Latest Articles
THE MASSIVE BIKERNET WEEKLY NEWS for July 3rd, 2025
Hey, Suddenly there’s a ton of action happening in Sturgis for the 85th. This was ...
WIN BY HARLEY-DAVIDSON RACERS JAKE LEWIS & CORY WEST
HARLEY-DAVIDSON® PAN AMERICA® ST RACERS JAKE LEWIS AND CORY WEST WIN IN MISSION SUPER HOOLIGAN ...
1939 Harley-Davidson Knucklehead is headed to someone’s garage
ONLY TWO DAYS LEFT CLICK TO WIN https://store.wheelsthroughtime.com/win-this-bike The 2025 WTT Raffle Grand Prize is ...
CLUB FIGHTS 1976
I just watched the George Clooney and Evan McGregor film, “Men who Stare at Goats.” ...
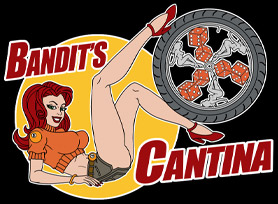
New in the Cantina
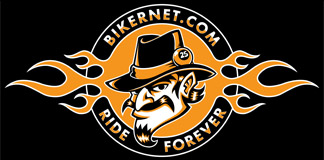
Weekly News
THE BROS BIKERNET WEEKLY NEWS for September 1, 2022
Hey,What can I say, we have tons of inspirational quotes in the news this week. ...
COOL BIKERNET WEEKLY NEWS for August 25th 2022
Hey, The Rally is a couple of weeks behind us, and hopefully I will launch my ...
POST RALLY BLUES BIKERNET WEEKLY NEWS for August 18th, 2022
Hey,The rally came and went in the blink of an eye. I’m trying to write ...
RALLY WINDING DOWN BIKERNET WEEKLY NEWS for August 11th, 2022
Hey,Thursday will be nuts. Not sure if the news will be finished on Thursday or ...
Tech Articles
2010 Horse Subscription Sweepstakes Sponsored by Bikernet.com, Part 2
"Chance of a lifetime," I said to a brother recently. It's my reoccurring adage for ...
Sturgis ’99 Project Bike
This is original assembly Excelsior-Henderson number 103. And we're proud to bring you an original, ...
Tail Gunner Report on Shocks
Well it's that time again, this month we attempt to stop my poor old Softail ...
Timbo’s ’64FL Panhead Part 3, Engine
After the engine was removed from the frame, I mounted it on an engine stand ...
Bike Features
Chopper Challenge Caveman Bike Comes to Bikernet
Hollywood is a strange place. Nothing seems real. You could run into a girl dressed ...
Tough Bikes From RS Performance Coatings
This story is about a Menlo Park, California, industrial coating shop that started three generations ...
Birth of an Evilution
I’ve often heard, and truly believe, that building your own motorcycle from the ground up ...
Sucker Punch Sally Boss Bike
It was a cold and rainy Ohio afternoon and Old School Jeff, a Sucker Punch ...
Event Features
WIN BY HARLEY-DAVIDSON RACERS JAKE LEWIS & CORY WEST
HARLEY-DAVIDSON® PAN AMERICA® ST RACERS JAKE LEWIS AND CORY WEST WIN IN MISSION SUPER HOOLIGAN ...
Roads to Redbud 2025
Hey all - anyone venturing to Buchanan Michigan on the 5th of July, for the ...
Happy Birthday ABATE Of Indiana
In the mid-seventies, the motorcycle rights movement really started in earnest. This is why many ...
AMA Motorcycle Hall of Fame Announces Class of 2025
Six distinguished motorcyclists to be inducted on Oct. 23 during the AMA Hall of Fame ...