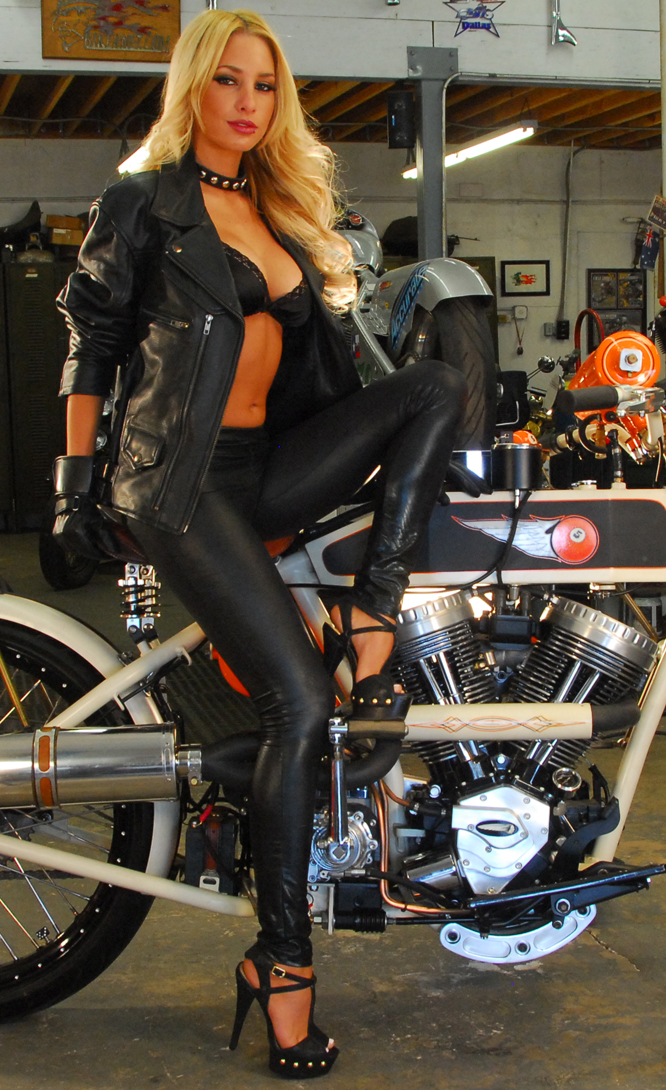
This has been the strangest tuning dilemma I’ve ever faced with a motorcycle in my 40 years of messing with these bastards. I fell in love with our Factory Racer CrazyHorse 100-inch engine. The day we started the bike for the first time, it fired to life immediately, no hiccups, stumbles, or coughs. Every time I hit the Phil’s Speed Shop electronic system starter button, it immediately rumbled to life. Then we attempted a break-in ride and it blubbered badly at mid-range. If I nailed it, it jumped forward, then stumbled and nearly died. I was perplexed.
At first we thought, and so did S&S, that our Crime Scene air cleaner, facing backwards, was the evil culprit. We began an extensive investigation. Larry Petri, the master Chop N Grind mechanic, came over and we tried some jetting changes, which didn’t seem to help. We went to Bonneville, so we shifted gears to our Peashooter project until we returned.
While cleaning the shop after Bonneville, I came across another S&S Super E, and installed it immediately. The bike did the same thing, so we ruled out the carb for a minute, and I investigated whether there was any chance it could be the ignition.
According to a few CrazyHorse experts, the Thunderheart ignition system could have been the problem, so I reached out to Thunderheart in Florida. They asked me to send them the ignition module and the cam sensor, which I did. They told me the cam sensor was defective and replaced it. I re-installed it and the bike did the same thing, blubbered at mid-range. I performed another Thunderheart test by running a power lead from the battery directly to the coil. No change. I tried the power lead to the other coil connection, and believe I blew out the ignition. It wouldn’t start again.
After speaking with several builders, I was convinced the problem was the Thunderheart. Frank at Black Hawk Motorworks builds a billet bottlecap cone, allowing us to install any Evo ignition to a CrazyHorse, so I headed in that direction. Frank recommended a mid-range S&S cam, which would require new adjustable pushrods, also from S&S. Ultimately, I ordered the S&S Quickee pushrods, so I didn’t need to remove the rockers for installation. Life was looking up. I also ordered a single-fire ignition from Compu-Fire, one of the easiest ignitions to install on the planet.
That’s the complicated direction we’re headed today, the S&S cam installation, the S&S pushrods, the Compu-Fire system install, and the whole unit detailed by Heather New, of New Line engraving.
First, I pulled the Thunderheart ignition, which I grounded to the bottom of the transmission, and we pulled the ignition cam sensor off the front of the engine.
Next, we pulled the pushrod caps and clipped off the pushrods with an old set of shop bolt cutters. The cutters were so old, I had to disassemble the cutters, grind the jaws, learn how to adjust the jaw alignment, and re-assemble the cutters. They worked fine. The S&S instructions always call for disconnecting the battery, which is a damn good idea. It’s always a good idea to run the engine to top dead center (TDC) before clipping the pushrods, so there’s a minimum of pressure on the rods and parts aren’t jettisoned around the shop.
With the stock non-adjustable pushrods out of the way, we could remove the cam, which was also an S&S unit 35-0157. We were going to replace it with an S&S 561V , part number #33-5076 configuration, which was recommended by Frank Aliano of BlackHawk Motorworks in Florida. He has studied and built products for the bottlecap Indian engines for years.
I removed the cam plate fasteners and carefully removed the plates. The BlackHawk Cone came with replacement gaskets and O-rings, but I was careful not to damage anything. The stock S&S cam slipped right out of place, along with the thrust washers. I dug around for more replacement thrust washers for setting up the proper cam clearance.
You need to read the S&S cam installation instructions closely. Depending on the year, the cam lobe height, the model, engine size, etc., you may need to follow different portions of the directions. For instance, S&S recommends that you replace the cam bearings in 1992 and later big twin engines with a Torrington bearing, which has a higher radial load rating and can handle the performance stress.
I replaced the cam several times and checked the clearance with various thrust washers. S&S calls for an endplay measurement of .005-.015. This CrazyHorse 100-inch monster has the new oil pump mounted to the front of the motor, so there was no breather gear alignment issue. I thought it was a breeze and aligned the cam dot with the pinion bearing. There was also a red paint mark on the pinion gear about two teeth from the alignment dot. The red mark was there for gear size when the engine was originally built, not alignment.
But after I bolted up the cam plate, I questioned my alignment and removed the plate again. The cam had two marks on it. One was for a breather and the other for the pinion gear. I needed to make sure I was using the proper indicator for pinion gear alignment.
I ducked through this process several times. Another stumbling block surfaced: the lifters didn’t stay securely in the lifter stools. In the old days, solid lifters stuck well above the stools, so they could be held by hand or with a rubberband while the cam and thrust washers were replaced. I monkeyed with this, even removed the rear lifter stool so I could check the endplay and push two lifters out of the way. Ultimately, a sharpened piece of welding rod, bent just so, helped with the process of holding the cam followers in line.
I bolted up the new cam chest plate, with new O-rings. I made sure to oil the cam bearing surfaces. I had a set of standard S&S adjustable pushrods, which require removing the rocker arm assemblies in an Evo configuration and dropping in the pushrods from the top. I anticipated a problem with this endeavor and ordered a set of S&S Quickee Pushrods for this application. I didn’t want to mess with the engine to create the clearance to remove the rear rocker box.
Again, when I received the instructions, they were broken down for virtually every model available, from Buells to Panheads. I went with the 1984-1999 Big Twin instructions, which call for rotating the engine until the front piston is as top of its stroke, with both front lifters at their lowest position (TDCC–top dead center, compression stroke). If you look in the timing hole of the Crazy Horse engine, a black dot indent emerges at TDCC, so it was a breeze to find. I cleaned the pushrod tubes and replace the O-rings with a light coat of oil, inserted the new pushrods through the tube assemblies, and installed each one in the proper position.
I extended the adjusting screw to remove all the lash in the pushrod, then compressed the hydraulic unit in the exhaust lifter four complete turns or 24 flats, then tightened the lock nut (Frank recommended 4.25 turns). Then you are required to wait 5 to 10 minutes before adjusting the intake pushrod, so the valves don’t run into each other. After the waiting period, the pushrods should turn with fingertips.
I repeated the above procedure for the rear cylinder, and then replaced the cover clips and spark plugs. The instructions called to starting the motorcycle and checking for leaks. That’s good info. I blew oil all over the place before I discovered a pushrod cover that hadn’t seated properly.
Here are a couple of helpful warnings. First, if you are unsure about the lifters, here’s a way to check it. If you adjust the pushrod down four turns and wait, then try to turn it with your fingertips, and it doesn’t turn, you have hydro-solids.
Next, S&S Quickee pushrods for all big twin engines contain two long and two short pushrods (exhaust-long, intake-short). All Sportster models and Twin Cam 88 pushrods are the same length.
Now I could install the Compu-Fire ignition system. I left the engine in the TDC position for this maneuver. Compu-Fire has several systems, including single fire, dual-fire, and kick-start units. You can remove your point system and drop in one of these puppies in a flash. The system is a breeze to tune and it’s and all-in-one unit in the cone.
I’ve known the boss of Compu-Fire, Martin Tesh, for a couple of decades. He knows his shit when it comes to these simple, easy-to-tune, solid-state units. The unit comes with complete instructions, but basically, you replace the cam plate, install the ignition plate in the cone with a drop of Loctite, and run the wiring harness to the coil. Install three wires, tune the bastard with the supplied magnets, and you’re good to go. It even has switch settings to allow you to adjust the timing curve at 35 degrees before top dead center at 1500 rpm, to 35 degrees at 3500 or 4,000 rpm, depending on the model. You flick a switch, test ride it, and it’s set.
Here are the official Compu-Fire ignition installation requirements. First, I cleaned out the pristine Black Hawk timing cavity. I didn’t need to worry about the seal, it was brand-new. I installed the trigger with the long supplied Allen screw, and checked the gap between the trigger and the ignition plate. It seemed excessive, so I checked it again, and installed the supplied shim to tighten the gap. I aligned the trigger with the notch and torqued the Allen screw to 25 inch-pounds. The large round TDC indicator ding in the flywheel was still centered in the timing hole, so I was good to go for timing.
Just to be sure, the locating cam notch falls in the same place for every big twin cam, if the TDC mark is on the compression stroke. It always comes up at 7:00, so I checked it and was good to go. If it wasn’t, I needed to run the engine over one more time to be on the correct compression stroke. It was time to set the timing.
The directions called for turning the ignition switch off and reconnecting the ground wire to the battery. The instructions called for stripping the Compu-Fire red wire and temporarily connecting it to the battery positive terminal. I rotated the timing plate counterclockwise to the full retarded position. The Accu-Ray timing light may be on or off when you start this procedure. I used the disc magnets to turn it off and on by swiping them across the timing plate. It’s like magic. I turned the light off, then rotated the plate clockwise until it popped back on. I did this several times until I could lock the plate in the exact spot where the light came on.
Frank, at Black Hawk suggested that I rotate the plate a hair past the light-on spot to advance the timing slightly. Then I locked the plate down and I was done. Except to install the new Heather New engraved timing plate cover.
I disconnected the hot lead, and then wired the Compu-Fire ignition system in place according to the single-fire wiring diagram with a new Compu-fire single-unit, single-fire coil.
Okay, so I fired the beast up and went for a ride. Same problem. It blubbered at mid-range. It had to be a carburetor issue, so I yanked the S&S and installed a Mikuni 42-mm slide carb. I pulled it out onto the street, fired it up, adjusted the mid range air nozzle and the idle screw, and slammed the tank shifter into first. She popped but ran like a top.
That did it. It had to be a jetting issue, but then an uncustomary California storm rolled in, and it rained solid for a week. Hell, it’s rained for six weeks in Brisbane, Australia. And we thought we had flooding issues. I’ve been working with Paul Cavallo and his teams at Spitfire on our 2011 bike build efforts. I’ve had the privilege to speak often to his main builder, Larry Scrotum, a guy who has been building bikes for as long as I’ve been writing about them. Just recently, during a break in the weather, I mentioned my problem to him, and he was the first to come up with real solutions.
It could still be the Crime scene air cleaner and the way it’s positioned, leaving the choke vent open. He says the air rushing over it causes a problem with the fuel delivery inside. I needed to block off the outside vent and take the Allen screw out of the underside of the body adjacent to the vent. I’ll let you know what happens next. He also made a tuning suggestion regarding the air bleed vent in the float bowel. I’ll let you know the outcome.
Contacts:
CrazyHorse
http://www.crazyhorsemotorcycles.com/
Black Hawk Motorworks
http://www.blackhawkmotorworks.com/
New-Line Engraving
http://www.new-lineengraving.com/
Compu-Fire
http://www.compufire.com/