinda like a '70s bobber, which hits me the right way, hence my choice for the Ironhead rebuild. Of course the Street Bob is bigger than my basket case, but I think you can dig what I'm sayin' here. If you like that era, this bike will give you wood, as a production bike that has a lot of work already finished for you. She's sweet the way she is. One of the many things I like about this bike is that H-D is copying H-D. They're snagging notions from previous Dyna owners.
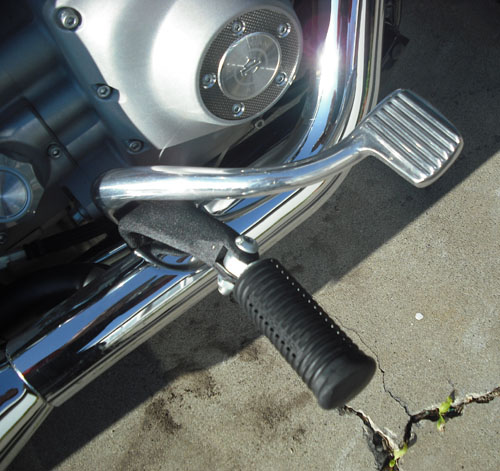
Think about it for a second. Everyone replicates Harley-Davidson, who has always had the corner market on this shit. Fuckin' Honda just came out with a bike called, “The Fury.” It's a facsimile of a Harley chopper, copied from Harley copier? It's enough to make yer head spin. Fuck 'em all……Harley-Davidson copied itself truer than the copiers….fucking brilliant!
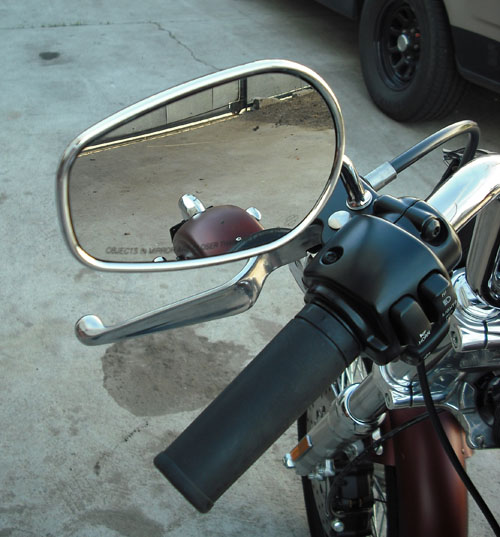
I really enjoyed the saddle time on this one. Unfortunately, said saddle time was cut short even though they let me have more time on this model. You see, I thought it was a grand idea to drop off some photos of a previous test to Bandit out in the badlands of Wilmington, California. It happens to have roads reminiscent of a war zone in Iraq. Let me explain the roads there. This town is right at Los Angles Harbor, one of the busiest shipping ports in the world. So, you have 10,000 ship hands on leave from every walk of life, from all over the world, bouncing around horny as hell looking for pussy and dodging the 40,000 crazy Mexicans driving big rigs from the port to god knows where. These trucker fuckers are flooring it in those big ass heavy rigs and just tearing the shit out of the roads in the area.
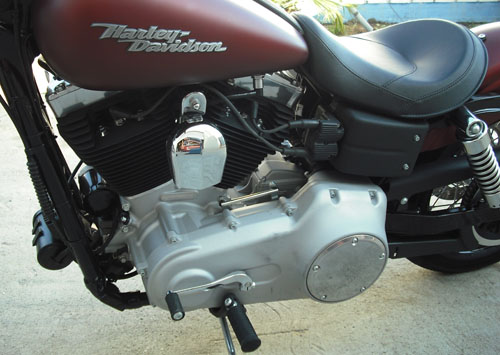
Here I come, innocently, happily puttin' along on my fine ride. It looks like bumps and pot holes from incoming shell fire, and oh so much fun to dodge or get slammed by. Sneaky fuckers too, those pot holes. Just when the road is smooth for a spell, ya think they're gone, but noooo! I smacked one that came out of nowhere, going too fast to react. I personally think this particular one came into existence about 30 seconds before my arrival. I was really gassin' it when I punched the foreword lip of this grand canyon hole and it just about sent me down into the abyss. The bike handled it, but I wasn't so lucky with my body.
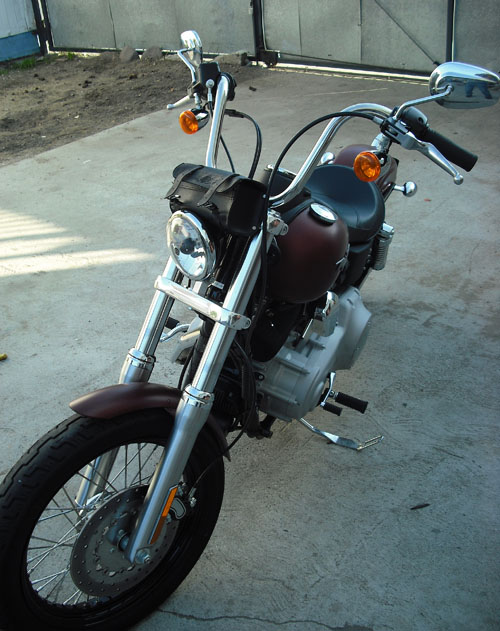
I didn't go down (a miracle) and held on like this was a death grip or die, effort. We limped back to the Bikerenet Headquarters. Bandit, myself and three shop techs looked over the bike and found no damage. It's a fucking Harley, what would ya expect? The official Bikernet Headquarters nurse looked me over with considerable poking and prodding and questions….
“Does anything hurt?”
“No!”
“Did you crap yer pants from the incident? You smell like it.”
“No!
“Then quit yer bitchin', ya pussy,” said Sin Wu, and slapped me on the ass.
“Thank you, ma'am.
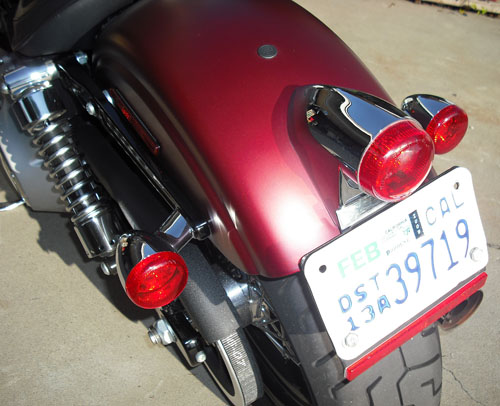

I'm thinkin', this ain't right…something had to have broke or I should be in pain or some shit like that. Nothing, Nada….all seemed fine, so I thought. The next morning, pain hit….pain from the depths of hell itself! like a.44 shot into my shoulder. Had to call my bro (no, not some riding pal) but my biological brother and tell him I needed to go to a doctor as I was passing out from the pain, and thought it might not be a good idea to be driving at this point. After hours past, pills took effect and some booze filled my veins, it was at least tolerable. So, there the Street Bob sat in my garage. Wudda drag. A perfectly bitchen ride sitting there while my shoulder hung like a limp dick.
A couple of days later I was shootin' the shit with my neighbor and he said, “dude, yer left shoulder is hanging way lower than the other.” I sez, “yeah, well it was up late last night and it's kinda tired.” What am I supposed to say…a bump in the road kicked my ass? Anyway, the bike was a blast and I wished I had more time with her, but when you're me, this kind of shit happens. It's the, “Towle,” curse, and I'm thinking of changing my last name. With that said, let's get into some figures and shit about the Street Bob with one of those fancy factory charts. It will tell yooze just about everything ya wanna know about this here bike. See ya soon, Jon Towle–
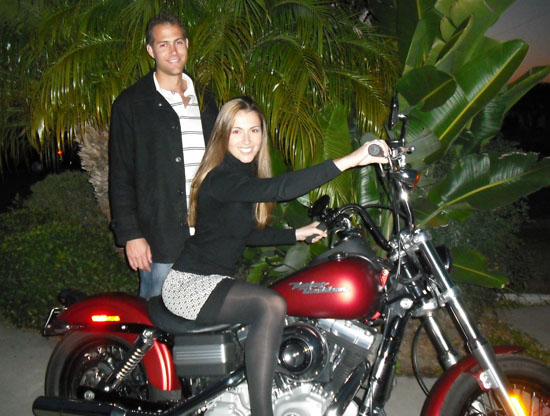
FXDB DYNA STREET BOB MODEL OVERVIEW
A modern distillation of classic post-war Bobber design, the Dyna Street Bob is stripped down to the edge of street-legal trim. That look gets refined for 2009, with a new rear fender chopped even higher and topped with a curved, retro LED tail light. The solo seat gets redesigned, and new laced wheels feature gloss black rims. Internally wired mini-ape-hanger bars, the authentic Fat Bob fuel tank and wrinkle-black trim complete the minimalist Street Bob profile.
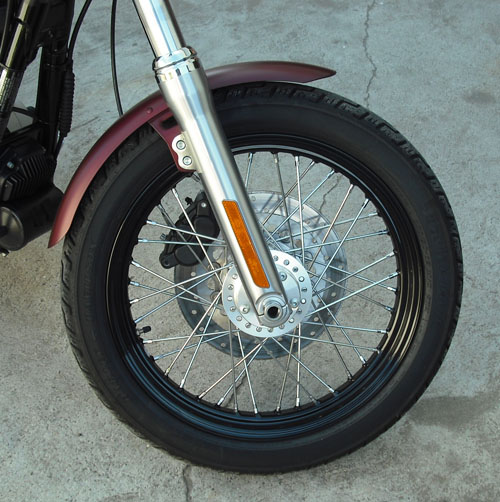
FXDB Street Bob features:
Vibration isolated Twin Cam 96 engine
6-speed Cruise Drive transmission
New black and silver powder-coated engine with non-highlighted cylinder fins
New gloss black steel laced wheels 19-inch front / 17-inch rear
New 25.6-inch solo seat
New chopped rear fender
New retro-LED tail light
New stop/tail/turn incandescent rear signals
New silver-faced speedometer with range countdown
New low profile front fender
New fuel sender
New Straight Cut Chrome Staggered Shorty Dual exhaust
160 mm-17 rear / 100 mm-19 front tires
4.8-gallon Fat Bob fuel tank
Mini ape-hanger-style handlebar
29-degree fork angle
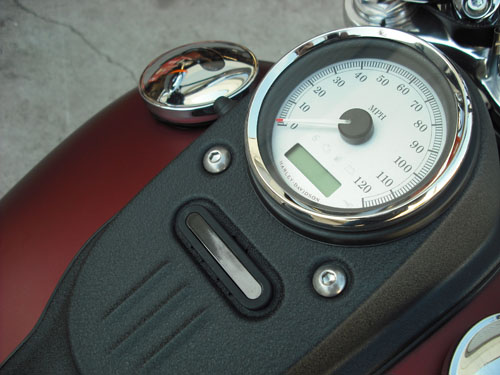
Wrinkle-black console, battery cover and belt guard
Mid-mount foot controls
Optional Anodized Aluminum Profile laced wheelsOptional Smart Security Systembox
