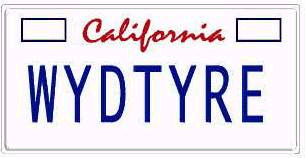
As I pulled to a stop in my driveway, every detail that went into the construction of my new bike raced through my head. It had just completed its first ride, a 250-mile round trip break in.
Motorcycle riding wasn?t exactly new to me. I had ridden plenty of dirt bikes, but riding on the street was completely different. In fact, I?d never ridden a street bike before Memorial Day Weekend 2002. Throw in the fact that I?d just dumped $38,000 and seven months of time and effort into building this bike, taken my first ride during one of the busiest travel and traffic weekends of the year and rode the last 70 miles of the trip at 70 miles an hour into a 45 mph headwind, solo, with a failing battery, a problematic oil breather leak, at dusk and with half of the free world returning from their 3 day weekend.
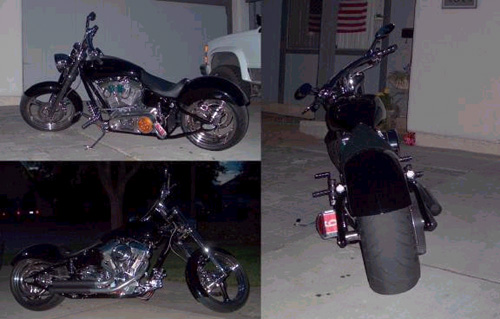
Very first pictures of the completed bike? at dusk, just returning home from the 250 mile-break-in ride
I was ecstatic about the bikes performance levels, but I was happy to be home safe and sound. Going from a lifted 4X4 truck with a fully enclosed 42-inch seat height, to being completely exposed at 20 inches off the asphalt takes some getting used to. So does that semi truck with the 40-foot trailer turning on the direction signals when you?re cruising along somewhere about mid-trailer.
It didn?t help much that my 2 buddies who worked along side me to build the bike weren?t concerned about it breaking down; they were more concerned with the fact that at 70 mph, something bad could happen. You know, ?like the wheels falling off.? But with their beer in hand, they stood safely on their concrete driveway and waved good-bye as I set off for home. ?Good Luck.? They had helped build this bike, and I?m sure they had to have at least some faith in it.
This isn?t a story about first rides, shakedown runs, oil leaks or holiday traffic. It?s a documentary about the trials and tribulations of building a custom motorcycle. As with anything, your results may vary.
Before all of you old skooler?s, long time riders and 1%?ers get all over me for being a newbie with a little bit of disposable income jumping on the motorcycle bandwagon, hear me out.
Building a motorcycle, at least the way I did it isn?t brain surgery. I began this project with great anticipation and high expectations. I had researched the project over a year before I spent any money. I poured over 5 ?big book? catalogs and hundreds of web pages. I had a parts list a mile long. I was dead set on every component that was going to be bolted to this bike. It was something I?ve wanted to do for years. Every other hot rod or custom car project I had ever done was always on a very limited budget. My time had come, I had the means to build something I wanted, the way I wanted to do it, and so I did. More importantly, I had my wife?s signature on the second mortgage giving me the capital to get started.
Basically, that?s exactly what it takes to build a custom motorcycle, capital. Capital and patience. Capital, patience, the cooperation of parts suppliers and venders across the nation, UPS, FedEx, and the individual at the US Postal Service who lost my certified cashier?s check I sent Gambler Motorcycles to pay for my frame.
While building a motorcycle isn?t brain surgery, I found the motorcycle industry to be a bit of a closed society. Many don?t like outsiders coming in and building a bike. I guess they feel it dilutes the bloodline, I don?t know.
It?s not like I came in completely unprepared. I had a strong mechanical sense instilled in me by my Dad. I had years of hot rodding, 4X4 truck modifying, race engine building, and racecar fabrication, machine shop and auto parts counter experience. I know who Willie G, Sonny Barger, Mickey Jones and Billy Lane are. I?ve had e-mail correspondence with Bandit. On a monthly basis I read Easyrider, Hot Bike, Hot Rod Bikes, American Iron, In the Wind, Biker and The Horse. (Just to keep me grounded) I was 6?-3? 230 pounds, drank beer, had long hair, tattoos and liked hanging out in strip clubs. 22 years in construction had beat me down, tanned my skin, wrinkled my face and given me the vocabulary of, well, a biker. In essence, I looked, walked and talked like most bikers I ever saw, minus one thing. I did have some mental reservations buying leathers and a helmet. I didn?t really see myself as a leather-wearing-biker-type. I wear a tee shirt, shorts and basketball shoes, everyday, rain or shine, hot or cold. I just wanted to build a bike and ride it. Leathers were cheap insurance for a new rider, and a helmet is required in California so I got them. A 38-inch inseam happens to look good in leather chaps, or so I?ve been told. I?d never consider myself to be a ?biker,? but I do own and ride a bike I built. That?s gotta count for something, right?
I tried not to ask stupid questions without first trying to solve the problems myself. It takes a bit to break through to the inside of the motorcycle elitists, but once inside, it still doesn?t mean jack to the parts suppliers and venders. It seemed to me, if you don?t have a big name shop, or you aren?t one of the elite builders, chances are you get to wait a bit longer for special order parts. Once while standing in Ron Simms shop after completing my bike, I overheard Ron tell his employee to order parts for a customer?s bike he was customizing. He told the guy to tell the supplier that he wanted a ?Critical Rush? placed on this part order. Whether that was a line he was feeding everyone for the customer?s benefit, or something he has available to him, I?ll never know.
Here is one other bit of information you might find useful when starting your own custom bike project; a ?custom shop? doesn?t mean they make custom parts. It doesn?t mean they can give you a name of a company or individual that makes custom parts. It doesn?t even mean they understand what a custom part is. I am positive shops like this exist; I didn?t find any while building my bike.
I visited every custom cycle shop I happened to drive past during different phases of the construction of my bike. Most times I?d walk in and look around and ask a question about a certain problem I might be having at the time. Of the 7 or 8 ?custom cycle? shops I visited personally around the San Jose/Morgan Hill/Santa Cruz area, not one could give me a name of someone who could build pipes, most had never heard of a right side drive transmission, and one shop completely dismissed the fact that I had a drive side brake system and actually said there isn?t anything like that available. One shop owner, who I had just met 5 minutes before, spent 30 minutes trying to convince me how tough he was, how everyone else (except him) was ?a prick? and how he wanted to tear the head off his ex-wife?s new boyfriend while his own ?slut-trophy-girlfriend? watched. He then proceeded to tell me that the engine I picked sucked, the frame I picked sucked and everything else, sucked. I guess the custom shops I saw, might be able to bolt chrome parts to a bike and then call it a custom. Some, I?m still not sure about.
While this is a small percentage of shops in the area, we decided to spend more time fabricating things we needed, rather than asking for a name to get it done.
While I might not be a ?biker,? I can say I know more about a Gambler frame based, 250 rear tire bike pushed by a 121? TP Evolution, right side drive transmission with a open belt primary, than most other ?bikers? and custom bike shops that I?ve talked to. I understand this is a very limited knowledge base, but at least I know what I?m talking about.
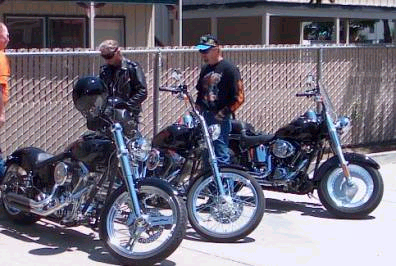
Rob?s custom, Kim and Brian at the Jamestown, CA Harley-Davidson
When building from the ground up, don?t expect a lot of help from instruction manuals that are included or in most cases, not included with your parts. I spent a lot of time looking through magazines, Bikernet.com and other web pages for tech articles and adapted what I learned from them. Simple things like fluid capacities or torque spec?s on aftermarket parts usually tell you to refer to your ?Owner?s Manual.? That isn?t always possible. The bike I built was very simple, because I tried to keep it simple. I bought a custom frame built to my specs, the motor in a crate and the transmission in a box. The motor was carbureted, not fuel injected, electronic ignition, and the wiring was very basic, with few relays or modules. Other than machining a few parts to fit, everything was pretty much a direct bolt up. Even the Billet4U belt drive was simple because of the set up they use. Because of its design, alignment and clearances aren?t as critical as most.
Another important fact is this; Just because you see a pretty picture in a glossy catalog, the catalog says it will fit what you are building, a shop takes your money and orders the part, it doesn?t mean that part is available anywhere in the USA. It doesn?t mean it will be available anytime soon. It doesn?t mean anyone is making it anymore. But it might still be in next year?s catalog.
I had a tach and speedometer on order for 5 months. They were in 5 catalogs and on 16 web pages of various online distributors but no one could find them for 5 months. When they did become available, the manufacture of the 1-1/2? thick handlebars I bought and heavily modified to accept my hand controls, decided that the gauge mount I had ordered from them, which was advertised to fit my bars and gauges, probably wasn?t going to fit the gauges. I called, faxed and e-mailed them repeatedly, asking them to let me know what the solution would be. At the time of writing this, they still have not contacted me. I either wasted $300 on gauges I can?t use, or $350 on handlebars I can?t put gauges on. I?m told this is typical for a custom bike.
Without a doubt, I can say that Gambler Motorcycles is one of the best companies I worked with during this project. CK Spurlock was as helpful and understanding as an individual can be. I chose a Gambler Bigg Ballz 270 soft tail style frame. The choice was an easy one. I had a vision for this bike. Wide tire, wide tank, big forks, and burly look to the overall package. The Bigg Ballz frame is based on a symmetrical design. The frame doesn?t need the 2? offset in the motor that some frame builder?s use. It also doesn?t offset the back tire 2? like others. The reason this is possible is due to the fact that Gambler has seen the right way to build a wide tire bike. They have incorporated the right side drive transmissions now on the market into their frame set-ups. This frame is built so everything is centered on the backbone. Since I have a construction and design background, symmetry it very important to me. Second, the frame is 1-3/8? chromemoly tube construction. You can?t get any better material in a motorcycle frame. CK will also tell you that he has the best welder in the entire world working for him. The 1-3/8? tube size fit the ?burly? theme of the bike. It also had a symmetrical swing arm. It was strong and it was lightweight. The choice was made even easier because I grew up on racetracks in California. Racing, was a big part of my life. I watched the World of Outlaws for most of my adult life. Gambler Sprint Cars dominated the series at the time. The quality race cars Gambler put out every year, along with the innovation they showed me every season were more than I needed to pick Gambler as my frame builder. As a bonus, CK was there every time I had a question. He was willing to help long after cashing my check and moving on to the next customer. This is something I have found doesn?t exist much with a lot of parts vendors.
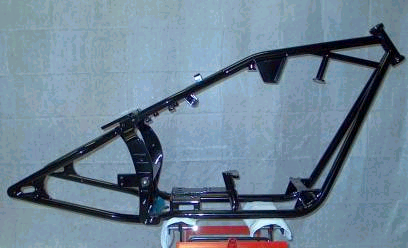
Gambler frame before final assembly
The next choice was an engine. I had picked a 107? Total Performance Engineering motor. I was going to order a black engine and transmission. The TP had great reviews, reliability and a superior oil pump, so it was a no-brainer. They also pre-run the engines, time and tune them. They re-torque the important bolts before shipping. The ignition system, as well as the carburetor and air filter is also included. What happened next took me by surprise. The shop I bought the majority of my parts from, heard about a deal on a polished 121? TP through Drag Specialties. There were only 6 available. I bought one along with a polished Baker Right Side Drive 5 speed, for about $500.00 more than I was expecting to buy the black 107? and transmission for. Very cool. Last, but not least, I can?t say enough about the help and quality parts I received from Todd at Billet4U. The Billet4U belt drive has been popping up all over the magazine pages and he even designed a motor/coil mount for me after we talked about it over the phone. He did some custom machine work to build a wheel spacer for my drive side brake system when PM declined to fix the half-inch misalignment they built into my rear wheel. He always had a kind word and good advice every time I talked to him. After that, it tends to go downhill fast?.. I spent $25,000 in one shop. I would expect, as I?m sure most people would, to get a bit of customer service after spending that much coin in a small town shop. At the very least, a couple of phone calls to let you know how the parts ordering/delivery process was going. In the 7 months I was dealing with this shop, I got one phone call and one page from the shop owner. The page was to inform me, that the Performance Machine wheels I ordered 3 weeks before weren?t available, because they didn?t make an 8-1/2? wheel for the wide tires. I ?informed? the shop owner, he might try again, since they are one of the few that actually do make an 8-1/2? wheel. This was just the tip of the iceberg. It seems my $25,000 parts list wasn?t being delivered as fast as I had hoped. Repeated calls to find out where things were got me nowhere. Parts trickled in here and there for months. The most important thing missing were the wheels, because I couldn?t get the fenders fabricated and hung without wheels. It also was apparent that I had lost 3 weeks up front, because obviously they just never got ordered. After finally ordering the wheels, the 6-week special order slowly turned into 8 weeks. The wheels, calipers, rotors, drive side brake system were finished and PM finally shipped the parts to the bike shop. The shop owner missed the C.O.D. delivery three separate times, on 3 consecutive days. The parts were shipped back to PM because of UPS policy. I came unglued. I confronted the shop owner, making sure he understood he was not financing this project, and there was absolutely no reason for him not to be around to pay for my parts, during normal business hours, with the money I had already given him. It took another 2 weeks to get PM and UPS to get the parts delivered back to his shop. When the parts arrived, it was obvious the front wheel had been dropped. Not during shipping, the box was fine. The wheel was dropped on the assembly line at PM. The rear wheel was assembled incorrectly. PM confirmed the work order had spec?d a 1? axel, but it was assembled for a 3/4? axel. This meant the rear wheel and drive side brake system had to be returned to PM. When we asked about the front wheel, and the damage we saw, the quote from PM was ?Take it or leave it. It meets our run-out specs, otherwise we would not have shipped it.? I just spent $5000 on a damaged wheel, incorrectly built parts and spent 11 weeks waiting to get it. The front wheel was accepted under duress, but the rear wheel and brake parts went back for exchange. Another 2 weeks passed, the brake parts came back, with a 1? axel set up. A call to PM was made to find out the status of the missing wheel. PM thought they needed to build a new wheel, and said we should have it in another 6-8 weeks. We slowly explained that only the bearings needed to be replaced. We received the wheel a week later. Many people in the industry told me, this is pretty normal for a custom bike; especially PM. Parts can take forever. The other thing I found very frustrating about ordering parts was that when you got the part, it never came with the complimenting accessories. Example, when you order a set of headers for a car, you get the headers, the gaskets, the bolts, the collectors, the collector gaskets and bolts. When you order pipes for a bike, you get pipes, nothing else. When you order a headlight, you need the shell, the bulb, the lens, a mounting bracket, and a bolt for the mounting bracket. If the shop you order parts from isn?t very thorough, you are looking at multiple orders, and several weeks of waiting. I know this from experience now. A bright spot to the parts ordering was Road Rider, in San Jose, CA. James and Mike took care of me when I needed the balance of the parts for the bike and I had given up all hope on the first shop I was using. James is an ?old school? guy. He saw the newbie in me. James busted my hump every time I walked in, but I think he sees that I?m serious about this, so he?s coming around and cutting me a little slack. Mike always took the time to get me the special order stuff in a few days, not months like it had been taking before. Things were starting to look up again, but that was going to change. With the wheels, tires, forks and frame in hand, a call was made to Don at Fat Katz to schedule the fender fabrication and tank mounting. The tank was built and had been shipped to me in December. Since we had talked a few times before of, he knew I was almost ready to drop the bike off. This is when he tried letting me down, easy. ?I?m heading to Daytona for Bike Week. I?ll be back in a couple of weeks and we can schedule work on your bike then,? he told me. Great, I?d just lost an additional 3 weeks because of the wheel debacle. I?d placed my order for the frame, motor and transmission on 11/1/01 and it was now the end of February. The bike had been at a virtual stand still for most of the past 4 months due to problems caused by a shop owner and wheel manufacturer. Granted we mocked up the engine and tranny, bolted on the forks and forward controls, but we were stuck. So we waited patiently for Don to get back. Don at Fat Katz knows his stuff. In 5 minutes after we arrived, he pointed out all the wrong choices I had made for my sheet metal and why. He got me going in the right direction and we left the bike in his capable hands for a couple of weeks. When his e-mail came the first week of April telling me it was done, I couldn?t have been happier. We picked it up as soon as possible. It was perfect, better than I had hoped. One thing Don told me before he started as we toured his shop was that he tells his employees to concentrate on what they are doing. His philosophy is that one day, bondo will be labeled as a hazardous material by the State of CA. and with that in mind, the sheet metal work needs to be perfect. It sounds a bit extreme, and I doubt that will ever happen, but I can say the front fender doesn?t have a single drop of bondo applied to it. The painter of the bike was very impressed with the work at Fat Katz. If you ever need any sheet metal for your bike I highly recommend you see Don. Now that the fenders and tank were hung, it was finally time to get going. I hustled the bike down to Hollister, CA. so Corbin could build a seat. I mounted the directional signals on the rear fender and stripped the bike of all the sheet metal. The tank and fenders were dropped off at the painter, Kim Kwiatkowski. He lives next door to Brian Treanor. Brian and I go way back, over 25 years. The three of us would be the ones to fabricate, paint, wire and assemble the remaining parts of this bike. First order of business was a fake oil bag. The shocks on this Gambler run along each side of the battery, under the seat. The oil tank sits under the transmission. Brian owns a HVAC shop in Tracy, CA. Much of the fabrication took place here as well as the final application of paint and clear coat. The oil bag would hide the shocks and most of the wiring and relays used in the project. Brian made quick work of this and we turned it over to Kim to paint. While Kim painted, Brian and I worked on different things to keep the project moving forward. We fabricated a set of pipes. All of the pipes I wanted to use had clearance problems because the RSD transmission is 2-1/4? farther right than a stock transmission. This is why the transmission works without the 2? offset. The pulley is exactly where it needs to be. Second, the frame of the Gambler is much wider at the swing arm pivot supports and the Gambler swing arm is 18-1/4? wide at the axel covers. We tore into the pipe stock and bent some on the mandrel bender. We were so happy to just have something put together, we never really took a ?big picture? look at what we were building. Luckily Kim decided to take a break from the paint prep and stopped by the shop. ?What are you guys doing?? he asked. ?You don?t like it?? we replied. ?Well, you should throw that mess away, before anyone sees what you did,? was all he could say. Brian and I stepped back and took a long look, and Kim was right. We sat Kim down with a couple of beers and let him direct us until we got it right. The pipes are extruded .093-wall tubing. This is 3 times thicker than commercially available exhaust pipes. It?s a 3-step pipe. 1-3/4? – 2? – 2-1/2? set up. Since we only had a MIG welder available to us, we tacked the pipes together and let Drake Welding in Campbell, CA TIG weld the assemblies together. After they were finished at the welding shop, I put a die grinder to the welds to shape them into a 45-degree bevel. The pipes were sent out to be CermaKrome coated at Cap?s Bright Hot Coatings in Fresno. The coating has a polished aluminum color and texture. It will never blue, and never rust. The ?tail pipes? were coated in the same material, but in a flat black color at my request. Cap?s had not tried applying two colors on the same part before in the 30 years they were in business. I think they finished out very well. Everyone who sees the pipes is happy with the results. One drawback, they are the loudest pipes I have ever heard. So far, everyone who has heard the bike run says the exact same thing. Kim spent most of his free nights and weekends for about 4 weeks prepping the parts for paint. It was flawless, 2 miles deep. Kim is a perfectionist and did a great job. I can?t thank him enough. House of Kolor Black was applied to the sheet metal. Kim did minimal bondo work on the Fat Katz sheet metal. Applied several coats of at least 3 different primers, block sanded and painted several more coats of black under numerous coats of clear. Wet sanded with 2500 grit paper, buffed and polished. Pictures cannot do this paint job justice. The frame came back from Component Finishing Inc., a powder coat company in the Silicon Valley. I had done a small amount of molding and grinding on the welds in the highly visible areas. The color matched the paint perfectly. We loaded up the sheet metal in Tracy, CA and headed to San Jose where the final building would take place. I had an area of about 8?X16? in my garage to build the bike. Getting it out when we were finished, was another problem altogether. Assembly was a breeze. I had built and taken apart the bike and all of its parts at least 6 times. I knew everything fit. It took awhile longer to wire than I thought. Brian was ?volunteered? to wire, while I assembled, since I was in ?over-kill mode? when I pre-wired the hidden switches and wiring in my handlebars. I guess 14 gauge wire is a bit much for momentary switches going to relays? (Note to self, lighten up on the wire, it isn?t a house) Anyway, this used up most of the room in the center tube for hiding all the wires and caused some delays pulling other wires into place. Next bike will be different. Half way through this phase, we had enough wiring finished to start the motor, if nothing else than for moral support. I had already primed the oiling system, so we decided to crank it over. After a few failed attempts with a dead battery, the battery out of my truck, jumper cables and some head scratching, we gave it a final attempt. If I had to guess, I?d say the motor cranked only about 30 degrees before firing to life. Of course this is after everyone who wanted to stick around to hear it start, had gone home. Granted it was also 8-1/2 hours after we thought it would be ready to start. We made phone calls and held the phone to the pipes. It was a sad attempt at an apology for everyone missing the initial start up. We chased what we thought were some wiring problems the next day. It turned out to be a bad battery, no wiring problems at all. The next weekend was Memorial Day Weekend. After a false start and some minor tweaks it was road ready. There was a lot of faith placed in this bike. I was about to ride an untested bike 75 miles East away from home. It was assembled, wired, oiled, and then it hit the road directly from the gas station. While I gassed up, Brian loaded the tools, spare wire, some oil and anything else he saw, just in case we needed it. The plan was to head East, out to Tracy, CA to break in the motor and do any final adjustments when we got to his house. We spent a lot of the weekend re-tightening bolts, replacing batteries and washing the bike. Most importantly, we did some riding, the initial 250-mile break in. I feel the bike was a complete success. It had the exact look I wanted. Going against every bit of advice, I had 5? of stretch put into the backbone. I found some forward controls with 3? extensions built in. To top it off, I used drag bars with very little pull back. Everyone was convinced it was a bad combination?. ?TOO LONG, too stretched, you?ll never reach,? I was told time and time again, ?This is your first bike, you don?t know what you are doing with such radical alterations.? When it all came together, and I dropped it off the jack and set it on the ground for the very first time, a song popped into my head. The cowbell intro from War?s ?Low-ride-r? kicked in. I knew right then, it was perfect. As an added bonus, I seem to be the only person able to comfortably sit on the bike, reach the forward controls and the handlebars without a booster chair or 2X4 blocks duct taped to the pegs. This eliminates the long lines of friends wanting to ?take it for a spin.? The bike is a perfect fit for me. The fourth weekend it was on the road I had a 400-mile ride on it one day. I don?t see longer rides being any problem at all. It had almost unlimited power. (125 hp and 130 lbs. of torque at the rear wheels) Black and chrome are a classic look. It was big, burly and had an unmistakable sound from the custom built pipes. Most important for me, it blends into the crowd. Unless you know what you are looking at, it?s a black motorcycle with some chrome bolted on. No flames, no skulls, no multi-color paintjobs that beg for attention. I?m convinced the parts I have picked will last me for years of riding. I believe it?s put together with enough craftsmanship and trick parts to be featured in any magazine around, but it won?t get wasted on a trailer going from one show to the next. I plan on riding this bike with my buddies who helped me build it whenever I can. I have over 2300 miles on the bike in the first six weeks it has been running. To build a custom bike, you need a support group, someone to keep your spirits up when you haven?t seen a new part come in for 5 weeks, someone to calm you down when all you want to do is wring someone?s neck for not ordering parts in a timely matter, someone with a beer and a sandwich at just the right time and someone who didn?t mind running out to the bike shop to pick up parts when you couldn?t. I had such a support group. While building this project, I kept a spreadsheet to log my hard costs for parts, order dates, delivery dates and mileage driven to and from parts stores and other venders. Between 4 of us, we had over 5000 miles logged. It seems like a lot of miles, but they add up quick. I can?t thank everyone enough for helping out in this area. Brian and Jenny Treanor picked up the majority of the miles I didn?t log myself. Brian pushed the project along every chance he got. He made calls, pick up supplies and made his shop, tools and welding equipment available to me, 24/7. Jenny quickly got the nickname of ?Parts Chickie,? or ?Hottie Parts Girl? at the bike shops when she drove out to pick up parts. She made calls for me to save the long distance charges from my location, because she was only a few miles from the bike shop. She chased lunch for us so we never had to look up from what we were doing. She also helped with the styling of the bike, in that very subtle way of hers. This usually involved hacking, coughing or choking sounds if you mentioned a part she didn?t particularly like; ?Oh, that?s nice? was a death sentence. My wife Stacey made sure we ate on a modified schedule when everyone was working on the bike at my house. She was there to bleed the brakes at midnight and make me get some sleep when I was caught working on the bike until 5 am on repeated occasions. She also put up with my long hours away from home working on the fabrication we did at Brian?s shop, or going out of town to pick up or drop off parts for the bike. She showed great understanding when all of my focus was directed at the bike and not the chores around the house. My daughter Heather contributed in her own way. She held parts in place while I bolted them up and was always there when I needed a hand. She gave certain parts nicknames that made everyone laugh when they heard them. Example, a ?fatty tire holder? was the name given to the swing arm. Stacey, Jenny, Brian and Kim all had a lot of time and effort invested in this project. I cannot thank them enough. I hope they understand how much it has meant to me to have them so closely involve with this bike. If not, I hope they do after reading this. I could write an entire book explaining all the things that can (and most likely, will), go wrong when building a custom motorcycle, but I’d rather spend my time riding. Just remember: Watch where you spend your money, and above all–have PATIENCE. I cannot emphasize this enough. This advice was given to me by every single person that I ever spoke with, that had been through the experience themselves. Now, that I have been there, and done it myself–I wish you the best of luck. Ride well. Submitted by Rob Steffens (slightly tweaked and edited by Jenny Treanor) Bike Specifications Fat Katz sheet metal Pro-One Performance Machine ?Trespasser? chrome wheels Performance Machine brakes Avon 250 rear tire Metzler 120 front tire Carlini Drag Bars BDL Hand Controls and rear pegs Custom built pipes by owner and support crew Barnett Scorpion Billet Clutch Paint by Kim, House of Kolor, Black Powder coating by Component Finishing Inc. Misc. parts All other fabrication by Owner, Brian, Kim and Todd at Billet4U Web sites:
On the Speed?s Performance Plus Dyno at the 2002 Hollister Rally
Kim on the Standard, Brian in the back on the FatBoy and Rob on the custom
2002 Hollister Rally
Entered a ?Show and Shine? in Hollister on a whim, won Best of Show
2001 Gambler Bigg Ballz 270 soft tail frame
5? backbone stretch
35-degree rake
Total Performance Engineering 121 cubic inch motor
Bore: 4 1/8″ (4.125)
Stroke: 4 1/2″ (4.500)
Combustion Chamber Volume: 102 cc
Swept Volume: 986.77 cc
Unswept Volume: 112.16 cc
Static Compression Ratio: 9.8:1
Intake Valve Diameter: 2.00″
Exhaust Valve Diameter: 1.62″
T.P. Roller Rockers
Camshaft: Intake Duration @ .053 : 260 Degrees
Exhaust Duration @ .053 : 266 Degrees
Valve Lift .600″ Intake & Exhaust
Lobe center angle: 108 Degrees
Carburetion: 45 mm Mikuni
T.P. Cases Flywheel Assembly Cylinder & Piston Kit
Ignition System: Crane HI-4 Electronic, Breakerless, Single fire
Tappets Hydraulic
Adjustable Pushrods
Horse Power: 125hp @ 5500 rpm, depending on exhaust system & sea level
Torque: 130ft @ 3900 rpm (rear wheel)
Note: Horsepower and torque figures are SAE corrected, taken at rear wheel.
Baker Right Side Drive Transmission w/hydraulic clutch
Billet4U 3? Open Primary Belt Drive
Custom built with no offset for Gambler RSD frame
Custom motor/coil mount
Karata pulleys and belt
11? strutless rear fender
Front fender
Oversized 5.5 gallon tank, stretched 5? w/ seat pocket
?Monster? front end
3? Extended forward controls
Oil cooler
3-1/2? X 21? front
8-1/2? X 18? rear
Chrome rotors to match wheels front and rear
Chrome 4-piston front caliper
Chrome 4-piston rear caliper, drive side brake
Matching chrome rear drive pulley
Custom brake mounting using Performance Machine parts
1-1/2? tube
5? rise
Steel braided hose throughout
Corbin Hollywood Solo seat
VDO tach and speedometer, if the gauge mount ever shows up
Spyke chrome starter
H-D battery
Phantom rear seat
http://www.gamblermotorcycles.com
http://www,tpeng.com
http://www.bakerdrivetrain.com
http://www.billet4U.com
http://www.fatkatz.com
http://www.pro-one.com
http://www.beltdrives.com
http://www.performancemachine.com
http://www.corbin.com
http://www.houseofkolor.com
http://www.capsbhc.com
http://www.avontyres.com
http://www.metzeler.com
http://www.carlinidesign.com
http://www.speedsperformanceplus.com