
Removing bolts with rounded heads, stripped threads, frozen, or even broken flush with the material like the one shown here, can be a real challenge. Here are ten ways to help remove problem fasteners.
One of the biggest frustrations when disassembling a vehicle for restoration, or even repair, is the dreaded seized or stripped bolt. Stuck hardware occurs when a bolt or nut gets corrosion between the threads and they won’t budge. Many times this leads to breaking the bolt off and having to drill and retap the hold or trying to remove it with a bolt extractor. We won’t even mention what happens when the drill, tap, or extractor breaks off in the same hole.
Below are the top 10 ways our friends at Eastwood have come up with to deal with getting these suckers extracted without wrecking the precious part they are in:
1. Blunt Impact/Force: This is usually our first step when attempting to loosen stubborn bolts. We always use this method before attempting to remove exhaust studs from a cylinder head. There are a few methods to accomplish this. One is to hit on the head of the bolt in the center with a chisel or punch. Another is use an impact wrench/gun and hit it a few brief times in reverse and forward. Either of these methods work on the theory of freeing the corrosion bond between the threads by vibration or impact. It works on lightly seized bolts, but isn’t a 100 percent winner every time. Keep in mind it can be combined with many of the other methods to help make the job easier.
2. Heat: If you paid attention in chemistry class you would have learned that when you heat and cool metal it expands and contracts. The way that we have used this method in the past is to heat the head/body of the bolt until it is almost red hot. By doing this the bolt expands due to the heat, and when it cools it will contract thus breaking the corrosion bond between the threads. A similar method is to heat the area around the bolt to make the hole it is threaded into actually expand and open up a little bit so that the bolt fits a bit looser and can be threaded out. Use of an impact wrench/gun helps when initially breaking it loose since the force from the hammering of the impact wrench breaks the corrosion apart as well. Use penetrants like Kroil or CRC Freeze-Off to aid in the removal process.

The expansion and contraction of the metal from the heating and cooling process can help loosen frozen fasteners.
3. Relief Cuts: This method is our “sure-fire” method for removing most stripped bolts and nuts. It isn’t as clean or civilized as the others, but it is a heck of a lot faster. With this method you will be putting two-three cuts in the bolt head or nut. The goal is to cut just enough that you are almost all the way through the head of the bolt or the nut. Then hit the cuts with a chisel and a hammer a few times, thus splitting the nut or bolt and relieving the tension on them. With nuts you can normally just split it off of the bolt, clean up the threads, and install a new nut. With bolts you can use some locking jaw pliers to grab the bolt head and turn the bolt out. Usually the relief cuts will let the pliers squeeze the head of the bolt enough that it turns out easily.

Relief cuts can often provide the room needed to “free up” a fastener that is frozen by thermal or other types of corrosion.
4. Rock The Bolt: This is another one to try early in the process, and in-conjunction with other methods. Using a ratchet and socket, slowly work the bolt or nut back and forth. Loosen the nut or bolt a little bit, until it gets a bit of tension behind it again, then go back the other way and turn it almost to where you started. Then loosen it a little bit further than last time. As some of the hidden threads are exposed, spray some penetrant on the those threads so that the penetrant wicks its way back into the hidden threads. It can be a slow process, but we’ve gotten some pretty stuck bolts out this way, just by using a little bit of patience.
5. Drill’er out: This is the same concept as the relief cuts with a couple small twists or surprises that can occur along the way. We like to use this one as one of our last ditch efforts. It may be the last resort if the bolt has broken off flush with the surface. Using a small drill bit, drill all the way through the bolt lengthwise. This uses a bit of the other methods too. It heats the bolt by drilling it, and it also makes a hollow portion in the bolt so it can contract more as you attempt to remove it. We’ve had times where just drilling the bolt will allow the frozen bolt to turn out quite easily. Other times you may have to keep stepping up your size of the drill bit until you are just a bit smaller than the diameter of the bolt. At this point you may be able to carefully chisel or break the bolt apart in the hole. Then extract the pieces and clean the threads back up with a tap set or a universal tap tool.

This broken bolt has been drilled through the center and extracted with a pair of locking jaw pliers.
6. Weld’er Up: This is one that can be used if the nut or bolt head is so severely stripped it can’t turn it with locking jaw pliers, or if the head is completely broken off the bolt. Simply take a nut and a bolt of a slightly larger size, and tack weld it to the bolt body. Once you have it tack welded, fill the nut with weld and run a bead around the base of where it meets the bolt body. This allows you to put a socket on the bolt again, as well as puts heat into the bolt that will allow it to expand and contract, breaking some of the corrosion. We prefer to use a MIG welder to do this job as it allows for a little more control than with a stick welder.

Welding a new bolt to the stud or broken bolt can provide a surface for the wrench to grip. The heat from welding the bolt onto the broken fastener can further help by breaking any corrosion bonds between the threads.
7. Air Hammer/Chisel: This combines a few of the methods mentioned, and can be used when the bolt head is stripped. Basically, using an air hammer and chisel on the bolt or nut so that the bolt loosens. We have had it work with moderate success, but it helps if the bolt or nut is an open area.
8. Bolt or screw extractor: There are many styles of extractors, some work well, but many do not. They use hardened bits that grab into the inside of the bolt or nut to remove it. Many of these require you to drill a small hole in the bolt, then thread the extractor in. Whatever you do, DO NOT break the extractor off inside the hole, or you are in for a long, horrible process. These are hardened steel parts and normal drill bits will not work on them. Specialty drill bits are required to drill through the broken extractors.
9. Pipe Wrench: This is a pretty basic way to tackle a stripped bolt, and almost everyone has a pipe wrench kicking around their shop. Tighten the pipe wrench down on the bolt or nut. As you crank on the bolt with the pipe wrench, it actually grabs harder onto the bolt head.

A pipe wrench may help with bolt heads or nuts that have been rounded to the point where a box or open-end wrench will not work.
10. Reinstall Surrounding Nut and Bolts: Sometimes a number of bolts in a area hold a part in place. Occasionally these are meant to be removed in a specific order. Make sure you check your repair manual for any installation/removal order. If no procedure exists, we like to work from the center to the outside. Reinstalling some of the bolts around the stuck bolt may take some of the force off of the stuck bolt and allow you to remove it.
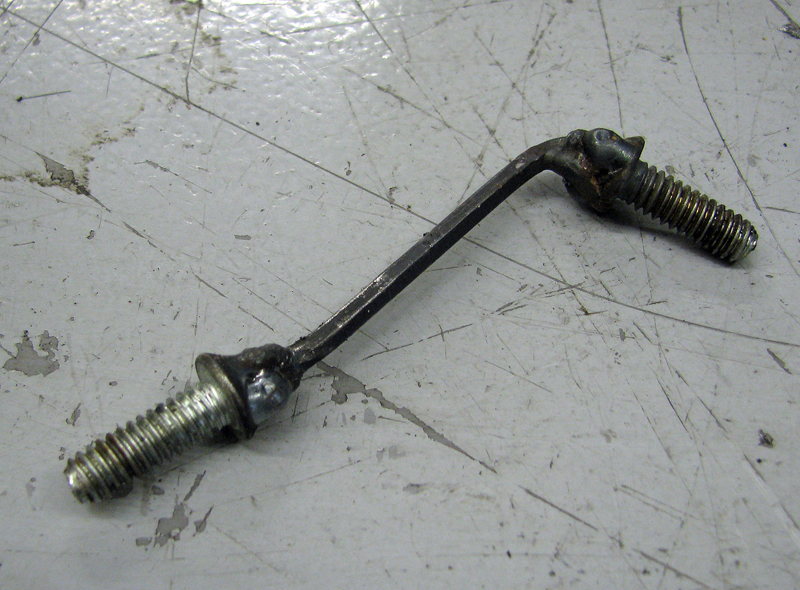