In the first article on the most magnificent ARCH driveline, I mentioned Gard Hollinger’s motorcycle mantra, his two-wheeled mission, once he became the keeper of the ARCH. It’s one thing to build the coolest one-off custom motorcycle on the planet, if that’s even possible, but turn it into a world class production motorcycle, and now you’re talkin’ a whole new level of creative synergy, regulations, management, manufacturing, marketing, you name it.
In this chapter, we will discuss only the front end components, including this short list: handling, rake, frame geometry, front fender construction, front brakes, headlight, cowling materials, carbon fiber manufacturing, wiring, electronics, gauges, handlebars, risers, levers, throttle, front axle, axle spacer design, front wheel manufacturing, and what the hell did I forget?
Hell, we thought we were just discussing the front end, and it would be a simple, straightforward journalistic maneuver. I could write a thousand words just about the front axle planning and manufacturing. Keep in mind the strategic goals behind the magnificent ARCH. Gard wanted to build an American performance V-twin with style, wonderful handling characteristics, state-of-the art design, just the right amount of technology without getting crazy, a bike designed narrow to handle extreme traffic, and with the proper ground clearance to handle any dragon winding road. And he wanted to build the first-ever manufactured motorcycle designed to be manhandled, worked on, and serviced.
So let’s dive into the front end, and start with carbon fiber manufacturing from the Wikipedia encyclopedia:
Carbon fiber–reinforced polymer, carbon fiber–reinforced plastic or carbon fiber–reinforced thermoplastic (CFRP, CRP, CFRTP or often simply carbon fiber, or even carbon), is an extremely strong and light fiber-reinforced polymer that contains carbon fibers.
CFRPs can be expensive to produce, but are commonly used wherever high strength-to-weight ratio and rigidity are required, such as aerospace, automotive and civil engineering, sports goods and an increasing number of other consumer and technical applications.
The binding polymer is often a thermoset resin such as epoxy, but other thermoset or thermoplastic polymers, such as polyester, vinyl ester or nylon, are sometimes used. The composite may contain other fibers, such as aramid e.g. Kevlar, Twaron, aluminium, ultra-high-molecular-weight polyethylene (UHMWPE) or glass fibers, as well as carbon fiber.
The properties of the final CFRP product can also be affected by the type of additives introduced to the binding matrix (the resin). The most frequent additive is silica, but other additives such as rubber and carbon nanotubes can be used.
The material is also referred to as graphite-reinforced polymer or graphite fiber-reinforced polymer (GFRP is less common, as it clashes with glass-(fiber)-reinforced polymer). In product advertisements, it is sometimes referred to simply as graphite fiber for short.
Manufacturing Carbon fiber reinforced polymer
The primary element of CFRP is a carbon filament; this is produced from a precursor polymer such as polyacrylonitrile (PAN), rayon, or petroleum pitch. For synthetic polymers such as PAN or rayon, the precursor is first spun into filament yarns, using chemical and mechanical processes to initially align the polymer atoms in a way to enhance the final physical properties of the completed carbon fiber. Precursor compositions and mechanical processes used during spinning filament yarns may vary among manufacturers.
After drawing or spinning, the polymer filament yarns are then heated to drive off non-carbon atoms (carbonization), producing the final carbon fiber. The carbon fibers filament yarns may be further treated to improve handling qualities, then wound on to bobbins. From these fibers, a unidirectional sheet is created. These sheets are layered onto each other in a quasi-isotropic layup, e.g. 0°, +60° or -60° relative to each other
From the elementary fiber, a bidirectional woven sheet can be created, i.e., a twill with a 2/2 weave. The process by which most carbon-fiber-reinforced polymer is made varies, depending on the piece being created, the finish (outside gloss) required, and how many of this particular piece are going to be produced. In addition, the choice of matrix can have a profound effect on the properties of the finished composite.
Many carbon-fiber-reinforced polymer parts are created with a single layer of carbon fabric that is backed with fiberglass. A tool called a chopper gun is used to quickly create these composite parts. Once a thin shell is created out of carbon fiber, the chopper gun cuts rolls of fiberglass into short lengths and sprays resin at the same time, so that the fiberglass and resin are mixed on the spot.
The resin is either external mix, wherein the hardener and resin are sprayed separately, or internal mixed, which requires cleaning after every use. Manufacturing methods may include the following:
Molding
One method of producing graphite-epoxy parts is by layering sheets of carbon fiber cloth into a mold in the shape of the final product. The alignment and weave of the cloth fibers is chosen to optimize the strength and stiffness properties of the resulting material. The mold is then filled with epoxy and is heated or air-cured.
The resulting part is very corrosion-resistant, stiff, and strong for its weight. Parts used in less critical areas are manufactured by draping cloth over a mold, with epoxy either pre-impregnated into the fibers (also known as pre-preg) or “painted” over it. High-performance parts using single molds are often vacuum-bagged or autoclave-cured, because even small air bubbles in the material will reduce strength. An alternative to the autoclave method is to use internal pressure via inflatable air bladders or EPS foam inside the non-cured laid-up carbon fiber.
Vacuum bagging
For simple pieces of which relatively few copies are needed (1–2 per day), a vacuum bag can be used. A fiberglass, carbon fiber or aluminum mold is polished and waxed, and has a release agent applied before the fabric and resin are applied, and the vacuum is pulled and set aside to allow the piece to cure (harden). There are three ways to apply the resin to the fabric in a vacuum mold.
The first method is manual and called a wet layup, where the two-part resin is mixed and applied before being laid in the mold and placed in the bag. The other one is done by infusion, where the dry fabric and mold are placed inside the bag while the vacuum pulls the resin through a small tube into the bag, then through a tube with holes or something similar to evenly spread the resin throughout the fabric. Wire loom works perfectly for a tube that requires holes inside the bag. Both of these methods of applying resin require handwork to spread the resin evenly for a glossy finish with very small pinholes.
A third method of constructing composite materials is known as a dry layup. Here, the carbon fiber material is already impregnated with resin (pre-preg) and is applied to the mold in a similar fashion to adhesive film. The assembly is then placed in a vacuum to cure. The dry layup method has the least amount of resin waste and can achieve lighter constructions than wet layup. Also, because larger amounts of resin are more difficult to bleed out with wet layup methods, pre-preg parts generally have fewer pinholes. Pinhole elimination with minimal resin amounts generally requires the use of autoclave pressures to purge the residual gases out.
Compression molding
A quicker method uses a compression mold. This is a two-piece (male and female) mold usually made out of fiberglass or aluminum that is bolted together with the fabric and resin between the two. The benefit is that, once it is bolted together, it is relatively clean and can be moved around or stored without a vacuum until after curing. However, the molds require a lot of material to hold together through many uses under that pressure.
Filament winding
For difficult or convoluted shapes, a filament winder can be used to make CFRP parts by winding filaments around a mandrel or a core.—Wikipedia
Gard’s team rolled through 18 versions of the front carbon fiber fender design to reach their currently manufactured piece. They wanted it to be ultimately strong, sporty, but not a copy of any fender, mounted close to the tire, light, with a cohesive pattern of fibers, and offering a very tight, super-slick surface, with areas designed for painted accents.
Then they spent months delving into the mounting system, which started out to be a standard two-point locating boss and became a three-point, triangulated unit with two stylish billet machined aluminum pieces mounted to the 6-piston ISR mono-bloc calipers for a strong, vibration-handling mounting position.
This bike is partially rubber-mounted, but the big 124-inch S&S V-twin power source and the long chassis affords a degree of vibration excitation. It became a regular issue to contend with, and they did it by creating a double layer of carbon inside the fender. Just making this fender involved months of development. Some of these inherent vibrations will not be significant for the rider, but felt predominately by components at the far ends of the chassis front and rear.
Carbon fiber manufacturing involves a multitude of considerations, including thickness, weave, tint, design constraints, finish, external and internal components, machining, fixtures for drilled holes, and mounting considerations.
“There’s a fine line between manufacturing and design,” Gard said.
“We have 1.5 years into the design of this fender,” Ryan Boyd added, “and the process never ends.”
In order to force the fabric to be an exacting element of the product’s appearance, a wet lay-up process was initiated to pre-impregnate the carbon weave direction. Then, like any custom paint job, the fender was baked after each coat of clear, then wet sanded followed by another coat of gloss or matt clear.
Get this, no matter how many coats it takes to afford one piece a dead-on correct finish, all the other pieces for that particular bike must be cleared the same number of times for a matching finish. So each set of carbon fiber pieces for one KRGT-1 must be a matching set. Each five-piece set is numbered. They’re not messing around.
The gauge cowling went through a similar process, but also included a separate inner piece for a finished look above the dash.
The Ohlin’s upside down performance tubes are simply the best, most adjustable on the market today. Ohlins made caliper brackets for a while, but stopped. Satya Krause took it upon himself to design a set for his customers and Gard liked them and started to work with Satya on bracket development for the ARCH motorcycle. Ohlin’s ride can be adjusted for rebound modifications, compression, and preload.
I love this story about the front axle. Simple right? Not so fast, Kimosabe. This 4130 chromoly tubular front axle is centerless ground, like most fork tubes, then nickel-plated.
“So we had a sort of obsession with the design of this axle,” Ryan, the master ARCH machinist said.
“But this is indicative of our goals for serviceability,” Gard pointed out.
The reasoning behind the centerless ground manufacturing process included an easy, highly accurate fit in the bearings. The nickel plating prevents corrosion. It also fits through the axle spacers seamlessly.
The axle spacers are designed to fit together like pieces of a puzzle, so the wheel, the rotor, and the axle spacers can be installed as one piece, rolled between the fork legs, and then the axle slips through in one smooth movement, without grappling or a fight. We’ve all been there.
“It’s designed to be worked on effortlessly,” Gard said.
Now take a look at the locking and unlocking titanium axle nuts (light as a feather, special tool in owner’s box) made by the German company, Gilles Tooling. Each nut contains its own locking device, tightened after installation, then untightened easily for adjustment, and tightened again. As you know, the level of abuse axle nuts take is extreme. Gard’s design affords his customer a sharp looking piece, while avoiding all the pitfalls of standard, painted, or chromed hex fasteners.
How about the trees? They needed to be narrow for the slim design of the bike. They are not raked, but super strong, with a dirt bike touch, including pinch bolts, and machined with an artsy flair. The fork stops are integrated into the trees along with the fork lock, which is an integral component of the ignition key switch.
The ARCH team met with Zadi, an Italian manufacturer of mechanical, electromechanical, Electronic, photometric, switches and components for a large number of OEM motorcycle manufactures. And although ARCH didn’t have the production numbers, Zadi offered to supply ignition switches with a custom ARCH face. Simplicity is also a major benchmark to the ARCH design. Only one key is required to lock the ignition, the neck, and the seat.
The trees also include an angled landing for the four-piece risers. This allowed the risers to be adjusted shorter or longer to bring the bars closer or farther from the rider without changing the bars. They monkeyed with the angle, starting with 25 degrees off the surface of the top tree, but they ultimately added 15 degrees, and four different cowling iterations consumed months of design and testing to come up with the perfect cowling.
This area of the motorcycle, like the seat and the position of the rider pegs and controls, is critical to rider comfort, vision, and handling. It wasn’t just about looks. Plus where Gard is 5’10”, fortunately Ryan is 6’5”, so they worked with a variety of sizes, inseams, arm lengths, and shapes to test each design element. Of course, the owner of the famous Bikernet Shrunken FXR, Buster Cates, is also an ARCH team member, and another size test rider.
They worked with the Moto Gadget dash and formed a secondary bezel and angled the dash edges to fit the two-piece cowling comfortably, which is manufactured to use rubber isolators to prolong the life of the carbon fiber. The mounted angle of the dash surface was critical to reading the gauge. The bottom edge of the carbon fits the headlight and the air dams, which substitute as headlight mounts and headlight adjusters.
The dash also contains machined guides to allow wiring to slip behind the dash to mate with connections and components. Another relief allows the cables to reach their goals effortlessly. The risers are also poly-isolated.
Let’s shift to the bars and the Domino handlebar switch plates mated with ISR ultimate adjustable Radial Racing levers. The switch plates are water proofed and they also chose a Domino throttle housing. They rewired the switch plates and worked with Domino to give them the controls and nomenclature they needed for riding ease.
Everyone loves the CRG handlebar end mirrors and turn signals, allowing complete wide viewing from the front or the rear.
It took the team three months to work out a deal with JW Speaker for their LED headlight, which came with plans for the ARCH billet bucket that took 40 hours to machine, including the other billet front end components. They chose the 7-inch version to fit their narrow 210 mm front end spread.
They use only flexible automotive TXL wire and Deutsch connectors, like Harley. “I want it to be as bullet proof as possible,” Gard said. The overall electronics with the dash include: ignition, headlight, turn signals, and of course the S&S Electronic Fuel Injection connection.
There is only one set of special tools for this bike, two spanner wrenches, one for the swingarm and neck, and a similar, smaller version for the headlight. The tools are manufactured by the ARCH team and supplied to each owner.
The 19 by 3-inch carbon fiber front wheel from BST in South Africa is light as a feather, and the hub was configured just for ARCH and the ISR floating rotor. The ISR 320 dampened full floating rotors gained surface diameter in the circumference then lost some in the width.
The front end is raked 30 degrees with around 5 inches of trail. “I was always looking for the absolute sweet spot,” Gard said. “I want the best in stability but with smooth, agile turning ability. The prototype contained a 70-71-inch wheelbase, but they have reduced the length to 68.5 inches for ease of turning.
I’m sure I missed something, but I’m also sure you’re beginning to picture the extreme level of thought, design, creativity, and engineering extended to every last component on this machine. I’ll try to step up this process and wrap up this series with the frame, swingarm, monoshock suspension, seat, wiring harness, you name it, in the near future.
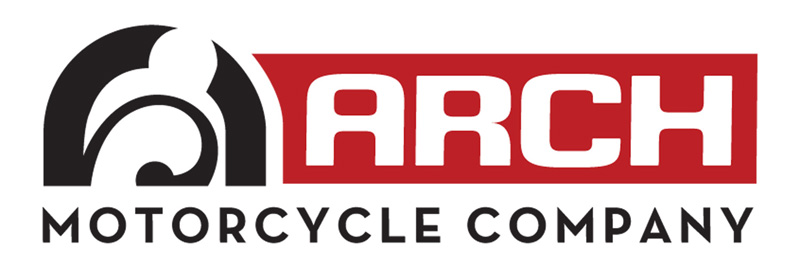