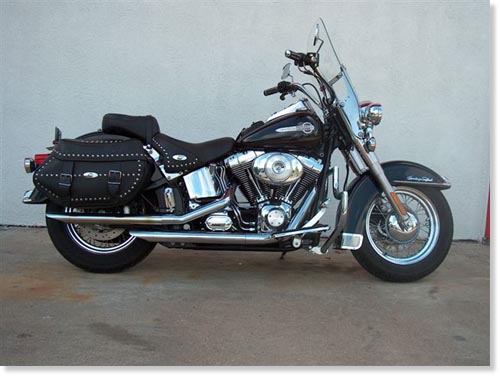

The before (top) and after shot of the Heritage modification.
A full moon glowed over the harbor the night a call came through from an irate reader, “You bastards had a Softail project and never finished it,” the caller exclaimed frothing at the mouth. “I'm comin' all the way to Califa to snatch your women, drink your whiskey and ride your Panhead home.”
I freaked. It wasn't the women or the whiskey, but the '48 El, dual-carbed Pan was family. That couldn't happen. That night I slept fitfully, tossing and turning, as if battery acid was dripping in my eyes. I had sizzling heartburn until the phone rang the next morning and I bolted out of the sack, as if a 9-point earthquake rocked the Bikernet headquarters. I lifted the receiver tentatively, “Yep?”
“My '91 Sporty was lacking in style and sex appeal,” Terrie said excitedly, “when my husband purchased his custom Road King from Lucky Devil. I was not going to allow him to out do me, so I decided to see what Kent & Eric could do for me. We explored all the options and wound up digging into my stock Sportster…”
I was going out of my mind. This woman disturbed my WA while my mind spun with terror over the loss of my Panhead. What did I care about her Sportster?
“The transformation began with conceptual design discussions,” she blithered while I sat on the edge of the bed and sensed the enraged reader storming closer to the headquarters. “As the project progressed, Lucky Devil kept me involved in all major design considerations. I can't tell you how happy I was with the end results. Would you feature it?”
“Okay, okay,” I said reaching for my pint of Jack on the dusty bed stand. I was half out of my mind. Who the hell was Lucky Devil?
“That'll be great,” she chimed in.
I was as depressed as an Cuantanamo Bay terror suspect.
“You should see their Softail frame stretch,” she muttered as if trying to spur the lagging conversation.
“What,” I snapped? There was hope suddenly. She told me about the two Houston builders, Kent and Eric, but there was a twist. She didn't know which guy owned what name?
“They go by Lucky Devil,” Terrie said concern in her voice. “I don't know which is Lucky and which is Devil? I don't know which is Eric and which is Kent. I swear, every time I'm in the shop Lucky becomes Devil and visa-versa.”
I was intrigued and gave them a call. I didn't care who I talked to. Within minutes they e-mailed images and the tech was in motion. Watch for Terrie's Sportster tech next week. I needed to move on this one.
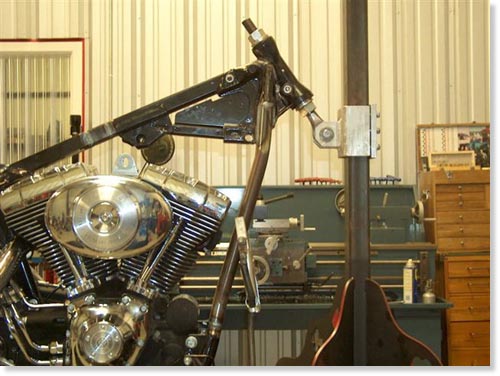
Eric and Kent have been in the metal fabrication industry for over a decade. Kent made handicapped people smile for five years building adaptive equipment, then another half decade welding and fabricating. The partnership has flourished in Houston for a year. Kent even has his own mobile secret frame table.
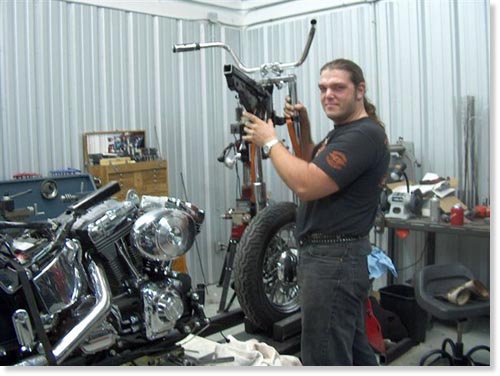
That's Lucky, Devil, Kent or Eric. Who knows?
“We stretched the backbone of Darryl's Heritage 2 inches and the down tubes 5 inches, and we only increased the rake 2 degrees,” said Lucky. They used the same quality seamless tubing as the factory an TIG welded the .120 wall mild steel segments into place.
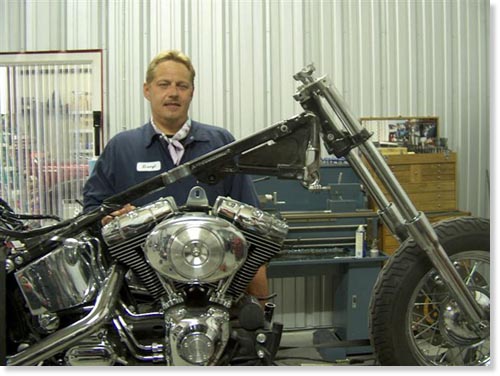
We know that this is the bike owner, Darryl. That's all we know.
“First we remove the front end and replaced the tubes with 6-inch over units. Then we stretched the square tubing back bone and set up the bike with the front end on the neck. Finally the downtube segments were tacked into place,” one of the partners explained. The frame was modified to make the front end length work perfectly.
“We ground out the tubing from the neck casting and replaced it with fresh material,” the Devil whispered.
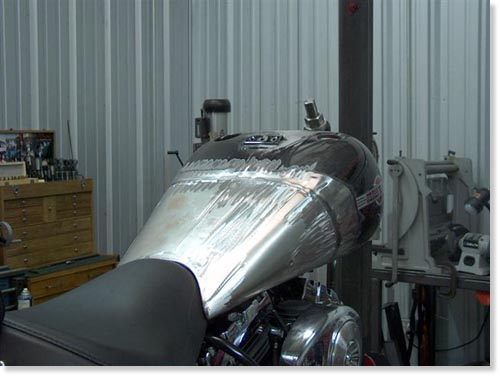
The stock frame was raked to 34 degrees, so this mod only bumped it to 36 degrees.
“After we installed the 6-inch over tubes,” Lucky explained, “we carved the plates out of the slider covers and made stretched covers with cold-rolled mild steel plate. Then the cowbells were chromed,” Lucky told me, I think. They also performed a cosmetic stretch on the tank.
“This was a fun project, it's not often you get to chop out a bagger,” Kent said, although I'm not sure.
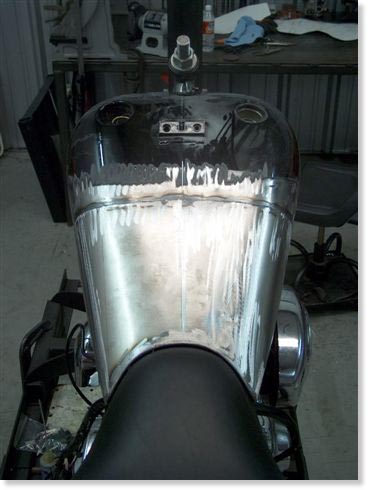
It takes 2-2.5 days to perform a front loop modification.
“We like them to handle well,” Lucky added, “No flopping around.”
A custom tank stretch takes 1.5 days.
“But the bike was down just under a month,” the Devil added. “Painters have a way of burnin' daylight.”
I couldn't tell who was who, either Lucky or Devil, but they do sharp work: Phone # 281-477-3590. Hope I sent that angry reader an e-mail in time. Thanks guys!
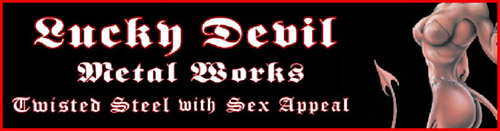