Sturgis 2000 Project Bike Crew
By Robin Technologies |
Daytec Center 17469 Lemon Street Hesperia, CA 92345 (760) 244-1591 | Downtown Harley-Davidson Russ Tom 6727 Martin Luther King Way Seattle, WA 98118 (818) 901-7037 | Bay Area Custom Cycles Ron Simms 25224 Mission Blvd. Hayward, CA 94541 |
Milwaukee Iron Randy Simpson 3000 Lenox Lynchburg, VA 24501 | Headwinds Cycle Products Joel Felty P.O. Box 661213 Arcadia, CA 91066-1213 (818) 359-8044 | Custom Chrome, Inc. See your local dealer Or Call (800) 729-3332 |
Performance Machine Ted Sands 6892 Marlin Circle LaPalma, CA 90623 (714) 523-3000 | South Bay Chrome 2041 S. Grand Ave. Santa Ana, CA 92705 (714) 434-1141 | S&S Cycle Rt. 2 Box 215 County G Viola, WI 54664 (608) 627-1467 |
Rich Products 12420 San Pablo Ave. Richmond, CA 94805 (510) 234-7547 | HiTech Products 11023 Glenoaks Blvd., Unit H Pacoima, CA 91331 (818) 834-1060 | Hannon’s Machine Shop 21050 Mission Blvd. Hayward, CA 94541 (510) 581-5315 |
Corbin 11445 Commercial Parkway Castroville, CA 95012 (408) 633-2500 | Weerd Bros. Inc 329 W. Lone Cactus, #10 Phoenix, AZ 85027 (623) 869-9477 (623) 869-9478 FAX | SJP Engineering www.sjp-engineering.nl |
Joker Machine 1078 West Kirkwall Road Azusa CA 91702 (626) 334-9371 www.jokermachine.com |
Sturgis 2000 Project Bike – Bandit II Lives
By Robin Technologies |
![]() |
Each custom motorcycle has a story. That’s one aspect of this treacherous world that sets it apart from stock bikes. Stop any rider of a chop and ask him about his bike and he’ll either punch you in the face or tell you how he started to build his bike, lost his wife and family in the process, and had to sell his home and move into a rented garage in order to complete the project. There’s a story of romance, heartbreak, hard work, and struggle behind any bike. This one is no different.
Now comes another saga, equally terrifying, equally fraught with intrigue and heart. This tale of woe begins five years ago with a project conceived with Ron Simms of Bay Area Custom Choppers. The plan was to build a bike as a tribute to the ’30s. But times changed and attitudes became harsh as the unit came together. The more we worked, the farther the project ventured from the reality of the hard-riding world. |
|
Ultimately, the bike was finished and featured in the February issue of VQ magazine. As a tribute to all who worked on it, we will feature the entire list of talents that it took to complete (…see the partial list of the crew). The sad part of the story is that the bike was ultimately unrideable. Hell, we couldn’t even trailer it to shows without damaging the chassis, and the bike was put up for sale with less than a couple of miles on it.
But we don’t like the idea of selling something that our brothers helped us build and a suggestion was made to turn it into the ultimate ground-pounding, coastal-bar-hopping bastard. We pondered the thought. We kicked around the years it took to build it in its current form, the times we went through, the love that was lost and gained, the adventures, the rides, and the wild times to come. We thought about Sturgis 2000 and what to ride. I spoke to my brothers. We had considered riding old bikes. So the gauntlet was tossed into the ring. Build a rigid flyer from the pieces of the Bandit II and keep it alive, or put dual carbs on a ’48 Panhead and take our time? Ah, but the Bikernet staff can’t proceed with anything that’s status quo, we’ve got to tear the whole enchilida to the ground and start over, and do it with a vengence. At another meeting at Harold’s dive bar in San Pedro while tossing back stout glasses of Jack, a contest was conjured up. Bikernet East (the chicken-shit Agent Zebra who couldn’t hold a job in Los Angeles and escaped to Miami with his European nymphet) against Bikernet West (Bandit himself, riding a Daytec Rigid). Since the homeless, jobless bastard of Barstow doesn’t have a dime to his name, but still writes vile stories about the upstanding members of Bikernet, we voted to build him a bike to ride to Sturgis. Bandit was already tweeking the drawing board with parts from the Bandit II, hence a contest. Bikernet East rides against Bikernet West to the Badlands and we’ll take a vote as to who has the coolest bike that makes it. Yeah that’s right – gotta make it there to be voted on. |
|
![]() Photo One |
As it turns out, we will be able to use the entire driveline from the Bandit II for the Bikernet West rigid chop, including the 98-inch S&S, Simms-built motor (photo 1) and Custom Chrome transmission. It will be placed into one of Daytec’s 4-inch stretched, wide-tire rigid. |
The Harley-Davidson narrow glide (photo 2) will stay with the original Paughco frame for the Bikernet East project and a new long front end will grace, perhaps a Weerd Brother glide, the Daytec chassis. | ![]() Photo Two |
![]() Photo Three |
Two Road Wings 60-spoke wheels have been laced and mounted to Avon tires. The front will be a 21 with a 5-inch wide 18 on the rear. And Bandit picked up a Yaffee sidemount license plate/taillight. All the brakes and controls will remain Performance Machine (photo 3). |
Harold Ponterilli will paint the reincarnated Bandit II cobalt blue with ’60s metal flake silver flames touched off with white pinstriping. The Bandit II will live to fly through the streets of Long Beach, Pedro, and L.A. And perhaps, if all goes as the Lord of Choppers dictates, across the desert into the Badlands this year.
You’ll see the entire saga unfold on bikernet, good, bad or ugly. |
|
Ride Forever, –Bandit |
Bikernet West – Electronics in a Weekend
By Robin Technologies |
![]()
Wiring is the nemesis of man, the puzzle of the best builders, the hornet’s nest of breakdown treachery. Bandit sat for hours drawing a wiring schematic for Agent Zebra’s Softail, only to rip it to shreds and toss it in the trash. He made lists while Sin Wu brewed strong coffee and baked peanut butter cookies. Bandit barked and growled for a couple of days with each run to the marine store for connectors, to the electronics store for switches, to the Custom Chrome catalog for components. The same formula fit his own West Coast entry in the Sturgis Bikernet Chop-Off. We knew as soon as he mentioned that the bike was ready to wire, that we should pack our shit and leave. We took the case of Jack fifths, the girls, and checked into the nearest fleabag motel. While we sat around the stanky pool and partied, Bandit thought about each wire, each connection, and each component. His mentor, Giggie from Compu-Fire, was his only sounding board and the only sonuvabitch big enough to snap back when Bandit growled about wire gauge or lost connectors. He wired the bike entirely with 14-guage wires. The only other sizes used were for the battery cables (stock units) and the wire that ran from the battery to the ignition switch (12-guage). Even when the sexually starved statuesque Asian roamed into the garage with cocktails, adorned in a sheer negligee, she was ordered back to the headquarters. Soon she found another plaything to keep her occupied, but that’s another story. Wiring, in the big guy’s mind, is a process of understanding what is happening with each component, where each component is located, watching for the safety of each wire, keeping the bike sanitary, and organizing each group of wires. Each wire is covered with shrink tubing, each connector supported with additional shrink tubing. Each bike had a minimum of wires carefully placed. Each bike had a minimum of components to keep the wiring process uncomplicated or enhance the reliability of the machine. No turn signals, no handlebar controls, and no micro switches. He used only millspec (military specifications) or marine quality switches. Vibration is a killer on motorcycles and much the same on boats, in addition to the moisture considerations. One additional component made wiring simple and risk free, the Custom Cycle Engineering starter mounted mechanical switch. (Check the article here in the Garage.) This unit eliminated the starter button, the starter relay, and all the associated wires. You must make sure you will have access to the switch, which is mounted directly on the starter, under the oil bag, (Photo 2) which can easily be interfered with by the position of the exhaust pipes.
![]() Photo 2
The concept is that you physically push the solenoid into contact with the starter gears and electrically engage the starter. We chose a Compu-Fire starter from Custom Chrome to kick this 98-inch monster to life. The key thing on fucking up starter motor installation is over tightening the brass lug wire fitting. It may turn the connection on the inside of the starter and ruin the contacts. Compu-Fire has designed a new line of starters which feature 6:1 gear reduction (Photo 3) and a 6-pole permanent magnet field to eliminate starter stall-out.
![]() Photo 3
These units deliver maximum cranking torque without overloading the battery. They also eliminate starting problems on fuel injected bikes. Only two switches were used and one 30-amp H-D (common at any electronic or auto parts store) circuit breaker. One on-off marine toggle for the ignition, which energized the Compu-Fire single-fire ignition system, the hydraulic brake switch, and the taillight. Since all the sweet parts like handlebar controls, foot controls, mirror, and taillight were Joker Machine components, he was in luck. Joker works the brake light switch into the body of forward controls, which eliminated the bulky hydraulic switch, the junction, and a two-piece rear brake line. Another wire went to the other switch, an on-off-on switch for the headlight (high/low beam). Two wires were run from it to the headlight. Daytec does a beautiful job of running guide tubes in the frame to hide the wires. Initially, if you chose to do so when ordering a Daytec frame, you can have two inserts welded to the frame seat post rail for electric box mounting. We ordered the certs for this frame but decided that with the simplified wiring program we could stuff switches and all the wires into the structure of the top motor mount. This was Giggie’s suggestion and Bandit readily agreed (a miracle). With careful measurements the switch holes were drilled with several bits until a 1/2-inch hole for each switch was attained. The only guide hole that the frame was missing was one for the headlight wires, but two wires were run through shrink tubing to the headlight and through a 5/16 hole in the motor mount. One wire was run from one side of the ignition switch to the circuit breaker, another, the 12-guage wire ran to the battery. From the circuit breaker a wire ran to the taillight down another guide hole along with the brake switch wire. From the brake switch another wire ran to the taillight, brake element. We also used a Compu-Fire regulator, which mounted to the front of the motor. One wire ran from the regulator back to the hot lead on the Compu-Fire starter motor. Bandit used the excess 12-guage wire to run from the battery to the hot side of the ignition switch. Giggie recommends that you use crimpers designed for Duetch connectors for a solid, vibration-handling connection. Bandit used water resistant connectors from a West Marine store. After some 20 hours in the garage, Bandit was finally lured into a well warmed King size bed by Sin Wu and her girlfriend Coral as the sun came up, but at that point the bike was ready to be fired to life. The question was, could Bandit be fired to life? –Wrench
|
Bikernet West – The Blue Bomb Explodes
By Robin Technologies |
In a mad rush to build and break-in a monster Simms built S&S motor rigid before the long haul to Sturgis, Bandit makes an abrupt move. At the final hour he decided to take the frame to a local powder coater in Orange County who is capable of layering on a two or three stage powder coating process. After much deliberation with the entire staff, the decision to attempt a match between the frame and sheet metal was made. Nuutboy pointed out that the powder coated frame would be more resilient to wear and tear. Snake, in a rare lucid moment, noted that we wouldn’t be able to cover Bandit’s crappy welds with bondo, because powder coating is baked at such a high temperature that it melts the bondo. Overnight shipping would have been less than $100 to truck the delicate metal parts to Sacramento for Harold Pontarelli to paint. In contrast if we had the frame powder coated locally, we could have it back in three days and be working on the bike. On top of the concern for the various components being shipped, damaged, lost or dented- which would really set things back- there was the overall concern of time. We needed to be building a bike. Some of the Bikernet gang like Renegade, who was pissed that we weren’t working on his bike (he won’t ever let any of our mitts near it), Snake, Nuutboy, and my most informed self, huddled around a large bottle of Jack and a small bonfire in the junkyard rubble behind the Bikernet World Headquarters in San Pedro, California to take a vote. Bandit was somewhere inside the luxurious offices chasing a new female recruit, an oriental girl, whom he had failed to introduce to the rest of us. He was building a deep-seated resentment amongst the staff. “I say, fuck that bastard, let’s burn his frame,” Renegade said taking a hit on the freshly opened bottle of Tennessee champaign. “You say that every day,” Snake mumbled filling his large rusting flask with the bottle while guzzling the last remaining can of Bud from his 12 pack. No one else drinks beer. “We’re supposed to be deciding whether to ship or powder coat,” Nuutboy said standing on the edge of the fire holding a wad of tools in each hand. He doesn’t drink, but smokes joints incessantly and fidgets constantly. “We’re running out of time.” The evening went south from there. More riders showed up, Japanese Jay from the antique bike shop, 34th Station, came by. Chris from Hill Products wandered in and filled his boot flask, put in his two-cents worth and moved on. Nuutboy and I pondered the question until we heard the giggling stop from inside the Headquarters and the large thump of boots against rickety floors. Bandit appeared bleary eyed but content and placed his vote. If we could get a sample of the paint color on a separate rod we could ship it to Harold for a paint match. We went to work. We delivered the frame to Primo Powder Coating in Huntington Beach, California (714) 596-4242. They had a sample of the metallic blue we were after, waiting for us. We immediately took that sample to a mail box joint and shipped it overnight. The tank and fenders were carefully boxed up and shipped to Harold via UPS second day air. Then we delivered the chrome to Orange County Plating (714) 532-4610 where they immediately photograph the items and enter them into a computer. In four days we had the frame and chrome back and were in the process of building the bike. Harold moved on the paint quickly, but even with a simple flame job on the table, a couple of days was spent at the body shop, then paint prep and primer, then undercoats of silver base were followed by a matching blue candy with a hint of pearl, then drying time before the graphics could be laid out. Two weeks have slipped past, but the progress with the frame in hand is considerable. The engine and tranny are bolted in. The Weerd brothers front end is in place. The wheels and P.M. brakes are in place along with the Samson exhaust system. Wiring will begin this weekend. Then with the BDL 3-inch primary belt in place we will haul the bike to Mikuni for a Carb and go for a ride. Here’s a sample of the paint from Vacaville, California near Sacramento.
![]() –Wrench
|
Bikernet East – An Eagle in the Garage
By Robin Technologies |
Custom Chrome introduces the world’s first rocket-powered Zebra. The power plant of the Great Zebra Northern Steamer for Bikernet Chop-Off 2000 by Special Agent Zebra 05.22.00. The Great Zebra Northern Steamer is to be a biker’s bike. No fantasyland Hollywood bullshit in the way of $80,000 paint jobs or diamond encrusted spokes, no chop-shop hoopla, the Zebra Steamer is going to the root of American bike building, tight, right, fast, and reliable. It’s being built by the rider, with help from Bandit, Wrench, the Chinaman and the torque kings at Casa El Horsepower, in an anonymous garage in San Pedro, California.
These suckers come complete with carb and ignition system. It is literally bolt-in ready when it comes off the truck with any OEM or custom frame that will hold an Evolution. The RevTechs aren’t a cheap amalgamation of aftermarket pieces. The entire system is designed on a CAD (computer assisted design) system, just like the ones used at the big automotive plants. This means you get the latest in engine technology available. Every component is created from new tooling techniques in a state-of-the-art ISO manufacturing plant. But high-tech engineering manufacturing equipment and techniques aren’t any good without great concepts to use them on. Again, Custom Chrome has put its money where its product is and created some revolutionary new thinking in big twins. The RevTech engines use no head or base gaskets. Why? Because they leak and they blow. Instead, CCI uses ultra-high temperature O-rings, which are hard as hell itself. Ignition is computer controlled. They come in 88 and 100-inch displacement. The 88s have 4 1/4 flywheel stroke with a 3 5.8 bore. The 100s boast 4 3/8 stroke and 3 13/16-inch bore. The cases are cut from 356T6 cast aluminum. Every stress point contains added materials for increased strength (read: you don’t walk across the Mojave Desert in August). They also have removable press-in/bolt-in bearing inserts on both the left and right sides of the cases and removable bottom sump-plate permits internal inspection. RevTech’s cylinders have increased fin surface in high-heat areas, for advanced cooling (Fourth of July runs, anyone who rides in New Orleans on the I-10 during rush hour or Miami before or after Christmas day). Steel liners are Perma-locked into the outer aluminum castings. The pistons are cast for controlled expansion, which reduces engine noise and wear.
Special Agent Zebra |

|
Bikernet East Installment 5
By Robin Technologies |
629 E. Sunrise Blvd
Ft. Lauderdale, Fl 33304
“I’m thinking of having a painter do up the bottom of the bike with some radical paint design because the fucker is so damned fast with this S&S 113 that it brings the front end off the ground in second gear. I’m not kidding. I had to switch it back to a chain from a belt, because the belt would just sit there and whizzzz, spin like crap and fry.”
“The customer is completely nuts,” Eddie Trotta continues, as he closely examines a gorgeous, low-slung chopper which he hand built for a local Fort Lauderdale, Florida client. “The fuckin’ guy, he walks in here, I let him take a ride, he comes flying back in and says, ‘Jesus Christ! That’s the best running motorcycle I’ve ever ridden! How much?!’” “I tell him ‘$40,000, he writes a check and then, then the crazy motherfucker spends the next half an hour, eeeeeeeeeeeeowww! ZZZZZoooooommmm! Back and forth, roaring up and down the street out front like he wants to kill himself on this fast damned scoot. We’re all in here watching with our jaws on the floor and this guy’s outside going completely nuts. Finally, he comes back in grinning like a lunatic, the thing’s smoking like crazy, the back tire’s fried and he laughs and says, ‘I gotta let you guys know, I ride pretty hard. This thing has to be bullet proof.’ I asked, ‘Can I give you your money back right now?’ And he says, ‘Hell no! I love this thing! It’s tough as shit!’” Eddie lets out a casual laugh as he pulls a massive hunk of turf out from under the bike. “What’s this?” he asks incredulously looking at what appears to be golf course sod wedged under the bike. “What the hell? I think he’s taking this thing off road! That crazy bastard. He came in here the other day with a tiny crack in the back fender. Turns out he JUMPED the sonofabitch with his old lady, some broad who’s huge and he actually cracked this fender. Feel how thick this thing is! That’s the heaviest fender made in the business. I gotta get this guy a slower bike or a lighter old lady. Or a shorter ramp. He’s totally nuts.” I feel the metal and it is a really heavy fender, a beauty. “He jumped it?” I ask, thinking I must have heard wrong. “Yes! I’ve fixed this tiny running light down here behind the pipes at least 15 times. That’s a $100 light. I’m going broke off this one light!” Eddie says laughing, examining the light closely. “I don’t know how the hell he’s doing it, probably has flames shooting out of the pipes and he’s melting it or something, shit I don’t know. The guy owns 53 businesses, he’s my roughest riding customer. Totally nuts. I fix it all for him for free. I stand behind my choppers. Once in a while he puts up a new gutter at my house. It evens out.”
Good customer service? You be the judge, but by my standards, that’s going above and beyond. Stands to reason. If you want a gorgeous custom chopper and I mean gorgeous by the most rigorous show standards, a no-nonsense, built to ride, powered by beat-the-motherloving-crap-out-of-it equipment like RevTech engines and Baker trannies, Eddie Trotta at Thunder Cycle Designs is the man. Eddie’s is one of the nation’s premier custom motorcycle builders, specializing in one-of-a-kind choppers. He started building in the 70’s and opened his shop, Thunder Cycle Designs in Fort Lauderdale, Florida in 1990. Currently he has around 50 custom bikes for sale on his showroom floor at any one time and there is nothing that he can’t build for a serious customer.
“My bikes average about $40,000,” Eddie tells me as he cranks up a gorgeous new chopper with a stunning paint job. The big S&S 113 rumbles to life. “Sit on it, tell me what you think of this shape.” I gladly get on and the long, elegant monster fits like a high-speed glove. This is what it must feel like for a fighter pilot to slip into the seat of a well-oiled F-16, I think. “I try not to price my motorcycles into dumbass numbers,” Eddie says.
“Which some other builders do. My goal is to make an incredible, unique chopper for my customer and sell it to them at a reasonable profit and have them ride the crap out of it. These bikes aren’t built for trailers. I build them to ride. Sure, they look pretty, but they run like motherfuckers. I have some customers who trailer from show to show and that’s okay, but I still build them with the components to ride and ride hard. These are motorcycles, not art. They might look like art, but first and foremost, they’re hardcore machines.” “And now we come to Zebra chopper,” Eddie says, winking. We walk up to my new chop, the Great Northern Steamer, my entry into the fierce Bikernet.com Chop-Off competition for Sturgis 2000. This will be the horse, which I try to beat the mighty Bandit with, out on the West Coast. Taking on the Godfather of motorcycling isn’t an easy task which is why I’ve called in the master, Eddie. “I’ve taken the fender off and re-cut it. It was okay the way you had it, but we made it better, hugs the tire tighter. Eddie Meeks, at Hardly Civilized is painting in the artwork (5437-A Church St., Greensboro, NC 27445, 336.545.9064) now,” Trotta says. Eddie Meeks, one of the top painters around, was kind enough to light up his spray gun and blast off a paint job in just under a week, including curing and shipping time. “I put on a different kickstand, rear passenger pegs, we’re going to raise the bike a bit as well. I might change out these brakes on front, put on two small calipers instead of the one big one. Not sure yet. We’ve taken off the back tire, checked all the alignments, double-checked all the rear end, it looks good. This is the seat. It’s a custom job, made from a nice tan leather that fits perfectly and matches your paint.” Eddie shows me my new seat, a hand built beauty, which ends in a fine dovetail over the bobbed fender where the lass will perch. “You’ve got a great tranny with this Baker six-speed,” Eddie continues, “which is what I use on my bikes. These RevTech 88’s are beauties, too. They’re strong and smooth. I’ve had no problems with either the Bakers or the RevTechs, and you know how my customers ride,” Eddie says, rolling his eyes. “You don’t plan to jump the motorcycle, do you?” “Not voluntarily,” I tell him. “But of course, it is Bikernet, so it would be foolish to rule out such things entirely.” Eddie chuckles and shrugs. “That’s true,” he says, “I’ve known Bandit for a long time and I know better than to put anything past that damned outlaw.” Look for more tech tips coming down from Eddie Trotta and his boys at Thunder Cycle Designs as they finalize the Zebra Great Northern Steamer and the break-in process begins. Eddie Trotta’s Thunder Cycle Designs is located in Fort Lauderdale, Florida. Their web address where you can see Eddie’s entire line of incredible choppers and his full catalog of custom parts (if you don’t see it, call, he can make it), is http://www.thundercycle.com. You can call Thunder Cycle at 954-763-2100. Or, visit Eddie and his metal magicians by taking I-95 to Fort Lauderdale, to Sunrise Blvd, exit, head east over the tracks to 629 E. Sunrise Blvd, which is on the north side of the street, you can’t miss it and you don’t want to. It’s well worth the trip.
Thanks to Eddie Trotta and his boys at Thunder Cycle Designs, RevTech, Burt Baker at Baker Transmissions, Ken Gold at Gold Rush, and Eddie Meeks at Hardly Civilized. Couldn’t do it without you. Bikernet recommends all these businessmen for your biker needs. They’re tried and true. Gear up, grease up and gas up, all you bros out there. The big run is fast approaching. We’ll see you in Sturgis. Ride hard, |
Bikernet West Bogged Down In Pheonix
By Robin Technologies |
I knew it! The sonuvabitch couldn’t make it to the Badlands and back on that piece of shit. I knew it! The way Bandit mounted that tank was fucked from the beginning.
![]() I told him. Nuutboy told him. Harold Pontarelli told him. Shit, his 78-year-old mother told him. Did the big bastard listen? Nooo. So it jumped off the frame in Aspen, Colo., and landed in his lap.
![]() Yeah, they welded it up in Aspen with the help of Randy Aron from Cycle Visions in San Diego, and he limped into Sturgis, rode around the Badlands for the week and then the scoot was kidnapped from him by someone who knows what the fuck he’s doing, namely Paul Yaffe from Paul Yaffe Originals in Phoenix. Paul is working with Kyle of Independent Tanks, who hand makes steel tanks from heavy 16-gauge material. It’s about time someone grabbed that bike before it exploded into flames and scorched the ornery sonuvabitch.
![]() So we sent that fly-bitten claybrain to Phoenix for a welding lesson and instructions on how to properly mount a gas tank. If he wasn’t such a hasty-witted old fool, he would have put the bike together right the first time.
![]() Here are shots of the existing piece of shit with the new tanks recommended by Paul, who builds some of the most innovative bikes on the planet.
![]()
![]() Paul’s philosophy is to manufacture enough custom components to allow his customers to build something without doing a piece-meal job. “Instead of buying fenders from me that don’t fit the other guys’ frame properly and then mount a gas tank from so and so, and nothing fits properly, I want to give the customer half a chance to build a world-class custom on his own.” Paul’s positioning himself, unlike Bandit, to afford customers with frames, plus the fenders, tanks and billet components to match. Paul began his operation building LED taillight products. Unlike the slob who runs this joint, Paul is a young man of vast energy and talent who could not contain himself building bikes with existing components. He began building his own fenders, air cleaners, frames, etc. The young upstart with the flaming red hair does share one notion with Bandit: “If you’re going to build a new full-custom for a customer, I want the bike to be a reliable runner, of the newest technology, or how can you call it a new bike?” So all of Paul’s bikes are built with Harley-Davidson Twin Cam drive lines. “I use as much Harley stuff as possible,” Paul said. “Plus the factory is going crazy building more new accessories all the time. The selection is growing by leaps and bounds.” Damn, if I told that lunkhead Bandit once, I told him a thousand times, it’s time to move away from the Evolution shit into the real world of Twin Cams. But that motley-minded minnow is still out in the garage trying to put two Mikuni’s carbs on his ’48 Panhead. If you want to check true customs, built to ride, check Paul’s site http://www.paulyaffeorginals.com Finally, after much consternation, Bandit succumbed to one of Paul’s buddies, Kyle at Independent Gas Tanks. These are new, contoured tanks and here’s how ya do it right.
![]() Kyle has been building his own line of steel gas tanks for two years. Prior to ’98, he built tanks for Roger Borget for three years and before that he built Porsche 911 race cars. He won’t get near aluminum. “Not with the engine sizes that are bouncing around in these frames,” Kyle said. None of his creations are Mig welded, either. “I only Tig weld my tanks. I’m glad to work with builders and make suggestions.
![]() I’ve hand-built over 1,000 tanks for Harleys, and if told the brand frame, the stretch and rake, I usually know which tank works the best. I can go with one of my six to eight standard styles, or I can design something out of this world. I can make a bike blend into the crowd or stand out anywhere.” Kyle’s tanks come with mounting straps. Don’t just weld ’em on and go, though. “Depending on how the tank is designed to mount will depend on if the existing tabs will work immediately or need to be modified,” Paul said. In this case, he created some spacers to allow the tank to set on the frame perfectly to capture the look the big bastard wanted, then he cut the tabs and tacked them to the frame. Next he removed the tank and solid tacked the tabs. He put the tank back on and made sure everything was in place. These tanks are handmade and not manufactured with a jig, so no two tanks are alike.
![]() The tabs were finish welded and the tanks shipped to Harold Pontarelli for repaint. Paul welds everything with Tig because the Argon gas shield makes for a more controlled burn. It gives him better penetration and a less brittle weld than a Mig. Kyle had one other recommendation. He often gets calls from brothers requesting tanks after they have taken their frame to the powdercoater. Don’t do that. Make sure all the sheet metal is prepped and assembled before any finish work is undertaken. In fact, many builders ride scoots without paint for a hundred miles or so before tearing down for paint. Saves the headache, and makes for a much tighter custom.
![]() Of course the whole operation must have a photo finish. Two days before the Love Ride, the tank is floating into town via Harold and eight H-D Performance troopers. The bike is rumbling in on the back of Paul Yaffe’s custom trailer. The two will meet with Bandit in Woodland Hills for the install and road test for the parties to come that weekend. He doesn’t deserve this scoot. It should be mine. –Renegade
|
|
Bikernet West – Amazing Progress
By Robin Technologies |
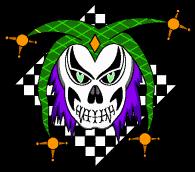
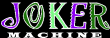
Late into the evening, Bandit, Nuut Boy, and my wonderfully-knowledgeable- self hammer, weld, bolt, space, and tear our beards out moving forward on Bandit’s rigid. The Weerd Bros front end is in place with the Roadwings 21-inch, 40-spoke wheel. The rear is a 180-18, both with Avon tires. The frame is stretched 6 inches up and 2 out. The trees on the clean front end are raked 6 degrees (photo 1). The S&S 98-inch stroker is bolted in place as is the 5-speed Sputhe trans.
We set the engine and tranny in place and then found a scrap inner primary to line everything up. With the stock 32-tooth pulley on the tranny, we put a 70-tooth narrow belt pulley from Harley on the back with a 134-tooth belt. It was too long. We tried to get a hold of the frame manufacturer for some guidance, but they wouldn’t get back to us, so we had to wing it. We had another option. Run a Harley Thunderstar 65-tooth wide pulley for taller gearing for the trip. We picked up a 130-tooth belt and it fit like a glove. The pulley on the wheel also felt good and afforded us plenty of tire clearance with the offset frame. With the rear wheel in the center of the adjustment axle slot and the tire centered in the frame, it was time to fit the rear fender. The rear fender was a Milwaukee Iron job, which took some time to mount up. First we centered the tire in the frame. Ignore the offset rear leg. Center it in the frame using the cross member behind the seat as a guide. We centered it then strapped chunks of 3/4-inch board (photo2) to the tire with green paint masking (low tack) tape.
Then we slipped the fender in place after the rear belt was adjusted. Again, make sure the fender is centered over the tire. The fender didn’t contour the tire completely, so you must decide what area you want contoured. We decided on the top, most visible area. Make sure the slot for the belt rides a good two inches above the belt and at least a 1/4-inch from the inside.
Then the Samson exhaust was removed from the box. They don’t build exhaust for rigids so natch the Dyna exhaust didn’t fit, since with rubbermount frames the engine sets higher in the chassis. They were also over 10 inches different in length. For performance we cut them to a more equal length (photo 4), about 27 inches.
We also ordered baffles and we cut them (guessing) to give the 2 1/4-inch exhaust some back pressure. Then we mounted them. The front pipe was way too close to the deck, so we cut 2 inches out of it and gas welded the pipe back together. During this process we were able to bring the pipe into closer alignment with the rear exhaust. None of the brackets would work so the madman with a torch went to work building brackets. The seat was also a trick. Bandit purchased an old cop solo with the plunger t-bar from 34th Station, a bike restoration shop on Pacific. After much contemplation he decided that he had to mount springs under the seat for something of a ride, but springs were a problem. He had some success with a set of valve springs on his dicey Knucklehead, “Made all the difference in the world,” Bandit said while pondering the ride. But the old Bates tapered 2- or 3-inch springs generally bottom out under any load. Then a bolt of lightening hit while attending the Harley-Davidson new model presentation to the motorcycling press. In addition to all the new models for 2001, they were showing off their new police bike, which had a sprung seat. Bandit drew the 4-inch crescent wrench he’s been carrying in his pocket for the last 32 years and began to take the springs off the new 2001 model. Seven factory executives struggled to pull him off the new demo bike. “But wait, guys. I just want to borrow ’em,” he screamed, pulling on his crescent wrench. Back at the top-secret massive 50-square-foot Bikernet testing facility, the gang was taking more measurements. It was determined that if he could narrow the seat one inch, all would fit, and the seat spring studs would line up with the center of the frame tubes. A call was made to California Harley-Davidson to order the springs, ASAP. Nuut Boy went to work stripping the seat to just the pan. With a die-grinder he cut a 1-inch strip out of the center of the pan then laid enough brazing rod into the jagged gap to sink a battleship. We decided not to use the old t-bar and with some standard 3/8-inch round stock, fashioned a triangle brace under the seat for support.
|
Bikernet West – Mikuni Carburators to the Rescue
By Robin Technologies |
With Sturgis 2000 looming over Bandit’shead we’ve been firing away at the getting the job done. Bikernet Eastmachine was well out in front in the competition when we wheeled the Agent’slow slung Softail onto a slick Gold Rush semi and said goodbye as the rig,packed with Ultra machines, Big Dogs and customs from the west coast, headedeast. Eddie Trotta from Thunder Design was more than happy to have thebike unpacked in his shop in Fort Lauderdale, so he could point a fingerat Bandit’s creation for Agent Zebra and bust out laughing, “You expectto ride that to Sturgis?” he said rolling on the floor of his shop. Weweren’t discouraged and neither was Bandit as we strapped the road wingswheels, the Weerd Brothers Front end on the Daytec rigid and went to work.
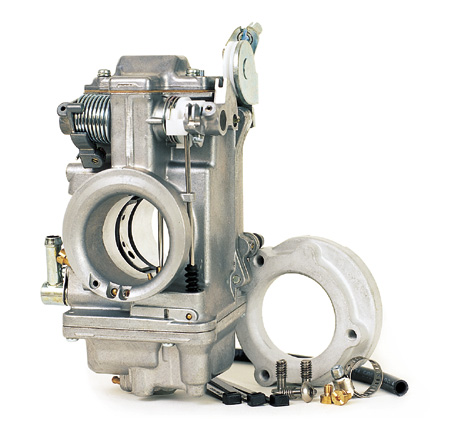
This was no ordinary installation. First,time was a factor, second it’s no normal, stock carburetor swap. The 98-inchS&S motor offered taller cylinders and improper intake manifold fitment.The stock Super E S&S manifold was too big for the 42 mm polished MikuniCarburetor. Stock manifolds shove the carb out too far and aren’t wideenough for the tall S&S cylinders so a quick call was made to JamesSimonelli of S&S who rushed the correct manifold to Mikuni. Lee alsowanted to explore an American Iron Horse manifold available for their customswhich pull the carb in closer to the engine and “L.T.” or James Littleof American Iron Horse moved equally fast and the parts were in hand inone day. The next hurtle: The cables. A call went out to Xavier at BarnettCables who turned about a set of Mikuni compatible cables which are setup the same as stock H-D cables, but cut to Bryan’s specifications forthe job. They also arrived in time.
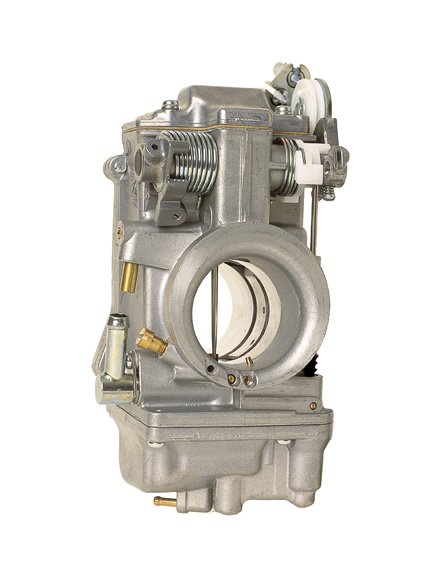
Bryan pointed out an adjustment on theleft side of the carb as you face it, a main jet air adjustment. He toldme to inform Bandit to turn it out a half turn in Denver for more compatiblerunning in altitudes. The bike immediately fired to life for the firsttime. Two weeks to go.
Bikernet West – Belt Drives Limited Open Belt Installation
By Robin Technologies |
![]() Here’s the deal. With less than two weeks to go I’m praying, laughin’, grinning and scrambling. The paint finally arrived from Harold Pontarelli of H-D Performance of Vacaville, California, and the dark haired beauty wanted to be at the shed when I opened it. I paced the floor waiting for her alabaster legs to bring her quiet self up the sagging stairs and into the world headquarters of bikernet.com. We took the carefully packed boxes to the basement where we were attacked by the foam peanuts assigned to protect the polished finish. First it was slabs of pressed foam, then thousands of bouncing peanuts, yards of plastic wrap, then plastic bags and bubble wrap until we finally reached the bright candy blue finish with cream flames, silver inserts, for dimension, and gray pinstriping. Unbelievable! The perfect match for the bike. I’m jazzed. But let’s explain some of the praying that’s going one. BDL Belt drives, especially this one in particular, are simple to install. Incredibly simple, but there’s a caveat, a loophole or a tiny chink in the armor. It’s called alignment and spacing. Hot Rod Bikes recently published a full-on BDL installation, and I read it several times. It never made any sense to my simple mind, yet it was full of very precise instructions. The key is how you install and space the motor and tranny. It turns out that your inner primary, or in our case, the motor plate, is the best alignment tool you have. According to Frank Kaisler, the editor, you leave the engine and tranny loose, bolt the inner primary or belt plate to the engine then pull the tranny into place and bolt it up tight and start checking under the engine and tranny for gaps with feeler gauges. In the article it showed big Frank filling the gaps with spacers as thin as .010. Damn, that’s getting touchy. Recently a Bikernet reader, Breeze, sent me the following on BDL installation suggestions and I added my two cents worth to his experience: “When I was installing the BDL 3-inch open kit (the one that comes with the motor plate) I was having a bitch of a time gettin’ the belt on. So, I called and got to talk to their tech support.”
“Anyway Buddy Bob, tech master, says, “Oooh, just file the pulley splines (Photo 1) it will go right on.” Filing splines applies to S&S motors with slightly larger main shafts, like .001 so take your time and it will work out fine. If you don’t and force the pulley on, you may have a serious problem taking it off. I used a handmade puller from the bottom of the tool box to get the pulley back off.” “As far as alignment I use the good ol’ straight edge across the pulleys method. Check at top, center, and bottom, to get things straight on both axis. I do this without the belt and space the front pulley out so you can use feeler gauges to compare the front to back space between the rear pulley and the straight edge. Of course the ultimate alignment test is to run it and see how the belt is tracking. It should not wander and should track on the front pulleys outer flange and center on the rear pulley.” “I think they have a great design there, it is one of the smoothes clutches I’ve run, but you need to check tolerances for reliable running. Be sure to follow the instructions on the clutch install, the Locktite they tell you to use on the basket splines is important for the basket to seat properly.” “They call me the Breeze, I keep rolling down the road!” Well, that’s the Breeze’s story. In fact Breeze has given me a couple more things to check. I put one of the polished rotor covers on, which threw my pulley alignment out of whack, so I had to take it back off. I’d rather have reliability that flash. Before you attempt to install the belt drive check these alignment areas. Bolt your rear motor mount bolts down tight, without the top one in place. With feeler gauges check the front motor mount. Space the front ones if there is any gap. Now bolt down the tranny plate and the tranny except for the single bolt on the right side (Photo 2.)
Check the clearance to the final stud from the frame and correct the spacing. Now with everything loosened up install the inner primary. The BDL system comes with a very heavy duty clutch bearing, so the the stock bearing race must be removed. Fortunately I had a JIMS puller for just that application.
That and a couple of crescent wrenches and the puppy was gone, and the new bearing installed. Slide the clutch and front pulley on, and make one more alignment check as you rotate the motor (Photo 4).
Grease the starter shaft and bolt in the starter pinion gear. Next install the clutch pack as per the manual. You can now install the belt guard and adjust the clutch. I’m carrying another set of clutch studs and springs, in case the clutch begins to slip. I’m hauling along another belt for safety, also. Couple of years ago, I ate one (it wasn’t a BDL, though). Seems like a lot of work, but actually this is one of the cleanest, simplest systems out there, and once you have it dialed in, you can put it on and take it off in minutes. Damn, I running out of time. Gotta git to the wiring. Rock and roll. –Bandit
|