This is a strange one on several levels. I covered it somewhat before when I wrote about Andrew Ursich’s Brass Monkey Sportster, the first bike he built. A high school buddy, Larry St. Marie, invited me to Andrew’s Westside Long Beach shop on the edge of the Port of Long Beach.
As it turned out, Andrew hung out with Kyle Ross, one of my girlfriend’s sons, who I let ride my Sturgis Shovel. That bike drew Andrew away from working on his ’59 Cadillac/El Camino project. The custom world unleashed itself on Andrew a while back when he dove into an apprenticeship with famed custom car builder Gene Winfield, but he was forced to motor 100 miles out into the blistering Mojave Desert to work in the sizzling sun and dust. After two years of developing invaluable skills, he took a secure “regular’ job at the Port of Long Beach, but in his spare time customized his old Caddy in his dinky shop space adjacent to McQuiston’s Custom Cycles, where he glimpsed some additional badass choppers.
With his Winfield training at his back, he handcrafted custom brass-monkey parts for the 1980 Sporty project. It got the ball rollin’ big time, so Andrew, while keeping his full-time mechanics gig at the Port, started wrenching away in his spare time on his second project, the bike called “Stardust” seen here.
“I wanted to build a complete contoured chopper which was challenging, since I hadn’t done it before, so I just started making up things as I went along,” said Andrew. “I cut a big chunk out of the Paughco frame’s front downtube and sent it to Hernan D’Aloia at Engrave It, Inc. for intricate traditional scroll work.” It was actually the first part of the bike completed and set the stage. He also wanted a Knucklehead motor, so it’s a brand new 93-inch S&S Knucklehead beefed up by Bennett’s Performance, in Long Beach at the base of Signal Hill. The motor had to be completely dissembled for engraving.
2. Each part was shipped out of town to Hernan’s shop for engraving.
3. In the case of the downtube, it was welded back into place and supported with slugs to strengthen the frame.
4. Hernan then touched up the engraving where the welding took place.
5. The part was chromed. Unfortunately, the entire frame was chromed, forcing Andrew to strip the areas to be painted.
6. Hernan has a special epoxy material he coats chromed pieces to be gold-plated. The rubber-type material is applied in some cases with a syringe to delicate areas.
7. The coating must be applied and cut away from areas to be gold-painted.
8. The part is sent to the gold plate specialist for coating.
9. Once back in their hands, they needed to carefully peel off the epoxy mastic material and clean each part.
10. For engine parts, the work of removing chrome, gold, or mastic from gasket surfaces could drive anyone out of their mind.
“Yeah,” Andrew said. “Then when she fired up for the first time the gold on the primary chain literally filled the air, but it did remain on the side plates of the chains.”
Most of the contoured areas on the bike were made out of sheet metal and welded into place. Andrew used minimal amounts of Bondo after each piece was carefully formed, welded and finished. He then applied the primer coat and hand wet and dry sanded each piece. Using mostly hand tools, Andrew molded the rear frame/fender/oil tank as one piece.
He also made the hand-shifter linkage, spider top motor mount, and the trick exhaust. Discovering an old girder of unknown manufacture lying in the shop next door, he chopped it up, extended it 9 inches, added a new shock and springs, and then had it engraved, plated, and gold-plated. The girder was originally made from solid square stock. He wrapped each leg with heated half-rounded stock, TIG-welded each piece in place, and ground and finished each piece before they were polished. You know the drill. He spent over $8,000 on plating and engraving.
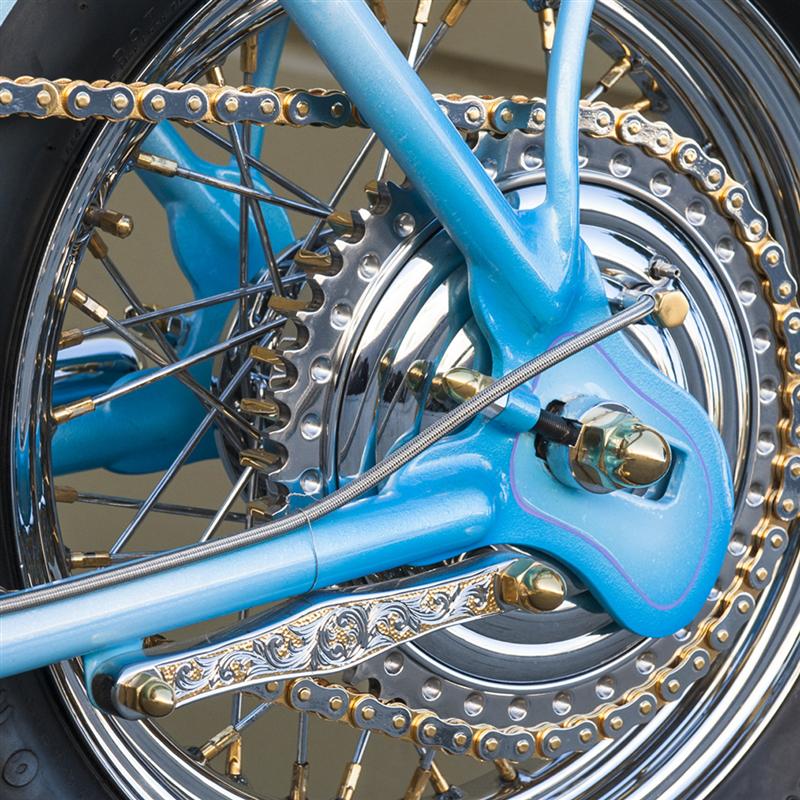
He went for an exotic Italian rear drum brake from Kustom Tech and a 4-speed Baker tranny, with a 4-in-1 drum to give him neutral comfortably at the bottom of the shift pattern. He mated the American-made trans to a foot suicide clutch and hidden internal throttle bar controls.
Danny D in Baldwin Park mixed up the custom ice blue paint, close enough to the color of Stardust. Andrew even built a pivoting frame stand to make painting all frame curves accessible.
In addition, gold plating including every nut and bolt followed extensive chrome plating. Even the chain is finished in chrome and gold with over 200 pieces going to the plater.
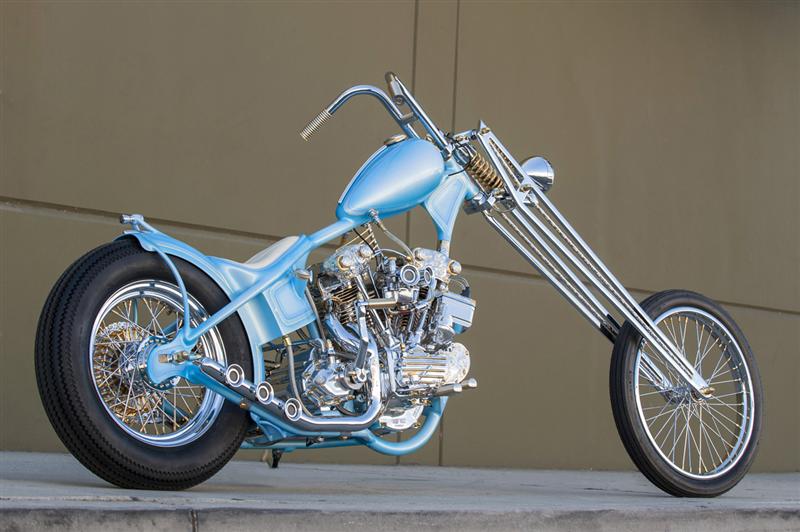
More kudos followed at the 2016 Sacramento Easyriders Show, where “Stardust” added a First Place in the Radical Custom class award to his trophy wall. Topping off the list of accolades was the selection by the vast and unrelenting editorial board, as the Easyriders Bike of the Year.
Not bad for a second bike build. Last week in Vegas, we witnessed Andrew’s third creation and second effort in the biker bling realm. He built a one-off custom around a 1949 British M-100 Panther 600 cc single engine linked to a 1956 Triumph four-speed transmission. It’s another masterpiece and I’m sure it will see the show circuit in 2017, but don’t let the bling get you down. His next bike promises to have bare elements, two engines and have classic racing lines and themes. Hang on!
Owner: Andrew Ursich/Ursich Customs
City: Long Beach, CA
General
Designer: Andrew Ursich
Year/make: 2015 Ursich Custom
Model: Knucklehead
Assembly: Andrew Ursich
Manufacturing: Owner
Welding: Owner
Time: 6 months
Plating/Chroming: Engrave It! (Ontario, CA)
Year: 2015
Model: Knucklehead
Rebuilder: Bennett’s Performance, Long Beach
Displacement: 93 cu. in.
Cam: S&S
Ignition: Morris Mag
Pistons: S&S
Heads: S&S
Lifters: S&S
Carb(s): S&S Super E
Air cleaner: custom dual stack
Pipes: Hand made custom 2-into-2
Make: Baker
Year: 2015 with 4 and 1 shift
Shifting: handshift
Painter: Danny D
Color/type: blue/Axalta
Year: 2015
Builder: Paughco
Type: Single loop
Rake: 40 degrees
Stretch: 2 inches
Other: Engraving by Engrave It!
Bars: custom rabbit eats
Handlebar controls: internal throttle
Fender: Gasbox
Headlight: ‘50s GM
Taillight: After Hours Chopper
Speedo: none
Electrics: V-Twin Mfg.
Gas tank: Lowbrow Alien
Oil tank: custom horseshoe
Oil system: S&S
Seat: California Upholstery
Pegs: JCW
Mirrors: nope
Grips: custom machined
Type: Girder
Extension: 9 over
Builder: Andrew Ursich
Front
Size: 21 inches
Wheel: Narrowglide spool
Tire: Firestone
Rear
Size: 16 inches
Wheel:
Tire: Firestone
Brake: Kustom Tech/hydraulic drum
Photographer: Markus Cuff